Versnelling van thermoplastische composieten in de ruimtevaart
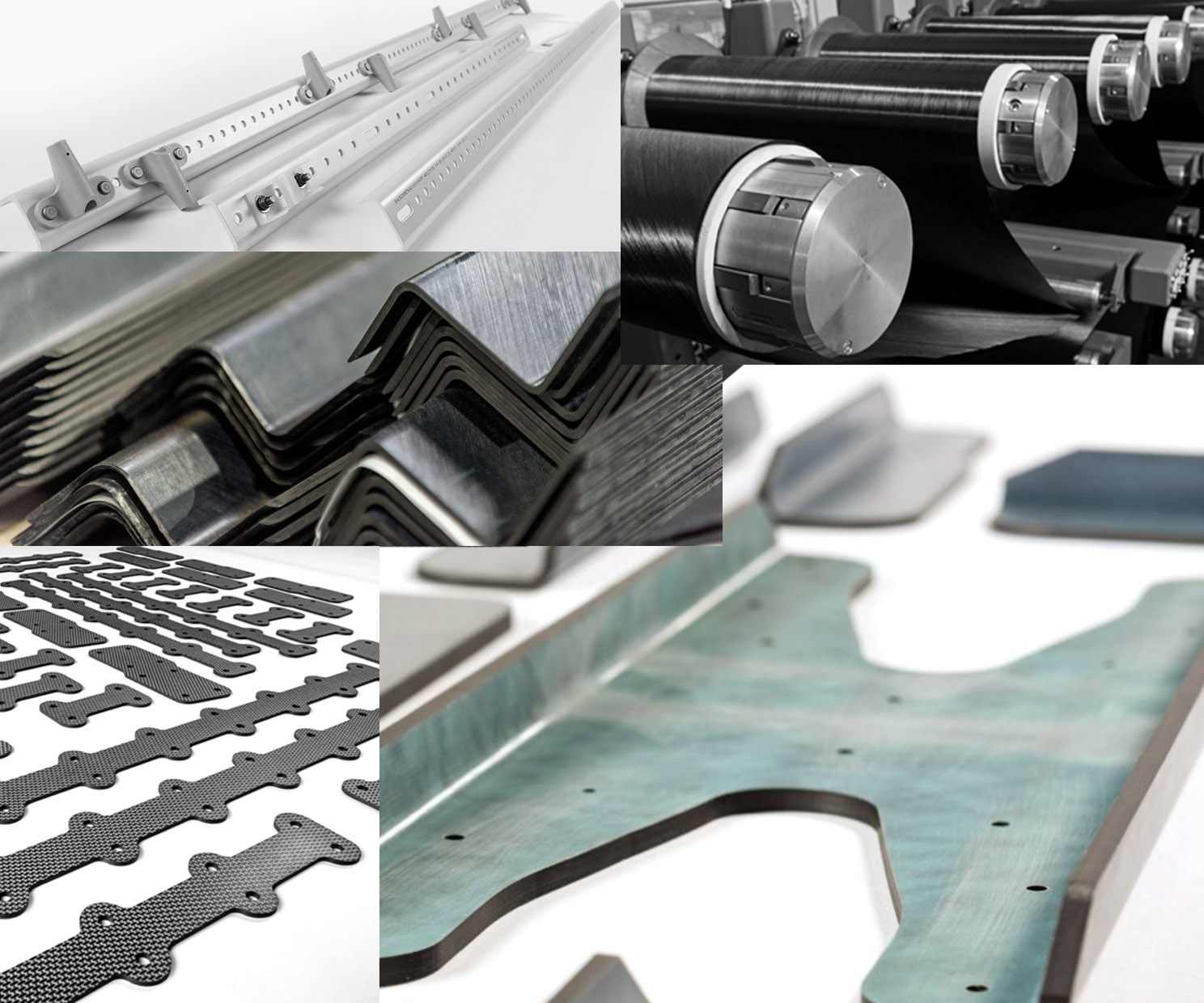
Doorlopende vezelversterkte thermoplastische composieten (TPC's) zijn aangehaald als een technologie die de toekomst van duurzame vliegtuigen mogelijk maakt, omdat ze hogere productiesnelheden bieden van lichtgewicht, zeer sterke onderdelen die zonder gaten of bevestigingsmiddelen kunnen worden samengevoegd tot voordelige gelaste assemblages.
