Composieten versnellen de fabricage van betonnen gevels
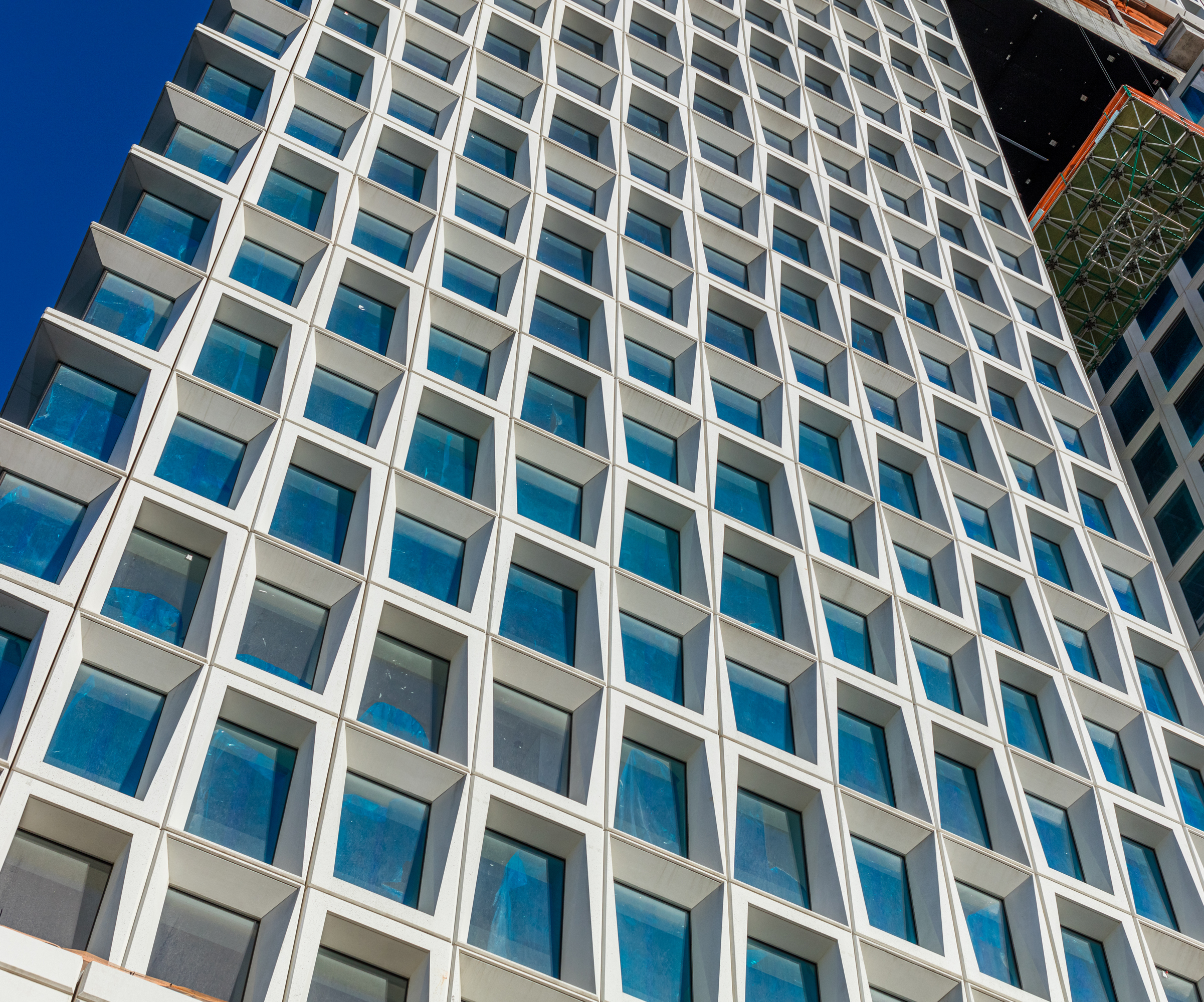
Elk gebouw met meerdere verdiepingen dat tegenwoordig wordt gebouwd, heeft een gevel nodig. Afgeleid van het Franse woord façade , die op zijn beurt afkomstig was van het Italiaanse facciata , het betekent 'gezicht'. Kortom, de gevel is de naar buiten gerichte constructie die het gebouw karakter, kleur en vorm geeft. Voor architecten zet de gevel de toon voor de rest van het gebouw en zegt veel over de architectonische intentie van de ontwerper.
