Kunststoffen en composieten combineren voor klasse A-onderdelen zonder gereedschap
Het produceren van composietonderdelen met een klasse A-afwerking is niet de heilige graal - er zijn genoeg bedrijven die dit routinematig doen. Als u dit echter doet met harsinfusie zonder dure tooling of gelcoats en met een snelheid van één deel per uur? Nou, dat is iets unieks.
Van kunststof tot composiet
Plastics Unlimited werd 25 jaar geleden opgericht door Terry en Nancy Kieffer, vertelt hun zoon Dakota Kieffer, sales- en marketingdirecteur van het bedrijf. "Ze waren boeren in Iowa en waren op zoek gegaan naar een nieuwe en groeiende industrie", legt hij uit, "Ze dachten dat plastic beter zou zijn dan lassen of houtbewerking en ze wilden niet concurreren met hun buren. Ze keken naar spuitgieten, rotatiegieten en recycling van kunststoffen, maar kwamen toen thermovormen tegen en begrepen het echt.” (Thermovormen maakt gebruik van warmte en vacuüm/druk om thermoplastische platen tot gevormde onderdelen te vormen.)
Toen kwamen de ouders van Kieffer in contact met een bedrijf dat onderdelen van glasvezelversterkte kunststof (FRP) maakte. "Ze zagen hoe sterk FRP was, maar ook dat het een lang proces van meerdere stappen vereiste, ongeveer vier uur per onderdeel - er werden dus slechts twee onderdelen per dag geproduceerd", vervolgt hij. “Vergeleken met onze productie in kunststoffen vonden ze dat te traag. We draaiden onderdelen om de 2-6 minuten - misschien produceerden we zelfs 5-6 onderdelen tegelijk - dus duizenden onderdelen per dag." Om de kloof te overbruggen, kwam de vader van Kieffer op het idee om een thermogevormde plastic schaal als gereedschap te gebruiken .
Het resultaat is een gereedschapsloos productieproces voor composietonderdelen, dat Plastics Unlimited Tool-less Engineered Composite (TEC) noemt. “Het verwijdert de gelcoat en tool release stappen”, zegt Kieffer. "Als je thermovormt, kun je het oppervlak van klasse A inspecteren en ervoor zorgen dat het perfect is." Met andere woorden, het Klasse A-oppervlak is niet verborgen onder een composietlaminaat. "Het enige dat nodig was, was een enkel thermovormgereedschap, en het proces was nog steeds logisch voor onze klanten met plastic onderdelen."
Gepatenteerd composietproces
Kieffer merkt op dat een composiet twee materialen combineert om een beter materiaal te maken dan elk afzonderlijk bestanddeel. "We combineren twee verschillende soorten materialen en twee verschillende processen om een beter product te maken." Met name een product dat bestaat uit plastic, hars en glasvezel om een unieke mix van voordelen te bieden. "Plastics presteren veel beter bij impact dan gelcoats", legt hij uit. “Ook is het mogelijk om elke textuur of elk ontwerp op het plastic te printen, bijvoorbeeld een camouflagepatroon. De kunststoffen bieden ook veel diepte van het beeld zonder polijsten achteraf, waardoor secundaire afwerkingsbewerkingen worden geëlimineerd.”
Ondertussen maakt deze gepatenteerde technologie, vergeleken met het spuiten van gehakte vezels in een open vormproces, een hoger vezelgehalte, hogere kwaliteit en geen/lage vluchtige organische stoffen (VOS) mogelijk. Hij wijst erop dat het spuiten van gehakte vezels op kunststoffen voor badkuipen en spa's niet gepatenteerd is. "We gebruiken altijd vacuüminfusie om het FRP-onderdeel van het product te maken", zegt Kieffer, en voegt eraan toe "onze onderdelen hebben een gladde afwerking, dus we zijn meer een lichte RTM met caulplaten. We brengen het altijd naar een hoger niveau. Klanten komen naar ons met een probleem en we proberen een oplossing te vinden die past bij hun behoeften. We zijn erg innovatief en we patenteren onze nieuwe ontwikkelingen.”
