Nieuwe prepreg voor persvormen in RAPM
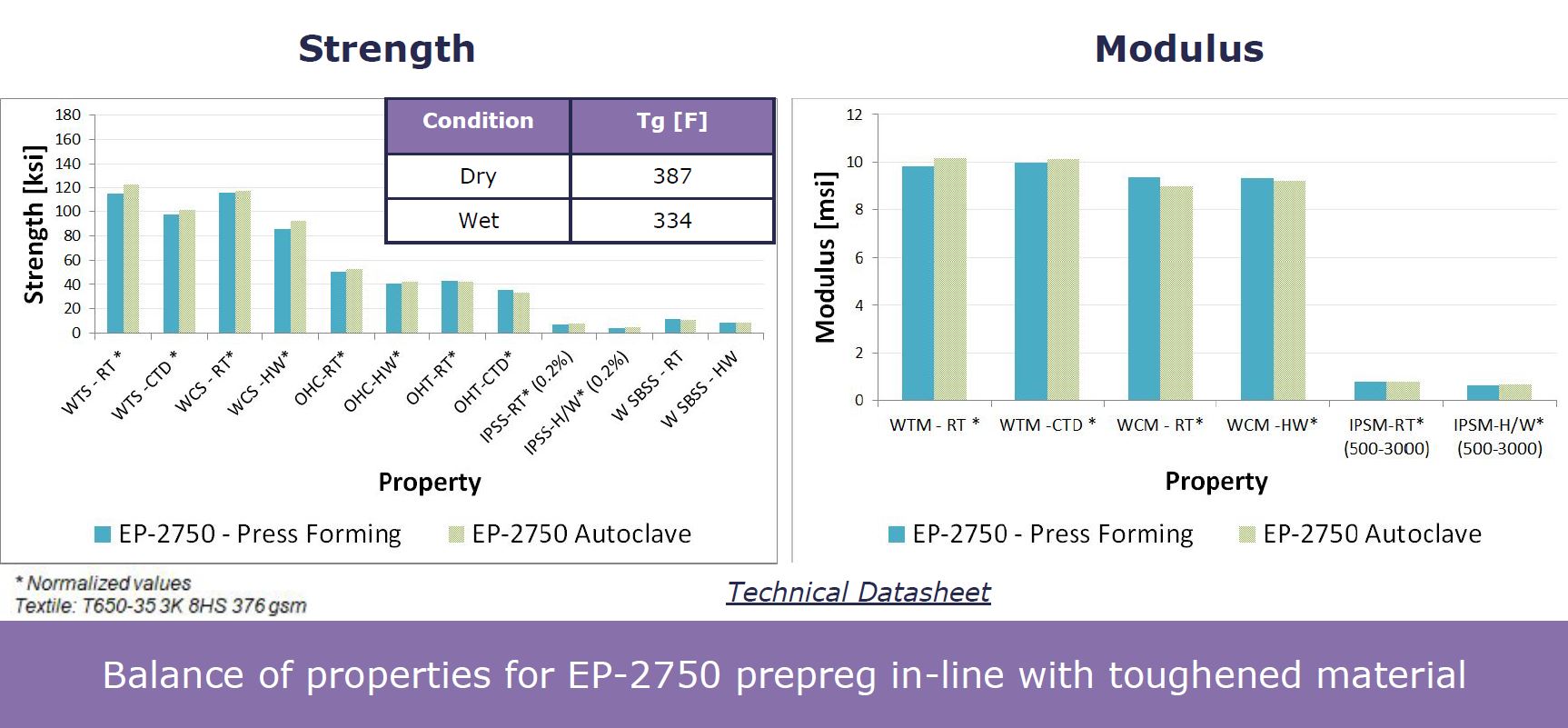
Prepreg van koolstofvezel/epoxy is al tientallen jaren het basismateriaal voor composieten in de lucht- en ruimtevaart omdat het hoge mechanische eigenschappen en nauwkeurig hars-/vezelgehalte biedt, evenals gebruiksgemak voor lay-up en autoclaafuitharding. Aangezien fabrikanten van vliegtuigen en stedelijke luchtmobiliteit (UAM) hogere productiesnelheden en lagere kosten onderzoeken, is persgieten aantrekkelijk, waardoor de cyclustijden worden verkort en de efficiëntie wordt verhoogd ten opzichte van de autoclaaf. Op zijn eenvoudigst omvat persvormen het voorverwarmen van het vormmateriaal, het plaatsen in een open gereedschapsholte en het consolideren met hydraulische druk bij temperatuur, waarbij het vloeibare thermohardende materiaal wordt omgezet in een vaste stof. Het uitgeharde deel wordt vervolgens uitgeworpen voor alle vereiste trim- en afwerkingsstappen.

De combinatie van persvormen en prepreg levert niet alleen een efficiënt proces met hoge snelheid op met de prestaties en gemakkelijke hantering van prepreg, het vermijdt ook een deel van de complexe procesdynamiek van het vullen van droge versterkingen met vloeibare hars tijdens processen zoals harsinfusie en harsoverdrachtsvormen (RTM). Vooral voor kleinere aerostructuren biedt prepreg-persgieten het potentieel voor takt-tijden van <30 minuten terwijl toch hoogwaardige, complexe geometrie-onderdelen worden bereikt.
Solvay Composite Materials (Alpharetta, Ga., V.S.) was een belangrijke partner in het RApid high-Performance Manufacturing (RAPM)-programma onder leiding van The Boeing Co. (Chicago, Illinois, V.S.). RAPM is het "vormende" deel van het Tailorable Feedstock and Forming (TFF)-programma, gelanceerd door het Defense Advanced Research Projects Agency (DARPA, Arlington, Va., VS) in 2015. Het doel is om snelle, goedkope en flexibele fabricage van kleine, complexe composietonderdelen en vergroot het vermogen van composieten om te concurreren met machinaal bewerkt aluminium in defensietoepassingen.
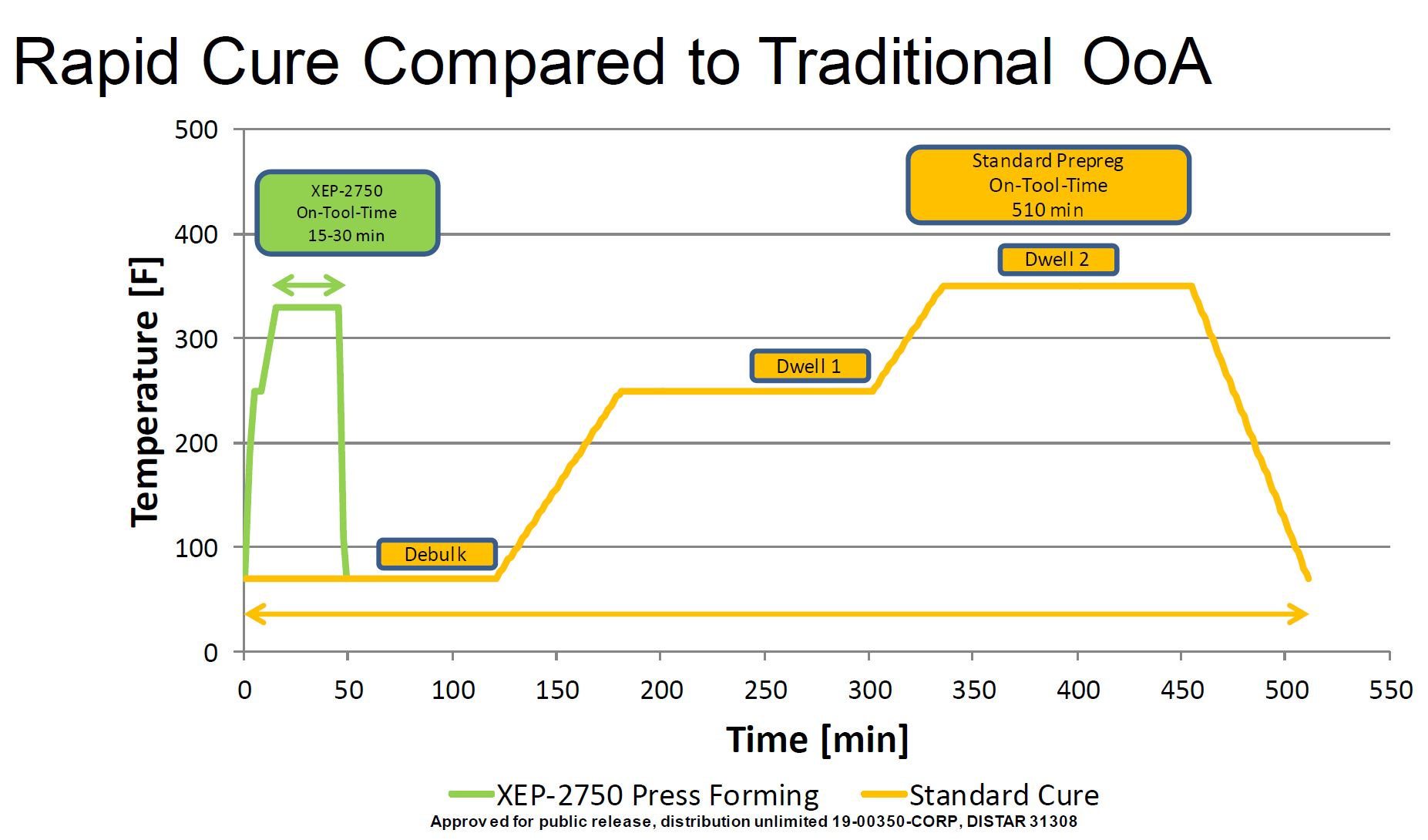
Solvay is al lange tijd leverancier van Boeing voor defensietoepassingen en is ook een leider in nieuwe oplossingen voor de commerciële lucht- en ruimtevaart, zoals de out-of-autoclave (OOA) epoxy prepreg CYCOM 5320-1, en ook voor de automobielindustrie, zoals de 1 minuut takt tijd, vinyl hybride SolvaLite 730 prepreg.
