Wing of Tomorrow-ribben:One-shot, thermoplastische, OOA-consolidatie
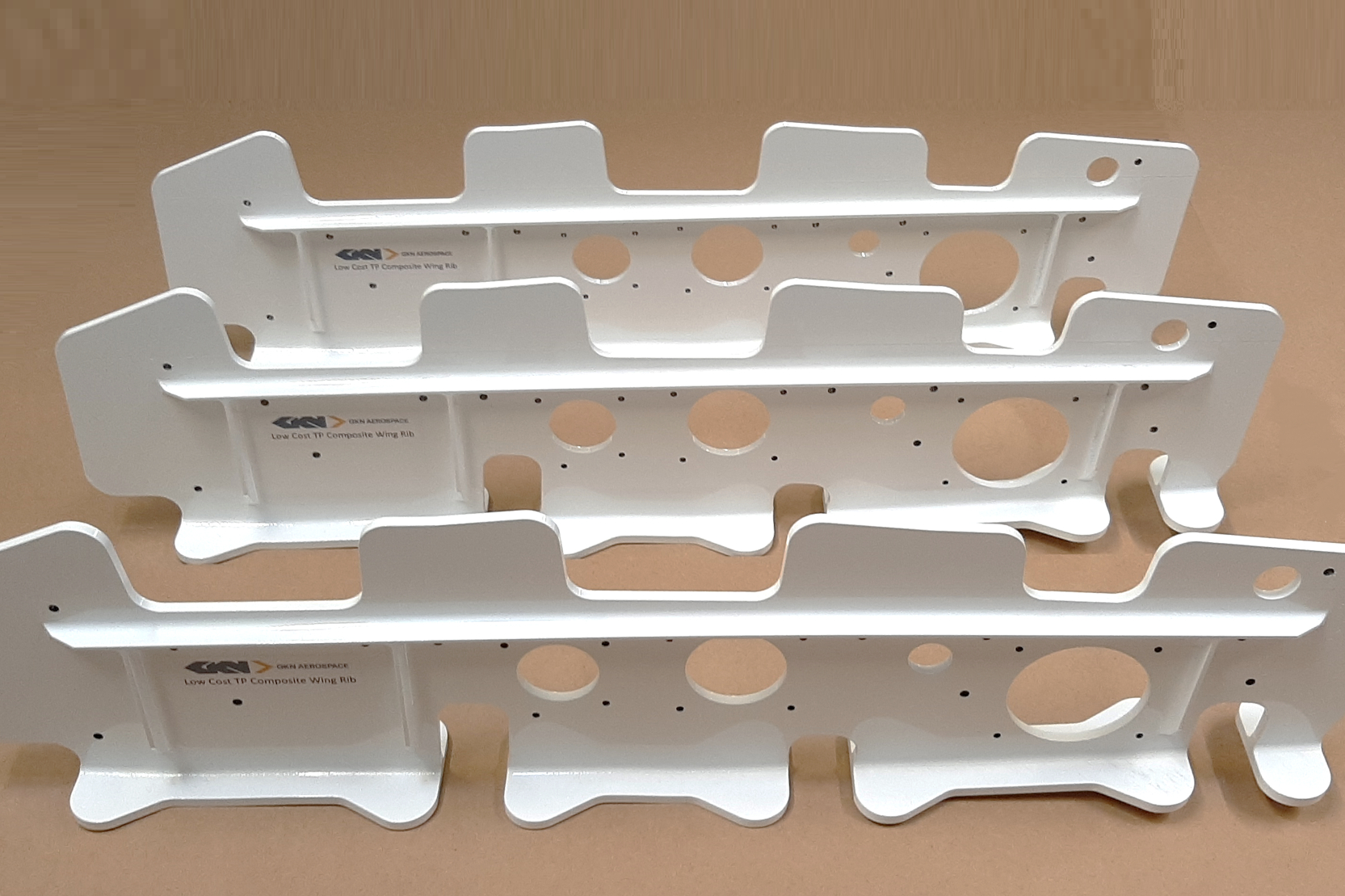
Airbus' Wing of Tomorrow (WOT)-programma, gelanceerd in 2015, heeft de afgelopen zes jaar besteed aan het onderzoeken van meer kostenconcurrerende, snellere materiaal-, productie- en assemblagetechnologieën voor commerciële vliegtuigvleugels met één gangpad (zie CW em> eerdere berichtgeving over het WOT-programma).
Volgens Arnt Offringa, directeur van het GKN Aerospace Global Technology Centre Netherlands (Hoogeveen), GKN Aerospace (Bristol, V.K.) is zeer actief geweest in het WOT-programma, inclusief de ontwikkeling van een vleugelliggerdemonstrator gemaakt via harstransfergieten (RTM) en vier aluminium vleugelribben. Een andere technologiedemonstrator die onlangs door GKN Aerospace werd geleverd, betrof de ontwikkeling van zowel een kostenconcurrerende thermoplastische composietrib als een innovatief, modulair perssysteem voor one-shot, out-of-autoclave (OOA) productie om deze te produceren.
