Op maat gemaakt proces produceert elke minuut composiet rempedaal
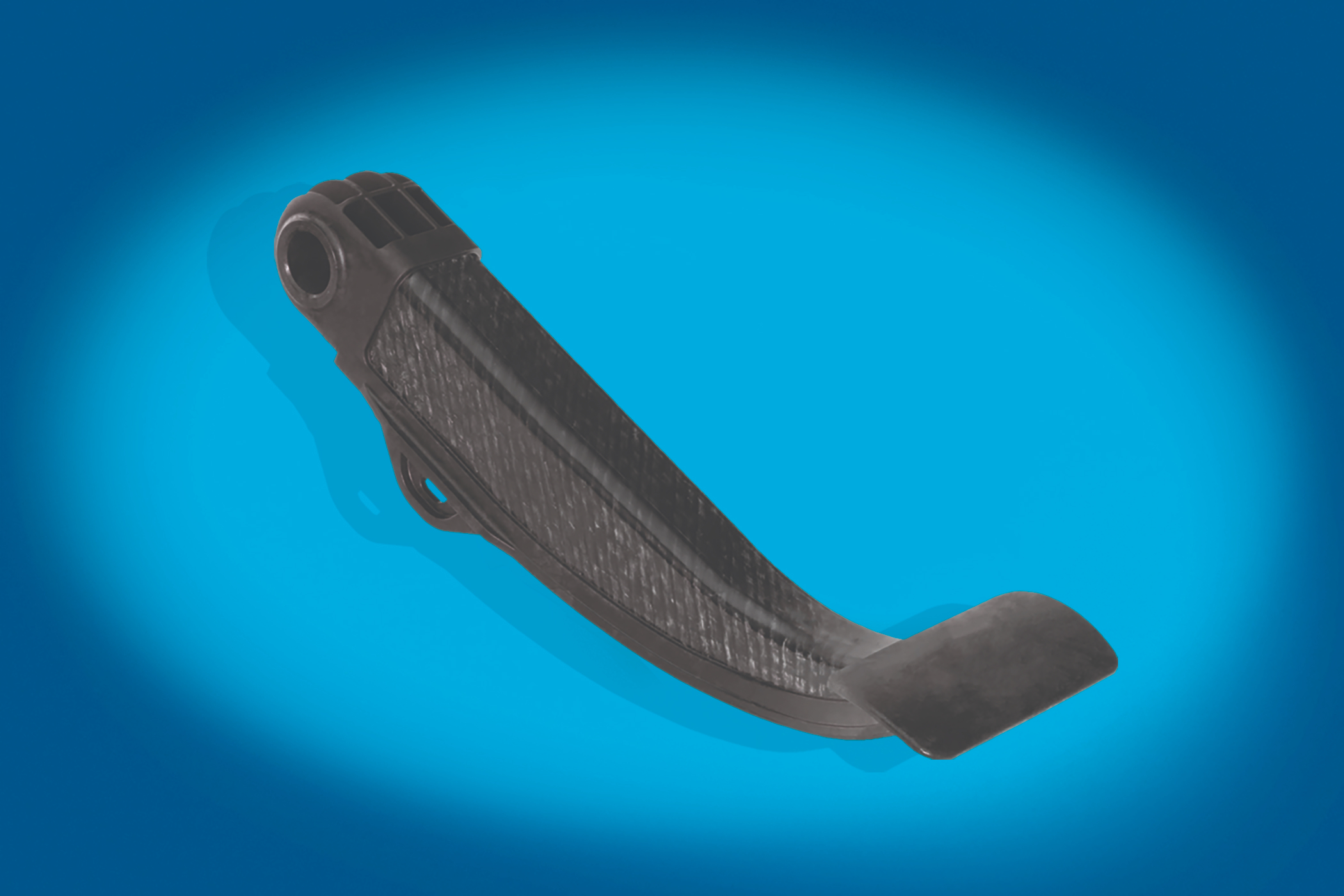
Tier 1 Boge Rubber &Plastics Group (Damme, Duitsland) produceert naar eigen zeggen de lichtste, goedkoopste en sterkste volledig samengestelde rempedalen ter wereld, en de eerste in commerciële productie. Zoals uiteengezet in de FOD van januari (zie "Thermoplastische composietstructuur vervangt metalen op veiligheidskritieke rempedalen"), produceert de leverancier momenteel een kwart miljoen rempedalen per jaar voor vier voertuigplatforms die door Duitse autofabrikanten worden geproduceerd en het systeem zou tot 1 miljoen pedalen per jaar. Dit is belangrijk omdat de pedalen structureel zijn, aan dezelfde strenge prestatie-eisen moeten voldoen als het bestaande staal en aluminium, en de ontwerpen zijn voorzien van drie verschillende soorten glasversterkte thermoplastische composieten.