Een gevel is ook functioneel. Het zorgt voor de structuur die ramen en deuren omringt, beschermt het gebouw tegen weersinvloeden en stoten en beïnvloedt de energie-efficiëntie van het gebouw. Een gevel kan worden opgebouwd uit verschillende materialen, waaronder composieten, steen, staal, glas of beton. Beton in een gevel kan vanwege zijn vormbaarheid worden gebruikt om een gebouw een zeer dimensionaal en visueel indrukwekkend uiterlijk te geven, vooral als de betonvormen gevarieerd zijn.
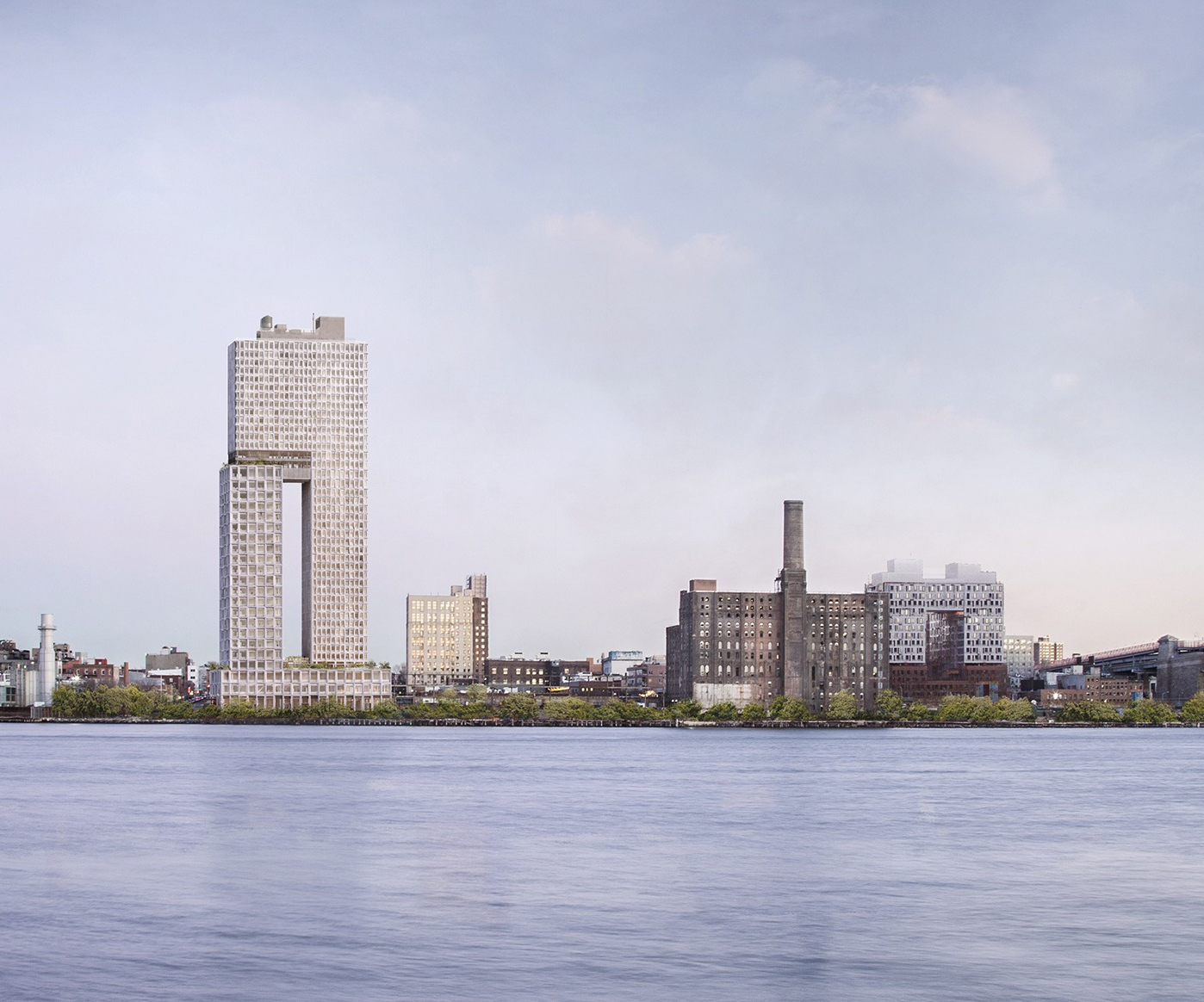
Suiker is koning
Dit was het geval bij Domino Park, een herontwikkelingsproject van 11 hectare langs de waterkant van Williamsburg in Brooklyn, NY, VS. In het hart van Domino Park ligt de 138 jaar oude Domino Sugar Refinery, die in 2004 werd gesloten en nu wordt gerenoveerd als kantoor- en winkelruimte. Een deel van Domino Park omvat verschillende nieuwe gebouwen, waaronder de 45 verdiepingen tellende One South First en de samengevoegde 10 Grand. Voor deze gebouwen heeft de architect COOKFOX (New York, NY) besloten om een betonnen gevel te gebruiken met meerdere oppervlaktehoeken, meerdere raamkozijnvormen en meerdere raamkozijnbreedtes om, van een afstand, losjes een gevoel van suikerkristalliniteit over te brengen, in in overeenstemming met de geschiedenis van de site.
