Overall Equipment Effectiveness (OEE) – Een praktische gids
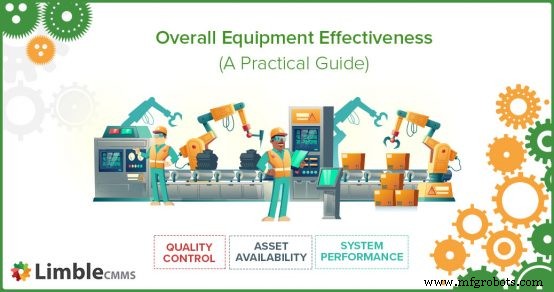
OEE (algemene effectiviteit van apparatuur) is een van de beste metingen die u kunt gebruiken om productieprocessen te optimaliseren.
Als we het hebben over productie op schaal, kunnen kleine verbeteringen een aanzienlijke boost geven aan uw bedrijfsresultaten. Dat is vooral duidelijk in de maakindustrie, waar het besparen van een paar seconden op één productieproces of het verminderen van het aantal defecten met slechts 1% elke maand tienduizenden dollars kan opleveren.
Lees dit artikel verder en ontdek hoe u optimaal kunt profiteren van OEE en de productie-output kunt maximaliseren. We bespreken definities, leggen formules uit en geven praktische voorbeelden.
Het wat en waarom van OEE
We zullen niet tegen je liegen. OEE kan ingewikkeld aanvoelen. Maar die complexiteit geeft je zoveel nuttige informatie. We zullen het allemaal opsplitsen en het stap voor stap doen.
OEE staat voor "Overall Equipment Effectiveness". Kortom, OEE is een key performance indicator (KPI) die de ideale prestaties van uw apparatuur vergelijkt met de werkelijke prestaties.
Het is een kwantificeerbare (d.w.z. gebruikt cijfers) manier om erachter te komen hoe goed uw apparatuur, mensen en processen hun werk doen door te meten:
- beschikbare tijd/uptime (beschikbaarheid )
- snelheid en consistentie behouden (prestaties )
- die weinig defecten produceert (kwaliteit .) )
OEE gebruikt productiviteitsgegevens om het percentage goede productietijd op een activum te vinden. Dat betekent dat elk apparaat zijn eigen OEE-score krijgt.
Hoewel het scoren van elke machine misschien stom klinkt, is het de moeite waard. OEE meet de productiviteit van de machine, ja. Maar het houdt ook rekening met de mensen die ze runnen. U weet net zo goed als wij dat machines niet altijd het probleem zijn. Personeel en processen zullen net zo goed de productiviteit verlagen.
Productie-utopie
Uw nieuwe machines zijn in topconditie en gaan nooit kapot. Uw personeel is goed opgeleid, komt nooit te laat en heeft nooit pauzes nodig. Je produceert maar één soort product in alle ploegen, ooit. Als een proces eenmaal is ingesteld, wordt het 100% van de tijd gevolgd.
Dat soort perfectie is onmogelijk (en het is ook een beetje griezelig op die sci-fi manier). Daar zal omschakelingen en defecten zijn. Er zullen downtime, storingen, personeelsproblemen en stappen zijn die worden gemist. Een warme en vochtige dag, waar niemand controle over heeft, zal iets - of iemand - oververhitten. En dat zijn slechts kleine problemen.
Aangezien we weten dat 100% productiviteit onbereikbaar is, hoe weet u dan wanneer u genoeg doet? Hoeveel afwijking van dat sci-fi-productiviteitsniveau is oké? En als je er te ver van afdwaalt, hoe begin je dan zelfs maar beter te worden?
Dit alles is waarom OEE in de eerste plaats bestaat. U weet dat productiviteit nooit perfect zal zijn. OEE geeft u een manier om te beoordelen hoe dicht uw proces het ideaal benadert. Niet alleen dat, het geeft je ook aanwijzingen over hoe je kunt verbeteren:
- het helpt je te achterhalen waar problemen optreden, zodat je ze gemakkelijker kunt oplossen
- het is een diagnose tool voor uw productieproces
- het brengt snel verliezen en zeer productieve gebieden aan het licht
- het helpt je steeds dichter bij je hoogste productiviteitsniveau te komen
Een paar dingen die u moet weten voordat u OEE begint
Als u met OEE begint, zijn er een paar best practices die u moet volgen om uw succes te garanderen.
Begin bij goed
De algehele effectiviteit van apparatuur brengt uw productieprogramma van goed naar geweldig - dus u moet beginnen met "goed". Dit betekent:
- Het hebben van solide SOP's (gestandaardiseerde operationele procedures)
- In staat zijn om gegevens over productiviteit in de loop van de tijd te meten en bij te houden
Als je in de Onderhoud zit, zijn deze misschien niet direct onderdeel van je baan. U moet samenwerken met uw productielijnen en managers. Ze hebben toegang tot de gegevens die je nodig hebt en zijn partners voor je bij het oplossen van problemen zodra je ze hebt gevonden.