De sprong maken naar thermoplasten
In 2018 begon GKN Aerospace interne discussies over materialen en productietechnologieën die zouden kunnen worden gebruikt om vijf demonstrators te produceren
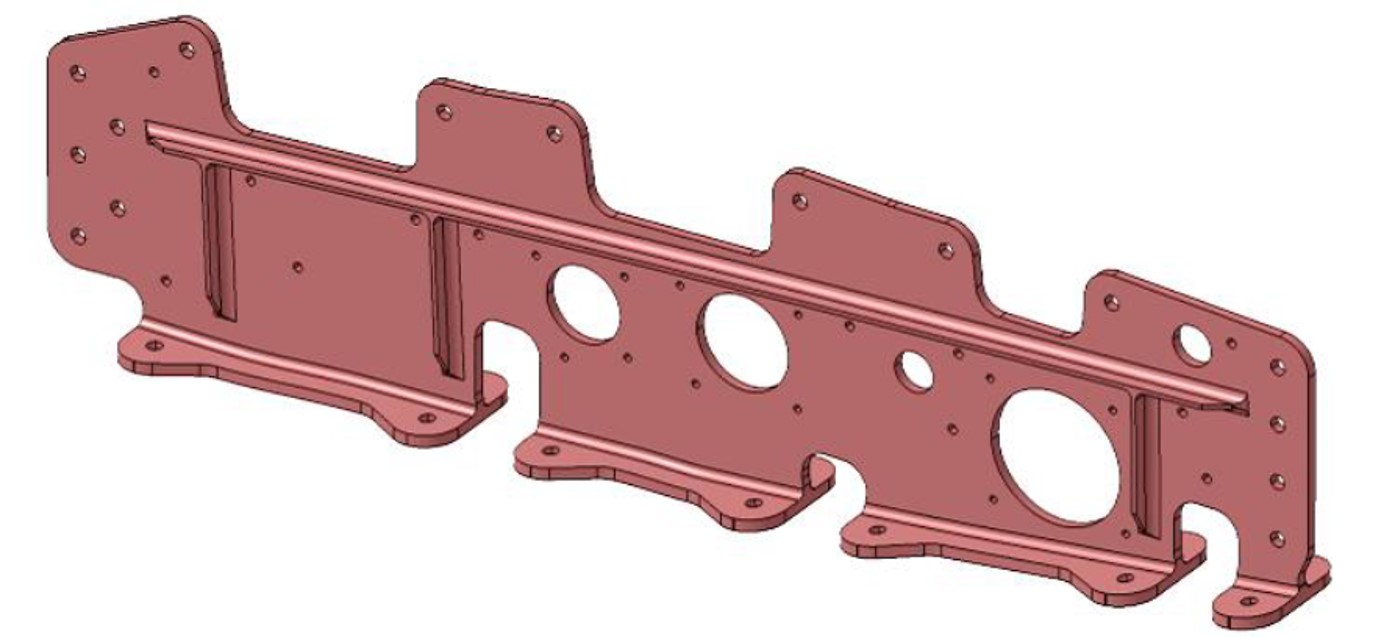
Het ontwerpen van de rib. Om een dun, lichtgewicht onderdeel mogelijk te maken, bevat het ribontwerp (bovenaan) GKN's stompe verbindingstechnologie (onder), met spuitgegoten verstijvervullers (midden, weergegeven in groen).
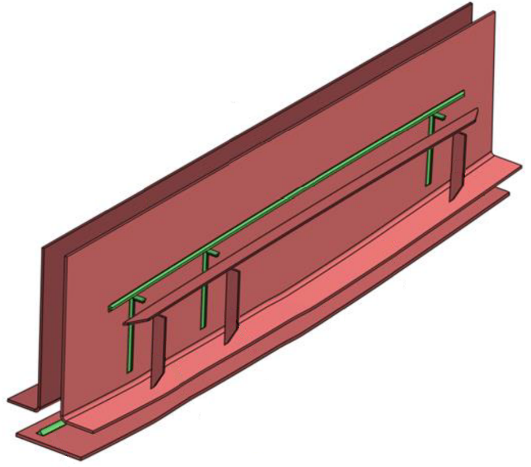
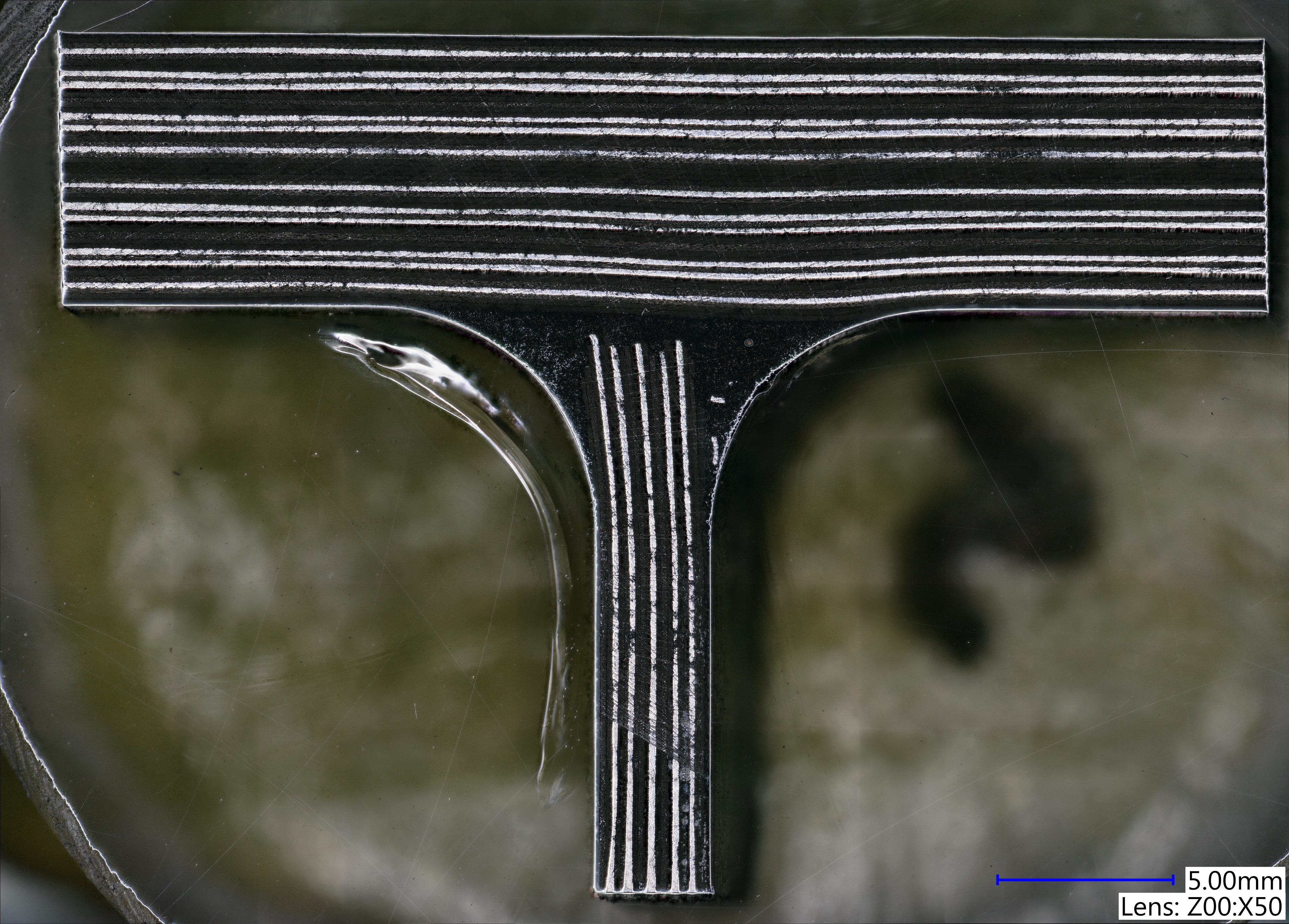
ribben voor het WOT-programma. GKN Aerospace vergeleek verschillende materiaalopties, waaronder thermohardende en thermoplastische composieten. Aluminium, het traditionele materiaal voor ribben van commerciële vliegtuigen, werd gekozen om vier grotere binnenboordribben te produceren, maar voor de kleinere buitenboordrib besloot het bedrijf een composietoptie te onderzoeken. Offringa merkt op dat omdat de WOT-demonstrator een composietvleugel zal zijn, het ontwikkelen van een composietrib die kan concurreren met aluminium een logische stap is.
"Een composietrib op een composietvleugel is om verschillende redenen gunstig", zegt hij. “Ten eerste betekent het gebruik van composieten met composieten dat er geen verschil is in thermische uitzetting tussen de materialen, zoals je zou hebben met een metalen rib op een composietvleugel of omgekeerd. Ten tweede heeft u geen problemen of zorgen met betrekking tot corrosie. Composieten betekenen ook minder gewicht. Last but not least maakt het gebruik van composieten de inspectie eenvoudiger.”
