3D-printen van CFRP-mallen voor RTM-flaperon, exoskeletten en meer
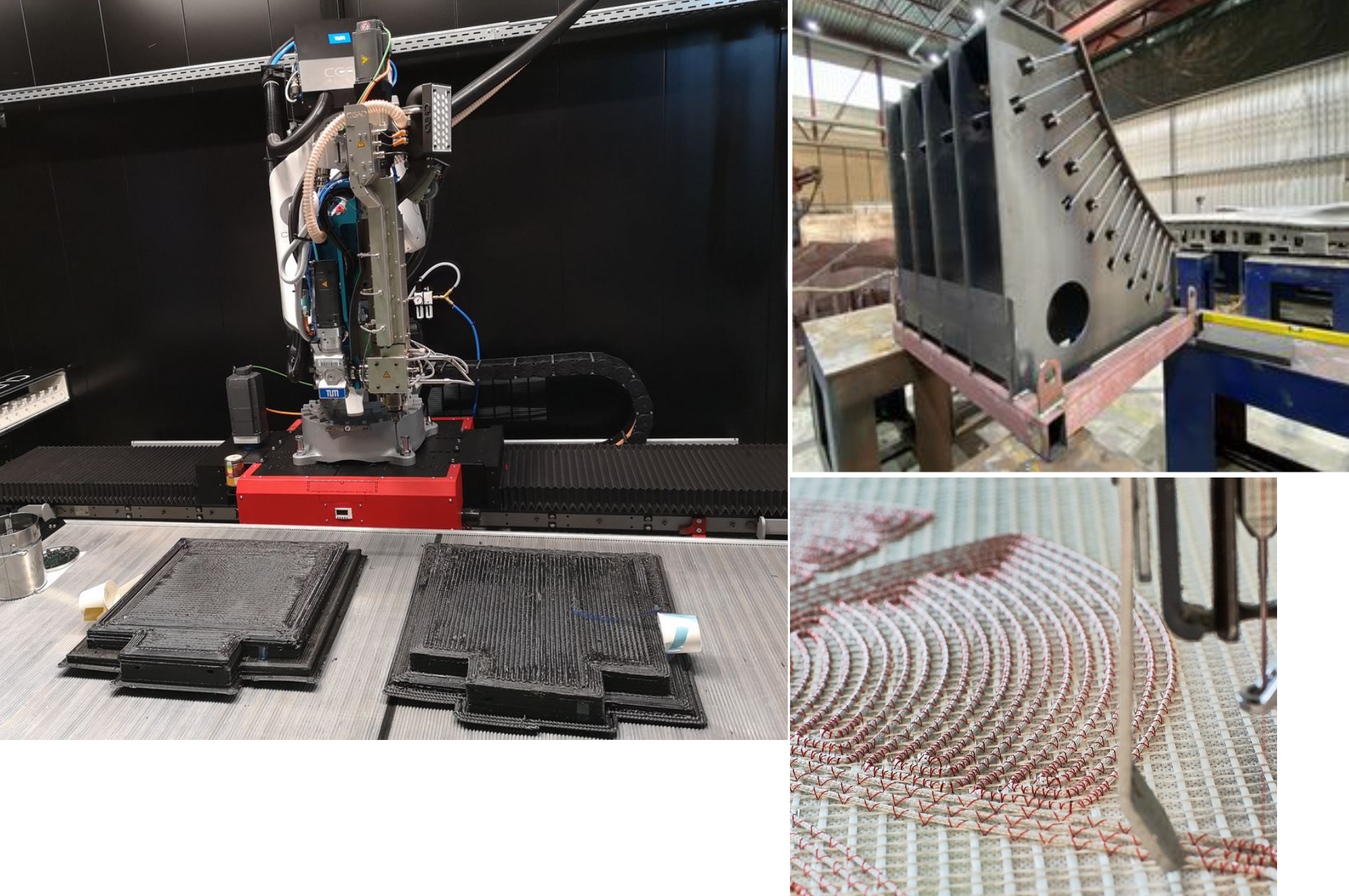
De leerstoel Carbon Composites (Lehrstuhl für Carbon Composites of LCC) werd in 2009 opgericht in de afdeling Werktuigbouwkunde van de Technische Universiteit van München (TUM, München, Duitsland) met financiering van SGL Carbon (Wiesbaden, Duitsland). Haar missie is om R&D uit te voeren op het gebied van koolstofvezelversterkte polymeer (CFRP) materialen, processen en toepassingen, inclusief projecten in simulatie en testen. Een 'leerstoel' in het Duitse universitaire systeem is de kleinste eenheid bestaande uit een professor en zijn team. Het LCC-team wordt geleid door Prof. Dr. -Ing. Klaus Drechsler en heeft momenteel 30 fulltime onderzoekers in dienst. Hoewel de SGL-financiering in 2016 eindigde, heeft de LCC haar leiderschap op het gebied van R&D voor composieten voortgezet, waaronder het bouwen van de mal voor de onderste helft van de Multifunctional Fuselage Demonstrator (MFFD), zie zijbalk hieronder, en omvat nu ook 3D-printen/additief productie.
