Mobiele susceptors gebruiken om thermoplastisch inductielassen te innoveren
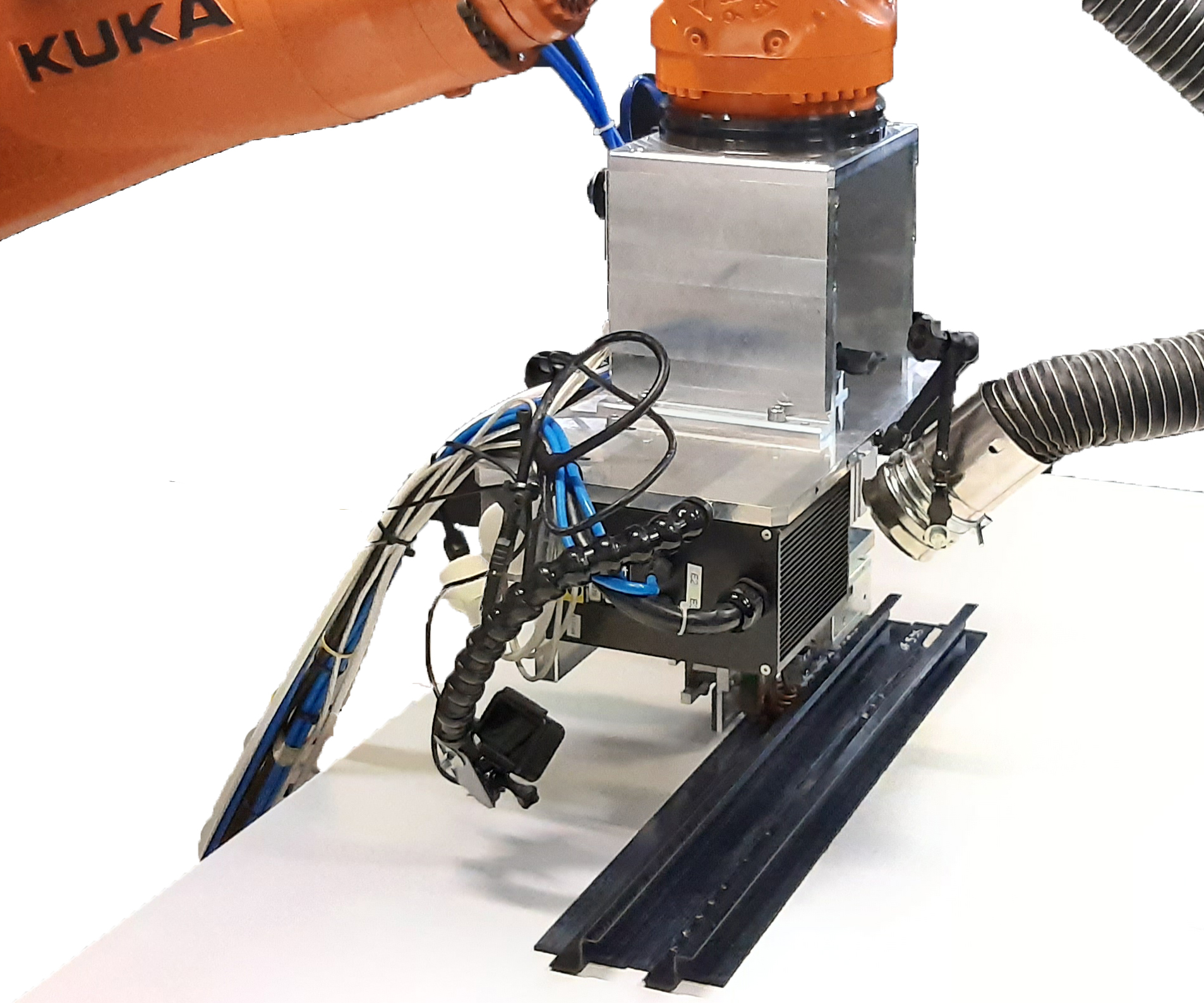
De Institut de Soudure Group (IS Groupe, Villepinte, Frankrijk) - letterlijk "het lasinstituut" van Frankrijk - heeft meer dan 100 jaar ervaring in het lassen van metalen en vestigt zich nu als leider in het lassen van thermoplastische composieten. Zoals gerapporteerd in CW ’s 2018-feature “Lassen van thermoplastische composieten”, IS Groupe en zijn composietmerk Composite Integrity ontwikkelde het "dynamische inductielassen"-proces dat wordt gebruikt om koolstofvezel (CF)/polyetherketonketon (PEKK) unidirectionele (UD) tapestringers en romphuiden te verbinden in het "Arches TP"-demonstratieproject met Airbus Tier 1-leverancier STELIA Aerospace (Toulouse, Frankrijk) , die werd onthuld op de Paris Air Show 2017.
