Een inleiding tot additieve metaalproductie met DMLS
Naarmate de productontwikkeling sneller gaat, veranderen de ontwerpregels. Nergens is dit duidelijker dan bij additieve productie van metalen. Direct lasersinteren met metaal is een additieve fabricagetechnologie voor metaal met een aanzienlijk potentieel in de medische en ruimtevaartindustrie. Maar het vereist een nieuwe manier van denken, zelfs in de vroege ontwerpfasen. In veel opzichten vertegenwoordigt het de transitie die ontwerpers moeten doormaken wanneer ze naar nieuwe technologieën kijken om productontwerp en fabricage sneller en innovatiever te maken.
Er zijn verschillende voordelen van DMLS, in de eerste plaats dat ontwerpers ontwerpen in ongebruikelijke vormen kunnen vervaardigen, zowel tijd- als kostenbesparend. Net als andere 3D-printtechnologieën bouwt DMLS onderdelen laag voor laag door verstoven metaalpoeder te sinteren met een krachtige laser.
Waarom Additive Manufacturing gebruiken voor metalen onderdelen?
Productontwerpers en -ingenieurs wenden zich vaak tot het proces om te experimenteren met organische vormen die niet gemakkelijk kunnen worden bewerkt. Bijvoorbeeld de mogelijkheid om implanteerbare lichaamsdelen te bouwen die op maat worden gemaakt voor de ontvanger. Traditioneel zouden deze implantaten normaal gesproken moeten worden geproduceerd via een subtractief fabricageproces, zoals een 5-assige CNC-machine. Nu bestaat de technologie om de daadwerkelijke botstructuur van een persoon te scannen en een directe DMLS-vervanging af te drukken die is aangepast aan hun lichaam.
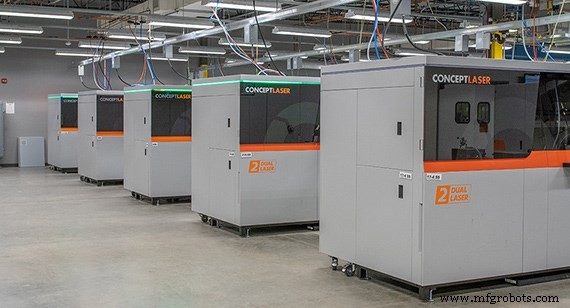
Een andere mogelijkheid zijn chirurgische instrumenten met ultrafijne kenmerken en medische componenten met organische vormen. Deze apparaten kunnen zijn ontworpen voor spuitgieten of gieten van metaal, die beide relatief hoge gereedschapskosten en levertijden hebben die weken kunnen duren. Maar met DMLS kunt u een prototype van een chirurgisch handgereedschap printen met het exacte gewicht en de sterkte van het eindproduct en het binnen enkele dagen in de handen van een chirurg hebben. Traditioneel spuitgieten van metaal is nog steeds waardevol en heeft een lagere stukprijs bij grotere hoeveelheden, maar het duurt nog steeds 6 tot 12 weken in plaats van een paar dagen.
Lucht- en ruimtevaart is een andere industrie die snel 3D-printen met metaal heeft overgenomen. Materialen die vaak in de lucht- en ruimtevaart worden aangetroffen, zoals Inconel en titanium, zijn direct beschikbaar via het DMLS-proces. De mogelijkheid om complexe metalen onderdelen met uitgeholde kenmerken te vervaardigen, opent een scala aan mogelijkheden voor ontwerpers die proberen componenten lichter te maken. Een ander voordeel van het 3D-printen van metalen onderdelen is de integratie van interne koelkanalen binnen een onderdeel.
Tijd, kostenbesparing en ontwerpvrijheid zijn essentieel om te kunnen experimenteren, snel te ontwerpen en te zien wat werkt. Maar DMLS vereist wel een verschuiving in ontwerpdenken. Een van de grootste aanpassingen is de aanpassing aan de introductie van interne spanningen tijdens het bouwproces. Beginnend met een metaalpoeder op kamertemperatuur, het toepassen van warmte voor een onmiddellijke smelting, gevolgd door snelle afkoeling veroorzaakt stress bij elke laag tijdens het bouwproces. De interne spanningen die ontstaan tijdens het bouwen van een DMLS zorgen ervoor dat een onderdeel tijdens het bouwen naar boven probeert te krullen.
