Betere onderhoudsplanning is MillerCoors silver bullet
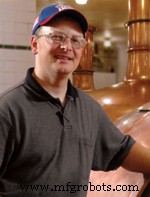
Plannen is niet sexy. Tom Clancy zal geen spionagethriller schrijven met de titel 'The Maintenance Planner'.
Je zet je vrienden niet op het randje van hun barkrukken om te vertellen over de tijd dat je alle nodige stappen hebt genomen en ervoor hebt gezorgd dat het revisieproject soepel verliep. ("Kerel, wat is er dan gebeurd?!")
Er is geen glitter of flits of eye-candy.
"Als een onderhoudsafdeling verbetering zoekt, ligt de nadruk meestal op het tonen van overwinningen en het maken van voor-en-na-foto's - 'wauw'-dingen", zegt Dan Roberts, de Asset CARE-directeur betrouwbaarheid voor Miller Coors in Golden, Colo.
"Voorspellend onderhoud is sexy. Met infraroodthermografie maak je een momentopname en zeg je:"Kijk eens wat ik heb gevonden." Met trillingsanalyse sluit je het aan, print je metingen en zegt:"Ja, ik heb een slechte peiling gevonden." Dat is allemaal belangrijk en noodzakelijk, maar in de kern wordt er goed gewerkt. Het is gewoon niet sexy. Hoe toont u de resultaten van effectieve planning en scheduling? Je kunt het niet doen met foto's van voor en na."
Stilletjes en heimelijk gebruikt de onderhouds- en betrouwbaarheidsorganisatie van MillerCoors planning en scheduling als een verbeteringsinstrument. Het zorgt voor balans in een omgeving waar onbalans grote gevolgen heeft.
De ketting onderhouden
MillerCoors, de op twee na grootste brouwer van Amerika, streeft al meer dan tien jaar naar verbeteringen in het onderhoud, en terecht. De Golden-brouwerij draait 24 uur per dag, zeven dagen per week, om elke dag 217 miljoen ounces bier te brouwen.
"Er zijn misschien twee dagen per jaar dat we niet produceren", zegt Tim Davison, een Asset CARE-planner in het brouwerijgedeelte van het grote complex met meerdere fabrieken in Golden.
Het bierbereidingsproces - van grondstoffen tot verpakte en verzonden goederen - verloopt in een nauw met elkaar verbonden keten, en veel procescomponenten zijn voorzien van niet-redundante machines. Als er een mechanische storing optreedt, is het verplaatsen van werk naar een soortgelijk apparaat mogelijk geen optie. In deze gevallen komt het proces tot stilstand.
"Als er een storing is, is dat meestal een groot probleem", zegt Ron Kerr, de Asset CARE-manager voor nutsbedrijven. "Het treft bijna iedereen stroomopwaarts en stroomafwaarts."
Persoperator Craig Doebele bedient de besturing langs de productielijn
op Rocky Mountain Metal Container, de joint venture MillerCoors/Ball.
Het doel is om machines maandenlang non-stop te laten draaien, vooral tijdens het hoogseizoen, totdat een kort onderhoudsvenster kan worden ingepland.
De unieke structuur van de Golden business units zorgt voor stress in de keten. Hoewel MillerCoors eigenaar is van de brouwerij, is het een gezamenlijke partner in de blikkenproductie (met Ball Corporation) en flessenproductie (Owens-Illinois). Iedereen in dezelfde richting laten trekken is noodzakelijk, maar het vereist geduld.
Het ontbrekende ingrediënt
Het tempo van verbetering van het onderhoud, jarenlang langzaam en gestaag, versnelde eind jaren negentig nadat topspeler Anheuser Busch prijsverlagingen aankondigde. Om concurrerend te blijven, probeerde MillerCoors opnieuw te investeren in de voorkant van het bedrijf.
"De kosten van onze goederen moesten met een grote marge omlaag", zegt Roberts. “We moesten achter een aantal elementen aan, waarvan operations er één van was. De kans en het doel was om de meest betrouwbare operatie mogelijk te worden.”
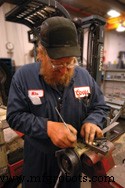
Asset CARE (een acroniem voor Capability, Availability, Reliability and Enhancement) werd de strijdkreet. Reliability-Centered Maintenance (RCM), root cause failure analysis (RCFA) en predictive maintenance (PdM) tools werden gebruikt. Zelfs met deze positieve stappen ontbrak er iets.