CW publiceerde in 2018 een reeks artikelen over TPC-tapes, in-situ consolidatie en lassen en presenteerde in 2019 twee webinars over TPC's in automobieltoepassingen en TPC-ontwikkelingen voor de lucht- en ruimtevaart. De meeste van mijn artikelen en presentaties tot nu toe verwijzen naar fabrikanten van TPC-onderdelen en leveranciers van apparatuur in Europa, evenals de Automated Dynamics-divisie van Trelleborg in de VS. Ik heb ook een rondleiding gegeven door het in de VS gevestigde Tri-Mack Plastics. Maar ik heb helaas een andere fabrikant van TPC-onderdelen hier in de VS over het hoofd gezien die al 15 jaar stilletjes de technologie en productie-envelop naar voren duwt. ATC Manufacturing — gevestigd in Post Falls, Idaho, net buiten Spokane, Washington — produceert een miljoen onderdelen per jaar, allemaal continu vezelversterkte thermoplasten en allemaal voor de lucht- en ruimtevaartindustrie. Met een unieke expertise in het snel vormen van 3D-onderdelen, is ATC ook een belangrijke partner in het RApid high-Performance Molding (RAPM) onderzoeksprogramma met Boeing Co. (Chicago, Illinois, VS) en het Defense Advanced Research Projects Agency (DARPA, Arlington, Va., VS) voor het Amerikaanse ministerie van Defensie (DoD).
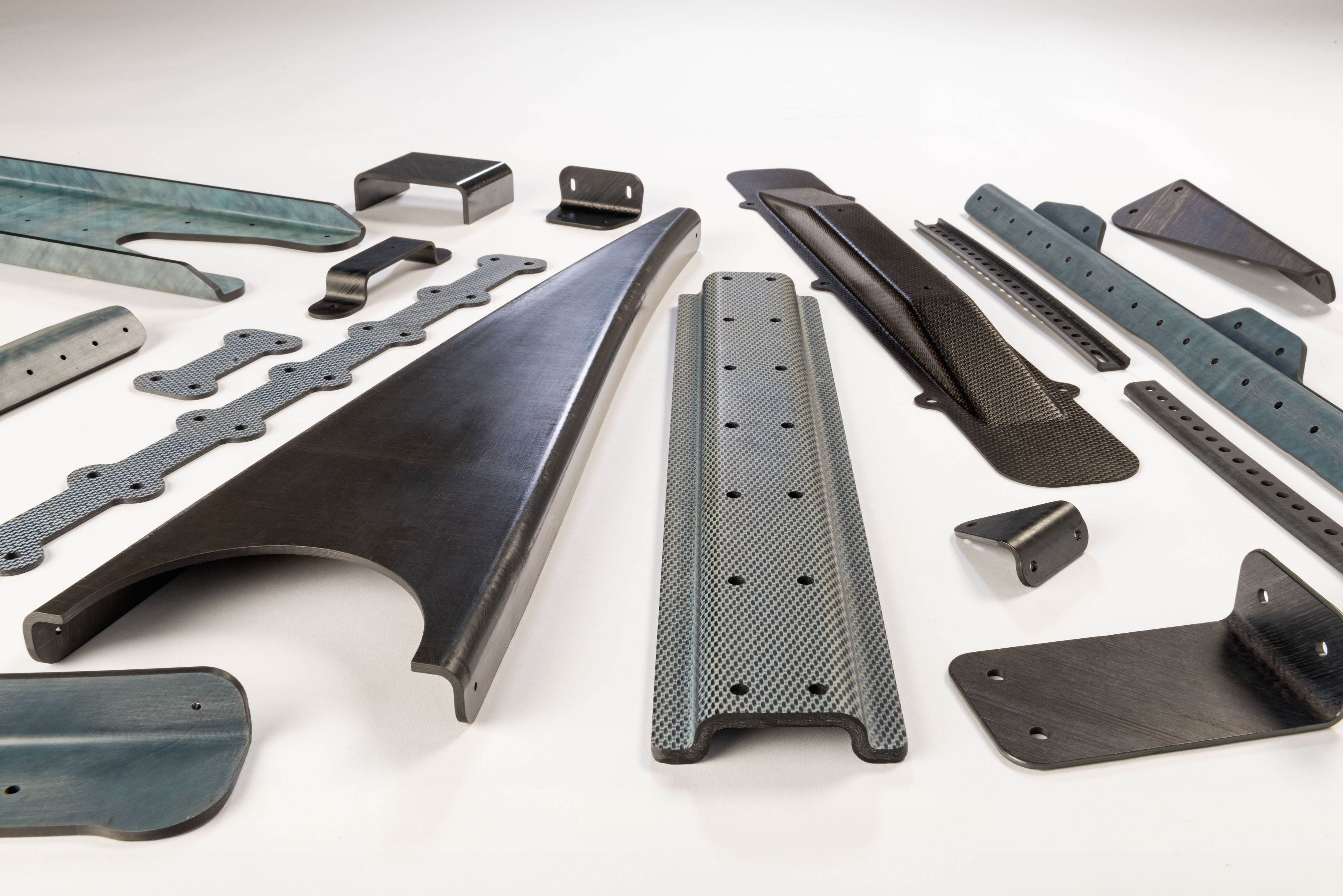
ATC Manufacturing produceert jaarlijks een miljoen thermoplastische composietonderdelen voor ruimtevaarttoepassingen, waaronder ribben, clips, beugels en verstijvers. BRON | ATC-productie
Wie is ATC?