Hoe 3D-geprinte metalen onderdelen te ontwerpen
Nu we de algemene toepassingen en voordelen van 3D-printtechnologie voor metaal hebben besproken, gaan we eens kijken naar enkele basisrichtlijnen voor het ontwerpen van kenmerken op 3D-geprinte metalen onderdelen.
Zelfondersteunende hoeken
Een zelfdragende hoek beschrijft de hoek van het element ten opzichte van de bouwplaat. Hoe lager de hoek, hoe kleiner de kans dat het zichzelf ondersteunt. Elk materiaal zal iets anders presteren, maar de algemene vuistregel is om te voorkomen dat een zelfdragende functie wordt ontworpen die minder is dan 45 graden. Deze tip zal u goed van pas komen in alle beschikbare materialen. Zoals u in de bovenstaande afbeelding kunt zien, wordt de oppervlakteafwerking van het onderdeel ruwer naarmate de hoek kleiner wordt en uiteindelijk zal het onderdeel falen als de hoek te ver wordt verkleind.
Uitsteeksels
Uitsteeksels verschillen van zelfdragende hoeken doordat het abrupte veranderingen in de geometrie van een onderdeel zijn - geen vloeiende helling. DMLS is vrij beperkt in zijn ondersteuning van overhangen in vergelijking met andere 3D-printtechnologieën zoals stereolithografie en selectieve lasersintering. Elke overhang van meer dan 0,020 inch (0,5 mm) moet extra ondersteuning krijgen om schade aan het onderdeel te voorkomen. Bij het ontwerpen van overhangen is het verstandig om de limieten niet te verleggen, aangezien grote overhangen kunnen leiden tot vermindering van de details van een onderdeel en, erger nog, ertoe kunnen leiden dat het hele gebouw crasht.
Kanalen en gaten
Interne kanalen en gaten zijn een van de belangrijkste voordelen van DMLS, omdat ze onmogelijk zijn met andere productiemethoden. Conforme kanalen zorgen voor gelijkmatige koeling door een onderdeel en helpen bij het verminderen van het gewicht van een onderdeel. Het wordt aanbevolen dat kanalen een diameter van 0,30 inch (8 mm) niet overschrijden. Net als bij niet-ondersteunde structuren, zullen de naar beneden gerichte structuren vervormd raken naarmate u meer dan 0,30 inch overschrijdt. Een tip om deze beperking te omzeilen is om geen cirkelvormige kanalen te ontwerpen. Ontwerp in plaats daarvan kanalen met een druppel- of ruitvorm. Kanalen die deze vormen volgen, zorgen voor een meer uniforme oppervlakteafwerking binnen de goot en stellen u in staat de diameter van de goot te maximaliseren.
Het wordt aanbevolen dat kanalen een diameter van 0,30 inch (8 mm) niet overschrijden. Net als bij niet-ondersteunde structuren, zullen de naar beneden gerichte structuren vervormd raken naarmate u meer dan 0,30 inch overschrijdt. Een tip om deze beperking te omzeilen is om geen cirkelvormige kanalen te ontwerpen. Ontwerp in plaats daarvan kanalen met een druppel- of ruitvorm. Kanalen die deze vormen volgen, zorgen voor een meer uniforme oppervlakteafwerking binnen de goot en stellen u in staat de diameter van de goot te maximaliseren.
Bruggen
Een brug is elk vlak naar beneden gericht oppervlak dat wordt ondersteund door 2 of meer elementen. De minimaal toegestane niet-ondersteunde afstand die we aanbevelen is 0,080 inch. In vergelijking met andere 3D-printtechnologieën is deze afstand relatief kort vanwege de spanningen van de snelle verwarming en afkoeling. In de onderstaande afbeelding ziet u hoe de brug de ondersteunende structuren naar binnen trekt naarmate de vrijdragende afstand groter wordt. Onderdelen die deze aanbevolen limiet overschrijden, hebben een slechte kwaliteit op de naar beneden gerichte oppervlakken en zijn structureel niet in orde.
