Bocht in de weg:eerste gebogen gepultrudeerde auto-onderdelen
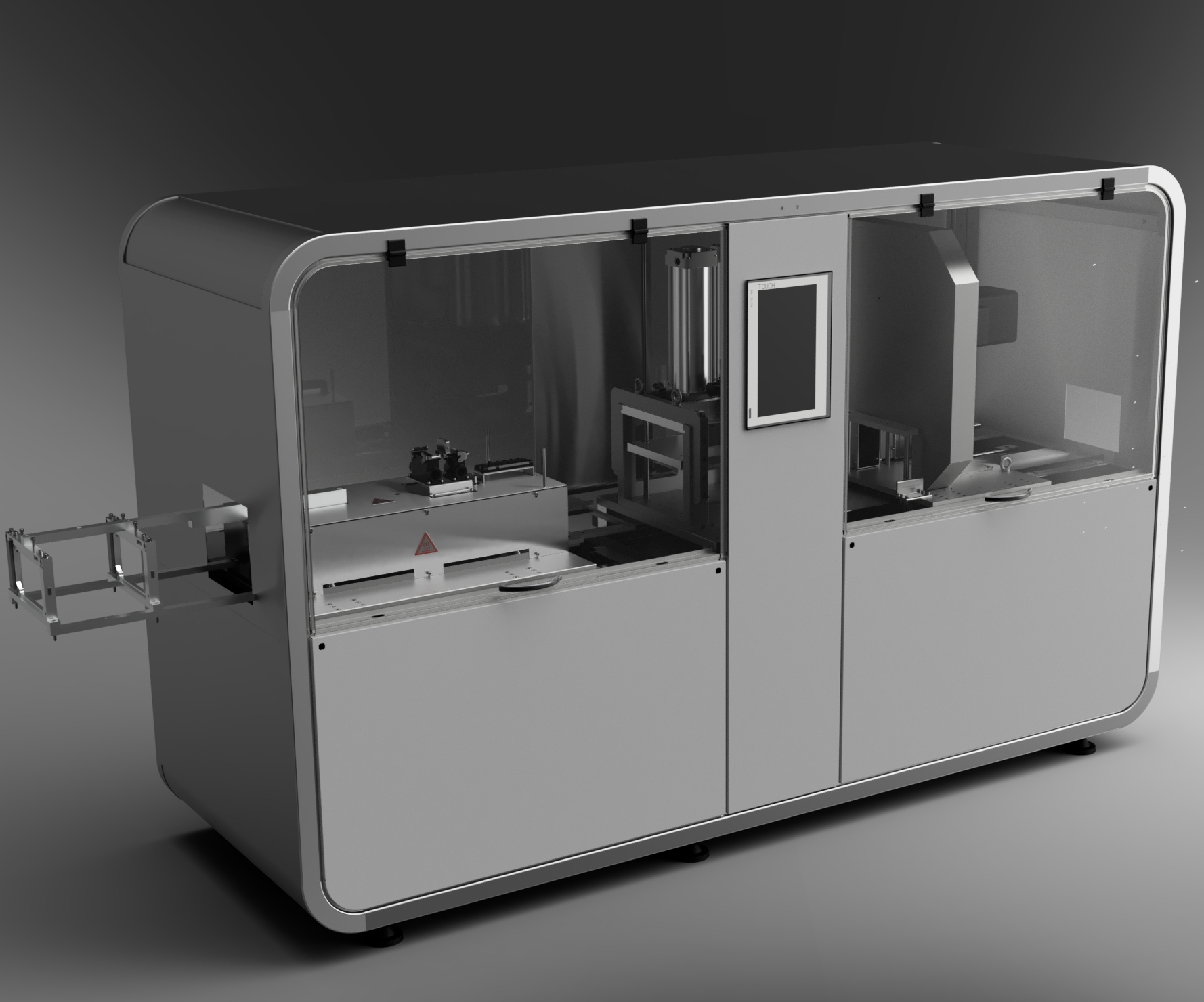
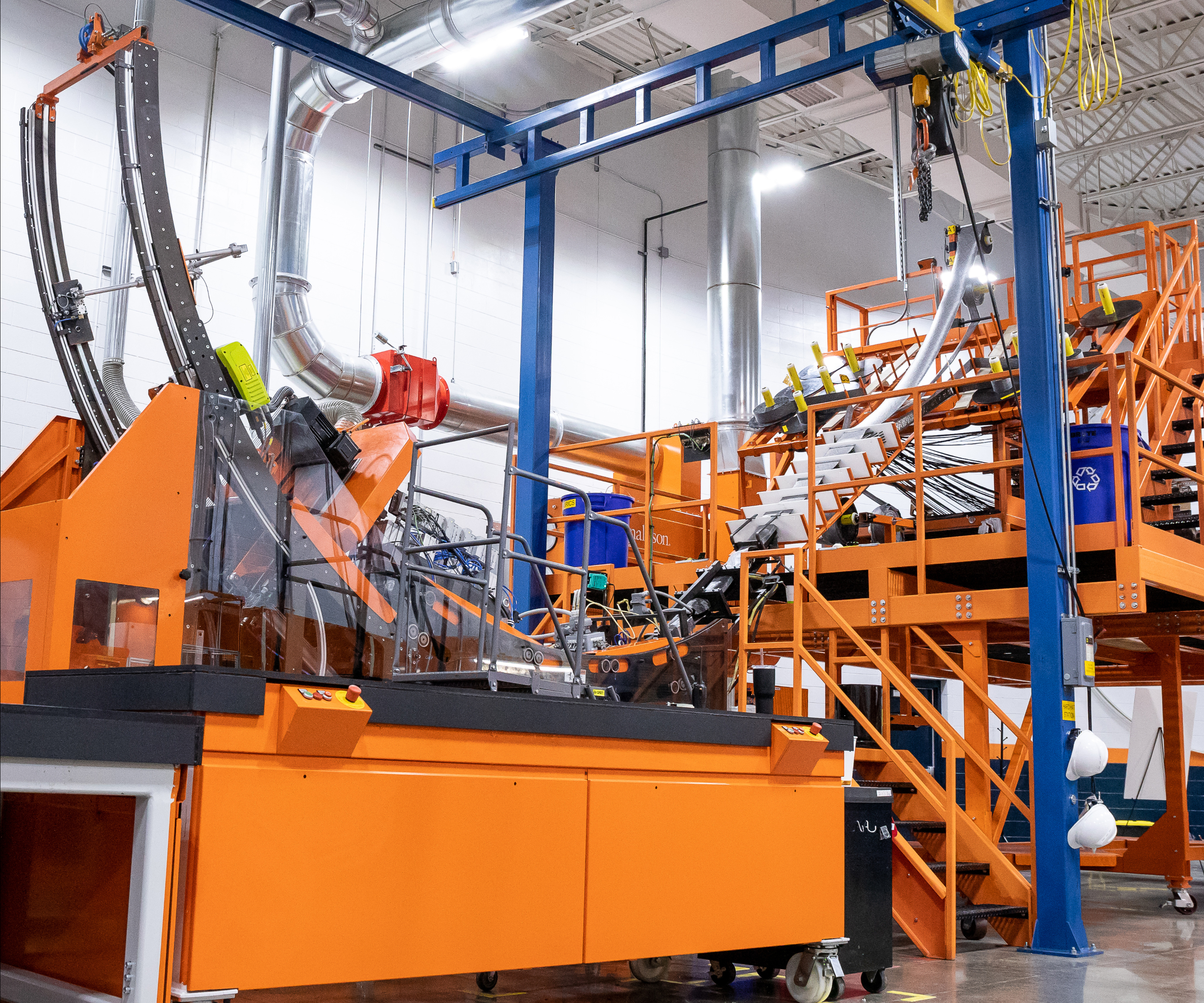
Pultrusie is een van de oudste vormprocessen voor thermohardende composieten en zou de eerste continue vezel zijn geweest thermohardend vormingsproces. Tegenwoordig wordt het gebruikt voor de productie van producten variërend van elektriciteitspalen tot raamkozijnen, evenals ladders, wapening en onderdelen voor windturbines. Eenvoudig te automatiseren met weinig arbeid en in staat om zeer structurele componenten te produceren - sommige vrij groot - tegen redelijke kosten en snelheid, traditionele pultrusie kan profielen produceren (hol of massief, symmetrisch of asymmetrisch) in bijna elke vorm die door een matrijs kan worden geperst . Die vorm moet echter wel een constante doorsnede/dikte hebben. In tegenstelling tot thermoplastische extrusie of extrusie van metalen buizen en pijpen - waar druk en warmte kan worden uitgeoefend op profielen tijdens de productie, of daarna op afgewerkte onderdelen, om ze in nieuwe vormen te buigen - was het ook moeilijk om pultrusie te gebruiken om iets anders te produceren dan rechte, lineaire profielen. Dat heeft natuurlijk het gebruik van pultrusie in veel industrieën beperkt, vooral in segmenten met een hoog volume zoals de automobielindustrie, die pultrusie zouden willen gebruiken, behalve dat er niet veel rechte balken op auto's zijn die goede kandidaten zouden zijn.
Dat begint te veranderen dankzij Thomas GmbH + Co. Technik + Innovation KG (TTI, Bremervörde, Duitsland), die een gepatenteerd proces heeft ontwikkeld om veel van de beperkingen van traditionele pultrusie te overwinnen. In feite is het eerste gebogen gepultrudeerde auto-onderdeel zojuist in commerciële productie gegaan met de lancering van de 2020 Chevrolet Corvette sportwagen van General Motors Co. (Detroit, Mich., V.S.) (zie het volledige artikel over de Corvette gepultrudeerde achterbumperbalk). Tier 1-leverancier Shape Corp. (Grand Haven, Mich., VS) produceert een gebogen achterbumperbalk voor de auto met behulp van TTI's radiuspultrusie-mould-proces in met koolstofvezel versterkt polyurethaan-acrylaat.