Deze blog begon toen CEAD (Delft, Nederland) me vertelde dat LCC een van zijn op extruder gebaseerde AM flexbot-systemen had gekocht voor 3D-printen met behulp van een robotarm. Mijn daaropvolgende interview met LCC-onderzoeker Patrick Consul onthulde echter een schat aan projecten, waaronder COMBO3D, binnen Clean Sky 2, om een thermoplastische composiet RTM-mal 3D te printen voor de productie van een thermoset composiet vliegtuigflaperon, en EMOTION om de tool te produceren voor het vormen van de onderste helft van de thermoplastische composiet multifunctionele rompdemonstrator (MFFD) van Clean Sky 2, evenals een secundair gedeeltelijk hulpmiddel om aan te tonen hoe dezelfde romp kan worden geproduceerd via directe in-situ consolidatie (uit autoclaaf). Ik vond de hele discussie over hoe TUM dit punt heeft bereikt en waar het naartoe gaat interessant.
MMFD onderste helft mal
Zie mijn blog van februari 2020:" LM PAEK-lassen bewijzen voor multifunctionele rompdemonstrator". Deze zijbalk is afkomstig uit de paper van februari 2020, "Development of a Multifunctional Fuselage Demonstrator" van Bas Veldman, programmamanager voor de MFFD bij GKN Fokker (Hoogeveen, Nederland).
De schaal van de onderste helft van de MFFD bestaat uit een thermoplastische huid, verstevigd met gelaste stringers, clips en frames. Het te demonstreren productieproces omvat drie belangrijke stappen:
- Prepreg-tape voor de grote huid van de demonstrator wordt op een vlakke, gekantelde tafel gelegd door NLR's bestaande laser AFP-machine.
- Layups worden robotisch met zuignappen naar een vrouwelijke consolidatievorm getransporteerd en erin gedrapeerd zonder verwarming.
- Na vacuümzakken wordt de huid verstevigd in een autoclaaf.
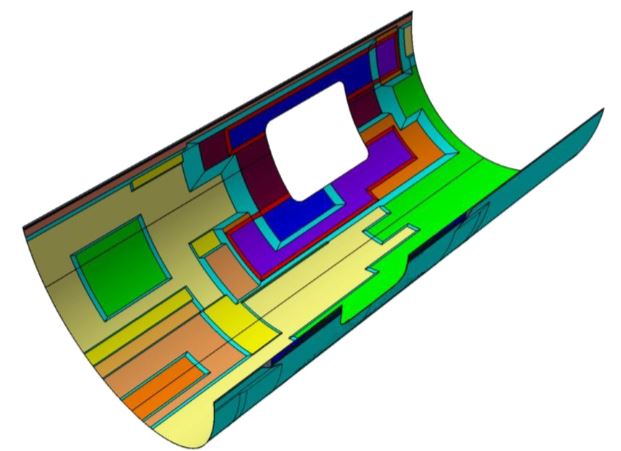
Het gebruik van een vrouwelijke consolidatievorm biedt een veel eenvoudiger (plat) oppervlak dan voor een mannelijk hulpmiddel, terwijl de aerodynamische beperkingen op de kwaliteit van het buitenoppervlak van de huid direct worden gecontroleerd.
Het MFFD-project roept ook op tot buiten de autoclaaf te onderzoeken processen — die parallel aan de grote multifunctionele demonstrator van de romp beginnen — in een volgende demonstrator van kleiner formaat. In het bijzonder in-situ thermoplastisch composiet fabricage waarbij consolidatie wordt bereikt tijdens de lay-up, zal worden overwogen, aangezien dit de autoclaafstap volledig kan elimineren, en dus de fabricage kan reduceren tot een procedure in één stap.
Verbeterde mal voor thermoplastische romp in en uit autoclaafconsolidatie, of EMOTION (https://cordis.europa.eu/project/id/864474), is het Clean Sky 2-project voor het produceren van de MFFD-gereedschappen voor de onderste schaal. "Het klinkt eenvoudig", zegt Patrick Consul van de projectcoördinator, TU München, "maar het is eigenlijk best een uitdaging omdat het moet worden verwarmd tot 400 ° C. Dit is ruim boven het temperatuurbereik waarin Invar36 geen significante CTE [coëfficiënt van thermische uitzetting] heeft.” Invar wordt vaak gebruikt voor composietvormgereedschappen vanwege de lage uitzetting tijdens uithardingscycli bij hoge temperaturen. De CTE van Invar neemt echter toe met de temperatuur. "De uitdaging", merkt Consul op, "zal zijn om de thermische uitzetting tijdens het opwarmen en afkoelen voor de 8 meter bij 4 meter schimmel en de romphuid tijdens het uitharden te beheersen."
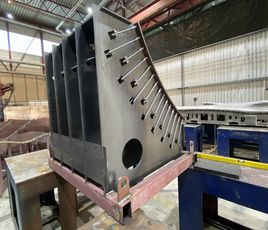
Vooruitgang in additive manufacturing
"We zijn 8-9 mensen die werken aan additive manufacturing binnen de LCC", zegt Consul. Hij begint de geschiedenis van dit werk met de aankoop door het LCC van een lasergestuurde plaatsingsmachine van thermoplastische composiettape van AFPT (Dörth, Duitsland) in 2012. Later voegde hij een Coriolis Composites (Quéven, Frankrijk) machine toe om geautomatiseerde vezelplaatsing (AFP) mogelijk te maken. ) van thermohardende prepregs. De eerste op filamenten gebaseerde desktopprinters werden in 2017 aangeschaft. "In 2017 ben ik ook lid geworden om te helpen bij het ontwikkelen van nieuwe toepassingen en onderzoeksprojecten, waaronder het schrijven van voorstellen voor bijvoorbeeld Clean Sky 2." Hij legt uit dat Clean Sky 2-projecten worden toegekend op basis van voorstellen die zijn ingediend bij topicmanagers in reactie op publiekelijk gepubliceerde Calls for Proposals (CFP). LCC is geslaagd in haar voorstellen voor het CFP08 COMBO3D-project en het CFP09 EMOTION-project. Beide worden hieronder besproken.