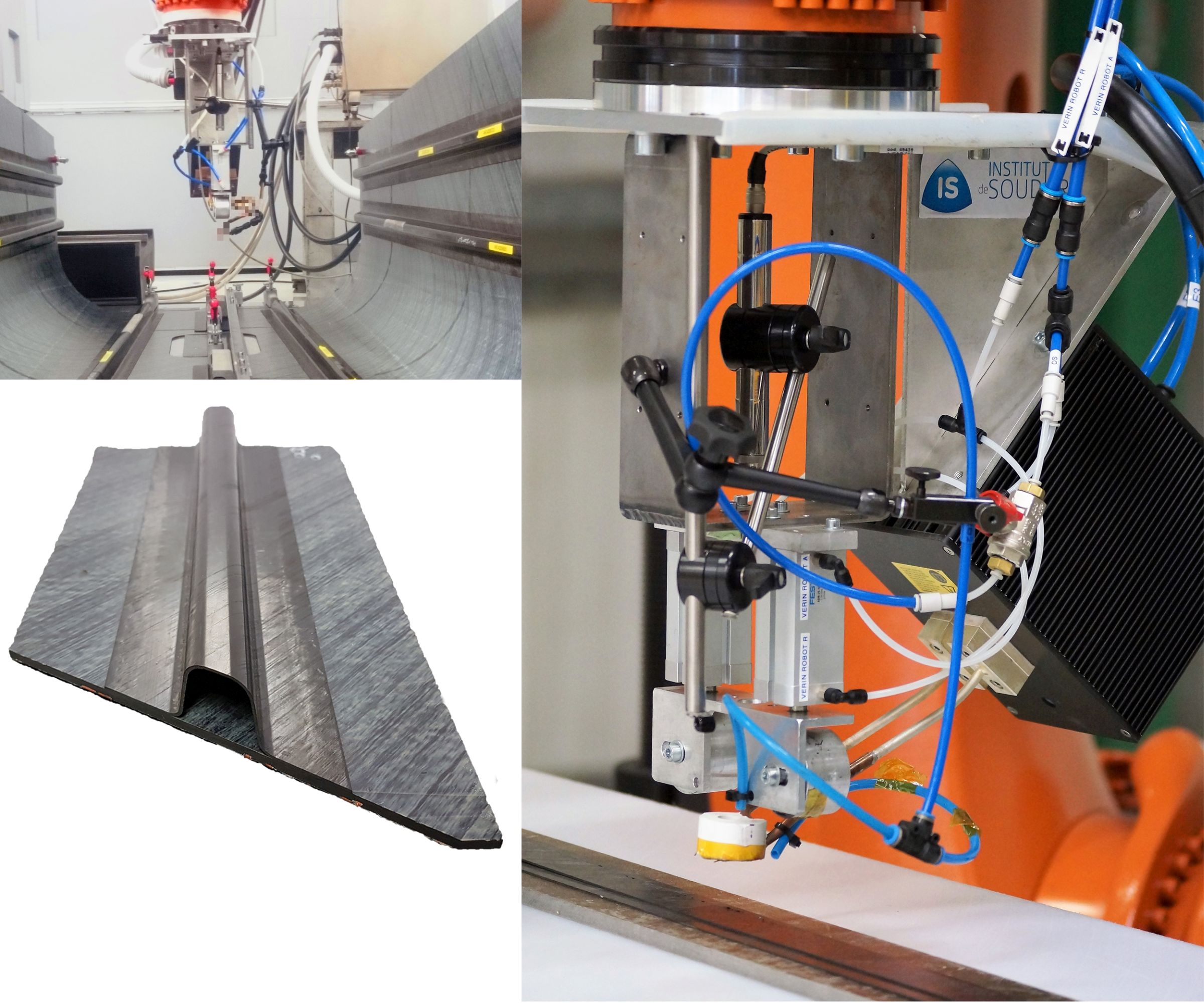
"Dit was het begin van onze ontwikkeling met inductielassen voor structurele onderdelen voor de luchtvaart", legt Jérôme Raynal uit, directeur luchtvaart &composieten van IS Groupe. "Hoewel het door ons ontwikkelde dynamische inductielasproces succesvol was, had het enkele beperkingen met betrekking tot de prestaties in de straal van de gelijmde stringer en globale verwarming van het paneel omdat er geen susceptor op de interface is."
