casestudy over betrouwbaarheid van farmaceutische planten
Onderhouds- en betrouwbaarheidsprofessionals kunnen het verschil maken. In de meeste fabrieken betekent dat gericht werk waardoor operaties meer afgewerkt product (of het nu gaat om frisdranken, motorfietsen, gloeilampen, auto's, cupcakes, boilers, enz.) de deur uit kunnen krijgen.
In de biosynthetische humane insuline (BHI) fabriek van Eli Lilly in Indianapolis krijgt het maken van een verschil een extra betekenis.
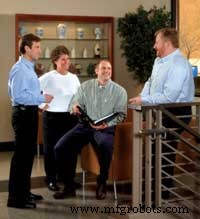
Bijna 21 miljoen mensen in Amerika – en 200 miljoen mensen wereldwijd – hebben diabetes. Alleen al in de VS worden elk jaar bijna 1 miljoen nieuwe gevallen gediagnosticeerd. Veel mensen met diabetes hebben insuline nodig om hun bloedsuikerspiegel (glucose) onder controle te houden, en de BHI-plant helpt in die behoefte te voorzien. De site werd in 1992 geopend voor productie en produceert een aanzienlijk percentage van 's werelds medicinale insuline. Onderhouds- en betrouwbaarheidswerk dat de productiviteit verhoogt, stelt het bedrijf in staat om hoogwaardige, levensondersteunende medicijnen in handen te krijgen van degenen die het nodig hebben.
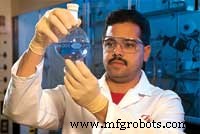
Of je nu werkt voor een bedrijf dat computerchips of chips maakt, als je waarde toevoegt aan de stakeholder of aan de economie, dat kan op geen enkele manier worden gekleineerd”, zegt Ken Swank, teamleider onderhoud en betrouwbaarheid van de fabriek. “Het maakt niet uit wat je doet. Het is belangrijk. Er is echter één duidelijk verschil. Ik werkte vroeger voor een industrieel coatingsbedrijf. Onze coatings gingen overal in, van golfballen tot de Space Shuttle tot chirurgische instrumenten. Toen ik het eindproduct zou zien, wist ik dat ik daar deel van uitmaakte. Maar als je voor een farmaceutisch bedrijf werkt. . . het betekent veel op persoonlijk vlak.
Ik heb in het weekend een stel ontmoet dat een jonge zoon heeft. We raakten aan de praat en ik kwam erachter dat de jongen diabetes heeft. Ik vroeg of hij Type 1 of Type 2 had. De vader vroeg, hoe weet jij zoveel over diabetes? De jongen vertelde me dat hij Type 1 was. Ik keek hem aan en zei:'Raad eens wat ik voor de kost doe? Ik maak insuline aan. Ik werk bij Eli Lilly en maak Humulin.’ Hij zei:‘Bedankt. Ik hou echt van mijn medicijn. Ik voel me er een stuk beter door.'
“Mijn afdeling is verantwoordelijk om ervoor te zorgen dat dit gebouw elke keer het medicijn maakt dat het moet maken. Er zijn miljoenen mensen die ervan afhankelijk zijn en er elke dag naar grijpen.”
De campus van Indianapolis bevat
productielocaties en kantoren.
Toenemende eisen
De BHI-fabriek is groot en technisch complex. Het herbergt meer dan 17.000 apparaten, 13.000 input/output punten en 600 operationele units. De verwerkingsmethode om het BHI-molecuul te genereren omvat verschillende centrifugatiestappen, een handvol reacties, veel zuiveringsstappen en verschillende stappen voor het uitwisselen van oplosmiddelen. Als gevolg hiervan wordt ongeveer een derde van de operationele eenheden geclassificeerd als een operatie met een hoog risico of een veiligheidskritieke operatie.
Een paar jaar geleden besloten leiders op het gebied van onderhoud en betrouwbaarheid dat het noodzakelijk was om substantiële veranderingen door te voeren om de tijd, vaardigheden, middelen en potentiële impact van de afdeling op de fabriek te maximaliseren. BHI draaide op meer dan twee keer zijn oorspronkelijke ontwerpcapaciteit en de zakelijke vraag bleef toenemen. Technici waren overcommitteerd, herstelwerkzaamheden kregen vaak een nieuwe prioriteit om aan de behoeften van het moment te voldoen en cruciale systemen kregen onvoldoende aandacht.