Offringa legt uit dat typische metalen ribben visuele menselijke inspectie vereisen zodra de laatste vleugel is gemonteerd. Vanwege de locatie van de ribben aan de binnenkant van de vleugel, betekent dit echter dat grote elliptische luiken in de onderste vleugelslaag moeten worden gesneden, zodat mensen de vleugel kunnen binnengaan om ze te inspecteren. “Als je naar een composietrib gaat, heb je minder vermoeiing in de ribben en minder potentiële vermoeiingsscheuren die je moet inspecteren. Inspectie wordt veel eenvoudiger en minder intensief en u hoeft geen luiken meer in de wingskin te bouwen. Het zal een doorlopende vleugelslaag zijn”, zegt hij.
Gewichtsvermindering, corrosieweerstand en minder invasieve inspectievoordelen kunnen worden behaald met thermohardende of thermoplastische composieten. "We hebben een interne studie gedaan en gekeken naar gewicht, kosten en industrialisatie, en na vergelijking van de verschillende technologieën, werd de keuze gemaakt om voor thermoplasten te gaan, omdat dit het meeste potentieel en de beste businesscase had met betrekking tot kosten", zegt Offringa. .
Gezien de nabijheid van Airbus's Filton, V.K. vleugeltechnologiecentrum waar de WOT-demonstrator zal worden getest, is de Bristol, V.K.-vestiging van GKN Aerospace het belangrijkste knooppunt van het WOT-werk van het bedrijf. Gezien de expertise van GKN Aerospace Netherlands op het gebied van thermoplasten uit de tijd als Fokker Technologies, hebben de twee GKN Aerospace-teams hun krachten gebundeld voor de ribdemonstrator. "Het ontwerp is gedaan in het Verenigd Koninkrijk, maar de ontwikkeling van de productie is in Nederland gedaan, dus het was een heel fijne samenwerking tussen de verschillende teams in GKN Aerospace", zegt Offringa.
