Interview met experts:Sintavia President Doug hedges op het bereiken van serieproductie met 3D-metaalprinten
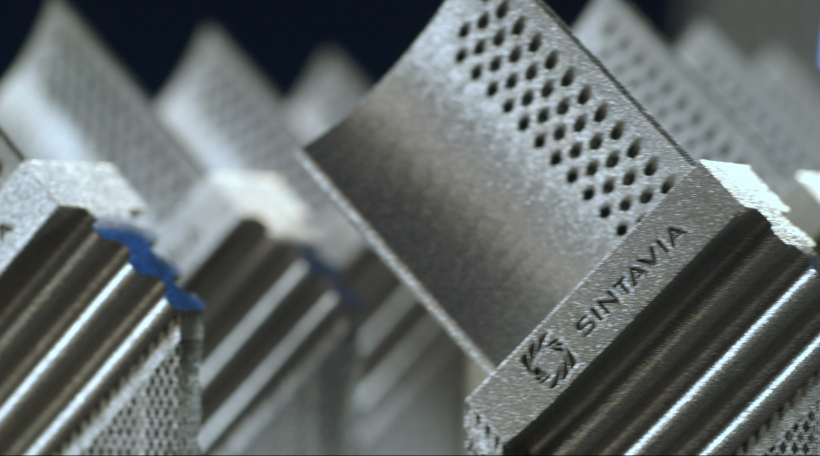
Sintavia is een onafhankelijke fabrikant die metaaladditieve productiediensten levert voor kritieke industrieën zoals lucht- en ruimtevaart en defensie en olie en gas .
Met een focus op de serieproductie van metalen onderdelen met behulp van additive manufacturing, biedt het bedrijf een unieke, end-to-end service die niet alleen productie en nabewerking omvat, maar ook testen , metallurgie en poederkarakterisering in het eigen laboratorium.
Onlangs kondigde Sintavia zijn uitbreidingsplannen aan, met de verhuizing naar een gloednieuwe faciliteit van 55.000 vierkante meter met een duidelijke nadruk op productie.
Deze week zijn we verheugd in gesprek te zijn met de president van Sintavia, Doug Hedges, om te bespreken hoe het bedrijf hoogwaardige, gecertificeerde metalen onderdelen produceert, waarom AM perfect is voor de lucht- en ruimtevaartindustrie en wat de AM-industrie kan doen om de acceptatie van de technologie te versnellen.
Kun je ons iets over Sintavia vertellen?
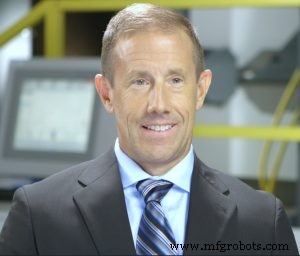
Sintavia werd in 2012 opgericht door Brian Neff, de CEO en voorzitter van het bedrijf. Het bedrijf werd opgericht als een interne additieve productie-inspanning met een bedrijf genaamd CTS Engines, een onafhankelijke MRO voor straalmotoren, gevestigd in Fort Lauderdale, Florida.
Sintavia werd in 2015 een apart bedrijf en we verhuisden naar Davie, Florida, waar we nu nog steeds zijn.
Als bedrijf hebben we een uitgebreide achtergrond in de luchtvaart. We zagen dat er een mogelijkheid was om deze achtergrond te gebruiken om een bedrijf te creëren dat verticaal geïntegreerd is met veel verschillende aanbiedingen. Om goed te zijn in additieven, moet je ook goed zijn in metrologie, metallurgie, machinale bewerking, warmtebehandelingen, testen enzovoort.
Dus terwijl onze kerncompetentie additieve productie is, gebruiken we onze ervaring in de MRO- en OEM-productievelden om een nieuw, op zichzelf staand bedrijf te creëren dat zich richt op lucht- en ruimtevaart en defensie, maar ook op olie en gas.
Het unieke aan Sintavia is dat verticale integratie ten grondslag ligt aan alles wat we doen:van nabewerking, kwaliteit, metallurgie, scanning et cetera. Al deze elementen bevinden zich onder één dak in onze productiefaciliteit hier in Davie, Florida.