Gate Precast Co. (Jacksonville, Fla., VS) won het contract voor de constructie van de betonnen gevel - in feite een reeks raamkozijnen - voor het One South First-project. Het bedrijf zou, zoals typisch is voor een betonnen gevel, de frames in zijn eigen fabriek fabriceren en vervolgens de afgewerkte frames naar de werklocatie verschepen waar ze met een kraan op hun plaats zouden worden gehesen voor installatie. Als Gate had besloten om de traditie te volgen, zou het houten mallen hebben gebouwd om alle betonnen frames te vormen. Gate besloot echter de traditie niet te volgen.
Om dit te begrijpen, ga terug naar 2017, toen Gate samenwerkte met het Precast/Prestressed Concrete Institute (PCI, Chicago, Illinois, VS) en Oak Ridge National Laboratory (ORNL, Oak Ridge, Tenn., VS) om een voorlopige beoordeling uit te voeren van het gebruik van additieve fabricage op groot formaat om composietmallen te bouwen voor in-plant prefab betonvorming. Deze beoordeling is gedaan met behulp van een BAAM (Big Area Additive Manufacturing) machine bij ORNL. BAAM is een additieve fabricagemachine van groot formaat met een bouwomhulling van 25 vierkante meter, mede ontwikkeld door ORNL en Cincinnati Inc. (Harrison, Ohio, VS) Gate, die zich ertoe heeft verbonden composietmallen te bouwen voor de One South First-gevel. Voor het project waren in totaal 80 mallen nodig, waarvan er 37 zouden worden bedrukt. De overige 43 zouden van hout zijn. Tegen de tijd dat deze beslissing werd genomen, waren de tijdlijnen voor de levering van de matrijs krap.