Jij bent op jouw beurt ook een partner voor hen. Uw onderhoudsprogramma moet ook op een goede plek staan, met goed geoliede PM en tools zoals Limble om te helpen bij het verzamelen van gegevens.
Het lange spel spelen
OEE kan aanzienlijke beloningen verdienen. Maar velen vermijden het vanwege de moeite die het kost om de gegevens die u nodig heeft in de loop van de tijd bij te houden en te verzamelen.
Als u middelgrote of grootschalige productie uitvoert, zult u blij zijn dat u het de tijd en moeite hebt gegeven. Een besparing van twee seconden hier en drie defecten daar zal een grote impact hebben op uw bedrijfsresultaten. En zodra u die verbeteringen aanbrengt, zullen de besparingen en efficiëntie die u wint alleen maar toenemen in de loop van de tijd.
Diep gaan
OEE geeft u een diepgaand inzicht in uw productiviteit. Met deze grotere diepte en detail zul je merken dat je veel kunt doen wat je voorheen niet kon. OEE meet de productiviteit van de machine, ja. Maar het houdt ook rekening met de mensen die ze runnen.
U weet net zo goed als wij dat machines niet altijd het probleem zijn. Personeel en processen kunnen net zo goed problemen veroorzaken en de productiviteit verminderen. Inzicht krijgen in alle onderdelen van uw strategie is waar OEE om draait, zodat u:
- Knijp elke druppel uit je apparatuur
- Verminder het aantal defecte producten
- Maximaliseer de productiviteit van het personeel
- Verlaag reparatiekosten door problemen vroeg op te merken
- Elimineer verspillende stappen in uw productieproces
- Behaal productie-efficiëntie
Als u eenmaal op weg bent naar die verbeteringen, bent u goed op weg naar een slank productieproces.
Bij grootschalige productie moet je dieper graven om verder te gaan.
De basis leggen voor OEE
Voordat we met de kop in de wiskunde duiken, moeten we een paar belangrijke statistieken pakken. U kunt dit gebruiken als een checklist om er zeker van te zijn dat u heeft wat u nodig heeft. Voor alles wat u momenteel niet meet, moet u een proces uitwerken om die gegevens te verzamelen voordat u met uw OEE-berekeningen begint.
Simpel gezegd, de nummers die je nodig hebt, vallen in twee hoofdcategorieën:onderdelen en tijd.
Het aantal geproduceerde onderdelen meten
- Goede telling – het aantal goede onderdelen (die de eerste keer aan de kwaliteitsnormen voldoen) gemaakt gedurende een bepaalde periode.
- Totaal aantal – het aantal alle onderdelen (inclusief defecten) gemaakt tijdens een bepaalde periode.
- Defect aantal – Het aantal defecte onderdelen (afgekeurd omdat ze niet voldoen aan de kwaliteitsnormen) gemaakt gedurende een bepaalde periode.
Meten hoeveel tijd productie in beslag neemt
We kunnen meten:
- Geplande productietijd: Totale tijd dat een apparaat wordt verwacht en volgens planning zal werken.
- Duurtijd :De hoeveelheid tijd dat een proces daadwerkelijk wordt uitgevoerd. Runtime is exclusief downtime, maar wel omvatten kleine stops, vertraagde productie of tijd besteed aan het adresseren van afgekeurde onderdelen.
- Stoptijd :De totale hoeveelheid tijd dat de productie is gestopt vanwege zowel ongeplande als geplande stops. Geplande tussenstops zijn wanneer de productie wordt stopgezet vanwege een geplande gebeurtenis zoals een omschakeling of een voorbereidingsgebeurtenis. Ongeplande stops zijn wanneer de productie wordt stopgezet vanwege een ongeplande gebeurtenis zoals een storing of materiaaltekort.
Uw ideale productiviteit meten
Naast deze echte cijfers, moet u een ideale . hebben ter vergelijking. Denk eens terug aan het beeld dat we iets eerder schetsten van 100% productiviteit. In dat geval, hoeveel delen zou produceer je in een uur? Hoe lang zou het duren om een goed stuk te maken?
Ook al zul je ze nooit bereiken, het is noodzakelijk om te weten hoe 100% productiviteit eruit kan zien als je wilt weten hoe dicht je daarbij bent. Dit zijn de ideale productiviteitsmaatregelen die u moet instellen.
- Ideale cyclustijd: de ideale tijd die nodig is om één . te produceren deel.
- Ideale snelheid: het maximale aantal onderdelen gemaakt in een minuut onder ideale omstandigheden/bij maximale productiviteit.
- Netto-runtime: de snelste/ideale hoeveelheid tijd die nodig is om een bepaald aantal onderdelen te produceren.
