AFP combineren met 3D-printen voor flexibele productie van onderdelen
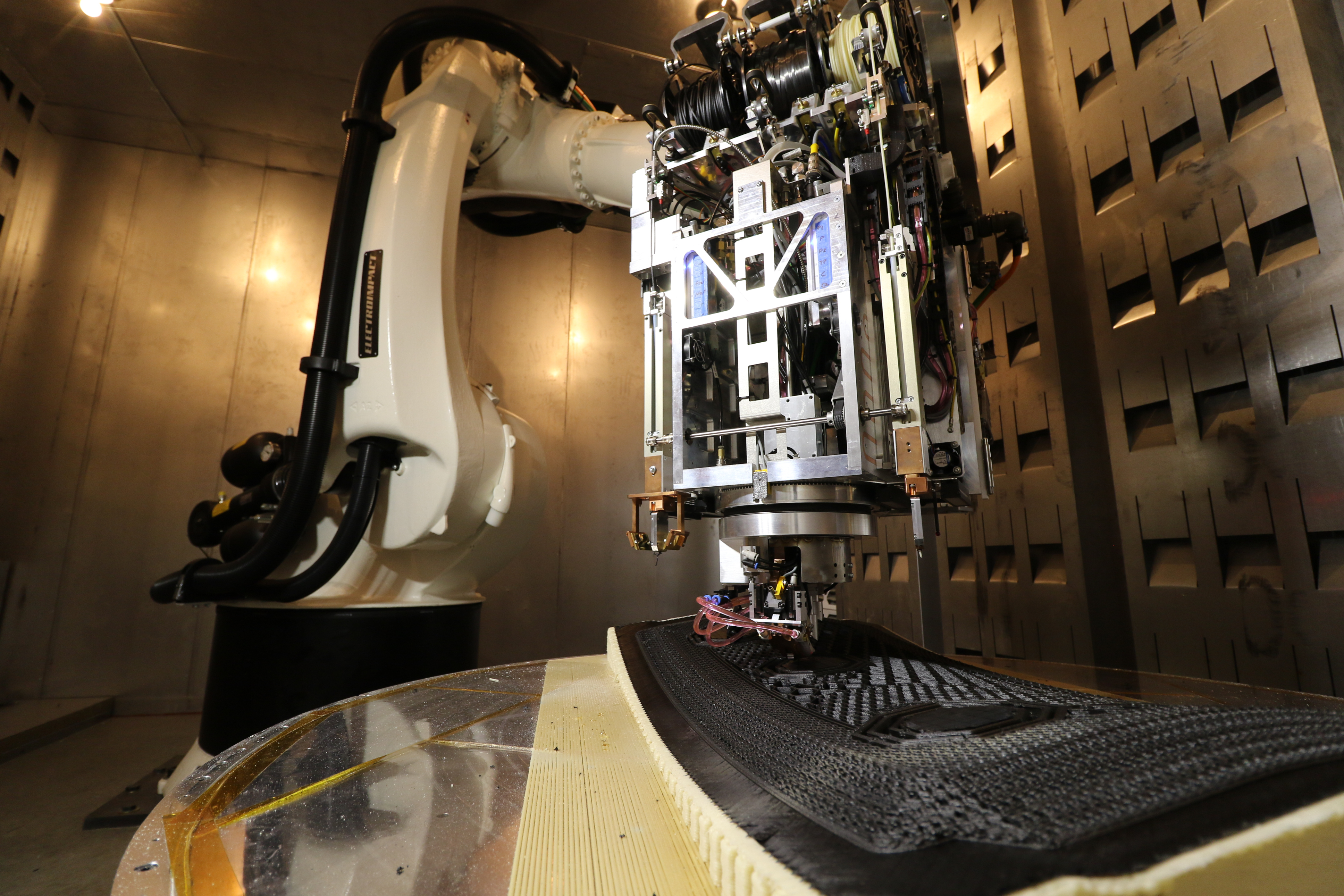
Electroimpact (Mukilteo, Wash., V.S.), opgericht in 1986, is een wereldwijde leverancier van tooling en productieautomatisering die beweert 's werelds grootste integrator van vliegtuigassemblagelijnen te zijn. Op het gebied van composieten staat het bedrijf bekend om zijn geavanceerde technologie in high-speed automatic tape-lay- (ATL) en fiber placement (AFP)-systemen. Electroimpact benadrukt dat het door ingenieurs wordt aangedreven - 400 van de 600 medewerkers hebben een ingenieursdiploma - met ontwikkelingen die zijn bedacht en voltooid door hetzelfde ingenieursteam, van concept tot ontwerp, productie, installatie en afkoop door de klant.