Lucht- en ruimtevaart is een centraal aandachtspunt voor Sintavia. Kunt u ons enkele voordelen van additive manufacturing voor de lucht- en ruimtevaartindustrie uitleggen?
Additive manufacturing werkt om verschillende redenen goed voor de lucht- en ruimtevaart.
Ten eerste is het belangrijk op te merken dat de technologie begon als een prototype-ontwikkelingstool voor OEM's in de lucht- en ruimtevaart- en defensie-industrie om snel ontwerpen en testen te herhalen de motoren. Het is nu geëvolueerd tot een punt waarop bedrijven motoren bouwen met additieve onderdelen.
Dus dat is nog steeds een grote drijfveer. Maar dan zijn er nog alle andere typische voordelen die AM tot een geweldige technologie maken. Hier verwijs ik naar de consolidatie van lasverbindingen, complexe gietstukken, lichtgewicht, ontwerp zonder gereedschap. Natuurlijk is complexiteit niet gratis, maar het wordt enorm uitgebreid door het gebruik van additieven.
Bijvoorbeeld, een primaire focus voor ons in termen van onderdeelselectie zijn externe kleplichamen aan de buitenkant van straalmotoren en kanalen. Ook binnen de luchtvaartindustrie zien we een opkomende markt voor chassis en warmtewisselaars.
Een van de metalen 3D-printtechnologieën die u gebruikt, is Powder Bed Fusion. Wat zijn de voordelen van deze technologie voor ruimtevaarttoepassingen?
Nou, metaal 3D-printen in het algemeen leent zich echt voor unieke ontwerpen.
Het vroege stadium van wat we doen, is het gebruik van poederbedfusie met lasers en elektronenstralen om hogedrukkanalen en componenten laag voor laag te bouwen. Er is duidelijk het voordeel van het gebruik van de technologie als vervangingsgereedschap voor las- en gietstukken die al in de industrie worden gebruikt.
Maar de kracht van additieven gaat veel verder:je kunt onderdelen maken die beter, lichter en sterker zijn, wat in wezen betere prestaties mogelijk maakt. Om de kracht van AM echt te benutten, moeten de componenten worden ontworpen voor additive manufacturing.
Je kunt additieve fabricage gebruiken - ik heb het hier vooral over lasers - voor componenten zoals warmtewisselaars en chassis om geometrieën te maken die voorheen onmogelijk te vervaardigen waren.
Je hebt ook bijvoorbeeld flow bodies of afsluiters die je met AM sneller kunt maken en consolideren. Dit stelt onze klanten in staat om niet alleen hun bestaande supply chains te optimaliseren, maar ook om betere producten te maken en in te spelen op de sterke punten van de OEM-luchtvaart- en defensiemarkt.
Neem als voorbeeld warmtewisselaars:additive manufacturing stelt u in staat om zeer fijne wanden en kleine, ingewikkelde geometrieën in het onderdeel te maken. U kunt dus een wand hebben van 200 micron of minder. Bovendien heeft u met additive manufacturing nu een betere manier om de warmte uit het onderdeel te geleiden. Dit is geweldig omdat het doel van het eindspel met warmtewisselaars is om de warmte uit het onderdeel te halen, zodat je er meer elektronica in kunt stoppen.
We gebruiken additieve fabricage van metaal om hun producten te verbeteren. Alles van kleplichamen, externe straalmotorcomponenten, kanalen en warmtewisselaars tot chassis en verschillende soorten buisconstructies die zijn gemaakt door lasverbindingen met veel complexe mallen en bevestigingen om ze aan elkaar te lassen.
Dat gezegd hebbende , doen we ook veel meer dan dat. We werken bijvoorbeeld aan wat zich in de uitrusting van turbomachines bevindt, van een kleinere waaier die zich in een compressor zou kunnen bevinden, tot een grotere waaier die zich in een raket zou kunnen bevinden.
We hebben een focus op de commerciële lucht- en ruimtevaart - in wezen straalmotoren - en een andere focus op voortstuwing, wat raketonderdelen zou zijn.
