Clean Sky 2's PASSARO-project richt zich op one-shot OOA composiet cockpit
Het PASSARO-project (caPAbilities for innovation Structural and Functional Testing of AeROstructures) heeft tot doel nieuwe multifunctionele materialen te ontwikkelen — met integratie van geluidsisolatie en hoge energie-impactweerstand — en inspectieoplossingen voor een nieuwe composiet cockpit die in één keer wordt vervaardigd en aangevuld met autoclaaf (OOA) technologieën zoals in-situ consolidatie van thermoplastisch composiet en vloeibare harsinfusie. Deze composiet cockpit is ontwikkeld door Airbus Defense and Space (Madrid, Spanje) tijdens Clean Sky 1, gebaseerd op het C295-vliegtuig. Het project is ook gericht op de automatisering van productieprocessen en op nieuwe testbenaderingen op basis van Industrie 4.0-concepten en de ontwikkeling van ergonomische geavanceerde concepten die het pilootcomfort en de verbeterde mens-machine-interface bevorderen.
Het PASSARO-project, onderdeel van het Airframe-platform van Clean Sky 2, startte in juli 2016 met een totale duur van 48 maanden. Het bestaat uit elf partners uit Portugal en Spanje die nauw samenwerken met Airbus Defence and Space.
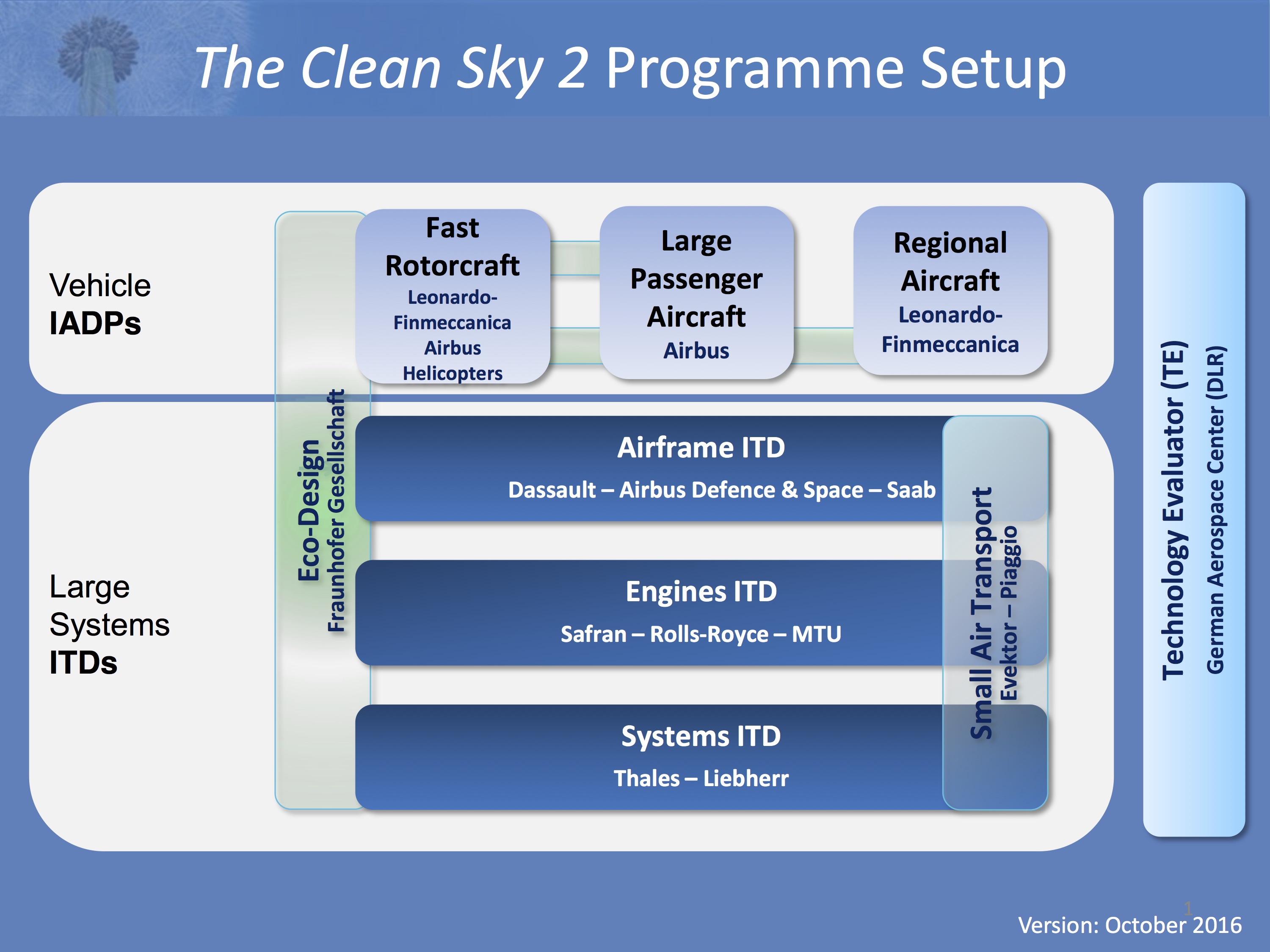
BRON:Clean Sky 2
Synergieën met regionaal MOSHO-project in Portugal
Veel Clean Sky 2 (CS2)-projecten delen synergieën met regionale EU-lidinitiatieven (bijv. CORAC in Frankrijk). Het PASSARO-project heeft complementaire activiteiten met Portugese nationale O&O-initiatieven bevorderd. Het MOSHO-project (Advanced solutions for impact materials, repair of composite aero-structures and their monitoring) vormt een aanvulling op de PASSARO-activiteiten waarbij enkele van de partners betrokken zijn en wordt ondersteund door ADS (Airbus Defense and Space) als Clean Sky 2-coördinator voor de ITD casco. Het project zal geavanceerde oplossingen ontwikkelen en integreren voor de reparatie van composiet aerostructuren.
