Diep en smal snijden
OSG EXOCARB® WXS®-freesserie biedt betrouwbaar alternatief voor machinale bewerking van diepe holtes
Magnus Hoyer, OSG Duitsland
Een aantal uitdagingen, zoals slechte spaanafvoer, trillingen, klapperen, instabiliteit van het gereedschap en een slechte standtijd, worden vaak geassocieerd met het bewerken van diepe holtes. Bij diepe toepassingen worden de zijwanden van het werkstuk barrières voor een goede spaanafvoer. Spaanafvoer zou alleen maar erger worden naarmate een frees dieper in een onderdeel gaat. Bovendien kunnen gereedschapshouders en adapters in botsing komen met het werkstuk vanwege de hoge contour en de smalle baanomgeving. Bij standaard snijgereedschappen zijn de snijkanten volledig verbonden met het werkstuk, wat resulteert in zijdelingse snijkrachten die trillingen, klapperen en dus gereedschapsstoringen kunnen veroorzaken. Verspanen met elektrische ontlading (EDM) wordt vaak gebruikt als alternatief voor machinale bewerking van diepe holtes, maar het is zeer tijdrovend en kostbaar.
Meissner AG, een Duitse fabrikant van prototypes, productiegereedschappen en matrijzen, ondervond zo'n uitdaging bij het werken met de productie van watermantelkerngereedschappen die de verwerking van krappe zakken, smalle banen en hoge contouren vereisen. Als fabrikant die altijd op de hoogte is van de nieuwste productieapparatuur en -technologieën, heeft Meissner ontdekt dat zelfs met het gebruik van 5-assige bewerking, optimale prestaties niet kunnen worden bereikt voor dit soort werk.
Meissner, opgericht in 1922 en met hoofdkantoor in Biedenkopf-Wallau, Duitsland, biedt diensten aan, waaronder de ontwikkeling, het ontwerp en de productie van prototypes en productiegereedschappen en matrijzen voor klanten over de hele wereld. Productgereedschappen kunnen gereedschappen zijn voor het gieten van motorblokken, cilinderkoppen, autovelgonderdelen van verschillende materialen, blaasvormen voor brandstoftanks en vulpijpen, en meer.
Meissner heeft in totaal 340 medewerkers, van wie ongeveer 50 ingenieurs. Meissner legt grote nadruk op productexcellentie, betrouwbaarheid en continue innovatie. Meissner maakt gebruik van moderne apparatuur en technologie met vrijwel alle CAD-systemen in de auto-industrie en een op CAD gebaseerd gegevensbeheer om effectieve en efficiënte communicatie met zijn klanten mogelijk te maken.
Meissner is een van de eerste bedrijven in Duitsland die 5-assige bewerking introduceert. De verkorting van de cyclustijd en de toename van de precisie zijn twee grote voordelen van 5-assige CNC-bewerkingscentra. Productingenieurs bij Meissner hebben echter steeds vaker ontdekt dat het voor bepaalde componenten niet altijd zinvol is om te vertrouwen op 5-assige bewerking.
Volgens Christoph Schwarz, groepsleider mechanische productie bij Meissner, is het onvermogen om het potentieel van een 5-assig bewerkingscentrum volledig te maximaliseren, vooral duidelijk bij de bewerking van watermantelkerngereedschappen.
"Met deze tools hebben we krappe ruimtes, krappe zakken, smalle banen en hoge contouren", zei Schwarz. “Er worden grenzen gesteld aan de zwenkbewegingen van machines, waardoor de snelheden en voedingen afnemen.”
Volgens Schwarz leggen de rotatiebewegingen ook meer druk op de gereedschappen. Dus, afhankelijk van de geometrie van het werkstuk, is een 5-assig bewerkingscentrum niet altijd zinvol. Meissner heeft ook werkstukken met diepe caviteit bewerkt met EDM, maar dit is tijdrovend en kostbaar.
"Met het juiste gereedschap hebben onze vergelijkingen aangetoond dat we voor bepaalde werkstukken veel sneller zijn met een 3-assig bewerkingscentrum", zegt Schwarz.
Voor diepe en smalle holtes is meestal zeer lang en dun gereedschap nodig. De doorbuiging van het gereedschap is een veelvoorkomend probleem tijdens de verwerking. Om deze reden is Meissner op zoek gegaan naar een alternatief, omdat het noch schuin in 5-assig wilde frezen, noch voor EDM wilde kiezen.