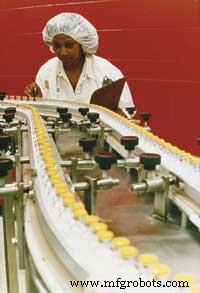
We hebben ons nooit zorgen gemaakt over het functioneren van onze apparatuur in een gekwalificeerde staat”, zegt Swank. “Maar net als de rest van de farmaceutische industrie in die tijd, legden we geen extra nadruk op onze apparatuur, behalve dat we altijd de meeste uptime wilden hebben om de meeste medicijnen te maken. Maar als je kijkt om zoveel mogelijk kilo's de deur uit te krijgen, kwamen we op het punt dat je je afvraagt:'Blijven we faciliteiten toevoegen of doen we het slim vanuit een zakelijk perspectief en richten we ons op betrouwbaarheid?'”
Het was iets waar een groot aantal Eli Lilly-faciliteiten eind jaren negentig over nadachten. BHI engineering manager Ron Reimer leidde bijvoorbeeld inspanningen om het proactieve werk en de uptime te verhogen en de onderhoudskosten te verlagen op de Clinton (Ind.) Laboratories-site van het bedrijf. Als onderdeel van dat project, dat vervolgens werd gesystematiseerd en Proactive Asset Management werd genoemd, huurde hij de eerste betrouwbaarheidsingenieur van het bedrijf in.
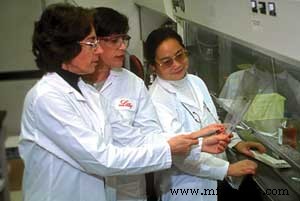
Directe betrokkenheid van alle belangrijke belanghebbenden bij de betrouwbaarheid van fabrieken
(productie, HSE, kwaliteitscontrole, financiën, engineering en
management) helpt het succes van het prioriteringsinitiatief voor betrouwbaarheid
te verzekeren.
De verbeteringsinspanningen van BHI begonnen met de toevoeging van een betrouwbaarheidsingenieur in 1999 en de introductie van Reliability-Centered Maintenance (RCM) en root cause failure analysis (RCFA)-projecten. Die inspanningen namen toe toen regelgevende instanties zoals de Food and Drug Administration en de Environmental Protection Agency het onderhoud in de farmaceutische industrie nauwkeurig begonnen te onderzoeken. De boodschap van de agentschappen was simpel:onderhoud staat gelijk aan betrouwbaarheid van de fabriek; fabrieksbetrouwbaarheid is gelijk aan productbetrouwbaarheid; en algehele betrouwbaarheid is gelijk aan naleving. "Onbetrouwbare" bedrijven kunnen boetes krijgen, waaronder het stopzetten van hun activiteiten.
Het belang van communicatie
Volgens Ken Swank, teamleider van het onderhouds- en betrouwbaarheidsteam, speelt communicatie een belangrijke rol in het succes van het initiatief voor het stellen van prioriteiten voor betrouwbaarheid van de BHI-fabriek.
"Communicatie is een van de belangrijkste onderdelen van mijn werk", zegt hij. “Ik ontmoet de productieleiders regelmatig en leg hun uit wat er in de pijplijn zit. Ik krijg hun betrokkenheid en help hen de waarde te begrijpen die het toevoegt. Ze moeten ook wat middelen verzamelen. Een goede analyse is natuurlijk niet alleen onze afdeling. Het gaat om engineering, onderhoud, betrouwbaarheid, operaties, technische diensten, soms automatisering. We besteden veel tijd om ervoor te zorgen dat ze de waarde begrijpen.
Ik moet behoorlijk wat dansen en zingen om ze te helpen begrijpen. Maar van alle accounts was de buy-in goed.”
"Toen denk ik dat betrouwbaarheid de focus begon te krijgen die het tegenwoordig heeft", zegt Swank. "Op onze reis om een echt betrouwbare fabriek te worden, is de visie dat wanneer de productie een stuk apparatuur, het is in een gekwalificeerde staat, het is beschikbaar wanneer ze het nodig hebben en het zal werken op het vooraf bepaalde prestatieniveau. Daar spelen we natuurlijk een grote rol in. De onderhoudsstrategieën die we hebben opgesteld, gaan over het in een goede staat houden van dat apparaat. gekwalificeerde staat. Ook is de diepte van de onderhoudsstrategieën gericht op het vereiste gebruik of de vereiste uptime. Er zijn activiteiten in de faciliteit die meer draaien dan andere, minder redundantie hebben dan andere of essentiëler zijn dan andere. Die vereisen meer aandacht en meer gedetailleerd onderzoek .”