Idealen zijn hypothetisch (d.w.z. ze zijn verzonnen). Ze moeten hoog genoeg zijn zodat je altijd iets hebt om naar toe te werken. Maar niet zo hoog dat het geen relevante vergelijking is.
Dus de voor de hand liggende vraag is deze:als al deze ideale metingen verzonnen en onmogelijk te bereiken zijn, hoe weet je dan in hemelsnaam wat ze zouden moeten zijn?
Hoe stel je een ideaal in?
Baseer je idealen op de minste tijd die nodig is om een onderdeel te maken. Om dat te vinden, moet u met uw collega's samenwerken om het volgende te overwegen:
- Machinecapaciteit
- Productiedoelen
- Vaardigheidsniveau machinebedieners
- Planningsproblemen of conflicten met andere apparatuur
- Kwaliteit en beschikbaarheid van materialen
Werk samen met andere leiders om de ideale statistieken te ontwikkelen die geschikt zijn voor u en uw bedrijf.
De formules:hoe OEE te berekenen
Terwijl we erin duiken, laten we één basisregel instellen voor de getallen die je gebruikt:gebruik altijd de kleinst mogelijke meeteenheid. Anders krijgt u niet de juiste OEE-score. Dat betekent dat tijd wordt weergegeven als seconden in plaats van minuten of uren.
Laten we dat in de praktijk brengen en nu een kleine rekenkundige warming-up doen om vast te stellen dat er 3.600 seconden in een uur zitten. Dat zie je terug in onze onderstaande voorbeelden:
60 seconden in een minuut x 60 minuten in een uur =3600 seconden in een uur
Zien? U kunt dit doen.
De eenvoudige OEE-formule
Als OEE nieuw voor u is of een atypisch productiemodel of -proces heeft, kunt u hiermee beginnen. Het gebruikt minder berekeningen om tot een score te komen, maar biedt niet zoveel diepte of detail. Het gaat als volgt:
Voer eenvoudig de nummers in die u voor elk item hebt verzameld en sluit ze aan op deze formule. U heeft dan een eenvoudige OEE-score. Laten we een voorbeeld met reële getallen doornemen.
- Het snelste dat uw productiesysteem één onderdeel kan maken, is 6 seconden per onderdeel. Uw ideale cyclustijd is dus 3.
- Laten we ook doen alsof je 4.000 van die onderdelen moet maken. Dat maakt dat je goed 4.000 telt.
- Als je de een met de ander vermenigvuldigt, zul je zien dat het idealiter ongeveer 12.000 seconden zou kosten om die 4.000 delen te maken. Als we wat meer rekenen, komt 12.000 seconden op 3 uur en 20 minuten voor die 4.000 onderdelen, op voorwaarde dat er geen onderbrekingen, defecten, enz. zijn.
- Je dienst duurt 18.000 seconden (of 5 uur). Dit is uw geplande productietijd.
- Als je 12.000 deelt door 18.000, krijg je .667.
- Converteer dat naar een percentage (d.w.z. verplaats de komma twee plaatsen naar links en voeg een %), en je ziet dat je ongeveer 66,7% OEE hebt.
Laten we eens kijken in formuleformaat:
(ideale cyclustijd van 3 seconden x goede telling van 4.000) / geplande productietijd van 18.000 seconden =66,7%
Laten we zeggen dat 500 van de 4.000 producten die we hebben gemaakt defect waren. Welke invloed heeft dat op onze OEE-score met deze berekening?
(ideale cyclustijd van 3 seconden x goede telling van 3.500) / geplande productietijd van 18.000 seconden =58,3%
Dat is nogal een verschil!
Hoewel dit een acceptabele berekening van OEE is, geeft het ons onvoldoende inzicht om te weten wat we moeten veranderen als we het willen verbeteren. Daarvoor moeten we de geavanceerde versie van deze berekening gebruiken.
De geavanceerde OEE-berekening
De volledige OEE-score omvat drie cijfers, en elk ervan vergt een beetje wiskunde om op zichzelf te komen. Het is niet moeilijk, maar er zijn een paar stappen bij betrokken, dus als je dit op een maandagochtend leest, laten we dan nog een kop koffie pakken en beginnen.
Beschikbaarheid
Beschikbaarheid is de hoeveelheid tijd dat uw apparatuur of proces naar behoren werkt. Het is het percentage van uw geplande productietijd dat werd besteed aan het produceren (runtime ). Hier is de formule daarvoor:
Als we ons voorbeeld van hierboven gebruiken, hoewel onze geplande productietijd een shift van 5 uur was (18.000 seconden), stopte de productie gedurende 45 minuten (2.700 seconden) vanwege een storing. Dat geeft ons een looptijd van 15.300 seconden.
15.300 Runtime / 18.000 Geplande productietijd =0,85
Deel 15.300 door 18.000 en doe onze magie achter de komma, en we krijgen een beschikbaarheidsscore van 85% . Dit is het eerste getal in onze geavanceerde OEE-score.