We hebben dan het "tussenin" binnen de lucht- en ruimtevaart- en defensie-industrie, waarmee ik doel op de obscure componenten die ooit van 10 tot 100 stuks werden gemaakt, maar die we nu kunnen maken in één enkel stuk met behulp van additive manufacturing.
Kun je wat meer vertellen over enkele van de ontwerpuitdagingen die bij die toepassingen horen?
AM is een relatief nieuw proces in de productie. We gebruiken lasers of elektronenstralen om het poeder laagsgewijs te smelten. Wat we in wezen doen, is het maken van kleine tot middelgrote lasnaden, of "microlassen".
Bij dit microlasproces vindt er een snelle afkoeling plaats waarbij de laser het metaalpoeder blootlegt. Je hebt twee uitersten:een zeer heet drukproces, met daarnaast een snelle afkoeling.
Vanwege deze extreme temperatuurverschillen is uw onderdeel onderhevig aan vervorming. Deze onderdelen zijn dus niet zoals traditionele lasnaden gemaakt met gegoten onderdelen; het zijn op zich unieke items.
Een van de belangrijkste uitdagingen is om te kunnen voorspellen hoe deze onderdelen zullen bewegen binnen het additieve fabricageproces. Een belangrijk onderdeel van deze uitdaging is het gebruik van deze zeer moderne technologie en hightech tools om de voorspelling aan het begin te doen, om te helpen bij de volledige coördinatie van het proces.
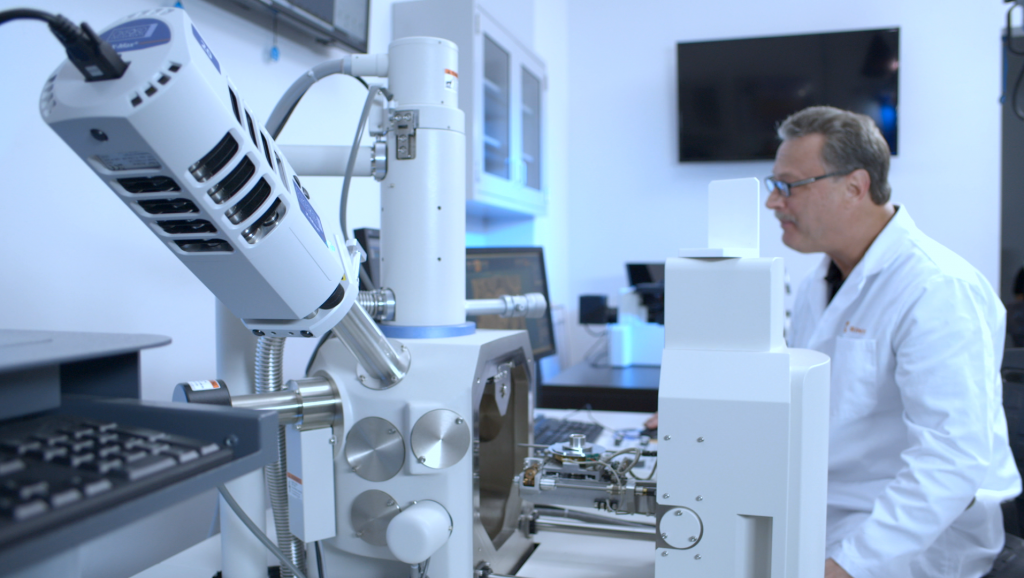
Bij Sintavia gebruiken we eindige-elementenanalyse (FEA) aan het begin van de ontwerpcyclus. De ingenieurs van Sintavia krijgen de eerste gegevens van onze klanten in de vorm van CAD-modellen, tekeningen en specificaties. Onze ingenieurs werken samen met onze klanten om belangrijke parameters uit te werken, zoals hoe een onderdeel op de bouwplaat moet worden geplaatst, onder welke hoek een onderdeel zal worden gemaakt en hoe steunen zullen worden gebruikt, ofwel om het onderdeel vast te houden of om de warmte uit de bouwplaat te halen. onderdeel.
We gebruiken wiskunde om te voorspellen hoe het onderdeel gaat vervormen en minimaliseren die vervorming om een zeer natuurgetrouw onderdeel te maken. We moeten weten hoe dat onderdeel op ons gaat bewegen en schuiven, zodat we voorraad kunnen toevoegen aan flenzen, boringen, gaten, enz. om ervoor te zorgen dat er voldoende voorraad is om op te ruimen aan het einde van het proces. Met deze aanpak kunnen we de nabewerking van dat deel ook op een later moment verantwoorden.