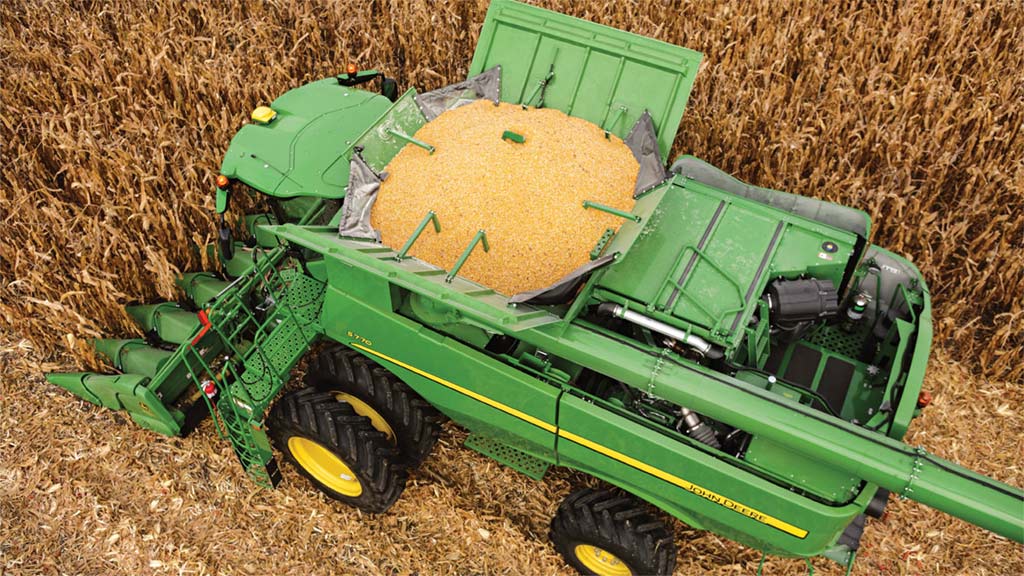
Voorbeeld onderdelen
Een van de onderdelen die Plastics Unlimited met dit proces produceert, is een graantankverlenging voor John Deere-maaidorsers, gemaakt door Deere &Company (Moline, Ill. U.S.). "Dit is het bovenste deel van de maaidorser, dat open is, waar het graan zit", legt Kieffer uit. “Vergeleken met de originele stalen tank is de onze duurzamer. We maken het met een gladde afwerking aan de binnenkant en John Deere groen aan de buitenkant met zwarte inzetstukken op de hoeken. Het is de grootste uitbreiding van de graantank die beschikbaar is en kan plat worden opgevouwen. Het is een meer ontwikkeld product in vergelijking met onze concurrenten, met schuim en ribben die zijn toegevoegd om de stijfheid te vergroten.” Er is ook wat staalwapening nodig, die volgens Kieffer eigenlijk is ingegoten, "niet secundair verlijmd".
Deze combinatie van materialen en proces geeft veel taaiheid aan het afgewerkte onderdeel. "We hebben video's van het laten vallen van betonblokken op deze delen", zegt Kieffer. Door stalen armaturen te gieten, zegt hij dat de uittreksterkte 4-5 keer groter kan zijn dan bij secundaire verlijming met behulp van industriestandaard methylmethacrylaatlijmen.
Plastics Unlimited kan tot 2.500 van deze onderdelen per maand maken, waarbij sommige panelen 1,5 bij 2 meter lang zijn. "Dit zou dure gereedschappen vereisen, als het niet met onze methode is gemaakt", zegt Kieffer, en hij merkt op dat TEC voor vrij grote onderdelen kan worden gebruikt - tot 8 bij 3 meter. “Onze onderdelen kunnen meer vorm en geometrie hebben dan staal. Dit is belangrijk voor onze klanten omdat het hen in staat stelt te differentiëren via styling. Onze UV-bestendigheid is ook beter dan de meeste gelcoats.”