Roberts haalt het voorbeeld aan van een ventilator die drie dynamische storingen heeft ondervonden gedurende een tijdsbestek van 18 maanden. Na de eerste storing identificeerde RCFA smering als hoofdoorzaak. Er werd een automatisch smeersysteem geïnstalleerd. Na de tweede storing werden de automatische smeermiddelen als problematisch beschouwd. Na de derde storing deden onderhoudsleiders een stap terug.
"We nemen nu deel aan oefeningen voor het in kaart brengen van oorzaken waarmee we meerdere grondoorzaken kunnen onderzoeken", zegt Roberts. "RCFA zegt niet dat er één oorzaak is, maar het leidt mensen in die richting."
Door dieper te gaan, kwamen planning en planning naar voren als een bijdrage aan het probleem.
Een maand voor de derde storing had trillingsanalyse afwijkingen geconstateerd. Er zijn echter geen passende maatregelen genomen om onderhoud te plannen en er een prioriteit van te maken voordat er een storing optrad. De les:substantiële winst is onwaarschijnlijk als basisplanning en planning niet aanwezig zijn.
"Voorafgaand aan onze geconcentreerde inspanningen waren we niet per se aan het plannen en plannen", zegt Roberts. “Planners bekeken werkbonnen in het computersysteem, printen ze uit, gaven ze aan een supervisor en wachtten tot de supervisor ze uitdeelde aan de bemanning. Er werd weinig moeite gestoken in het wekelijks aan tafel zitten met de operaties en het bekijken van wat er stond te gebeuren, het bepalen van prioriteiten en het identificeren van middelen.”
De installaties functioneerden in een reactieve onderhoudsmodus. Planners besteedden veel tijd aan het zoeken, opslaan en verspreiden van vervangende onderdelen.
“Als onze organisatie vooruitstrevend is, vinden we de dingen die gecorrigeerd moeten worden, schrijven we de werkbon, plannen we de werkbon en krijgen we de klus geklaard. Als het reactionair is, kopen we eersteklas stoelen in vliegtuigen om een motor te vervoeren”, zegt Bobby McCall, onderhoudsmanager voor verpakkingsactiviteiten.
Reactief werk had zijn beloningen - schouderklopjes en bedankjes van de productie. Elk jaar werd een reizende trofee uitgereikt aan de planner die verantwoordelijk is voor de meeste nachtelijke leveringen.
Toen bedacht MillerCoors een betere manier door essentiële componenten van een effectieve onderhoudsplanning te identificeren. Deze maximaliseren de middelen, minimaliseren de kosten en verhogen de algehele betrouwbaarheid van de apparatuur. De secties die volgen, schetsen een aantal van deze componenten.
Dan Roberts is de Asset CARE-directeur van
betrouwbaarheid voor MillerCoors Brewing Bedrijf in
Golden, Colorado. Hoewel de fabrieken van het bedrijf
aanzienlijke vooruitgang hebben geboekt,
geeft hij toe dat "we er nog niet zijn."
Echt toegewijd
Zoals bij elke inspanning, is toewijding de sleutel tot succes. Bij MillerCoors begint vooruitstrevend onderhoud met toegewijde planners en middelen.
Een planningsorganisatie heeft het juiste aantal planners nodig. Elke planner moet een verantwoordelijkheidsgebied hebben dat is:
• redelijk in geografische omvang;
• redelijk in aantal vertegenwoordigd ambachtspersoneel; of,
• redelijk in aantal apparaten.
Hoe kan de planner zonder dergelijke grenzen de juiste tijd en middelen besteden om dat gebied effectief te onderhouden?
Davison zegt dat met een te groot gebied, één planner zich niet kan concentreren op het hele bereik, alleen op de slechte actoren en noodsituaties die zich voordoen. Wanneer een planner zich richt op slechte actoren en mislukkingen, is de noodzakelijke voorspellende en proactieve planning niet mogelijk.
"Twee mensen kunnen geen 4.000 apparaten plannen", zegt Davison. "Het enige waar ze tijd voor hebben is het bestellen van onderdelen."
Heftruckmonteur Jerry Mitchell verwijdert een wiel om
een lager voor preventieve onderhoudswerkzaamheden.