Een susceptor is een materiaal dat tussen de twee aanhechtingen van een gelaste thermoplastische composietverbinding wordt geplaatst die wordt verwarmd door de inductiespoel in de laskop. De susceptor kan elektrisch geleidend zijn voor weerstandsverhitting of magnetisch voor hystereseverhitting, waarbij de matrix smelt op het lasinterface die gelijktijdig samengedrukt wordt om een smeltgebonden verbinding met zeer hoge sterkte te creëren. Zoals uitgelegd in het artikel van januari 2000, "Ontwerp van een resistieve susceptor voor uniforme verwarming tijdens inductiebinding van composieten" door Bruce Fink, Shridhar Yarlagadda en John W. (Jack) Gillespie, waren susceptors die worden gebruikt in inductiegelaste thermoplastische composieten aanvankelijk een metaal scherm of gaas, soms geïmpregneerd met polymeer.
IS Groupe was van mening dat de aanvankelijke problemen die het tegenkwam, konden worden opgelost met meer ontwikkeling. "We begonnen aan een nieuwe ronde van interne reflectie", zegt Raynal. Dit omvatte besprekingen met leverancier van thermoplastische (TP) materialen Arkema (Colombes, Frankrijk), die overgingen tot een ontwikkelingspartnerschap. "We hebben nu samen met Arkema nieuwe technologie ontwikkeld en gepatenteerd, genaamd Innovative Solution for Welding (ISW)", voegt Raynal toe.
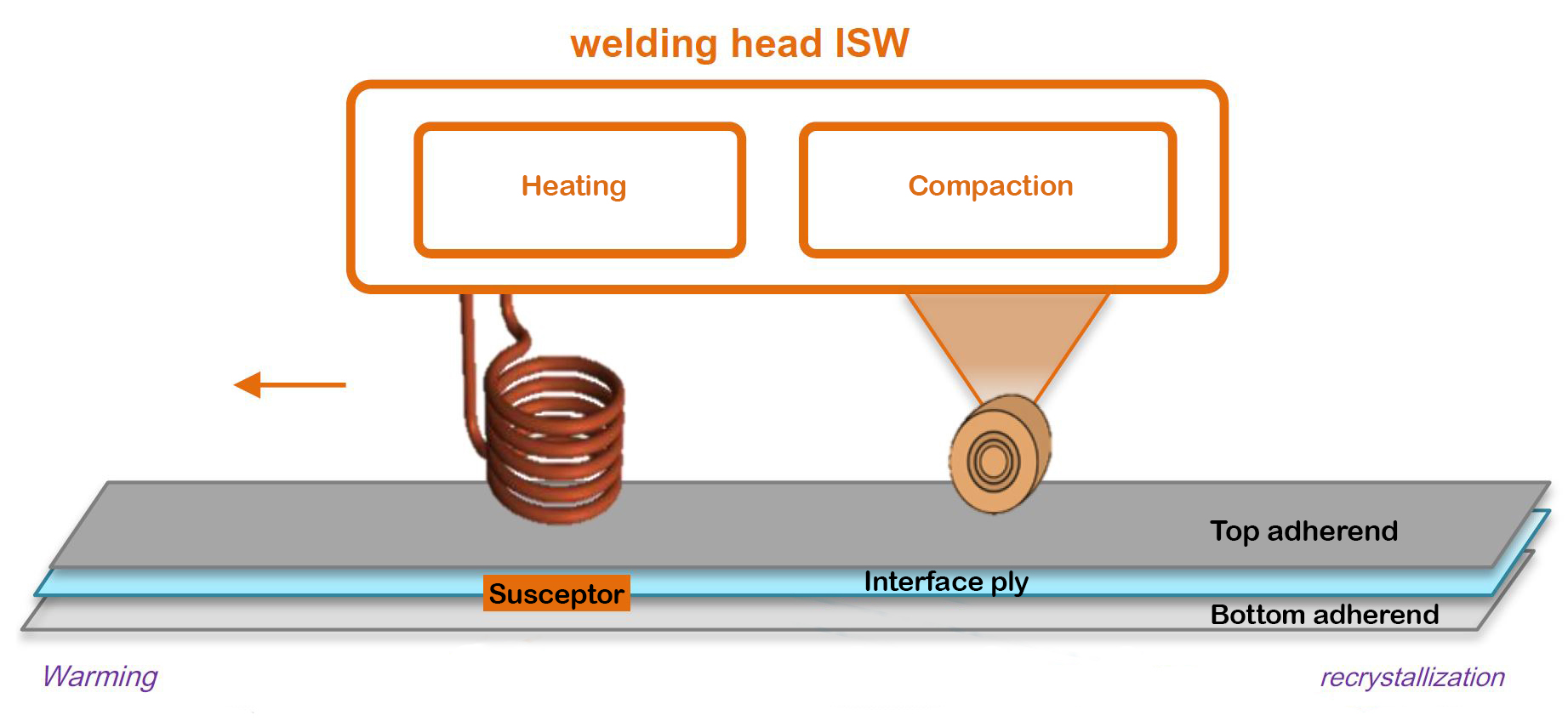
ISW-basisprincipes
"De basis van ISW is om een susceptor te gebruiken om de lasinterface te verwarmen, maar dit is een mobiele susceptor die is gekoppeld aan de laskop", legt Raynal uit. "De susceptor stelt ons in staat om de verwarmingszone bij de las perfect te lokaliseren, maar de laskop met susceptor beweegt zodat er niets in de interface achterblijft dat de eigenschappen van de gelaste structuur verstoort." In vroege iteraties