"We hebben een paar andere projecten, sommige kijken naar 3D-printen met continue vezelversterking", zegt Consul. “Anderen gebruiken een lasergeïntegreerde printkop om het composietsubstraat voor te verwarmen om op reeds geconsolideerde CFRP-onderdelen te printen of om de interlaminaire afschuifsterkte (ILSS) tussen geprinte lagen te vergroten. Een ander project onderzoekt bijvoorbeeld gereedschapstoepassingen waar je een klein aantal gespecialiseerde composietonderdelen hebt.”
“Deze projecten worden continu ondersteund door numerieke simulaties om het gedrag van de additief vervaardigde onderdelen tijdens en na het printproces te voorspellen”, vervolgt hij. “Het LCC is ook betrokken bij een project met het Imperial College of London dat tot doel heeft exoskeletten te vervaardigen met behulp van 3D-geprint CFRP. Een ander project onderzoekt roosterstructuren om de eigenschappen van 3D-geprinte onderdelen te optimaliseren met betrekking tot stijfheid, sterkte of energieabsorptie.”
Vooruitgang in printers

"We begonnen met het gebruik van een eenvoudige 3D-printer op basis van FDM (fused depositionmodeling) van Apium (Karlsruhe, Duitsland) om gespecialiseerde testopstellingen te printen die een hoge stijfheid vereisen", legt Consul uit. “De printer was 3 meter lang en 1 meter breed met een hoge materiaaluitvoer om de printtijd te verkorten. Hoewel het geen continue vezel kon gebruiken, was het goed ontworpen om te printen met PEEK, PEKK en gehakte koolstofvezelversterkte PEEK. Het gebruikte niet alleen een verwarmd bed, maar ook een verwarmde plaat rond de printkop, wat hielp om een homogene temperatuurverdeling in de prints te produceren, thermische stress te verminderen en kristallisatie te garanderen.”
"We hadden ook een tijdje een Markforged-printer (Cambridge, Mass., V.S.) en kregen toen een Anisoprint [Esch-sur-Alzette, Luxemburg]", zegt Consul. Hoewel de Markforged-printer FDM met continue glasvezel mogelijk maakte, koos het LCC-team ervoor om het niet te behouden. “Het probleem dat we hadden was dat het systeem erg gesloten was”, legt Consul uit. “De slicer-software van Markforged was te moeilijk om te gebruiken voor onderzoek omdat het onze mogelijkheden ernstig beperkt. We konden alleen een laag continu vezelmateriaal printen en vervolgens een laag kort vezelversterkt thermoplastisch filament erop. De slicer die de code genereert, accepteert geen G-code van ons. Er was dus geen manier om de machine te vertellen om het te printen zoals we wilden met continue vezels in elke laag, enz."
Wanneer hiernaar wordt gevraagd, legt Markforged uit dat zijn systemen nooit bedoeld waren om voor onderzoek te worden gebruikt, maar in plaats daarvan waren ontworpen om eenvoudig en robuust te zijn voor wijdverbreid gebruik bij het maken van onderdelen, gebruikmakend van op regels gebaseerde vezelpading en weinig inspanning en tijd vergen om de slicer te configureren . Het is Met Eiger-software kunnen gebruikers lagen afzonderlijk configureren, en Markforged verwelkomt feedback en geeft prioriteit aan het verbeteren van de gebruikerservaring voor zijn klanten.
