Metaal 3D-printen:waar zijn we vandaag?
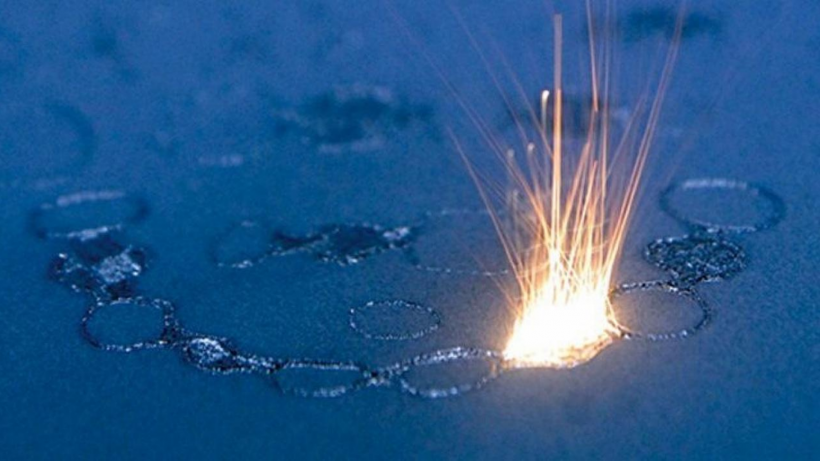
Slechts tien jaar geleden geloofden maar weinigen dat 3D-printen van metaal ooit een serieuze concurrent zou kunnen zijn voor serieproductie. De technologie heeft echter een snelle evolutie doorgemaakt, vooral de laatste jaren. Nu metalen onderdelen worden gebruikt in toepassingen die zo verstrekkend zijn als de medische sector, de auto-industrie en de ruimtevaart, maakt de technologie zich op voor productie.
Maar waar staan we nu?
Terwijl de markt voor 3D-printen voor metaal blijft groeien, is het belangrijk om gelijke tred te houden met het steeds veranderende landschap. Daarom kijken we vandaag naar de evolutie van 3D-printen met metaal:hoe ver de technologie is gekomen, waar de zaken momenteel liggen en wat de toekomst in petto heeft voor deze innovatieve technologie.
Belangrijke gebeurtenissen die metalen 3D-printen hebben gevormd
Sinds de jaren tachtig is het technologische en marktlandschap aanzienlijk geëvolueerd voor 3D-metaalprinten. Terwijl de groei van de technologie in het begin van de jaren 2000 stapsgewijs was, is het landschap de afgelopen vijf jaar veranderd, met een aantal nieuwe spelers die de markt betreden.
Metal AM-systemen zijn zo geëvolueerd dat ze nu in staat zijn meer materialen te verwerken en een breder scala aan toepassingen mogelijk te maken.
Een kort overzicht van enkele van de belangrijkste gebeurtenissen om de evolutie van de technologie vorm te geven:
- jaren '80 :Dr. Carl Deckard (Universiteit van Texas) patenteert een selectieve lasersintertechnologie voor kunststoffen. Deze uitvinding maakt de weg vrij voor 3D-printen van metaal.
- 1988 :Dr. Ely Sachs (MIT) ontwikkelt een nieuw binder jetting-proces dat de basis zou worden van metal binder jetting. Metal Binder Jetting zou vervolgens in 1996 in licentie worden gegeven aan ExOne.
- 1994 :EOS onthult zijn prototype EOSINT M160-machine, gebaseerd op metaallaser-sintertechnologie. Het jaar daarop lanceert het bedrijf de EOSINT M250-machine, die als eerste metaallaser-sintertechnologie gebruikt.
- 1995 :Het Fraunhofer Instituut in Aken, Duitsland, dient het eerste patent in voor het lasersmelten van metalen.
- 1998 :Optomec commercialiseert zijn Laser-Engineered Net Shaping (LENS) metaalpoedersysteem, een van de Direct Energy Deposition-technologieën.
- 2000 :Electron Beam Melting (EBM) technologie is gepatenteerd en in licentie gegeven door Arcam AB.
- 2002 :Arkham lanceert de eerste EBM-machine, de S12.