Drie materialen verhogen de vezelefficiëntie
Om de pedalen licht, dun, kosteneffectief en in staat te houden om te voldoen aan de uitdagende OEM-specificaties, gebruikt Boge continue glasvezel organosheet als de schaalstructuur om de hoofdbelastingen van het onderdeel te dragen, die tot 3.000 Newton kunnen oplopen. Organosheet-blanco's worden voorgesneden op maat geleverd, met twee of drie lagen volledig geconsolideerd door leverancier Lanxess Deutschland GmbH (Keulen, Duitsland). Om de belangrijkste belastingspaden op de onbewerkte organoplaat te versterken, voegt Boge stroken unidirectionele (UD) glasvezeltapes (geleverd door Celanese Corp., Irving, Texas, VS) toe in oriëntaties en lay-ups op basis van simulatieresultaten met eindige elementen. Om dit te doen, gebruikt Boge software die het heeft aangepast en materiaalkaarten die het bedrijf met zijn leveranciers heeft ontwikkeld op basis van spannings-/rekcurves die voor elk materiaal zijn gemeten onder temperatuur- en vochtigheidsomstandigheden die zijn gespecificeerd door OEM-klanten. Om functionele geometrie toe te voegen, gebruikt Boge overmolded gehakte glasvezelverbindingen (van meerdere leveranciers) om structurele ribben en bevestigingsfuncties te bieden.
Alle materialen zijn voorzien van matrixen van voorgekleurd zwart polyamide 6 (PA6), een taai polymeer dat veel wordt gebruikt in de auto-industrie. Mochten OEM-specificaties dit vereisen, dan heeft Boge ook de mogelijkheid om een hogere temperatuur, minder hygroscopische PA6/6-matrix te gebruiken in de overmolding compound, aangezien beide polymeren vergelijkbaar genoeg zijn om aan elkaar te hechten. Door drie verschillende soorten composieten te gebruiken met glasversterking in drie verschillende vormen, is Boge in staat om vezels precies daar te plaatsen waar nodig om aan de prestatie-eisen te voldoen en over-engineering te voorkomen. Het neveneffect van deze hybride-composietbenadering is dat het materiaalgebruik, nominale wanddikte, cyclustijd en totale onderdeelkosten vermindert.