Nabewerking van metalen 3D-geprinte onderdelen
Zodra een onderdeel klaar is met bouwen in de machine, kunnen verschillende stappen worden genomen om de mechanische eigenschappen en de kwaliteit van de oppervlakteafwerking te verbeteren en ervoor te zorgen dat de kenmerken van het onderdeel binnen de toleranties vallen.
Warmtebehandeling
Het is noodzakelijk om onderdelen een warmtebehandeling te laten ondergaan nadat een onderdeel is gebouwd, omdat dit de interne spanningen helpt verminderen die tijdens het sinterproces ontstaan. De spanningen in een constructie stralen naar buiten uit naar de rand van het onderdeel en bouwen op met elke extra laag. Onderdelen met dikke doorsneden zullen bijvoorbeeld meer spanning hebben. Er zijn verschillende warmtebehandelingsprocessen die kunnen worden gebruikt om dit aan te pakken:
- Vacuümoven: Onderdelen worden in een vacuümverzegelde oven geplaatst en vervolgens blootgesteld aan een omgeving met hoge temperaturen, waardoor interne spanningen worden verminderd.
- Heet isostatisch persen (HIP): Dit proces, gewoonlijk HIP genoemd, oefent zowel druk als warmte uit op het onderdeel om de porositeit te verminderen en de dichtheid te vergroten.
Post-build CNC-bewerking
Sommige toepassingen vereisen mogelijk extra bewerking nadat het metalen onderdeel 3D-geprint is. Dit is handig wanneer nauwe toleranties of een verbeterde kwaliteit van de oppervlakteafwerking vereist zijn voor specifieke kenmerken, maar de algehele geometrie vereist dat additive manufacturing wordt geproduceerd. Een onderdeel van een raketmotor met complexe koelkanalen heeft bijvoorbeeld een koppelingskenmerk waarvoor een tolerantie van +/- 0,001" vereist is. efficiënter gebruik van materialen.
Kwaliteitsinspecties
Vaak vereisen metalen onderdelen die met additieve productie zijn gebouwd dimensionale validatie of een evaluatie van de microstructuur van het materiaal. Hiervoor kunnen coördinatenmeetmachines (CMM's) worden gebruikt om te controleren of onderdeelkenmerken binnen de tolerantie vallen. CT- of röntgenscanning kan ook worden gebruikt om interne kenmerken te onderzoeken en een niet-destructieve oplossing te bieden om de structurele integriteit te waarborgen.
Meer informatie over 3D-printen met metaal
Als u meer wilt weten over DMLS en 3D-metaalprinten in het algemeen, hebben we verschillende andere bronnen beschikbaar. Lees eerst onze whitepaper over het vervaardigen van metalen onderdelen. Dit omvat zowel machinale bewerking als 3D-printen en helpt u te beslissen welk proces het beste is voor uw toepassing. En voor meer details over het ontwerpen van metalen onderdelen voor additive manufacturing, bekijk ons on-demand webinar "Designing for Metal 3D Printing."
Industriële technologie
- Productie van vloeibare additieven:3D-objecten bouwen met vloeistof
- Additieve productie versus subtractieve productie
- Voordelen van additieve fabricage
- Verbeteren van additieve productie met reverse engineering
- Wat kunt u doen met 3D-metaalprinten?
- Productie van metaaladditieven:wat u moet weten
- Vijf verrassende feiten over de productie van metaaladditieven
- Wat is additieve fabricage? Aan de slag met 3D-printen
- Hybride productie gebruiken met metaaladditieven en subtractieve technologieën
- Additive Manufacturing met industrieel 3D-printen:strategieën voor succes na verwerking
- Additieve productie in de lucht- en ruimtevaart