Zorg ervoor dat spuitgietontwerpen klaar zijn voor productie met deze checklist
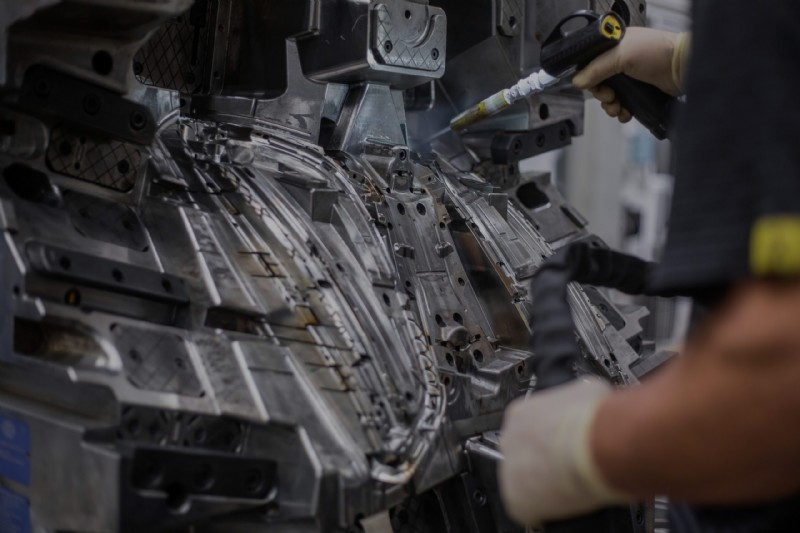
Spuitgieten maakt de productie van identieke onderdelen in grote volumes mogelijk tegen een lage prijs per onderdeel. Het proces omvat het injecteren van gesmolten materiaal in duurzame metalen mallen via een onder druk staande spuitmond, het uitwerpen van het onderdeel zodra het materiaal is uitgehard en dit wordt herhaald. Een breed scala aan alledaagse artikelen, waaronder waterflessen, plastic speelgoed en elektronicabehuizingen, worden gemaakt met spuitgieten. Terwijl thermoplasten en thermoharders de meest gebruikte materialen zijn bij spuitgieten, kan metaal ook worden gespuitgiet.
Wanneer u een onderdeel maakt met spuitgieten, moet u rekening houden met een aantal variabelen die van invloed zijn op de kwaliteit en functionaliteit van het eindproduct. Er zijn veel manieren waarop een spuitgegoten onderdeel kan falen, waaronder vloeilijnen, verzakkingen en kromtrekken, maar u kunt de meeste problemen voorkomen door een paar belangrijke ontwerpprincipes te volgen.
Hier bij Fast Radius werken we elke dag met klanten aan hun spuitgegoten onderdelen. Ingenieurs komen vaak naar ons met geweldige onderdeelontwerpen die moeten worden aangepast voordat ze effectief kunnen worden gemaakt. Onze experts op het gebied van ontwerp voor fabricage (DFM) hebben duizenden onderdeelontwerpen geëvalueerd en aangepast, en ze hebben de meest voorkomende problemen geïdentificeerd en gecompileerd. Door deze veelvoorkomende fouten in uw ontwerp op te lossen, kunt u kostbare fouten voorkomen en veel tijd besparen bij ontwerprevisies.
Voordat u uw onderdeelontwerp indient om te worden spuitgegoten, controleert u het aan de hand van deze lijst met ontwerpregels:
Gebruik de juiste diepgangshoeken
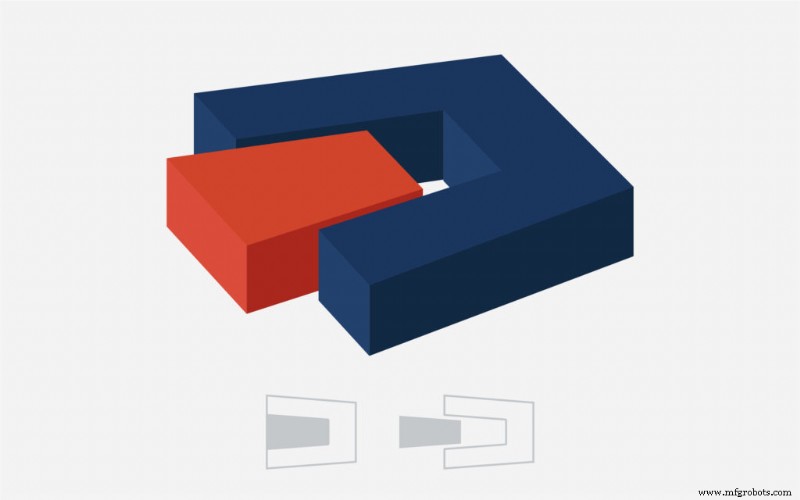
1,5-2 graden diepgang is doorgaans een veilig minimum voor de meeste onderdelen.