Een prioriteringsinitiatief dat begin 2004 begon, stond centraal in deze strategie om uptime en betrouwbaarheid te leveren aan de operationele eenheden die de meeste aandacht verdienen.
Hoe Eli Lilly betrouwbaarheidsrollen definieert
Volgens Eli Lilly BHI onderhouds- en betrouwbaarheidsleiders omvatten de taken en verantwoordelijkheden van hun betrouwbaarheidsingenieurs:
- Minimaliseer apparatuurstoringen via RCFA's, FMEA's, RCM-analyse, onderzoeken naar leadafwijkingen, enz.
- Metrieken ontwikkelen om de inspanningen en middelen op het gebied van betrouwbaarheid te optimaliseren.
- Eigen onderhoudsplannen (bekijken/genereren/goedkeuren) voor nieuwe en bestaande apparatuur.
- Lever op betrouwbaarheid gerichte projecten die een stroombrede impact hebben.
- Focus zakelijke praktijken op onderhoud en betrouwbaarheid om de beschikbaarheid van apparatuur te vergroten.
- Mentor betrouwbaarheidstechnici.
- Integreer met controlekamerteams om hun bedrijf effectief te ondersteunen.
- Zoek en implementeer nieuwe technologieën om de prestaties en beschikbaarheid van apparatuur te verbeteren.
De functies en verantwoordelijkheden van betrouwbaarheidstechnici omvatten:
- Ondersteun site-initiatieven.
- Invullen en verwerken van CMMS-gegevensinvoerformulieren.
- Betrouwbaarheidsingenieurs helpen met RCFA's, datamining, FMEA's, RCM's, afwijkingen, wijzigingscontroles, veldverificatie, CMMS-gegevensverbeteringen, enz.
- Speciale projecten – ondersteuning van inspanningen op het gebied van betrouwbaarheid, enz.
Maak er een prioriteit van
Swank vertelt over de marsorders die uiteindelijk zouden leiden tot een betrouwbaarheidsremedie.
"Mijn baas zei destijds:'Bedenk hoe we de BHI-faciliteit betrouwbaarder gaan maken. We moeten hier grip op krijgen'", zegt Swank. "Wat hij eigenlijk bedoelde te zeggen was:'U en uw team moeten de zakelijke behoeften van de faciliteit begrijpen, een methode bepalen om een weg vooruit te vinden om de correct geprioriteerde betrouwbaarheidskloven te verhelpen, deze aan het bedrijf verkopen, uitvoeren en ervoor zorgen dat het is duurzaam.”
Klinkt makkelijk genoeg, of dat dacht hij tenminste.
"We begonnen in februari (2004) en gingen ervan uit dat we in maart of april klaar zouden zijn", zegt hij. “We realiseerden ons al snel dat dit ingewikkelder en complexer was dan we hadden verwacht. Bovendien wilden we het goed doen.”
Het plan zou zijn om een analyse te ontwikkelen die bestaande gegevens gebruikt om prioriteit te geven aan systeemherstel als een continue verbeteringsinspanning buiten de dagelijkse ondersteuningsinspanningen van de afdeling. De analysevereisten waren dat:
- het zou de geïdentificeerde systemen nemen en ze rangschikken op basis van zakelijke impact op basis van gegevens;
- alle belanghebbenden zouden vertegenwoordigd zijn;
- de analyse kan in minder dan één manweek (40 uur) worden uitgevoerd.
Deze uitdaging werd op de schouders van de afdeling betrouwbaarheidsengineering van de afdeling gelegd. De groep bestond uit senior betrouwbaarheidsingenieurs Mark Lafever, Vadim Redchanskiy en Rod Matasovsky (nu met pensioen), en betrouwbaarheidstechnici David Doyle, Mary Ann Dust en Matt O'Dell. Ze begonnen de inhoud van de analyse te strategiseren.
“Zij zijn de slimsten. Ik was de vertaler van het management naar de jongens op de vloer”, zegt Swank. "Ze begrepen de datasystemen en wat logisch was en wat niet."
