Hoe volwassen zijn 3D-printtechnologieën voor metaal?

[Image credit:CCDC Army Research Laboratory]
Metaal 3D-printen omvat een breed scala aan technologieën, elk met zijn eigen voordelen en toepassingen — evenals zijn eigen mate van volwassenheid.
Bij het zoeken naar een specifieke metalen 3D-printtechnologie voor productie, is het cruciaal om te begrijpen waar de mogelijkheden en beperkingen momenteel liggen. Als het echter om metaal 3D-printen gaat, staan bedrijven voor de uitdaging om de realiteit van de hype te scheiden.
Om bedrijven te helpen de volwassenheid van de belangrijkste metaal-3D-printtechnologieën gemakkelijker te beoordelen, gaan we vandaag kijken hoe klaar ze zijn voor de productie van eindonderdelen, gebaseerd op een Technology Readiness Level (TRL)-systeem, voor het eerst ontwikkeld door NASA.
Wat is het Technology Readiness Level (TRL) precies?
Het 'Technology Readiness Level', voor het eerst ontwikkeld door NASA in de vroege jaren 1970, is een benadering die wordt gebruikt om te beoordelen of een opkomende technologie geschikt is voor verkenning van de ruimte. In de jaren negentig werden TRL's toegepast bij veel Amerikaanse overheidsinstanties en worden ze nu algemeen gebruikt in veel sectoren.
Het TRL-systeem meet de volwassenheid van een technologie van Niveau 1 (conceptevaluatie) tot en met niveau 9 (succesvolle implementatie) . Elk van de negen niveaus toont een mijlpaal in de ontwikkeling van de technologie.
Hoe kan de TRL worden gebruikt om de volwassenheid van metalen 3D-printtechnologieën te beoordelen?
We hebben deze aanpak toegepast om de volwassenheid van de verschillende 3D-printtechnologieën te beoordelen. Om een TRL voor elke metaal 3D-printtechnologie te identificeren, hebben we de evolutie ervan geanalyseerd, de industrieën die het gebruiken, hoe het vandaag wordt gebruikt en de ontwikkelingen die de toekomst bepalen.
Met name in sommige gevallen kan de TRL toepassingsspecifiek zijn. Zo zit de Direct Energy Deposition-technologie op een TRL 8 voor productietoepassingen, terwijl de toepassingen voor reparatie niveau 9 hebben bereikt.
Op basis van ons onderzoek zijn we van mening dat het merendeel van metaal 3D printtechnologieën hebben de TRL 7 overschreden, wat verwijst naar testen in een operationele omgeving om prestatieproblemen aan te pakken, en toepassingen in functionele prototyping en tooling.
Sommige zijn ook succesvol gebleken onder normale bedrijfsomstandigheden (TRL 8) en zijn op weg naar integratie in het bredere productie-ecosysteem (TRL 9).
Laser poederbed Fusion

Technologiegereedheidsniveau:8
Laser Powder Bed Fusion (PBF) is een van de meest gevestigde 3D-printtechnologieën voor metaal. Het metalen PBF-proces omvat het selectief aanbrengen van een krachtige, nauwkeurig afgestemde laser op een laag metaalpoeder. Op deze manier worden metaaldeeltjes laag voor laag met elkaar versmolten tot een onderdeel.
De oorsprong van metaal PBF gaat terug tot 1995, toen het Fraunhofer Instituut in Aken, Duitsland, het eerste patent indiende voor het lasersmelten van metalen. Sindsdien zijn veel bedrijven, waaronder gevestigde spelers zoals EOS, Concept Laser (overgenomen door GE) en SLM Solutions, de PBF-markt betreden met hun kijk op de technologie.
In het afgelopen decennium hebben fabrikanten van metalen PBF 3D-printers hard gewerkt aan het optimaliseren van de technologie voor productie. Daarom hebben we belangrijke marktspelers oplossingen zien lanceren voor geautomatiseerde en geïntegreerde productie.
De meeste van deze oplossingen hebben vergelijkbare kenmerken:ze zijn modulair, configureerbaar en bieden een hoge mate van automatisering om de efficiëntie te maximaliseren en de hoeveelheid handmatige arbeid te verminderen.
