Stereolithografie en digitale lichtverwerking:waar zijn we vandaag?
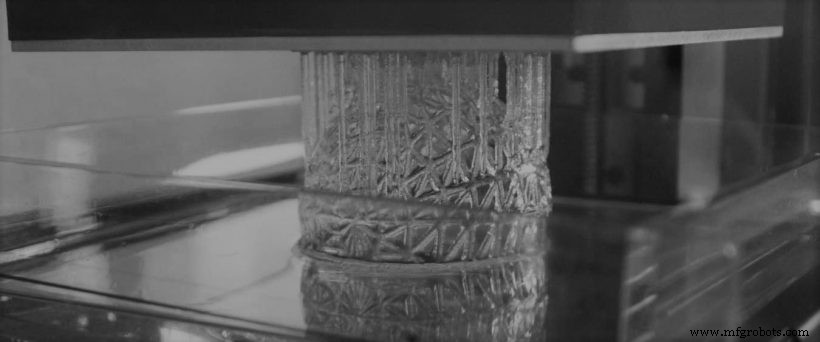
Stereolithografie (SLA) en Digital Light Processing (DLP) zijn twee van de meest populaire 3D-printtechnologieën die er zijn. Met een aantal overeenkomsten, vallen zowel SLA als DLP in de btw-polymerisatiefamilie van 3D-printtechnologieën. De twee technologieën hebben het afgelopen decennium een enorme evolutie doorgemaakt, waarbij ze van hun snelle prototyping-oorsprong naar productie zijn gegaan.
Dankzij de hoge precisie en uitstekende kwaliteit van de geproduceerde onderdelen, kunnen SLA en DLP worden gebruikt voor een breed scala aan toepassingen, waaronder functionele prototypes, tandheelkundige producten, consumentengoederen en zelfs sieradenvormen.
Na ons vorige artikel over de evolutie van 3D-metaalprinten, duiken we vandaag diep in stereolithografie en vergelijkbare 3D-printtechnologieën:hoe ze zijn geëvolueerd, huidige toepassingen en toekomstige kansen.
SLA, DLP en vatpolymerisatie:de voorwaarden uitgelegd
SLA en DLP vallen beide in de categorie btw-polymerisatie van 3D-printen.
Vt-polymerisatie is een 3D-printproces waarbij een lichtbron, zoals UV-licht, wordt gebruikt om vloeibare fotohardende harsen (ook bekend als fotopolymeren) uit te harden (stollen) om een vast onderdeel te creëren, laag voor laag.
In principe gebruiken zowel SLA als DLP vloeibare harsen en een lichtbron om 3D-geprinte onderdelen te produceren. Een belangrijk verschil tussen de twee technologieën ligt echter in het type lichtbron dat wordt gebruikt om het materiaal te stollen:bij SLA is dit een UV-lamp, terwijl bij DLP een digitaal lichtprojectorscherm wordt gebruikt.
Het SLA-proces begint met een 3D-printer met daarin een tank met UV-uithardende hars. Wanneer een print begint, wordt het bouwplatform ondergedompeld in de tank en volgt een laserstraal de contouren van een onderdeel, waardoor de laag vloeibare hars stolt. Zodra de laag voltooid is, wordt het bouwplatform neergelaten, waardoor er ruimte ontstaat voor de volgende laag.
DLP 3D-printers werken op bijna dezelfde manier als SLA-systemen. Het belangrijkste verschil is echter dat DLP een digitaal lichtprojectorscherm gebruikt om een afbeelding van elke laag tegelijk te flitsen. Omdat een hele laag harsmateriaal in één keer aan de lichtbron wordt blootgesteld, is DLP doorgaans een sneller proces dan SLA.
Hoewel het sneller is, moeten er compromissen worden gesloten in resolutie en oppervlakteafwerking als het gaat om DLP 3D-printen. Dit komt omdat de digitale lichtprojector licht in pixels levert - waardoor volumetrische pixels of voxels in de hars worden gecreëerd. Dit resulteert op zijn beurt in een gepixelde vorm die gladde randen voorkomt.
Er zijn ook andere, gepatenteerde technologieën die gebruik maken van harsmateriaal om polymeeronderdelen te maken. Bijvoorbeeld Carbon's eigen Digital Light Synthesis™ (DLS) technologie levert sneller hoogwaardige onderdelen dan veel andere 3D-printprocessen,
DLS gebruikt een fotochemisch proces waarbij licht door een zuurstofdoorlatend membraan in een vat met UV-uithardbare vloeibare hars wordt geprojecteerd. Een geprogrammeerd thermisch uithardingsbad of oven wordt vervolgens gebruikt om de mechanische eigenschappen van het onderdeel in te stellen om het te versterken.