Trekhoeken verwijzen naar de zachte tapsheid die is toegevoegd aan de oppervlakken van een spuitgegoten onderdeel die uitgelijnd zijn met de trekrichting, waardoor het onderdeel uit de mal kan worden verwijderd zonder te worden beschadigd door wrijving of zuiging.
De vereiste trekhoek voor een onderdeel hangt af van een aantal factoren, waaronder de wanddikte, de krimpsnelheid van het materiaal van het onderdeel, de trekdiepte en of het onderdeel tijdens de postproductie een oppervlakteafwerking of textuur vereist. Hoewel de gemiddelde diepgang met 1 graad zou moeten toenemen voor elke extra inch onderdeeldiepte, is 1,5-2 graden diepgang doorgaans een veilig minimum voor de meeste onderdelen.
Behoud indien mogelijk een gelijkmatige wanddikte
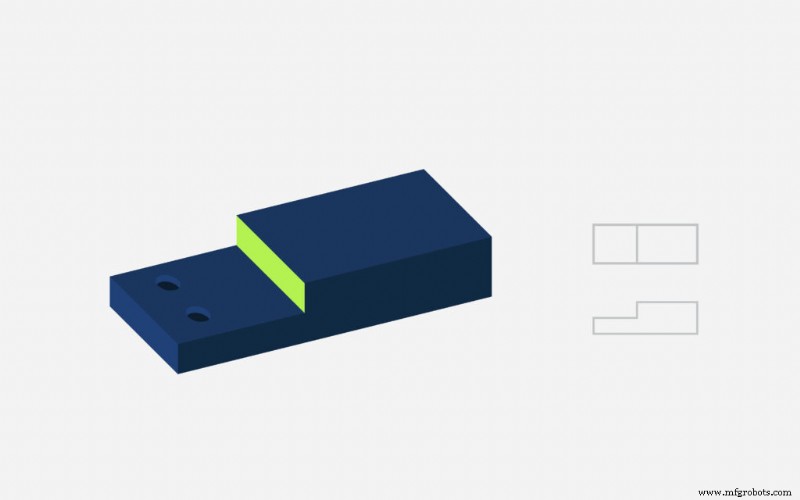
Indien mogelijk moeten spuitgegoten onderdelen over het gehele onderdeel een uniforme wanddikte hebben. Variaties in wanddikte kunnen ervoor zorgen dat het geïnjecteerde materiaal met verschillende snelheden afkoelt, wat kan leiden tot verzakkingen, holtes en kromtrekken.
Over het algemeen zijn wanddiktes tussen 1,2 mm en 3 mm ideaal (hoewel enige variatie kan worden verwacht, afhankelijk van het materiaal). De wanddikte moet bijna altijd onder de 5 mm blijven, omdat dikkere wanden de productiecyclustijden verlengen en ook de mechanische eigenschappen van het onderdeel negatief kunnen beïnvloeden.