- 2004-2005 :EOS stapt over van de CO2-laser die wordt gebruikt in kunststof SLS naar een fiberlaser die meer geschikt is voor het smelten van metalen.
- 2017:de in de VS gevestigde startup, Digital Alloys, kondigt zijn gepatenteerde Joule-methode voor 3D-metaalprinten aan en sluit het volgende jaar een Series B-financiering van $ 12,9 miljoen af.
- 2018:na het succes met zijn Multi Jet Fusion-systeem voor polymeren, gooit HP zijn hoed in de metalen 3D-printring met het debuut van zijn Metal Jet 3D-printsysteem voor metalen. In hetzelfde jaar verscheen hetWohler's Report kondigt een groei van 80% aan in metalen AM-systemen voor 2017.
- 2019:Desktop Metal, dat zijn productie-, winkel- en studiometaal AM-systemen aanbiedt, sluit $ 160 miljoen af in een Series E-investeringsronde.
De evolutie van metalen AM-systemen
DMLS — het startpunt
De oorsprong van direct 3D-printen van metaal gaat terug tot 1994, toen EOS voor het eerst zijn EOSINT M250-machine introduceerde. Deze machine was gebaseerd op directe metaallaser-sintertechnologie (DMLS).
In die tijd werkte het DMLS-sinterproces op dezelfde manier als Selective Laser Sintering voor kunststoffen, in die zin dat metaalpoeder gedeeltelijk werd gesmolten en samengesmolten om metalen onderdelen te maken.
Sinteren is echter niet de meest efficiënte manier om volledig dichte metalen onderdelen te vormen.
Tussen 2004 en 2005 introduceerde EOS krachtigere fiberlasers in zijn machines — en dit veranderde het spel aanzienlijk.
Nu, hoewel de term DMLS de erfenis van sinteren behoudt, moderne DMLS-machines kunnen metaalpoeders volledig smelten en leveren onderdelen met een dichtheid van meer dan 99%.
Vanaf 2019 blijven DMLS en EBM de twee meest gebruikte productieprocessen voor metaaladditieven.
Nieuwe machines
Dankzij voortdurende technologische verbeteringen en toegenomen concurrentie op de markt voor metaal 3D-printen, worden metalen AM-systemen steeds meer geoptimaliseerd voor productie.
De afgelopen jaren waren bijzonder spannend, omdat er nieuwe productieconcepten voor 3D-metaalprinten zijn ontstaan.
Sleutelspelers zoals EOS, Concept Laser en 3D Systems hebben allemaal onlangs oplossingen gelanceerd die hun respectievelijke visie op 3D-metaalprinten als onderdeel van een slimme fabriek weerspiegelen.
De meeste van deze oplossingen hebben vergelijkbare kenmerken:ze zijn modulair, configureerbaar en bieden een hoge mate van automatisering om de efficiëntie te maximaliseren en de hoeveelheid handmatige arbeid te verminderen.
Nu de industrie steeds meer automatiseert en flexibeler is, kunnen deze modulaire platforms fabrikanten een middel bieden om de technologie gemakkelijker in hun productieprocessen te integreren en sneller op te schalen.
Nieuwe spelers
De markt voor metaal 3D-printen is een groeiend activiteitsgebied, met meer dan 20 bedrijven die metalen AM-systemen produceren. Het aantal nieuwe spelers dat de markt betreedt, groeit voortdurend, omdat bedrijven het voortouw willen nemen in de richting van serieproductie.
Digitale legeringen en Joule Printing
Een voorbeeld is Digital Alloys, dat zijn eigen Joule-printtechnologie heeft ontwikkeld om de problemen van snelheid en kosten aan te pakken.
Joule-printen maakt gebruik van metaal in draadvorm, dat doorgaans goedkoper is dan metaalpoeders. Het hogesnelheidsproces wordt bestuurd via een gesloten-lussysteem, waarbij de metaaldraad in een nauwkeurig bewegingssysteem wordt gevoerd.
De technologie, die in 2020 commercieel op de markt komt, belooft een grotere procesbetrouwbaarheid, hogere snelheden en lage grondstofkosten. Deze factoren gecombineerd kunnen helpen om de totale productiekosten aanzienlijk te verlagen.