Tegelijkertijd wordt de materiaalkeuze voor PBF voortdurend uitgebreid. Zo introduceerde EOS vorige maand vier nieuwe metaalpoeders voor zijn metalen 3D-printers. Onder hen zijn RVS CX, Aluminium AlF357, Titanium Ti64 Grade 5 en Titanium Ti64 Grade 23.
Dankzij deze ontwikkelingen heeft laser PBF zijn weg gevonden naar vele industrieën en toepassingen. Een sector die bijzonder enthousiast is geweest over het gebruik van metalen PBF, is de ruimtevaart.
Tegenwoordig drijven 3D-geprinte metalen PBF-onderdelen cruciale vliegtuig- en ruimtevaartuigsystemen zoals motoren aan. Dit is waar de belangrijkste mogelijkheden van de technologie - de productie van complexe onderdelen met vereenvoudigde montage en minder materiaalverspilling - echt uitblinken.
Vanaf nu is laser PBF-technologie in staat om herhaaldelijk functionele onderdelen te leveren. Het vereist echter nog wat fine-tuning en testen voordat fabrikanten zich kunnen committeren aan volledige productie. Daarom stellen we voor dat het zich momenteel op technologiegereedheidsniveau 8 bevindt.
In de toekomst zullen het gebruiksgemak en de betrouwbaarheid van metalen PBF-systemen toenemen, in veel opzichten gedreven door de vooruitgang in software en in het algemeen werkstroom.
Een voorbeeld dat deze trend ondersteunt, komt van de in Californië gevestigde fabrikant van metalen 3D-printers, VELO3D.
Bij de ontwikkeling van zijn laser PBF-technologie, Intelligent Fusion genaamd, heeft het bedrijf de nadruk gelegd op software- en hardware-integratie. Het resultaat is een strak geïntegreerd systeem dat onderdelen kan printen met minder ondersteuningen, een betere oppervlakteafwerking en naar verluidt een hoger slagingspercentage. Dit leidt weer tot een grotere betrouwbaarheid, snellere productie en minder nabewerking.
Laser PBF blijft de drijvende kracht achter de metaal 3D-printindustrie. Metal PBF 3D-printers hebben de grootste installed base onder andere metalen 3D-printtechnologieën. En fabrikanten van PBF 3D-printers hebben de grootste aandelen op de markt voor metalen 3D-printen in vergelijking met bedrijven die andere soorten metalen 3D-printers produceren.
Daarom worden eerst een aantal materialen ontwikkeld voor metaal PBF-technologieën. Dit betekent dat de evolutie van deze technologie zal doorgaan, gedreven door de vraag naar hoogwaardige, complexe metalen 3D-geprinte onderdelen.
Elektronenstraal smelten
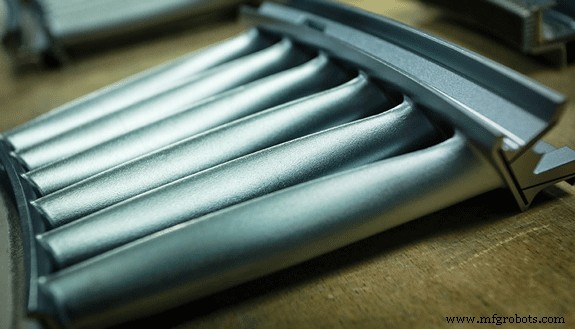
Technologiegereedheidsniveau:8
Electron Beam Melting behoort, net als laser PBF, tot de poederbedfusiefamilie van 3D-printtechnologieën. EBM werkt op dezelfde manier als laser PBF doordat de metaalpoeders ook worden gesmolten om een volledig dicht metalen onderdeel te creëren.
Het belangrijkste verschil tussen de twee technologieën is de energiebron:in plaats van een laser gebruiken EBM-systemen een krachtige elektronenstraal als warmtebron om lagen metaalpoeder te smelten.
Sinds het patenteren van de technologie in 2000, is het Zweedse bedrijf Arcam de belangrijkste fabrikant van EBM 3D-printers gebleven.