De groep erkende dat om steun voor dit initiatief te krijgen, de analyse gebaseerd moet zijn op feiten en direct moet worden betrokken bij en zinvol moet zijn voor alle belangrijke belanghebbenden bij de betrouwbaarheid van fabrieken - productie; gezondheid, veiligheid en milieu (HSE); kwaliteitscontrole (QC); financiën; Engineering; en management. Dit zou een ongelooflijke evenwichtsoefening worden.
"Iedereen kan naar buiten gaan en een heleboel gegevens verzamelen", zegt Lafever. "We moesten beslissen waar we de gegevens vandaan moesten halen, hoe we ze wilden ophalen en uitzoeken of de gegevens ons de informatie zouden geven die we nodig hadden om de juiste beslissingen te nemen."
Tabel 1. Samenvatting van de gewichten voor de vijf scenario's.
Tabel 2. Voorbeeld uit de gevoeligheidsanalyse van het eerste scenario.
Na verschillende iteraties - en "veel hoofdschudden", zegt Lafever, kwam het team tot een analyse waarbij rekening werd gehouden met de belanghebbenden door gebruik te maken van bestaande gegevens van de afgelopen 12 maanden. Deze gegevens omvatten:
1) Uren noodwerk, gelijkgesteld aan uitvaltijd van apparatuur, om de productie te bevredigen. Dit werd verzameld uit het geautomatiseerde onderhoudsbeheersysteem van de fabriek, dat alle uren bijhoudt die aan elke bedrijfseenheid zijn afgeschreven. Noodwerk werd gedefinieerd als 'werk dat niet kan wachten'. Hoewel dit geen traditionele meting van systeemuitvaltijd is, houdt dit direct verband met de mate van verstoring van de productie die werd gevoeld toen het systeem niet goed functioneerde.
2) Risicoclassificatie, volgens Lilly's Globally Integrated Process Safety Management (GIPSM), om te voldoen aan HSE. Het classificatiesysteem kent vier mogelijkheden:veiligheidskritische werking, de hoogste risicofactor; hoog risico, dat een aanzienlijk milieu-, gezondheids- en brandrisico met zich meebrengt; mechanische integriteit, gedefinieerd door de Occupational Safety and Health Administration; en geen risico of "geen van bovenstaande."
3) Aantal afwijkingen van het proces veroorzaakt door apparatuurstoringen om te voldoen aan de QC. Dit was gericht op afwijkingen die het gevolg waren van problemen met de betrouwbaarheid van de apparatuur, niet van bedieningsfouten of andere problemen die niet met de apparatuur waren. Er werd rekening gehouden met het aantal afwijkingen en een niveau (1, 2 of 3) dat de impact van de afwijking op de productkwaliteit aantoonde.
4) Kosten van reactief werk om aan de financiering te voldoen. Dit werd opnieuw overgenomen uit het CMMS, dat alle budgettaire lasten tegen de operationele eenheden bijhoudt. Deze kosten omvatten alle onderdelen en arbeid die verband houden met reactief werk aan het systeem.
5) Input van procesingenieurs om engineering tevreden te stellen. De procesingenieur die verantwoordelijk is voor elk systeem, werd ondervraagd over onderwerpen als de leeftijd van het systeem, uren aan potentiële uitvaltijd als gevolg van systeemstoringen en de impact van regelgeving.
6) Staat van het onderhoudsplan van het systeem, ook om aan de engineering te voldoen. Dit is ontworpen om vier niveaus te omvatten:niveau 1, geen routine-onderhoud uitgevoerd, dat als het meest ernstig werd beschouwd; Niveau 2, er is preventief onderhoud aan het systeem; Niveau 3, periodieke kwalificatie-evaluaties (PQE's), ontworpen om ervoor te zorgen dat het systeem in een constante staat van kwalificatie en gebruiksgeschikt is, worden uitgevoerd; en, niveau 4, werd een RCM-gebaseerde analyse op het systeem gebruikt om een onderhoudsplan te genereren.
Deze gegevens leidden tot een evaluatie van "cruciale apparatuur", waarbij werd gekeken naar de 420 operationele eenheden en die werden geïdentificeerd met het potentieel om de productie te stoppen of een OSHA- of EPA-rapporteerbaar incident te veroorzaken.