Met betrekking tot planner-to-craft-dekking, zegt Roberts dat zijn huidige doel één planner is voor elke 15 tot 18 ambachtslieden. De algemene regel is dat naarmate je verder komt in de richting van wereldklasse, je meer handwerkmensen per planner kunt hebben. Als je op de onderste sporten van de ladder staat, is een groter percentage planners geschikt.
Het doel van de brouwer is om zijn planners specifiek te beperken tot taken die betrekking hebben op de betrouwbaarheid en het onderhoud van het gedefinieerde verantwoordelijkheidsgebied. Anders kunnen planners gemakkelijk afgeleid worden door werk dat buiten hun rol en functie valt.
"Productie kan de planner zien als een 'go-fer' of een Wal-Mart, daar om aan al hun behoeften en wensen te voldoen", zegt Brad Simpkins, een Asset CARE-manager die verantwoordelijk is voor mobiele apparatuur.
Plant- en afdelingsbeheer kan planners ook hinderen bij administratieve, rapportage- en gegevensinvoertaken.
"Zonder de mogelijkheid om echte focus te hebben, wordt planning reactief", voegt Simpkins toe.
Even belangrijk is dat deze planners ook toegewijde middelen (tijd en mankracht) nodig hebben om gepland en gepland werk te voltooien. Dit kan een bittere pil zijn voor sommige onderhouds- en productiemedewerkers.
"Sommige monteurs zeiden per uur:'We vinden het leuk wat we nu doen.' Ze vinden het leuk om op het witte paard te komen en de dag te redden", zegt Jay Johnson, de onderhoudsmanager voor procesbewerkingen. “Maar ze zagen dat het management hier 100 procent achter stond. Dit zou niet verdwijnen."
Productiemanagers en operators waren ook huiverig om het witte paard in de wei te zetten.
In de verpakkingsorganisatie van MillerCoors was de onderhoudsploeg gelijk verdeeld over drie ploegen. "Hun doel was om machines te repareren en aan de gang te krijgen", zegt Kerr.
Toen kwamen de eerste wijzigingen in de planning. Een aanzienlijk percentage van de ambachtslieden die 's nachts en in het weekend werkten, werden overgeschakeld naar gepland werk in de dagploeg.
"De productie vertelde ons:'U ondersteunt onze storingen niet!'", zegt Kerr. "Je hebt gelijk. Ik ga je storingen niet ondersteunen. Ik ga het proactieve werk ondersteunen. Het was een sprong in het diepe om ze dat te laten accepteren.”
Van de functionele afdelingen binnen MillerCoors is de verpakking momenteel de pionier in het pushen van toegewijde middelen naar proactief, gepland werk.
"We gaan 100 procent van de beschikbare uren plannen voor gepland onderhoud", zegt McCall. "We horen nog steeds:" Dat kun je niet doen; pannes moet je plannen.’ Nee, pannes gaan we niet plannen. We zullen plannen om gepland werk te doen. We zullen de storingen oplossen als ze zich voordoen."
Op alle niveaus moet de organisatie zich realiseren dat operators en ambachtspersoneel in een productiefaciliteit bestaan, omdat er een proces is om te bedienen en te onderhouden. Planners zijn er om de effectiviteit van operators en beheerders te maximaliseren. Wanneer alle niveaus in de operatie als een team beginnen samen te werken, voor een gemeenschappelijk doel van verbeterde operationele betrouwbaarheid en prestaties, is er niet langer een focus op "white horse wins" maar op duurzame winst op lange termijn.
Tijdbeheer
Een andere sleutel tot het planningssucces van MillerCoors is het maximale uit uw tijd halen.
Zoals opgemerkt in de vorige sectie, was de productie een beetje sceptisch. Als onderhoud de pijn van de productie zou verlichten, zouden deze 'vooruitstrevende denkers' hun waarde moeten bewijzen. Onthoud dat een offline machine enorme gevolgen kan hebben.
Een uitdaging was om de productie te laten inzien dat het beter was om een machine gedurende 40 minuten stil te leggen voor preventief onderhoud gedurende een vooraf bepaalde tijd en dag dan een uitval van drie uur na een storing op een onbekende tijd en dag. De extra uitdaging was om de productie te laten geloven dat de kostbare tijd niet verloren zou gaan.