HP's Metal Jet
HP betrad voor het eerst de 3D-printscene met zijn Multi Jet Fusion-technologie, die wordt gebruikt voor kunststoffen. In 2018 deed het bedrijf zijn eerste inval in de metalen 3D-printarena met zijn Metal Jet-systeem.
Het systeem is gebaseerd op HP's binder jetting-technologie, waarbij gebruik wordt gemaakt van kant-en-klare metaalspuitgietpoeders (MIM) om de kosten te drukken. Het systeem, dat ook gepland staat voor een release in 2020, zou 50 keer sneller zijn dan vergelijkbare systemen voor het stralen van bindmiddelen of selectieve lasersmeltsystemen.
Desktop Metaal
Opgericht in 2015, werd het in de VS gevestigde bedrijf mede opgericht door Ely Sachs, de uitvinder van het binder jetting-proces.
Met als doel om 3D-printen van metaal te maken als toegankelijk mogelijk te maken, biedt Desktop Metal zijn Studio System, gericht op kleine oplagen, en zijn Production System, gericht op grootschalig 3D-printen. Meer recent introduceerde het bedrijf ook een Shop-systeem, ontworpen voor machinewerkplaatsen.
Desktop Metal is nu een van een handvol 3D-printstartups die de status van eenhoorn hebben bereikt, met een waarde van ongeveer $ 1,2 miljard.
De vlaag van activiteit binnen de metalen 3D-printruimte is nog een ander positief teken van de technologie die vooruitgaat in de richting van de droom van seriële AM-productie.
Directe energiedepositie (DED)
Een andere technologie die voor spannende ontwikkelingen zorgt in de wereld van 3D-metaalprinten, is Direct Energy Deposition (DED).
De DED-technologie is ontstaan uit lasprocessen en gebruikt een laserstraal om metaalpoeders of draad terwijl ze door een mondstuk op een bouwplatform worden geduwd. In tegenstelling tot binder jetting en poederbedprocessen, is deze technologie vooral geschikt voor het maken van grotere componenten.
Historisch gezien werd DED gebruikt om componenten te repareren door functies aan een bestaand onderdeel toe te voegen. Nu is het breder voor productie in industrieën variërend van ruimtevaart en defensie tot olie en gas.
Het Noorse bedrijf Norsk Titanium, bijvoorbeeld, gebruikt zijn eigen DED-technologie (Rapid Plasma Deposition) om FAA-goedgekeurde titanium vliegtuigonderdelen te produceren voor de Boeing 787 Dreamliner.
Een hybride aanpak
Een belangrijke ontwikkeling die wordt aangedreven door DED-technologie is hybride productie.
In dit type fabricageproces kan DED worden gecombineerd met een subtractief proces zoals frezen, om onderdelen binnen één systeem te vervaardigen en af te werken.
Voor veel industrieën kan deze aanpak het productieproces aanzienlijk stroomlijnen. Het voordeel is duidelijk:in plaats van een onderdeel 3D te printen en voor de afwerking naar een ander apparaat te verplaatsen, kan de hele operatie in één machine plaatsvinden. Dit proces vermindert de tijd die nodig is om elk onderdeel te produceren en na te bewerken.
Er is nu een klein aantal bedrijven die hybride oplossingen aanbieden, waaronder Hybrid Manufacturing Technologies en Imperial Machine &Tool Co.
Evenzo zijn er verschillende fabrikanten van snijgereedschappen en CNC-freesmachines , zoals DMG Mori en Mazak, bieden nu een vorm van AM-mogelijkheden.
Hybride hardware-oplossingen blijven beperkt vanwege het vroege stadium van de technologie. Dat gezegd hebbende, heeft het gebruik van additieve en subtractieve bewerkingen in één systeem het potentieel om de manier waarop onderdelen worden vervaardigd te transformeren.
Ontwikkelingen in materialen voor 3D-printen van metaal
Materiële diversiteit bereiken
Het ontwikkelen van metalen voor additive manufacturing is een uitdagend proces — het ontwikkelen van een volledig nieuwe metaallegering kan tot 3 jaar duren.