In juli 2020, CW rapporteerde over het nieuwe Scalable Composite Robotic Additive Manufacturing (SCRAM) -systeem van het bedrijf. Hier delen we ons interview met een deel van het engineeringteam van SCRAM:projectmanager Cody Brown, procesontwikkelings- en besturingsingenieur Ryan Bischoff en hoofdwerktuigbouwkundig ingenieur Reese Allen. Hun uitleg van de oorsprong, implementatie en toekomst van deze continue vezeladditieve productie geeft inzicht in hoe de volgende generatie composietproductie eruit zou kunnen zien.
Streven naar grootschalige FDM
Bruin :“We zijn hier al vier jaar mee bezig, maar wilden wachten tot we konden laten zien dat het echte onderdelen van ruimtevaartkwaliteit zou opleveren. Ons oorspronkelijke doel was om een grootschalige 3D-printer voor fused filament fabricage (FFF) te produceren die complexe onderdelen kon maken met behulp van continue vezels. We waren niet van plan om een AFP-type proces te ontwikkelen, maar toen we probeerden het vezelvolume te vergroten en een hogere fysieke sterkte in de geprinte delen te bereiken, liepen we tegen een muur aan met FFF. Het is gewoon geen geschikt proces voor in-situ consolidatie met een hoog vezelgehalte en weinig holtes. We zijn dus uitgekomen op een proces dat thermoplastisch composiet AFP combineert met FFF met behulp van onversterkte en/of gehakte vezelgevulde filamenten.”
Allen :“AFP is eigenlijk een additief productieproces. In SCRAM gebruiken we het echter niet op een conventionele manier met een vast, hard gereedschap, maar in plaats daarvan printen we een gereedschap dat we daarna kunnen uitwassen om zeer complexe geometrieën te creëren die echt structureel zijn."