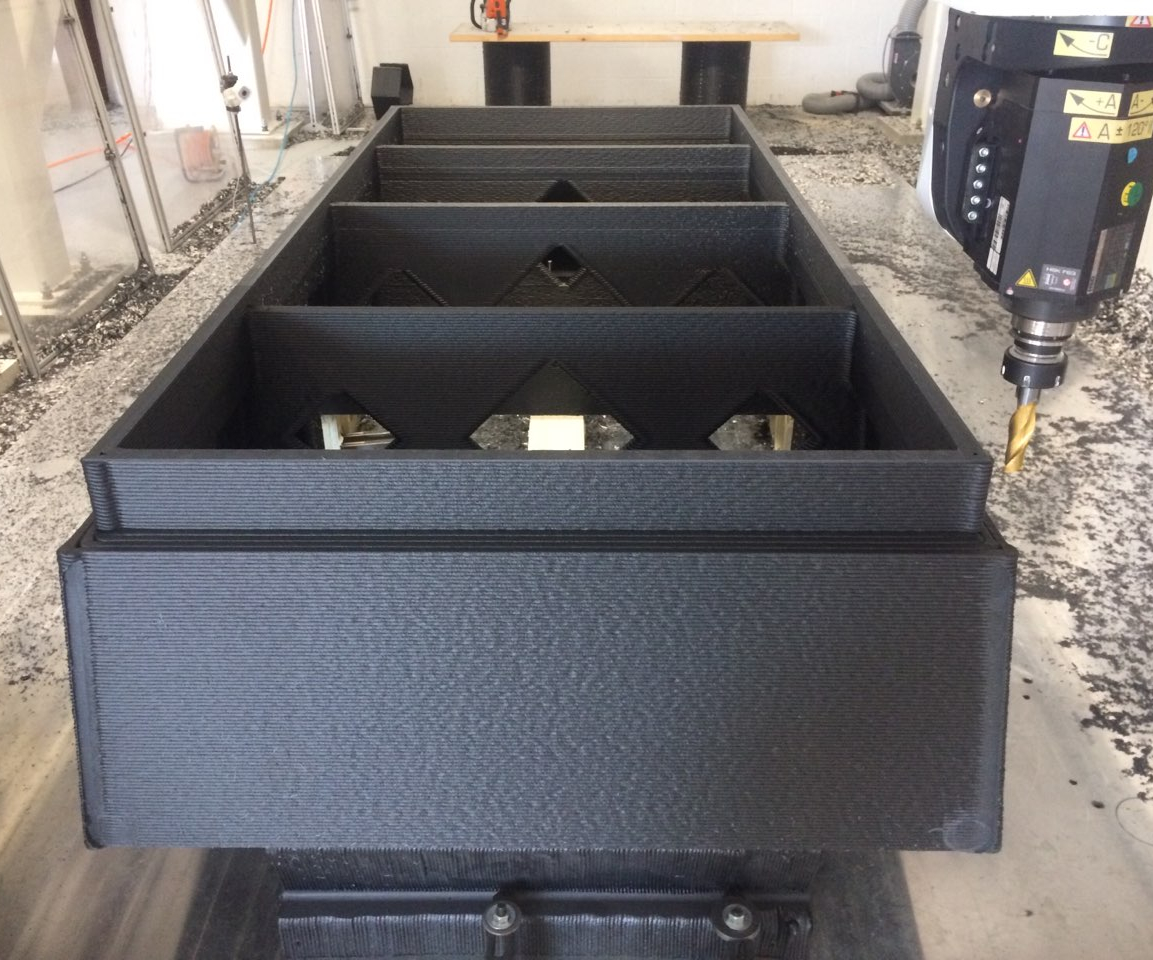
In 2016 had Additive Engineering Solutions (AES, Akron, OH) zijn eerste BAAM-machine gekocht van Cincinnati Inc. Daarom wendden ORNL en Gate Precast zich tot AES voor hulp. Andrew Bader, VP en mede-oprichter van AES, zegt dat zijn bedrijf en ORNL het werkpakket hebben verdeeld, waarbij AES 18 van de 37 mallen heeft geproduceerd. Bader zegt dat elke raamkozijnvorm ongeveer 5 tot 6 voet breed, 9 tot 10 voet lang en 16 duim diep is en ongeveer 500 pond weegt.
Bader zegt dat het interieur van de geometrie van de mallen, omdat ze zijn ontworpen om frames te produceren die rechthoekige ramen omringen, relatief eenvoudig was. Het ontwerp van de buitenoppervlakken van de frames was, zoals opgemerkt, echter complexer, met verschillende diepten en hoeken die in elke mal waren geïntegreerd. Eén gedrukte vorm verving een houten vorm die was samengesteld uit vele individueel gesneden stukken die aan elkaar waren genageld. "De geometrie was eenvoudig, maar gecompliceerd", zegt Bader. "Het project vereiste verschillende unieke frame-ontwerpen, afhankelijk van de locatie van het frame."