Prestaties
Dit is de snelheid van uw productieproces en uw vermogen om in de loop van de tijd in dat tempo te blijven. Het is het percentage van hoe dichtbij uw runtime was ideaal.
In ons voorbeeld hierboven weten we dat het 3 seconden zou duren om één onderdeel onder perfecte omstandigheden te maken. Het maken van 4.000 onderdelen zou 12.000 seconden in beslag nemen. Aangezien onze werkelijke looptijd om dat aantal 17.100 seconden te maken, ziet onze berekening er als volgt uit:
(3 seconden Ideale cyclustijd x 4.000 totaal aantal) / 15.300 looptijd =.784
Dat is een prestatiescore van 78,4% . Niet slecht!
Kwaliteit
Kwaliteit verwijst naar, nou ja, de kwaliteit van onderdelen en hoe vaak je defecten maakt. En deze is vrij eenvoudig. Het is het percentage van alle onderdelen die je hebt gemaakt dat aan je kwaliteitsnormen voldeed (goed).
Als we ons voorbeeld hier gebruiken, weten we dat van de totale onderdelen die we hebben gemaakt (4.000), 3.500 aan onze normen voldeden. Dus...
3.500 goede onderdelen / 4.000 totale onderdelen =.875
Dat is een kwaliteitsscore van 87,5% .
Uw definitieve OEE
We gaan nu de thuiswedstrijd in! We hebben onze scores voor beschikbaarheid, prestaties en kwaliteit. Laten we ze combineren om onze definitieve OEE te krijgen.
.85 Beschikbaarheid x .784 Prestaties x .875 Kwaliteit =.583
Gefeliciteerd. Je hebt het gehaald! U heeft een OEE-score van 58,3% .
Dat is geweldig!
... is het niet? Of is dat niet zo geweldig? Of ergens tussenin? Hoe weten we? We hebben onze OEE-score en nu hebben we een beetje context nodig. Gelukkig is er veel onderzoek om je te helpen je score te interpreteren en te vergelijken met industriestandaarden. Verder!
Uw OEE-beoordeling interpreteren
Nu je je heldere en glanzende nieuwe OEE-score hebt, gaan we eens kijken wat het betekent en hoe het zich verhoudt tot anderen.
Eerste basislijn
Voordat u begint aan het pad naar continue verbetering en lean manufacturing, is het belangrijk om duidelijk te zijn over de reikwijdte van uw beoordeling. Als dit uw eerste OEE-score is, zal deze dienen als uw baseline, de benchmark waarmee u alle toekomstige scores vergelijkt.
Het zal het startpunt zijn om toekomstige OEE-scores te vergelijken en verbeteringen te meten. Houd bij het maken van deze verbeteringen en vergelijkingen rekening met:
- Hoeveel gegevens heeft u in deze baseline opgenomen? Meting over een langere periode geeft een nauwkeurigere score.
- Welk deel van het productieproces was inbegrepen? Overweeg om OEE-scores van verschillende ploegen of machines te vergelijken.
Wat het nummer zelf betekent
OEE-scores zijn altijd percentages, ongeacht wat ze meten. Ze zijn op deze manier ontworpen, zodat ze gemakkelijker te vergelijken zijn. Dit helpt u te weten hoe uw OEE zich verhoudt tot anderen, zowel binnen als buiten uw bedrijf.
We kunnen zien dat een OEE van 85% prestaties van wereldklasse is. Een score van 60% is heel gebruikelijk en impliceert dat er ruimte is voor substantiële verbetering. En 40% OEE is typisch voor degenen die net beginnen met het proces van tracking en continue verbetering.
We weten nu dat onze score van bovenaf van 58,3% OEE redelijk gemiddeld is - niet slecht, niet geweldig - en dat we nog wat ruimte hebben voor verbetering.
via GIPHY
De sleutel hier is dat het verkrijgen van uw OEE-score nog maar het begin is, ongeacht uw score en hoe deze zich verhoudt tot die van anderen. Uw OEE kan u niet alleen vertellen waar u staat, maar hij kan u ook vertellen welke kant u op moet gaan om te verbeteren.
De zes grote verliezen
OEE is niet de auto die uw organisatie zal verbeteren, maar dat bent u. Maar OEE biedt wel de routekaart om u te brengen waar u heen wilt.
De weg naar uw OEE-score kan lang en bezaaid zijn met wiskundige wendingen en bochten. De waarheid is dat die wendingen - elk nummer en elke formule die je hebt gebruikt - je duidelijk vertellen hoe je kunt verbeteren.