Nu we de basisprincipes van vatpolymerisatie onder de knie hebben, gaan we eens nader kijken hoe de technologie is geëvolueerd.
De evolutie van SLA en DLP in kaart brengen
Het tijdperk van 3D-printen begon met stereolithografie. Hoewel de oorsprong van SLA gewoonlijk wordt toegeschreven aan uitvinder Chuck Hall, was het de Japanse onderzoeker, Dr. Hideo Kodama, die voor het eerst een nieuwe benadering introduceerde voor het uitharden van lichtgevoelige harsen met UV-licht in een laag-voor-laag manier.
De term 'stereolithografie' werd echter in 1984 bedacht door Hull, die met succes een patent voor de technologie indiende. Twee jaar later, in een poging om de technologie te commercialiseren, richtte Hull 3D Systems op, en de eerste SLA-machine werd in 1987 uitgebracht.
Hoewel de geschiedenis van SLA nauw verbonden is met 3D Systems, is de evolutie van DLP is nauw verbonden met een ander Amerikaans bedrijf:EnvisionTEC.
Al Siblani, CEO van EnvisionTEC, ontwikkelde in 2000 samen met zakenpartner Alexandr Shkolnik de eerste functionele DLP-printer. Twee jaar later bracht EnvisionTEC de eerste DLP-machine, de Perfactory 3D-printer, op de markt.
- 1981 :Dr. Hideo Kodama dient een octrooiaanvraag in voor een apparaat voor snelle prototyping, beschreven als een harsuithardingssysteem met laserstraal. Hoewel het apparaat kan worden gezien als een voorloper van stereolithografie, werd het volledige patent nooit voltooid - naar verluidt vanwege een gebrek aan financiering.
- 1984 :Chuck Hull dient een patent in voor een "Apparatus for Production of Three-dimensional Objects by Stereolithography".
- 1986 :Hull gaat verder met het oprichten van 3D Systems.
- 1987 :3D Systems commercialiseert het eerste SLA 3D-printsysteem — de SLA-1 machine.
- 2000 :Al Siblani en Alexandr Shkolnik van EnvisionTEC ontwikkelen het eerste functionele prototype van een DLP-printer.
- 2002 :EnvisionTEC brengt de Perfactory DLP 3D-printer op de markt.
- 2010s :Verschillende patenten voor SLA en andere 3D-printtechnologieën beginnen af te lopen, waardoor nieuwe bedrijven hun eigen SLA-systemen ontwikkelen.
- 2011 :Formlabs betreedt de 3D-printmarkt met zijn goedkope, professionele desktop SLA 3D-printer — de Form 1.
- 2013 :Photocentric ontwikkelt zijn Daylight Polymer Printing-technologie - een goedkopere 3D-printtechnologie die LCD-schermen als lichtprojector gebruikt.
- 2014 :Carbon onthult zijn Digital Light Synthesis (DLS)-technologie, die in staat is om met hoge snelheden te printen en onderdelen te produceren die wedijveren met de kwaliteit van spuitgieten.
- 2016 :3D Systems onthult de Figure 4, een modulaire, door robots aangedreven 3D-printer die is gericht op het automatiseren van het SLA 3D-printproces.
- 2018 :Adidas mass produceert 3D-geprinte tussenzolen voor zijn Futurecraft 4D-assortiment sneakers met behulp van Carbon's DLS-technologie.
De jaren 2010:een nieuw tijdperk voor SLA
De jaren 2010 waren bijzonder vruchtbaar als het gaat om de evolutie van SLA- en DLP-technologieën.
Tussen 2011 en 2016 ontstonden er verschillende nieuwe fotopolymerisatietechnieken, die de grenzen verlegden van wat mogelijk is met 3D-printen.
SLA naar desktop 3D-printen brengen
Desktop 3D-printen is van oudsher het domein van FDM.
Maar toen verschillende patenten met betrekking tot SLA tegen het einde van de jaren 2000 begonnen af te lopen, werd het potentieel voor desktop SLA 3D-printen geboren. Een bedrijf dat profiteerde van dit veranderende landschap was Formlabs.
Formlabs werd in 2011 opgericht met als doel om goedkopere SLA-desktopprinters op de markt te brengen.
Op de tijd bestond de SLA-markt uit grote, dure industriële 3D-printers, ontoegankelijk voor veel kleinere bedrijven.