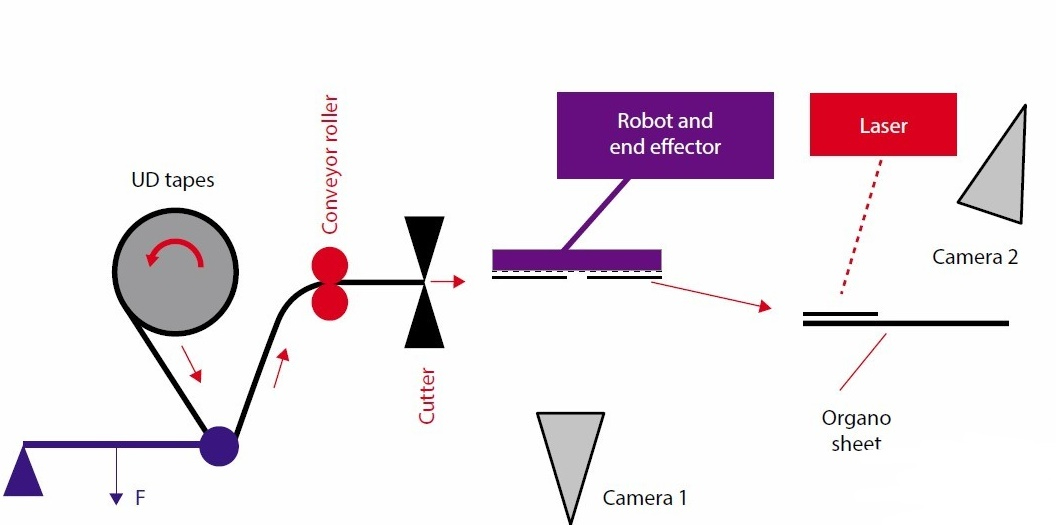
Processtappen en apparatuurcriteria
Samenwerken met automatisering/assemblagelijnontwikkelaar M.A.i. GmbH &Co. KG (Kronach, Duitsland), heeft Boge een productieproces in drie stappen ontwikkeld dat snel en efficiënt is en kwaliteitsgecontroleerde onderdelen produceert tegen betaalbare kosten. Bij het ontwerpen van proces en apparatuur had het team een aantal eisen. Ten eerste moesten de bedrijven, om de onderdeelkosten laag te houden, de totale effectieve cyclustijd op ongeveer 1 minuut houden. Om dit te bereiken zou automatisering nodig zijn om ervoor te zorgen dat materialen soepel door de productiecel gaan.
Ten tweede, terwijl de organosheet-blanco's voorgestapeld, volledig geconsolideerd en voorgesneden op maat (voorgevormd) worden geleverd, betekende de vereisten van verschillende pedaalontwerpen dat het team flexibiliteit nodig had om tapestroken van verschillende lengtes op verschillende locaties en richtingen te snijden, oriënteren en plaatsen op verschillende locaties en richtingen om de hoofdbelastingspaden van de organosheetschaal. Nogmaals, om de kosten laag te houden, werd een op maat gemaakt tape-legproces ontworpen om een hoge mate van flexibiliteit en controle te bieden, evenals snelheid.
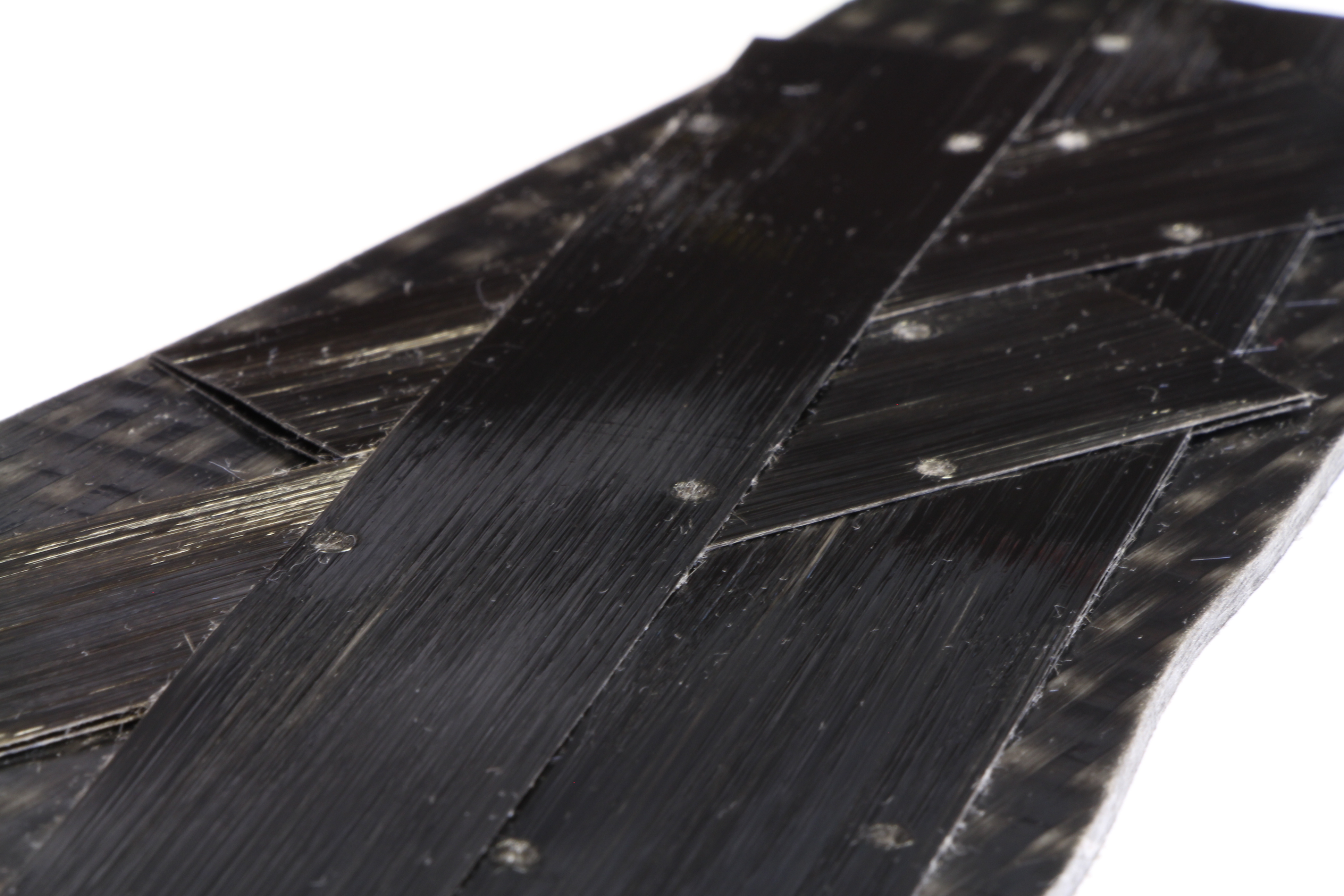
Aan het begin van het proces bevat de productiecel twee stapels voorgesneden organosheet-blanco's in cassettes en vier spoelen met UD-tapes tegelijk. Eerst pakt een robot een voorgevormde blanco organoblad op en verplaatst deze naar het werkoppervlak. Tegelijkertijd wordt UD-tape uitgevoerd en op de gewenste lengte gesneden. Strips worden vervolgens op een vacuümband geplaatst die ze op hun plaats houdt terwijl de transportband voortgaat. Vervolgens plukt een robot met een draaiende pick-and-place unit (eindeffector) strip voor