Bruin :"We kunnen dat oplosbare hulpmiddel op plaatsen plaatsen die niet in een raster zijn vergrendeld, zodat je interne holtes kunt creëren. Het doel is niet om te concurreren met onze grote AFP-systemen, maar om een zeer handig systeem te maken dat zo dicht mogelijk bij een 3D-printer ligt. Om dit te doen met echte zes vrijheidsgraden en nauwkeurigheid is eigenlijk heel ingewikkeld. De resulterende cel elimineert bevestigingsmiddelen en lijmen en produceert geïntegreerde, complexe onderdelen die zeer snel kunnen worden herhaald.”
Hoge prestaties voor ruimtevaart
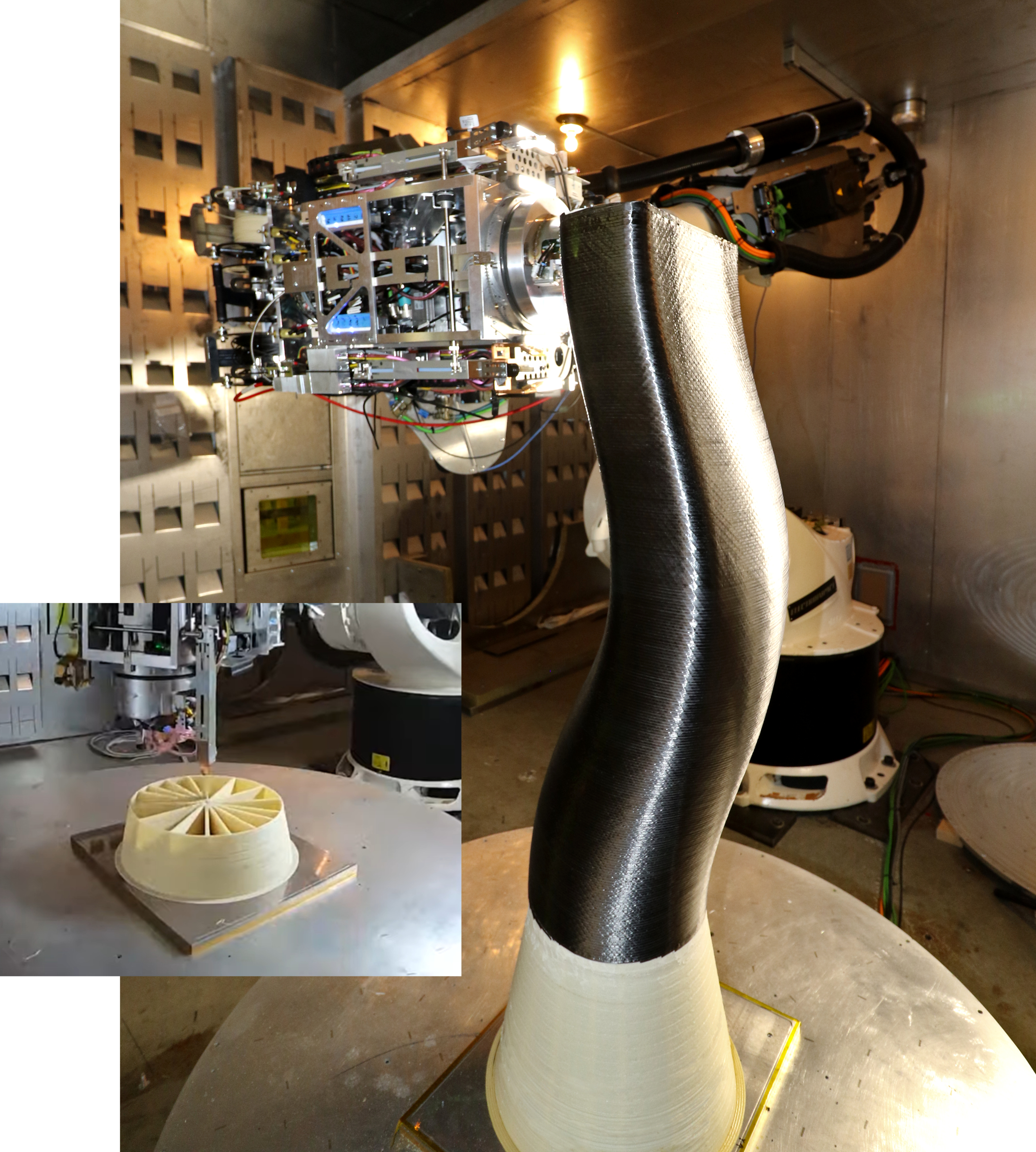
Bruin :"De eerste toepassingen waarop we ons richten in de lucht- en ruimtevaart en defensie hebben de opdracht gekregen om te beginnen met PEEK [polyetheretherketon]. Daarna hebben we met enorm succes gewerkt met PEKK [polyetherketonketon] en laagsmeltende PAEK [polyaryletherketon].”
Bischoff :“Coëfficiënt van thermische uitzetting [CTE] is je grootste vijand. Dit is de reden waarom het gebruik van PEEK zo uitdagend is - het houdt ervan om te kristalliseren en te krimpen. Hoewel de CTE voor PEKK en andere PAEK-harsen niet nul is, is hun kristalstructuur veel beter controleerbaar en daardoor gemakkelijker om mee te werken. Alternatieve PAEK's bieden ook een veel betere verwerkbaarheid en hogere lay-upsnelheid.”
Allen :“Thermische gradiënten moeten worden vermeden vanwege het CTE-probleem, dus je probeert het proces en onderdeel zo isotherm mogelijk te houden. Anders krijg je kromtrekken. Het gebruik van de verwarmde kamer is een must - zelfs als je hem niet op een hoge temperatuur houdt - om er zeker van te zijn dat er geen tocht is en dat een deel van de afdruk niet op een andere temperatuur is dan de rest."
Lasergebaseerde cel
Bruin :"Veel dingen die dit systeem mogelijk maken, bestonden niet toen we begonnen, inclusief de PAEK-tape en de compacte, krachtige laser die we gebruiken, evenals echte zes-assige CAM-software voor additieve fabricage."