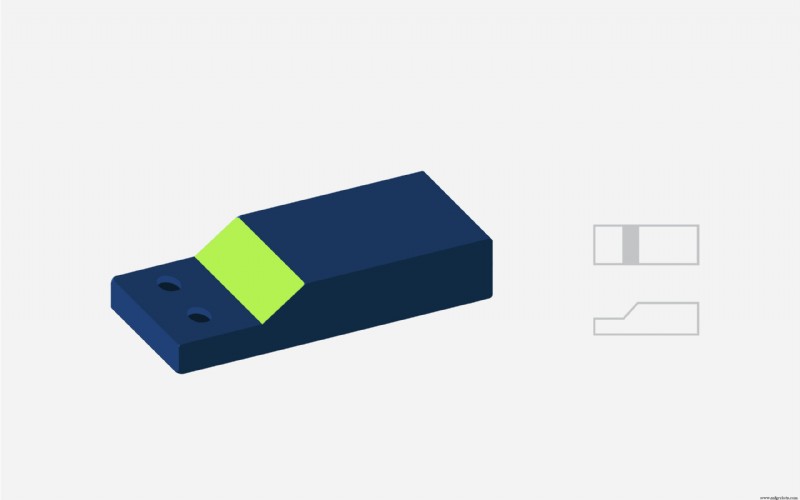
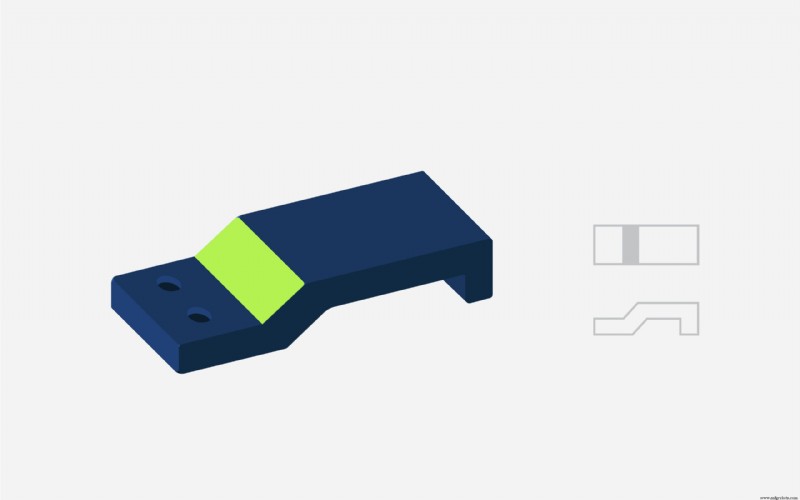
Als een onderdeel variaties in wanddikte vereist, moet je de overgang tussen secties zo geleidelijk mogelijk maken. U kunt dit doen door afschuiningen (aflopende hoeken of randen) of filets (afgeronde hoeken of randen) in het ontwerp van het onderdeel op te nemen, die ervoor zorgen dat het gesmolten plastic de mal volledig vult, grondig en gelijkmatig afkoelt en kromtrekken of niet -uniforme krimp.
Als algemene regel geldt dat de lengte van de overgang tussen secties met een verschillende wanddikte 3x de verandering in wanddikte moet zijn (bijv. als de wanddikte met 1 mm afneemt, moet de overgang over 3 mm plaatsvinden).
Ondersnijdingen vermijden
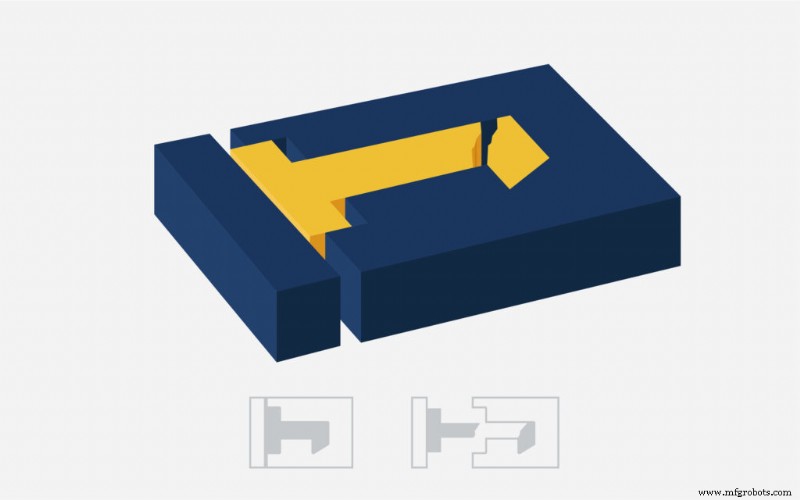
Ondersnijdingen zijn verzonken of overhangende oppervlakken of kenmerken - zoals schroefdraad, groeven of klikverbindingen - die voorkomen dat een onderdeel uit de mal wordt geworpen met een enkele, unidirectionele trekkracht zonder schade. Het is mogelijk om ondersnijdingen te vermijden door elementen evenwijdig aan de treklijn te oriënteren of door acties op te nemen in uw matrijsontwerp.
