Bewijs van LM PAEK-lassen voor multifunctionele rompdemonstrator
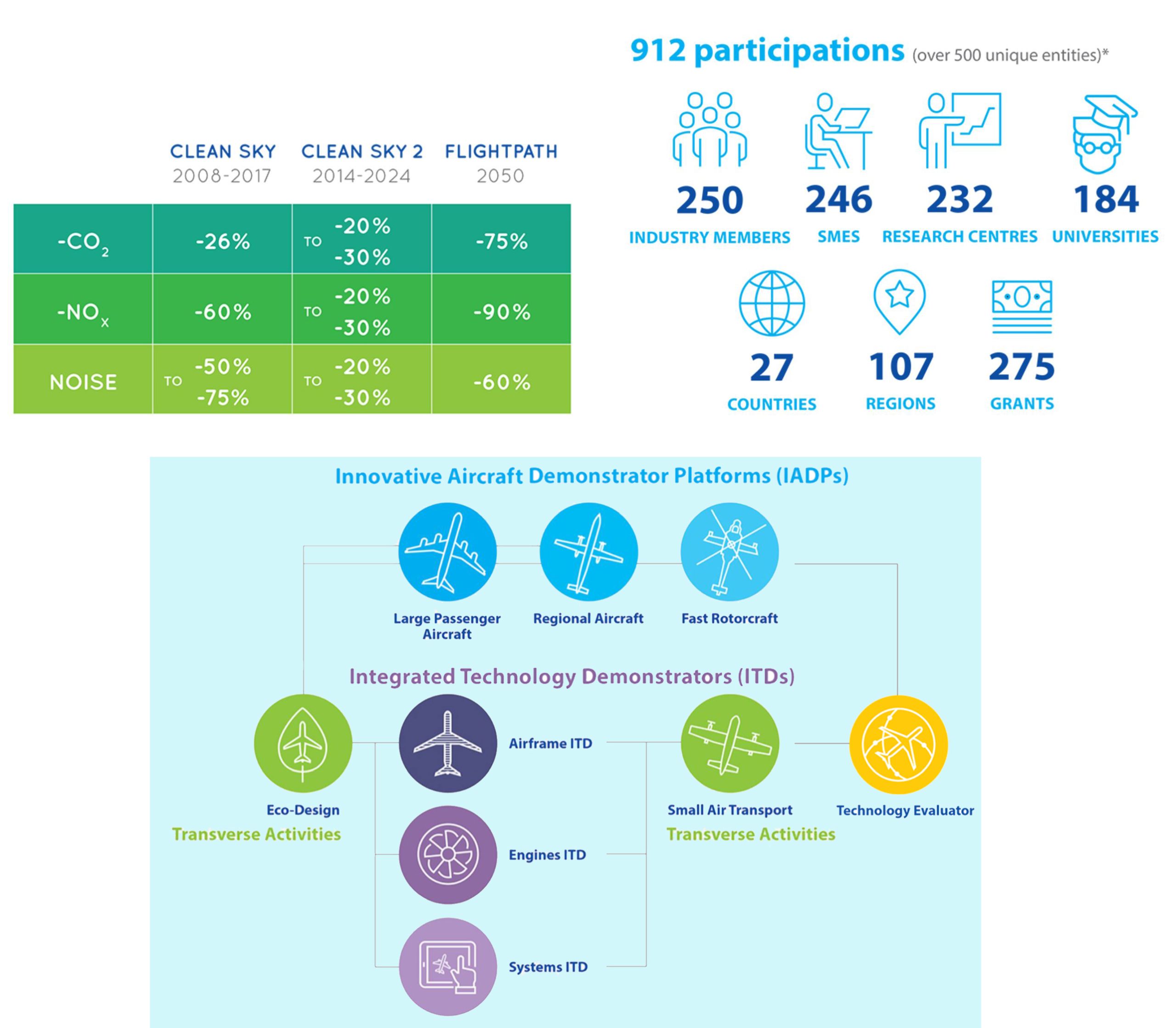
Dit type luchtvaartonderzoek begon met het Kaderprogramma (KP) van de Europese Commissie voor O&O-financiering, dat zich uitstrekt van KP2 (1987-1991) tot KP7 (2007-2013). Deze programma's hebben substantieel bijgedragen aan het rijpen van een breed scala aan technologieën tot Technology Readiness Level (TRL) 6 en implementatie in vliegtuigen zoals de Airbus A350.
Een van de verschillen in Clean Sky 2 is de organisatie rond grote demonstranten. De MFFD is een van de drie volledige rompsecties die worden geproduceerd binnen het Large Passenger Aircraft (LPA) Innovative Aircraft Demonstrator Platform (IADP) (zie blauwe tekst bovenaan het blauwe vierkant in de infographic hierboven) . Binnen de LPA IAPD zijn er drie platforms. De MFFD bevindt zich in Platform 2 "Innovative Physical Integration Cabin-System-Structure", met twee andere grote demonstrators.
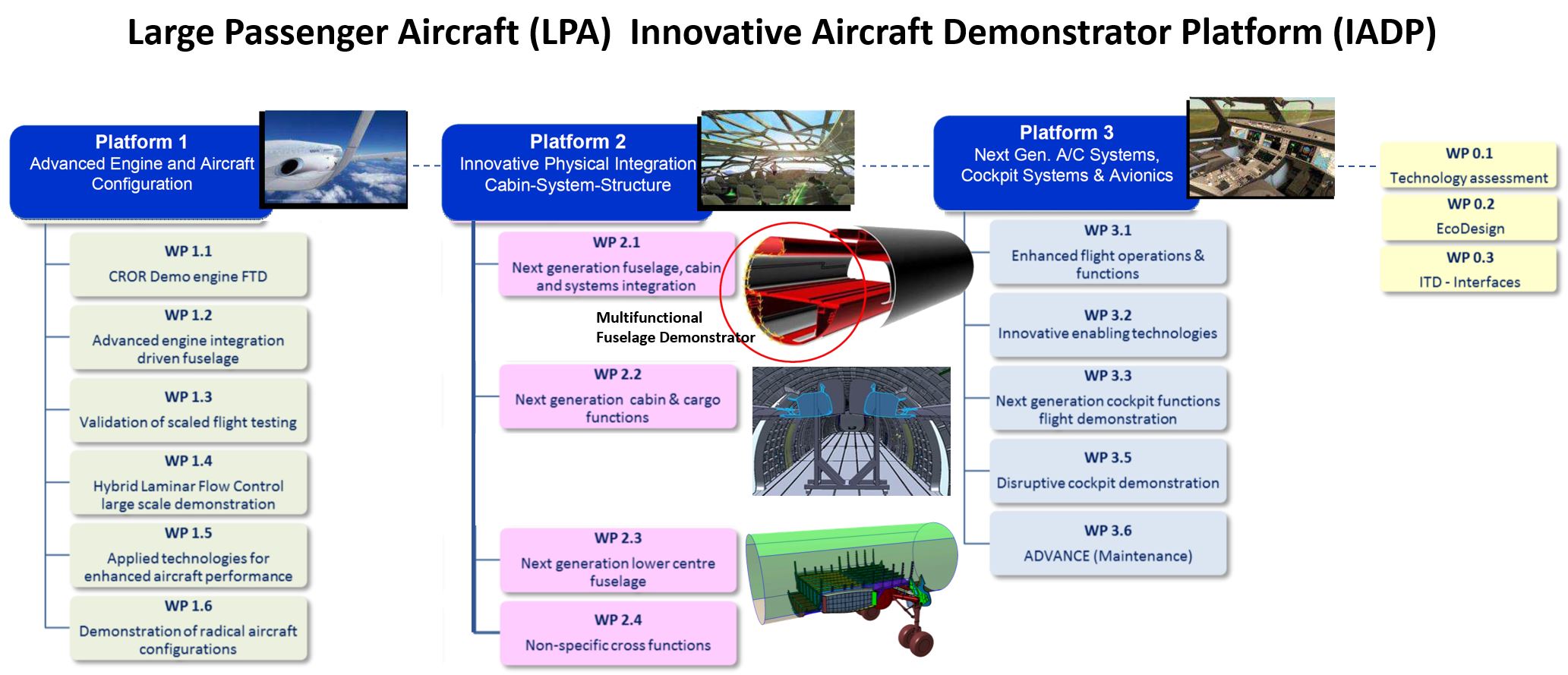
Om te begrijpen wat dit betekent, ga ik terug naar iets dat ingenieurs van Airbus Airframe Research &Technology (R&T) uit Getafe, Spanje, me vertelden toen ik in 2015 onderzoek deed naar multifunctionele composieten. Ze zeiden in wezen:"We willen niet langer de duplicatie en verspilling van het maken van een externe structurele cilinder en een interne cilinder; we willen het structurele casco integreren met de cabinesystemen.” Ik had moeite om te visualiseren wat dit betekende - totdat ik een schets van de MFFD zag.
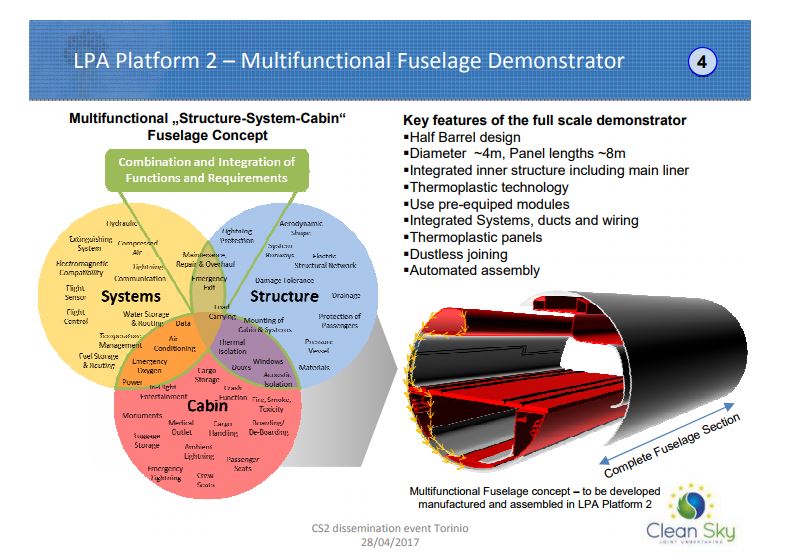
BRON | Verspreiding van Clean Sky 2 (CS2) en "Demonstrators van thermoplastisch composiet — EU-routekaart voor toekomstige casco's".