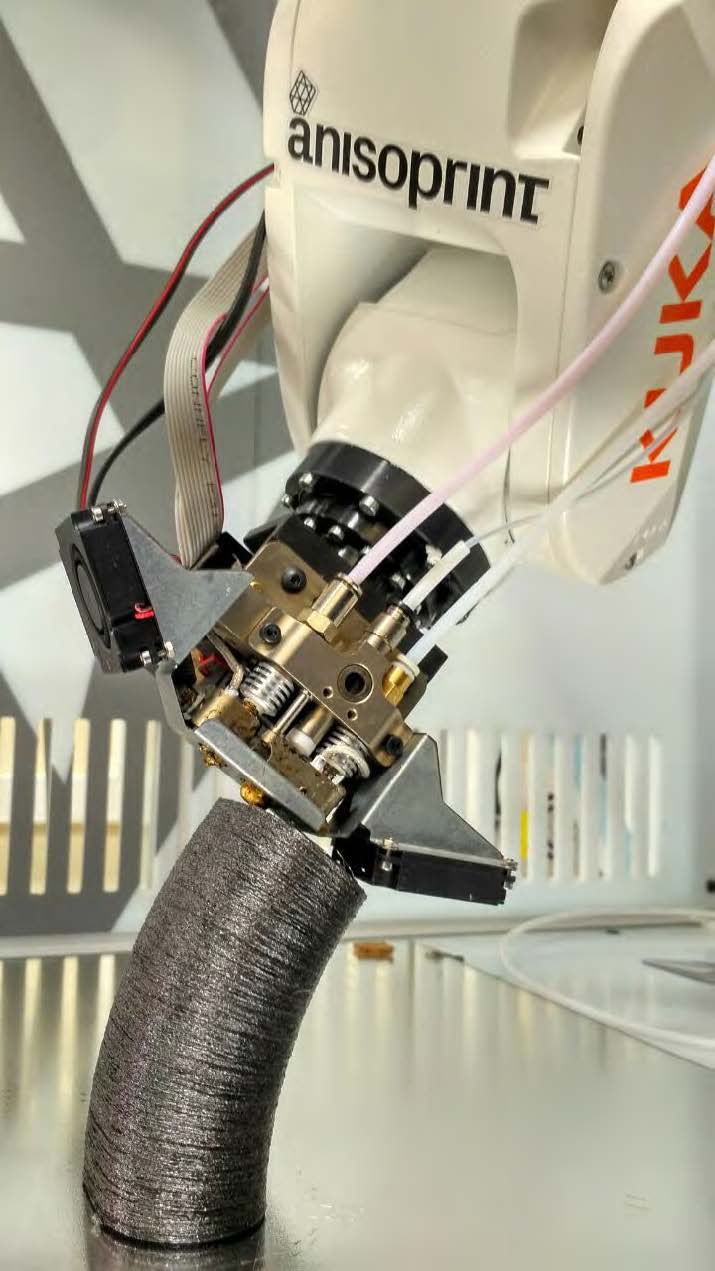
“Anisoprint, dat een volledig open G-code slicer gebruikt, gaf ons meer toegang tot het proces”, zegt Consul. “Het is ook in staat om continue koolstofvezel te printen en niet alleen in 2D-lagen, maar ook uit het vlak, in 3D-curven. We hebben een Anisoprint-printkop voor een kleine Kuka-robot, die onderdelen van 1 meter bij 1 meter kan produceren, wat groter is dan de meeste desktops, maar klein voor een robotsysteem."
Maar hoe zit het met de dubbele matrix van Anisoprint thermohardende thermoplastische (TS-TP) materialen? Zoals uitgelegd in mijn blog van 2019 over Anisoprint “… het impregneert eerst continue vezelversterking met een thermoset polymeer en extrudeert dit tijdens het printen in het gesmolten thermoplastische filament.” Consul antwoordt dat de hechting tussen het TS-filament en de TP redelijk goed is. “Bij onze eerste tests konden we een hoger vezelvolume krijgen in vergelijking met de Markforged-printer, maar dit was omdat we de G-code konden wijzigen. De Anisoprint-printkop duwt het TS-filament in de TP en legt dat vervolgens. We zijn van plan die printer te gebruiken voor onderdelen van het exoskelet. Het is een gemakkelijke manier om sterkere vezels te integreren."
Geëxtrudeerde pelletprinters
De volgende stap was naar een grootschalige printer, eerst met korte vezelversterkte TP en vervolgens continue vezel TP. “We ontwikkelden eerst een extruder gemonteerd op een robot, en daarna volgde al snel onze interesse in de CEAD-machine. We hopen volgend jaar continue glasvezel in beide systemen te integreren.”
Maar waarom had je de CEAD-machine nodig als je al een extruder op een robotarm had? "De eerste extruder was de bètaversie van een Dyze Pulsar-pelletextruder, die een maximum van ongeveer 2 kg/u en ongeveer 1 kg/u met PAEK's produceert, maar hij worstelt met meer dan 20% koolstofvezelbelasting", zegt Consul. “De gemiddelde output is echter lager omdat de robot tijdens het printen vaak versnelt en vertraagt. Voor COMBO3D hadden de eerste kleinschalige matrijshelften al minimaal 36 kilogram nodig, dus we hadden ongeveer 48 uur nodig om een enkele helft te printen. We moesten ook altijd iemand bij de hand hebben, omdat fouten, zoals een geblokkeerde materiaaltoevoerlijn of het kromtrekken van onderdelen, op elk moment kunnen optreden.”
Omdat de COMBO3D final demonstrator ongeveer 10 keer groter is dan de aanvankelijke kleinschalige onderdelen, was het printen met dit eerste extrudersysteem niet haalbaar, zegt Consul. “Ook hadden sommige van de materialen die Victrex ons leverde een hogere viscositeit en deze eerste extruder kon niet genoeg koppel leveren om die polymeren te extruderen. Met de CEAD-printer hebben we een maximale output van ongeveer 12,5 kg/u en na een paar uur testen hadden we een stabiele gemiddelde output van ongeveer 5-6 kg/u. Hierdoor konden we de kleinschalige malhelft in minder dan 8 uur printen en konden we hogere vezelgehalten gebruiken om het kromtrekken te verminderen, waardoor het proces over het algemeen gemakkelijker te controleren is.”
"Dus terwijl de Pulsar ons al in staat stelde om pellets te gebruiken, een hoge materiaaloutput te bereiken en te profiteren van de vrijheidsgraden van een robot", vervolgt hij, "breidt de CEAD-printer onze mogelijkheden uit naar grotere onderdelen, hogere vezelinhoud en een breder scala aan polymeren . De Pulsar overbrugt de kloof tussen onze op filamenten gebaseerde printers en de CEAD, niet alleen in output, maar ook in nozzle-afmetingen en resulterende details van de prints.”