Dit is het echte doel van OEE:u helpen de "zes grote verliezen" aan te pakken. De zes grote verliezen zijn de problemen die het meest leiden tot inefficiëntie en verspilling in de productie. Ze vallen in drie groepen en – verrassing! – je weet al wat ze zijn:
- Beschikbaarheidsverliezen
- Prestatieverliezen
- Kwaliteitsverliezen
De zes grote verliezen. Bron : OEE.com
Vervolgens zullen we alle drie de categorieën doornemen, u vertellen wat de zes grote verliezen zijn en hoe u deze kunt aanpakken. Omdat ze allemaal rechtstreeks in uw OEE-score worden verwerkt, ziet u uw OEE-score in de loop van de tijd stijgen als u ze corrigeert.
De beschikbaarheidsverliezen verminderen
De eerste twee van de zes grote verliezen vallen onder jouw score en hebben te maken met het zoveel mogelijk draaiende houden van je proces. Als uw beschikbaarheidsscore laag is, duik dan in uw runtime en plan de productietijdcijfers .
Schemaverlies wordt niet in aanmerking genomen voor OEE-berekeningen, omdat het geen zin heeft om OEE te meten op momenten dat de productie niet eens zou moeten draaien. Schemaverlies wordt gebruikt voor het berekenen van TEEP (Total Effective Equipment Performance).
Groot verlies #1:uitval van apparatuur (ongeplande uitvaltijd)
Uitval van apparatuur is uw belangrijkste bron van ongeplande stops en stationair draaien. Als ongeplande downtime uw bedrijfstijd naar beneden haalt, moet u hier beginnen.
De oplossingen zijn:
- Maak een degelijk preventief onderhoudsplan . Of, als je kunt, sensoren gebruiken op je meest kritieke productiemiddelen en conditiegebaseerd of voorspellend onderhoud uitvoeren.
- Implementeer een gebruiksvriendelijk CMMS zoals Limble . Het zal u helpen het meeste uit uw PM te halen, storingen te verminderen en de prestaties van de apparatuur te maximaliseren.
- Houd uw uitvaltijd bij. De meeste CMMS-oplossingen hebben modules voor het volgen van shutdowns en hun redenen. Limble maakt dit eenvoudig met aangepaste dashboards waarmee u automatisch rapporten over apparatuurproblemen kunt ophalen. Ze helpen je de grootste problemen te identificeren, zodat je ze op het juiste moment kunt repareren of vervangen.
- Voorspel en implementeer maatregelen om shutdowns te voorkomen. Zodra u patronen in uw downtime vindt, kunt u ze vermijden. Als een apparaat kapot gaat na een bepaalde gebruiksduur, plan je diensten daar dan omheen totdat je een oplossing voor de langere termijn hebt.
via GIPHY
Big Loss #2:Setup en aanpassingen (geplande downtime)
Het instellen en aanpassen van apparatuur kost tijd. Er is geen ontkomen aan. Het goede nieuws is dat ze ons ruimte geven om te verbeteren. Doe ze op het juiste moment – op de juiste manier – om productieverliezen te minimaliseren.
Hier leest u hoe u de frequentie en lengte van deze geplande stops kunt verminderen:
- Grotere batches betekent minder batches – en minder materieelwissels op uw werkvloer. Als je het totale aantal eenheden dat je uiteindelijk nodig hebt goed kunt voorspellen, kun je je productie veel efficiënter plannen. (Als u een continu productiesysteem gebruikt, hoeft u hier niet over na te denken.)
- Implementeer Single-Minute Exchange of Die (SMED) techniek. De SMED-techniek is een principe van lean production. Kijk goed wat er gebeurt tijdens je geplande stops. Zoek naar manieren om stappen te elimineren of te verkorten. Je doel is om zo snel mogelijk te stoppen - zo dicht mogelijk bij een minuut of een enkel cijfer als je kunt.
Prestatieverliezen verminderen
De volgende twee van de zes grote verliezen vallen onder je prestatiescore en hebben, kortom, te maken met snelheid. Door deze twee verliezen aan te pakken, kunt u uw productie maximaliseren.
Als je prestatiescore laag is, kijk dan naar de consistentie van je looptijden en cyclustijden.
Groot verlies #3:kleine onderbreking
Kleine stops zijn moeilijk te controleren en kunnen onbelangrijk lijken. De waarheid is dat veel kleine stops in een grootschalig productieproces snel oplopen. Hier is waar te beginnen.
Afwijkingen in realtime aanpakken
Train machinisten om meer kleine problemen ter plaatse op te lossen. Dit is de basis voor autonoom onderhoud en bespaart veel tijd. Uw onderhoudsteam heeft meer tijd voor ernstigere storingen en uw productieteam hoeft niet te wachten om een kleine storing te verhelpen.
Als je een CMMS zoals Limble hebt, heb je een uitstekende tool tot je beschikking om AM te starten. Door ze toegang te geven tot Limble, hebben ze alle hulp en instructies die ze nodig hebben binnen handbereik.
Volg patronen van prestatieverlies
Wanneer zijn kleine stops of langzame cycli het meest waarschijnlijk? Patronen in deze gegevens kunnen u helpen de hoofdoorzaak te vinden en te voorkomen.