Eerste gebruikers van 3D-metaalprinten haalden metaalpoeders uit de giet- en smeedmarkt. Deze zijn echter niet de ideale keuze voor additive manufacturing, waar specifieke chemie en microstructuren vereist zijn.
Naarmate de technologie is geëvolueerd, zijn materiaalontwikkelaars en early adopters, die meer bekend zijn met de technologieën en machines, begonnen metalen materialen te ontwikkelen die geschikt zijn voor AM.
Terwijl 3D-printen van metaal steeds meer in de richting van serieproductie gaat, zal materiaaldiversiteit een steeds grotere rol gaan spelen. Hoe meer kwaliteitsmaterialen er beschikbaar zijn, hoe breder het toepassingsgebied van de technologie.
3D-printen van uitdagende metalen
De ontwikkeling van krachtige lasers binnen DMLS-systemen heeft ertoe geleid dat er meer materialen met de technologie kunnen worden verwerkt. Deze omvatten metalen zoals roestvrij staal, titanium, kobaltchroom en Inconel-legeringen.
Niet alle metalen lenen zich echter gemakkelijk voor 3D-printen. Zo zijn koper en edele metalen bijzonder uitdagend om te printen, deels omdat ze de warmte reflecteren die wordt toegepast door een laserstraal.
Gelukkig zijn er stappen gezet om nieuwe systemen te ontwikkelen die dergelijke metalen in 3D kunnen printen.
Tijdens formnext 2018 demonstreerde TRUMPF zijn groene lasertechnologie die zowel puur koper als andere edele metalen kan printen.
Het bedrijf is van mening dat 3D-printen van puur koper een alternatieve manier kan worden om geleidende inductoren en warmtewisselaars te maken, die met name nuttig zijn voor de elektronica- en auto-industrie.
Op dezelfde manier, Electron Beam Melting (EBM), een proces waarbij een elektronenstraal als warmtebron wordt gebruikt, is ontwikkeld voor het verwerken van hittegevoelige en scheurgevoelige materialen, zoals titaniumaluminide (TiAl).
Dankzij zijn unieke vermogen om extreem hoge temperaturen te bereiken, is EBM naar verluidt de enige commerciële AM-oplossing voor het vervaardigen van onderdelen van titaniumaluminide.
Materiaalleveranciers stappen over op metaal AM
Ondanks de uitdagingen bij het ontwikkelen van metaalpoeders en legeringen die geschikt zijn voor 3D-printen, wordt de lijst van leveranciers van fabricagematerialen die op de markt willen komen gestaag groter.
Bedrijven als Carpenter Technology, Sandvik AB, voestalpine en Höganäs AB zijn slechts enkele van de bekende namen die metaal 3D-printen hebben geïdentificeerd als een waardevolle kans op lange termijn.
In de afgelopen twee jaar heeft de industrie deze bedrijven zien investeren in AM, waardoor ze hun aanwezigheid op de metaalpoedermarkt consolideren.
In februari 2018 kondigde Sandvik, een toonaangevende leverancier van metaalpoeders, een investering van $ 25 miljoen aan in de bouw van een fabriek voor de productie van metaalpoeder in Zweden. De nieuwe fabriek zal nikkel- en titaniumlegeringen produceren.
Carpenter Technology heeft ook zijn activiteiten in metaal AM uitgebreid, met een reeks investeringen in bedrijven zoals CalRAM, een AM-servicebedrijf, en Puris, een maker van titaniumpoeders.
In 2018 nam het bedrijf LPW Technology over, een toonaangevende leverancier van metaalpoeders voor DED- en Powder Bed Fusion-technologieën.
Als een belangrijke speler in de ontwikkeling van metalen materialen voor AM, is LPW Technology ongetwijfeld een belangrijke toevoeging aan Carpenter's portfolio, waarmee het bedrijf een stevige intrede op de materialenmarkt heeft gedaan.
Nu andere materiaalbedrijven ook stappen ondernemen om te reageren op de groei van de markt voor 3D-metaalprinten, kan de industrie de komende jaren aanzienlijke ontwikkelingen verwachten in de diversiteit en prestaties van nieuwe metaallegeringen.