"De SCRAM-kop maakt gebruik van twee 3D-printnozzles aan weerszijden van het AFP-systeem [openingsbeeld]. De ene wordt gebruikt om de oplosbare tooling te printen en de andere print ongewapend of gehakt vezelfilament. Je kunt zien dat die is uitgerust met een steiger. Deze bevat een set spiegels om het laserlicht rond de punt van de spuitmond om te leiden en het substraat te verwarmen. Dit stelt ons in staat om een uitzonderlijke hechtsterkte tussen de lagen te bereiken in vergelijking met traditionele FFF. De lampjes op het systeem moeten het onderdeel voor de camera's verlichten [Fig. 2]. We gebruiken deze overal zodat de operator veilig kan zien wat er aan de hand is zonder gevaar van de laser.”
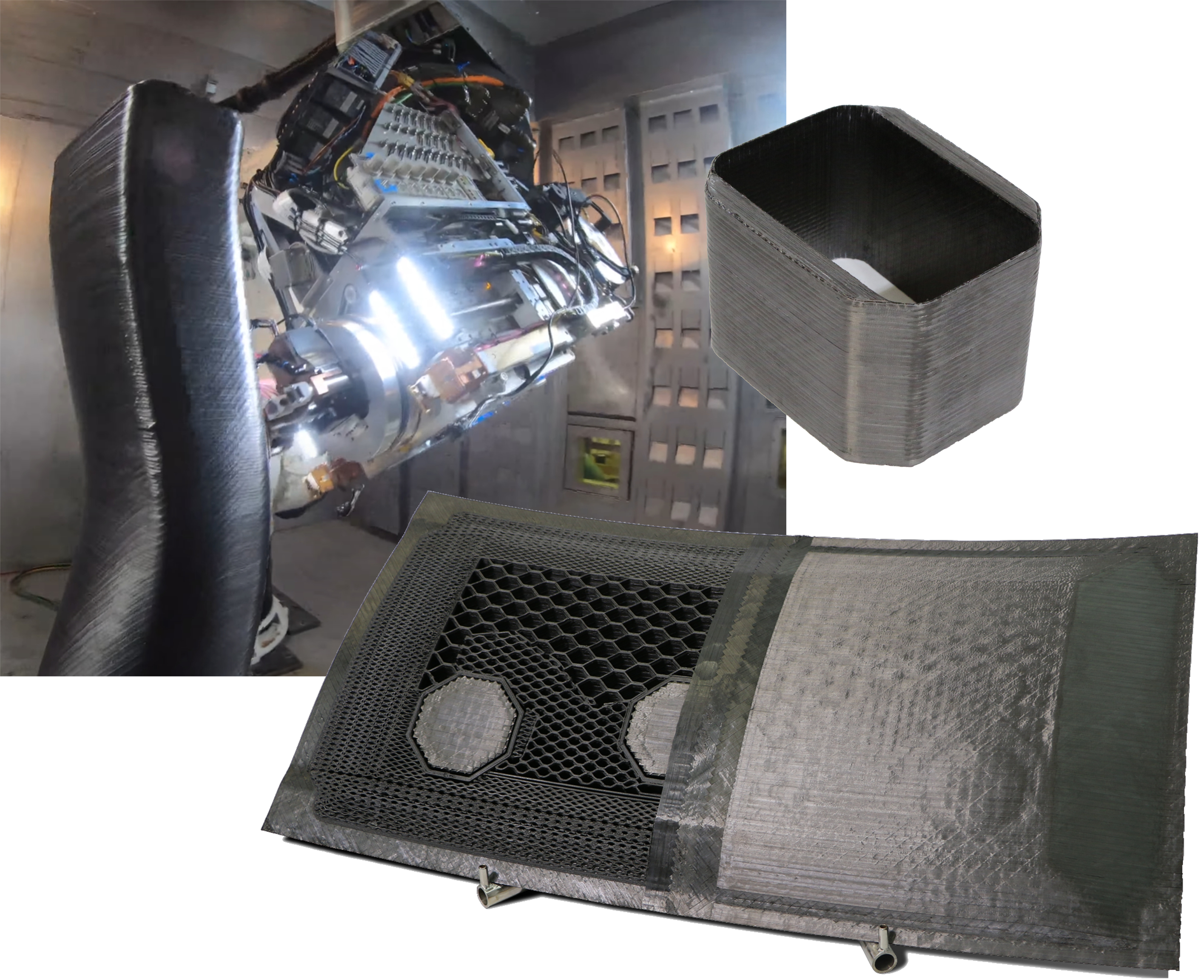
Materiaalformaten en porositeit
Bruin :“We hebben veel verschillende materialen gebruikt, de meeste op maat gemaakt volgens onze specificaties van vezels, hars, vezelvolume en afmetingen. We hebben onlangs geëxperimenteerd met meer in de handel verkrijgbare spleetkabels. De gehakte vezel FFF-filamenten zijn ook gemaakt volgens onze specificatie met dezelfde hars en vezels die we selecteren voor de continue vezeltapes. We hebben filamenten met een diameter van 1, 3,5 en 6,35 millimeter gebruikt. We kunnen groter gaan, maar hebben dat nog niet nodig gehad."