Sue Partridge, hoofd WOT bij Airbus, merkt op:“Samenwerking met partners is een belangrijk aspect van het Wing of Tomorrow-programma. Door onze middelen te combineren, kunnen we oplossingen ontwikkelen die de capaciteiten van onze beide organisaties benutten voor een beter resultaat.”
Voor de WOT-ribben die aan Airbus werden geleverd, gebruikte GKN Aerospace Solvay's (Brussel, België) APC-tapes van koolstofvezel/polyetherketoneketon (PEKK-FC), die is gebaseerd op de Novaspire PEKK-FC (FC) snelkristalliserende formule van het bedrijf. Offringa merkt op dat Toray Advanced Composites' (Morgan Hill, Californië, VS) laagsmeltende koolstofvezel/polyaryletherketon (PAEK) materiaal ook wordt geëvalueerd als een optie voor toekomstige ribstructuren.
Een vleugelrib van de volgende generatie ontwerpen
Er zijn meer dan 20 ribben op een typische vliegtuigvleugel met één gangpad. De demonstratorrib van thermoplastisch composiet is de 14e op de demonstratorvleugel; de anderen zullen alternatieve materialen en processen demonstreren.
Thermoplastische composietribben worden vaak vervaardigd via stempelvorming voor kleine vliegtuigen, zegt Offringa. GKN Aerospace sloot traditionele stempelvorming echter uit als een optie voor de WOT-rib omdat de vleugels van commerciële vliegtuigen, zelfs voor smalle lichamen zoals de WOT-demonstrator, onder zeer hoge compressie- en trekbelastingen worden geplaatst.
"Als je in de traditionele zin van een thermoplastische ribbe zou gaan stempelen, dan zou je een zeer dikke ribbe moeten maken, met een dik web om het sterker te maken, zodat het bestand is tegen de krachten die erop werken", zegt Offringa, en dat verdient niet de voorkeur gezien de vereisten voor gewichtsvermindering. Bovendien zou stempelvorming niet in staat zijn om een dubbelzijdige onderflenscomponent te creëren op de ribbe waar het onderdeel aansluit op de onderste vleugelhuid; een extra onderdeel zou moeten worden gefabriceerd en aan de rest van de ribbe worden vastgeschroefd. GKN Aerospace had een productieproces nodig dat meer flexibiliteit mogelijk maakte voor het ontwerp dat het team in gedachten had.
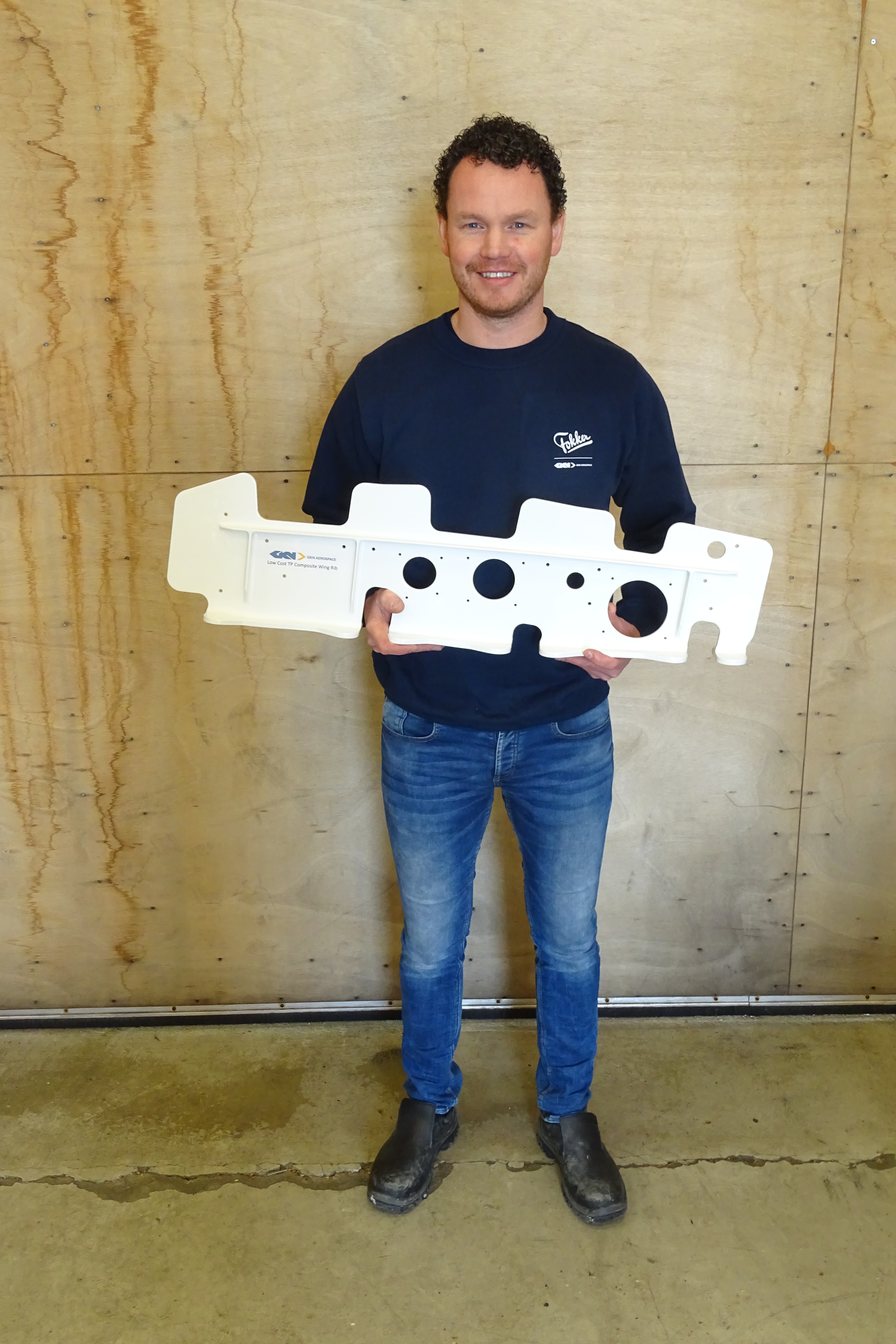