ATC Manufacturing werd in 2004 opgericht door voormalig Boeing-ingenieur Dan Jorgenson, die de co-voorzitter van het bedrijf blijft. "We hebben altijd een sterke technische en technische focus gehad", zegt David Leach, directeur bedrijfsontwikkeling voor ATC Manufacturing. Het bedrijf heeft ook een lange geschiedenis bij Boeing, werd de afgelopen vijf opeenvolgende jaren erkend als leverancier van Silver-niveau en werd in 2016 en 2017 genomineerd als Boeing-leverancier van het jaar. beugels en kleinere gestempelde onderdelen", zegt Leach. "Maar de afgelopen jaren zijn we geëvolueerd naar complexere assemblages, evenals veel dikkere, grotere onderdelen - tot 60 inch lang - en onderdelen die bedoeld zijn voor primaire structuren." Deze laatste omvatten structurele componenten van de vleugeltip, lange balken met op maat gemaakte lay-ups in verschillende dwarsdoorsneden, evenals romp- en empennage-structuren.
Het bedrijf heeft 150 medewerkers met meer dan 20 ingenieurs. De productie is geconcentreerd in een enkele faciliteit van 67.000 vierkante meter, speciaal gebouwd in 2015 en ontworpen voor een geoptimaliseerde workflow met ruimte om uit te breiden. (Let op:52.500 vierkante meter aan ruimte is al gepland voor toekomstige groei.) "Alles bevindt zich onder één dak", merkt Leach op, "wat de operaties vereenvoudigt." Dit omvat negen stempelpersen met capaciteiten variërend van 30 tot 150 ton en plaatoppervlakken tot 60 inch bij 30 inch. "We installeren een extra pers van 200 ton die eind 2019 volledig operationeel zal zijn", voegt hij eraan toe. ATC heeft 10 CNC-bewerkingsstations die onderdelen tot 12 voet lang kunnen verwerken en waterstraalsnijden voor onderdelen tot 30 voet lang.