van inductielassen bleven metalen gaassusceptors in de las, maar dit werd als ongewenst beschouwd. Meer recente technieken hebben susceptors kunnen elimineren omdat de koolstofvezel in gewone luchtvaartlaminaten elektrisch geleidend is. Dit heeft ook het gebruik van koolstofvezelmaterialen als susceptors mogelijk gemaakt.
Een ander onderdeel van de ISW-oplossing is het gebruik van een pure TP-matrix of laag vezelvolume op de lasinterface om de harsstroom te vergroten. De smelttemperatuur en viscositeit van deze interfacelaag kunnen worden aangepast en kunnen ook worden gefunctionaliseerd om elektrische geleidbaarheid of isolatie te bieden om galvanische corrosie te voorkomen, bijvoorbeeld tussen koolstofvezel en aluminium of staal.
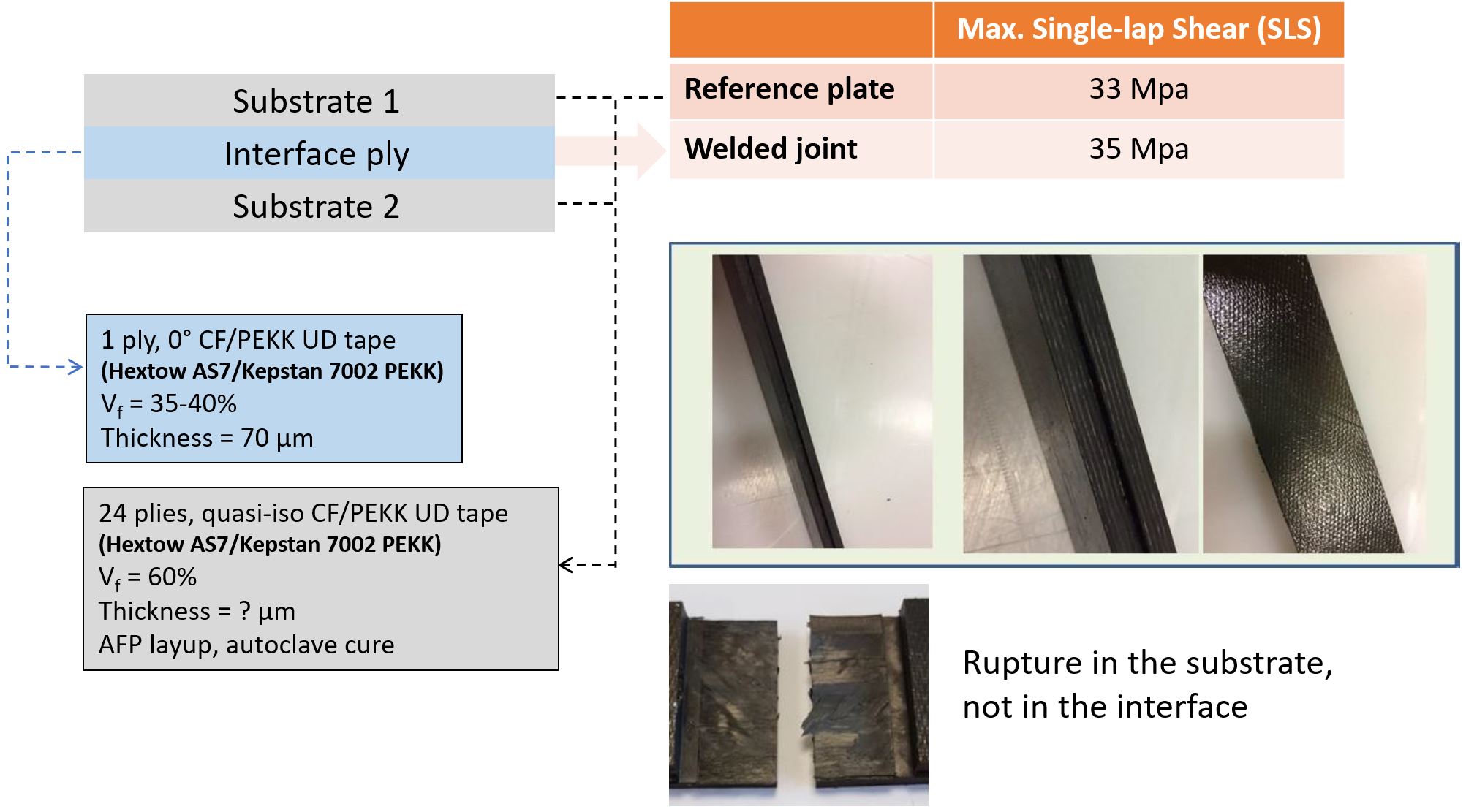
ISW-resultaten
"We eindigen met een gezamenlijke coëfficiënt van 80-90%", zegt Raynal. De verbindingscoëfficiënt komt overeen met de sterkte van de las en wordt gebruikt bij metaal, kunststoffen en composieten. "Bij het testen op afschuifkrachten in één ronde van twee voorgeconsolideerde platen die aan elkaar zijn gelast met ISW, hebben we 80-90% van de eigenschappen van de ongelaste, in de autoclaaf geconsolideerde referentieplaten bereikt." Bij deze proeven werd gebruik gemaakt van UD-tape gemaakt met Hextow AS7-koolstofvezel (Hexcel, Stamford, Conn., VS) en Arkema Kepstan 7002 PEKK.
Raynal zegt dat ISW kan worden gebruikt om elk soort matrix te lassen:PE, PA, PEKK, PEEK, evenals met koolstof-, glas- of aramidevezelversterkte thermoplastische composieten. "We hebben ook aangetoond dat het geen probleem is om componenten te lassen met kopergaas voor blikseminslagbescherming (LSP), wat essentieel is voor de productie van aerostructuren", voegt hij eraan toe. ISW is ontworpen om volledig geautomatiseerd te worden met de laskop bevestigd aan een 6-assige robotarm.