Ronde scherpe randen en hoeken af
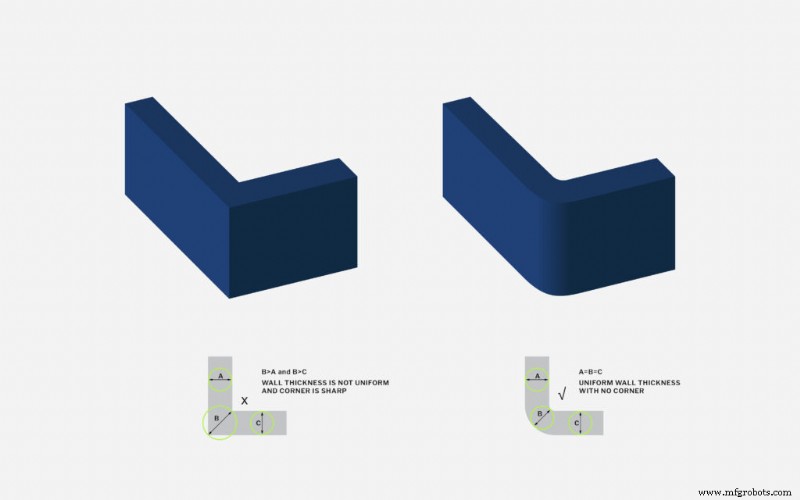
Waar mogelijk moeten ontwerpers en ingenieurs kiezen voor ronde kenmerken in plaats van scherpe randen en hoeken. Randen vereisen extra druk om te vullen, waardoor het moeilijker wordt voor een shot om efficiënt en gelijkmatig in de mal te vloeien. Scherpe randen hebben ook de neiging om tijdens het uitwerpen aan de mal te blijven kleven, waardoor het risico op beschadiging en defecten van onderdelen toeneemt. U kunt beide problemen vermijden met afgeronde binnen- en buitenhoeken.
Binnenhoeken, of die waar deelwanden de vloer raken, moeten een straal hebben van ten minste 50% van de aangrenzende wanddikte. Buitenhoeken, of die aan de bovenkant van deelmuren, moeten een straal hebben van 150% van de aangrenzende muur om plastic efficiënter en effectiever te laten stromen. Dit helpt ook om restspanning en barsten te minimaliseren.
De basis van alle verticale elementen binnen een onderdeel (zoals nokken, ribben of klikpassingen) moet ook afgerond zijn. Boss-radii moeten 25% van de aangrenzende muur zijn, met een minimale straal van 0,015” (of 0,381 mm).
Plaats scheidingslijnen strategisch
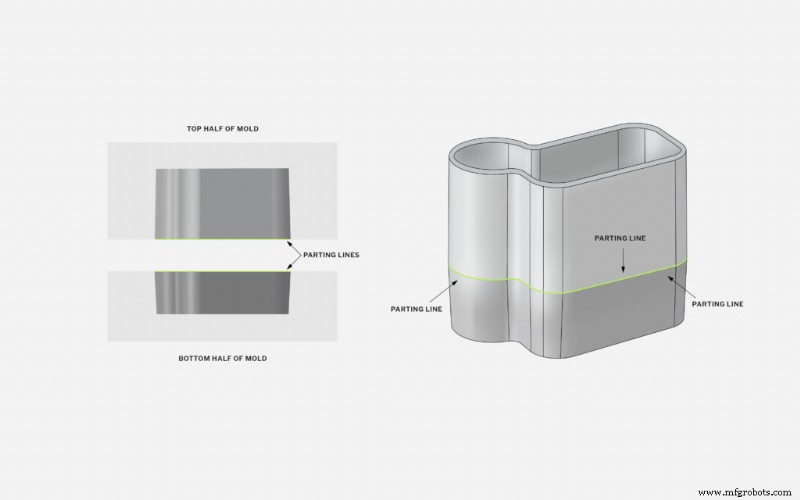
Een fysiek merkteken, bekend als de scheidingslijn, verschijnt waar de twee helften van een mal elkaar ontmoeten. In veel gevallen zijn scheidingslijnen gemakkelijk te zien en te voelen, maar het is meer dan een esthetische kwestie. De plaatsing van de scheidingslijn bepaalt hoe de matrijs opent (en dus de richting waarin u diepgang moet toevoegen aan de kenmerken van het onderdeel), en het kan zowel de kosten van matrijsgereedschappen als eventuele vereiste nabewerking beïnvloeden.