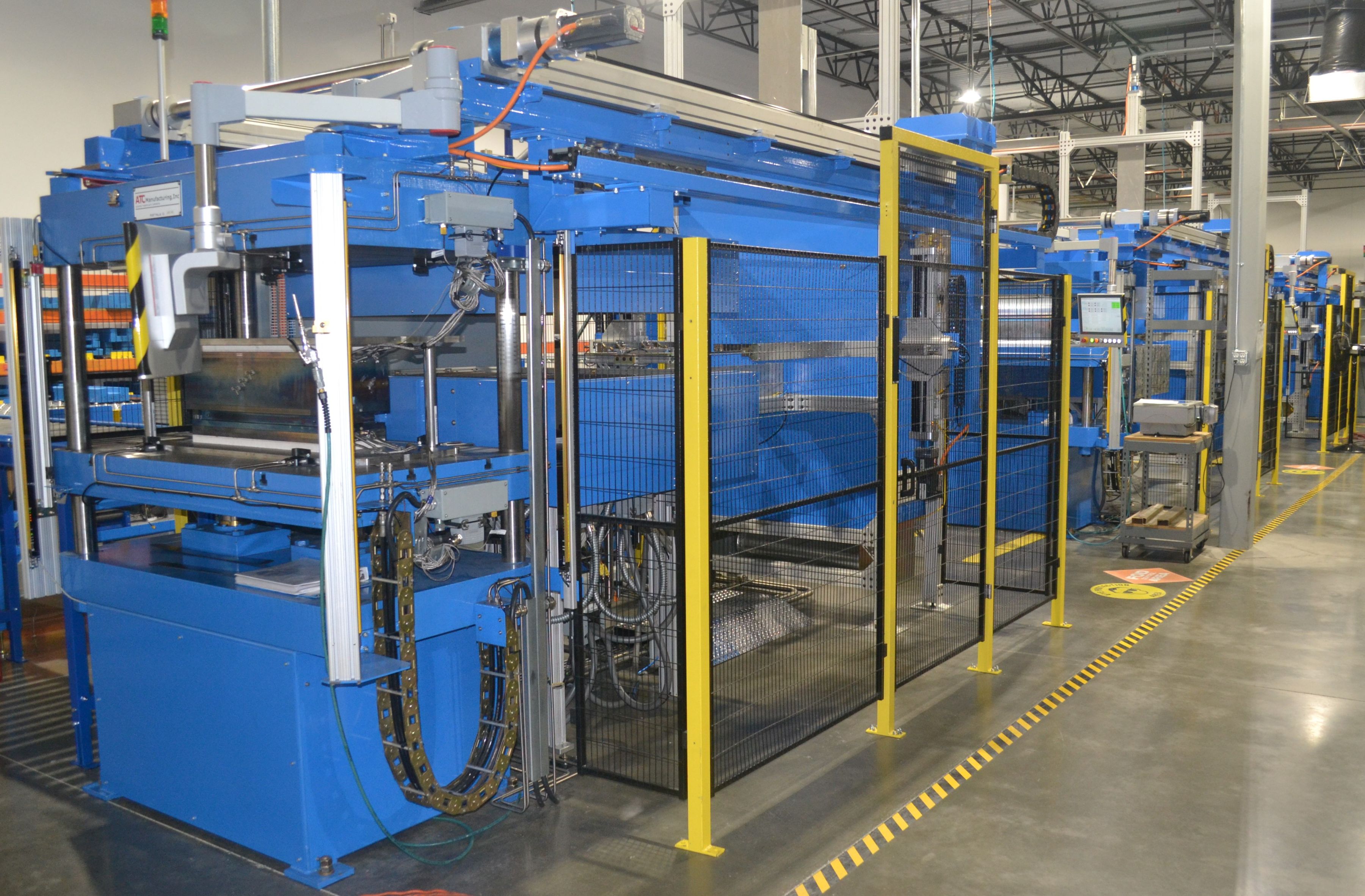
ATC Manufacturing exploiteert 9 stempelpersen, waaronder de hier getoonde 80-tons pers, met capaciteiten tot 150 ton en plaatoppervlakken tot 60 x 30 inch.
BRON | ATC-productie
Niet-destructieve inspectie (NDI) is ook geïntegreerd in de activiteiten en het workflowontwerp van de faciliteit, waaronder vijf C-scan-tanksystemen die puls-echo bieden en transmissietests uitvoeren voor onderdelen met een lengte tot 30 voet. Andere in-house expertise omvat alle oppervlaktevoorbereiding en schilderwerk. "We hebben een zeer efficiënte oppervlaktevoorbereiding ontwikkeld voor thermoplastische composieten, die moeilijk te schilderen en te hechten zijn", zegt Leach, waarbij hij opmerkt dat ATC ook heeft gewerkt aan plasmabehandeling van TPC-onderdelen. Het bedrijf schildert 200.000 onderdelen/jaar en randafdichtingen 70.000 onderdelen per jaar.
“We hebben ook flink geïnvesteerd in onderzoek, zoals het RAPM-programma voor DARPA, en we zijn lid van het ThermoPlastic composites Research Centre (TPRC, Enschede, Nederland)”, vervolgt hij. ATC neemt deel aan de 10-jarige jubileumconferentie van de TPRC, getiteld "Future of Thermoplastic Composites", die op 8 oktober wordt gehouden aan de Universiteit Twente in Nederland. "Corbin Chamberlain, vice-voorzitter van ATC, zal deelnemen aan een panelsessie en we zullen ook structurele onderdelen van de ruimtevaart demonstreren die we hebben gefabriceerd op een tentoonstelling die in samenhang met de conferentie wordt gehouden", zegt Leach.