RAPM was een perfecte gelegenheid voor Solvay om zijn experimentele systeem XEP-2750, nu gecommercialiseerd als CYCOM EP2750, te testen en te verfijnen, dat werd ontwikkeld om een brug te slaan tussen de productie van lucht- en ruimtevaart en autocomposieten. Deze blog - een online zijbalk bij de mei 2020-functie "Revolutie van het kostenparadigma van composieten, deel 2:Vormen" - bespreekt die ontwikkeling, evenals de gebruikte persgietprocessen en wat CYCOM EP2750 te bieden heeft aan fabrikanten van composieten in de ruimtevaart en auto's.
Referenties voor deze blog zijn onder meer:
- "Spring Frame Press Fabrication of Aerospace Production Components" door Timothy J. Luchini
1
, Alejandro J. Rodriguez
2
, Scott A. Rogers
2
, Aurele Bras
3
, Adam Whysall
3
, Richard Russell
3
, Scott Lucas
2
, Gail L. Hahn
1
. SAMPE-conferentieprocedures. Charlotte, North Carolina, 20-23 mei 2019.
- "Uitdagingen van de geometrieën van structurele onderdelen in de lucht- en ruimtevaart voor high-rate compressievormen" door Aurele Bras
1
, Alejandro J. Rodriguez
2
, Richard Russell
1
, Timothy J. Luchini
3
, Travis Adams
3
, Adam Whysall
1
, Scott A. Rogers
2
, Scott Lucas
2
, Gail L. Hahn
3
. Society for the Advancement of Material and Process Engineering - North America.SAMPE Conference Proceedings. Seattle, WA, 4-7 mei 2020. Society for the Advancement of Material and Process Engineering - Noord-Amerika.
- "Snel hoogwaardig gieten van structurele xEP-2750 Prepreg voor compressiegieten" door Timothy J. Luchini 1 , Alejandro J. Rodriguez 2 , Scott A. Rogers 2 , Aurele Bras 2 , Adam Whysall 2 , Richard Russell 2 , Scott Lucas 2 , Gail L. Hahn 1 . SAMPE 2019.
1 The Boeing Company, Saint Louis, MO 63134, 2 Solvay Composite Materials, Anaheim, Californië, V.S. en 3 Solvay Composite Materials, Heanor, VK
- CompositesWorld-webinar:"Automotive-processen voor de productie van hoogwaardige aerospace-composieten" door Alejandro Rodriguez, Solvay Composite Materials, Anaheim, Californië, VS
Materiaal- en procesdoelen
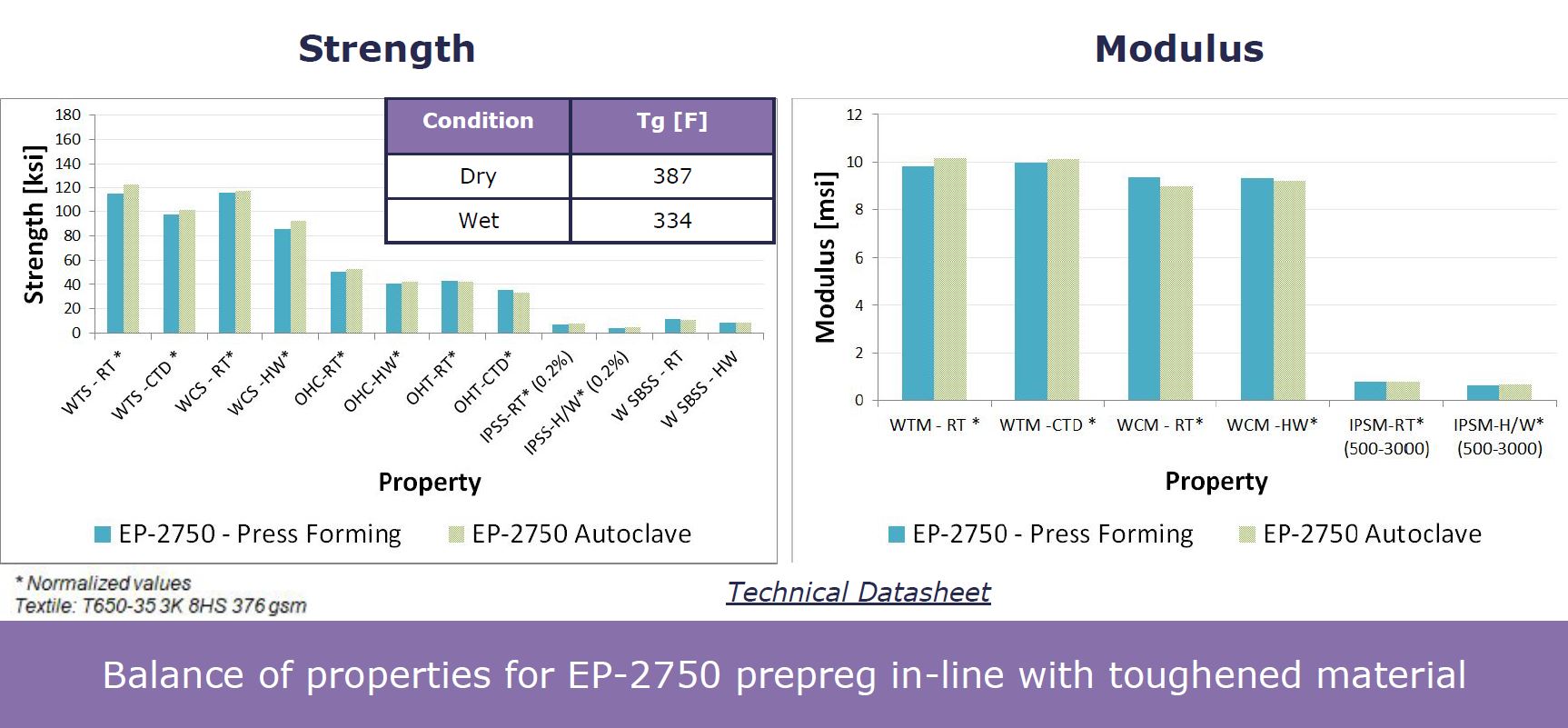
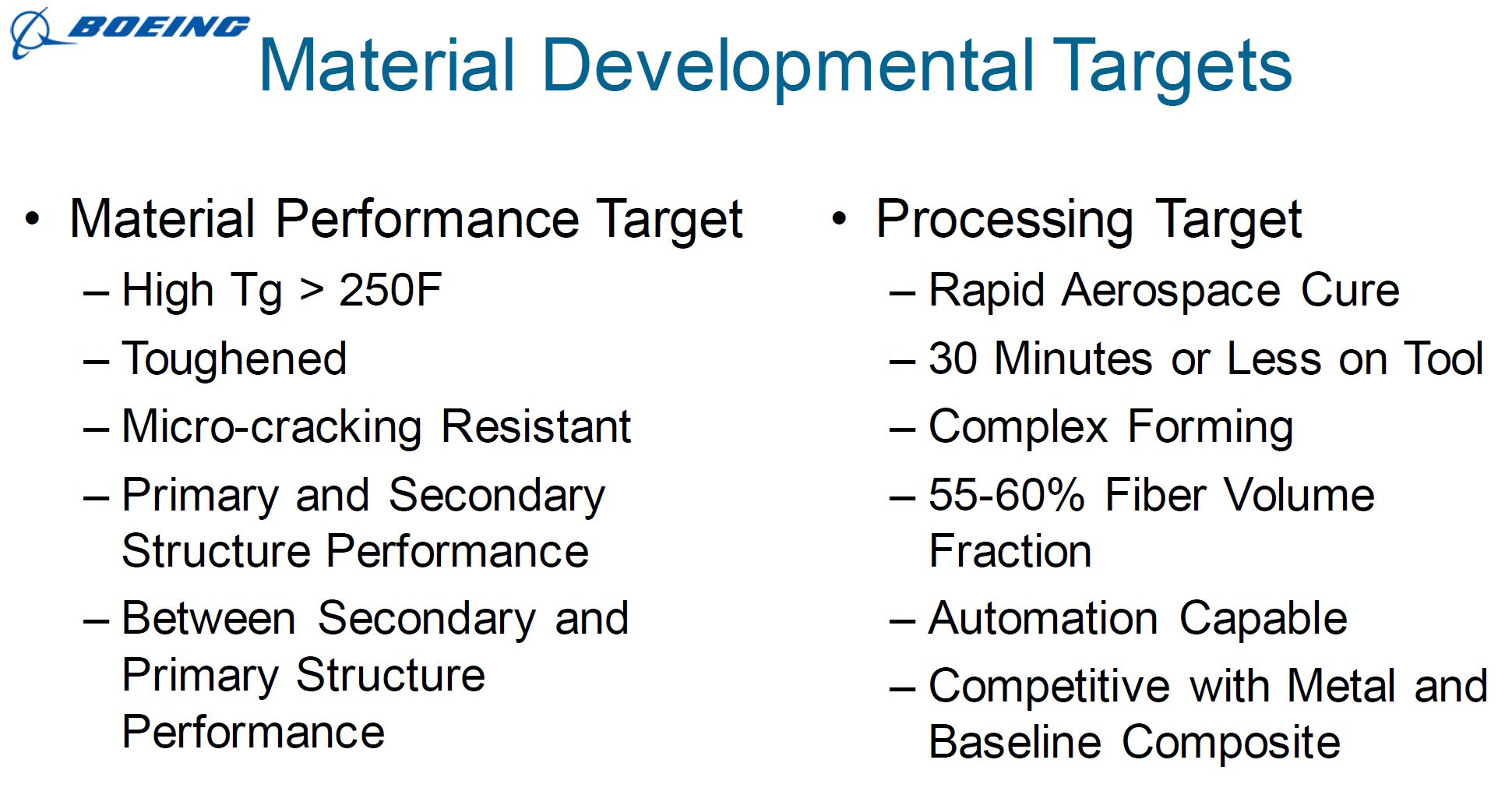
CYCOM EP2750 is ontwikkeld om te voldoen aan de prestatiedoelstellingen die door Boeing zijn vastgesteld voor een door de ruimtevaart geharde epoxy, met een evenwicht tussen glasovergangstemperatuur (Tg) tot 350 ° F, goede kerfeigenschappen - bijv. open-gatcompressie (OHC) en open-gatspanning (OHT) — en bestand tegen oplosmiddelen. Deze nieuwe klasse prepreg is toepasbaar op zowel primaire als secundaire aerostructuren en is compatibel met meerdere versterkingen (bijv. koolstof en glasvezel).