“We hadden een slechte staat van dienst met planning en planning. We moesten bewijzen dat als je ons de tijd geeft, we het geplande, proactieve werk gedaan krijgen”, zegt Davison. “Ze hebben de lijn naar beneden gehaald. Ze zijn geld aan het verliezen. Je moet het meeste uit dat venster halen.”
Tijdmaximalisatie vindt plaats door effectieve planning en planning.
Ten eerste moet een onderhoudsvenster duidelijk worden gedefinieerd (geplande tijd, datum, omvang en duur) en overeengekomen door onderhoudsplanners en productieleiders. Van daaruit bestelt de planner alle benodigde onderdelen en materialen en zorgt hij ervoor dat de juiste hoeveelheid middelen beschikbaar is om de klus te klaren. De planner ziet erop toe dat er geen verrassingen of, erger nog, afmeldingen optreden als het loket opengaat. Vastgelopen of niet-productieve onderhoudsarbeid heeft een directe impact op de kosten voor het bedrijf.
Betrokkenheid stopt daar niet. Tijdens het raam observeert, assisteert en evalueert de planner het werk om zo volledig kennis van het werk te krijgen. Die kennis wordt toegepast om soortgelijke taken in de toekomst beter te plannen en in te plannen. Hij of zij verdient ook een mate van respect en waardering van de ambachtslieden die aan het werk zijn. Dit is essentieel wanneer er later technisch advies en vragen rijzen.
Hoewel dit bij MillerCoors de conventionele, plan-as-work-arises-methode is, bestaan er ook gespecialiseerde plannings- en planningsmethoden.
De fabriek voor de productie van blikjes, die constant moet draaien om aan de behoeften van de brouwerij te voldoen (12 miljoen blikjes per dag), maakt gebruik van een downtimeplan van 12 maanden dat gezamenlijk wordt ontwikkeld door managers op het gebied van operations, onderhoud, engineering, procescontrole, kwaliteit, magazijn en planning.
Het plan voor 2005 vermeldt de data, locaties, onderhoudsactiviteiten en projectdetails voor 1.655 uur geplande uitvaltijd. Het plan voor 2006 werd in september uitgewerkt.
"We zetten 20 mensen in een kamer en zoeken het uit als een team", zegt David Miller, de directeur van technische diensten voor Rocky Mountain Metal Container (de joint venture MillerCoors/Ball). “We zetten alles op de planning en onderzoeken, wat kunnen we nog meer doen tijdens die storing? Hoe kunnen we die tijd maximaliseren? We kunnen gedurende het jaar niet voor verrassingen komen te staan. We moeten voorop lopen. Daarom is het downtimeplan ons leidende document om de betrouwbaarheid van de apparatuur te garanderen en de levering van aluminium blikjes om aan de vereisten van de brouwerij te voldoen.”
De fabriek voor flessenproductie, die 3 miljoen flessen per dag produceert, maakt gebruik van toekomstgericht denken voor geplande sluitingen van één machine en volledige fabrieken.
"Vroeger draaiden we het hele jaar door en stopten toen met Kerstmis voor preventief onderhoud (PM)", zegt Tim Hood, manager engineeringservices bij Rocky Mountain Bottle Company (de joint venture MillerCoors/Owens-Illinois). "De rest van het jaar heb je te maken met storingen als ze toeslaan, omdat we geen andere uitvaltijd hebben gepland."
Tegenwoordig plannen planners en onderhouds- en productieleiders in deze fabriek downtime-sessies die 'maxi-pitstops' worden genoemd. Net als bij het downtimeplan van de blikfabriek, worden deze stops voor PM's en revisies ruim van tevoren vastgelegd.
“We plannen verschillende machines op verschillende tijdstippen”, zegt Hood. “Zo heb je niet al je apparatuur in één keer leeg. We verplaatsen de middelen om de downtime te compenseren.”
Een jaarlijkse sluiting van de fabriek, onder leiding van één enkele planner, vindt plaats in september.
"Hij is betrokken bij het hele plan en probeert erachter te komen wat er tijdens de storing moet gebeuren", zegt Hood. “We doen stoomreiniging op de machines en PM-en gedurende deze tijd alle elektrische distributieapparatuur. Het is een enorme onderneming. Als we de ene shutdown hebben afgerond, maakt de planner al een plan voor de volgende.”
Het brouwproces begint met het mouten van gerst.
Gerst wordt ondergedompeld in water en aangemoedigd om te ontkiemen.