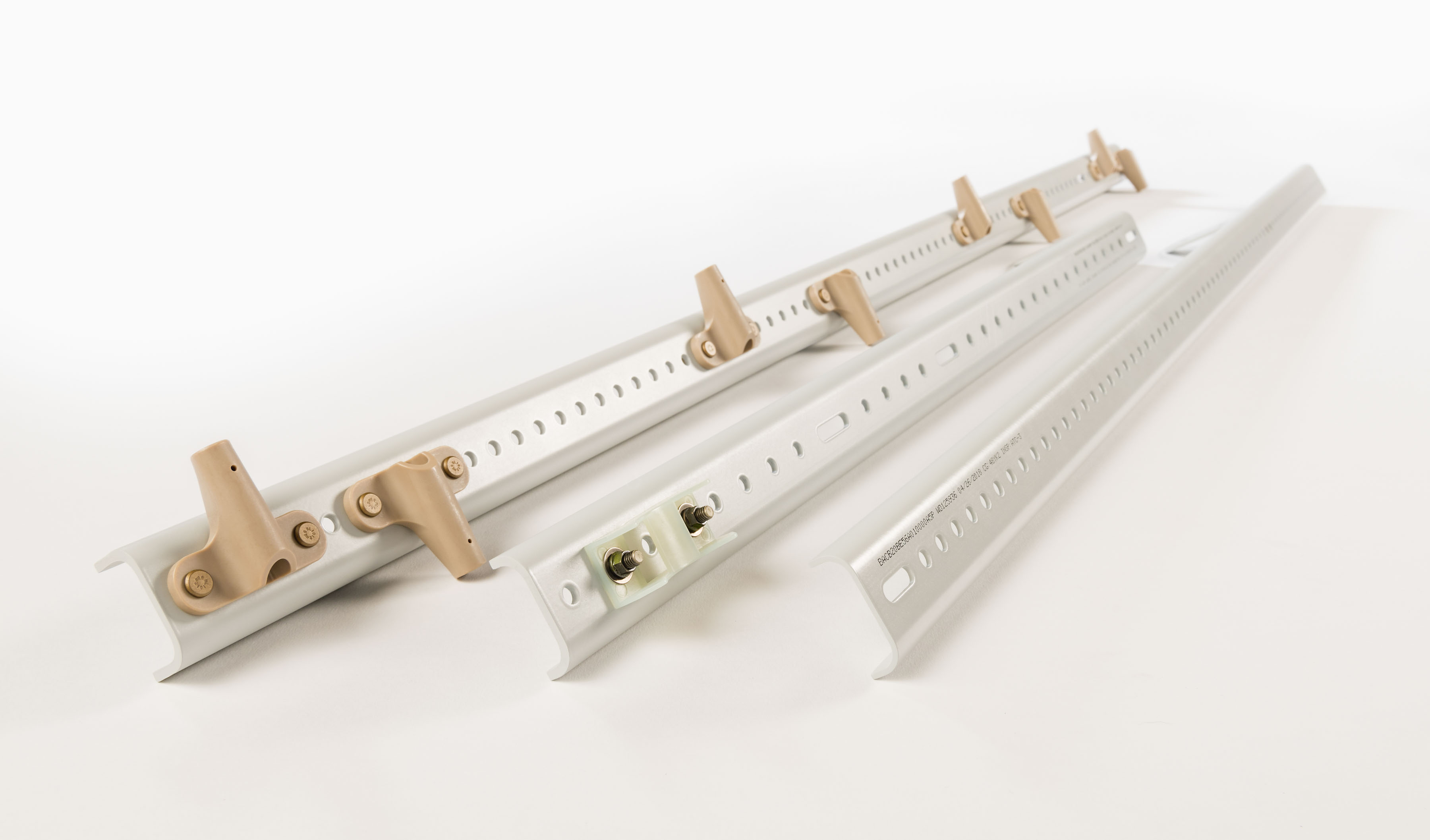
Geverfde kanalen van thermoplastisch composiet met gemonteerde fittingen. BRON | ATC-productie
Stof tot UD-tape, vorming en snelle cyclustijden
Hoewel ATC's productie van TPC-beugels en clips begon met weefselversterkingen, zijn ze nu gemigreerd naar het gebruik van unidirectionele (UD) tape. "Vervolgens evolueerden we naar grotere structurele onderdelen omdat we al goede ervaring hadden opgedaan met het vormen van 3D-onderdelen met UD-tape", legt Leach uit. “Deze onderdelen, die in dikte variëren van 1-2 millimeter tot 6,5 millimeter, moeten passen bij andere structuren. We moeten voldoen aan strakke maattoleranties voor faying-oppervlakken, bijvoorbeeld ± 0,010 inch (0,25 millimeter) profieltolerantie en ± 0,5 graden hoektolerantie.”
Het bedrijf begon toen lange TPC-profielen te ontwikkelen. "We maken onze eigen platte laminaatvoorraad met behulp van continu persen (CCM)", zegt Leach. "We hebben twee CCM-machines voor platte laminaten en een die TPC-prepregs vormt tot een doorlopend 3D-profiel, waardoor kanalen tot 75 voet lang worden geproduceerd."