Na de overname van het bedrijf door GE in 2016 bleef de EBM-technologie evolueren. In 2018 bracht Arcam zijn volgende generatie EBM-machines op de markt, de Spectra H.
De 'H' staat voor 'heet metaal', wat betekent dat het hitte- en scheurgevoelige materialen zoals titaniumaluminide kan verwerken (TiAl) bij temperaturen tot 1000°C.
Arcam EBM Spectra H heeft een aantal nieuwe functies die gericht zijn op het verhogen van de productiviteit en het verlagen van de totale kosten.
De EBM Spectra H is bijvoorbeeld uitgerust met een 6kW HV-vermogen unit, die helpt om voor- en naverwarmingsstappen met 50% te verminderen in vergelijking met andere EBM-machines die momenteel op de markt zijn.
Bovendien is het gelaagdheidsproces verbeterd om hoge temperaturen te verminderen. Hierdoor kunnen fabrikanten tot vijf uur besparen op een volledige bouwhoogte en de printsnelheden tot 50% verhogen in vergelijking met andere EBM-machines.
GE Aviation-bedrijf, Avio Aero, gebruikt naar verluidt 35 Arcam machines:31 Arcam A2X-machines en 4 Arcam EBM Spectra H-machines. Bij Avio Aero worden de 3D-printers gebruikt om TiAl-bladen te produceren voor lagedrukturbines van de nieuwe grote GE9X-motor.
Naast de lucht- en ruimtevaart maakt de medische industrie op grote schaal gebruik van de technologie om medische implantaten te produceren . Het eerste gebruik van EBM voor deze toepassing dateert van 2007.
Gesteund door GE's middelen en expertise in metaal AM, is EBM-technologie op weg naar industrialisatie. De technologie wordt toegepast in productieomgevingen binnen sterk gereguleerde industrieën zoals de lucht- en ruimtevaart en de medische sector. Gezien deze aanvragen heeft EBM de TRL 8 bereikt.
Directe energieafzetting
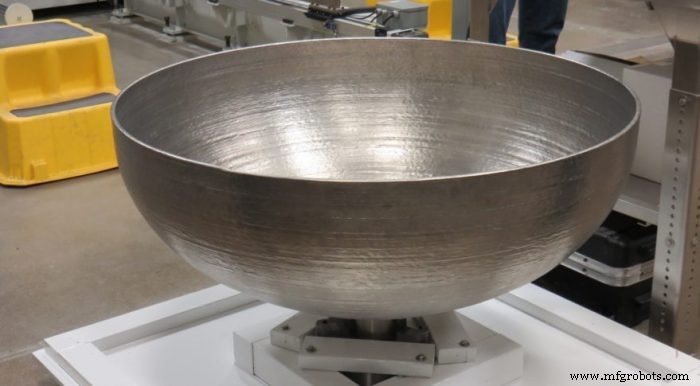
Technologiegereedheidsniveau:8
Afkomstig uit lasprocessen, houdt Direct Energy Deposition (DED) in dat metaal wordt gesmolten met een laser of een elektronenstraal terwijl het materiaal door een mondstuk op een bouwplatform wordt geduwd.
DED-systemen gebruiken draad of poeder als grondstof. De meeste systemen gebruiken in de handel verkrijgbare materialen die zijn ontwikkeld voor lassen of poedermetallurgie. Het gebruik van kant-en-klare materialen heeft veel voordelen, waaronder een bredere materiaalkeuze, hogere kwaliteit en lagere prijs.
Een van de eerste en meest succesvolle toepassingen van DED was de reparatie van beschadigde componenten. De technologie wordt gebruikt om materiaal toe te voegen aan de beschadigde onderdelen zoals turbinebladen en inzetstukken van spuitgietmatrijs. Door versleten onderdelen te repareren, helpt DED de uitvaltijd en de kosten die gepaard gaan met het vervangen van een onderdeel te verminderen, terwijl ook de levensduur van het onderdeel wordt verlengd.
Om het gebruik van DED beyond repair-toepassingen mogelijk te maken, hebben fabrikanten van DED-systemen oplossingen ontwikkeld en geoptimaliseerd voor de productie van functionele metalen onderdelen.