De desktop-SLA-systemen van Formlabs hebben geholpen om deze status-quo te veranderen door machines aan te bieden die niet alleen kleiner zijn, maar ook voordeliger. Dit betekent op zijn beurt dat deze industriële machines toegankelijk zijn voor een breder scala aan bedrijven.
De overstap van SLA naar desktop was van cruciaal belang voor Formlabs, vooral omdat desktopsystemen steeds meer industriële toepassingen vinden. Inderdaad, slechts een paar jaar na de oprichting bereikte Formlabs de status van eenhoorn. Het bedrijf beweert 's werelds grootste verkoper van SLA 3D-printers te zijn, met meer dan 40.000 verkochte systemen.
In minder dan tien jaar heeft Formlabs zich gevestigd als een van de toonaangevende bedrijven in desktop SLA 3D-printen, dankzij een combinatie van technologische innovatie en scherpzinnig strategisch denken.
Nieuwe benaderingen van DLP ontwikkelen
Sinds de introductie op de markt in 2002 is de DLP-technologie gestaag geëvolueerd om een grotere nauwkeurigheid en hogere afdruksnelheden mogelijk te maken. EnvisionTEC, een leider in DLP-technologie, heeft aanzienlijk bijgedragen aan de vooruitgang op dit gebied.
Om fabrikanten de mogelijkheid te geven sneller te printen en grotere onderdelen te produceren, onthulde het bedrijf begin 2016 zijn Continuous Digital Light Manufacturing (cDLM)-technologie.
Een draai aan DLP-technologie , werkt cDLM door de bouwplaat continu langs de Z-as te bewegen. Vergeleken met traditionele DLP-methoden kan cDLM hogere printsnelheden van 20-50 mm/u leveren en kan het ook grotere onderdelen produceren.
Eind 2018 kondigde EnvisionTEC de release aan van het nieuwste systeem in zijn lijn van cDLM 3D-printers:de Envision One cDLM. De nieuwe lijn komt in twee modellen:de Envision One cDLM Dental en de Envision One cDLM Mechanical, respectievelijk ontworpen voor tandheelkundige en technische toepassingen.
Een nieuw licht schijnen op 3D-printen met fotopolymeer
Daylight Polymer Printing (DPP) is een van de nieuwste ontwikkelingen op het gebied van 3D-printen via vatpolymerisatie.
De technologie, ontwikkeld door de Britse harsspecialist Photocentric, geeft een nieuwe kijk op fotopolymerisatieprinten door gebruik te maken van daglicht in plaats van ultraviolet licht om verhard de hars.
Photocentric bereikt dit door zijn 3D-printers uit te rusten met in massa geproduceerde LCD-schermen. Het bedrijf onthulde de eerste daglicht fotopolymeer 3D-printer in november 2015.
Omdat de kosten van een LCD-scherm slechts een fractie zijn van de kosten van lasers of digitale lichtprojectoren, zijn de 3D-printers van Photocentric minder duur dan SLA /DLP-printers, terwijl ze dezelfde afdrukkwaliteit bieden (ter referentie, Photocentric biedt momenteel 3 machines aan, met een prijs die varieert tussen $ 2.300 en $ 4.800).
Photocentric, opgericht in 2002, is naar verluidt een van de weinige fabrikanten van fotopolymeerharsen ter wereld.
Naast het kostenvoordeel zijn er nog andere voordelen van DPP-systemen. De zeer lage lichtintensiteit genereert bijvoorbeeld bijna geen warmte tijdens het polymerisatieproces, waardoor het minder waarschijnlijk is dat een object tijdens het printen aan de harstank blijft kleven.
Maar misschien wel het grootste voordeel van allemaal, DPP maakt grootformaat afdrukken met hoge resolutie mogelijk tegen lage kosten. De onlangs onthulde LC Maximus 3D-printer van Photocentric demonstreert dit.
Ontwikkeld voor 'massaproductie en grootschalige prototyping', gebruikt de machine een 4K 40-inch LCD-scherm en heeft een bouwvolume van 700 x 893 x 510 mm. Met een prijs van minder dan $ 15.000 is de LC Maximus-printer zeer concurrerend met vergelijkbare SLA- en DLP-systemen.