Voor een deel van de productie koos AES voor een LNP THERMOCOMP AM-compound, een materiaal met hoge modulus en lage vervorming op basis van ABS met 20% gehakte koolstofvezelversterking, geleverd door SABIC (Houston, Tex., VS). Bader zegt dat het de BAAM-machine 8-10 uur kostte om elke monolithische mal te bouwen, gevolgd door 4-8 uur bewerking en afwerking in een Quintax (Stow, Ohio, VS) CNC-machine. Hij meldt dat de mallen zijn geschuurd tot de vereiste afmetingen, maar niet verzegeld.
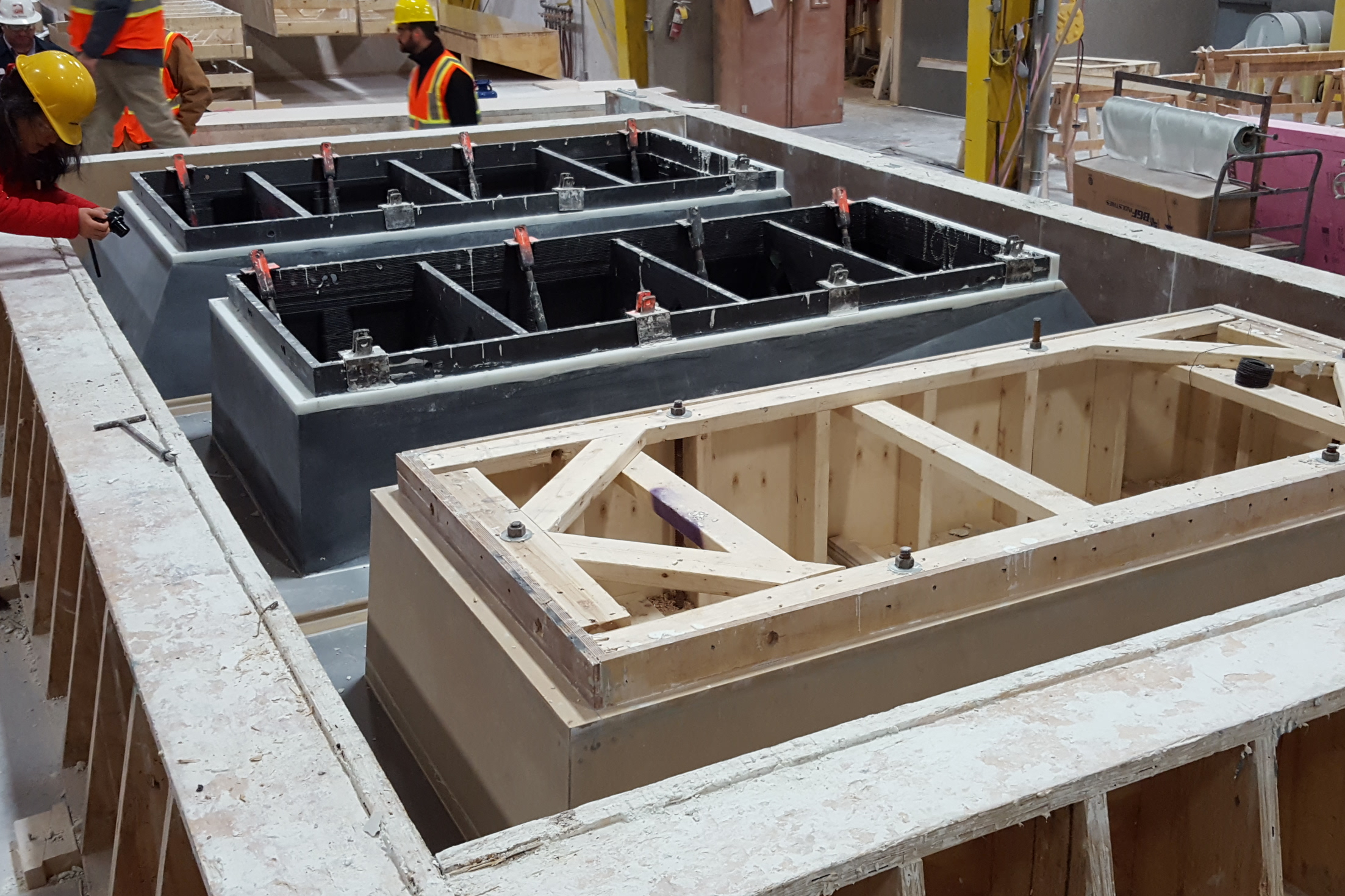
Kozijnen maken
De mallen werden geleverd aan Gate's fabriek in Winchester, Ky., VS, waar ze werden gebruikt naast de 43 traditionele houten mallen die Gate voor het project bouwde. De houten mallen werden met de hand geassembleerd door Gate-medewerkers, vervolgens werden een glasvezelmat en harslaag aangebracht, met vormolie erop gespoten om het loskomen van het gevormde betonnen frame te vergemakkelijken. Er werd ook vormolie op de composietmallen gespoten om het lossen te vergemakkelijken.