CYCOM EP2750 is ook ontwikkeld met de mogelijkheid om de productie op te schalen met behulp van geautomatiseerde verwerking en persgieten. Dit omvat een uithardingstijd op het gereedschap van 15-30 minuten bij 330-370°F, met een naharding van 1 uur bij 350°F. Deze takttijd van 30 minuten of minder maakt een jaarlijks productievolume van 10.000 onderdelen per gereedschap mogelijk.
Solvay gebruikte twee varianten van persvormen tijdens het RAPM-programma:vormen met een veerframe en dubbel diafragmavormen (DDF). Beide gebruiken het principe om een platte plano vast te houden en deze door een infrarood (IR) voorverwarmfase te voeren voordat deze in een bijpassende metalen gereedschapsholte wordt getransporteerd. De pers sluit vervolgens de stalen mal volgens een geautomatiseerd programma en oefent volledige druk uit op de prepreg voor de resterende tijd op het gereedschap.
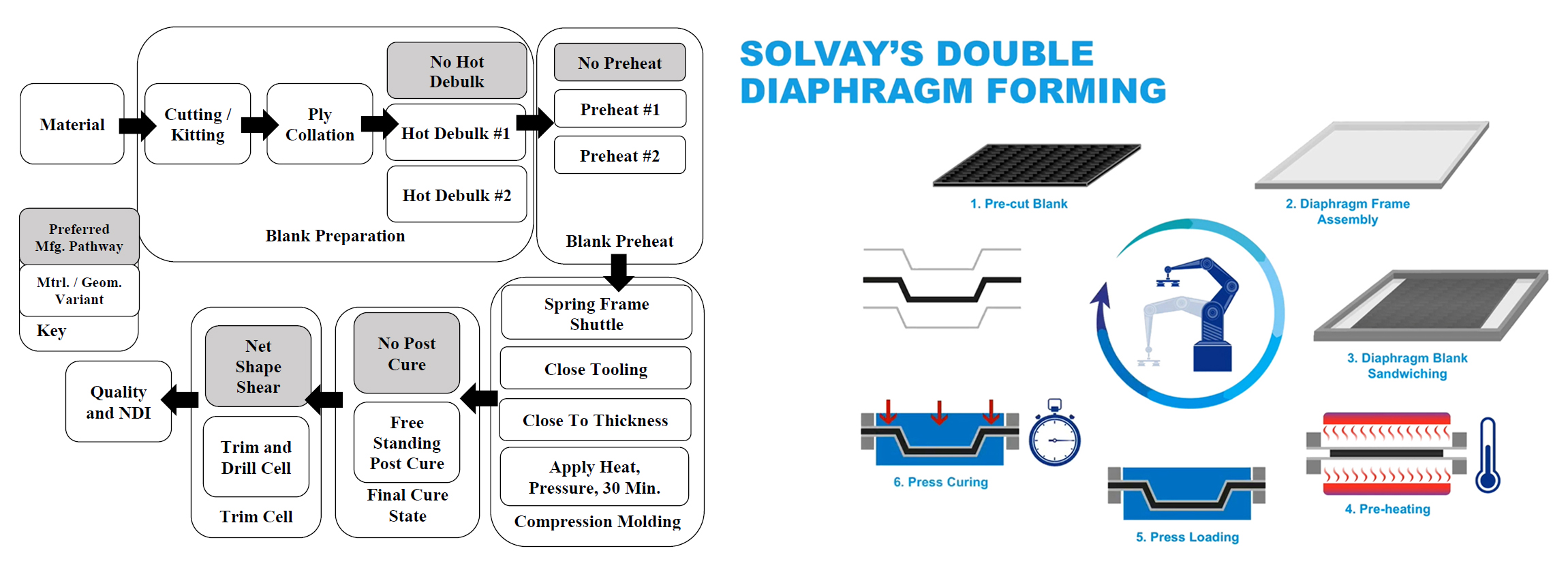
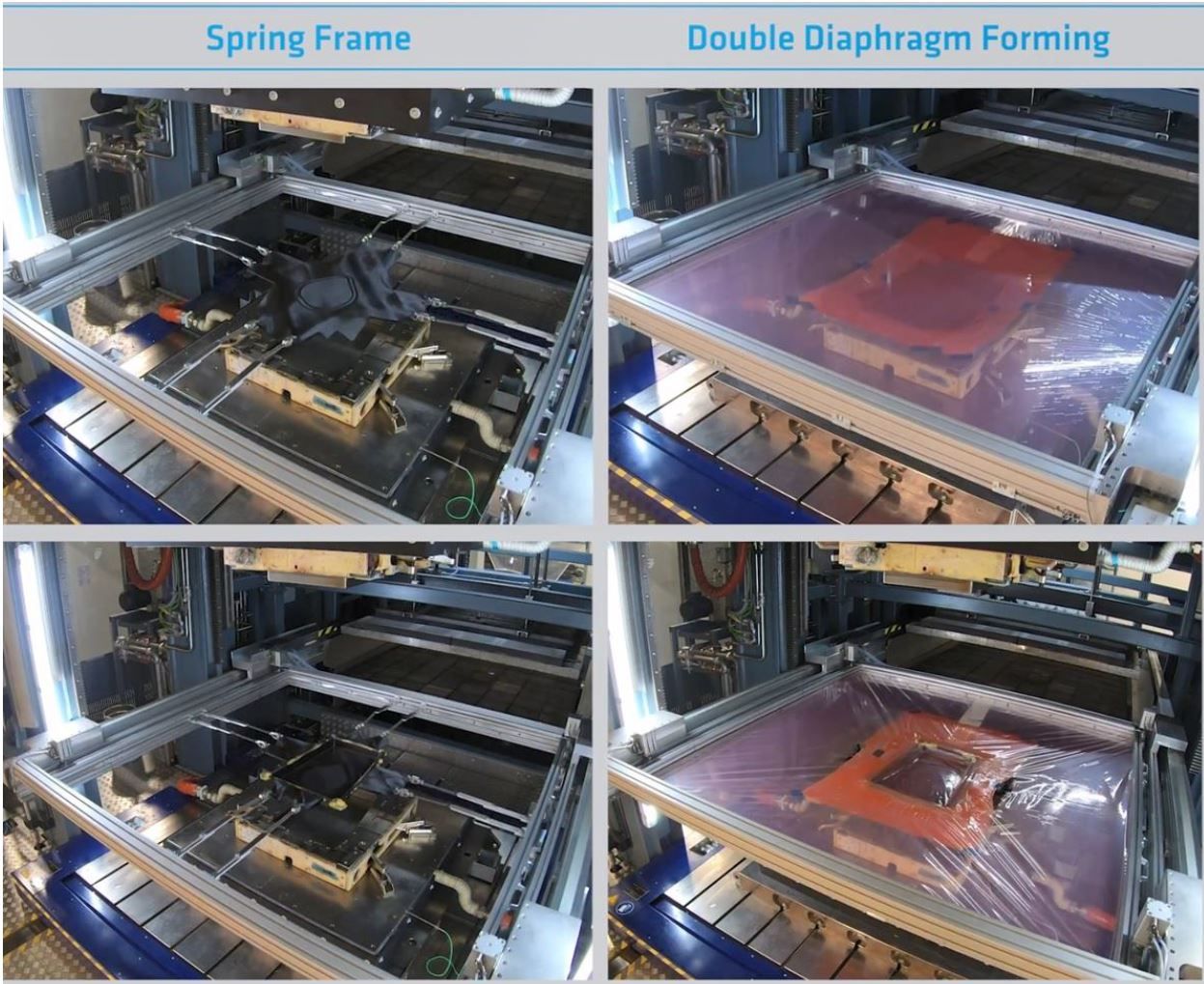
Zowel het vormen met een verend frame als DDF maken gebruik van op elkaar afgestemde metalen gereedschappen en bieden een hot-in, hot-out-benadering, waardoor het opwarmen en afkoelen van het gereedschap wordt geëlimineerd, voor een productie met hoge snelheid. Beide werden gebruikt om met succes meerdere soorten complexe geometrische onderdelen te vormen met pad-ups, verticale flenzen en diktevariaties van 3,8 tot 8,9 millimeter. Deze onderdelen zijn gemaakt in het applicatiecentrum van Solvay in Heanor, VK. Hoewel niet beschikbaar tijdens RAPM, beschikt Heanor nu over een volledig geautomatiseerde persvormlijn van prepregrol tot gegoten onderdeel, waardoor een takttijd van 15 tot 60 minuten wordt bereikt voor lucht- en ruimtevaartonderdelen gemaakt met EP2750 en takt. tijden van 3 minuten of minder voor kleine tot middelgrote onderdelen met prepregs voor auto's. Solvay ziet meerdere voordelen in het DDF-proces, waaronder:
- Eliminatie van voorvormstap – 2D blanco naar 3D onderdeel
- Geen schimmelverwijdering of reiniging vereist
- Vermindering van hulpmaterialen (bijv. ontluchter, ontluchter, zakken, tape) versus autoclaaf
- Verbeterde 'buy-to-fly' vs. veerframe, omdat er minder overtollig materiaal nodig is voor het bevestigen van veerklemmen.