"Modulariteit, integratie en het creëren van gemeenschappelijke platforms zijn de sleutelwoorden", zegt Ralf Herrmann, Airframe R&T Typische romp bij Airbus Operations GmbH (Bremen, Duitsland) en leider van het MFFD-programma. Ik citeer hier van de MFFD-pagina op de Clean Sky 2-website:
Herrmann:"We weten al lang dat de voordelen van gewichtsvermindering en het verlagen van terugkerende kosten in de vliegtuigproductie - bij het gebruik van thermoplastische composieten — kan alleen worden bereikt door de integratie van meerdere disciplines. Dit betekent dat alleen focussen op de structuur kunnen niet het volledige voordeel van composiettechnologie bereiken.”
De veelzijdigheid van thermoplasten moet worden toegepast in combinatie met een ontwerpaanpak, volgens Clean Sky 2 projectmedewerker Paolo Trinchieri:"Het is noodzakelijk om de kunstmatige functiescheiding te verwijderen in de pre-designfase van het vliegtuig en om vanaf het begin een hoge productiesnelheid van vliegtuigbouw, assemblage en installatie te plannen.”
Herrmann was eerder de projectmanager voor het FP7-project MAAXIMUS (More Affordable Aircraft structure through eXtended, Integrated, &Mature nUmerical Sizing). MAAXIMUS, dat van april 2008 tot september 2016 liep, omvatte 60 partners en was bedoeld om de snelle ontwikkeling en de eerste keer juiste validatie te demonstreren - door virtuele en fysieke enablers gelijktijdig te laten rijpen - van een sterk geoptimaliseerde composietromp om 50% reductie in montagetijd van grote rompdelen, 10% verlaging van de terugkerende kosten, 10% lager structureel gewicht en een 20% kortere ontwikkelingscyclus. De doelstellingen van de MFFD kunnen worden gezien als een uitbreiding:
- Maak productiesnelheden van 70-100 vliegtuigen/maand mogelijk
- Verminder het gewicht van de romp met 1000 kg
- Verlaag de terugkerende kosten met 20%.
Een belangrijke factor is stofvrij deelnemen (geen gaten, geen bevestigingsmiddelen) via gelaste componenten van thermoplastisch composiet. Herrmann legt uit dat de huidige sequentiële benadering van vliegtuigbouw - waarbij de rompstructuur redelijk compleet moet zijn voordat systemen plus cabine- en vrachtvoorzieningen kunnen worden geïnstalleerd - tijdrovend en "foutgevoelig" is. In plaats daarvan streeft MFFD naar vooraf uitgeruste, sterk geïntegreerde structurele elementen en systeemmodules die vrij vroeg kunnen worden geïnstalleerd, lang voor de uiteindelijke montage.
Wijzigen in langsvoegen en LM PAEK
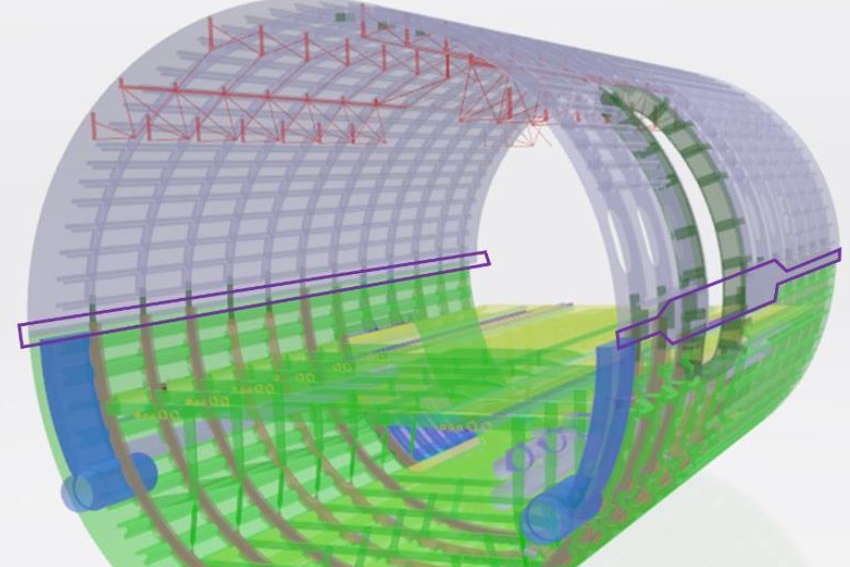
MFFD-projectactiviteiten zijn gestart in 2017. Jaarlijks is er minimaal één call for proposals (CFP) waarin projectleiders onderwerpen schetsen die verdere ontwikkeling behoeven. Zoals te zien is in de onderstaande afbeelding, was het ontwerp van de schuine verbinding dat wordt getoond in CFP08 (april 2018) tegen CFP09 (september 2018) veranderd in een langsnaad.
"De schuine verbinding leverde problemen op met betrekking tot de toegankelijkheid en bevestiging van vloerconstructies waarvan we ons realiseerden dat ze binnen de gegeven tijdsperiode moeilijk te overwinnen zouden zijn", legt Herrmann uit. “Dus hebben we besloten om terug te vallen op het conventionele ontwerp om het risico te verlagen. Onze belangrijkste interesse is om te laten zien hoe alle systemen en cabine-elementen kunnen worden geïntegreerd die vóór de Main Components Assembly (MCA) kunnen worden geïnstalleerd. Dit zal ook de eerste keer zijn dat dit thermoplastische composietmateriaal wordt toegepast in volledige primaire rompconstructies voor grote passagiersvliegtuigen.”
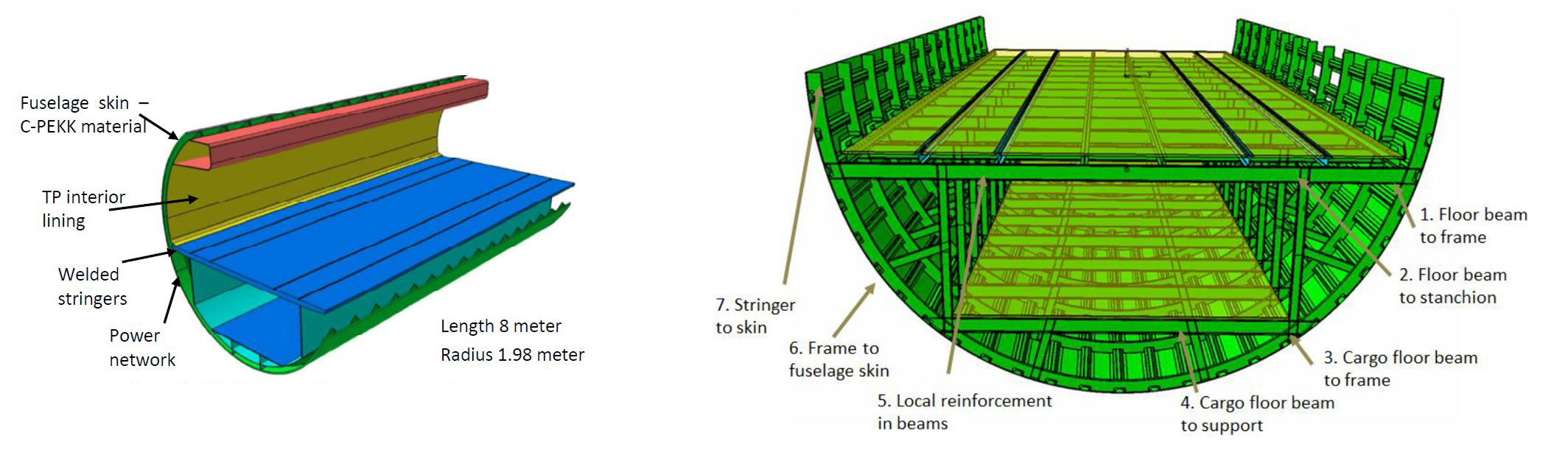
Het ontwerp van de MFFD is in 2018 veranderd van een ontwerp met een schuine verbinding naar een meer conventionele langsnaad. BRON | CFP08 p.87 (links) en CFP09 p. 133 (rechts).
Een andere verandering was in het thermoplastische composiet (TPC) matrixmateriaal. MFFD-onderwerpen in CFP08 en CFP09 verwijzen naar koolstofvezel/PEKK (polyetherketonketon), maar tegen CFP10 (maart 2019) werd het basismateriaal beschreven als koolstofvezel en PAEK (polyaryletherketon). PAEK is de algemene familie van polymeren waarbinnen PEEK, PEKK en LM PAEK zich bevinden.
Zoals beschreven in mijn blog over PEEK vs. PEKK vs. PAEK, produceert Cetex-materiaalleverancier TenCate, nu Toray Advanced Composites, alle drie de polymeren als met koolstofvezel versterkte tape en beweert dat de eigenschappen in principe hetzelfde zijn. Cetex TC1225 CF/LM PAEK tape smelt bij 305 °C terwijl TC1320 CF/PEKK tape smelt bij 340 °C . En, volgens Toray Advanced Composites global CTO Scott Unger, "LM PAEK heeft een veel betere doorstroming ... en kan ook met hogere snelheden worden verwerkt dan PEKK en PEEK." TC1225 kost ook minder.
MFFD onderste romp:project PRACHTIG
STUNNING is de projectnaam voor de ontwikkeling en fabricage van de volledig uitgeruste onderste helft van de MFFD. Het project wil verder rijpen:
- Geautomatiseerde assemblageprocessen
- Thermoplastische productie- en assemblagetechnologieën
- Geïntegreerde ontwerp- en productieontwikkelingstechnologieën
- Ontwikkeling van geavanceerde elektrische systeemarchitecturen.
Bas Veldman, programmamanager bij GKN Fokker (Hoogeveen, Nederland) en projectmanager voor STUNNING, legt uit dat de MFFD 8 meter lang en 4 meter breed wordt met een straal van 2 tot 2,5 meter, wat reële schaal is voor een enkel gangpad A320 familie vliegtuigen. "Het is vergelijkbaar met de A321, die niet precies rond is, maar ruwweg eivormig (een beetje hoger dan breed)", voegt hij eraan toe.