Om een betonstorting uit te voeren, werden meerdere mallen op een houten giettafel van 40-50 voet lang geplaatst. Er werden mallen samengevoegd om een enkel frame, een dubbel frame of een drievoudig frame te produceren. Stalen wapening werd in elke mal geplaatst en beton werd rond de wapening gegoten. De giettafel werd vervolgens getrild om het beton te consolideren. Na 14-20 uur uitharden werden de raamkozijnen uit de vorm gehaald, met zuur gewassen en gepolijst. Daarna werden de ramen geplaatst en werd het hele pakket per vrachtwagen naar de bouwplaats in Brooklyn verscheept.
Bader zegt dat de AES-composietvormen, die naast de traditionele houten mallen werken, al snel hun voordelen onthulden. Ten eerste, zegt hij, laat een houten mal slechts 15-20 betonstorten toe voordat deze uit dienst moet worden genomen en opnieuw moet worden opgeknapt of vervangen. De AES-mallen daarentegen lieten 200 betonstorten toe met minimale renovatie of buitengebruikstelling. En de 200 gietbeurten, zegt Bader, vertegenwoordigden het einde van het project, niet het einde van de levensduur van de mal. "Dat is precies waar ze stopten", zegt hij. "Als onze mallen goed worden onderhouden, denken we dat ze honderden en honderden keren kunnen worden gebruikt."