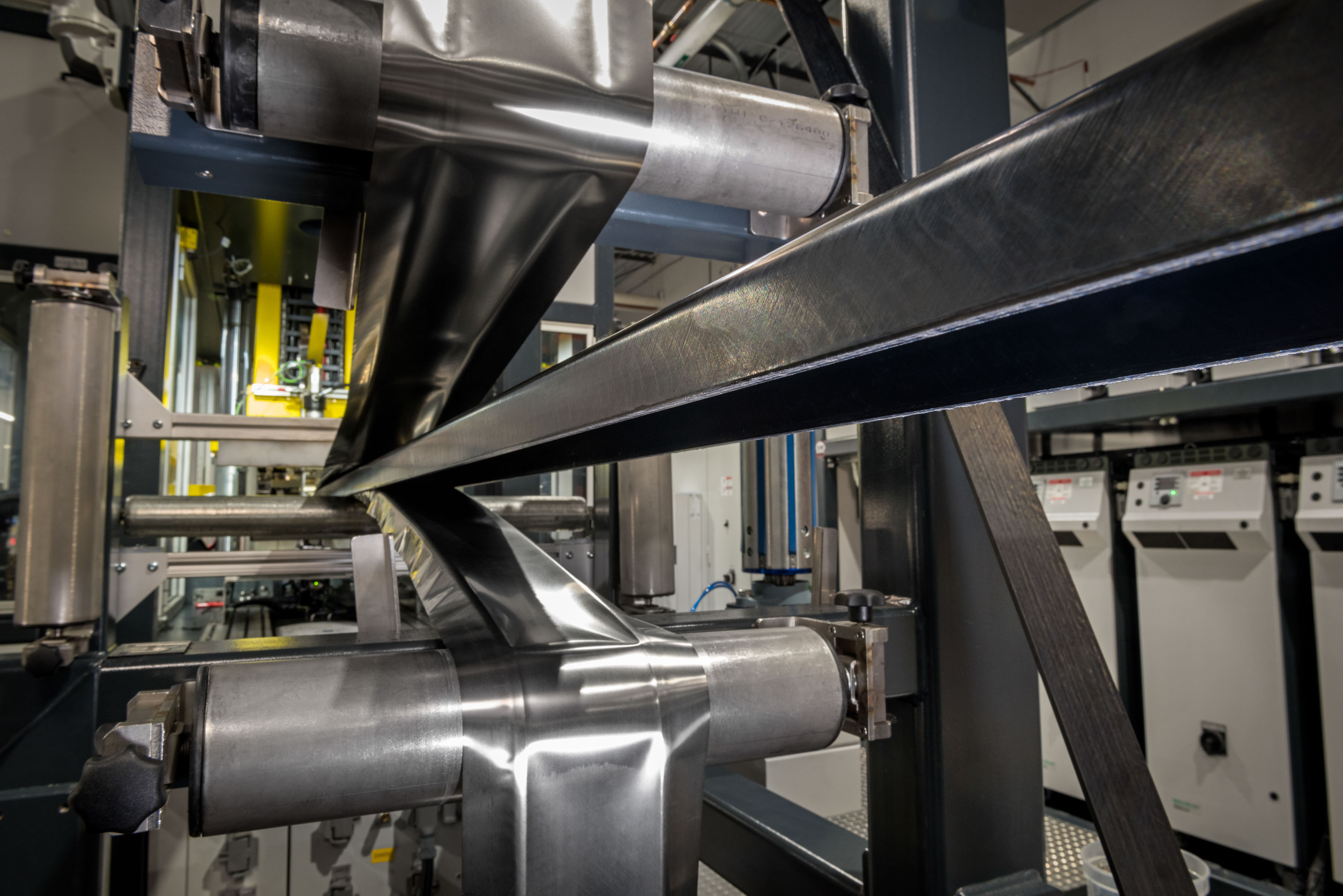
Thermoplastisch composietprofiel dat wordt gevormd met behulp van continu persen (CCM). BRON | ATC-productie
Gevraagd naar de uitdagingen bij het vormen van 3D-profielen en -vormen, legt Trevor McCrea, directeur R&D-engineering van ATC Manufacturing, uit dat bij stoffen "het weefsel zelf een groot deel van de vervorming controleert. Bij UD zijn er verschillende dynamieken. Bijvoorbeeld 90° naar de straal wil uitdunnen of dikker worden, maar dat kan je niet hebben in een constructiedeel. Deze problemen worden erger met complexere vormen. Je hebt ook meer uitdaging in het managen van het proces bij het vormen.”