Het onderste rompgedeelte van 180° omvat de onderste rompschaal met gelaste draagbalken en frames, de cabine- en laadvloerstructuur en relevante hoofdinterieur- en systeemelementen. “We gaan grote, voorgemonteerde modules leveren voor een zeer snelle, plug-and-play montage”, zegt Veldman.
GKN Fokker is de leidende partner in STUNNING en heeft vier divisies die deelnemen, waaronder Aerostructures (Papendrecht, Nederland), Fokker ELMO (Hoogerheide, Nederland), GKN Fokker Engineering Romania (Boekarest) en GKN Fokker Technologies (Papendredcht, Nederland). GKN Fokker ELMO is leverancier van kabelbomen voor vliegtuigen en elektrische systeemtechniek. "Het is verantwoordelijk voor de systeemarchitectuur in STUNNING en zal zich richten op het optimaliseren van het elektrische systeem", legt Veldman uit, "en werkt samen met het CFP08-consortium MISSION aan de ontwikkeling van een innovatief stroombussysteem."
"Diehl Aviation (Laupheim, Duitsland) is verantwoordelijk voor de interieurstructuur, inclusief subsystemen en de vloer, zijwandpanelen en hoe ze worden verbonden, monumenteninterfaces en slimme systeem-multipoorten", vervolgt Veldman. “NLR (Netherlands Aerospace Centre, Amsterdam) is verantwoordelijk voor de fabricage van de romphuid en stringers en de TU Delft assisteert bij de montage vanuit haar expertise op het gebied van ultrasoon lassen.” (Zie "Thermoplastische composieten lassen" voor meer informatie over ultrasoon lassen.)
MECATESTERS-lastestprogramma
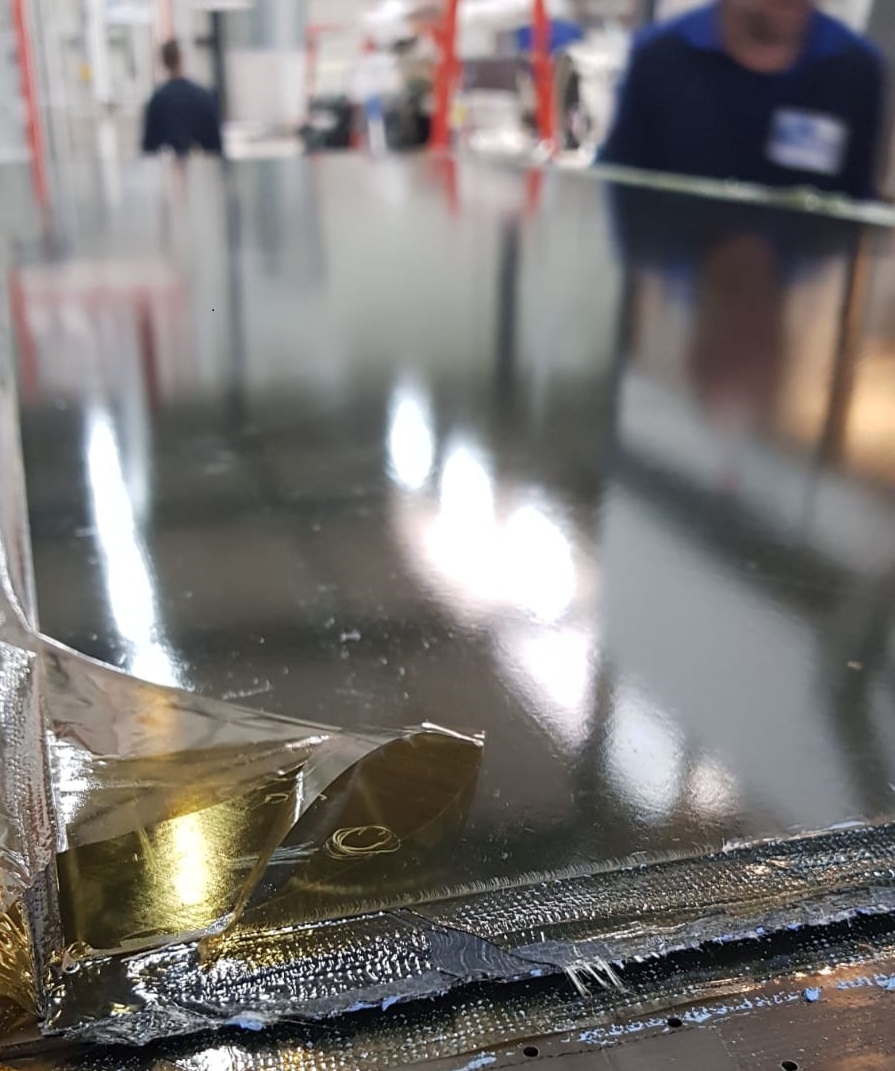
"STUNNING heeft zeven CFP-onderwerpen gelanceerd en vijf zijn begonnen, waaronder MAYA, MISSION, EMOTION, TCTool en MECATESTERS", zegt Veldman. Dit laatste is een groot lastestprogramma met KVE Composites (Den Haag, Nederland) en Rescoll (Pessac, Frankrijk) die in april 2019 is gestart met een looptijd van 30 maanden. Veldman legt uit dat hoewel KVE een lange geschiedenis heeft met inductielassen van zowel stof als UD-tape thermoplastische composieten, de inductiegelaste onderdelen die tot nu toe in vliegtuigen vliegen, stof hebben gebruikt. "In STUNNING stellen we best practices vast met UD-versterkingen en LM PAEK-materialen, en vergelijken we ook inductielassen met conductielassen onder typische gebruiksbelasting en omgevingscondities." Hoewel weerstandslassen en ultrasoon lassen zijn opgenomen in andere MFFD-werkpakketten en CFP's (zie "De twee helften verbinden ” hieronder), zijn inductielassen en conductielassen de enige twee technieken in MECATESTERS.
Labordus van KVE legt uit dat KVE voor de drie MECATESTERS-werkpakketten (WP 1, 2 en 3) alle testlaminaten zal maken met in de autoclaaf uitgeharde TC1225 UD-koolstofvezel/LM PAEK-tape (zie "Eerste Toray LM-PAEK-laminaat voor Clean Sky MECATESTERS-project"). KVE zal ook inductiegelaste monsters voorbereiden voor testen, terwijl GKN Fokker geleidingsgelaste monsters zal produceren en Rescoll alle fysieke tests zal uitvoeren. "De naam Rescoll is afgeleid van onderzoek en collage, wat Frans is voor binding", zegt Labordus. "Ze staan bekend om hun onderzoek naar alle soorten verbindingen en bieden een goed uitgerust testlaboratorium voor polymeren en composieten, inclusief mechanische, milieu-, ontvlambaarheidstests en elke mogelijke test voor kwalificatie in de lucht- en ruimtevaart, de automobielindustrie, de spoorwegen en andere industrieën."
Procesparameters en tests
"We beginnen eigenlijk met WP 2 om procesparameters in te stellen, zoals boven- en ondergrenzen voor de temperatuur en druk van inductielassen", zegt Labordus. “We hebben bijvoorbeeld een nominaal druk die we normaal gebruiken, maar we zullen naar lagere drukken gaan totdat we defecten zoals holtes beginnen te zien, en dan zullen we die laseigenschappen evalueren om de lagere drukgrens vast te stellen. Testen zal ook de lassnelheid evalueren, die de afkoelsnelheid en kristalliniteit van de las beïnvloedt, en mogelijk de mechanische eigenschappen. Dezelfde parameters worden bij Fokker onderzocht voor conductielassen.
Voor evaluatie voert het MECATESTERS-programma meerdere tests uit, waaronder:
- Lapshear-test volgens ASTM D5868–01
- Trek- en afschuiftest op coupons met L-profiel
- GIC en GIIC volgens respectievelijk ISO 15024 en ISO 15114
(deze taaiheidstest zal daadwerkelijk worden voltooid in WP 1)
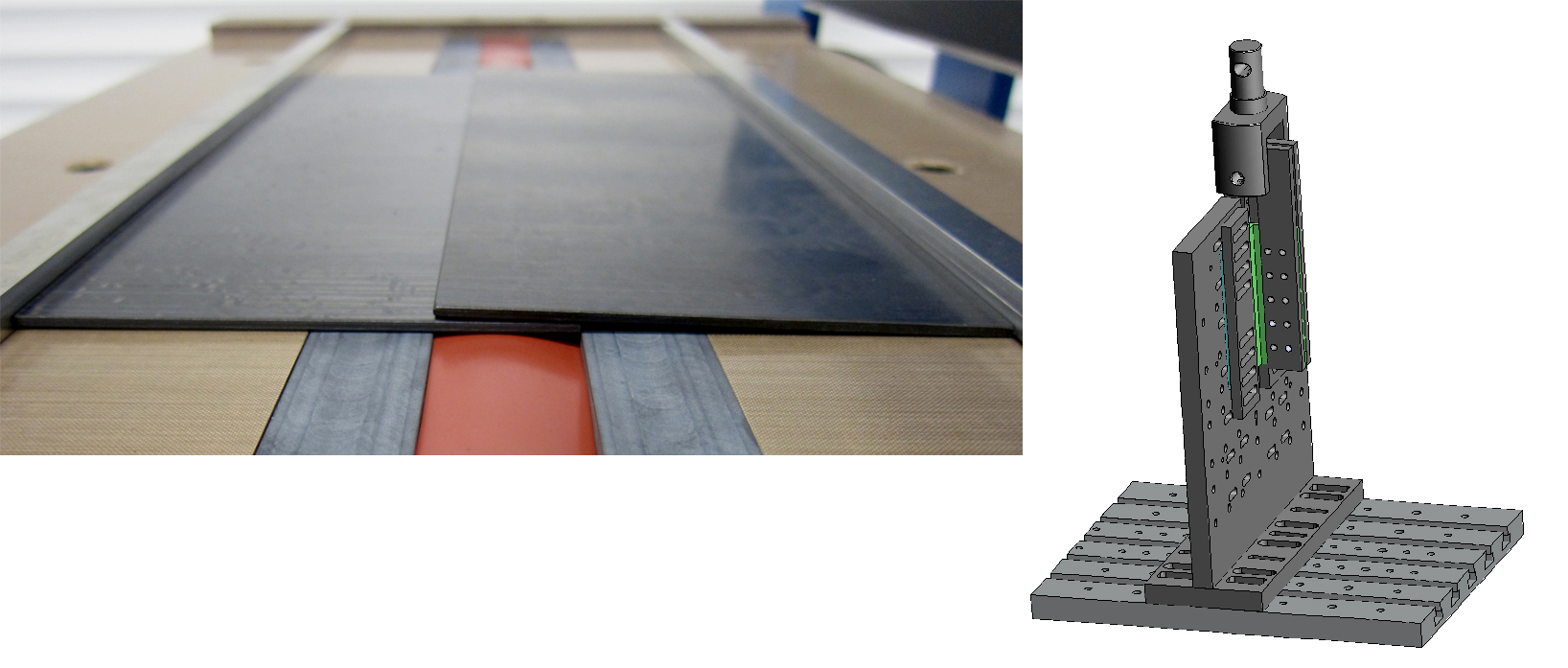
Enkele overlappende afschuifcoupon van UD-tapelaminaat klaar voor inductielassen (links) en testopstelling voor gecombineerd afschuif- en afpeltesten van gelaste L-profielcoupon met behulp van door Rescoll ontwikkeld gereedschap (rechts). BRON | KVE Composites, Rescoll.