“We bereiken 50-60% vezelvolume voor de AFP, maar aanzienlijk minder voor de FFF-porties omdat die worden geëxtrudeerd. Porositeit is in de orde van traditionele processen buiten de autoclaaf, maar is dramatisch afgenomen naarmate we het proces verfijnen. Met behulp van extreem hoogwaardige materialen en in een laboratoriumomgeving hebben we een porositeit van minder dan 0,5% bereikt, gemeten met CT [computertomografie]-scans. Zoals altijd zijn er een groot aantal variabelen die van invloed zijn op dit aantal en wanneer we zeer complexe onderdelen produceren, is het een uitdaging om een lage porositeit te behouden. We hebben veel destructieve en niet-destructieve tests uitgevoerd op onderdelen en coupons die met het systeem zijn gemaakt.”
Hoognauwkeurige robotbesturing
Bischoff :“SCRAM levert zeer nauwkeurige robottechnologie. Standaard kant-en-klare robots zijn een betaalbare oplossing om een bewegingsvrijheid van 6 graden te bereiken voor plaatsen en afdrukken, maar ze zijn lang niet nauwkeurig genoeg voor AFP van ruimtevaartkwaliteit. Jaren geleden begonnen we uit te zoeken hoe we deze robots konden toepassen op AFP-systemen in de ruimtevaart. Je moet echt de fundamenten van het systeem en de problemen met het bereiken van nauwkeurigheid begrijpen. We hebben een hele robotgroep van 60-70 ingenieurs, en dat is alles wat ze doen.”
“Het is een ongelooflijk complexe kwestie om een hoge positie- en padnauwkeurigheid te bereiken. Je hebt onnauwkeurigheden in de robot (CTE van de robot, speling, trillingen, enz.) en in de externe as, gereedschapspuntkalibraties, een draaiend onderdeelframe en verschillende andere bronnen. Het niet verantwoorden/aanpakken van een van deze kan catastrofaal zijn als je eenmaal begint met printen in een echte 3D-ruimte. Om dit te bereiken, gooien we de controller die bij de robot zit weg en laten we alles draaien met een Siemens CNC. Vervolgens voegen we de gepatenteerde secundaire feedback van Electroimpact toe aan alle robotassen, wat ons van een tolerantie van 30-40 mils [0.030-0.040 inch] naar ±15 mils [0.015 inch] brengt. Vervolgens passen we een kinematische compensatie van hoge orde toe om ±10 mils [0.010 inch] te bereiken.”
Snelheid, eindeffectors en roterende printtafel
Bruin :“We gebruiken in-situ consolidatie, dus de applicatiesnelheid zal niet in de buurt komen van die van thermohardende prepreg-tapes. Dit is ook een robot, geen groot, verstijfd portaalplatform (zoals AFP), dat is gebouwd voor hogere snelheden. En snelheid is niet alleen leggen en printen, maar omvat ook de doorlooptijd voor tooling. De echte maatstaf is hoe snel je een digitaal vervaardigd onderdeel bij de hand kunt hebben?”
"Het deel in de video was 36 inch lang (met de afgedrukte basis was het meer dan 4 voet) en de diameter was 16 inch. Als we non-stop in ploegen zouden draaien, zouden we dit in een paar dagen kunnen produceren, wat een ongelooflijk korte tijd is om een onderdeel in handen te hebben. Onderdelen worden ook rechtstreeks vanuit het CAD-bestand geproduceerd, dus als u moet itereren, wijzigt u de CAD, plaatst u de gereedschapspaden opnieuw en drukt u het nieuwe onderdeel af.”
