Interview met experts:Andy Kalambi, CEO van RIZE, over het duurzaam en schaalbaar maken van industrieel 3D-printen
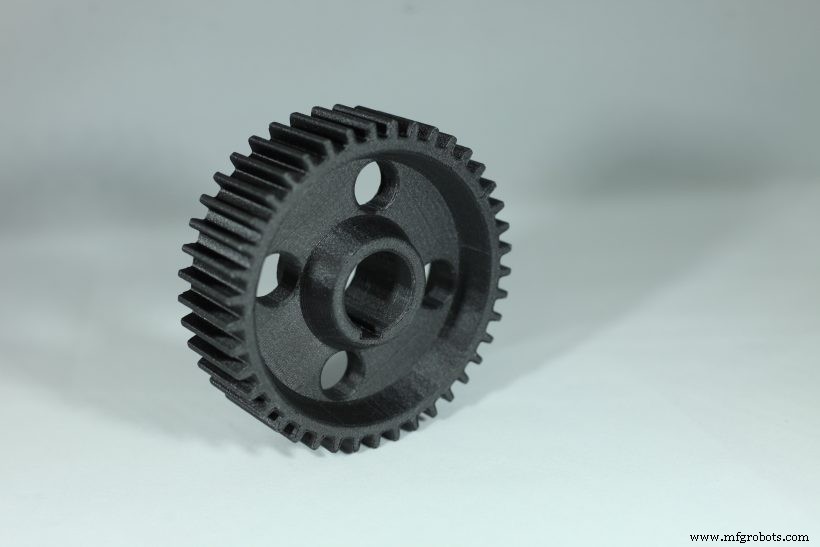
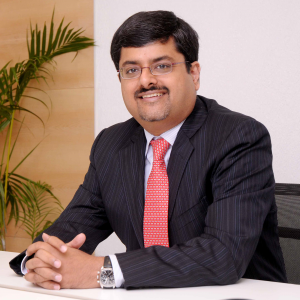
RIZE is een fabrikant van 3D-printers met een ambitieus doel: industrieel 3D printen inclusief, duurzaam en schaalbaar. Het in Boston gevestigde bedrijf, opgericht in 2014, heeft zijn eigen Augmented Deposition-technologie ontwikkeld, ontworpen om de productie van hoogwaardige, digitaal versterkte 3D-geprinte onderdelen mogelijk te maken.
Deze week zijn we verheugd om met Andy Kalambi, CEO van RIZE, te praten over de unieke voordelen van de APD-technologie van RIZE, de toekomst van industrieel 3D-printen en hoe bedrijven aan de slag kunnen met de technologie.
Kun je me iets vertellen over je achtergrond in AM en hoe je bij RIZE bent gekomen?
Ik ben werktuigbouwkundig ingenieur van opleiding. Ik begon in de software-industrie, meestal in de productie, en werkte in het begin van mijn carrière in de ERP-ruimte met SAP. Daarna stapte ik over naar de afdeling productlevenscyclusbeheer en werkte ik 17 jaar bij Dassault Systèmes.
Mijn achtergrond in additive manufacturing kwam van Dassault Systèmes, waar we ontwerpsoftware voor AM ontwikkelden. Ik had veel rollen binnen Dassault Systèmes, en in mijn laatste was ik de CEO van een van hun merken, ENOVIA. Ik leidde ook het 3DEXPERIENCE®-platform, een digitaliseringsplatform.
Ik kwam in november 2017 bij RIZE. Een van de redenen waarom ik bij het bedrijf kwam, was dat ik zag dat additive een ruimte zou worden die transformatief zijn in termen van impact op productie, toeleveringsketens en ontwerp.
Ten tweede zag ik dat additief echt een convergerend platform is waar software, materialen en hardware samenkomen om uiteindelijk het onderdeel te produceren. Ik zag de convergentie in mijn eigen ervaring in productie en ontwerp hier.