“De pull-off testmethode komt voort uit een interne standaard die GKN Fokker heeft ontwikkeld”, legt Rescoll engineer Thomas Salat uit. "Trektesten van de gelaste profielen zijn loodrecht op de huid voor afpelbelasting", merkt Labordus op, "en evenwijdig aan de huid voor schuifbelasting. Schil en afschuiving zijn de twee uitersten, maar we zullen ook nieuwe combinaties hiervan testen die een weerspiegeling zijn van praktische, in-service belastingscondities.” Deze test zal worden voltooid voor twee verschillende laminaatdiktes die zijn afgeleid van het MFFD-rompontwerp - 2,2 en 2,8 millimeter - bij kamertemperatuur (RT), koude temperatuur (-55°C) en hoge temperatuur (80°C) met behulp van statische belasting.
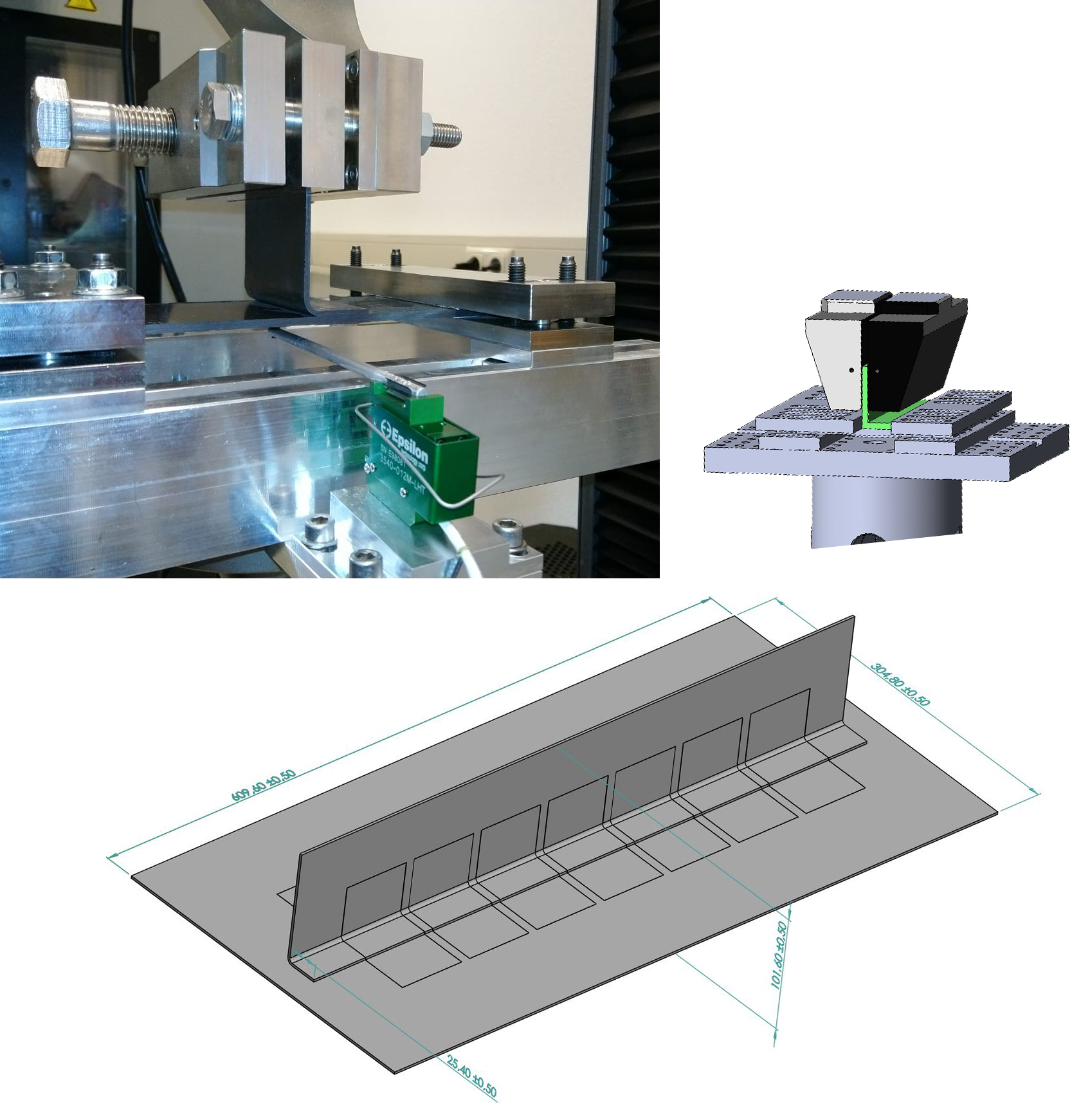
Pull-off tests op L-profiel coupons bij KVE Composites (linksboven). In MECATESTERS wordt bij dit type testen gebruik gemaakt van een door Rescoll ontwikkelde grijper en testopstelling om doorbuiging van de huid te elimineren (rechtsboven). Testbonnen worden gesneden uit gelaste panelen (onder). BRON | Rescoll, KVE Composites.
Voorbereiding van het oppervlak, veroudering en vermoeidheid
WP 1 begint met taaiheidstesten. "Voor de fissurisatietests (GIC en GIIC) zullen we een scheur in het composiet initiëren en meten hoe deze scheur zich gedraagt onder belasting", legt Salat uit. “Een daarvan is een statische test die de belasting verhoogt totdat deze faalt. We zullen ook een dynamische test doen waarbij we de statische belasting een miljoen keer herhalen, wat een tot twee weken in beslag neemt. We zullen zien of de composietlas deze vermoeiing kan weerstaan. Deze modus II is een nieuw soort cyclische test. We zijn een methode aan het ontwikkelen die is ontleend aan een technisch artikel dat is gepubliceerd door de Universiteit van Europa en we zijn nu bezig met het afronden van de parameters.”
Ook in WP 1 zullen de lasparameters die zijn vastgesteld in WP 2 worden gebruikt om de effecten van oppervlaktevoorbereiding en veroudering en vermoeidheid te onderzoeken. "We zullen kijken naar oppervlakteverontreinigingen en hoe deze de las kunnen beïnvloeden", zegt Labordus. “We zullen ook drie verschillende soorten lossingsmiddelen onderzoeken die vaak worden gebruikt in pers- en autoclaafverwerking; specifieke soorten oppervlaktevoorbereiding, waaronder schuren, schuurmiddelen en plasmabehandeling; en ook het gebruik van een extra harsfilm op het te lassen oppervlak. Daarnaast gaan we de invloed van vezeloriëntatie bestuderen, bijvoorbeeld plus/min 45 graden op het lasinterface.”
Rescoll zal ook een conditioneringskamer bij 70°C en 90% vochtigheid gebruiken om veroudering tijdens gebruik te simuleren, zegt Salat. “Vervolgens voeren we de standaardtesten uit om te kijken of dit de lasprestaties beïnvloedt.” Labordus voegt eraan toe dat er een beperkt aantal monsters zal worden genomen tot 100°C en 120°C, "om de bewering te valideren dat thermoplastische composieten geen scherpe knockdown hebben boven 80°C."
Naast de dynamische fissurisatie/GIIC-test, zullen vermoeiingstests worden uitgevoerd in de modi voor afschuiving en afschuiving met één ronde. "We beginnen bij 80 procent van de statische faalbelasting en gaan naar 50 of 75 procent hiervan in vermoeidheid gedurende een miljoen cycli", zegt Labordus. "We zullen ook andere tests doen, maar deze zijn nog aan het bespreken", voegt Salat toe.
Lassen aan korte samengestelde beugels
Hoewel de details van WP 3 nog worden afgerond, is het gericht op het onderzoeken van lassen van persgegoten beugels gemaakt van kortvezelmateriaal op de UD-laminaathuid. "We zullen opnieuw procesparameters benchmarken en de mechanische eigenschappen van de las karakteriseren", zegt Labordus, "maar we werken nog steeds aan het definiëren van de geometrie voor het testen."