- Daalt de productie tijdens een bepaalde dienst?
- Na routine-onderhoud?
- Na een bepaalde looptijd?
Proces standaardiseren
Er is een reden waarom SOP's bestaan. Ze zijn meestal goed onderzocht en grondig getest. We hebben het al eerder gezegd en we zeggen het nog een keer:volg elke keer hetzelfde proces. Dit leidt tot minder fouten en kleine stops en daarom werken veel organisaties waar mogelijk aan procesautomatisering.
Groot verlies #4:verminderde snelheid
Optimaliseer uw productiecyclus en snelheid
Verlaagde snelheid is bijna altijd het gevolg van slijtage, slecht onderhoud of misbruik. Dit is een gebied waar wij mensen mee kunnen omgaan. Naarmate we ouder worden, hebben we de neiging om wat langzamer te worden. Maar als we een goed trainingsregime hebben en voor onszelf zorgen, kunnen we lange, lange tijd in een goed tempo doorgaan.
Doe hetzelfde voor uw apparatuur. Het in topconditie houden is het beste wat je kunt doen om het zijn productiesnelheid te behouden. Doe wat u moet doen om uw PM-programma te versterken. Train uw machinebedieners om de apparatuur op de juiste manier te gebruiken en er zorg voor te dragen. Geef het een naam en koop bloemen als je wilt. Het punt is, behandel het goed.
Kwaliteitsverliezen verminderen
via GIPHY
Een kwaliteitsscore van minder dan 100% betekent dat uw productieproces leidt tot defecte goederen.
Hoe lager de kwaliteitsscore, hoe hoger het percentage defecten. Kijk naar de productieprocessen en apparatuur op plaatsen waar uw kwaliteitsscore het laagst is.
Groot verlies #5:productafval
De meeste defecten zijn het gevolg van verslechtering van uw apparatuur. Volg de soorten defecten die u ziet en houd verouderde apparatuur nauwlettend in de gaten.
Mogelijk hebt u een zeer bekwaam onderhoudsteam dat de apparatuur draaiende kan houden. Maar er zal een tijd komen dat de verminderde snelheid en het aantal defecten en herbewerkingen niet de moeite waard zijn om de asset online te houden. Het is gewoon logischer om het te vervangen.
Groot verlies #6:opstartschroot
Verminder de opstartproductie
Het is gemakkelijk om opgewonden te raken als je eindelijk oude apparatuur vervangt. De oude is misschien zo lang zo traag en inefficiënt geweest dat je het gevoel hebt dat je de verloren tijd moet inhalen.
Weersta de drang om hem meteen in een hogere versnelling te trappen. Het kan enkele batches duren voordat het product aan uw kwaliteitsnormen voldoet. Houd het in de tussentijd bij kleinere porties. Hiermee kunt u problemen vinden en oplossen voordat u op volle kracht draait, waardoor u tijd en materiaal bespaart.
Kwaliteitsvariatie verminderen
Als de nieuwe apparatuur eenmaal is ingesteld en goed werkt, ga er dan niet vanuit dat dit zo zal blijven. Instellingen vinden manieren om te verschuiven en materialen veranderen in de loop van de tijd. Controleer beide in het begin vaak, zodat u eventuele wijzigingen snel kunt oplossen.
Nog één ding
Je hebt misschien twee veelvoorkomende thema's opgemerkt toen we bespraken hoe je de zes grote verliezen kunt verminderen. Ze volgen en training . Dit zijn beide essentiële elementen van elk productieproces dat zijn zout waard is. Als uw organisatie geen van beide heeft, vindt u het misschien een uitdaging om OEE in te voeren.
Zorg ervoor dat uw organisatie de waarde van deze twee onderwerpen begrijpt en de middelen geeft die nodig zijn om ze goed te kunnen doen. Limble CMMS is gebruiksvriendelijk en houdt allerlei soorten gegevens bij. Het biedt ook sjablonen en checklists voor onderhoudspersoneel en onderhoudsoperators om uw trainingsprogramma's te ondersteunen.
OEE implementeren in uw organisatie
Het is altijd een goed idee om grote procesveranderingen te testen. Piloten helpen je problemen op te sporen en op te lossen voordat ze overal problemen veroorzaken. Ze helpen u ook te begrijpen hoe deze veranderingen uw organisatie zullen beïnvloeden. OEE is niet anders.
- Definieer de reikwijdte van uw pilot. Selecteer een productiegebied, apparaat of team dat graag wil verbeteren. Dit wordt je proefgroep.
- Bepaal het tijdsbestek voor de eerste gegevensverzameling. Definieer een tijdlijn voor gegevensverzameling, OEE-analyse en implementatie van verandering. Zoals we eerder hebben besproken, is het essentieel om voldoende gegevens - en de juiste gegevens - te verzamelen om een nauwkeurige OEE-score te ontwikkelen. Volg de definities van elke statistiek nauwkeurig.