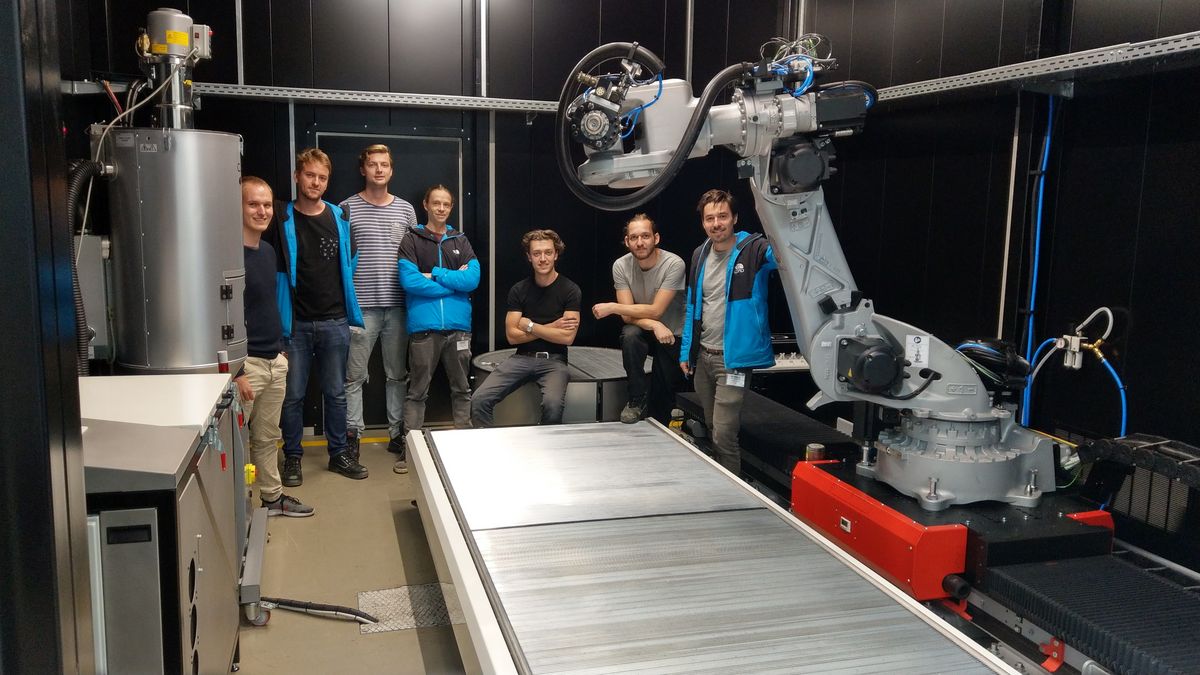
CEAD AM Flexbot technische gegevens:
- AM Flexbot technische gegevens:
- Extrusie op basis van pellets tot 12,5 kg/uur (onversterkt en met korte vezels versterkt)
- Verwerking van materialen tot 450 °C
- Bouwvolume 3000 x 1200 x 1700 millimeter
- Bouwplaat op een draaitafel of vlakke tafel (verwarmbaar)
- Nabewerking door middel van een freeskop.
COMBO3D
Het doel van dit Clean Sky 2 project is het 3D printen van een mal om een demonstrator composiet flaperon (1,5 bij 3 meter) te maken voor een groot passagiersvliegtuig, onderdeel van Werkpakket A-3.1:Multidisciplinaire vleugel voor hoge en lage snelheid. Het doel van het gebruik van additive manufacturing is om de doorlooptijd voor gereedschapsproductie te verkorten. Het project ging van start in januari 2019 en loopt tot maart 2021. Partners zijn onder meer Alpex Technologies (Mils bei Hall, Oostenrijk), lichtgewichtmetaalspecialist Leichtmetallkompetenzzentrum Ranshofen (Ranshofen, Oostenrijk) en Victrex (Thornton Cleveleys, VK), leverancier van de hoogwaardige thermoplast polyaryletherketon (PAEK).
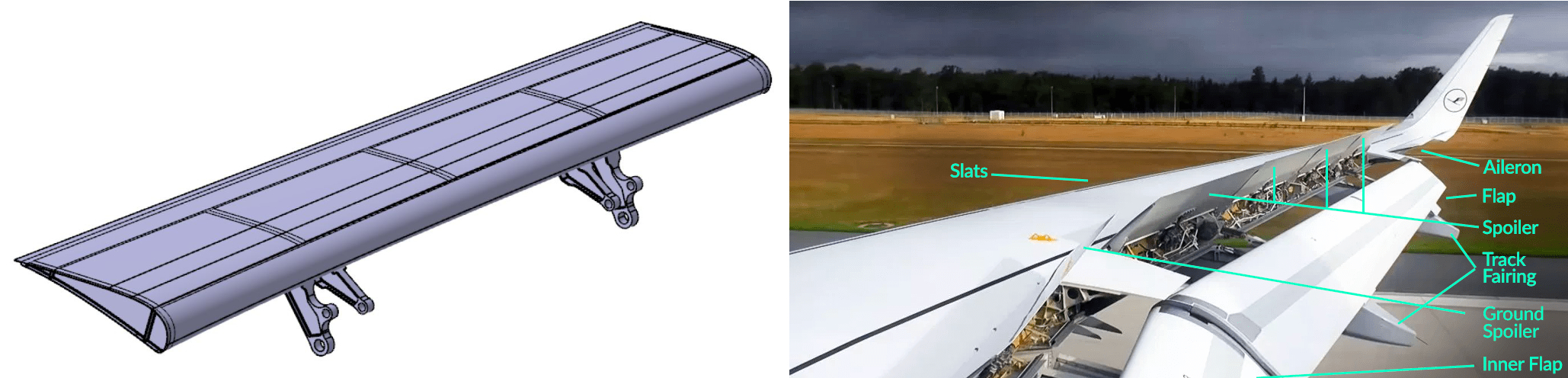
Een ander belangrijk onderdeel van het project is om aan te tonen dat deze flaperon van koolstofvezel/epoxy gemaakt kan worden met resin transfer molding (RTM) in plaats van geautoclaveerd prepreg. Het RTM-onderdeel hardt uit bij dezelfde 180°C als de autoclaafonderdelen. Om thermische stabiliteit te garanderen, wordt het gereedschap bedrukt met korte koolstofvezelversterkte PAEK, die een smelttemperatuur van 305°C heeft.