Volledige vs. gedeeltelijke impregnering handhaaft druk
Kenmerken van EP2750 die persvormen vergemakkelijken, zijn onder meer de lage kleefkracht voor geautomatiseerde pick-and-place handling en de volledig geïmpregneerde aard in vergelijking met CYCOM 5320-1, die gedeeltelijk is geïmpregneerd om randademhaling te vergemakkelijken, wat nodig is voor holtevrije laminaten met OOA-verwerking. Compressiegieten maakt echter gebruik van een zeer snelle, geforceerde harsstroom vanwege de hogere toegepaste drukken - bijv. tot 350 psi (typisch maximum voor EP2750) vergeleken met 35 psi gebruikelijk bij autoclaafverwerking en 14,7 psi bij alleen vacuüm OOA-verwerking.
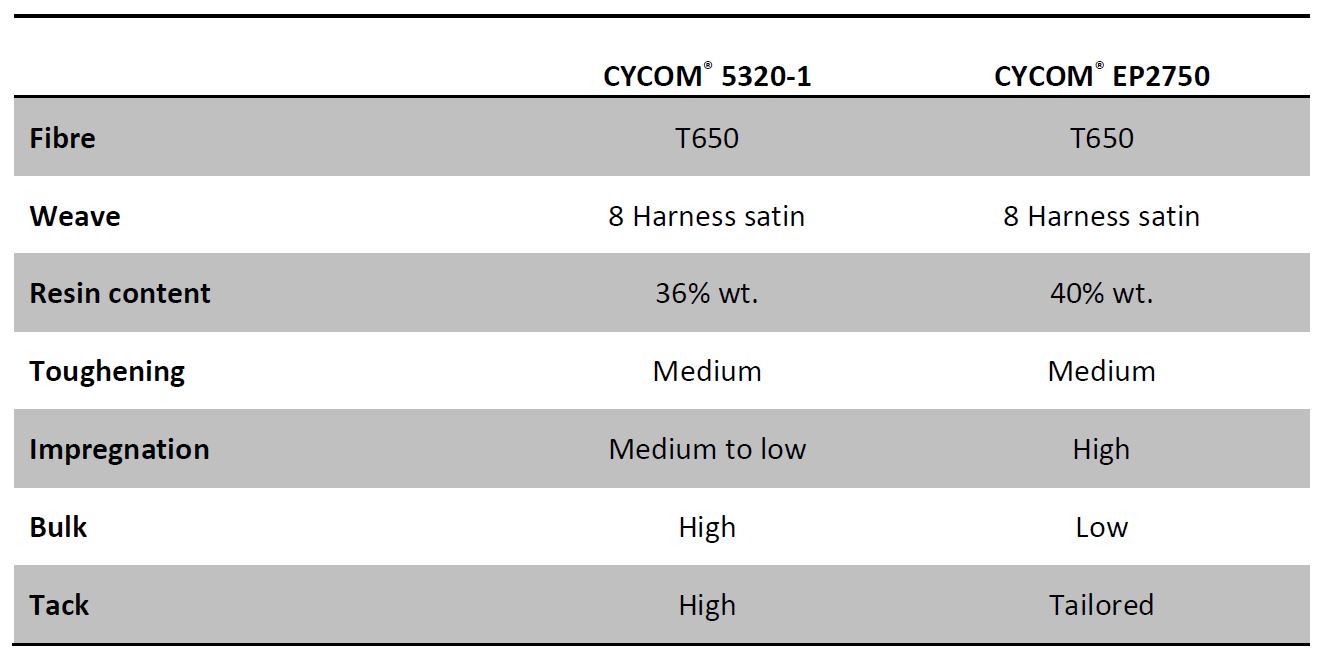
Met een meer volledig geïmpregneerde prepreg, hoewel het harsgehalte slechts iets hoger is - 40% in CYCOM EP2750 vergeleken met 36% in CYCOM 5320-1 - handhaaft hydrostatische druk tijdens verdichting en uitharding in de bijpassende metalen gereedschapsholte, wat resulteert in minder risico voor droge gebieden, inconsistente dikte van uitgeharde onderdelen (CPT), rimpels en andere defecten terwijl een goede oppervlaktekwaliteit wordt gegarandeerd.
Solvay heeft met name een gepatenteerde Transformer Film ontwikkeld om de hydrostatische druk te verhogen bij gebruik van CYCOM 5320-1 prepreg met een lager harsgehalte. Toegepast op de lay-out van het onderdeel voorafgaand aan het persgieten, verhoogt de Transformer Film het harsgehalte en hielp het de CPT aan de vereisten te brengen in RAPM-proeven voor het vormen van onderdelen.
RAPM onderdelen gietproeven
Zoals uitgelegd in het hoofdartikel van CW van mei 2020, was CYCOM EP2750 een van de primaire materialen die werd getest in RAPM's thermohardende prepreg-track. Pathfinder-onderdelen getest in de eerste productie- en ontwikkelingsfase inbegrepen
TS-RAPM-001 en -009 toegangspanelen met kralen, TS-RAPM-002 rib en TS-RAPM-003 gebogen C-kanaal. De onderdelen zijn ontworpen bij Boeing (meerdere locaties wereldwijd), het gereedschap is gemaakt bij C-Con GmbH (München, Duitsland), de onderdelen zijn vervaardigd in het Solvay's Applications Center in Heanor, VK en vervolgens getest in Solvay Anaheim, Californië, VS en Boeing St. Louis, Mo., VS