- Analyseren en verbeteren. Zodra u over de benodigde gegevens beschikt, voert u uw OEE-berekeningen uit. Bepaal de scores die verbeterd kunnen worden. Bekijk de zes grote verliezen hierboven en kies er een of twee om aan te pakken.
- Analyseer opnieuw. Nadat u wijzigingen heeft aangebracht, gaat u verder met het verzamelen van gegevens. Beoordeel uw OEE opnieuw en kijk hoe deze is veranderd.
Als je pilot voorbij is, pas je zo nodig je proces aan op basis van wat je hebt geleerd. Pas het dan breed toe. Onthoud dat het verzamelen van gegevens constant is en dat CI nooit klaar is.
Om die reden moeten uw gegevensverzamelingsprocessen geautomatiseerd zijn of ingebouwd zijn in de dagelijkse functies. Binnenkort heeft u uw eerste organisatiebrede OEE-score!
Veelvoorkomende OEE-fouten en hoe ze te vermijden
Overall Equipment Effectiveness kan uw productieproces naar een hoger niveau tillen. Als het echter niet correct wordt gedaan, profiteert u mogelijk niet ten volle van de voordelen. Hier zijn enkele van de meest voorkomende fouten met OEE.
Focus op de OEE-score, niet op de verliezen
Houd in gedachten dat OEE een middel tot een doel is - niet het doel zelf. Het is een hulpmiddel dat u kunt gebruiken om uw voortgang te meten op een langer en zinvoller pad naar verbetering. Het is een tijdmeting en zal niet veranderen tenzij u zich richt op verbetering.
Net als uw bankrekeningsaldo, kunt u de hele dag naar dat aantal staren, en het wordt niet groter totdat u uw mouwen opstroopt, aan het werk gaat en een salaris verdient. OEE is een gemakkelijke manier om te meten waar u zich op een bepaald punt bevindt. Maar als u wilt verbeteren, moet de echte focus liggen op de verliezen en de stappen die u neemt om deze te minimaliseren.
OEE gebruiken om niet-gerelateerde processen en fabrieken te vergelijken
Van 0 naar 60 MPH gaan in 3 seconden in een Ferrari wordt verwacht - daar is hij voor gebouwd. Maar hetzelfde doen in uw Toyota Prius is ronduit onmogelijk. Het zijn verschillende machines met heel (heel) verschillende doeleinden. Door ze te vergelijken wordt de waarde van beide voertuigen geminimaliseerd.
Het is moeilijk niet om de vele OEE-scores binnen uw organisatie te vergelijken, maar doe dit met de nodige voorzichtigheid. U moet elk afzonderlijk proces in overweging nemen om te bepalen waarom ze mogelijk verschillende OEE-scores produceren - en waarom ze altijd - verschillende OEE-scores kunnen produceren.
Het is een vergissing om ongelijke productieprocessen te vergelijken, omdat het te veel belang hecht aan de OEE-score. En hebben we je daar in de vorige paragraaf niet voor gewaarschuwd? Onthoud dat wat je moet waarop u zich moet concentreren, zijn de verbeteringen die u aanbrengt om verliezen te minimaliseren.
Omschakelingen uitsluiten in uw OEE-berekening
Ja, omschakelingen kosten productietijd. Er is geen manier omheen. Maar het zijn ook essentiële onderdelen van uw bedrijf en rijpe gebieden voor verbetering.
Het is verleidelijk om ze uit je tijdmetingen te halen, omdat ze zo'n groot verschil maken. Maar dat minimaliseert niet alleen de nauwkeurigheid van uw score, maar het ontneemt u ook een van uw meest winstgevende mogelijkheden voor verbetering.
OEE implementeren in de hele fabriek
Wauw daar, Nelly. Het kan spannend zijn om een tool te hebben die uw productiviteit in één gemakkelijk te begrijpen getal samenbrengt. Als je het soort persoon bent dat er niet van houdt om iets half te doen, wil je het misschien graag overal gebruiken, direct buiten de poorten.
Onthoud dat het behoorlijk wat tijd en moeite kost om het correct te doen. Gebruik die middelen dus zorgvuldig. Door het programma te testen, kunt u gebieden vinden waar OEE het meest nuttig zal zijn en gebieden waar dit niet het geval zal zijn.
Uw gegevensverzameling is te traag
via GIPHY
Door het verzamelen van gegevens die maar door blijven gaan, loopt u het risico veranderingen in processen, personeel, seizoenen, enz. te overspannen. Al deze dingen kunnen uw gegevens in de war brengen en het moeilijk maken om te weten wat er precies moet worden verbeterd.