Na vier tot vijf dagen wordt de "mout" verwarmd om verdere
groei te stoppen. De mout wordt vervolgens gekraakt door stalen rollen om
de inhoud ervan bloot te leggen.
Nuttige informatie
Het planningssucces van MillerCoors hangt ook samen met het optimaal benutten van informatie. Het begint met zoiets basaals als het verstrekken van nauwkeurige informatie over de beschikbare middelen voor een bepaalde dienst.
"Wie is hier? Hoe lang zijn ze hier? Met hoeveel middelen moeten planners plannen? Vroeger, zoals in elke reactieve organisatie, was het vaag”, zegt McCall. “In SAP leggen we het vast. Planners zien dat 'ik een venster van acht uur heb en tien mannen. Ik kan 80 uur aan werk plannen. Hier zijn 80 uur aan werk om aan dat plan te besteden.'”
Een ander voormalig grijs gebied waren werkorders. Zoals in de meeste fabrieken wordt er een werkorder aangemaakt wanneer werk wordt geïdentificeerd. Maar welke informatie staat er op die werkbon?
De onderhoudsleiders van MillerCoors leren van het verleden en zeggen nu dat een werkorder in staat moet zijn om de juiste apparatuurladingscode, alle apparatuurgeschiedenis, arbeids- en materiaalkosten en contractservicevereisten vast te leggen. Om apparatuurstoringen nauwkeurig te volgen, wordt een gedetailleerde werkbeschrijving ingevoerd wanneer de order wordt aangemaakt en een nauwkeurige beschrijving van wat er is gedaan om de storing te verhelpen, wordt ingevoerd na voltooiing van de werkorder. Als dit niet wordt gedaan, is de geschiedenis van een bepaald apparaat vervormd en kan het zijn dat er geen nauwkeurige verklaring is voor storingen of storingen. Ook wordt het juiste materieelnummer op de werkorder ingevuld. Zonder dit zijn essentiële maatregelen voor het bijhouden van de geschiedenis, zoals gebruikt materiaal en in rekening gebrachte arbeidsuren, gekoppeld aan het verkeerde apparaat of ontbreken ze volledig.
"In het verleden werden slechte beslissingen genomen omdat we geen nauwkeurige werkorderinformatie hadden", zegt Davison.
Wanneer een werkorder bij MillerCoors wordt aangemaakt, worden aantekeningen gemaakt om het volgende te helpen identificeren:
• alle onderdelen, vaardigheden of externe middelen die nodig zijn om het werk te voltooien;
• alle mogelijk noodzakelijke speciale gereedschappen, apparatuur of middelen; en,
• eventuele veiligheids- of milieuproblemen.
Met deze up-front informatie haalt de planner de benodigde onderdelen en materialen, verzamelt de benodigde middelen en plant en plant het werk nauwkeurig. Dit verhoogt de sleuteltijd.
Wanneer de klus is geklaard, voert een vakman gedetailleerde informatie in om de werkorder goed af te sluiten. In het SAP-werkordersysteem van het bedrijf voert hij of zij nauwkeurig een oorzaakcode, storingscode en objectdeel in op het laatste historiegedeelte van de melding. Een gedetailleerde, lange tekstbeschrijving van het uitgevoerde werk wordt gedocumenteerd, samen met eventuele problemen of discrepanties.
Maar al die stappen zijn waardeloos als je de informatie niet gebruikt.
Onderhoudswerkzaamheden zijn repetitief. Wat vandaag over een machine wordt geleerd, blijkt nuttig te zijn wanneer dezelfde of een vergelijkbare machine in de toekomst onderhoud nodig heeft. Geschiedenissen identificeren trends en helpen bij het ontwikkelen van effectieve betrouwbaarheidsstrategieën.
"Als de gegevens voor dat apparaat niet kloppen, krijg je niet het volledige beeld en maak je fouten bij het onderhoud van dat apparaat", zegt Davison. “Als het niet in het systeem wordt vastgelegd, heb je geen gegevens om te analyseren. De planners hebben dat nodig om te beslissen hoe ze het de volgende keer plannen, het beter doen en het voor de oorzaak gebruiken.”