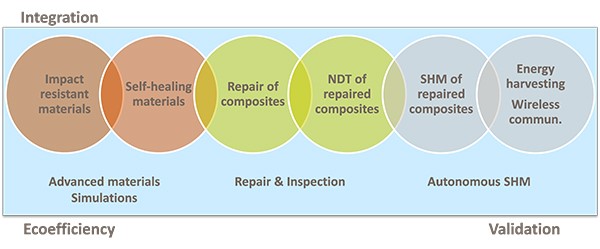
Figuur 3:technische reikwijdte van het MOSHO-project BRON: https://www.cleansky.eu/commissaris-moedas-meets-passaro-at-isq
PASSARO collaboratieve robots verkorten de cyclustijd voor handlay-up tot 70%
Als onderdeel van de doelstellingen van het PASSARO-project om te onderzoeken en te ontwikkelen hoe collaboratieve robots kunnen worden gebruikt bij de productie van composieten, heeft het OPTIMAL-project een praktische en kosteneffectieve geautomatiseerde oplossing ontwikkeld om de traditionele handoplegging te vervangen, met behulp van gekwalificeerde materialen.
Traditioneel is het vervaardigen van composietcomponenten met prepreg in wezen een handgemaakte activiteit, maar er worden stappen gezet richting automatisering. In het afgelopen decennium zijn er verschillende geautomatiseerde lay-upoplossingen ontstaan voor relatief eenvoudige geometrische onderdelen. Deze oplossingen zijn vaak vrij duur en vereisen vaak dat fabrieken helemaal opnieuw worden ontworpen voor hun installatie. Ze vereisen doorgaans speciale omgevingen in de vorm van geïsoleerde cellen met speciale veiligheidssystemen. Als alternatief kunnen collaboratieve robots (cobots) worden geïntegreerd in de bestaande productieworkflows om sommige taken te automatiseren en de productiviteit te verbeteren zonder de omgeving drastisch te veranderen.
Industriële robots zijn snel, sterk en hebben een uitzonderlijke nauwkeurigheid en herhaalbaarheid, maar ze zijn alleen ontwikkeld met het oog op optimalisatie van het eindresultaat. Ter vergelijking:cobots zijn langzamer, minder nauwkeurig en kunnen kleinere payloads aan, maar hebben wat nodig is om eenvoudige taken te automatiseren, vooral naast mensen, tegen aanzienlijk lagere kosten. Cobots hebben lastsensoren die de kleinste schokken detecteren en veilig stoppen.