De 90 centimeter lange, 24 centimeter hoge thermoplastische ribbe van GKN Aerospace heeft een verticaal web en een bidirectionele 8 millimeter dikke flens die uitsteekt vanaf de onderkant van de rib. Om aan de gewichtseisen te voldoen, is het web slechts 7 millimeter dik. Om knikken te voorkomen en de stijfheid te vergroten, is het web versterkt met 3 millimeter dikke verstijvingselementen met behulp van GKN Aerospace's stompe verbindingstechnologie, die gebruik maakt van platte verstijvingsvoorvormen en spuitgegoten "vulmateriaal" om een sterke, doorlopende verbinding te creëren (zie "Thermoplastische primaire aerostructuren zetten nog een stap voorwaarts” om meer te weten te komen over het gebruik van deze technologie op een Gulfstream-romppaneel vervaardigd met Solvay's koolstofvezel/PEKK-FC-tapes).
"We wisten dat als we deze vorm in composieten konden maken en robuust konden maken, we een zeer lichtgewicht ontwerp zouden hebben met de gewichtsvermindering waarnaar we op zoek waren. Maar het probleem was, hoe maak je zo'n ingewikkelde vorm kosteneffectief en tegen hoge tarieven? Daar hebben we ons in gestoken om dit nieuwe product te maken”, zegt Offringa.
Eenstaps, OOA-productie
Het proces bouwt voort op technologie die GKN Aerospace eerder heeft gebruikt voor het TAPAS-project (Thermoplastic Affordable Primary Aircraft Structure) en voor de ontwikkeling van een romppaneel voor Gulfstream waarbij gebruik wordt gemaakt van de stompe verbindingstechnologie van het bedrijf. Voor de WOT-rib ontwikkelde GKN Aerospace een OOA, eenstaps consolidatieproces. "We hebben ons eerdere werk naar een hoger niveau getild door voor het eerst uit de autoclaaf te gaan", merkt Offringa op.
Eerst worden unidirectionele (UD) thermoplastische tapes op de juiste breedte gesneden en wordt een laminator gebruikt om de platte elementen voor te vormen tot twee L-vormige baanvoorvormen. De baanvoorvormen, een platte voorvorm voor de flens en kleinere voorvorm- en spuitgegoten vulelementen die de draagbalken vormen, worden allemaal in een gereedschap geladen, dat in een modulaire co-consolidatiepers wordt geplaatst die vergelijkbaar is met een harsoverdrachtsvorm. (RTM) druk. De pers sluit en een blaassysteem wordt gebruikt om zowel horizontale als verticale druk te creëren, waarbij de druk in een autoclaaf wordt gesimuleerd. Een geïntegreerd weerstandsverwarmingssysteem brengt het composiet kort op smelttemperatuur voordat het afkoelt voor consolidatie.