Uiteindelijk heb ik voor RIZE gekozen omdat het bedrijf een zeer unieke benadering van de markt heeft, waarvan ik dacht dat deze zeer schaalbaar was.
Wat is de visie van RIZE?
De visie van RIZE is heel eenvoudig:we willen 3D-printen inclusief en duurzaam maken. Door het inclusief en duurzaam te maken, geloven we dat deze technologie echt kan schalen.
3D-printen bestaat al sinds 1986, toen stereolithografie voor het eerst werd uitgevonden. Sindsdien is de technologie enorm geëvolueerd. De technologie is echter grotendeels in het domein van experts geweest en veel mensen hadden zelf geen toegang tot de 3D-printers. Ook al werkte ik voor het grootste 3D-softwarebedrijf ter wereld, Dassault Systèmes, we hadden niet al te veel 3D-printers om ons heen.
De reden is dat 3D-printen complex is. Er is veel complexiteit verbonden aan de machine, evenals de voor- en nabewerking van het onderdeel. Die complexiteit creëert de behoefte aan expertise en specialisatie. Het creëert ook de behoefte aan faciliteiten waar de printers uit de buurt van de gebruikers worden gehouden.
Daarom heeft RIZE zich niet alleen gericht op het vinden van nieuwe manieren om een onderdeel te maken, maar ook op de gebruikerservaring. We hebben ons ten doel gesteld de gebruikerservaring te vereenvoudigen om het gemakkelijk en veilig te maken, en daardoor elke gebruiker in staat te stellen industrieel 3D-printen te gebruiken.
Wij geloven dat met een dergelijke benadering 3D-printen een een tool die door veel verschillende stakeholders binnen een organisatie wordt gebruikt. Daarom geloof ik dat RIZE anders zal zijn.
We hebben vorig jaar de IDC Award gewonnen als een van de vier topvernieuwers. Dit jaar hebben we de Frost &Sullivan Award gewonnen voor beste praktijken op het gebied van nulemissie. Mensen beginnen de waarde te waarderen van wat 3D-printtechnologie kan doen als het gemakkelijk en veilig wordt gemaakt.
RIZE heeft zijn eigen Augmented Deposition-technologie ontwikkeld. Kunt u uitleggen wat de technologie is en wat de waarde ervan is voor de markt?
We hebben de Augmented Deposition-technologie ontwikkeld om drie belangrijke problemen in de branche op te lossen.
Het eerste en grootste probleem dat we wilden oplossen, betrof de voor- en nabewerking. Tot 80% van de tijd en kosten van het 3D-printen zit niet in het daadwerkelijke printen van het onderdeel, maar in het voorbereiden van het onderdeel voor het printen en het vervolgens gereed maken voor gebruik.
Het verwijderen van de ondersteuning is een onderdeel van dit proces. Een ander onderdeel is ervoor zorgen dat het object goed wordt afgedrukt, zodat het niet faalt. 3D-printen is een proces waarbij het materiaal laag voor laag wordt afgezet om het onderdeel te maken. Deze benadering creëert echter enkele zwakke punten rond bepaalde dimensies in het onderdeel. Dat probleem wilden we ook oplossen.
Het tweede probleem dat we wilden oplossen was om 3D-printers volkomen veilig te maken voor gebruik overal en door iedereen. Dit betekent dat het materiaal bij het printen geen dampen mag afgeven.
Ten slotte wilden we het probleem van authenticiteit bij 3D-printen oplossen. Wanneer je een onderdeel 3D print, is het erg moeilijk om te bepalen of het een authentiek onderdeel is, omdat iedereen een model kan nemen en afdrukken.
Om deze problemen op te lossen, hebben we gekeken naar alle bestaande technologieën en zag dat de enige weg vooruit was om een hybride proces te creëren. We hebben de Fused Filament Fabrication-technologie gebruikt en deze gehybridiseerd met een inkjettechnologie.
Het resultaat is een innovatieve en gepatenteerde technologie genaamd Augmented Deposition.