Om de uithardingscyclus te verkorten, zal de 3D-geprinte mal actieve temperatuurregeling integreren. “We moeten de mal sneller kunnen opwarmen en afkoelen dan in de autoclaaf”, merkt Consul op. “We gebruiken een gaas van elektrische verwarmingselementen 3 millimeter onder het matrijsoppervlak en integreren ook bedrukte kanalen voor verwarmde olie of lucht op 6 millimeter onder het matrijsoppervlak. Op deze manier kunnen we het matrijsoppervlak zeer snel verwarmen, maar ook de kanalen gebruiken om het hele gereedschapsvolume te verwarmen. We streven naar een verwarmings- en koelingssnelheid die 50% sneller is dan de autoclaaf en we hebben er vertrouwen in dat we een snelheid van minstens 30% kunnen bereiken.”
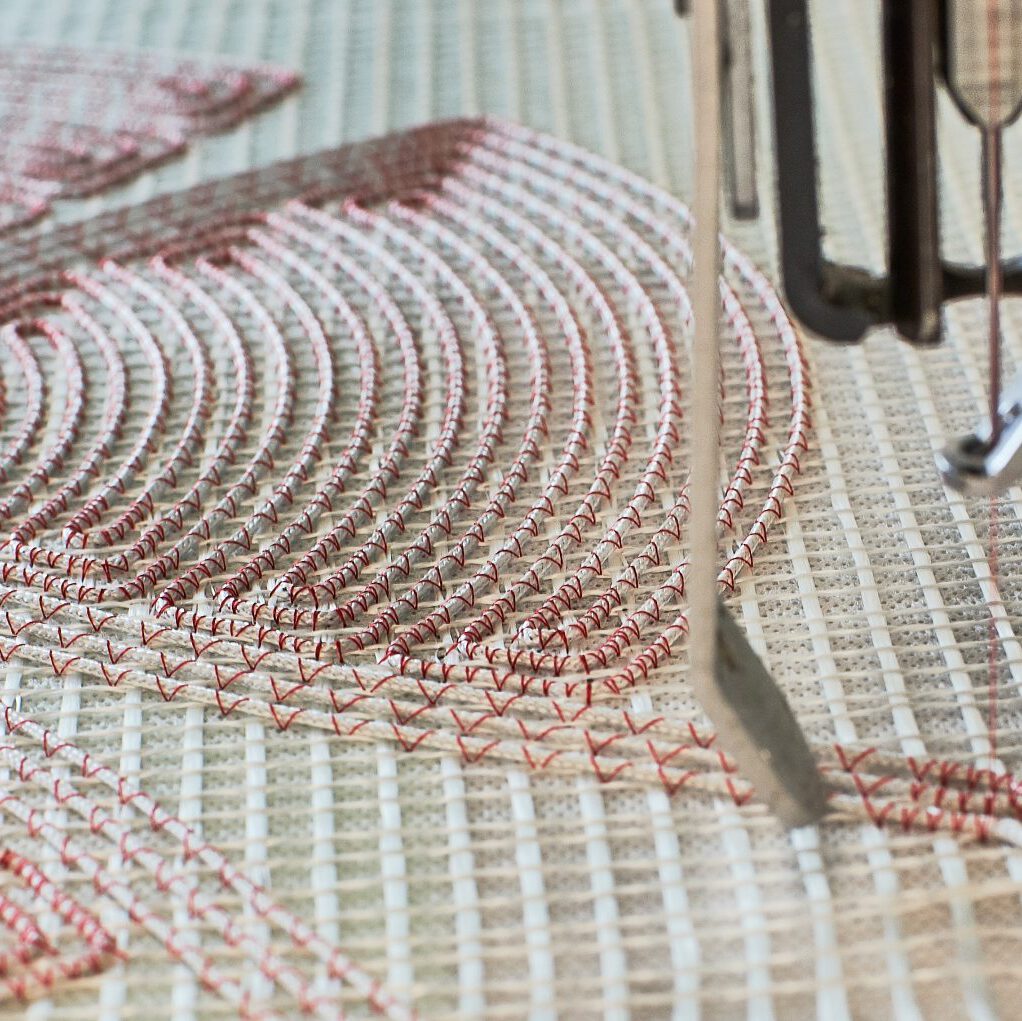
Wat zijn de verwarmingselementen die in de 3D-print moeten worden geïntegreerd? "We hebben op maat gemaakte vezelplaatsing (TFP) van koolstofrovings op een glasvezeltextiel als verwarmingselementen gebruikt om verschillende verwarmingszones in een CFRP-mal voor een helikopterrotorblad te realiseren", legt Consul uit. “Dit was voor een Clean Sky 1-project dat we hebben voltooid in samenwerking met QPoint Composite (Dresden, Duitsland). We gaan met een soortgelijk concept werken aan de COMBO3D mal.”