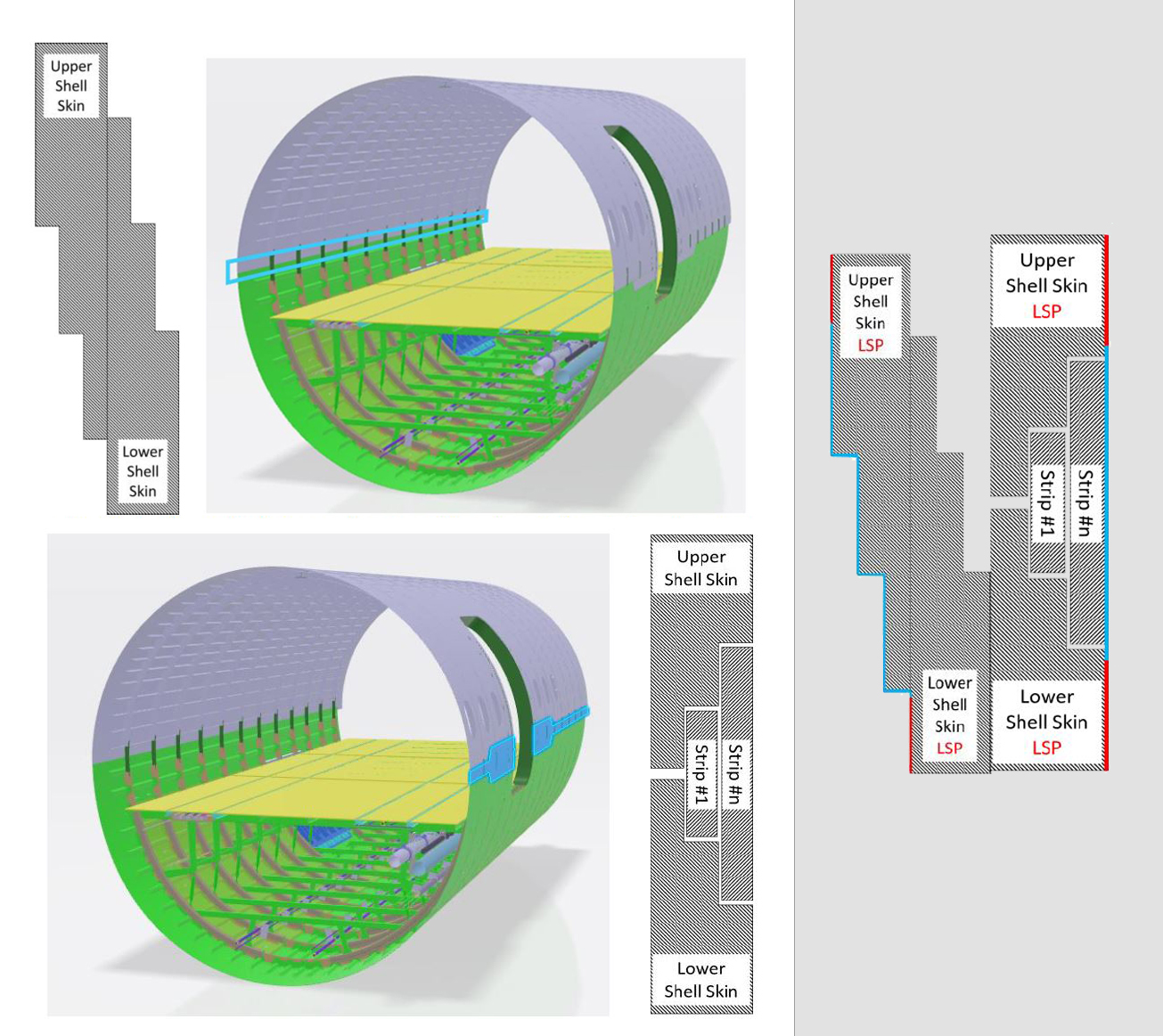
Stringers en clips gelast aan een thermoplastische romp. BRON:Clean Sky 2 11 de Oproep tot het indienen van voorstellen JTI-CS2-2020-CfP11-LPA-02-35, "Innovatieve onthechtingsstopfuncties voor lange thermoplastische gelaste verbindingen", Afbeelding 2, p. 94.
Gelaste clips en beugels
Zoals uiteengezet in het CFP10-onderwerp JTI-CS2-2019-CfP10-LPA-02-31, zullen alle frameclips en systeembeugels voor de onderste romp van de MFFD worden vervaardigd door middel van spuitgieten van kortevezelverbindingen gemaakt door hergebruik van fabrieksafval van de topicmanager GKN Fokker's productie van continuvezel TPC-laminaten. CF/PAEK is het basismateriaal en lassen is de basisverbindingsmethode, hoewel de specifieke lasmethode niet wordt voorgeschreven.
Volgens de CFP10-tekst zal de onderste romp van de MFFD 13 frames en ongeveer 36 stringers hebben, waarvoor ongeveer 500 frameclips nodig zijn (let op:dit zijn primaire constructies die structurele tests vereisen en dit totaal omvat clips die worden gebruikt voor testen) en ongeveer 270 systeembeugels (die zijn secundaire constructies) opgesplitst volgens de onderstaande typen:20 systeembeugels (1), 120 systeembeugels (2), 50 systeembeugels (3) en 80 systeembeugels (4).
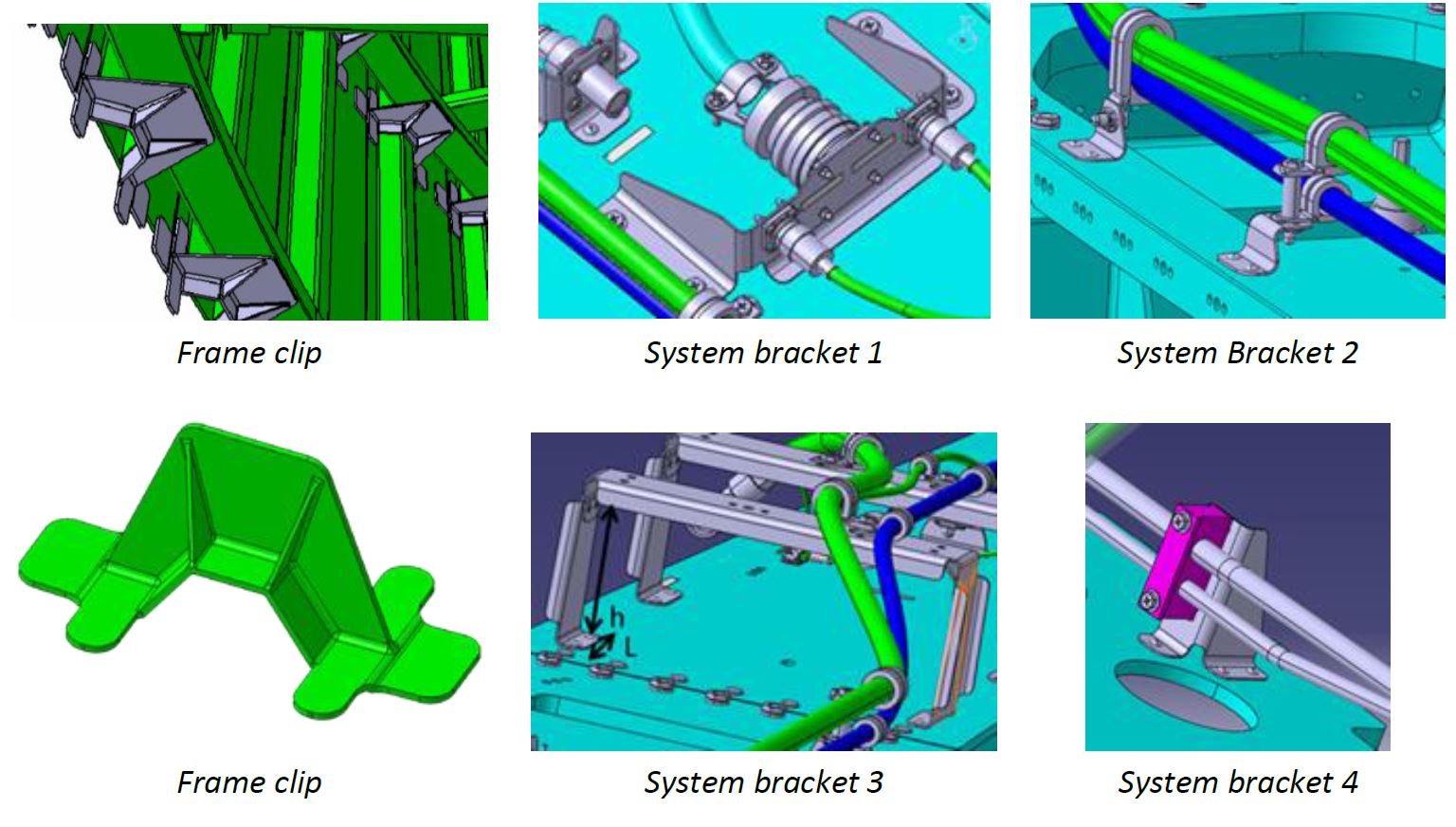
Voorbeelden van te leveren onderdelen in Clean Sky 2 topic JTI-CS2-2019-CfP10-LPA-02-31, Figuur 2. BRON | Clean Sky 2 CFP10, p. 146.
Ook in CFP10 is het MFFD-onderwerp van de bovenste romp JTI-CS2-2019-CfP10-LPA-02-30, "Ontwikkeling van innovatieve lassystemen voor structurele verbindingen van op thermoplastische matrix gebaseerde composieten", geleid door Aernnova Composites Illescas (Illescas, Spanje). Het doel is om na 1Q 2020 van start te gaan en het doel is om een lassysteem te ontwikkelen om een structurele verbinding tot stand te brengen tussen verstevigingsdelen (hoekplaten, wiggen, fittingen) en structurele frames om een sterk geïntegreerde Door Surround Structure (DSS) te verkrijgen. Ik hoop in een toekomstige blog meer details te geven over de bovenste romp van de MFFD. Voor nu is het voldoende om te begrijpen waarom het MECATESTERS-werkpakket 3 belangrijk is en hoeveel er zal worden bereikt zodra MECATESTERS, STUNNING en de MFFD zijn voltooid.
De twee helften verbinden
Eenmaal voltooid, gaat de onderste helft van de MFFD naar het Fraunhofer Institute for Manufacturing Techanology and Advanced Materials IFAM (Stade, Duitsland) om te worden samengevoegd met de bovenste helft, legt Veldman uit. "We zijn vastbesloten om onze helft van de romp tegen eind 2021 op te leveren", voegt hij eraan toe.
Zoals hierboven vermeld, is Ralf Herrmann bij Airbus de MMFD-projectleider; zo integreert Airbus het werk van Fraunhofer IFAM en het consortium CFP07 MultiFAL (Multifunctional automation system for Fuselage Assembly Line) - dat verantwoordelijk is voor het verbinden van de twee romphelften, in samenwerking met de STUNNING en de bovenste rompteams —om oplossingen te ontwikkelen voor de talloze uitdagingen.