Met Augmented Deposition, de extrusietechnologie creëert het onderdeel door gesmolten polymeren af te zetten. De jetting-technologie deponeert de inkten. Augmented Deposition gebruikt twee soorten inkten, lossing en markering, elk met zijn eigen functie.
De functie van lossingsinkt is het creëren van een dunne laag die het onderdeel en de ondersteunende structuur scheidt. Hierdoor kunnen gebruikers de steunen eenvoudig als een klittenband verwijderen. Met een markeringsinkt kunt u tekst en afbeeldingen in het onderdeel plaatsen. Dankzij de markeringsinkt kunt u het onderdeel authenticeren door merkinformatie, revisienummers en QR-codes in het onderdeel te plaatsen.
Neem als voorbeeld QR-codes. U kunt een QR-code koppelen aan elke gegevensbron die u heeft. U heeft bijvoorbeeld informatie in een ERP-, CRM- of productlevenscyclusbeheersysteem. U kunt uw onderdeel in principe op deze systemen aansluiten, dus wanneer het onderdeel wordt geprint, wordt niet alleen het fysieke onderdeel maar ook het digitale onderdeel afgedrukt.
Onze technologie stelt gebruikers in staat hun onderdelen te koppelen aan een digitale platform en creëer een digitale draad tussen het onderdeel en alle digitale informatie die er is.
Je kunt ook gebruikmaken van zaken als augmented en virtual reality. Met QR-codes kunt u niet alleen het onderdeel zien, maar ook alle gerelateerde informatie. U kunt bijvoorbeeld zien hoe het onderdeel moet worden gemonteerd of welke onderdelen bij dat onderdeel horen.
Dus hoe werkt het Augmented Deposition-afdrukproces precies?
Het hele proces begint met een CAD-model. U neemt dit digitale model en exporteert het naar onze software die het model voorbereidt om te worden afgedrukt. De software voert bijvoorbeeld automatisch een snijproces uit. Vervolgens genereert onze software snel de ondersteuningen.
Het enige wat u hoeft te doen is een bouwplaat in te voeren en het onderdeel via een geheugenstick of via het netwerk te verzenden. In wezen is het slechts één druk op de knop, waarbij u een onderdeel kiest en op de afdrukknop drukt.
De machine is volledig geautomatiseerd wat betreft het uitlijnen en gereedmaken voor het afdrukproces. Meestal moet je bij andere 3D-printers een bouwplaat uitlijnen en voorbereiden door er een soort lijm op te doen. Dat is allemaal niet nodig met onze 3D-printers.
Als het onderdeel wordt geprint, wordt de inkt in het onderdeel gespoten. Dan hoef je alleen maar dat onderdeel van de bouwplaat te halen en de steunen eraf te halen.
Dit proces, dat vroeger uren in beslag nam, duurt nu slechts ongeveer een halve minuut. Bij andere extrusieprocessen moet u het onderdeel nemen en in een chemisch bad doen, handschoenen gebruiken en de chemicaliën zeer zorgvuldig beheren en afvoeren. Dat alles vereist een bekwame technicus en een aparte ruimte om dat hele proces te beheren.
Al deze problemen worden geëlimineerd met onze Augmented Deposition-technologie.
Welke bedrijfstakken of branches kunnen het meeste profiteren van uw technologie?
Laat me eerst de drie verschillende toepassingsgebieden van de Augmented Deposition-technologie behandelen.
Het eerste gebied is prototyping. Momenteel heeft 3D-printen de grootste impact op prototyping. 3D-geprinte prototypes bieden een haptische ervaring en laten u zien hoe een onderdeel aanvoelt en eruitziet voordat u beslist over verdere ontwerpiteraties.
3D-geprinte prototypes zijn ook een geweldige manier om ideeën en ontwerpen over te brengen aan verschillende belanghebbenden. Door het onderdeel in hun handen te kunnen houden, kunnen ontwerpers, ingenieurs en belanghebbenden het onderdeel nauwkeuriger en sneller beoordelen in vergelijking met 2D-tekeningen of 3D-modellen.