U kunt het uiterlijk en de functionaliteit van een onderdeel vaak verbeteren door de scheiding lang langs een rand te plaatsen in plaats van op een plat oppervlak. Dit helpt de naad te verbergen en vermindert ook de kans op flitsen (overmatig materiaal rond waar de mal samenkomt).
Overweeg plaatsing van uitwerppin
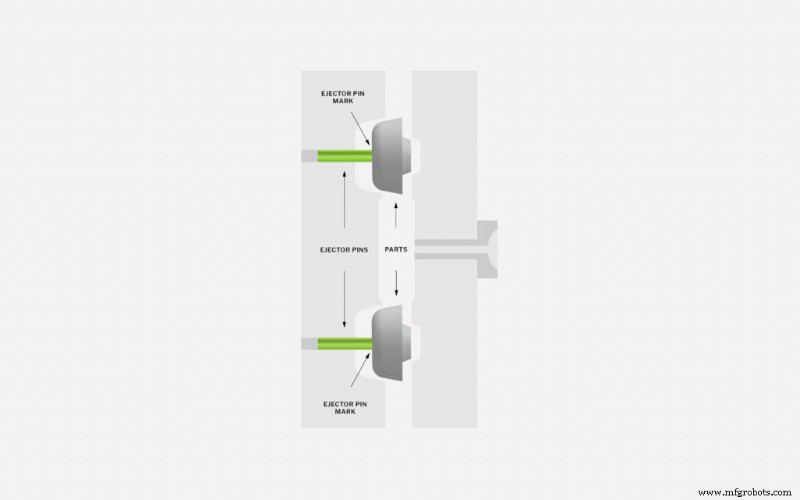
Om goed te werken, hebben uitwerppennen vlakke oppervlakken of kussens nodig, die loodrecht op de bewegingsrichting van de pen worden geplaatst. De plaatsing en het aantal pinnen moet worden bepaald door de vorm van het onderdeel, de ontwerphoeken, de textuur van de zijwand en de wanddiepte - die allemaal van invloed zijn op hoe een onderdeel zich aan de vormwanden zal hechten.
Materiaalkeuze moet ook worden meegewogen in de plaatsing of grootte van pinnen. Kleverigere harsen hebben bijvoorbeeld meer kracht nodig om uit te werpen. Evenzo hebben zachtere kunststoffen waarschijnlijk een groter aantal pinnen of bredere pinnen nodig om de uitwerpkracht effectief te verdelen en schade aan het onderdeel te voorkomen.
Optimaliseer de grootte van de steunribben
Ribben worden vaak gebruikt om deelwanden te versterken in situaties waar twee deelwanden elkaar ontmoeten in een hoek van 90 graden, of waar de lengte van een bepaalde sectie wordt verzwakt door de wanddikte van de sectie.
Het is belangrijk op te merken dat dikkere ribben niet noodzakelijkerwijs meer steun betekenen - in feite leiden ribben die te dik zijn vaak tot verzakkingen. De basisdikte van de steunribben mag maximaal tweederde van de dikte van de aangrenzende muur bedragen.