Sommige hiervan worden onthuld in twee onderwerpen in de 11 e Oproep tot het indienen van voorstellen (november 2019), beide geleid door Airbus om te beginnen na het vierde kwartaal van 2020 en getiteld "Tooling, uitrusting en hulpstoffen voor de sluiting van een longitudinale loopverbinding:"
- JTI-CS2-2020-CfP11-LPA-02-33, ":Butt strap-integratie en continuïteit van Lightning Strike Protection"
- JTI-CS2-2020-CfP11-LPA-02-34, ":Overlapverbinding en framekoppeling integratie"
Geschreven door Piet-Christof Woelcken, topicmanager bij Airbus Bremen en MFFD-werkpakketleider, zijn de belangrijkste uitdagingen bij deze onderwerpen:
JTI-CS2-2020-CfP11-LPA-02-33
- Kontbandverbinding (Fig. 3 hieronder):
- De linkerkant van de demonstrator (in vliegrichting) omvat de omlijsting van de passagiersdeur. De variatie in huiddikte in dit gebied vereist een getrapte integratie van de buttband, die de boven- en onderhuid verbindt.
- Gezien de complexiteit van de verbindingen, geleidingslassen het gebruik van een verwarmde drukplaat is de geprefereerde verbindingstechnologie.
- Elektrische continuïteit van de blikseminslagbeveiliging (Fig. 4 hieronder):
- Elektrische continuïteit van de metalen blikseminslagbeveiliging (LSP) moet worden bereikt over beide langsverbindingen aan de buitenkant van de romp.
- Er wordt verwacht dat de gereedschapskop die is voorzien voor de integratie van de kontband voor dit doel kan worden gebruikt.
JTI-CS2-2020-CfP11-LPA-02-34
- Overlappingsvoeg (Fig. 2 hieronder):
- De 8 meter lange overlapverbinding aan de rechterkant van de demonstranten (in vliegrichting) verbindt de bovenste en onderste romphuid. In de lengterichting is de huiddikte kleiner dan 3 mm constant in de laszone. In de omtreksrichting hebben de huiden een getrapte geometrie voor verbeterde structurele prestaties.
- Ultrasoon lassen is de voorkeursverbinding om een hoge productiesnelheid te bereiken.
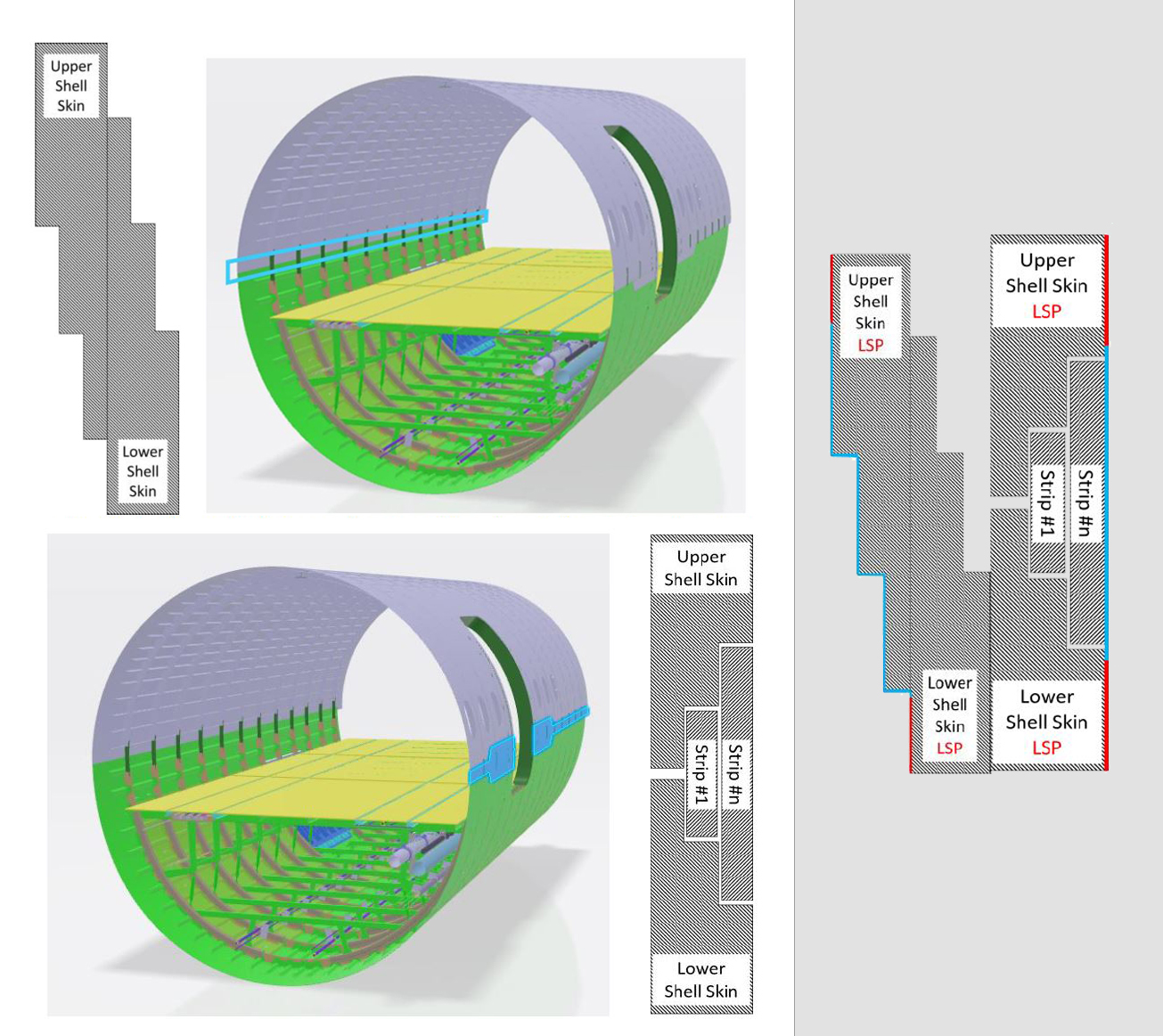
Afb. 2 (Linksboven) :Overlappingsvoeg:Er is gekozen voor een getrapte benadering in het ontwerp van de overlapvoeg. Merk op dat de onderste schaal aan de binnenkant van de romp ligt. Afb. 3 (Linksonder) : Butt strap integratie:Een aantal overliggende strips vereisen integratie over de getrapte verbinding. Merk op dat de Butt-riem aan de buitenkant van de romp zit. Afb. 4 (Rechts) :Elektrische continuïteit van metalen LSP moet worden bereikt over de langsverbindingen aan de buitenkant van de CFRP-romp. Rood geeft een vooraf uitgeruste LSP aan, blauw geeft aan dat LSP moet worden toegepast als onderdeel van dit onderwerp. BRON | Clean Sky 2 11 de Oproep tot het indienen van voorstellen JTI-CS2-2020-CfP11-LPA-02-33 en -34, “Butt strap integratie en Lightning Strike Protection continuïteit”, pp. 78 en 86.
JTI-CS2-2020-CfP11-LPA-02-34
- Frame koppeling integratie (Fig. 5):
- Overlapverbinding:framekoppelingen onder de overlapverbinding moeten de bovenste en onderste schaalframes structureel verbinden.
- Buttband:framekoppelingen onder de buttband moeten de bovenste en onderste schaalframes structureel verbinden en aansluiten op de huid.
- Weerstandslassen is de voorkeurstechnologie voor deze technische uitdaging.
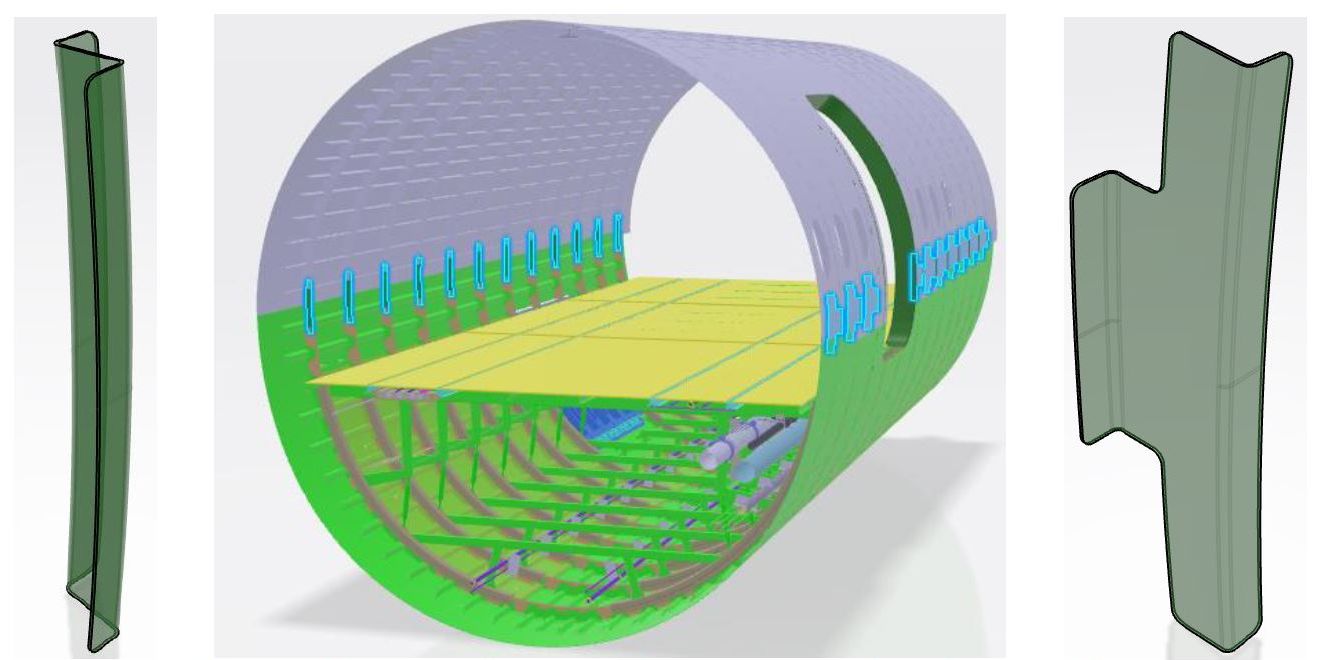
Frame koppeling integratie. Merk op dat framekoppelingen per zijde verschillen als onderdeel van de technologiedemonstratie. BRON | Clean Sky 2 11 de Oproep tot het indienen van voorstellen JTI-CS2-2020-CfP11-LPA-02-34, "Gereedschap, uitrusting en hulpmiddelen voor de sluiting van een longitudinale loopverbinding:overlapverbinding en integratie van framekoppeling", Fig. 5, p. 86.