Om waarde toe te voegen aan deze toepassing, hebben we' verplaats de machine naast de ingenieur, waardoor hij de prototypes veel sneller klaar kan krijgen. Gewoonlijk moeten technici tussen een dag en soms twee weken wachten om het onderdeel in handen te krijgen. Nu kunnen ze het binnen enkele uren krijgen - en ze kunnen het naast hen doen.
Het tweede gebied is de productie, waaronder het ontwerp van aangepaste gereedschappen zoals mallen en armaturen.
Het derde gebied waar 3D-printen steeds meer wordt gebruikt, zijn serviceonderdelen. Als je iets moet repareren, maar je hebt er niet meteen een reserveonderdeel voor of je hebt niet genoeg reserveonderdelen, dan kun je 3D-printen gebruiken om vervangende componenten te produceren.
Vanuit de industrie gezien, onze 3D-printers worden veelvuldig gebruikt in de automobielsector, zowel door OEM's als in de toeleveringsketen, op alle drie de gebieden die ik zojuist noemde.
Onze machines worden gebruikt in de biowetenschappen, voornamelijk voor preklinische ontwikkelingsactiviteiten, bijvoorbeeld om aangepaste apparatuur in 3D te printen om een medicijnformulering te testen. Binnen de life sciences worden onze 3D-printers ook gebruikt in de farmaceutische sector en in de sector van medische hulpmiddelen, waar ze deze gebruiken voor prototyping-toepassingen.
De defensie-industrie is een andere gebruiker van onze technologie. We hebben een recente case study van het Amerikaanse leger dat het gebruikt om aangepaste onderdelen te produceren die nodig zijn in het veld als ze pech hebben. Het zijn dus vervangende onderdelen voor 3D-printen.
We hebben onlangs een full-colour 3D-printer geïntroduceerd en het wordt een belangrijke doorbraak op dit gebied. Er zijn tegenwoordig full-colour 3D-printers op de markt, maar ze zijn erg duur en erg moeilijk te maken. De onderdelen die ze produceren zijn niet erg functioneel en worden voornamelijk gebruikt voor visuele toepassingen.
In tegenstelling tot deze machines kan onze printer niet alleen full-colour, maar ook functionele 3D-geprinte onderdelen maken.
Onze full colour machine wordt steeds vaker gebruikt in consumententoepassingen, architectuur, techniek, bouw en onderwijs. De laatste is momenteel een zeer grote sector voor ons in termen van focus.
Samenvattend, het is een zeer brede dwarsdoorsnede van industrieën, en omdat onze technologie universeel bruikbaar is, zien we veel van verschillende klanten en verschillende industrieën die het gebruiken.
Welke tips zou je een bedrijf geven dat aan de slag wil met additieven, maar niet weet waar te beginnen?
Bekijk additief allereerst als een technologie voor continue verbetering. Het lijkt veel op een desktopcomputer. Toen je je eerste computer kocht, begon je te kijken naar problemen om met de computer op te lossen en elke dag vond je iets om op te lossen in termen van toepassingen.
3D-printen is meer een praktijkgerichte technologie, wat betekent de beste manier om te beginnen is om een 3D-printer te hebben.
Kijk rond en je zult genoeg toepassingen vinden waar je dingen op een zeer complexe manier doet of soms niet kunt ze helemaal niet. Met een 3D-printer vind je manieren om het veel sneller te doen.
Dus a) gebruik 3D-printen als een praktijkgerichte benadering en b) zoek naar het laaghangende fruit, zoals prototyping , mallen, gereedschappen en armaturen. Terwijl je begint met het opbouwen van capaciteiten, kun je kijken naar de onderdelen voor het eindgebruik.
Ik denk ook dat een veelgemaakte fout die mensen maken bij 3D-printen, is dat ze dingen die ze doen in conventionele productie overnemen en doen in additief.