Temperatuurregeling
Zoals uitgelegd in het Kirk/Yarlagadda/Gillespie-document hierboven, is een veelvoorkomend probleem bij metalen susceptors die aan een magnetisch veld worden onderworpen, de resulterende niet-uniforme temperatuurverdeling in het onderdeel dat wordt gelast. "We beheersen dit door een susceptor te gebruiken om alleen de lasinterface te smelten", legt Raynal uit. “We nemen de temperatuur waar met een laserpyrometer die de rand van de susceptor vanaf de zijkant meet. We weten dus precies de temperatuur op de interface. We gebruiken ook koeling om de temperatuur te beheersen en te zorgen voor voldoende kristallisatie in het thermoplastische materiaal door de hele las heen.”
STELIA stringer-skin lasproeven
De Tier 1-leverancier van Airbus, STELIA (Toulouse, Frankrijk), is een van de eerste klanten voor deze ontwikkeling van inductielassen. IS Groupe en Arkema hebben een specifieke studie uitgevoerd voor STELIA om een 7-laags CF/PEKK stringer te lassen op een 14-laags huid met kopergaas voor blikseminslagbescherming (LSP). Het uiteindelijke doel is het lassen van constructies van 30 meter lang, met rechte en dubbelgekromde secties. De componenten zijn gemaakt met 194 gsm UD-tape bestaande uit Tenax HST45 koolstofvezel (Teijin, Osaka, Japan) en Kepstan 7002 PEKK. STELIA specificeerde een homogene las met een mechanische prestatie>85% van het autoclaaf-geconsolideerde referentiemateriaal en zonder thermische of mechanische aantasting van de eigenschappen van de lijmverbindingen. Het vroeg ook om een proces dat robuust is met betrekking tot verandering in de dikte van het aanhangsel. Chemische en eigenschapstests op de gelaste componenten werden uitgevoerd door IS Groupe.