Dit is waarom dat zo belangrijk is.
Bewegend versus stilstaand
Bij conventionele lineaire pultrusie wordt een heen en weer bewegend treksysteem met grijpers gebruikt om droge versterkingen uit hun korven te trekken, door een bad waar ze worden geïmpregneerd met vloeibare thermohardende hars. Vervolgens worden de geïmpregneerde versterkingen in een stationaire verwarmde matrijs getrokken waar het profiel wordt gevormd en volledig uitgehard. Bij het verlaten van de matrijs koelt het bewegende profiel af (wordt nog steeds meegetrokken door de pull-off unit) en wordt vervolgens op lengte gesneden en verpakt.
Aanvankelijk was vezelversterking strikt beperkt tot unidirectionele rovings - met andere woorden, continu glas, koolstof of andere vezels die 0 graden ten opzichte van de trekas waren georiënteerd. In de loop van de tijd is er echter een verscheidenheid aan multiaxiale weefsels - zowel weefsels als non-crimp weefsels (NCF) - opgenomen in gepultrudeerde profielen, waardoor een reeks vezeloriëntaties mogelijk is zonder vervorming / vezelbeweging. Bijna elk thermohardend harssysteem kan worden gebruikt om versterkingen bij pultrusie te impregneren, hoewel een aanzienlijk aantal toepassingen polyurethaan gebruikt. In de afgelopen decennia is pultrusie zelfs aangepast om het gebruik van geprepolymeriseerde thermoplasten mogelijk te maken.
Veel kenmerken van conventionele pultrusie zijn ondersteboven gekeerd in het radiuspultrusieproces van TTI, maar het belangrijkste aspect om te begrijpen is dat bij radiuspultrusie de matrijs niet stationair is; het beweegt en trekt materiaal om ofwel een lineaire constante doorsnede of een constant gebogen profiel te creëren.
De matrijs, of een reeks matrijzen, beweegt niet alleen heen en weer over het profiel, vormt en hardt het materiaal uit terwijl beide langs een baan voortbewegen - in dit geval met het profiel in een enkele richting en de matrijs in beide richtingen - maar de matrijs trekt ook de droge versterkingen door het harsbad en het uitgeharde profiel mee naar de grijpers en snijder. Om een lineaire dwarsdoorsnede te produceren, bewegen zowel de mal als het profiel langs een recht stuk van de baan; om een gebogen doorsnede te produceren, bewegen de mal en het profiel langs een gebogen gedeelte van de baan.
"Bij deze technologie vervangt de matrijs effectief de heen en weer bewegende trekker, die wordt vervangen door stationaire grijpers die openen en sluiten, maar verder niet bewegen", legt Sebastian Mehrtens, hoofd verkoop bij TTI, uit. "De grijpers sluiten en ondersteunen het uitgeharde profiel wanneer het een vooraf gespecificeerde lengte bereikt en klaar is om te snijden, maar blijven verder open en laten het profiel naar de snijeenheid bewegen." Om het risico op uittrekken van vezels uit het hete materiaal te verminderen, zijn verwarmde matrijzen verchroomd.
Bovendien is het verkleinsysteem veel gemakkelijker te verzenden, kan het met slechts een vorkheftruck worden verplaatst, is het sneller op te zetten dan conventionele lijnen en vereist het veel minder ruimte op de fabrieksvloer. “Dit kan in sommige toepassingen interessante voordelen hebben”, merkt Mehrtens op. “De machine kan bijvoorbeeld worden opgesteld in de buurt van een brugrenovatie om structurele elementen te produceren als dat nodig is. Of het kan worden opgezet terwijl er een nieuwe snelweg is aangelegd en wapening kan produceren die op de werklocatie op maat kan worden gesneden.” Nog een ander voordeel van pullCUBE is de veiligheid van de werknemers, aangezien de unit volledig is omsloten en operators hun handen niet zullen verbranden aan hete schimmeloppervlakken, bekneld raken door grijpers of snijden door de zaag.
Hars
- De weg naar industriële IoT-beveiliging
- DARVA – de evenementassistent
- De zekering 1 afdrukken met de zekering 1
- De voordelen van onderdelenstandaardisatie benutten
- Plastic onderdelen kopen:de ultieme checklist
- Een van de eerste commerciële portfolio's van duurzame TPE's
- Op pad met IoT
- De eerste composiet rompsectie voor de eerste composiet commerciële jet
- De PID-leercurve aanpakken
- De waarde van waterstraalsnijden in de geneeskunde
- De complete gids voor bewerkte onderdelen