De bestaande productiepraktijken zijn goed ingeburgerd en behoorlijk geavanceerd. Ze produceren een hoge mate van consistentie en kwaliteit. Conventioneel gemaakte onderdelen nemen en ze met additieven produceren, betekent proberen additief te forceren in iets dat er niet voor bedoeld is.
Additive manufacturing is bedoeld voor op maat gemaakte, eenmalige dingen, waarbij je de complexiteit wilt verminderen . Zoals ze zeggen, komt met additieve complexiteit gratis omdat je zeer complexe onderdelen kunt produceren. Een assemblage van 100 onderdelen kan bijvoorbeeld worden teruggebracht tot misschien vijf onderdelen met AM.
Dus mijn advies is om te zoeken naar problemen die traditionele productie niet heeft kunnen oplossen en probeer ze op te lossen met AM, in plaats van te proberen te repliceren wat er in traditionele productie is met additieven. Dat zou een veel betere manier zijn om deze technologie te gebruiken.
Zie het ten slotte als een reis. Je zult waarschijnlijk sommige dingen doen die goed zullen gaan met additieven en sommige dingen die dat niet zullen doen. Maar zolang je het plant als een reis voor de komende jaren dat je het gaat gebruiken, zul je altijd manieren vinden om een continue verbeteringsaanpak te stimuleren.
Hoe ziet u additive manufacturing de komende vijf jaar evolueren?
Additive manufacturing gaat zeer opwindende tijden tegemoet omdat het geleidelijk mainstream wordt.
Het interessante van additive manufacturing is dat het een directer effect heeft in kleinere organisaties waar het aanzienlijke kostenbesparingen kan opleveren. Met AM kunt u de kosten soms tot wel 90% verlagen, en dat is uiterst belangrijk voor kleine bedrijven om concurrerend te blijven. We zien dat een hele reeks van onze klanten echt kleine en middelgrote bedrijven zijn.
Dus ik denk dat de acceptatie van additieven alleen maar zal toenemen. In sommige industrieën is het stilletjes breder geworden als je er goed naar kijkt. De tandheelkundige industrie is bijvoorbeeld volledig gesprongen om additief te worden. Er zijn dus enkele industrieën die de sprong wagen, en andere zullen ook volgen.
Er vindt veel innovatie plaats in de industrie. Je ziet om de dag een 3D-printbedrijf langskomen. Naar verluidt had de 3D-printindustrie vorig jaar het maximale aantal patenten ingediend. De enige andere industrie die in de buurt komt, is de elektrische auto-industrie. Het goede nieuws is dat er veel nieuwe technologieën zullen verschijnen.
Je zult veel consolidatie zien en je zult zien dat sommige bedrijven het niet kunnen halen omdat de technologie niet schaalbaar of gewoon vanwege de uitvoeringsuitdagingen die ze kunnen hebben.
Maar het is allemaal goed in termen van toevoeging aan het algehele ecosysteem en de mix die binnenkomt. Dus de creatieve churn zal veel meer technologie en mogelijkheden waardoor meer mensen 3D-printen kunnen gaan gebruiken.
Wat was de aanleiding voor de beslissing voor RIZE om zich in de desktop 3D-printruimte te begeven?
We zagen de behoefte aan een industriële desktop 3D-printoplossing. Er zijn tegenwoordig veel desktopmachines beschikbaar. Maar voor ons moet een desktopmachine industrieel, eenvoudig, veilig en draagbaar zijn. Dan zet je hem echt op je bureaublad.
Daarom hebben we in 2016 onze eerste 3D-printer, RIZE ONE™, geïntroduceerd. Onze machine weegt slechts 60 kg, wat betekent dat mensen hem kunnen oppakken en neem het rond. Het is iets dat op het bureau van de persoon past. Het is groot genoeg om industriële onderdelen te produceren, maar het is geen grote machine die veel ruimte in beslag neemt.