"De manier waarop onze structuur is opgezet in ons CMMS en de manier waarop we onze incidentdatabase beheren, was de beste manier om te gaan", zegt Lafever. “Soms is een bedieningseenheid een stuk gereedschap. Meestal is het een belangrijk apparaat, en nog veel meer.”
Redchanskiy zegt bijvoorbeeld dat bedieningseenheid EV1411 (verdampingsproces) "50 tot 60 apparaten en instrumentatie omvat, zoals kleppen, warmtewisselaars en pompen."
De evaluatie bracht de aanvankelijke lijst met 70 procent terug, van 420 operationele eenheden naar 135.
De feiten liegen niet
Als het gaat om het bepalen van het belang van een bepaalde operationele eenheid, is het moeilijk om de feiten te betwisten.
"Voordat we deze analyse deden, was het enige waar de productie over sprak de centrifuge op de voorkant”, zegt Ken Swank, teamleider onderhoud en betrouwbaarheid van Eli Lilly. "Na de analyse en ze te laten zien wat we bedachten - ik wees erop dat centrifuge op de 63e plaats stond (op de lijst van 135 operationele eenheden) - vragen ze er niet veel naar.
“Hierdoor kijken we ook buiten de definitie van productieapparatuur. Vóór de analyse vergaten mensen om afvaltanks, luchtbehandelingssystemen, enz. Op te nemen. Ze dachten niet aan Tank 1099 in controlekamer 2, waar alle vloerafvoeren naartoe gaan. De spoeling gaat door de afvoeren en in de tank. Als die tank niet operationeel is, moeten we onze zuiveringsstappen stilleggen.”
Gewichten en maten
Om een juiste prioritering van de resterende 135 eenheden te garanderen, besloot de groep een weging toe te passen op elke gegevensbron en voerde ze een handvol gevoeligheidsanalyses uit.
"We hadden niet het gevoel dat de zes criteria even zwaar waren", zegt Swank. "We waren van mening dat veiligheid en kwaliteit een grotere impact hadden dan bijvoorbeeld de hoeveelheid geld die we uitgaven aan spoedeisend werk."
Een scoresysteem (nul tot 3, waarbij nul de minste impact en ernst is en 3 de meeste impact en ernst) werd ontwikkeld voor elke dataset en toegepast op elke operationele eenheid. De verdeling was als volgt:
Uren van noodwerk (HEW) :minder dan 15 uur (score van nul), 15 tot minder dan 25 uur (één), 25 tot minder dan 40 uur (twee) en 40 of meer uur (drie).
Risicoclassificatie (RC) :geen HSE-risico (nul), mechanisch integriteitssysteem (één), hoogrisicoproces (twee) en veiligheidskritieke werking (drie).
Afwijkingen (D) :Er zijn vier indelingen gemaakt door rekening te houden met de niveaus en aantallen afwijkingen. Er werd vastgesteld dat een afwijking van niveau 2 gelijk was aan driemaal een afwijking van niveau 1 en een afwijking van niveau 3 gelijk was aan tweemaal een afwijking van niveau 2. Dit maakte een afwijking van niveau 1 één punt waard, een afwijking van niveau 2 drie punten en een afwijking van niveau 3 zes punten. Dit werd toegepast op elke afwijking. Als resultaat waren de waarden:twee of minder (nul), groter dan twee tot en met vijf (één), groter dan vijf tot acht (twee) en groter dan acht (drie).
Kosten van reactief werk (CRW) :minder dan $ 5.000 (nul), $ 5.000 tot minder dan $ 7.499 (één), $ 7.500 tot $ 14.999 (twee) en $ 15.000 of meer (drie).
Invoer van procesingenieurs (PEI) :minimaal impactsysteem (nul) en oplopend tot maximaal impactsysteem (drie).
Status van systeemonderhoudsplan (SSMP) :RCM-analyse uitgevoerd op het systeem (nul), PQE uitgevoerd op routinebasis (één), PM's uitgevoerd (twee) en geen routinematig onderhoud uitgevoerd (drie).
De 135 bedrijfsonderdelen zijn gescoord. De informatie werd vervolgens in een spreadsheet geladen en er werden verschillende gewichten toegepast om het belang van verschillende datasets te benadrukken. Het project voor gevoeligheidsanalyse omvatte vijf verschillende wegingsscenario's om ervoor te zorgen dat een enkel gegevenspunt niet de prioritering van een systeem aanstuurde.