Verzamel data grondig en snel zodat je een score krijgt die echt aansluit bij jouw productieproces. Het gebruik van CMMS en andere op de cloud gebaseerde technologie helpt enorm omdat het proces voor het verzamelen van gegevens grotendeels kan worden geautomatiseerd.
OEE “op jouw manier” doen
OEE is het meest waardevol in vergelijking met vergelijkbare teams, productielijnen en zelfs vergelijkbare organisaties en industrieën. Maar wanneer u de regels verandert en OEE op uw manier berekent, verliest u het vermogen om uzelf met anderen te vergelijken. Bovendien verlies je het voordeel van het snel vinden en aanbrengen van verbeteringen.
You’re in the Major Leagues now
Excellent maintenance and manufacturing teams practice consistency, leverage the right tools, and use best practices for continuous improvement.
They also take every opportunity they can to reduce waste and use as few resources as possible. OEE is an excellent tool for this because it helps you:
- Collect valuable data on maintenance operations and production, helping you take a big-picture approach.
- Use proven assessments and analysis to peel back the layers and uncover ways to improve.
OEE is essential in your organization’s TPM (total productive maintenance strategy) and the first big step toward a lean manufacturing process. Once you implement it, we are confident that you will uncover and solve stubborn inefficiencies. You will also get better at directing, helping, and empowering all team members to work toward efficiency.
Limble is your partner in OEE and many other efficiency strategies. We offer an easy-to-use platform that enables each step in the OEE process. You can start a free 30-day trial here, request a demo, or even try out our online self-demo.
You now have the knowledge about OEE – and the tools – to make the most of your production process. Do not let this newly acquired power go to waste.
9 Comments
-
adnan akcora June 7, 2019, 9:59 am
Thanks for good information
What is diffrenece between OEE and mtbf also mttr .
Which ismuch more effective .
And how about Reliability ?
Thanks
Reply -
Abraham Milks December 10, 2019, 8:30 am
This web site is known as a stroll-by way of for the entire information you wanted about this and didn’t know who to ask. Glimpse right here, and you’ll undoubtedly uncover it.
Reply -
PHAM HUY KHA February 10, 2020, 10:30 pm
how we can to created a OEE ?
Reply -
Senko February 11, 2020, 1:38 am
I’m not 100% sure what you are asking, could you elaborate a bit?
Reply -
Aays August 18, 2020, 12:09 am
for performance section:
plant XYZ produces 3600 for 60 min
then the planned production time is 240 min
The total count should be (3600/60)*240 =14400 right?
How did you get 14100 ?I’ll try with my manufacturing and i get my performance as 100%. Can you help me?
Thank you.
Reply -
Senko August 18, 2020, 2:51 am
Hi,
In short, 3600 units in 60 min is in ideal conditions (what the machine manual would say the machine can do when it is brand new).
We randomly selected a lower number of the total actual produced units that represents a more realistic scenario where conditions are not ideal. In other words, in that example, we imagine that wear and tear or poor quality of the input material slows down the production a tiny bit so the total number of produced units is less than theoretically possible.
Maybe the text didn’t explain that point in the clearest way, I hope that this clears things up a bit.
Reply -
Aays August 19, 2020, 1:57 am
Okay, thank you for the explanation.
Reply
I want to ask one question. I want calculate OEE for my machines. So, how can I randomly chooses any number for the total count. The calculation for performance is 100%. Is it okay? As I don’t randomly choose lower number as you do. -
Senko August 21, 2020, 8:25 am
You definitely should not take a random number 🙂 If possible, you should measure the actual output and that will be your total count. Then you can see if that actual output was the same as maximally possible output you defined earlier.
Reply -
Sangeet September 25, 2020, 10:08 pm
You need to calculate the downtime of a machine first on a daily basis.
Reply
Downtime will include 4 losses of availability i.e. Shutdown loss, Production adjustment loss, equipment failure loss, and process failure loss.
Then deduct these loss timing from planned production time( the result will run time). Now calculate availability as (run time/planned prod. time).
Then calculate performance as {(ideal cycle time*total count)/run time}.
At last, calculate Quality as (good count/total count).
calculating OEE =Availability*Performance*quality
Onderhoud en reparatie van apparatuur
- De toekomst van onderhoud:een praktische gids voor Industrie 4.0
- Drew Troyer:algehele effectiviteit van apparatuur
- Nieuw boek is Primer on Overall Equipment Effectiveness
- Verbeter de effectiviteit van apparatuur door 11 grote verliezen aan te pakken
- Inzicht in onderhoudsstatistieken:algehele effectiviteit van apparatuur
- Een gids voor het maken van een onderhoudsprogramma voor apparatuur
- Huren versus kopen van productieapparatuur
- Gids voor het kopen van gebruikte compacte bouwmachines
- Een gids voor compacte apparatuurhulpstukken
- Beknopte handleiding voor het kopen van gebruikte bouwmachines
- Gids voor het huren van sleuvengravers en bekistingsmateriaal