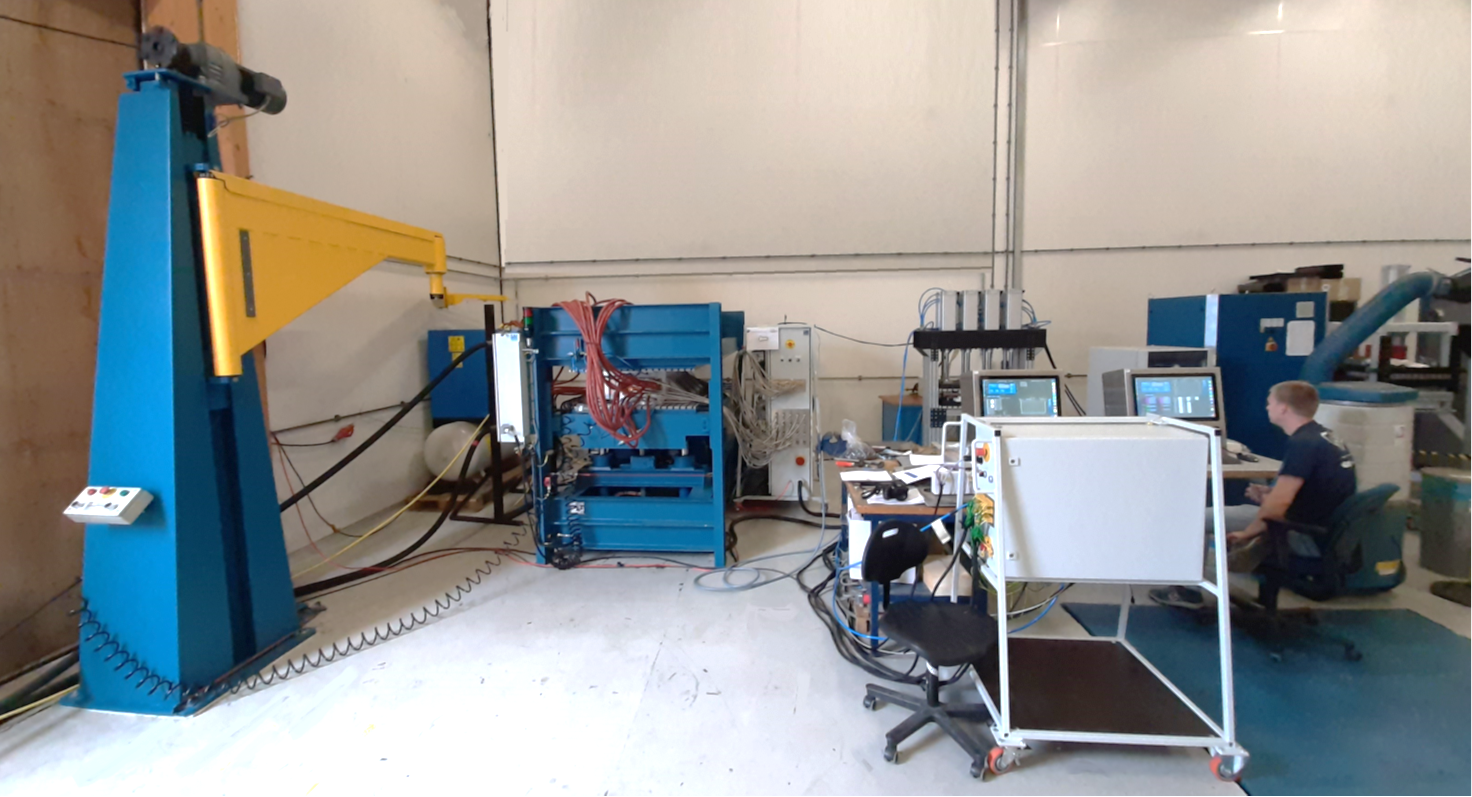
"We hebben de meeste ontwikkelingsinspanningen gestoken in het afstemmen en optimaliseren van de tooling", zegt Offringa. Het systeem is modulair ontworpen; het gereedschap kan worden verwisseld om plaats te bieden aan ribben met verschillende afmetingen of andere soorten onderdelen, terwijl hetzelfde verwarmings- en koelsysteem behouden blijft. Hoewel dit niet nodig is voor deze ribben, kan de pers die GKN Aerospace heeft ontwikkeld in haar technologiecentrum, onderdelen tot 6 meter lang opnemen, waaronder ook andere panelen of balken.
Het procesbesturingssysteem is essentieel bij het verwerken van thermoplasten. Thermoplasten smelten bij hogere temperaturen dan thermoharders en moeten worden gekoeld in een gecontroleerd, consistent proces om kromtrekken te minimaliseren en cystalliniteit te maximaliseren. "Het is erg belangrijk om het exacte proces van begin tot eind te beheersen", zegt Offringa. “Het thermisch beheer van de verwarmingscyclus is erg belangrijk.” (zie de zijbalk "Thermoplastische (TP) vormingsproblemen" in dit artikel voor meer informatie over problemen en het belang van procesbeheersing bij het gebruik van thermoplasten).
Er worden speciale gereedschapsfuncties gebruikt om de dunne, geïntegreerde verstijvers gemakkelijk van het gereedschap los te maken. Het uit de vorm gehaalde onderdeel heeft een bijna netto vorm en wordt vervolgens bijgesneden om het voltooide onderdeel te vormen. Van tool in tot tool out, het hele proces duurt ongeveer 45 minuten. Dit betekent dat er met één druk op de knop zo'n 15 vleugelribben kunnen worden vervaardigd in een shift van acht uur.