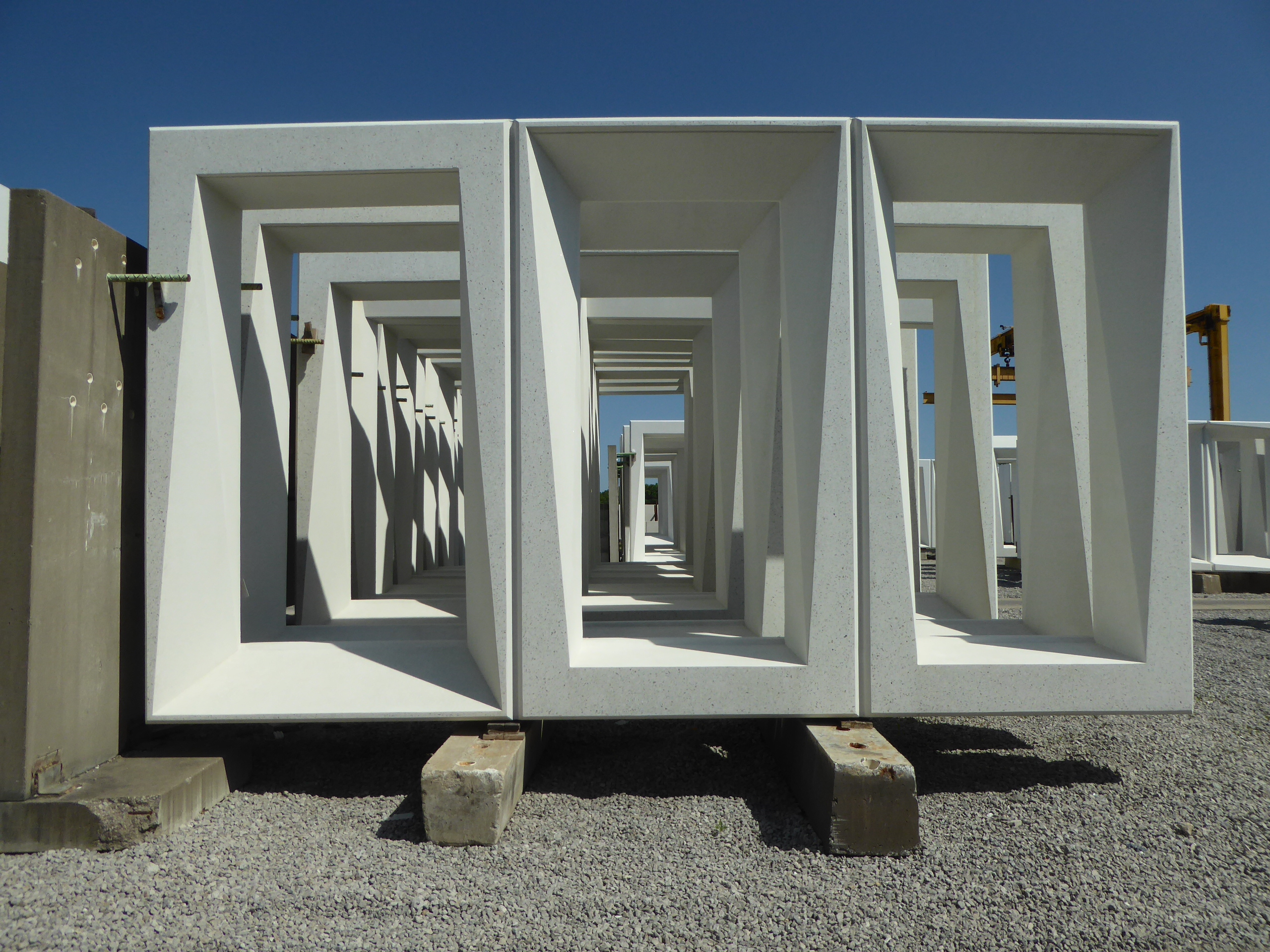
Verder berekent Gate voor gebruik van 150 gietbeurten of meer dat er tot 10 houten mallen nodig zouden zijn om aan de prestatie van één AES-mal te voldoen. Aangezien Gate 40 manuren nodig heeft om een houten mal te produceren, zou het bedrijf zonder de 37 composietmallen niet hebben voldaan aan de planningsvereisten van het One South First-project.
Bader geeft toe dat een AES composiet mal vier keer zoveel kost als een houten mal, maar zeker 10 keer duurzamer is. "De manier waarop geprefabriceerde vormen zijn gebouwd, is decennialang relatief onveranderd gebleven", stelt Bader. "Ineens, op een dag, maken we 3D-formulieren van 500 pond en iedereen was geschokt." Dat gezegd hebbende, erkent hij dat additieve fabricage van dergelijke mallen de meeste . is kosteneffectief in toepassingen waar concrete vormen een gecompliceerde geometrie of veel herhaling hebben - vaak dezelfde vorm.
AES, zo meldt Bader, bezit en exploiteert nu vier BAAM-machines en kan onderdelen tot 2 meter hoog produceren. Er zijn veel grotere onderdelen geconstrueerd door meerdere stukken samen te voegen.