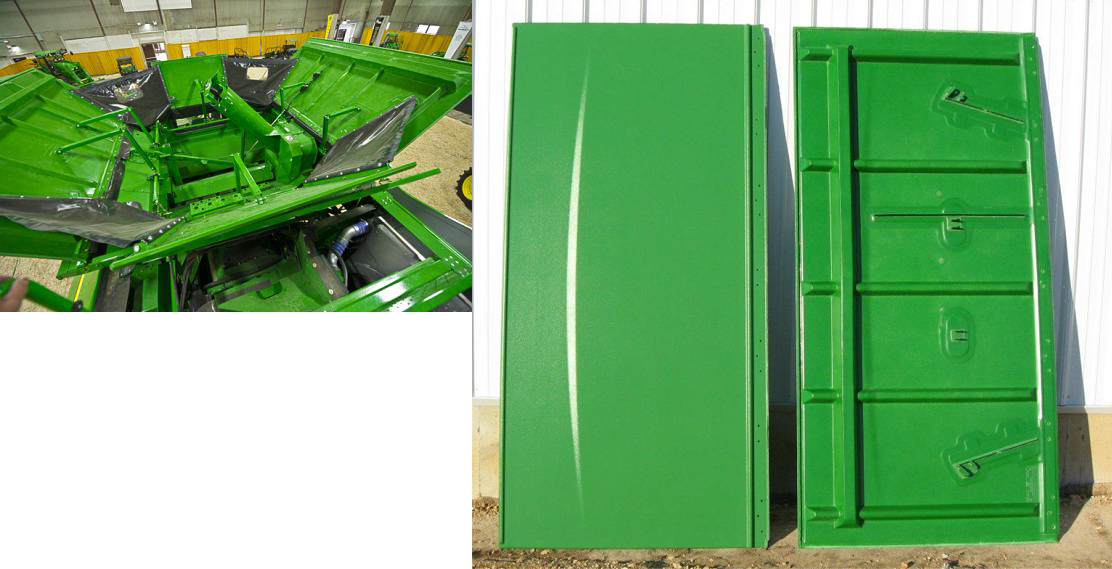
Plastics Unlimited levert onderdelen voor verschillende bedrijven, waaronder Harley-Davidson en Gehl telescopische liften. "We maken ook zacht aanvoelende onderdelen die eruitzien en aanvoelen als leer", zegt Kieffer. Het bedrijf heeft ook vrachtwagencomponenten gemaakt voor Navistar en onderdelen voor recreatievoertuigen (RV) voor Winnebago. "We geven de voorkeur aan volumeproductie, van 100.000 onderdelen per jaar tot een paar honderd."
Kieffer erkent dat lange-vezelinjectie (LFI) en harsspuitgieten (RIM) concurrerende processen zijn, “maar de onderdelen zijn niet zo structureel als wat wij doen. Een graantank van een maaidorser bevat bijvoorbeeld 400 bushels, wat 10 ton kracht uitoefent. RIM-onderdelen, die niet zwaar zijn versterkt, kunnen eenvoudigweg niet aan dit soort belastingseisen voldoen en RIM-gereedschap is erg duur.”
Voortdurende ontwikkeling
“We doen veel R&D-werk met onze klanten”, zegt Kieffer. “We onderzoeken verschillende harsen, schuimen, laminaten, versterkingslagen en afwerkingen en laten ze vervolgens prototypes zien zodat ze heel snel tests kunnen doen. We zullen proberen het onderdeel beter produceerbaar te maken, waarbij we kijken hoe we de kosten kunnen verlagen en de prestaties kunnen verbeteren, en daarnaast zullen we voldoen aan de verschillende in-service-eisen, zoals extreme warme en koude temperaturen en impact.”