Eén ding om in gedachten te houden is dat additive manufacturing een enorm krachtig proces is om complexe onderdelen te maken, maar het moet worden gebruikt in coördinatie met traditionele processen. De coördinatie van het additieve proces met het subtractieve proces is van cruciaal belang.
We horen veel over de uitdagingen die komen kijken bij de nabewerking van metalen onderdelen, en dat is een van de diensten die Sintavia biedt. Kun je ons door enkele van de grootste uitdagingen met nabewerking en jouw aanpak leiden?
Nabewerking moet een gecoördineerde inspanning zijn tussen het drukproces zelf en de nabewerking die bij dat onderdeel na de productie hoort.
Een veelvoorkomende uitdaging die de meeste mensen niet zien, is het verwijderen van poeder na het proces. Na het printproces moet al het poeder van het onderdeel worden verwijderd. Omdat sommige van deze onderdelen zeer complexe geometrieën hebben, maken we machines op maat – ofwel ultrasoon ofwel traditionele vibratiesystemen – om het poeder te verwijderen.
Het is gebruikelijk om het poeder van het onderdeel te verwijderen voor de volgende stap, wat bijna altijd stressverlichting is. We verlichten de stress intern met een vacuümoven of een bakoven om de restspanning van het additieve bouwproces te verwijderen.
Van daaruit ga je naar een draadvonkmachine of een lintzaag om het onderdeel van de plaat te verwijderen. Dan moet u natuurlijk de steunen verwijderen. Deze steunen kunnen van alles zijn, van eenvoudige roostersteunen tot iets zeer solide dat wordt gebruikt om het onderdeel vast te houden en om zeer grote onderdelen van superlegeringen van nikkel te produceren. Deze zijn onderhevig aan veel thermische belasting.
Hierdoor heeft u mogelijk een zeer robuust machinaal proces nodig om de steunen van deze onderdelen te verwijderen. Daar kan behoorlijk wat werk aan zitten. En als ik zeg 'machineproces', kan dit veel verschillende dingen betekenen. Het zou zoiets eenvoudigs kunnen zijn als ze gewoon met een tang af te breken tot een zeer stijve vijfassige werktuigmachine om die steunen van het onderdeel te verwijderen.
Vanaf dit punt heb je verschillende keuzes. U kunt bijvoorbeeld terecht bij HIP, die wij ter plaatse aanbieden, of wij maken gebruik van verspaning. In dit geval, als ik machinale bewerking zeg, bedoel ik machinale bewerking om af te drukken. Dit is dus echt niet anders dan wat je zou zien in een machinewerkplaats.
Voor het grootste deel hebben we een 2D-tekening met veel bedieningselementen en we machinaal dat onderdeel om het in overeenstemming te brengen met de specificaties.
Overgaand op de metaalpoeders zelf, wat is het proces van het ontwikkelen van metaalpoeders in Sintavia?
Voor alle duidelijkheid, we ontwikkelen niet echt poeders op zich. Maar we zijn betrokken geweest bij het helpen van bedrijven bij het ontwikkelen van legeringen die in het verleden niet in de handel verkrijgbaar waren.
We hebben bedrijven waarmee we samenwerken die bijvoorbeeld een variant van gereedschapsstaal of een variant van RVS hebben. Dit zijn typisch speciale legeringen die ze hebben ontwikkeld om in de toekomst te worden gebruikt voor een soort prestatievoordeel.
Wat we wel hebben, zijn vlucht-goedgekeurde poederoplossingen voor de lucht- en ruimtevaartindustrie. We kopen het poeder, brengen dat naar ons lab en voeren dat door een groot aantal tests voordat de bouw begint.
Een van onze sterke punten bij Sintavia is dat we ons poeder ter plaatse in ons laboratorium volledig kunnen karakteriseren. Hierdoor kunnen we monsters nemen en begrijpen wat er met het poeder gebeurt. Meestal besteden andere bedrijven dit proces uit. Dus hoewel we materialen kunnen inkopen bij onze poederleverancier, doen we de stromingstesten, morfologie, deeltjesgrootteverdeling, gasanalyse, ICP voor chemie enzovoort.