Sciaky, een van de pioniers van DED-technologie, heeft bijvoorbeeld closed-loop besturing geïntroduceerd in zijn Electron Beam Additive Manufacturing-systemen. Het procesbewakingssysteem van Sciaky combineert realtime optische beeldvorming met machinevisie om de grootte, vorm en temperatuur van de smeltbad te meten.
Op basis van de gegevens die uit het beeld zijn verkregen, wordt vervolgens een geeft instelcommando's aan de software die het straalvermogen, de draadaanvoersnelheid en de beweging van de machine regelen. Hierdoor kan de herhaalbaarheid van het proces aanzienlijk worden verbeterd.
DED-technologie is al toegepast in meerdere ruimtevaart- en defensietoepassingen. Voorbeelden zijn titanium brandstoftankkoepels voor satellieten, structurele titanium onderdelen voor de Boeing 787 Dreamliner en vervangende onderdelen voor militaire voertuigen.
De technologie heeft zichzelf bewezen als een gemakkelijk beschikbare onderhoudsoplossing. Met deze applicatie staat DED op TRL 9.
Als het gaat om productietoepassingen, kan DED ook worden gebruikt als productietool. Er zijn echter meer ontwikkelingen nodig om de procescontrole te verbeteren en de afdrukresolutie te verbeteren.
Vanaf nu produceert de technologie bijna-netvormen, die substantiële bewerkingen nodig hebben om onderdeelspecificatie en een goede oppervlakteafwerking te bereiken. Door de afdrukresolutie te verbeteren, kunnen fabrikanten de tijd en kosten die nodig zijn voor secundaire bewerkingen verminderen.
Metalen bindmiddel spuiten
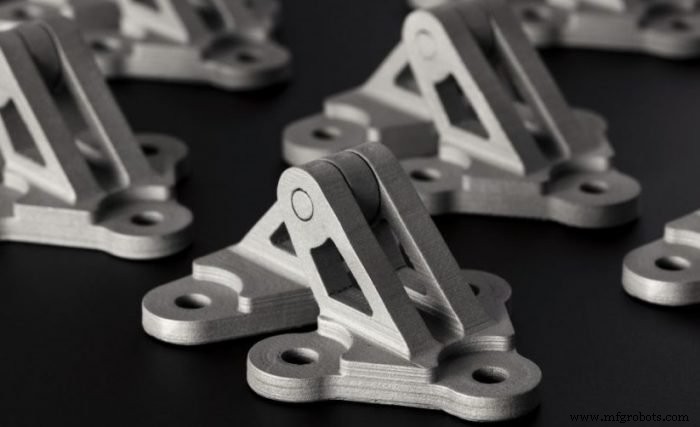
Technologiegereedheidsniveau:varieert
Metal Binder Jetting evolueert snel naar een veelbelovende productietechnologie. Het technologiegereedheidsniveau varieert echter sterk tussen metaalbinderstraaltechnologieën die momenteel op de markt zijn.
Metal binder jetting werd voor het eerst ontwikkeld in 1993 aan het MIT. Het printproces begint met het verspreiden van een dunne laag poeder, waarbij printkoppen strategisch druppeltjes bindmiddel in het poederbed afzetten. Het proces herhaalt zich laag voor laag totdat het onderdeel compleet is, waarbij ongebruikt poeder (ongeveer 95%) wordt gerecycled.
ExOne, dat sinds 1996 de technologie van MIT in licentie geeft, bleef het enige bedrijf dat metaal aanbood binder jetting diensten en systemen tot het begin van 2010s. ExOne's spuitsystemen voor metalen bindmiddelen werden grotendeels gebruikt om metalen prototypes en gereedschappen te maken.
Toen de patenten voor het stralen van metaalbindmiddelen echter afliepen, laaide de concurrentie op, wat het bedrijf aanmoedigde om te beginnen met de ontwikkeling van oplossingen op productieniveau. De nieuwste, X1 25PRO 3D-printer, werd een paar maanden geleden commercieel gelanceerd.