Het proces managen? "Voor ons is dit heel anders dan vormen in thermoharders, omdat we maar 2 seconden hebben om te vormen", zegt McCrea. "Je kunt veel zonden bedekken in een autoclaafcyclus", voegt hij eraan toe. “Maar we gebruiken zeer snelle vorm- en stempelprocessen zonder die speelruimte. We moeten ook de kristalliniteit beheersen.” Dit komt omdat hoogbelaste vliegtuigstructuren gebruik maken van semikristallijne thermoplastische matrixpolymeren - zoals polyetheretherketon (PEEK), polyetherketonketon (PEKK) en laagsmeltend polyaryletherketon (LM PAEK) - die hun opmerkelijke mechanische eigenschappen en chemische weerstand ontlenen aan de kristallijne structuur die zich ontwikkelt als ze afkoelen. "Je kunt isotherm kristalliseren, wat niet al te moeilijk is voor vlakke platen, maar veel uitdagender wordt met 3D-vormen", zegt McCrea. “De materialen moeten voldoende worden verwarmd om te vormen [let op smelttemperaturen voor deze materialen liggen tussen 300-400 °C] maar dan snel genoeg afgekoeld om heet te worden ontvormd om thermische cycli van de gereedschappen te voorkomen, terwijl vorm, tolerantie, kristalliniteit en oppervlakteafwerking worden beheerd .”
Een van de redenen dat TPC-onderdelen de afgelopen jaren zijn gegroeid, is hun vermogen om echt snelle cyclustijden te bieden. "We hebben ribben gemaakt voor demonstranten van militaire vliegtuigen met een cyclustijd van 5 minuten, en onze gemiddelde cyclustijd is ongeveer 10 minuten", merkt Leach op. "We kunnen de hoge productiesnelheden die momenteel worden nagestreefd door OEM's van vliegtuigen mogelijk maken." Die zeer snelle gemiddelde cyclustijd resulteert eigenlijk in een constant wisselende mix van onderdelen. "We zouden graag maandenlang slechts één onderdeel produceren, maar onze snelheid overtreft die van vliegtuigbouw", zegt McCrea. “We fietsen dus altijd door verschillende delen.” Het grootste deel van de productie van ATC is in één ploeg per dag, 5 dagen per week. "We hebben voldoende capaciteit om aan de verhoogde productie te voldoen", merkt Leach op.
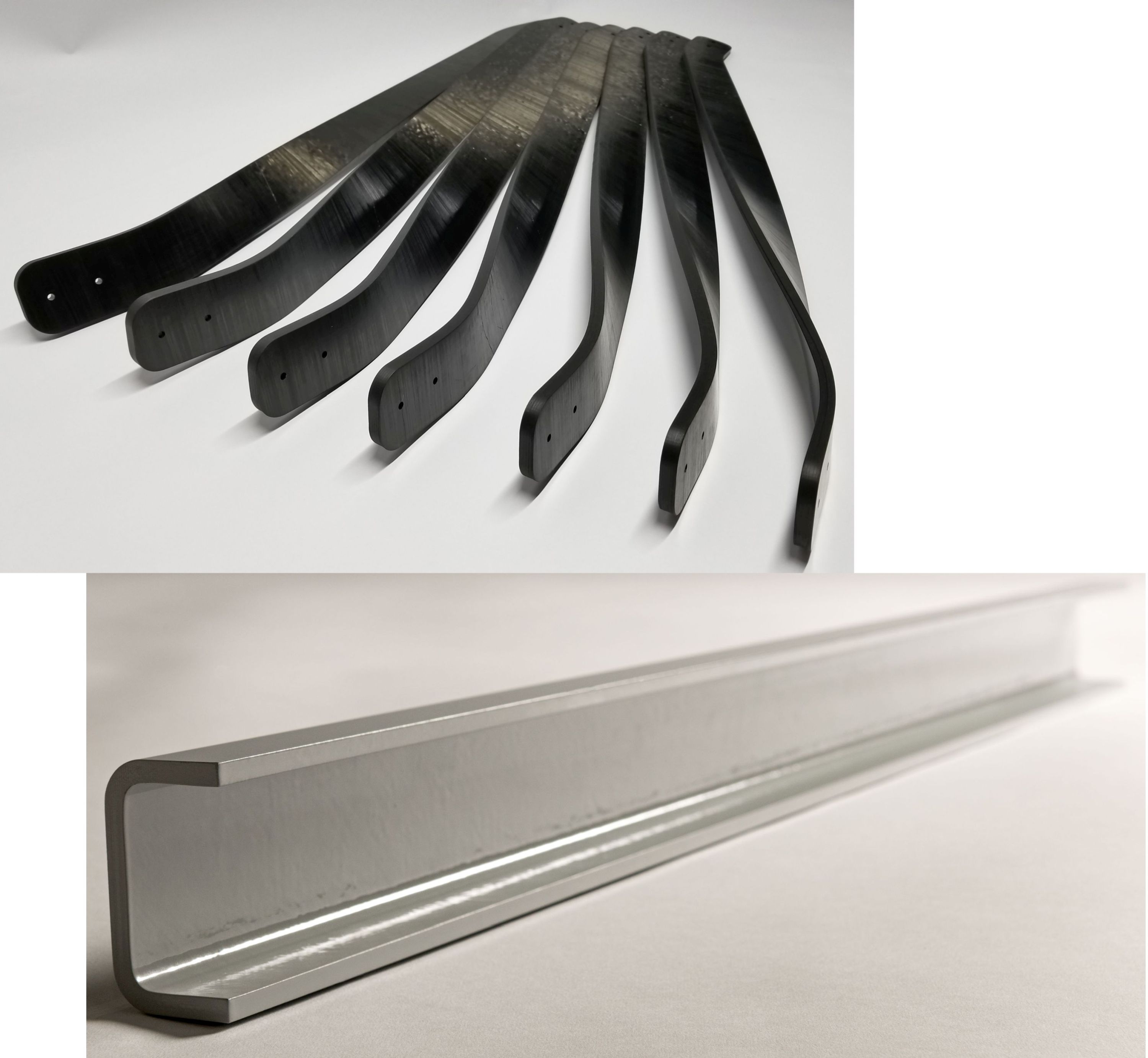
Thermoplastische composieten structurele banden en geverfd profiel. BRON | ATC-productie
Visie voor de toekomst
ATC biedt een aanzienlijke waarde dankzij zijn tien jaar plus TPC-productie-ervaring. "We helpen onze klanten vaak bij het ontwerpen van onderdelen voor productie", zegt Leach. “We zijn vaak onderdelen aan het ombouwen van thermohardend composiet, bijvoorbeeld een fitting van de primaire structuur van de romp die wordt geproduceerd om de oorspronkelijke dikte te behouden. Maar het zou een veel lichter onderdeel kunnen zijn als het oorspronkelijk voor TPC was ontworpen.” Waarom? "Omdat