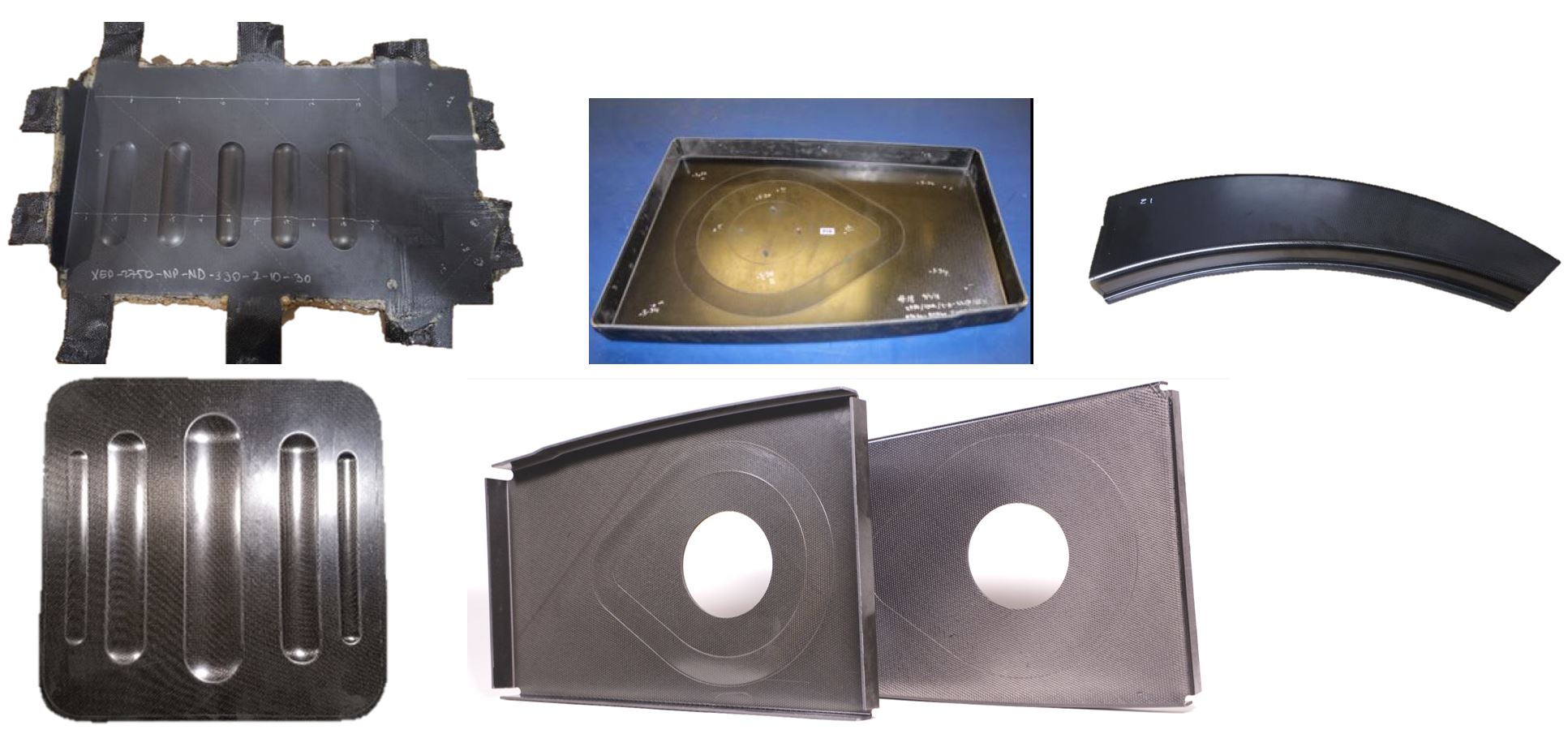
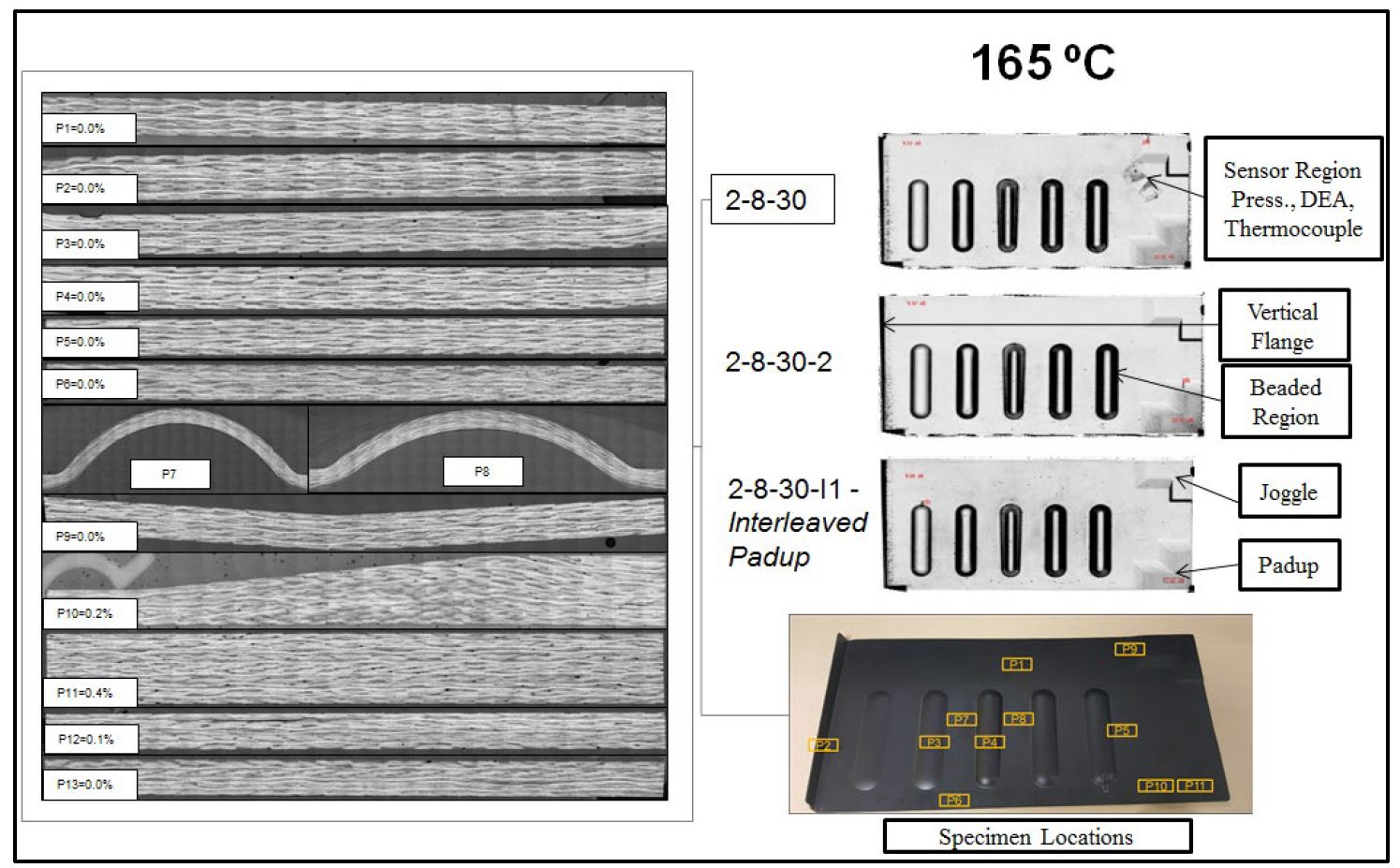

De oppervlaktekwaliteit werd geëvalueerd met behulp van niet-destructieve inspectie (NDI) en geselecteerde panelen werden doorgesneden op porositeit, korte bundelafschuiving, vezelvolumefractie, harsgehalte, mate van uitharding en glasovergangstemperatuur.
Porositeitsniveaus van minder dan 0,5% werden gemakkelijk bereikt, toegeschreven aan de hoge consolidatiedrukken van persvormen. Hoewel de procesparameters voor elk afzonderlijk onderdeel moesten worden geoptimaliseerd, bleek het proces, eenmaal vergrendeld, herhaalbaar te zijn.
TS-RAPM-009 kralenpaneel
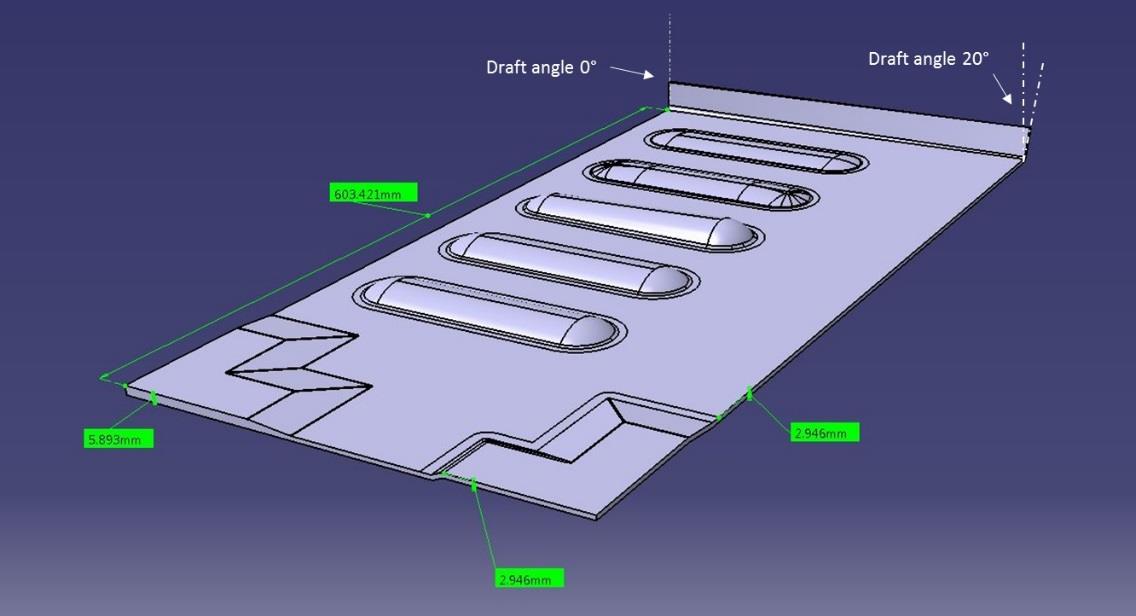
Dit 600 millimeter lange platte deel had parallelle kralen met verschillende geometrieën. De dikte nam toe van 3 tot 6 millimeter in één hoek (pad-up), terwijl de tegenoverliggende hoek een constante dikte had. De tegenoverliggende rand omvatte een verticale flens met een diepgangshoek die lineair varieerde van 0° tot 20°.
Slipperen van opvullingen
De eerste proeven werden uitgevoerd met pad-ups die op het oppervlak van de lay-up waren gestapeld. Omdat de opvullagen zich echter dicht bij de rand van het onderdeel bevonden, was het mogelijk dat ze uit het onderdeel werden geperst, wat resulteerde in een gebied met lage druk tijdens het uitharden en porositeit. De oplossing was om de opvullagen in de laminaatstapel te verweven. Het risico van wegglijden en porositeit werd niet gezien in latere delen waar de opvullingen zich niet bij de randen bevonden en effectief werden opgesloten door omringend materiaal.
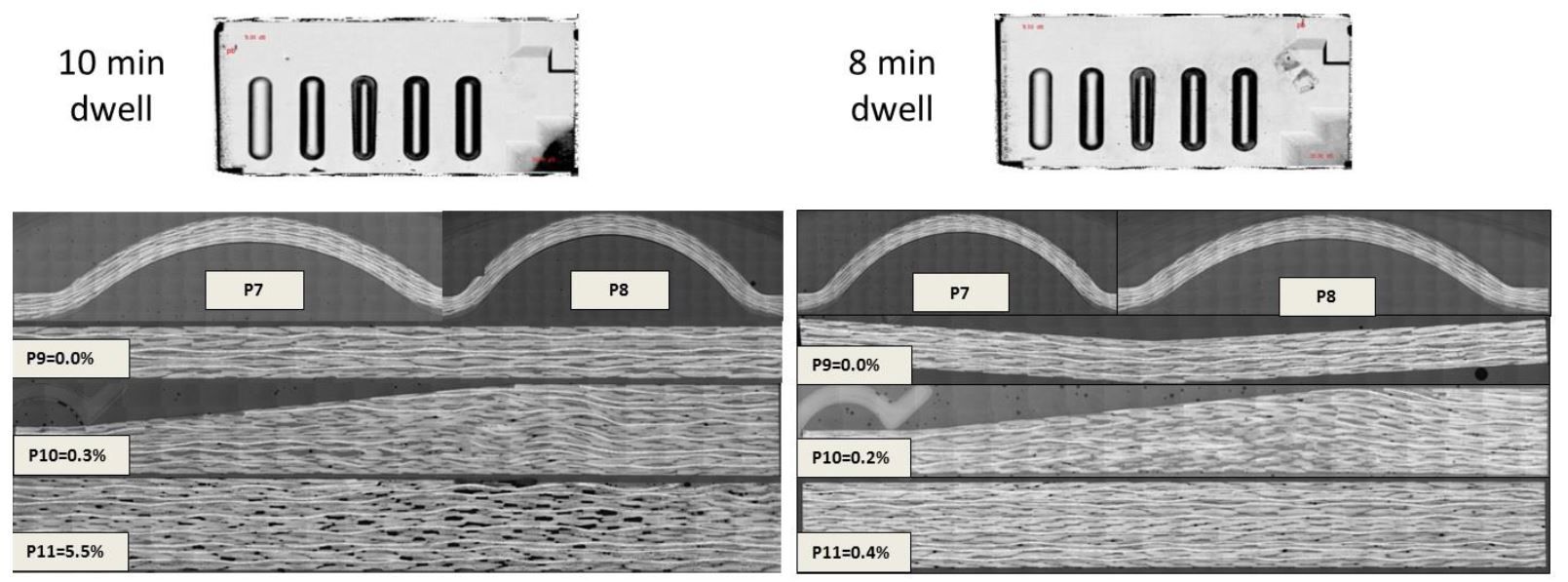
Porositeit met verblijftijd
Verhoogde porositeit werd ook gezien als de verblijftijd te lang was. Panelen met kralen die waren gemaakt met een verblijfsduur van 8 minuten hadden een lager gehalte aan lege ruimte dan die gemaakt met een verblijfsduur van 10 minuten. Dit was met name het geval in het opvulgebied, waar het leegtegehalte 5,5% was voor de verblijfsduur van 10 minuten en 0,4% voor de verblijfsduur van 8 minuten. De kortere verblijfsduur handhaaft een hoge harsstroom, waardoor de vezels effectief worden bevochtigd en de druk in de gereedschapsholte wordt gehandhaafd tijdens het uitharden.