Een andere grote speler op de markt voor het stralen van metalen bindmiddelen is Digital Metal. De DM P2500 3D-printers, voor het eerst geïntroduceerd in 2017, hebben naar verluidt meer dan 300.000 componenten geproduceerd in verschillende industrieën, waaronder ruimtevaart, luxegoederen, tandheelkundig gereedschap en industriële apparatuur.
Er zijn ook een paar nieuwkomers op het gebied van metal binder jetting, waaronder HP en Desktop Metal.
Na de onthulling van zijn Multi Jet Fusion-technologie voor polymeeronderdelen in 2016, introduceerde HP in 2018 de volgende uitbreiding van zijn additievenaanbod:een Metal Jet 3D-printsysteem. Met een nieuw systeem wil HP de technologie in een productieomgeving met grote volumes plaatsen.
Om dit te bereiken heeft het bedrijf zijn systeem uitgerust met meer nozzles en innovatief bindmiddel geïntroduceerd. Gecombineerd wordt gemeld dat deze verbeteringen het afdrukproces sneller en eenvoudiger maken.
De technologie achter de 3D-printer van Desktop Metal is wat het bedrijf Single Pass Jetting (SPJ) noemt, een snellere versie van het typische binder jetting-proces. Het bedrijf beweert dat zijn systeem tot 12.000 cm3/uur kan printen, wat zich vertaalt in meer dan 60 kg metalen onderdelen per uur.
Interessant is dat HP's Metal Jet en Desktop Metal's productiesysteem een enigszins vergelijkbare waarde delen voorstel. Beide op binder jetting gebaseerde machines lijken de traditionele productie te verstoren door een grotere snelheid en schaalbaarheid mogelijk te maken.
Terwijl het productiesysteem van Desktop Metal eerder dit jaar werd uitgebracht, staat de technologie van HP gepland voor een release in 2020 en is deze momenteel alleen beschikbaar via HP Metal Jet Production Service.
Toegegeven, veel van de metaalbindmiddelstraaltechnologieën zijn pas recentelijk verschenen. Het betekent dat ze enige tijd nodig hebben om te bewijzen dat ze klaar zijn voor serieproductietoepassingen door middel van verdere tests, zowel intern als bij de klant.
Met een staat van dienst in productietoepassingen, bevinden de oudere technologieën, zoals die van Digital Metal en ExOne, zich tussen technologiegereedheidsniveaus 7 en 8. We verwachten dat meer recente metaalbinderstraaltechnologieën de TRL zullen bereiken en overschrijden. 8 in de komende jaren.
Metalen binder jetting-systemen zullen blijven evolueren om de markten aan te pakken die een uitdaging vormen voor andere metaal 3D-printtechnologieën om door te dringen, waaronder de productie van grotere hoeveelheden auto's en industriële goederen. Dit creëert in de toekomst veel opwindende groeimogelijkheden voor deze technologie.
Gebonden metaalafzetting
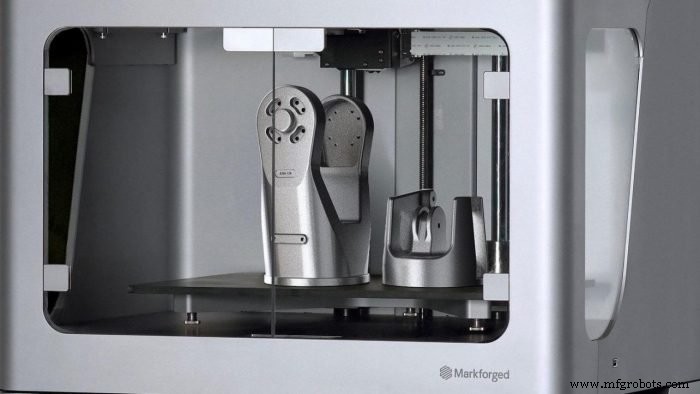
Technologiegereedheidsniveau:7
Bound Metal Deposition is een opwindende nieuwkomer op het gebied van metaaladditieve productie. De technologie werkt op dezelfde manier als Fused Filament Fabrication (FFF), waarbij een filament wordt verwarmd en geëxtrudeerd door een mondstuk, waardoor een onderdeel laag voor laag ontstaat. In tegenstelling tot de plastic filamenten die worden gebruikt in FDM, gebruikt metaalextrusie echter filamenten gemaakt van metaalpoeders of -pellets die zijn omhuld met plastic bindmiddelen.