deze semikristallijne TP-matrixmaterialen beter presteren", legt hij uit. “Je hoeft niet te ontwerpen voor microscheurtjes en schadetolerantie zoals je zou doen met een thermohardende matrix, en er is ook veel minder warm/nat knockdown. In PEEK, PEEK of PAEK is er in feite helemaal geen natte knockdown. Er is ook geen hete knock-down tenzij je dicht bij de Tg bent, die doorgaans ≈150°C is. Voor de standaard open-gatcompressietest (OHC) voor schadetolerantie, bijvoorbeeld, waarbij u de sterkte beoordeelt wanneer u het monster van kamertemperatuur naar 120°C brengt, is er nauwelijks sprake van een knockdown.”
"We zullen dunnere onderdelen kunnen ontwerpen en ook veel van het aluminium en titanium kunnen elimineren dat aanwezig is in de huidige eerste generatie ontwerpen voor composieten [zoals de Boeing 787 en Airbus A350 widebody-vliegtuigen]", voegt McCrea toe. "We blijven de vorming van deze materialen bevorderen en dat zal nieuwe toepassingen blijven openen."
Leach gelooft dat dit een aanzienlijke impact zal hebben op toekomstige vliegtuigtoepassingen. "We kijken nu eigenlijk naar onderdelen die je gewoon niet kunt produceren met thermoharders vanwege de eigenschappen en productiesnelheid die worden gevraagd."
Voor meer informatie zal ATC Manufacturing de technische paper 'Cost Effective Thermoplastic Composites in Aerostructures' van de auteurs Corbin Chamberlain, David Leach en Trevor McCrea presenteren op CAMX 2019 in de Thermoplastic Materials and Applications Session, woensdag 25 september om 16:00 uur. in kamer 210C.
Het presenteerde ook een gezamenlijk document met Boeing in een besloten sessie op SAMPE 2019 (4-7 mei, Charlotte, NC, V.S.) getiteld:"Rapid High Performance Molding of Structural Thermoplastic Composite Parts". Zie mijn blog:https://www.compositesworld.com/news/darpa-presents-tff-program-for-rapid-low-cost-composites-to-replace-metals-in-small-parts-for-defense- toepassingen
Hars
- Hoe 3D-printen de ruimtevaart veranderde
- Covestro verhoogt investeringen in thermoplastische composieten
- Collins Aerospace neemt thermoplastische onderdelenfabrikant Dutch Thermoplastic Components over
- Thermoplastische composieten bij Oribi Composites:CW Trending, aflevering 4
- Problemen oplossen met thermovormen van thermoplastische composieten
- Thermoplastische composieten:structurele bumperbeugel
- Toray Advanced Composites breidt mogelijkheden voor thermoplastische composieten uit
- ACMA lanceert Thermoplastic Composites Conference 2020-programma
- Thermoplastische composieten:schilderachtig uitzicht
- Thermoplastische composieten lassen
- Consortium thermoplastische composieten streeft naar productie in hoog volume voor Automotive en Aerospace