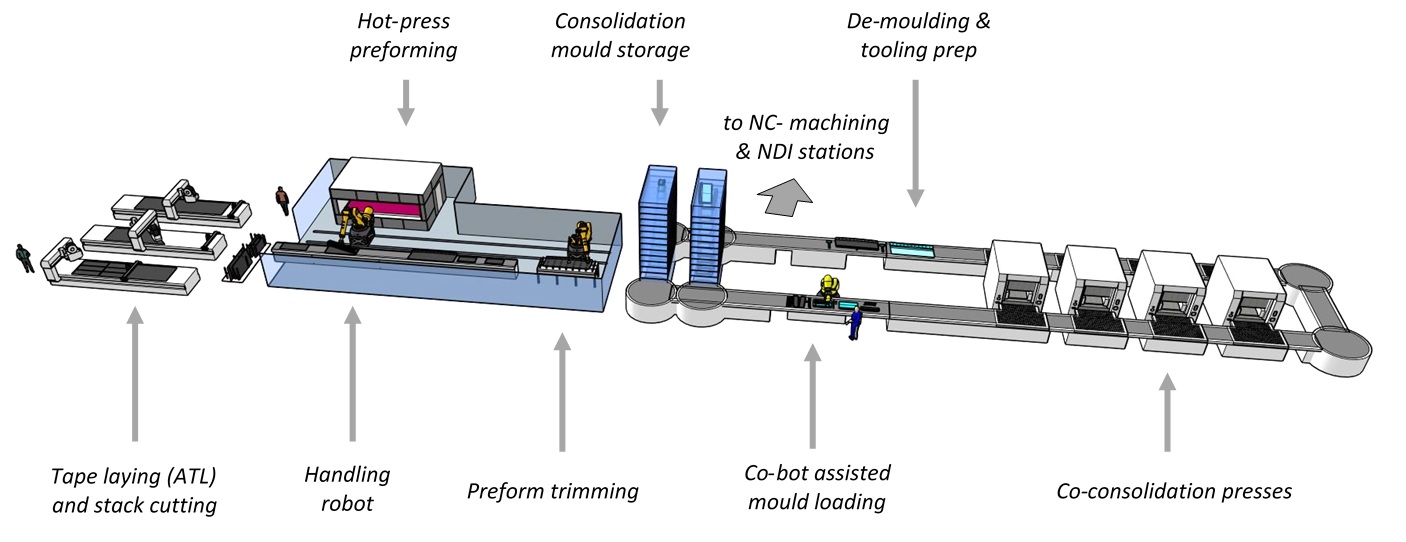
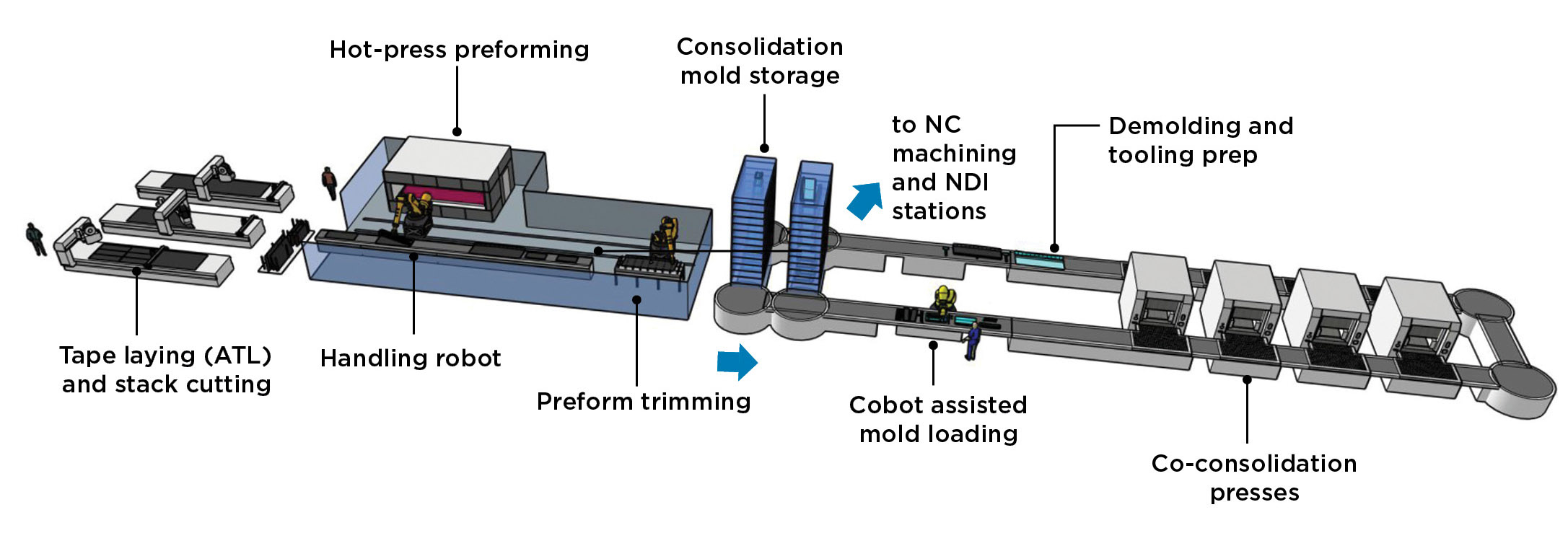
"Het wordt uiteindelijk een eenvoudig productieproces", merkt Offringa op. “We doen veel dingen tegelijk:het coconsolideren van preforms met verschillende vormen, het creëren van de onderkant van de rib met een bidirectionele flens, en tegelijkertijd verstevigen we het web met de butt-jointed-technologie. Maar uiteindelijk nemen we alle elementen van het materiaal, plaatsen ze in een tool, en creëren we één homogeen onderdeel in één bewerkingsstap.”