De twee meest vooraanstaande bedrijven die op dit gebied actief zijn, zijn Markforged en Desktop Metal. Beide bedrijven onthulden voor het eerst hun metalen 3D-printsystemen (Markforged's Metal X en Desktop Metal's Studio System) in 2017.
Momenteel wordt de technologie grotendeels gebruikt om sneller en goedkoper metalen prototypes en gereedschappen te maken.
Een voorbeeld is Dixon Valve &Coupling Company, een fabrikant en leverancier van accessoires voor de vloeistofoverdrachtindustrie. Het bedrijf heeft Markforged's Metal X gebruikt om grijperbekken in 3D te printen. Deze gereedschappen zijn in wezen klemmen, die zijn gemonteerd op een robotarm die afdichtringen aan de stalen koppelingen toevoegt.
De productie van dergelijke gereedschappen duurt 14 dagen en kost $ 355. Ter vergelijking:het 3D-printen van een metalen grijper kost $ 7 en heeft 1,25 dagen nodig om te voltooien - een reductie van meer dan 90% voor zowel de kosten als de doorlooptijd.
Terwijl de gebonden depositietechnologie grote vooruitgang boekt in kosten- effectieve prototyping en het versnellen van de time-to-market, blijft het gebruik aan de productiekant beperkt. Ten eerste worden dergelijke systemen gepositioneerd als compacte metalen 3D-printers, die moeilijk schaalbaar kunnen zijn.
Naarmate echter meer bedrijven de technologie toepassen, vooral voor afgelegen locaties zoals olieplatforms, kunnen we meer voorbeelden zien van reserve- en eindgebruiksonderdelen die in de komende jaren zijn gemaakt met behulp van gebonden metaalafzetting.
Innoveren met 3D-printen van metaal
De meeste metaal 3D-printtechnologieën hebben een vrij hoog technologische gereedheidsniveau bereikt, wat betekent dat ze geschikt zijn voor productietoepassingen.
Het is duidelijk dat er nog veel werk moet worden verzet, met name aan het verbeteren van de rendabiliteit en snelheid van 3D-printtechnologieën voor metaal. Momenteel zijn poederbedprocessen, DED en metaalbindmiddelstralen aanzienlijk duurder dan conventionele productiesystemen.
Lagere-kosten gebonden poederdepositiesystemen maken het 3D-printen van metaal enigszins toegankelijk en kunnen een goed instappunt zijn voor kleinere bedrijven.
Uiteindelijk is het bevorderen van de technologie zelf slechts een stukje van de puzzel. Het is net zo cruciaal voor het ecosysteem rond 3D-metaalprinten om te blijven evolueren. Dit kan de ontwikkeling van beter geïntegreerde en gebruiksvriendelijkere softwareoplossingen, automatisering van nabewerkingen en het creëren van gestroomlijnde workflows inhouden.
Alleen door alle stukjes bij elkaar te brengen, is er een manier om significante proces- en productinnovatie te bereiken met 3D-metaalprinten.
3d printen
- Hoe objectmodellen worden ontworpen voor 3D-printen
- Hoe bruggen worden gebruikt bij 3D-printen
- Hoe kan 3D-printen het metaalgieten ten goede komen? Hier zijn 3 manieren
- Metaal 3D-printen:waar zijn we vandaag?
- Hoe volwassen is uw branche in de adoptie van 3D-printen? [Infographic]
- 10 spannende 3D-printtechnologieën die de afgelopen 12 maanden zijn ontstaan
- Hoe desktop 3D-printers 3D-printen transformeren
- AM Around the World:hoe volwassen is 3D-printen in de regio Azië-Pacific?
- Hoe de hardwaremarkt voor 3D-printen evolueert in 2020
- Hoe duurzaam is industrieel 3D-printen?
- Inzicht in 3D-printtechnologieën