Met de 2-groefs ring- en kogelfrezen van OSG lijkt een oplossing te zijn gevonden, met name voor het contourvoorbewerken en het afwerken van kerngereedschappen voor watermantels. Het idee om de ringkern- en kogelfrezen van OSG te gebruiken in combinatie met een 3-assig bewerkingscentrum ontstond aan het begin van het jaar uit een ander project. De ringkern- en kogelfrezen uit de WXS®-serie van OSG zijn om vele redenen gekozen, legt Schwarz uit.
“Ten eerste was het de positieve ervaring. OSG toonde altijd bereidheid in het beantwoorden van vragen, de levertijden waren kort en het advies was competent”, aldus Schwarz. "Belangrijker was echter het resultaat dat met deze snijgereedschappen werd verkregen."
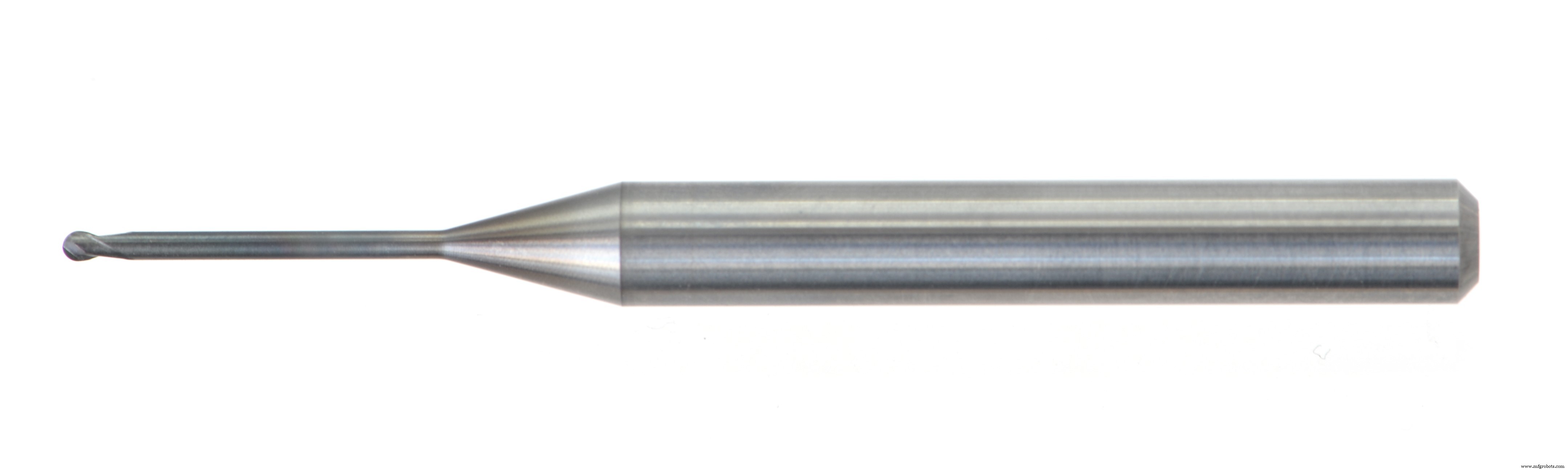
Terwijl de frezen in de WXS®- en WXS-C-serie afkomstig zijn uit het hoofdkantoor van OSG in Japan, worden gereedschappen uit de EPL-serie vervaardigd in de fabriek van OSG Duitsland in Göppingen. De WXS®-vingerfreesserie is ontworpen met een superharde coating met nanotechnologie voor een hoge hittebestendigheid. Het is ontworpen om uit te blinken in werkmaterialen boven 50 HRC. De originele WXL®-coating van OSG heeft een oxidatietemperatuur van 1300°C om hogere spilsnelheden en een langere standtijd mogelijk te maken, zelfs bij hogesnelheids- of droge bewerkingen. De unieke gereedschapsgeometrie maakt hoogwaardig en nauwkeurig frezen mogelijk, zelfs onder moeilijke bewerkingsomstandigheden. Naast de WXS®-vingerfrees, is de WXS-CRE een 5-snijder high-performance hardmetalen vingerfrees met een superradius en is ontworpen voor materialen tot 65 HRC. Last but not least, de EPL is een 2-fluits, high-performance, lange hals en kogelneusfreesserie ontworpen om uit te blinken in materialen van 45 HRC en tot 60 HRC.
Bewerkingsproeven werden uitgevoerd op het watermantelkerngereedschap met diepe holtes met behulp van 3-assig frezen. Gereedschappen van verschillende fabrikanten werden onder identieke omstandigheden op de proef gesteld. Volgens Matthias Bassler, Divisional Manager Production bij Meissner, viel de beslissing in het voordeel van OSG.