Een heel belangrijk aspect van 3D-printtechnologie zijn emissies. De meeste op extrusie gebaseerde 3D-printers stoten vluchtige organische stoffen (VOS) en ultrafijne deeltjes (UFP's) uit, die schadelijk zijn voor de gezondheid.
Tot voor kort wisten mensen hier niet veel van. Georgia Tech, een toonaangevende technische school in de VS, heeft een zeer gedetailleerd artikel gepubliceerd over hoe 3D-printers maar liefst 200 verschillende soorten VOC's uitstoten.
We hebben bewust gekeken hoe we de materialen met een nul kunnen selecteren VOC-kenmerk. Hierdoor hebben onze machines geen uitstoot, dus u hoeft zich geen zorgen te maken over ventilatie. Ze zijn volkomen veilig voor gebruik, voor contact met voedsel en huid.
Deze vereisten werden een essentieel onderdeel van ons desktopverhaal. Toen we begonnen met desktop 3D-printen, wilden we niets bewaren dat een persoon op welke manier dan ook zou kunnen schaden, hetzij door emissies of andere verontreinigingen.
Om de industriële ruimte te betreden, hebben onze 3D-printers ook moest onderdelen produceren die sterk genoeg waren om te worden gebruikt in eindgebruikstoepassingen. Dus daar ontstond de industriële kant van onze oplossing.
Hoe ziet de toekomstige productroadmap van RIZE eruit? Wilt u doorgaan met het ontwikkelen van desktop 3D-printers?
Momenteel hebben we twee 3D-printers in ons portfolio. De ene is een monochrome machine en de tweede, XRIZE™, is een full-colour machine.
We zullen blijven kijken naar het aanbrengen van nieuwe materialen op de machine. Toen we begonnen, hadden we één materiaal, RIZIUM™ ONE genaamd, en twee inkten, lossing en markering. Toen brachten we een zwart materiaal binnen genaamd RIZIUM™ Black.
Ons volgende materiaal dat dit jaar komt, heet RIZIUM™ Carbon. Het is een sterk koolstofcomposietmateriaal voor toepassingen met hoge sterkte. Het wordt zelfs gebruikt om metalen onderdelen te vervangen in industrieën zoals de lucht- en ruimtevaart en de auto-industrie.
Bovendien zijn we van plan ergens dit jaar nog een materiaal uit te brengen, RIZIUM™ ENDURA genaamd.
En natuurlijk , we brengen meerdere CMYK-kleuren binnen. We zullen dus doorgaan met het uitbreiden van de materiaalportfolio.
Ons idee is om een 3D-printer als een platform te maken, op een vergelijkbare manier als een smartphone waarmee je zoveel apps kunt toevoegen als je wilt. We willen dat mensen eenvoudig materiaal op ons huidige platform kunnen plaatsen.
RIZE heeft eerder dit jaar een Series B-financieringsronde doorstaan. Wat betekent dit voor de toekomst van het bedrijf?
Het is geweldig nieuws voor ons. We hebben een aanzienlijk bedrag opgehaald - meer dan we eigenlijk hadden gepland.
We hadden vier geweldige investeerders die zich bij ons voegden, die elk iets unieks op tafel brachten. De ronde werd geleid door Innospark Ventures, een zeer bekend durfkapitaalfonds uit Boston, gepromoot door mensen die experts zijn in kunstmatige intelligentie.
Ze investeerden in RIZE omdat ze het unieke karakter van onze technologie, die intelligente onderdelen kan maken door QR-codes in 3D in een onderdeel te printen. We hebben ook de mogelijkheid om geleidende inkten aan te brengen, wat betekent dat we elektrische circuits in een onderdeel kunnen plaatsen.
We hadden een andere investeerder genaamd Sparta Group LLC. Sparta Group wordt geleid door Desh Deshpande, die het Deshpande Center of Innovation aan het MIT leidt.
De derde investeerder was Converge, een fonds voor alleen vrouwen. Productie is van oudsher een mannenberoep, maar wij geloven dat 3D-printen een genderneutrale technologie kan zijn. Dus dat is nog eens onze boodschap over inclusiviteit.