Het doel van OPTIMAL bij het ontwikkelen van cobottechnologieën is het verbeteren van de eigen capaciteit, en die van andere bedrijven, om meer herhaalbare producten van hogere kwaliteit aan te bieden in grote hoeveelheden en tegen lagere prijzen.
Binnen het werkpakket 10 van het PASSARO-project werden drie hoofdstappen ontwikkeld met behulp van collaboratieve robots:
- Ply pick-up en sortering, rechtstreeks van de geautomatiseerde laagsnijder;
- Ply peeling met behulp van een speciale cel;
- Ply positioneren en stapelen in een tool.
Om deze activiteiten uit te voeren, is een cel ontwikkeld die prepreg-lagen van de laagsnijder ontvangt en deze automatisch pelt en op een mal stapelt.
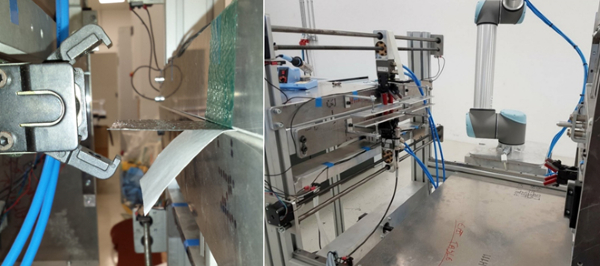
Samenwerkende robots gebruikt voor composietproductie in het PASSARO-project. BRON: ISQ-groep
Positionerings- en stapeltaken worden uitgevoerd door de robotarm met behulp van speciale zuignappen voor prepreg-behandeling. De dunschiller is een complexere machine, waarbij perslucht wordt gebruikt om de prepreg te pellen, die wordt beschermd door twee coatings - meestal een plastic en een papier, of gewoon door twee plastics. Het peelingconcept is gebaseerd op het feit dat verschillende materialen de neiging hebben om op verschillende frequenties te trillen wanneer dezelfde stimulus wordt toegepast. Door de verschillende trillingsfrequenties ontstaan luchtbellen tussen de prepreg en de deklaag. De plaatresonator past de trillingsamplitude aan voor verschillende materialen. Dit prototype kon afpelsnelheden bereiken met bijna 100% succes voor specifieke materialen en een stapelnauwkeurigheid van ± 0,5 mm, in elk van de twee vrijheidsgraden in het vlak van de mal, en ± 0,1º in rotatie.
De modulaire benadering van dit systeem maakt het onafhankelijk van de laagafmetingen. De breedte wordt afgedekt door meer parallelle schilmodules toe te voegen en de lengte door het openingsbereik van de schilmachine aan te passen. Deze technologie biedt, vergeleken met een menselijke operator, een duidelijke verbetering in procesnauwkeurigheid, herhaalbaarheid en vooral cyclustijd, met reducties tot 70%.
Auteurs:António Reis, Nicole Cruz, Marco Neves (OPTIMAL) en Rúben Buelga Sanchez (ADS). Voor meer informatie contacteer:
INEGI
Campus van FEUP
Rua Dr. Roberto Frias, 400
4200-465, Porto, Portugal
Tel:(+351) 229 578 710
E-mail:[email protected]
Hars
- Solvay breidt capaciteit thermoplastisch composiet uit
- Toray in Dutch Project for Aircraft Liquid-Hydrogen Tanks
- Clean Sky 2 FUSINBUL-project ontwikkelt full-scale drukschotten van koolstofvezel
- Het belang van harskeuze
- Clean Sky 2 FRAMES-project bevordert verwarmingssimulatie van thermoplastisch composiet AFP met xenon-flitslamp
- Clean Sky 2 publiceert projectresultaten
- Duitse composietspecialist INVENT werkt samen in SUSTAINair voor meer circulariteit van vliegtuigen
- Wing of Tomorrow-ribben:One-shot, thermoplastische, OOA-consolidatie
- Clean Sky 2 IMCOLOR-project ontwikkelt geïntegreerd productieproces voor lichtgewicht productontwerp
- Consortium streeft naar oplossingen voor thermoplastische composietstructuren van koolstofvezel
- Snelle productie van op maat gemaakte samengestelde blanks