"We kijken niet naar de laatste seconde, maar tijd is ook een belangrijke factor voor ons", zei Bassler.
“We hebben heel veel, erg tijdrovende nabewerkingen. Kwaliteit, standtijd en betrouwbaarheid van het proces zijn van enorm belang. Een eventuele nabewerking die – om welke reden dan ook – nodig mocht zijn, zou een enorm effect hebben op de kosten. Onze tests hebben aangetoond dat we met dit materiaal een extra stap moesten uitvoeren bij het gebruik van gereedschappen van andere fabrikanten. Met OSG daarentegen ging alles goed", zei Bassler.
Naast productiviteit stelt Meissner ook strenge eisen aan maatnauwkeurigheid en oppervlakteafwerking. Kerngereedschappen zijn voorbewerkt met een optimale bewerkingsalliantie van 0,3 mm. Na afwerking moeten toleranties op alle niveaus binnen het gespecificeerde tolerantiebereik van 0,03 mm liggen. Dergelijke resultaten vereisen natuurlijk de juiste programmering.
"Om het werk goed te doen, is het noodzakelijk om eerst de gereedschapsvolgorde te bepalen", zegt Christoph Rothenpieler, CAM-programmeur bij Meissner.
“De gereedschappen voor het voorbewerken en voorbewerken moeten zo worden gekozen dat er later tijdens het nabewerken zo min mogelijk doorbuiging optreedt. Dit is de enige manier om een optimale contour voor te bereiden,” voegde Rothenpieler toe.
Voorwaarden voor het bereiken van een dergelijke precisie zijn sterk afhankelijk van het bewerkingscentrum en de snijgereedschappen. In dit geval leveren bewerkingscentra van Hermle de beste resultaten. Tachtig procent van de afwerkingswerkzaamheden wordt op deze machines uitgevoerd. Op het gebied van snijgereedschap weet OSG Sales Manager Uli Blöcher wat er echt toe doet.
"De verschillen tussen gereedschappen worden voornamelijk bepaald door de keuze van hardmetaal, de geometrie van de snijkanten, de stijfheid van de taps toelopende delen en vooral door de ondergrond of hoe het gereedschap werkt aan de snijkanten", zegt Blöcher.
OSG's EXOCARB® WXS®-serie biedt unieke snijgereedschapgeometrieën die zijn ontworpen om snellere cyclustijden met diepe toepassingen mogelijk te maken. De spiraalvormige snijtechnologie van de snijgeometrie helpt trillingen en gebabbel te minimaliseren, waardoor stabiel contourfrezen mogelijk wordt.
Bekijk deze korte video voor een vergelijking van de warmteontwikkeling tussen OSG's EXOCARB® WXS® en een vingerfrees van een concurrent in D2-gereedschapsstaal:
Meissners zoektocht naar een alternatieve verwerkingsoplossing heeft hen in staat gesteld een aantal 3-assige bewerkingscentra nieuw leven in te blazen, terwijl hun 5-assige bewerkingscentra in volle productie kunnen zijn met andere taken.
Met het juiste gereedschap kan een 3-assige bewerkingscentrum beter presteren dan een 5-assig bewerkingscentrum om de winstgevendheid te maximaliseren. OSG's gereedschap laat zien dat diep en smal snijden op een 3-assige mogelijk is met minimale trillingen, cyclustijd en insteltijd, terwijl tegelijkertijd de verwijderingssnelheid en de standtijd worden verhoogd. Soms kan het in twijfel trekken van een gevestigde methode de eerste stap naar vooruitgang zijn.
Eerder verschenen in SHAPE IT Magazine.
Industriële technologie
- De belangrijkste verschillen tussen 3-assige en 5-assige bewerking:
- Fabricage van bewerkte onderdelen:wat zijn de voordelen van machinale bewerking op hoge snelheid?
- NADCAP-certificering en hoe dit van toepassing is op de precisiebewerkingsindustrie
- Bewerking, disruptie en de komende jaren
- Roestvrij staal:de beste producten voor snijden, slijpen en afwerken
- Snijden van titanium en HRSA-metalen:bewerkbaarheid, koelvloeistoffen en meer
- Hoe kies je de juiste frees en programmering voor CNC?
- Draaicentrum en de bijbehorende bewerking
- Draaibankbewerking is veelzijdig en veel gebruikt
- Conventionele en niet-conventionele soorten bewerkingsprocessen
- De allure van lasersnijden