Met correct ingevoerde werkorderinformatie heeft het personeel van MillerCoors toegang tot de werkorder- en kostenhistorie voor een individueel apparaat, afdeling, kostenplaats of hele faciliteit. Met deze gegevens bepalen planners PM-voltooiingspercentages, doorlooptijd van werkorders, gemiddelde reparatietijd en gemiddelde tijd tussen storingen. Ze hebben ook toegang tot de procentuele mix van PM, corrigerende, uitsplitsings- en projectwerkorders voor een bepaalde periode. Deze rapporten geven hen de tools om PM-frequenties aan te passen op basis van gegenereerde orders en MTBF.
"Op sommige apparatuur ontdekten we dat onze PM-frequenties te hoog waren", zegt McCall. “Onze planners bekijken regelmatig PM's. Zij zorgen ervoor dat de juiste PM, met de juiste frequentie, aanwezig is. Het idee is dat het werk dat we plannen het werk is dat gedaan moet worden. We willen onze tijd en geld zo goed mogelijk gebruiken en voor de juiste dingen gaan.”
Asset CARE-managers Bobby McCall (links) en Ron Kerr
bespreken motoren en tandwielkasten op de verpakkingslijn van de brouwerij.
Gouden resultaten
Planningsverbeteringen en planningsvaardigheden hebben een impact gehad bij MillerCoors.
"We hebben altijd geweldige mensen gehad met de wens om de juiste dingen te doen", zegt fabrieksingenieur Mike Fognani. "Door planning en planning kunnen we die geweldige mensen combineren met de tools, materialen en tijd die nodig zijn om succesvol te zijn."
Geplande en geplande werkzaamheden op veel locaties vormen nu meer dan 60 procent van de onderhoudswerklast; in het recente verleden was dat cijfer minder dan 30 procent.
Het voltooide PM-werk is dramatisch gestegen. Op het gebied van vorkheftrucks bijvoorbeeld, zegt Simpkins dat het voltooiingspercentage in minder dan 18 maanden van 31 procent naar 82 procent is gegaan.
De beschikbaarheid, productiviteit en uptime van apparatuur zijn allemaal toegenomen. Dit alles heeft geleid tot lagere onderhoudskosten.
"Vroeger was het 'onderhoud kan het niet draaiende houden', 'je bent niet betrouwbaar' en 'je geeft te veel geld uit'", zegt McCall. "Sinds we gestabiliseerd en proactiever zijn geworden, zijn onze onderhoudskosten gedaald."
Er zijn nog volop kansen.
"Op veel gebieden doen we wat we moeten doen en behalen we de resultaten die we zoeken", zegt Roberts. “We zijn op de goede weg, maar we zijn er nog niet. We hebben nog steeds kansen op het gebied van planning en planning, en we concentreren ons op manieren om stapsgewijze veranderingen door te voeren, zelfs in het kielzog van het geweldige werk dat al op stapel staat."
Lagere kosten. Verhoogde betrouwbaarheid. Betere beslissingen. Meer stabiliteit.
MillerCoors heeft misschien een manier gevonden om planning sexy te maken.
Alleen de feiten Site :MillerCoors-fabrieken in Golden, Colorado (inclusief de brouwerij en aanverwante productieondersteuningsgebieden), en Rocky Mountain Metal Container en Rocky Mountain Bottle Company (twee joint venture-fabrieken).Werkgelegenheid :Bijna 2.000 werknemers in de Golden-fabrieken.
Sitegrootte :Gelegen voornamelijk in een vijf mijl lange vallei in Golden.
Producten :Bijna een dozijn biermerken, waaronder Coors, Coors Light, George Killian's Irish Red Lager, Aspen Edge en Keystone. Ook moutdranken van het merk Zima.
Productievolume :Jaarlijks worden in Golden meer dan 20 miljoen vaten bier gebrouwen.
Onderhoud en reparatie van apparatuur
- Laat meer onderhoudswerk doen met een goede planning
- Effectieve onderhoudsplanning realiseren
- Ochtendvergaderingen:onderhoudsplanning en planning
- In onderhoud kunnen twee plus twee gelijk zijn aan acht
- Onderhoudsplanning:wat levert het u op?
- Teamwerk, planning en planning
- Reikwijdte voor onderhoudsplanners en anderen
- Boeing gaat akkoord met verbetering onderhoudsplanningsprocessen
- Is preventief onderhoud of voorspellend onderhoud beter?
- Waarom proactief onderhoud beter is dan alleen preventief onderhoud
- Onderhoudsplanning