Allen :“Op dit moment hebben we voor het printen van de ondersteuningstool een opgeschaald, op filamenten gebaseerd proces. De doorvoer is nogal traag, wat van invloed is op de afdruktijd. In juli hebben we onze eerste eindeffector met een pelletschroefextruder in gebruik genomen. Dit zal de output verhogen, maar zal dikke kralen produceren, dus we zullen ook een frees-eindeffector toevoegen voor het machinaal bewerken van het bedrukte oppervlak.”
Bruin :“We zullen een familie van compatibele eindeffectors hebben die de robot kan oppakken en afzetten, en zo nodig een breed scala aan additieve en subtractieve functies kan uitvoeren. De ophaal- en terugbrengprocedure van de eindeffector is volledig geautomatiseerd, wat een standaardfunctie is op al onze AFP-systemen en op SCRAM. De volledige eindeffector is aan de robot bevestigd met behulp van een interfacemodule voor automatische gereedschapswisseling en er zijn standaards voor opslag van eindeffector.”
“Het systeem print op een externe rotatie-as en wordt aangestuurd door de CNC. We hebben dit omdat de robot alleen niet elk punt kan bereiken op de onderdelen die we willen maken. Uiteindelijk willen we het systeem op rails zetten om grotere onderdelen te maken, maar we willen het systeem eerst op deze schaal verfijnen. We hebben gesproken over het gebruik van twee robots, en we weten filosofisch hoe we het zouden aanpakken. (We hebben andere geïntegreerde productiesystemen met meerdere robots geproduceerd.) Maar als je twee robots hebt die in overlappende werkzones werken, wordt de bediening extreem ingewikkeld.”
Toekomstige flexibele productie mogelijk gemaakt
Bruin :“Deze multifunctionele cel gaat waarde leveren aan de eindklant. Het hoeft niet altijd continu vezelversterkte thermoplastische onderdelen te produceren. Door extrusie en frezen toe te voegen aan de continue vezelafzetting, vergroten we het bereik en de flexibiliteit. Sommige van de structuren die we hebben gedemonstreerd, hebben bijvoorbeeld subtractieve functies binnen de onderdeelopbouw. De robot controleert vervolgens het oppervlak en sluit die holte af. Dit is momenteel niet mogelijk zonder meerdere stappen, gespecialiseerde tooling en/of eindmontage.”
“Er is echter een nog groter thema dan alleen het produceren van onderdelen. Op de lange termijn heeft deze benadering de kans om de manier waarop lucht- en ruimtevaart- en defensiesystemen worden ontworpen en vervaardigd drastisch te veranderen. Er zal niet langer een enkele productielijn aan een enkel product worden gewijd. In plaats daarvan zal de productie flexibel zijn. Als u gereedschap kunt verminderen, kunt u ook het aantal reserveonderdelen op de plank verminderen. Deze flexibiliteit heeft gevolgen voor de hele toeleveringsketen, inclusief het verminderen van afval als gevolg van het verstrijken van materialen.”
Bischoff :"Met een handvol SCRAM-cellen en digitale ontwerpen hoeft u alleen maar grondstoffen bij de hand te houden, in plaats van tientallen vaste gereedschappen en thermohardende materialen met een beperkte houdbaarheid."
Bruin :"We hebben nog een weg te gaan voordat de productie echt op deze manier wordt afgehandeld, maar nu kun je duidelijk zien hoe het mogelijk is."
Hars
- ACEO® onthult nieuwe technologie voor 3D-printen met siliconen
- Emiraten adopteren 3D-printtechnologie voor vliegtuigonderdelen
- Een inleiding tot 3D-printen met selectief lasersinteren
- TPU 3D-printen:een gids voor 3D-printen van flexibele onderdelen
- Is 3D-printen klaar voor de productie van eindonderdelen?
- De zekering 1 afdrukken met de zekering 1
- Impossible Objects werkt samen met BASF voor composiet 3D-printen
- Broetje-Automation vergroot AFP-portfolio voor seriële composietproductie
- Victrex en Bond-partner voor 3D-printen van PAEK-onderdelen
- VDMA ontwikkelt roadmap voor 3D-printen met manufacturing roadmap
- Traceerbaarheidspraktijken voor de productie van onderdelen voor precisiebewerking