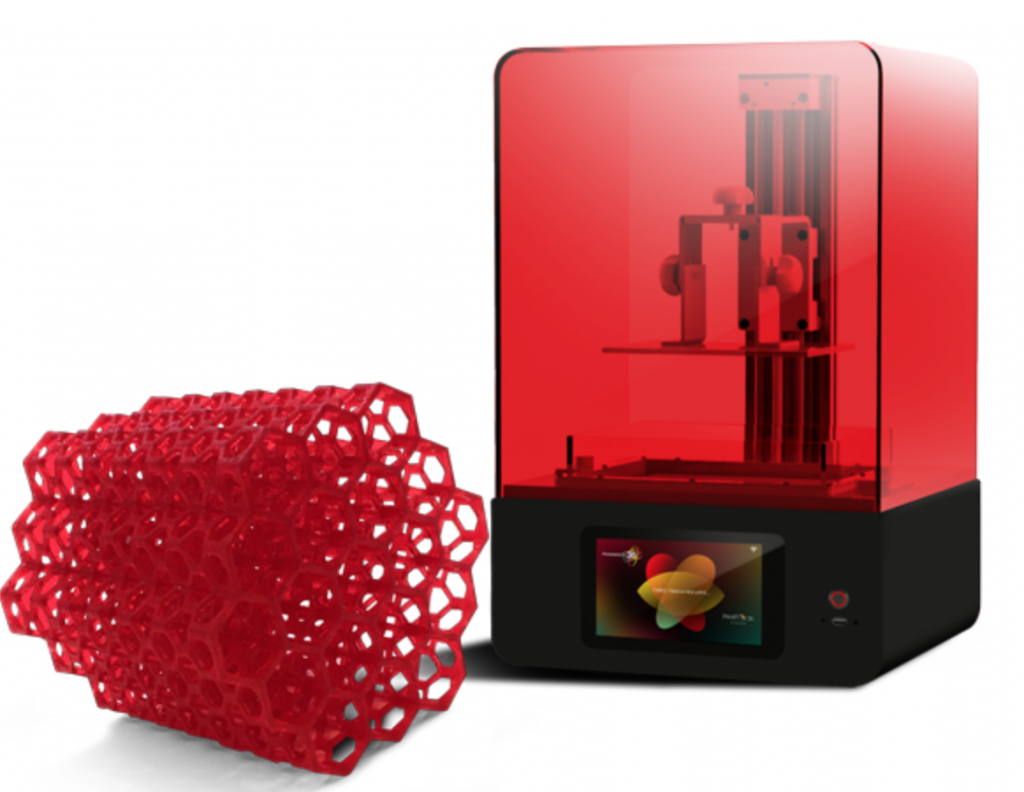
Hoewel de technologie van Photocentric nog steeds aan populariteit wint, kunnen de toegankelijkheid en voordelen ten opzichte van traditioneel SLA/DLP-printen het een levensvatbaar alternatief maken voor goedkopere SLA- en DLP-systemen.
De toestand van de materialenmarkt
De harsmarkt voor 3D-printen is het grootste segment binnen de AM-materialenmarkt geworden, met bedrijven als 3D Systems en EnvisionTEC die meer dan 25 eigen harsmaterialen aanbieden.
Dat gezegd hebbende, blijft de materiaalontwikkeling voor 3D-printen van fotopolymeer, dat wil zeggen bedrukbare lichtgevoelige harsen, traag.
Een obstakel voor een grotere materiaaldiversiteit is de gepatenteerde aard van veel harsmaterialen. De kosten zijn natuurlijk een andere.
En die twee gaan hand in hand. Een gepatenteerd materiaalmodel resulteert doorgaans in hogere materiaalprijzen en een langzamer innovatietempo voor nieuwe materiaalformuleringen. En toch, om de industrie te laten bloeien, is het belangrijk om toegang te hebben tot een zo divers mogelijk scala aan materialen.
Een ecosysteem voor open materialen tot stand brengen
Een mogelijke weg vooruit is een open materialenmodel.
Voor sommigen, om 3D-printen levensvatbaar te maken voor productie, moeten er honderden materialen van technische kwaliteit beschikbaar zijn - een hoeveelheid die waarschijnlijk niet door één bedrijf alleen kan worden bereikt.
Door strategische samenwerkingen en partnerschappen kan een open materialenbenadering een snellere materiaalontwikkeling mogelijk maken en de acceptatie van 3D-printen op de fabrieksvloer versnellen.
Origin is een bedrijf dat ontwikkelde een programmeerbare fotopolymerisatietechnologie (P3), die in de komende maanden gelanceerd zal worden. De technologie van Origin belooft verder te gaan dan standaard fotopolymeren om nieuwe soorten thermoharders en een geheel nieuwe chemie aan te bieden.
De sleutel hiervoor zal het Open Additive Production-platform van het bedrijf zijn, dat afhankelijk zal zijn van partnerschappen om de keuze aan materialen die beschikbaar zijn voor gebruikers van de technologie uit te breiden.
Tot nu toe, Origin heeft al samengewerkt met twee grote chemische bedrijven, BASF en Henkel.