Ten slotte werden we ondersteund door Longworth Venture Partners, onze bestaande investeerder, en Dassault Systèmes.
Elk van deze investeerders is brengen niet alleen geld, maar ook veel waarde die ons zal helpen ons bedrijf te laten groeien. De acceptatiegraad is goed, dus we zijn klaar voor een goede groei. Maar er is veel werk voor de boeg.
RIZE is onlangs ook een samenwerking aangegaan met Dassault Systèmes. Wat hoop je te bereiken met de samenwerking?
Dit is een zeer unieke en diepgaande samenwerking. Ik denk dat het de eerste in zijn soort is, zowel voor ons als voor Dassault Systèmes.
Dassault Systèmes heeft geïnvesteerd in RIZE als onderdeel van onze Series B-investering. We hebben $ 15 miljoen opgehaald en Dassault Systèmes werd een van de vier investeerders die in het bedrijf hebben geïnvesteerd.
We werken ook samen met hun SOLIDWORKS-merk en zullen samen met onze 3D-printer een SOLIDWORKS-licentie aanbieden. Door deze samenwerking willen we het idee van 3D-printen promoten als onderdeel van de ontwerpervaring. Dit is een oplossingspakket dat we in februari op SOLIDWORKS World hebben gelanceerd.
We werken ook samen met hun andere merken, zoals CATIA, evenals met de 3DEXPERIENCE®-marktplaats, die verschillende gebruikers met AM verbindt serviceproviders.
Dus we werken echt samen met Dassault Systèmes aan een breed scala aan oplossingen.
Wat biedt RIZE in 2019 de toekomst?
Alles wat ik kan zeggen is kijk naar deze ruimte.
Vorig jaar introduceerden we bij AMUG het concept van een digitaal vergroot onderdeel dat niemand in de branche eerder had gezien. Bij Formnext hebben we de full colour machine geïntroduceerd. Bij SOLIDWORKS World hebben we het gehad over hoe we de waarde kunnen verhogen door te verpakken in een volledig veilige, uniforme gebruikerservaring met Dassault.
Dus we zullen doorgaan met het introduceren van nieuwe technologieën. Momenteel maken we onze machine volledig IoT-ready. Het eerste IoT-ready platform wordt later dit jaar geïntroduceerd. Verder zullen we een hele reeks nieuwe materialen introduceren.
De 3D-printindustrie heeft een geschiedenis van te veel beloofd en dat willen we vermijden. Daarom introduceren we dingen waar we het over hebben gehad. We proberen niet te veel hype in de markt te creëren en komen er dan achter dat we het niet kunnen waarmaken.
Dus je zult veel innovatie zien met onze technologie doorsturen.
Ga voor meer informatie over RIZE naar: http://www.rize3d.com
3d printen
- Interview met een expert:professor Neil Hopkinson, directeur 3D Printing bij Xaar
- Interview met een expert:Philip Cotton, oprichter van 3Dfilemarket.com
- Interview met een expert:Spencer Wright van pencerw.com en nTopology
- Interview met een expert:Dr. Alvaro Goyanes van FabRx
- Expertinterview:Felix Ewald, CEO van DyeMansion
- Interview met expert:Duncan McCallum, CEO van Digital Alloys over Joule Printing en de toekomst van Metal 3D Printing
- Expertinterview:Nanoe CEO Guillaume de Calan over de toekomst van keramisch 3D-printen
- Expert Interview:Ultimaker President John Kawola over de toekomst van 3D-printen
- Interview met experts:een blik op de ultrasnelle, industriële SLA 3D-printers van Nexa3D
- Interview met expert:AMendate over zijn geautomatiseerde topologie-optimalisatiesoftware voor 3D-printen
- Interview met experts:Scott Dunham van SmarTech Analysis over de toekomst van 3D-metaalprinten, servicebureaus en de AM-materialenmarkt [Deel twee]