We voeren ongeveer acht of negen tests uit om ervoor te zorgen dat de poeders voldoen aan de productievereisten van onze klanten. Terwijl het poeder wordt gebruikt, nemen we monsters en archiveren we deze poedermonsters om te begrijpen wat er met het poeder gebeurt naarmate de opbouw vordert. Dit betekent dat we precies kunnen begrijpen wat er met het poeder gebeurt als het geleidelijk wordt gebruikt.
Sintavia heeft aangekondigd dat het van plan is om deze maand een gloednieuwe faciliteit te openen met een toename van het aantal machines. Kunt u de visie achter deze nieuwe faciliteit delen?
We zijn erg verheugd om deze maand onze nieuwe faciliteit te openen.
De nieuwe faciliteit zal 55.000 vierkante meter groot zijn en we gaan die faciliteit baseren op ons eerdere succes.
Een belangrijk punt is dat het grotendeels gebaseerd zal zijn op productie. We gaan meer dan $30 miljoen aan nieuwe machines huisvesten, grotere moderne AM-apparatuur, poederverwerkingssystemen, back-upgeneratoren, voedingen, inert gas. We voorzien dat we zullen oplopen tot meer dan 135 nieuwe banen voor Sintavia en Zuid-Florida.
De nieuwe faciliteit is echt de visie om wat we hebben gedaan op een kleinere schaal te doen, met 12 machines hier in onze huidige faciliteit, en dat op te schalen naar een faciliteit van 55.000 vierkante meter met maximaal 65 machines.
Er wordt veel geïnvesteerd in additive manufacturing, in warmtebehandelingen. nabewerking, afwerking, reiniging, et cetera.
In wezen willen we het additiefproces binnen één faciliteit beheersen. Dat is echt het bedrijfsmodel:we willen opschalen wat we hebben gedaan en dit in een productieproces brengen dat kwaliteit en herhaalbaarheid garandeert voor onze OEM-klanten.
Zou u in de toekomst willen uitbreiden naar andere industrieën, zoals de automobielsector of de medische sector, waar ook een grote vraag is naar 3D-geprinte metalen onderdelen?
Ja, absoluut. We hebben wel het een en ander aan de hand in zowel de auto- als de medische sector. En er zijn andere industrieën waarvoor additieven ook zinvol zijn.
We zijn bijvoorbeeld betrokken bij industriële gasturbines. Hoewel onze achtergrond aero-gasturbines is, zijn gasturbines op de grond voor energie in wezen opgeschaald en enigszins verschillende aero-turbinemotoren.
De technologie is ook zeer goed toepasbaar in de biomedische sector.
Sintavia is AS9100-geaccrediteerd — AS9100 is een kwaliteitsmanagementsysteem voor de lucht- en ruimtevaartindustrie. Ons laboratorium is ISO 17025 geaccrediteerd voor mechanische metingen, wat alles kan betekenen van poederkarakterisering en chemie tot trekproeven en vermoeiingstests.
De biomedische industrie heeft een ander accreditatiebureau; het meeste daarvan is te danken aan ISO 13485. Als je eenmaal AS9100 hebt, kun je overstappen op ISO 13485. Het is niet zo'n grote sprong om tussen deze verschillende industrieën te gaan. Immers:kwaliteit is kwaliteit en processen zijn processen. Als je aan ruimtevaart kunt doen, kun je die overstap naar andere markten maken.
Boven alles wat ik heb genoemd, is kwaliteitscontrole het belangrijkste aspect.
Vanaf dag één hebben we ons gericht op het ontwikkelen van ons kwaliteitssysteem met AS9100, ISO- en Nadcap-certificeringen. Dit is allemaal zeer gunstig voor onze OEM-klanten en kan zeker ook een hulpmiddel zijn voor andere industrieën.
Wat zijn volgens u enkele dingen die nodig zijn om de acceptatie van 3D-metaalprinten te versnellen?