Plastics Unlimited heeft 100.000 vierkante meter aan productieruimte en 75 medewerkers, waaronder een team van drie ingenieurs. De 5-assige Thermwood CNC-machine maakt in-house productie van gereedschappen en ook snelle prototyping mogelijk, de laatste belangrijk voor klanten omdat ze de ontwikkelingstijdlijnen willen verkorten.
"We werken ook samen met bedrijven voor openbaar vervoer en ruimtevaart", vervolgt hij. "Veel metro-interieurs zijn momenteel FRP met gelcoat plus aluminium structuur erachter. Ze hebben een lichtgewicht maar ook een cosmetische oppervlakteafwerking nodig. We kijken naar een breed scala aan toepassingen, waaronder medische, elektrische en constructieve toepassingen.”
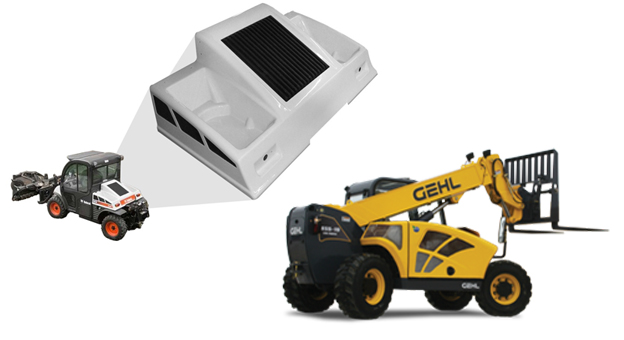
Het bedrijf kijkt ook naar thermovormen van koolstofvezelversterkte kunststoffen (CFRP). “We hebben Tepex- en Polystrand-materialen gevormd en werken aan verschillende ontwikkelingen met een medische klant”, zegt Kieffer. “We kunnen hoogwaardige plastic materialen zoals Kydex gebruiken en deze ondersteunen met CF/epoxy voor de ruimtevaart, of materialen zoals polyurethaan, polycarbonaat en ABS, die een mooie buitenafwerking geven en kosteneffectief zijn. Achter deze laatste kunststoffen kunnen we glasvezelversterkte polyester-, vinylester- of epoxylaminaten gebruiken.”
Plastics Unlimited opereert op het snijvlak van kunststoffen, metalen en composieten, zegt Kieffer. “Onze onderdelen zijn doorgaans 30 tot 40 procent lichter dan staal. Maar we merken dat de markt nog behoorlijk wat educatie nodig heeft over wat composieten zijn en wat ze kunnen doen.” Toch ziet het bedrijf veel potentieel voor toekomstige groei. "Niet alle materialen werken samen, en vooral niet alle harsen werken met alle kunststoffen", merkt hij op. “We hebben in de loop der jaren zoveel getest en ontwikkeld dat we het landschap en de mogelijkheden heel goed begrijpen. We hebben een unieke expertise en bieden een uniek scala aan mogelijke oplossingen.”
Hars
- Kubernetes in Azure:hulpprogramma's en tips voor succes
- Programmeerpatronen en tools voor cloudcomputing
- 'Smooth-Touch' TPE's voor opkomende vereisten voor verpakking en onderdelenontwerp
- Robotarmonderdelen voor pick-and-place-automatisering
- Aanpassen van ultrasone sensoren voor procesoptimalisatie en controle van composieten
- Herverwerkbare, herstelbare en recyclebare epoxyharsen voor composieten
- Combinatie van AC- en DC-diëlektrische metingen voor het bewaken van de uitharding van composieten
- Victrex en Bond-partner voor 3D-printen van PAEK-onderdelen
- 20 basislasgereedschappen en -apparatuur voor beginners
- Afwerkingsprocessen voor onderdelen en componenten
- DAGELIJKS EN PERIODIEK ONDERHOUD VAN TRANSPORTBANDEN EN ONDERDELEN