IS Groupe en Arkema waren in staat om aan de eisen van STELIA te voldoen en bereikten>85% van de prestaties op het gebied van single lap shear (SLS) en interlaminaire shear strength (ILSS) in vergelijking met de autoclaaf-geconsolideerde referentielaminaten. Er was geen uitpakken of degradatie in de componentlaminaten of LSP-gaas. Het enige gebied waar ze tekort kwamen, is snelheid. STELIA verzocht om een lassnelheid ≥ 1 meter/minuut. "Momenteel zitten we op 0,3 meter (10 inch) per minuut", geeft Raynal toe, "maar we blijven werken aan die doelsnelheid." Zit er een limiet in de dikte van de ondergrond die kan worden gelast? "We kunnen diktes lassen die typerend zijn voor ruimtevaartconstructies en hebben componenten van 5 millimeter dik gelast op een substraat van 5 millimeter."
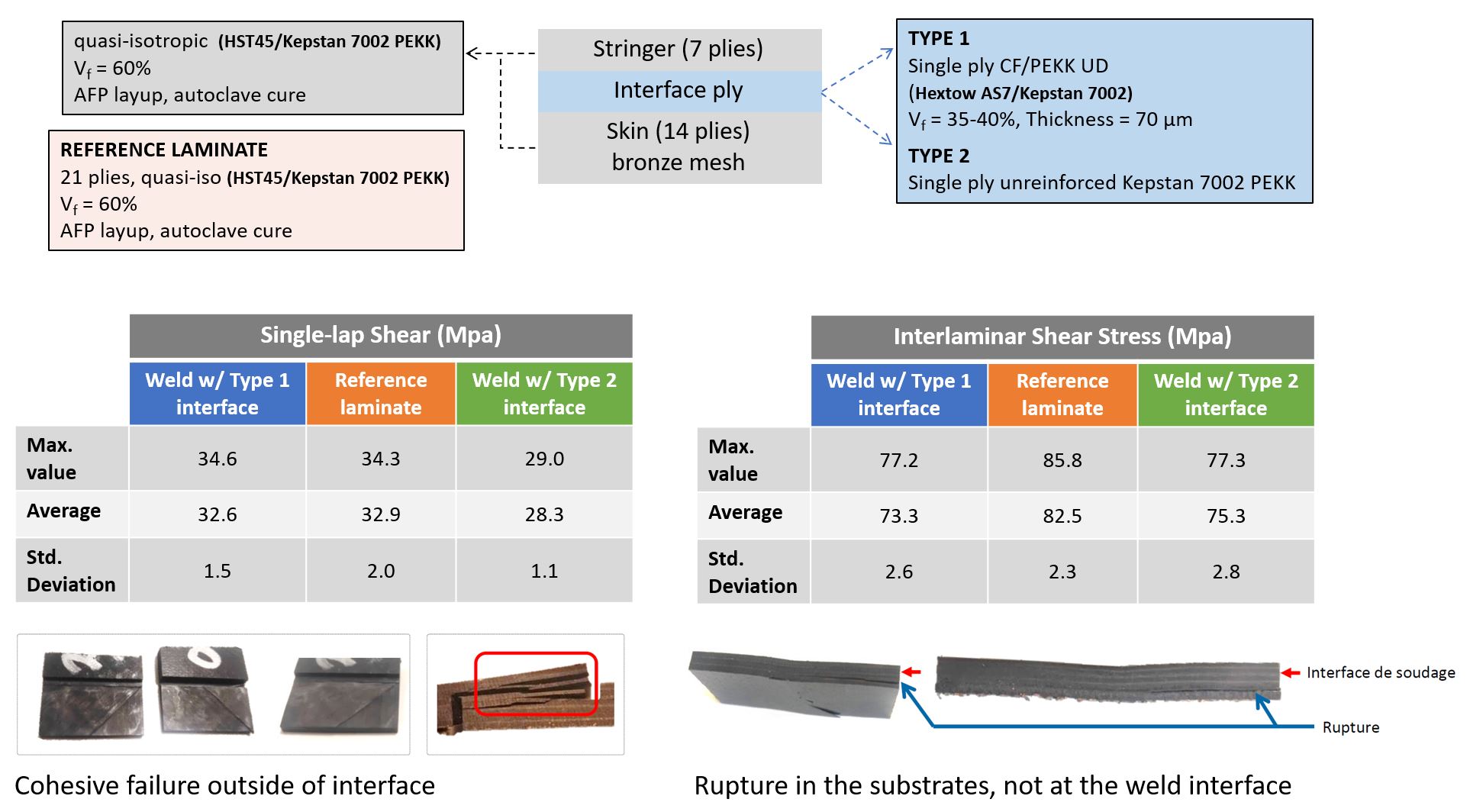
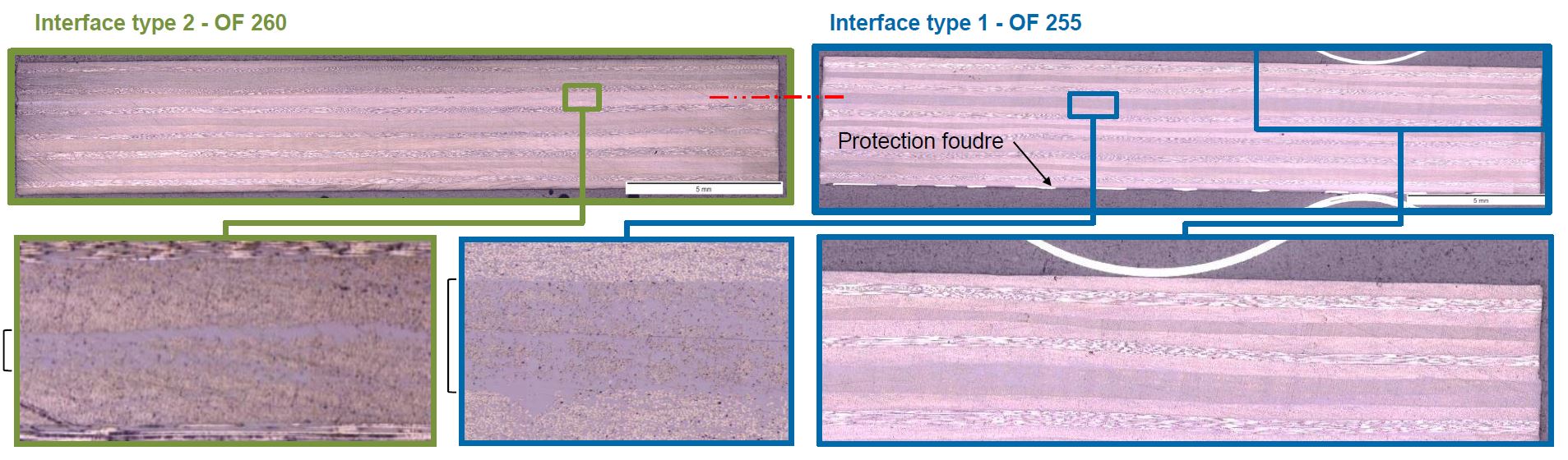
Arkema-partnerschap, kansen en uitdagingen
Waarom werken met Arkema? “Omdat er een relatie is tussen de techniek en de materialen”, legt Raynal uit. “Zo maken de materialen op het grensvlak en hun volumefractie het verschil. We zijn specialisten op het gebied van proces, maar we moesten nauw samenwerken met een partner voor materialen. Deze gezamenlijke ontwikkeling was nodig om de lastechniek volledig te optimaliseren.”
IS Groupe en Arkema zijn mede-eigenaren van de ISW-technologie en hebben deze technologie beschermd door een solide octrooiportfolio die al vijf Franse en internationale octrooiaanvragen omvat. ISW kan worden gebruikt met elke thermoplastische composietmatrix en IS Groupe demonstreert de technologie door middel van programma's die het heeft met bedrijven in Europa en de VS, waaronder Latécoère (Toulouse, Frankrijk), en Collins Aerospace Aerostructures (Chula Vista, Californië, V.S.).