Een andere nieuwe speler die de open materiële benadering omarmt, is Fortify. Fortify, opgericht in 2016, heeft $ 2,5 miljoen opgehaald om zijn gepatenteerde Fluxprint-technologie op de markt te brengen. De technologie zou in staat zijn om hoogwaardige composietmaterialen te verwerken.
Het bedrijf heeft zijn Fortify Fiber Platform opgericht om materiaalbedrijven en harsleveranciers te verwelkomen om samen met het team van materiaalwetenschappers en ingenieurs van Fortify hoogwaardige harsen te ontwikkelen. DSM, specialist in fotoactieve harsen voor AM, is een van de eerste partners van het Fortify Fiber Platform geworden.
Tot nu toe heeft Fortify koolstofvezel en met glasvezel versterkte harsen ontwikkeld, die naar verluidt de sterkste harsen zijn die op de markt verkrijgbaar zijn.
Uiteindelijk zou de open materiële benadering de industrie dichter bij massaproductie met additieven kunnen brengen, waardoor meer toepassingen op grote schaal mogelijk worden.
Op zoek naar productie
SLA en DLP gaan vooruit als massaproductietechnologieën. In één case study verving DLP 3D-printen de traditionele productie van hoortoestellen volledig.
Hoortoestelfabrikant Sonova, een marktleider op de hoortoestellenmarkt, gebruikt sinds 2001 DLP-technologie om op maat gemaakte hoortoestellen voor in het oor te produceren. Tegenwoordig maakt het bedrijf 3D-prints van honderdduizenden jaarlijks unieke stukken.
Met behulp van de technologie produceert Sonova de schelpen voor in-het-oor hoortoestellen, die zijn afgestemd op de individuele behoeften van elke drager. Het bedrijf is van mening dat dit niveau van maatwerk alleen mogelijk is met 3D-printen.
Andere industrieën zien ook succes met deze 3D-printtechnologieën, met schoenen als primair voorbeeld.
Vat-polymerisatietechnologieën bieden een aantal voordelen voor de schoenenindustrie. In 2018 kondigde sportkledingmerk Adidas bijvoorbeeld de massaproductie aan van Futurecraft 4D-sneakers met 3D-geprinte tussenzolen, mogelijk gemaakt dankzij Carbon's DLS-technologie.
De tussenzolen van de sneakers zijn gemaakt om slijtage te weerstaan en zijn gemaakt van een vloeistof van polyurethaanhars en hebben een complexe roosterstructuur in de hiel en voorvoet.
Deze structuur houdt rekening met voor de verschillende dempingsbehoeften van de drager tijdens het hardlopen, waardoor hogere prestaties en meer comfort mogelijk zijn.
Hoewel dit slechts twee voorbeelden zijn van massaproductie met 3D-printen, zijn de implicaties ervan bemoedigend:het is verre van een hulpmiddel alleen voor prototyping, SLA/DLP en 3D-printen als geheel zijn geschikt voor complexe productie eisen.
Stereolithografie:een voortdurende evolutie
Als het gaat om SLA, DLP en de bredere familie van vatpolymerisatietechnologieën, een van de belangrijkste trends, hoe toepassingen van de technologieën steeds meer evolueren naar productie op schaal. Deze trend wordt aangedreven door belangrijke technologische ontwikkelingen:snellere, nauwkeurigere systemen, een breder scala aan beschikbare harsmaterialen en natuurlijk toegang tot goedkopere desktopalternatieven.
Hoewel de technologie waarde blijft toevoegen aan reeds bestaande applicaties, zal de ontwikkeling van meer geautomatiseerde, schaalbare systemen deze applicaties nog meer verbreden. Met nieuwe ontwikkelingen die de hele tijd worden onthuld, is het zeker een opwindende tijd om getuige te zijn van deze evolutie.
3d printen
- Een inleiding tot stereolithografie (SLA)
- Waar bevindt u zich in uw reis naar automatisering van additieve productie?
- Stereolithografie — de originele 3D-printtechnologie
- Ontwikkelingsnormen voor 3D-printen:waar staan we vandaag? (update 2020)
- Industrie 4.0 fact-check:waar staan we vandaag?
- Digitale lichtsensor
- Waar worden lineaire actuatoren gebruikt?
- Waar staan de industriële bedrijven in hun digitale transformatie?
- De digitale fabriek:waar staan we in de snelle evolutie van industrie 4.0?
- Stereolithografie (SLA) 3D-printontwerptips
- Stereolithografie (SLA) 3D-printen:technologieoverzicht