Let op de wanddikte van de mal
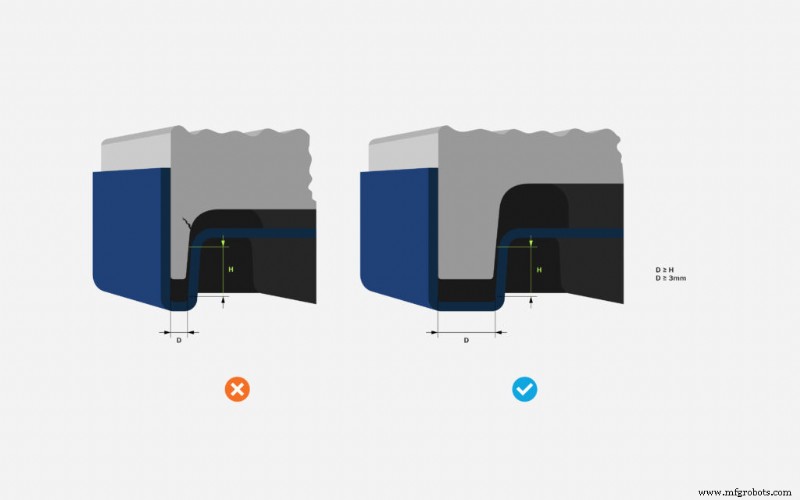
De dikte van de wanden van de mal is een andere belangrijke overweging - en een die voornamelijk wordt bepaald door de ruimte tussen de onderdelen van het onderdeel. Zorg ervoor dat verticale elementen, zoals ribben en nokken, niet te dicht bij elkaar staan, niet te dicht bij muren staan of dunne delen, omdat dit het koelproces bemoeilijkt.
De wanddikte van de mal kan ook van invloed zijn op de gereedschapskosten. De meeste spuitgietmatrijzen worden gemaakt door middel van CNC-bewerking en dunnere wanden van metaal in de mal zijn moeilijker goed te bewerken. Dunnere wanden resulteren ook in een kortere levensduur van de mal.
Hoewel de minimaal toelaatbare wanddikte van de mal wordt bepaald door de fysieke en mechanische eigenschappen van het materiaal van het onderdeel, is een speling van 3 mm tussen de onderdelen van het onderdeel over het algemeen acceptabel.
Efficiënt en effectief spuitgegoten onderdelen ontwerpen
Ontwerpfouten zijn duur. Het opnieuw knippen van een tool om een ontwerpfout te herstellen, kan productteams weken terughoudend maken en duizenden dollars kosten. Een goede productiepartner helpt u kostbare revisies met DFM te voorkomen, maar dat proces draagt ook bij aan uw tijdlijn. Als u uw ontwerp controleert op de problemen in deze handleiding voordat u het indient bij een productiepartner, kunt u sneller betere onderdelen krijgen.
Er zijn veel dingen die fout kunnen gaan bij spuitgieten, dus u moet een partner vinden die u kunt vertrouwen om uw onderdelen goed te krijgen. Hier bij Fast Radius zijn we er om het u gemakkelijker te maken en investeren we in het succes van uw project. Neem vandaag nog contact met ons op om aan uw volgende spuitgietproject te beginnen.
Voor meer informatie over spuitgieten - van materiaalkeuze tot de verschillen tussen mallen met één holte en meerdere holtes tot hoe we het proces hebben gebruikt om gezichtsmaskers te maken die de verspreiding van COVID-19 tegengaan - bezoek het Fast Radius-leercentrum .
Klaar om uw onderdelen te maken met Fast Radius?
Start uw offerteIndustriële technologie
- Spuitgieten met PolyJet-technologie
- Interface zes-assige robots met spuitgietpersen
- Hoe top spuitgietbedrijven meer kansen creëren met digitale marketing
- Wat zijn spuitgietfouten en hoe u ze kunt voorkomen:10 defecten aan kunststof onderdelen
- Micro Molding met polyurethaan
- Wat is reactie-spuitgieten?
- Gegoten versus spuitgieten
- Spuitgieten versus reactie-spuitgieten (RIM)
- Gietvormen versus reactie-spuitgieten
- Wat zijn de voordelen van kunststof spuitgieten?
- Undercut spuitgieten:effectief gebruik van ondersnijdingen in spuitgietontwerpen