Door de langere verblijftijd konden de harsstroom en -druk afnemen, vooral in het opvulgebied, vanwege de nabijheid van de rand van de gereedschapsholte, die geen afschuifrand of vermindering in doorsnede had. Zo nam de druk in de gereedschapsholte af aan de rand van het onderdeel, vooral in dikkere gebieden waar de doorsnede groter was. De afwezigheid van druk verhoogde hier ook het risico op slippen van de opvullagen. "Bij het ontwerpen van gereedschappen zal een vermindering van de doorsnede in de omgeving van de gereedschapsholte helpen bij het opbouwen en behouden van druk, met name voor onderdelen met verschillende diktes", legt Gail Hahn uit, Boeing-onderzoeker en hoofdonderzoeker van het RAPM-project. "Je moet een vorm van knijpen of verzegelen presenteren om een staat van hydrostatische druk in de holte aan te moedigen."
TS-RAPM-002 rib
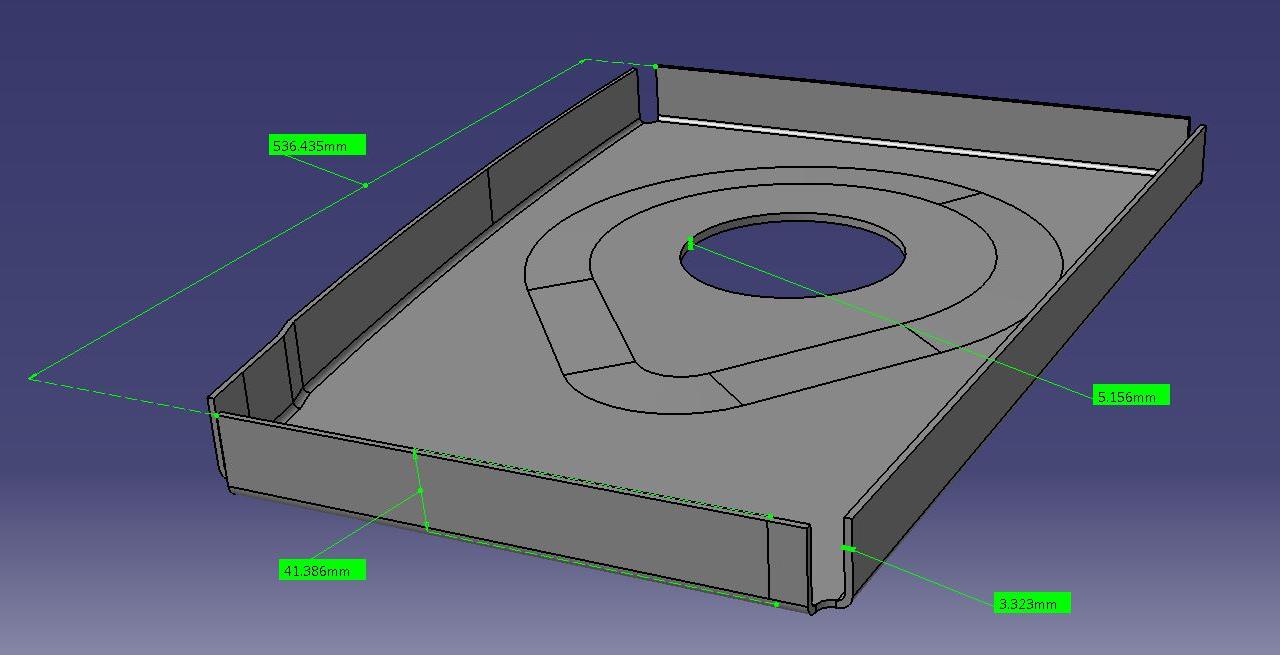
Nadat de verwerkingsparameters waren vastgesteld voor de TS-RAPM-009 kralenpanelen, werd het proces herhaald voor de TS-RAPM-002-rib, die 540 millimeter aan de langste rand was. De rib bouwde dikte in het midden op van 3,3 tot 5,2 millimeter en de diepte van de trek was 42 millimeter op het laatste getrimde deel. Alle vier de randen hadden verticale flenzen. Merk op dat een inspringende compensatiehoek werd bepaald tijdens de proeven met het kralenpaneel en vervolgens werd toegepast op de gereedschapsgeometrie van de rib. Proeven met panelen met kralen leidden ook tot een hoger spanningsvermogen en modulariteit van de veerlocatie op het veerframe.
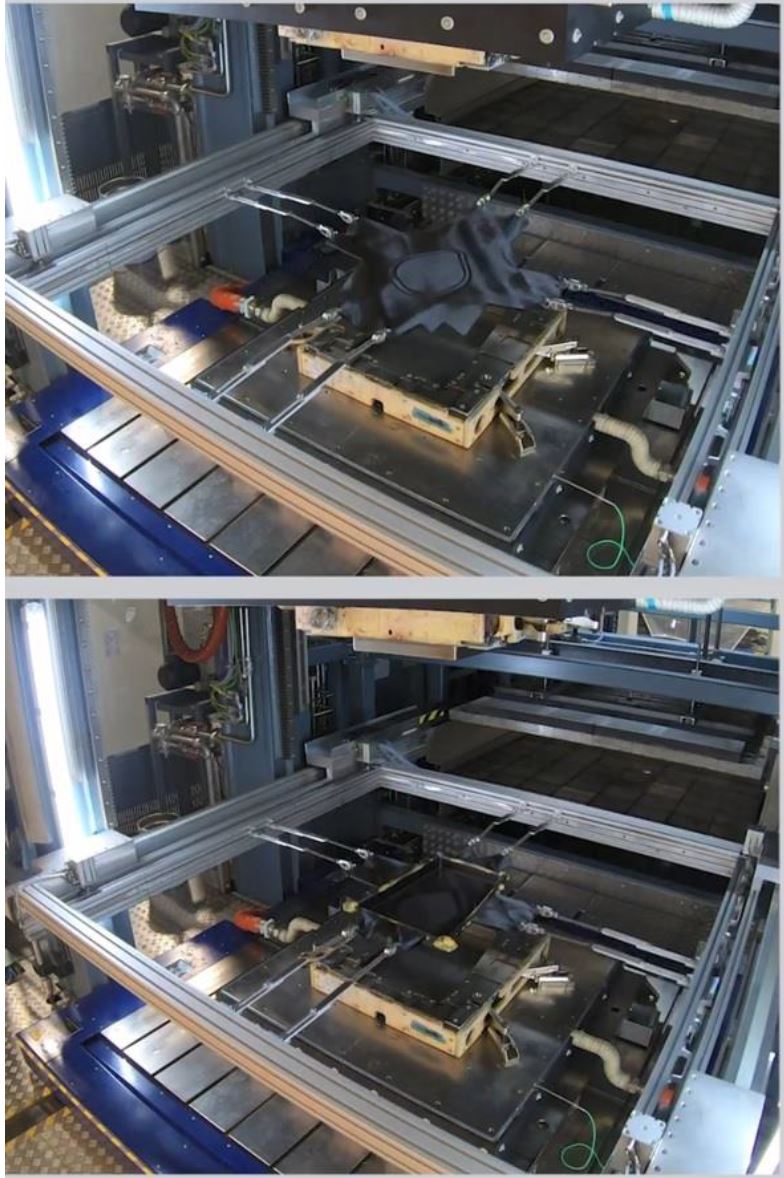
Overtollig materiaal voor klemmen
Ribben werden gemaakt met behulp van zowel veerframe-vormgeving als DDF. Door de diepe trek van de ribbe was er overtollig materiaal nodig om de frameveerklemmen te bevestigen, maar dit kon worden verminderd bij gebruik van DDF. Een ander probleem was dat het ontwerp van het gereedschap de ruimte voor de veerklemmen beperkte om zich dicht bij de gereedschapsholte te bevinden.
Variaties in CPT
De uitgeharde laagdikte (CPT) was hoger op de vlakke delen van de ribbe dan op de verticale randen. Er werd geredeneerd dat de geometrie van het onderdeel de hars binnen het centrale vlakke gebied hield, waarbij werd opgemerkt dat de verticale flenzen als een harsafdichting fungeerden. Dit hielp bij de verdichting en het afwerken van onderdelen in het centrale vlakke gebied. De verticale flenzen hadden echter last van sterke afschuiving tijdens het sluiten van het gereedschap, wat oppervlakteruwheid veroorzaakte maar geen porositeit (zie porositeitsgegevens hieronder). CYCOM EP2750, een materiaal met een lager volume, hielp dit effect te verminderen — de lagere dikte verminderde de afschuiving.
Variaties in baandikte met prepreg-harsgehalte
Kwaliteitsonderzoeken toonden herhaalbare ribben met een porositeit <0,1% en minimale vezelrimpels/golfvorming. Hoewel werd aangenomen dat variatie in de onderdeeldikte zou worden geminimaliseerd met aangepaste malverwerking, bleek uit onderzoek van materiaalverwerkingsparameters en CPT van het voltooide onderdeel dat hoewel de gereedschapsopening in de verticale flenzen van de ribbe vast en consistent was, de baandikte als functie kon variëren van het prepreg-harsgehalte (minder dan +/- 2%) en proces - CPT kan variëren tussen de flenzen en het web omdat hars de kans kreeg om in de holte te migreren.