Lasmethoden, gereedschapskoppen en toleranties
Herrmann legt uit dat geleidingslassen aan de linkerkant zal worden gedemonstreerd via de stootbandverbinding en ultrasoon lassen aan de rechterkant via de overlapverbinding, terwijl weerstandslassen zal worden gebruikt voor de framekoppelingen. "MFFD zal veel technische benaderingen demonstreren, dus het is niet hetzelfde als het vervaardigen van een echte romp, maar is in plaats daarvan ontworpen als een voertuig voor het demonstreren en volwassen worden van technologieën", voegt hij eraan toe.
Ontwikkelen van laskoppen
Het doel van deze twee door Woelcken geschreven onderwerpen is het ontwikkelen van de benodigde gereedschapskoppen voor deze lasverbindingen. "Als je twee stukken aan elkaar las, moet je warmte en druk uitoefenen", legt hij uit. “Dit wordt dus aangebracht door de gereedschapskop tijdens het lassen. Bij het Fokker-type conductielasproces oefen je aan de ene kant actief warmte en druk uit en aan de andere kant passieve druk van een steun. De stompe verbinding is een stapel van zes banden, en bij het samenvoegen plaatsen we de stapel en verwarmen deze tijdens het lassen. Omdat het LM PAEK UD-tapemateriaal echter relatief nieuw is in het lassen, moeten we de procesomstandigheden begrijpen en begrijpen hoe we toleranties kunnen compenseren. We moeten dus de materialen en dikte definiëren, evenals de geometrie van de gereedschapskop.”
"Merk op dat het gebruik van dit type stootvoeg een standaardproces is voor wat we doen aan andere verbindingen in ons vliegtuig", benadrukt Woelcken. "Voor de MFFD willen we de bovenste en onderste romp ongewijzigd laten ten opzichte van deze standaardpraktijk om de hoeveelheid materiaal die we moeten aanpassen te minimaliseren."
Flexibiliteit in toleranties
Woelcken merkt op dat, omdat de bovenste lasoppervlakken in wezen in vloeistof worden gesmolten en vervolgens tegen elkaar worden gedrukt, "dit veel flexibiliteit geeft om rekening te houden met toleranties." Let op, momenteel met thermoset koolstofvezelversterkte polymeer (CFRP) vleugels en rompen, deze tolerantieproblemen worden verholpen door een vloeibare vulplaatlijm aan te brengen. Hoewel weinig mensen dit in het openbaar willen bespreken, is het algemene probleem van shimming in composiet aerostructuren algemeen erkend en zijn er initiatieven gepubliceerd om dit te verminderen en/of te elimineren, zoals de Flexmont-montagemethode voor verticale staartvlakken.
“ We verwachten wel voordelen te behalen bij het aanpakken van toleranties door gebruik te maken van thermoplastische composieten”, zegt Woelcken, “vooral door gebruik te maken van onze ontwerpconcepten en gebruik te maken van onze ervaring met thermohardend CFRP en metallisch lassen. De sleutel zal zijn in situ monitoring tijdens verwarming en toepassing van druk.” Hij benadrukt dat warmte parameter nummer één is. “Het verbaast me hoe tolerant de lasprocessen van thermoplastisch composiet zijn voor druk. De grootste uitdaging daar is het beheersen van die druk en hoe deze afneemt. Momenteel bewaken we de achterkant van de lasverbinding.”
Fraunhofer IFAM geautomatiseerd assemblagesysteem (linksboven) met afmetingen aan het begin van CFP07 werkonderwerp (rechtsboven) wordt aangepast om plaats te bieden aan een 360°-romp voor het lassen van de langs- en omtrekverbindingen van de MFFD. BRON | Fraunhofer IFAM en cfk-valley.com, Clean Sky 2 7 th Oproep tot het indienen van voorstellen, JTI-CS2-2017-CfP07-LPA-02-22, p. 76.
Assemblageautomatisering
In de 7 de Oproep tot het indienen van voorstellen, het onderwerp JTI-CS2-2017-CfP07-LPA-02-22, "Ontwikkeling van een volledig geautomatiseerd installatiesysteem voor langs- en omtrekverbindingen van de romp" wordt geleid door Fraunhofer IFAM binnen het MultiFAL-consortium. Het onderstaande fragment werpt enig licht op hoe de hierboven besproken laskoppen, die nu in ontwikkeling zijn, kunnen worden geïmplementeerd:
“Om het assemblageproces van een thermoplastische romp te realiseren, worden toleranties een belangrijk onderwerp. The positioning and orientation of the fuselage shells, as well as resulting deformations caused by the welding process, need to stay within the tolerances. Comparable accuracies can be oriented to the state-of-the-art process of longitudinal joint. Here, the position error in each direction should be within 0.5 mm (in some exceptions up to 1 mm). … it can be assumed that a pre-load on the joint surface from both sides of approximately 1000N (independent of the welding technology) for a welding seam of 20 mm width is required by the automation system.”
Fraunhofer IFAM — which was also CTC Stade’s partner in developing the Flexmont VTP assembly process — describes its starting point:an in-house assembly plant system which can manipulate parts from 2 to 8 meters long and up to 6 meters high, including a 180° shell of a single-aisle aircraft. The system is enabled by a flexible arrangement of 10 cooperating hexapods (see “Reconfigurable Tooling:Revolutionizing composites manufacturing”), 24 linear units and modular rack elements. Vacuum grippers with 6-axis force and torque sensors adjust the pose and shape of the part, as required, to manage tolerances during assembly. The guidance and monitoring of these rapid, iterative adjustments is achieved through optical measuring devices.
According to the CFP07 text, Fraunhofer IFAM will modify this assembly plant system for holding a complete 360° fuselage, with work scheduled to begin in Q2 2018 and completed in 36 months.
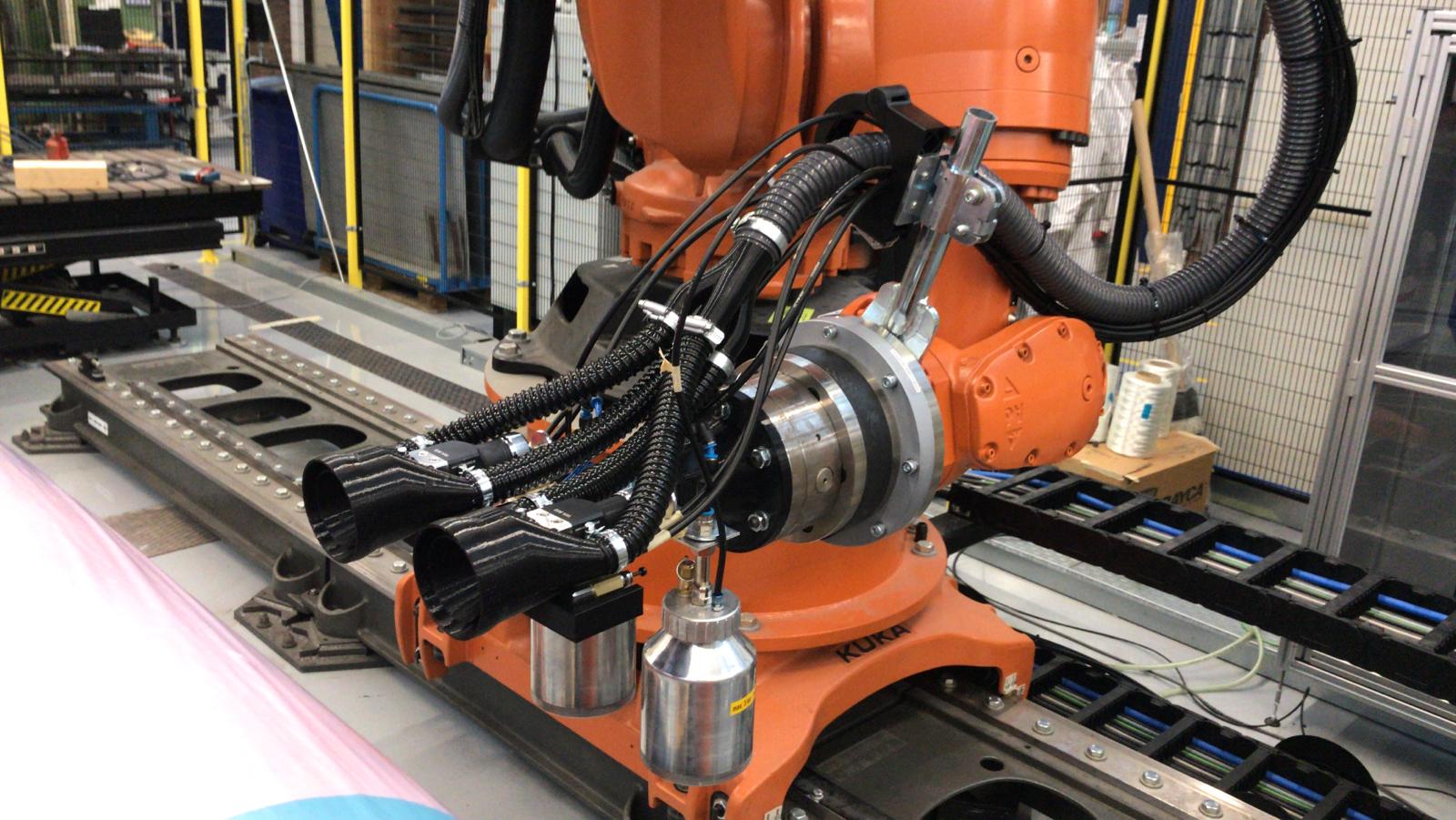
The STUNNING consortium is working with SAM|XL to develop automation for assembling the MFFD lower fuselage. SOURCE | samxl.com
Within STUNNING, activities are planned with the collaborative research center SAM|XL (Smart Advanced Manufacturing XL, Delft, Netherlands) to demonstrate automated welding techniques for assembling the lower fuselage. Specializing in automation for manufacturing large, lightweight composite structures, SAM|XL brings together TU Delft’s Aerospace Engineering group and Robotics Institute. GKN-Fokker is a major participant. One of the methods being investigated is sequential spot ultrasonic welding, which was proven in the Clean Sky 1 Eco Design project and TAPAS 2 as a fast and effective for connecting short fiber-reinforced brackets or clips to fuselage structures.
