Oppervlakte- en interne kwaliteitscontrolemethoden van gietstukken
De inspectie van gietstukken omvat voornamelijk dimensionale inspectie, visuele inspectie van uiterlijk en oppervlak, analyse van chemische samenstelling en mechanische eigenschaptest. Voor gietstukken met hoge eisen is ook niet-destructief onderzoek vereist. Niet-destructieve testtechnieken voor kwaliteitsinspectie van gietstukken van nodulair gietijzer omvatten bijvoorbeeld vloeistofpenetratietests, wervelstroomtests, magnetische deeltjestests, radiografische tests en ultrasone tests.
Testen van oppervlakte- en nabije oppervlaktedefecten van gietstukken
Vloeibare penetratietesten
Vloeistofpenetratietesten worden gebruikt om verschillende openingsdefecten op het oppervlak van gietstukken te inspecteren, zoals oppervlaktescheuren, gaatjes in het oppervlak en andere defecten die moeilijk te vinden zijn met het blote oog.
De veelgebruikte penetranttest is kleurstoftesten, dat is om de penetrant met hoge permeabiliteit op het gietoppervlak nat te maken of te spuiten, de penetrant in de openingsdefecten te infiltreren, de penetrantlaag snel af te vegen en vervolgens de gemakkelijk te drogen ontwikkelaar op het gietstuk te spuiten oppervlak. Nadat de penetrant die in de openingsdefecten achterblijft eruit is gezogen, wordt de ontwikkelaar geverfd om de vorm, grootte en verdeling van de defecten weer te geven.
Er wordt op gewezen dat hoe gladder het te testen oppervlak, hoe beter het effect van penetratietesten. Het oppervlak dat door de slijper wordt gepolijst, heeft de hoogste testnauwkeurigheid en zelfs interkristallijne scheuren kunnen worden gedetecteerd.
Naast het testen van kleurstoffen is het testen van fluorescerende penetrant ook een veelgebruikte testmethode voor vloeibare penetrant. Het moet worden uitgerust met een ultraviolette lamp voor bestralingswaarneming en de testgevoeligheid is hoger dan de kleurstoftest.
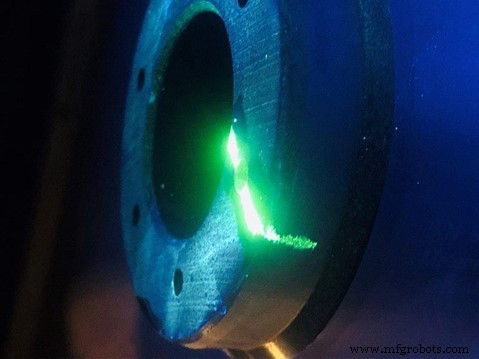
Wervelstroomtesten
Wervelstroomtesten zijn geschikt voor het testen van defecten onder het oppervlak die over het algemeen niet meer dan 6-7 MM diep zijn. Wervelstroomtesten zijn onderverdeeld in twee typen:de methode met geplaatste spoel en de methode met doorlopende spoel.
Wanneer het teststuk in de buurt van de spoel met wisselstroom wordt geplaatst, kan het wisselende magnetische veld dat het teststuk binnenkomt, wervelstroom induceren die vloeit in de richting loodrecht op het magnetische excitatieveld in het teststuk. Wervelstroom zal een magnetisch veld produceren dat tegengesteld is aan de richting van het magnetische excitatieveld, wat het oorspronkelijke magnetische veld in de spoel gedeeltelijk zal verminderen, wat resulteert in de verandering van de spoelimpedantie.
Als er defecten zijn op het gietoppervlak, zullen de elektrische kenmerken van de wervelstroom worden vervormd, om het bestaan van defecten te detecteren. De belangrijkste nadelen van wervelstroomtesten zijn dat het niet direct de grootte en vorm van de gedetecteerde defecten kan weergeven. Over het algemeen kan het alleen de oppervlaktepositie en diepte van de defecten bepalen. Bovendien is de gevoeligheid voor het testen van kleine openingsdefecten op het gietoppervlak niet zo gevoelig als het penetrant testen.
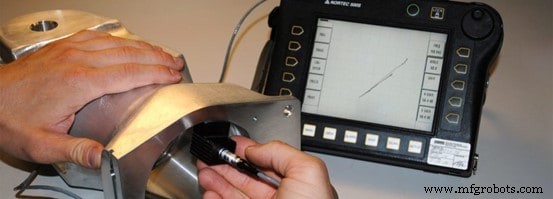
Testen met magnetische deeltjes
Magnetische deeltjestesten zijn geschikt voor het testen van oppervlaktedefecten en defecten enkele millimeters diep onder het oppervlak. Het vereist DC (of AC) magnetisatieapparatuur en magnetische deeltjes (of magnetische suspensievloeistof) om te testen.
Magnetisatieapparatuur wordt gebruikt om een magnetisch veld op de binnen- en buitenoppervlakken van het gietstuk te genereren, en magnetische deeltjes of magnetische suspensievloeistof worden gebruikt om defecten aan het licht te brengen. Wanneer een magnetisch veld wordt gegenereerd binnen een bepaald bereik van het gietstuk, zullen de defecten in het gemagnetiseerde gebied een magnetisch lekveld genereren. Wanneer het magnetische deeltje of de suspensievloeistof wordt gestrooid, wordt het magnetische deeltje aangetrokken, zodat de defecten kunnen worden weergegeven.