Ondanks al onze technologie en de bekwaamheid die we hebben op het gebied van analyse, moeten we ons echt concentreren op wat zaken drijft. Ondernemen wordt gedreven door geld en snelheid. Dit betekent dat de technologie sneller, goedkoper en meer ingeburgerd moet worden.
Dat gezegd hebbende, we zien hoe de dingen veranderen. Tijdens onze tijd hier bij Sintavia hebben we gezien hoe metal AM is geëvolueerd. Op een bepaald moment was aluminium bijvoorbeeld een relatief lastig materiaal om te printen in additive manufacturing, maar nu is het bijna alledaags. Naarmate we extra lasers zien, omdat we de expertise en het ontwerpen van onderdelen voor additieven zien, zal dit onze klanten een hogere snelheid en kostenbesparingen bieden.
Dit alles kwam historisch gezien voort uit de prototyping-industrie, en dat willen we verplaatsen naar serieproductie. Er zijn bepaalde dingen die we moeten doen om het sneller en goedkoper te maken, kwaliteit te bieden en de voordelen te bieden waarvan iedereen weet dat metaaladditieven kunnen bieden.
Hoe ziet u de productie van additieve metaalproductie de komende vijf jaar evolueren en hoe past Sintavia in die visie?
Wat we echt moeten doen, is om onderdelen op een productiemanier te gaan maken. Voor kritieke industrieën moeten we ervoor zorgen dat we echte metalen onderdelen produceren die volledig functioneel zijn.
We weten dat deze onderdelen buitengewoon goed concurreren met gietstukken voor mechanische eigenschappen. Met de juiste processen en controles kunnen ze ook concurreren met onbewerkte producten, en in sommige gevallen zelfs vervalste producten.
Kwaliteitscontrole, d.w.z. het begrijpen van de kwaliteitseisen en het kunnen valideren van uw onderdeel, zal in de toekomst echt een verschil maken.
Maar we mogen ook niet uit het oog verliezen dat de technologie nog relatief nieuw is. Als branche doen we veel dingen voor de allereerste keer.
Dit betekent dat de voorkant van het proces in de eerste plaats moet worden geleerd.
Bij het begin van het proces moeten technici bijvoorbeeld ondersteuningsstrategieën begrijpen en besteed tijd aan het leren hoe de geometrie van onderdelen en de ondersteuningsgeometrie het beste kan worden geoptimaliseerd, wat op zijn beurt zal helpen om betere onderdelen te produceren en ervoor te zorgen dat de ondersteuningen relatief gemakkelijk loskomen.
Dankzij dit werk dat bij de om te beginnen, hebt u de kostbare en tijdrovende stap voor het verwijderen van ondersteuning genomen en deze aanzienlijk goedkoper gemaakt. De technische inspanning om de onderdelen te maken, is echt cruciaal om het tot een volwassen punt te brengen om de een na de ander producten te maken.
Hoe ziet de toekomst eruit voor Sintavia?
Het ziet er erg spannend uit! Natuurlijk ziet het er ook behoorlijk uitdagend uit als we naar onze nieuwe faciliteit verhuizen. We gaan lean manufacturing implementeren. We hebben de eerste grootschalige, slanke productiefaciliteit voor additieven die speciaal is ontwikkeld voor onze afstemming op OEM's en de toeleveringsketen.
In 2019 zullen we veel van het werk dat we de afgelopen jaren hebben gedaan voortzetten, met betrekking tot het kwalificeren en ontwikkelen van onderdelen voor onze klanten.
Ik zal geen namen noemen, maar als je kijkt naar de belangrijkste lucht- en ruimtevaartbedrijven wereldwijd, is de kans groot dat we zaken voor hen doen.
In sommige gevallen gevallen, zoals onze relatie met Honeywell, waar we de eerste AM-leverancier zijn die is goedgekeurd om vluchtklare onderdelen voor Honeywell Aerospace te maken. We hebben een overeenkomst gesloten met Honeywell om onze huidige faciliteit en onze volgende faciliteit te gebruiken om dat naar buiten te brengen en productie-onderdelen voor Honeywell te maken.