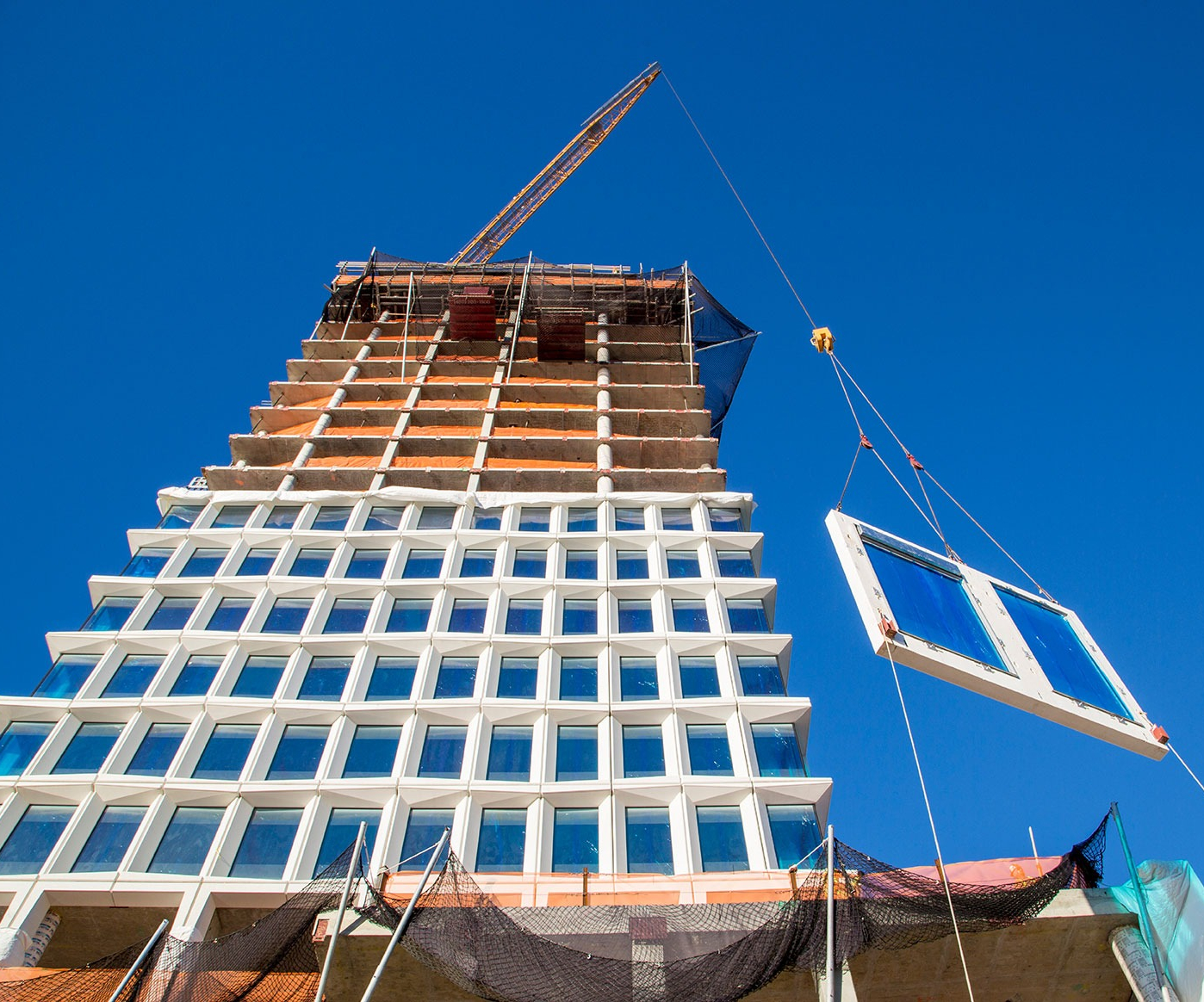
Hars
- Snelheidsmeter
- Beton
- CompositesWorld SourceBook 2022
- Problemen oplossen met thermovormen van thermoplastische composieten
- De evolutie van additieve composieten
- Thermoplastische composieten:structurele bumperbeugel
- Composieten als versterkingen voor het lichaam
- ATL Composites draagt bij aan saneringsproject voor betonnen pijlers
- RS Electric Boats selecteert Norco voor de fabricage van composieten
- Thermoplastische composieten lassen
- Hoogwaardige composieten in Israël