De defecten die bij het testen van magnetische deeltjes aan het licht komen, zijn in feite de defecten die dwars op de magnetische krachtlijn liggen, maar de lange strookdefecten evenwijdig aan de magnetische krachtlijn kunnen niet worden weergegeven. Daarom is het noodzakelijk om de magnetisatierichting tijdens bedrijf constant te veranderen om ervoor te zorgen dat elk defect in de onbekende richting kan worden getest.
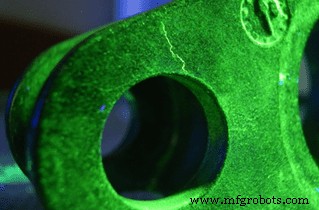
Testen van interne defecten van gietstukken
Voor interne defecten zijn de meest gebruikte niet-destructieve testmethoden radiografisch testen en ultrasoon testen. Onder hen is het effect van radiografisch onderzoek het beste. Het kan een intuïtief beeld krijgen dat het type, de vorm, de grootte en de verdeling van interne defecten weerspiegelt. Voor dikkere grote gietstukken is ultrasoon testen echter zeer effectief, waarmee de locatie, equivalente grootte en verdeling van interne defecten nauwkeurig kunnen worden gemeten.
Radiografische tests
Radiografische tests, in het algemeen röntgenstraling of γ-straling als de stralingsbron, de apparatuur voor het genereren van straling en andere ondersteunende voorzieningen zijn nodig. Wanneer het gietstuk wordt blootgesteld aan het stralenveld, zal de stralingsintensiteit van de straal worden beïnvloed door de interne defecten van het gietstuk. De stralingsintensiteit die door het gietstuk wordt uitgezonden, varieert plaatselijk met de grootte en aard van de defecten, waardoor een radiografisch beeld van de defecten wordt gevormd, dat wordt afgebeeld en vastgelegd door radiografische film.
De methode van opname door middel van radiografische filmbeeldvorming is de meest gebruikte methode, die gewoonlijk radiografisch onderzoek wordt genoemd. Het defectbeeld dat door radiografie wordt weerspiegeld, is intuïtief en de vorm, grootte, hoeveelheid, vlakpositie en verspreidingsbereik van defecten kunnen worden weergegeven.
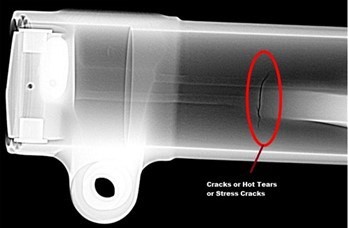
Ultrasoon testen
Ultrasoon testen maakt gebruik van de voortplanting van geluidsbundels met hoogfrequente geluidsenergie in het gietstuk om reflecties te genereren wanneer ze de binnenoppervlakken of defecten raken. De grootte van de gereflecteerde akoestische energie is een functie van de gerichtheid en eigenschappen van de binnenoppervlakken of defecten en de akoestische impedantie van een dergelijke reflector. De akoestische energie die wordt gereflecteerd door verschillende defecten of binnenoppervlakken kan dus worden toegepast om de locatie van de defecten, de wanddikte of de diepte van de defecten onder het oppervlak te detecteren.
Als een veelgebruikte niet-destructieve testmethode heeft ultrasoon testen de belangrijkste voordelen:hoge testgevoeligheid, die kleine scheurtjes kan testen; groot penetrerend vermogen, dat gietstukken met dikke secties kan detecteren. De belangrijkste beperkingen zijn:moeilijk te interpreteren reflectiegolfvormen voor discontinue defecten met complexe contourafmetingen en slechte gerichtheid; ongewenste interne structuren, zoals korrelgrootte, microstructuur, porositeit, insluitingsgehalte of fijn verspreide precipitaten, belemmeren ook de interpretatie van de golfvorm.
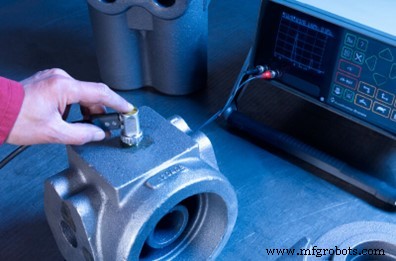
Industriële technologie
- Het gebruik van visuele inspectie bij activabeheer en kwaliteitscontrole
- Verbetering van kwaliteit en veiligheid in producttraceerbaarheid
- 4 redenen waarom het testen en inspecteren van apparatuur belangrijk is
- Wat is het testen van laskwaliteit? - 10 veelvoorkomende lasfouten
- Gids voor PCB-testmethoden
- Inleiding tot NDT (niet-destructief testen) voor gietstukken
- De basisprincipes van kwaliteitscontrole en inspectie bij CNC-bewerkingen
- Roterende vlakslijpmachine en verwerkingskwaliteit
- PCB-testen:een focus op in-circuit en functionele tests
- Gespecialiseerde methoden voor inwendig slijpen
- Op de hoogte:testen en inspecteren van robotonderdelen