Honeywell is een relatief snelle gebruiker van de technologie en ze hebben heel veel toepassingen. Maar als je buiten Honeywell gaat, is de kans groot dat we nu werk voor hen doen, of het nu een vliegtuigbouwer of een motorcentrale is, of het nu een lucht- en ruimtevaart- en defensieleverancier is.
We zien 2019 en 2020 als relatief grote jaren voor ons, wat betreft de adoptie van metaaladditieven. Het is echt opwindend dat Honeywell hier vandaag is, maar we zullen zien dat we de komende jaren meer klanten zullen hebben die serieproductie gaan doen.
We stemmen ons bedrijf af om die bron te bieden aan de OEM's van de wereld, zodat ze een one-stop-shop, verticaal geïntegreerde partner kunnen hebben voor het produceren van deze onderdelen met additieve fabricage.
Enige laatste gedachten?
Ik wil graag herhalen dat kwaliteit onze focus is.
Onze klanten zijn zonder twijfel de meest risicomijdende klanten ter wereld. Om ervoor te zorgen dat ze zich op hun gemak voelen bij het vliegen met deze kritische componenten die zijn gemaakt door additieve fabricage, staat kwaliteit voorop.
Uiteindelijk willen we producten aanpassen aan technische tekeningen en specificaties, om ze in echte toepassingen te gebruiken. Om dat te doen, is een focus op conformiteit nodig.
Ook vandaag is AM de plek waar alle media-aandacht is en waar veel tijd en geld aan wordt besteed. Maar uiteindelijk moet het gaan om het onderdeel dat u heeft gemaakt door middel van additive manufacturing en dat te laten voldoen aan de technische vereisten van uw klanten.
Dus ja, we praten graag over additive manufacturing. Maar ik zie het ook graag als geavanceerd fabricage. Ik wil afstappen van de modewoorden van additieve fabricage om te zeggen dat we een geavanceerde fabrikant zijn van precisieonderdelen voor de ruimtevaart. We willen geavanceerde onderdelen maken om ervoor te zorgen dat onze klanten hun huidige ontwerpen aanzienlijk kunnen verbeteren.
Ga voor meer informatie over Sintavia naar: https://sintavia.com/
Over Doug Hedges
Doug Hedges heeft meer dan 20 jaar ervaring in de lucht- en ruimtevaartindustrie, van het ontwerpen van experimentele OEM-componenten tot door de FAA goedgekeurde reparaties, aanpassingen en ontwikkeling van componenten op basis van industriestandaardspecificaties en controles.
Voorafgaand aan Sintavia was hij werkzaam als Senior Engineer bij CTS Engines, waar hij reparaties en processen ontwikkelde voor de revisie van General Electric straalmotoren, Lead Project Engineer voor HEICO Aerospace, Senior PMA Engineer voor Kapco Global en Design Engineer voor Rolls-Royce. Doug heeft een BSME-diploma in werktuigbouwkunde van de Universiteit van Minnesota.
Expertinterviews
AMFG's Expert Interviews-serie toont innovatieve bedrijven en individuen die helpen de toekomst van additive manufacturing vorm te geven. Neem voor meer informatie over deelname aan de serie contact op met [email protected].
3d printen
- Hoe kunt u opschalen naar seriële additieve productie met Additive MES?
- Interview met een expert:professor Neil Hopkinson, directeur 3D Printing bij Xaar
- Interview met een expert:Philip Cotton, oprichter van 3Dfilemarket.com
- Interview met een expert:Dr. Alvaro Goyanes van FabRx
- Expert Interview:Ultimaker President John Kawola over de toekomst van 3D-printen
- Interview met experts:Sintavia President Doug hedges op het bereiken van serieproductie met 3D-metaalprinten
- Interview met experts:Brian Alexander van Solvay over de ontwikkeling van hoogwaardige polymeren voor 3D-printen
- Expertinterview:medeoprichter van Carbon, Philip DeSimone, over de overgang naar productie met hoog volume met 3D-printen
- 4 uitdagingen op het gebied van additieve productie die met software kunnen worden opgelost
- Expert Interview:Jabil's Rush LaSelle over de toekomst van additieve productie
- Interview met expert:hoofdtechnoloog van ANSYS over het bereiken van succesvol 3D-printen met metaal met simulatie