Voor Arkema ligt de focus op PEKK, zegt Raynal, en wijst op de strategische alliantie van 2018 met Hexcel om CF/thermoplastische tapes voor toekomstige vliegtuigen te ontwikkelen, met de nadruk op lagere kosten en hogere productiesnelheden voor zijn klanten. Als onderdeel van dit partnerschap wordt in Frankrijk een gezamenlijk R&D-lab opgericht.
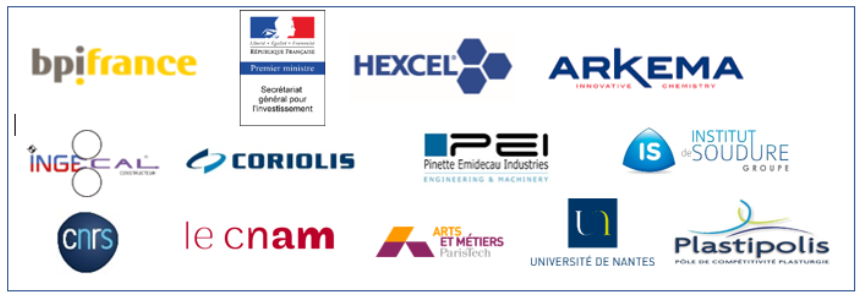
De 13,5 miljoen euro, 48 maanden sterk geautomatiseerde geïntegreerde composieten voor het uitvoeren van aanpasbare structuren (HAICoPAS)-project is een voortzetting van de strategische alliantie Arkema-Hexcel. Deze volledig Franse samenwerking omvat IS Groupe, evenals machineontwerper Ingecal (Chassieu), Coriolis Composites (Quéven), Pinette Emidecau Industries (Chalon Sur Saone) en een consortium van universitaire laboratoria. HAICoPAS zal het ontwerp en de fabricage van materialen voor de productie van composietonderdelen optimaliseren om tegen hoge snelheid concurrerende kosten te realiseren. Het heeft ook tot doel een productievere technologie te ontwikkelen voor het plaatsen/opleggen van composietmaterialen en een nieuw systeem voor het assembleren van definitieve onderdelen door middel van lassen met online kwaliteitscontrole.
Gerichte toepassingen zijn onder meer primaire constructies van vliegtuigen, structurele onderdelen voor de auto-industrie en pijpleidingen voor de olie- en gasindustrie. De voordelen van recycleerbaarheid en duurzaamheid van thermoplastische materialen zijn ook belangrijk voor deze markten en zullen worden aangetoond en gekwantificeerd in HAICoPAS.
“Een van de voordelen die we met ISW kunnen bieden, is een reductie van meer dan 50% in elektrisch vermogen vereist versus ons dynamische inductielasproces uit 2017”, benadrukt Raynal. “Bij conventionele inductie heb je een hoog vermogen nodig om het oppervlak te verwarmen. Maar met een susceptor op het grensvlak is het oppervlak dat je verwarmt veel kleiner, waardoor er veel minder energie nodig is.” Hij merkt op dat dit ook helpt bij het vermijden van decompactie in de straal van stringers. “Als je te veel verwarmt, kun je het materiaal in de radius zachter maken en de vezels hier laten bewegen. We moeten dus alleen de contactzone voor de gelaste substraten perfect verwarmen zonder de straal te verwarmen. Met ISW is dit geen probleem.”
Er zijn echter nog steeds thermische problemen. "Met platte vormen is thermische controle eenvoudig, maar het wordt een grotere uitdaging naarmate de vormen complexer worden", zegt Raynal. “Voor 2020 is het hoofddoel om de ontwikkeling en het lassen van stringers op huid op representatieve schaal voort te zetten en te realiseren. Onze focus ligt ook op het introduceren van de technologie in nieuwe ontwikkelingsprogramma's voor vliegtuigen."
Zie Composite Integrity op JEC World 2020, hal 5, stand N89 voor meer informatie.
Hars
- Top 5 voordelen van inductielassen
- C# met behulp van
- Een inleiding tot het ultrasoon lassen van kunststoffen
- Covestro verhoogt investeringen in thermoplastische composieten
- Grafeenversterkte thermoplastische masterbatches gelanceerd
- Solvay breidt capaciteit thermoplastisch composiet uit
- Epoxyhars gebruiken met artwork
- Thermoplastische composieten bij Oribi Composites:CW Trending, aflevering 4
- Thermoplastische composieten lassen
- Wat gemeenten missen als ze geen gebruik maken van mobiele inspecties
- Voorkomen van lasproblemen en defecten door het gebruik van geverifieerde metalen