In her 2016 paper, titled “Smart ultrasonic welding of thermoplastic composites,” Villegas states that it is possible to scale up the ultrasonic welding process via sequential welding — that is, letting a continuous line of adjacent spot welds serve the same purpose as a continuous weld bead. Lab-scale sequential spot welding was used in the Clean Sky EcoDesign demonstrator’s TPC airframe panel, using flat energy directors to weld a CF/PEEK hinge and CF/PEKK clips to CF/PEEK C-frames (Fig. 6). Experimental comparisons with mechanically fastened joints in double-lap shear and pull-through tests showed promise. The process is further explored in 2018 papers {and 2019 papers} by Villegas’ TU Delft team member Tian Zhao {and in Villegas’ 2019 paper}.
— “Welding thermoplastic composites”, G. Gardiner, 2018.
The STUNNING consortium’s work with TU Delft and SAM|XL is adapting this technology to weld multiple system and semi-structural brackets, stiffening elements and stringers to the MFFD lower fuselage shell.
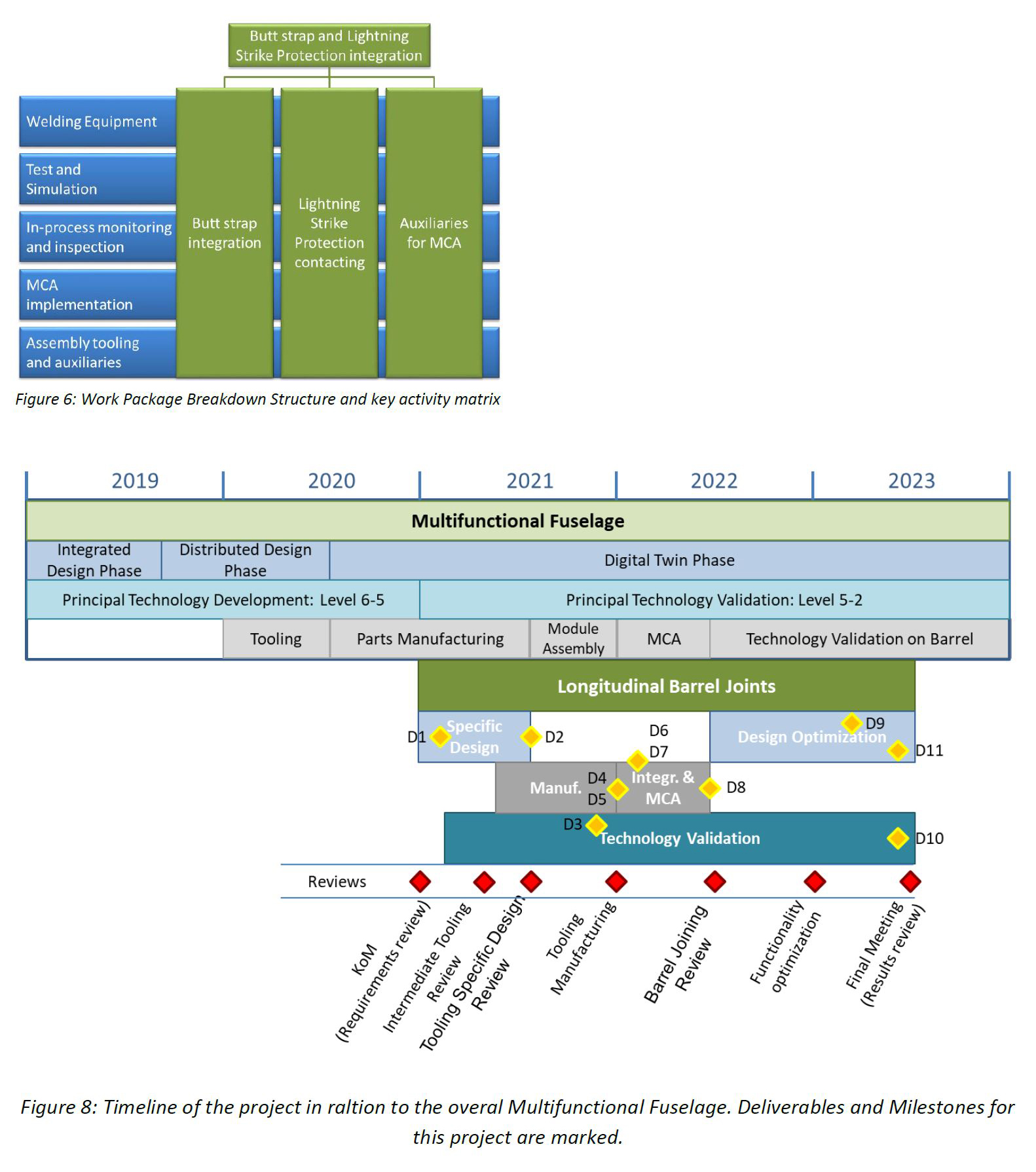
Work breakdown and timeline for MFFD assembly. SOURCE | Clean Sky 2 11 th Call for Proposals JTI-CS2-2020-CfP11-LPA-02-33, “Tooling, Equipment and Auxiliaries for the closure of a longitudinal Barrel Joint:Butt strap integration and Lightning Strike Protection continuity”, pp. 79 and 82.
Digital twin phase, 2020 and beyond
According to the Clean Sky website, the MFFD program reached an important milestone in Nov 2019 with the successful passing of its Critical Design Review (CDR). In the timeline above, the MFFD design enters a “Digital Twin Phase” in 2020-2021. What does this mean? “Though we have wrapped up the majority of the design phase, we are taking it a bit further by working with a specific lifecycle management approach,” explains Herrmann. “We are modeling imperfections and nonconformities from the NDT results and process parameters during component manufacturing. We want to combine this Industry 4.0 data with lifecycle management so that we continue to tailor the design according to what we are actually manufacturing. We want to see how far we can push this and what we can accomplish by the end of Clean Sky 2.”
For 2020, the chief agenda is manufacturing. “We hope to present various parts as they come together this year,” says Veldman. What will the largest challenge be for the STUNNING program? “Assembly,” he answers. “Not so much within STUNNING, but our lower fuselage has interfaces with the door surround structure, multiple Airbus-delivered components and the whole upper fuselage. Getting everything delivered at the right time and then bringing it all together will require a number of developments yet.”
That brings us to perhaps the biggest question:Will thermoplastic composites be used on the next aircraft entering production in 2030-35? “For sure, we want to try to use the technologies we are working on,” says Herrmann, “but I cannot say if or when thermoplastic composites will be on future aircraft. The most important part for us is that they are an enabler for dustless joining regarding ramping production to more than 70 aircraft per month. We have to show that it is feasible, not only with metallics but also with thermoplastic composites.”
“By the end of this project, we will have a more complete understanding of thermoplastic composite welding and will gain approval for its use in large primary aircraft structures,” says Salat. “If we can use this for future aircraft, we can achieve significant weight savings and improved sustainability.” But perhaps just as important is Clean Sky’s ability to bring Europe’s aviation research and innovation stakeholders closer together. “We have quarterly meetings where I sit with all of the LPA steering committee,” says Veldman. “I’m talking to the whole of the European aerospace industry, and it most certainly helps to open up opportunities for the future, not only for companies who can supply to us, but for a wide range of collaborations.”
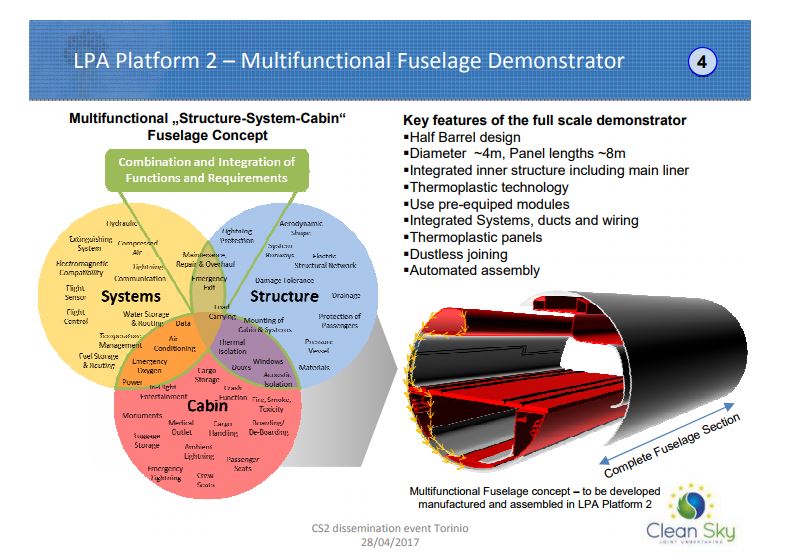
Hars
- 10 startups voor 3D-printen om in de gaten te houden in 2020
- Applicatie Spotlight:3D-printen voor vliegtuigcabines
- De waarde uit data halen voor AI
- 6 lastips voor fabrieksonderhoud
- Op zoek naar een ultrasterk plastic? Bekijk FR-4!
- Materialen:verbindingen en concentraten van medische kwaliteit voor laserlassen
- Tips en trucs voor het lassen van Inconel
- Ontwerpen voor geautomatiseerde composietproductie van aerostructuren met een klein volume
- Victrex en Bond-partner voor 3D-printen van PAEK-onderdelen
- De eerste composiet rompsectie voor de eerste composiet commerciële jet
- Toptips voor het lassen van aluminium