De hele ontwikkeling van de gedrukte tool wordt ondersteund door simulatie. Het ontwerp van het gereedschap wordt geoptimaliseerd door het verwarmings- en koelsysteem te implementeren in een thermische simulatie. Ook wordt het fabricageproces gesimuleerd en wordt het printproces ondersteund door kennis te genereren over de temperatuurverdeling tijdens het printen en deze te correleren met padplanning.
CEAD-machine-installatie en projectvoortgang
"Het CEAD-systeem werd zeer snel geleverd - van bestelling tot installatie duurde slechts 6 maanden", zegt Consul. “Tegen die tijd hadden we de materiaaltests voltooid, de plaatgereedschappen ontworpen en waren we begonnen met het printen van kleine onderdelen. We waren bang dat het lang zou duren om het proces goed te laten verlopen met de CEAD AM Flexbot, maar het werkte goed bij de eerste proeven.”
Plaatwerk? "Het is een kleine mal, waarin al koelkanalen en verwarmingselementen zijn geïntegreerd om CFRP-platen te produceren voor het testen van coupons", legt hij uit. "Deze test moest ervoor zorgen dat de kwaliteit van onze 3D-geprinte CFRP RTM-mal vergelijkbaar zal zijn met de huidige CFRP die Saab produceert met hun autoclaafproces."
Helaas werd het project onderbroken door COVID-19, "maar nu gaat alles goed en halen we de achterstand in", zegt Consul. En hoe zit het met het gebruik van PAEK voor de 3D-geprinte mal? "Het enige probleem momenteel is dat de Tg [glasovergangstemperatuur] voor PAEK 130-140 ° C is, wat lager is dan de 180 ° C-uitharding voor het demonstratiegedeelte", merkt Consul op. "We moeten dus nog zien hoeveel cycli we kunnen voltooien bij de uithardingstemperatuur voordat kruip optreedt of het oppervlak wordt beschadigd."
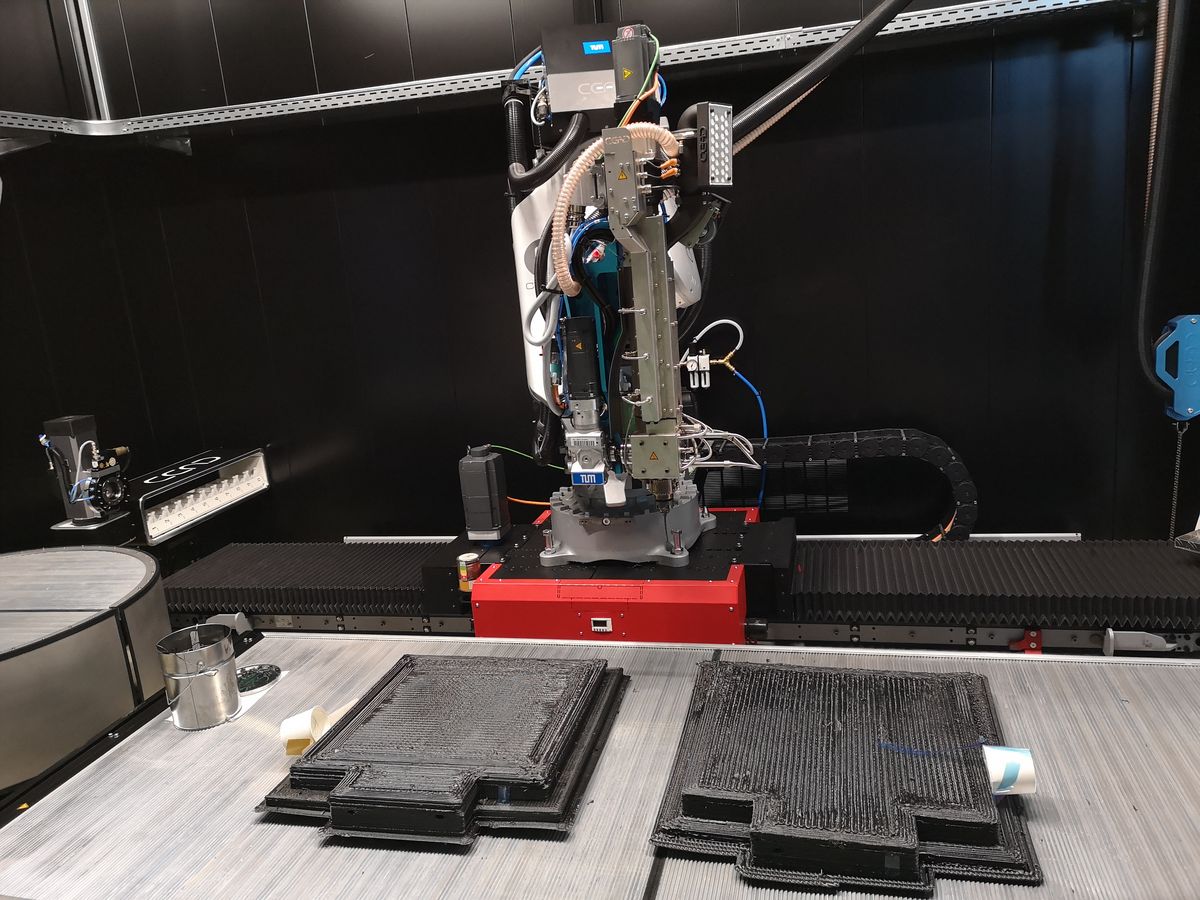
CEAD-machine in andere projecten?