Testen, levering en verder
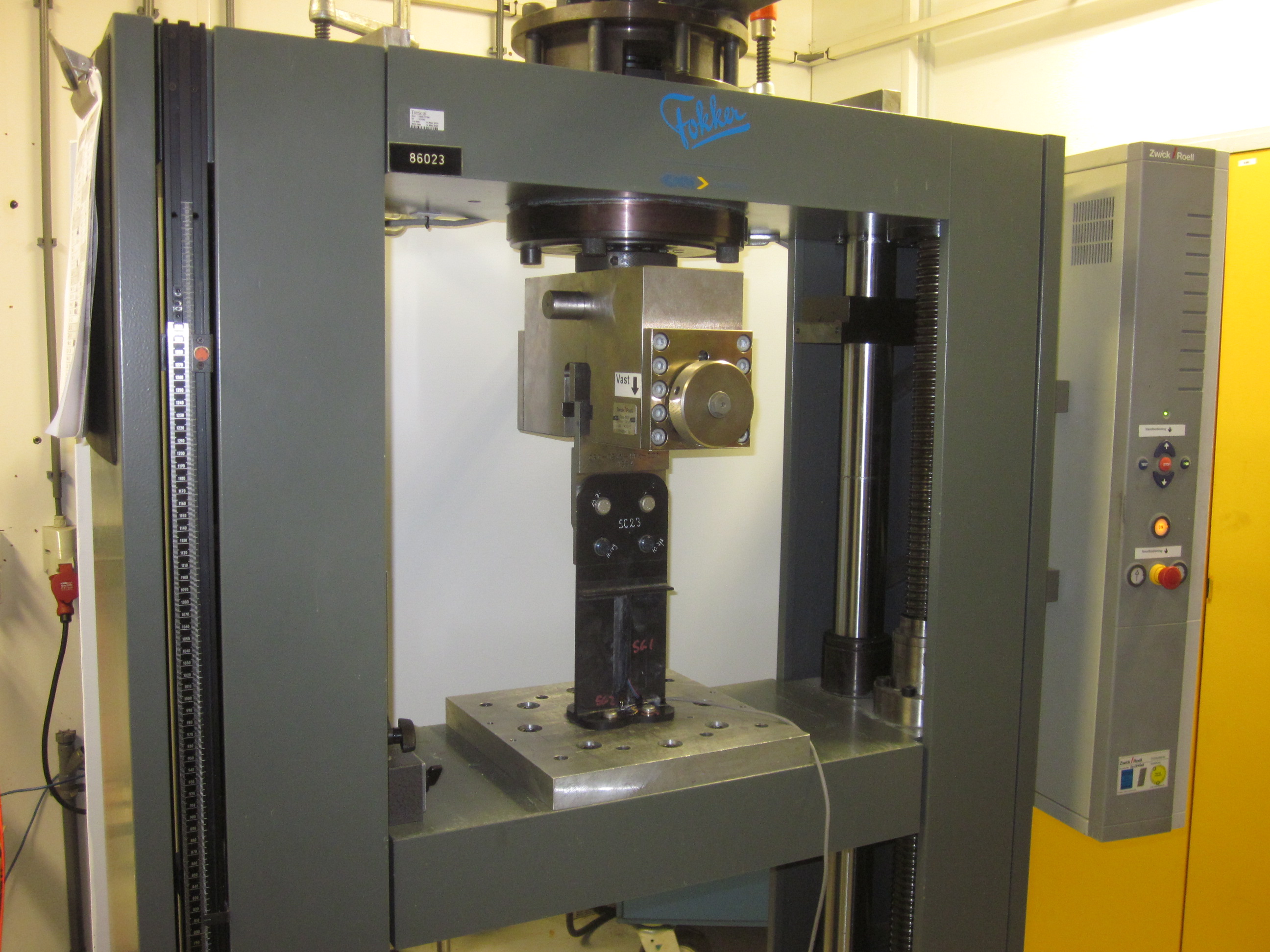
Testen. Subcomponenten zijn getest om te voldoen aan de eisen voor trek- en druksterkte in de faciliteiten van GKN op Isle of Wight en Hoogeveen.
Eind 2019 werden rib-subcomponenten getest in de faciliteiten van GKN Aerospace op Isle of Wight en Hoogeveen, en Offringa zegt dat ze "met een ruime marge" voldeden aan de vereisten voor trek- en compressiebelasting. Hij voegt eraan toe:"Het is sterk, het is taai, het is gemakkelijk te produceren. Dit is een concept dat precies is geworden zoals we hadden gehoopt.” Vergeleken met een aluminiumversie, zegt Offringa dat de thermoplastische composietversie aanzienlijke gewichtsbesparingen biedt en kostenconcurrerend is.
Het bedrijf heeft drie ribben aan Airbus geleverd, waarvan er één zal worden geassembleerd en getest op de WOT-demonstrator. GKN Aerospace blijft werken aan het optimaliseren van haar proces en materialen voor commerciële ruimtevaartribben, zowel voor Wing of Tomorrow als daarbuiten.
Hars
- Continu-vezelversterkte thermoplastische composiet volledig gemaakt van natuurlijke hulpbronnen
- Solvay breidt capaciteit thermoplastisch composiet uit
- Fraunhofer stelt geautomatiseerde Engel-productiecellen in gebruik voor R&D van thermoplastisch composiet
- DLR Institute of Structures and Design vergroot de maturiteit van thermoplastische composiet rompstructuren
- Solvay voltooit de installatie van de faciliteit in South Carolina, wat bijdraagt aan de capaciteit van thermoplastisch composiet in de VS
- Thermoplastische tapes blijven potentieel tonen voor composiet aerostructuren
- INEOS Styrolution gaat productielocatie bouwen voor StyLight thermoplastisch composiet
- Xenia introduceert CF/PP thermoplastische composietverbindingen
- Thermoplastische composietbuis in opkomst in de diepzee
- NIAR's NCAMP kwalificeert TenCate thermoplastisch composiet
- TenCate viert assemblage van thermoplastisch composietconsortium in Brazilië