De scenario's varieerden van een redelijk gelijkmatige gewichtsverdeling (HEW, HSE, D en SSMP, elk 20 procent; CRW en PEI, elk 10 procent) tot de eliminatie van twee categorieën (HEW, HSE, D en CRW, elk 20 procent; PEI en SSMP, nul procent). In het laatste scenario waren de resterende datasets "echte gegevens" die veranderden volgens het betrouwbaarheidsniveau dat door het systeem werd aangetoond. De scenario's worden weergegeven in Tabel 1.
Elk scenario in de gevoeligheidsanalyse nam de risicofactor en vermenigvuldigde deze met de weging van dat specifieke scenario. Per bedrijfseenheid is het product van elke categorie opgeteld. Tabel 2 toont een voorbeeld uit het eerste scenario.
Toen alle vijf scenario's waren voltooid, werden de eindscores voor de operationele eenheden in een grafiek gezet en onderzocht door het betrouwbaarheidsteam. Alvorens de definitieve ranglijst en saneringsplannen vast te stellen, zijn aanvullende factoren in overweging genomen. Is de betreffende unit recentelijk vervangen of staat vervanging in het kapitaalplan? Kunnen saneringsplannen voor deze unit worden toegepast op andere units? Welke functionele groepen zijn nodig voor deze sanering en zijn deze beschikbaar? Welke herstelactiviteiten zijn er in het verleden uitgevoerd?
"Een van de centrifuges kwam bijvoorbeeld bovenaan de lijst te staan, maar we wisten dat een andere locatie een RCM deed op een vergelijkbaar systeem", zegt Swank. "We hoefden de inspanningen niet te herhalen."
De definitieve lijst met voorgestelde saneringsactiviteiten varieerde, afhankelijk van de operationele eenheid, van een diepgaande RCM-analyse tot het helemaal niet saneren van het systeem.
Op dat moment wist het team dat ze een uitgebreid plan hadden.
"Het was een sleur", zegt Lafever. "We kwamen drie keer met een plan - het voelde als 30 - en we bleven maar zeggen:'Dit is niet goed genoeg.' 'Hoe zou kwaliteitscontrole hierover denken?' 'Hoe zou procestechniek hierover denken?' waren erg perplex. We moesten ervoor zorgen dat we alle facetten en alle mogelijke vragen beantwoordden.”
Swank voegt eraan toe:"De eerste steek was zoiets van:'Wauw, dit komt niet eens in de buurt'. Het werd duidelijk waarom het nog niet eerder was gedaan. Het is veel werk. Er zijn ook dagelijkse dingen die je van zoiets weghouden. Maar we zeiden tegen onszelf dat we ons eraan zouden houden en het voor elkaar zouden krijgen.”
Schriftelijk
Op 21 september 2004 presenteerde Swank het prioriteringsmodel formeel aan het hoofdteam van de fabriek, dat bestaat uit het hoofd van de locatie en alle functionele managers. De vermoeiende zeven maanden werk wierpen hun vruchten af.
"Er was geen ruilhandel of discussie heen en weer", zegt hij. “Ze hadden zoiets van:‘Dit is geweldig. Ga verder.'”
Een hoofdknik en een handgebaar gaan natuurlijk maar zo ver. Dus liet Swank Lafever een rapport maken waarin het evaluatieproces werd samengevat en gedetailleerd hoe de cruciale apparatuuranalyse jaar na jaar zou worden uitgevoerd. Het rapport zou dienen als sjabloon voor toekomstige evaluaties.
"Ik heb de leidende teamleden gezegd het te ondertekenen", zegt Swank. “Dat deden ze. Ik heb het op schrift. Er was geen aarzeling. Dat laat zien dat de analyse die we hebben gedaan erg sterk was.”
Op 28 februari 2005 werd de cruciale apparatuuranalyse geformaliseerd en goedgekeurd door het leidende team, en de saneringsactiviteiten voor de meest vitale operationele eenheden van de fabriek werden opgenomen in de bedrijfsplannen voor 2005 en 2006 van de fabriek.
De sjabloon heeft latere evaluaties bijna naadloos gemaakt.
"Vorig jaar was het een koud kunstje om de analyse uit te voeren", zegt Lafever.
Het plan voor 2006 werd in mei afgerond.
Resultaten van remedie
Leidinggevenden van de onderhouds- en betrouwbaarheidsafdeling van deze fabriek van Eli Lilly zeggen dat ze momenteel niet in staat zijn om de totale impact van het initiatief voor prioriteitsstelling op het gebied van betrouwbaarheid te kwantificeren.