strip van de vacuümband en controleert een camera elke strip op kwaliteit, afmeting en positie. Wanneer alle vier de stukken zijn opgepakt, gaat de robot naar de werkruimte en begint hij één strook per keer op de organosheet-blanco te plaatsen op de locatie en positie die zijn bepaald door op beeld gebaseerde positiecorrectie. Omdat elke strip wordt gepositioneerd, wordt voorkomen dat deze verschuift door meerdere puntlassen die door een laser zijn gemaakt. Ondertussen worden er meer tapestrips gesneden en op de vacuümband geplaatst en het proces herhaalt zich totdat alle tapes die nodig zijn voor een bepaald rempedaalontwerp zijn gestapeld en in de juiste positie op het organoblad geplakt.
Het systeem dat deze op maat gemaakte vezelblank produceert, is 100% numeriek bestuurd, waarbij elk aspect van de bewerking volledig programmeerbaar is voor maximale flexibiliteit. Bij elke stap detecteren camera's of andere sensoren, die zijn aangesloten op het online kwaliteitscontrolesysteem (QC) van het systeem, alle randen en posities van tapestrips en de organosheetschaal en vergelijken geometrische gegevens voor deze materialen met bekende parameters om te verzekeren dat elk materiaal is geplaatst waar het moet zijn.
Om de productiesnelheden hoog te houden, gaat de onbewerkte vezelplaat vervolgens naar een infraroodoven om beide materialen te verwarmen net voordat de tapes op het organoblad worden gedrapeerd/voorgevormd/consolideerd. Een speciaal antioxidantpakket in tape- en organosheetharssystemen voorkomt thermische schade. Vervolgens wordt de hete plano snel in de drapeer-/voorvormholte bewogen waar hoge druk wordt gebruikt om de plano in een U-kanaalvorm te vormen terwijl een hoogwaardig oppervlak wordt gegarandeerd. Het QC-systeem bewaakt opnieuw de consolidatie- en preformkwaliteit via tijd, temperatuur en druk.