"We doen een aanvraag voor een project in aerospace-tooling dat volgend jaar begint met GKN Aerospace Deutschland (München) met behulp van de CEAD-machine en polyethersulfon (PESU)", zegt Consul. [Opmerking:GKN in Duitsland maakt composiet vleugelkleppen voor de A330 en A350, evenals rolroeren voor de Bombardier Global-familie van zakenjets.] “CEAD zal hierbij verantwoordelijk zijn voor de machineontwikkeling voor continue koolstofvezels. We zijn ook van plan om de CEAD-machine intern te gebruiken om prototypematrijzen voor RTM te maken die anders zouden zijn uitbesteed. Het geeft ons een voordeel bij het versnellen van het werk.”
Consul merkt op dat PESU een hogere Tg heeft dan PAEK. "Het is ook amorf, niet semi-kristallijn, dus het zou gemakkelijker moeten zijn om te printen, hoewel kruipweerstand een probleem kan zijn. Wat we proberen te doen is PEI (polyetherimide) vermijden. In het verleden hebben we gekeken naar de kwestie van PEI-binding aan epoxyhars. RTM6 [epoxy voor RTM] lost PEI op, wat zorgt voor een goede hechting tussen de twee. Dit is precies wat je niet wilt in 3D-geprinte mallen die de onderdelen moeten losmaken, niet eraan blijven plakken.”
Toekomstige industriële (en vliegende) 3D-geprinte composieten
Bij het bespreken van enkele van de andere projecten die LCC op het gebied van additieve productie nastreeft, vraag ik de consul wat CFRP heeft tegengehouden in exoskeletten? "Omdat exoskeletten moeten worden aangepast aan elke drager, zijn de onderdelen gespecialiseerd, dus het volume is niet groot", antwoordt hij. “Ons project heeft tot doel de productie van patiëntspecifieke exoskeletcomponenten van de onderste ledematen mogelijk te maken om de productie van een patiëntspecifiek exoskelet in minder dan 24 uur mogelijk te maken. Deze exoskeletten zullen de revalidatie van patiënten met een beroerte ondersteunen op basis van hun biofysische profielen en unieke medische revalidatiebehoeften.” (Zie het CW-artikel, "C-FREX exoskelet hangt af van CFRP ...")
“Mensen hebben het idee dat 3D-printen elk onderdeel kan printen, maar je moet eerst ervaring hebben met 3D-printen en met composieten. Er zijn bijvoorbeeld vaak problemen met laag op laag hechting en anisotropie die moeten worden begrepen. 3D-geprinte composietonderdelen zullen niet hetzelfde ontwerp hebben als de onderdelen die momenteel van plastic en metaal zijn gemaakt.”
Hij merkt op dat er nog steeds problemen moeten worden opgelost voor het gebruik van 3D-geprinte composieten voor de productie van hoogwaardige vliegtuigonderdelen, bijvoorbeeld:hoe ontwerp je deze onderdelen voor additive manufacturing? Hoe identificeer je onderdelen waar additive manufacturing waarde toevoegt? "Aerospace tooling is het belangrijkste toepassingsgebied waar ons team momenteel naar kijkt", zegt Consul. “Met 3D printen past de mal goed. Deze mallen moeten bestand zijn tegen dezelfde uithardingsomstandigheden als de onderdelen, maar er is minder risico verbonden aan schimmels versus vliegende onderdelen. Een goed voorbeeld zijn ribverstevigers voor vleugels, waar er een groot aantal verschillende onderdelen is, maar niet veel cycli per onderdeel. Dit is dus een goede manier om ervaring op te doen met de technologie. Het is te vroeg om te proberen voor structurele onderdelen die zullen vliegen. We streven naar deze lange termijn, maar met printtools kunnen we het 3D-printproces stabiel genoeg krijgen met hoogwaardige eigenschappen en ook de mogelijkheid ontwikkelen om deze onderdelen en processen nauwkeurig te voorspellen in simulatie.”
Hars
- Waarom 3D-printen en software cruciaal zijn voor digitale transformatie
- Problemen oplossen voor onderhoud:meer dan alleen vallen en opstaan
- 3D-printoplossingen voor olie- en gasbedrijven
- DSM en Nedcam ontwikkelen nieuwe toepassingen voor grootformaat 3D-printen
- Acetal Color Masterbatches voor auto's en meer op basis van emissiearme dragers
- Automatisering voor IML en Stack Moulds
- Victrex en Bond-partner voor 3D-printen van PAEK-onderdelen
- Tips voor 3D-printvormen
- Tips voor CNC-bewerking van titanium:ruimtevaart en meer
- Formlabs om 3D-printen toegankelijker te maken voor het MKB
- SIGRABOND® Chemical CFRP voor componenten en samenstellingen