"Het ongelukkige is dat we niet altijd de resultaten van ons werk jaar na jaar zien", zegt Lafever. "Er kan een jaar vertraging optreden omdat het tijd kost om door het systeem te werken."
Maar dat betekent niet dat er geen voordelen en resultaten zijn geweest.
Redchanskiy en Doyle zeggen dat er onvermijdelijke kostenbesparingen zijn door alleen maar opnieuw te evalueren hoe het onderhoud aan een bepaald activum wordt uitgevoerd.
"In de analyse ontdekten we dat we een aanzienlijke hoeveelheid geld uitgaven aan een aantal systemen die geen reactief werk hadden", zegt Redchanskiy. “We hebben een ton uitgegeven aan preventief onderhoud. We overdreven het op PM's. We hebben de manier veranderd waarop we het onderhoud aan die systemen deden.”
"De grootste verschuiving hiervan is dat mensen voor sommige systemen nu kunnen zeggen dat het eigenlijk oké is om te falen", zegt Doyle. "Als dat onze diagnose en plan voor dat specifieke systeem is, is het goed. Dat is voor ons een heel andere filosofie.”
Swank zegt dat er positieve punten kunnen worden getrokken uit de productiviteitsniveaus van de fabriek.
"Het feit dat we onze voorraadniveaus hebben gehaald en het feit dat ons bedrijfsmodel op weg is naar een hogere productiviteit, toont aan dat we onze eerste grote mijlpaal al hebben bereikt", zegt hij.
Lafever is van mening dat betrokkenheid bij saneringsprojecten heeft geleid tot meer technische kennis en meer uptime.
"Als de meeste onderhouds- en operationele mensen uit een RCM-analyse komen, kunnen ze worden geclassificeerd als experts op dat systeem", zegt hij. “Iedereen heeft een beter begrip van de individuele functies van de groepen en hoe ze samenwerken om hun deel van het repareren van een apparaat uit te voeren of te identificeren wanneer er een probleem is met een apparaat. Die interactie zelf, denk ik, vermindert de hoeveelheid noodwerk die zich ontwikkelt.”
De beste indicator voor succes?
"Het maakt ons hogere management blij", zegt Doyle.
"En daar word ik blij van", zegt Swank.
Al deze verbeteringen zouden kunnen verklaren waarom BHI de Making Medicine Award 2005 ontving, die gaat naar de Eli Lilly-fabriek die "het beste voldoet aan de behoeften van het bedrijf en belichaamt hoe productie hoort te zijn bij het bedrijf."
Andere Lilly-fabrieken nemen kennis van het prioriteringsinitiatief en onderzoeken de haalbaarheid van adoptie. Dit heeft geleid tot een grotere zichtbaarheid in het hele bedrijf voor onderhoud en betrouwbaarheid.
"Een deel van het goede was het begrip van het bedrijf en het bewustzijn van de waarde die onderhoud toevoegt", zegt Reimer. "Het is iets waar we zeker van willen profiteren."
Dit team laat dagelijks zien dat professionals op het gebied van onderhoud en betrouwbaarheid het verschil kunnen en zullen maken.
Onderhoud en reparatie van apparatuur
- Casestudy:aandrijvingen en retrofits op papiersnij-opwinder
- Piston Plant neemt proactieve benadering van betrouwbaarheid en OEE
- Drew Troyer:hoe bedrijfsprocessen de betrouwbaarheid beïnvloeden
- Hoe fabrieksbetrouwbaarheid een lean-implementatie beïnvloedt
- Hydro-energiecentrale in Hawaï verhoogt efficiëntie en betrouwbaarheid
- Saoedi-elektriciteitsbedrijf om betrouwbaarheid energiecentrale te verbeteren
- Draadloos systeem om de betrouwbaarheid van de elektriciteitscentrale in Nevada te vergroten
- Beschikbaarheid verbeteren is veel meer dan onderhoud
- NV Energy installeert draadloze oplossing om fabrieksbetrouwbaarheid te vergroten
- Casestudy:Machine Down Crisis-oplossing
- CASE STUDY – REPARATIEOPLOSSINGEN VAN DE FABRIEK:KLEINE Charmilles-onderdelen veroorzaken GROTE problemen