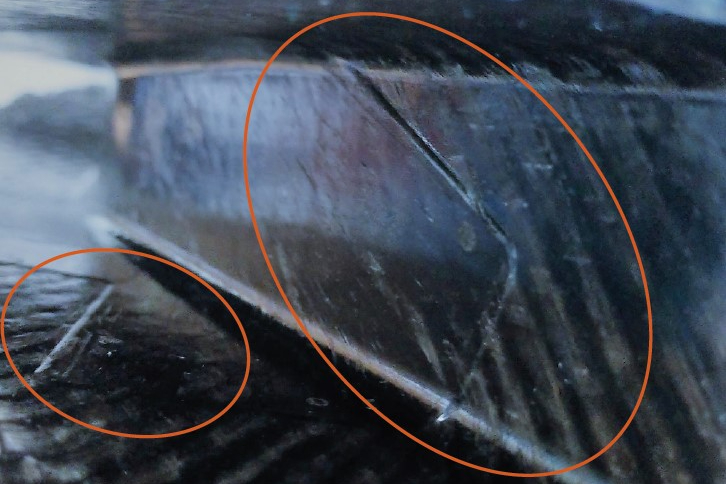
Ten slotte wordt het nog warme en gedrapeerde stuk in een spuitgietmatrijs geschoven waar het wordt overgoten met een korte glas/PA-verbinding om extra geometrie te creëren, zoals een complexe ribstructuur aan de onderkant. Na het ontvormen vindt een snelle, geautomatiseerde trim en visuele inspectie plaats. Er is geen verf of andere oppervlakteafwerking nodig. De uiteindelijke pedaalmaat is ongeveer 350 x 90 x 60 millimeter. Voordat het de productiecel verlaat, wordt op elk pedaal een unieke QR-code aangebracht om het terug te koppelen naar de fabricage- en materiaalgegevens voor dat pedaal in het kwaliteitssysteem. Na montage wordt een functionele test van het pedaal binnen de beugel en een laatste robotinspectie uitgevoerd. Ervan uitgaande dat de eenheid slaagt, wordt er nog een QR-code op het voltooide rempedaalsamenstel aangebracht om volledige traceerbaarheid van elk pedaal en aanvullende componenten te bieden voorafgaand aan verzending naar de OEM.
Omdat rempedalen veiligheidskritieke onderdelen zijn en moeten voldoen aan veeleisende OEM-prestaties en kwaliteitseisen, hebben Boge en zijn partners meerdere faalveilige mechanismen ingebouwd in het Industry 4.0-conforme QC-systeem om snel en nauwkeurig te verifiëren dat aan de specificaties werd voldaan bij elke stap in het proces. het proces. QC-gegevens worden opgeslagen en elk pedaal krijgt een uniek identificatienummer in de vorm van een QR-code om 100% traceerbaarheid te garanderen van materiaal, ploegen en procesomstandigheden die betrokken zijn bij de productie van dat onderdeel.
De volledig composiet rempedalen die Boge produceert, wegen ongeveer de helft van het gewicht van pedalen in metaal. Ze verbeteren ook het rijgevoel voor consumenten, zijn 100% recyclebaar aan het einde van hun levensduur en voldoen aan of overtreffen de sterkte-eis voor bestaand staal.
Hars
- De meest populaire composiet fabricagemethoden
- Cryogeen ontbramen en ontbramen
- Eerste volledig kunststof rempedaal voor batterij-elektrische sportwagen
- Solvay breidt capaciteit thermoplastisch composiet uit
- Thermoplastisch wiel neemt de ruige weg
- Depositieproces en eigenschappen van stroomloze Ni-P-Al2O3-composietcoatings op magnesiumlegering
- Architectonische bekledingscomposiet onthuld
- Betere composietfietsen maken in Arkansas
- Hoe het CMC-proces werkt
- De 4 kritieke dingen die elke kantpersoperator moet weten
- 4 dingen die elke bediener van een afkantpers in zijn slaap moet weten