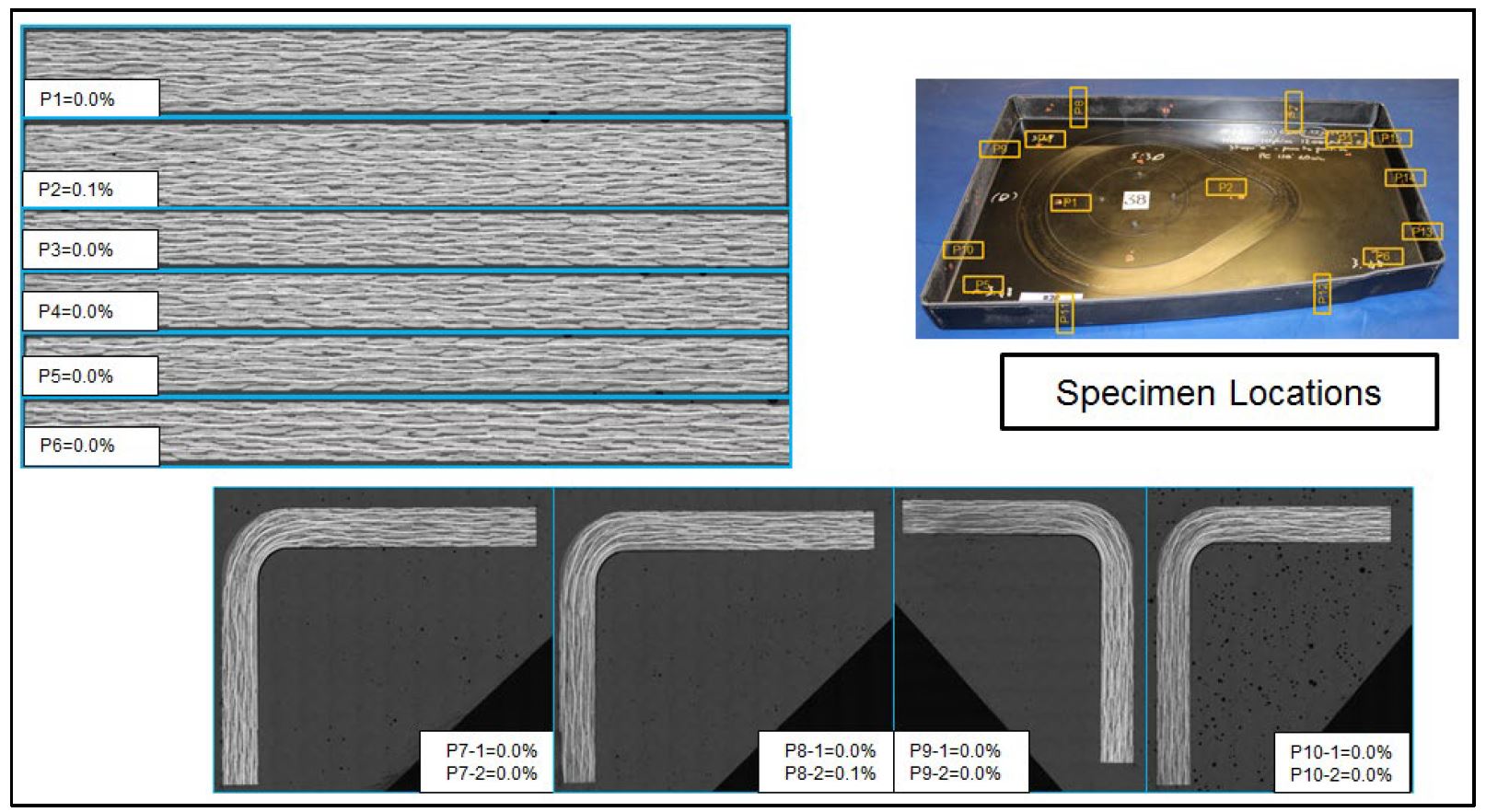
TS-RAPM-003 gebogen C-kanaal
Dit onderdeel was 640 millimeter lang met een 40 millimeter diep U-profiel op het laatste bijgesneden stuk. De binnenstraal van de sectie was groter dan de buitenstraal en de dikte nam toe van 6,6 millimeter in het smalle deel tot 8,8 millimeter aan het brede uiteinde. Het C-kanaaldeel was door zijn dikte aanzienlijk zwaarder dan de eerder besproken delen. Daarom had het veerframe meer bevestigingspunten nodig dan bij de vorige onderdelen.
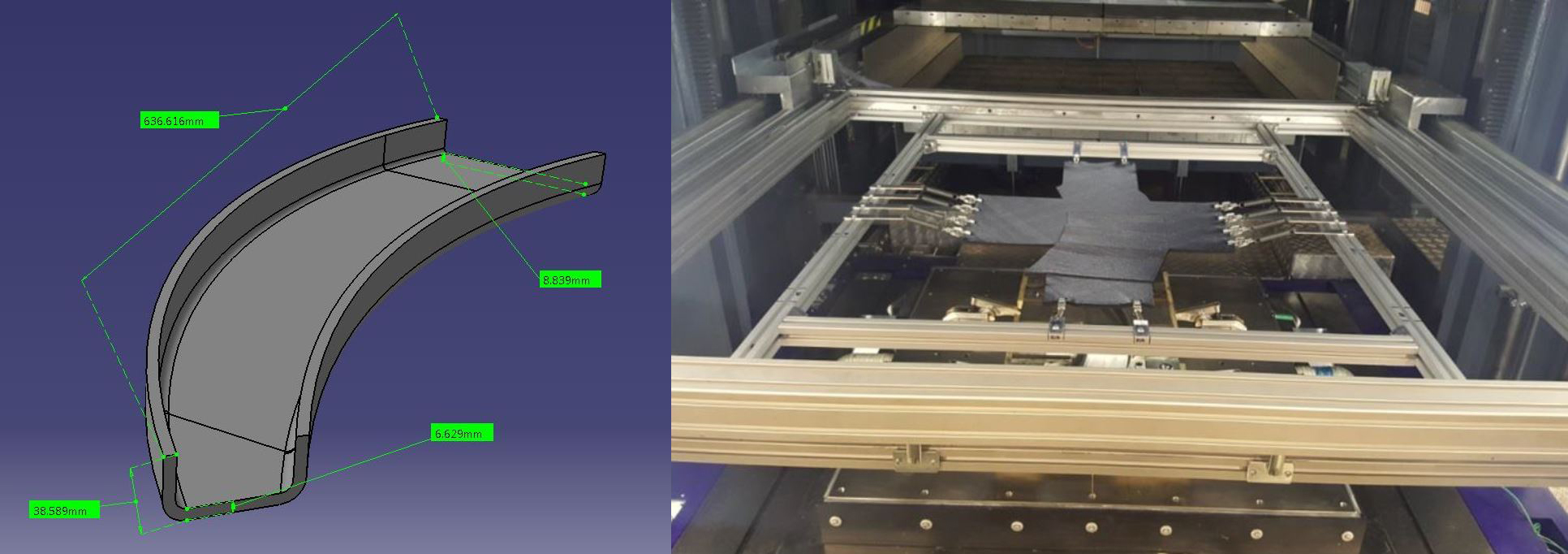
Dubbele rust om de druk in dikke delen te behouden
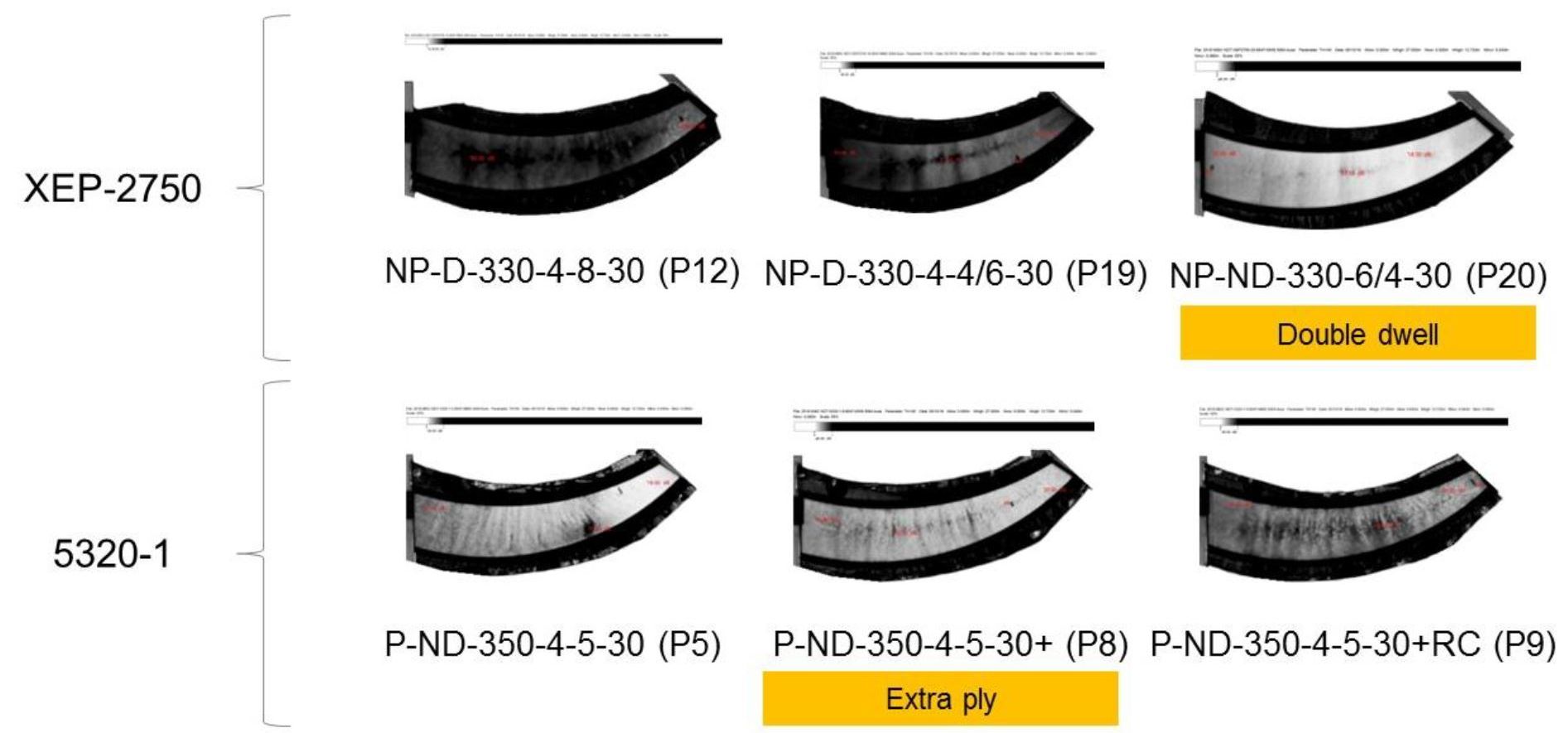
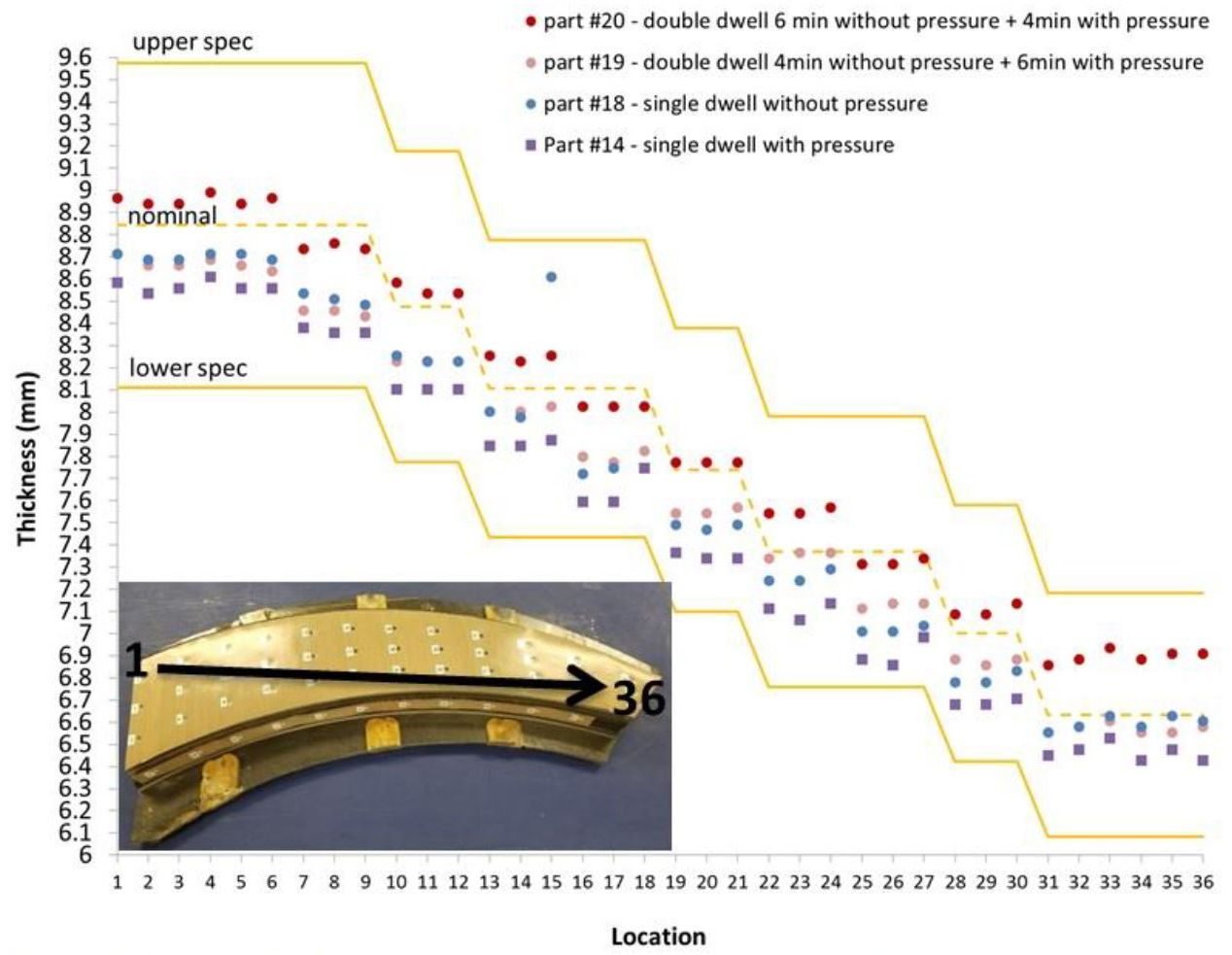
C-scans van gegoten onderdelen markeren een rimpel die zich voortplant van de binnenradius naar de buitenradius voor onderdelen die voorgeconsolideerde blanco's gebruiken. De grijsschaal geeft aan dat de rimpels ook porositeit hebben.
Deze rimpels en porositeit werden verwijderd voor CYCOM EP2750 prepreg-onderdelen met behulp van een “dubbele rust” werkwijze. Dit bestaat uit het uitoefenen van een bepaalde hoeveelheid druk tijdens de verblijftijd onmiddellijk na de viscositeitsopbouw van het materiaal. “Dit werd bepaald aan de hand van de gegevens die door de pers werden aangeleverd en de tools tijdens de ontwikkeling van het proces”, legt Hahn uit. “Kortom, er zijn twee stappen van progressieve drukopbouw voorafgaand aan volledige druktoepassing. Als resultaat heeft het druk-versus-tijdprofiel een soortgelijke vorm als het harsviscositeitsprofiel. Een eerste verblijf bij bulkdikte wordt gebruikt om de harsviscositeit te verhogen om te voorkomen dat de materiaallading [blanco of voorvorm] dunner wordt. Als de lading een aanzienlijke dikte heeft, worden twee verblijfstijden gebruikt om drukverlies als gevolg van harskrimp te voorkomen. De eerste staat op een tussenruimte van X en de tweede op een tussenruimte van Y, met Y
Fig. 18 hierboven toont het effect van dubbele stilstand op de dikte van het C-kanaal. Door de druk op de harsviscositeit af te stemmen, kon er meer hars in het onderdeel worden vastgehouden, waardoor de vezels werden bevochtigd voor een lage porositeit en opbouwdikte om de vereiste nominale maar behouden lage vezelvervorming te bereiken. Het RAPM-team benadrukte echter dat dit proces met dubbele stilstand alleen de voorkeur heeft voor dikkere onderdelen, en merkt op dat het CPT-oneffenheden kan veroorzaken in delen van verschillende diktes.
De RAPM-onderdeelproeven die hier worden besproken, hebben kennis bijgedragen aan de snelle fabricage van structurele onderdelen in de ruimtevaart met behulp van prepreg-persgieten. Geleerde lessen zijn onder meer:
RAPM heeft aangetoond dat prepreg-compressievormen hoogwaardige constructies van ruimtevaartkwaliteit kunnen produceren, terwijl de cyclustijd en arbeid worden verminderd. Hierdoor kunnen composieten beter concurreren in handelsstudies voor lucht- en ruimtevaarttoepassingen, terwijl ze tegelijkertijd een grotere gewichtsbesparing en betere prestaties van componenten opleveren (bijvoorbeeld weerstand tegen corrosie, barsten en vermoeidheid, enz.).
Solvay en Boeing hebben samengewerkt om het nieuwe EP2750 prepreg-systeem te verfijnen, waarbij takt-tijden tot 20 minuten worden aangetoond, dankzij een combinatie van materiaalchemie, prepreg- en proceskennis en automatisering.
Naast de onderdelen voor Manufacturing Development die hierboven zijn besproken, heeft RAPM ook verschillende Challenge- en Transition-onderdelen geproduceerd, bedoeld om te uitdagen eerste ontwikkelingen en overgang kandidaten met potentieel om te winnen tegen bewerkt aluminium in defensietoepassingen. Deze omvatten:
De resultaten en lessen die zijn getrokken uit deze deelproeven en andere onderzoeken naar de productie van RAPM zullen in 2020/2021 worden gepubliceerd.
Solvay heeft ook geïllustreerd hoe EP2750 presteert in auto-onderdelen, zoals een B-stijl van 36 bij 16 bij 2 inch met een dikte van 0,0725 inch, bestaande uit 5 lagen Solvay THORNEL T650-35 standaard modulus 3K sleepkoolstofvezel in een 376 gram/vierkante meter 8-harnas satijnen stof. Dit onderdeel is gemaakt bij Solvay Heanor, V.K. met DDF. In vergelijking met geautoclaveerd standaard prepreg, biedt de combinatie van CYCOM EP2750 en DDF een reductie van 60% in cyclustijd en 85% in takt-tijd (tijd tussen het starten van het ene onderdeel en het volgende onderdeel op een productielijn - dwz de pulstijd van de lijn) .
RAPM geleerde lessen en verdere onderdelentesten
Proeven van Solvay-auto-onderdelen
Hars
- Compressiegieten versus spuitgieten:wat is het verschil?
- Compressiegieten:hoe het werkt
- Compressiegieten en gietvormen:voor- en nadelen
- Zeer efficiënt zuiveringsmiddel voor het blaasvormen van polyolefinen
- Hoge viscositeit PEEK voor spuitgieten en extrusie
- Transportband aangepast voor preform molding
- Derde patent verleend voor flexibele thermoplastische prepreg
- Solvay lanceert epoxy prepreg voor het persen van aerostructuren
- Compressie-RTM voor de productie van toekomstige aerostructuren
- Toray aerospace prepreg geoptimaliseerd voor vacuümgeassisteerd drukvormen
- Continue tapes, D-LFT ontmoeten elkaar in nieuw compressievormproces