Drijzen de materiaalkosten naar beneden?
De kosten van metaalpoeders van AM zijn aanzienlijk hoger geweest dan de kosten van metalen voor traditionele processen.
"Materiaalprijs is een andere cruciale factor [voor de productie van AM-eindonderdelen]:de materialen zijn erg duur en bij de fabricage draait alles om de kosten", zegt HP's Tim Weber in een recent interview met AMFG.
“Als u een productiemethode heeft waarmee u onderdelen tegen lagere kosten kunt produceren, zullen de meeste fabrikanten meteen overstappen. Maar we moeten ervoor zorgen dat de totale materiaalkosten worden verlaagd.”
De kosten voor TI64-poeder kunnen bijvoorbeeld variëren van $ 150 tot $ 400 per kilogram. Deze poeders vereisen veel energie om te worden geproduceerd en moeten een bepaalde grootte en vorm hebben, terwijl ze een hoge mate van zuiverheid behouden. Deze factoren dragen bij aan de hoge kosten.
Met de komst van nieuwe spelers op de materialenmarkt zal deze toegenomen concurrentie er echter voor zorgen dat de prijs van metaalpoeders blijft dalen.
Een manier om de materiaalkosten te verlagen zou het gebruik van goedkopere metaalspuitgietpoeders (MIM) kunnen zijn.
Verschillende fabrikanten van apparatuur, zoals HP, Desktop Metal en Digital Metal hebben van deze gelegenheid gebruik gemaakt en hebben spuitsystemen ontwikkeld die geschikt zijn voor het verwerken van MIM-poeders.
Het gebruik van goedkope MIM-poeders die niet maakt de technologie alleen toegankelijker, maar breidt ook de materiaalkeuze voor metaal AM aanzienlijk uit.
Ontwikkelingen in software voor 3D-printen van metaal
Een ander groeiend, maar vaak minder besproken gebied van metaal 3D-printen is simulatiesoftware.
De aard van het 3D-printproces van metaal betekent dat het moeilijk kan zijn om de eerste keer een succesvolle afdruk te maken. De complexiteit van de geometrieën, gekoppeld aan de hoge temperaturen en benodigde ondersteunende structuren, zijn slechts enkele van de uitdagingen waarmee ingenieurs worden geconfronteerd bij het ontwerpen voor 3D-printen van metaal.
Metaalsimulatiesoftware is daarom een cruciaal element in het drukproces. Met simulatie kunnen ingenieurs voorspellen en analyseren hoe een onderdeel zich tijdens het proces zal gedragen voordat het onderdeel daadwerkelijk wordt afgedrukt. Gebruikers kunnen hun bouwvoorbereiding optimaliseren, waardoor de kans op afdrukfouten wordt verkleind.
Er is een groeiend aantal simulatiesoftwareoplossingen op de markt, waaronder Autodesk's Netfabb, Dassault Systèmes' SIMULIA en Simufact.
Interessant is dat, zoals het geval is met materialen, verschillende gevestigde spelers AM ook als een belangrijke kans zien.
Laten we ANSYS als voorbeeld nemen. ANSYS is een bekende leverancier van technische simulatiesoftware, die doorgaans wordt gebruikt om producten en halfgeleiders te ontwerpen, naast simulatieoplossingen die de productprestaties kunnen testen.
ANSYS deed zijn intrede op de metaal 3D-printmarkt met de overname van 3DSIM, een metaalsimulatiebedrijf in 2017. Sindsdien heeft het bedrijf zijn Additive Suite- en Additive Print-simulatieplatforms in begin 2018.
De uitdagingen van 3D-printen van metaal
Standaardiseren van metalen onderdelen
De overstap maken van prototyping naar productie is niet zonder uitdagingen. Vooral serieproductie is gebaseerd op een specifieke set voorschriften, documentatie en processen die gevestigde normen zijn geworden.
Metaal 3D-printen staat nog maar aan het begin van zijn reis naar het vaststellen van zijn eigen normen. Momenteel bestaan er voornamelijk normen om de algemene kenmerken van metalen 3D-printprocessen zoals DED en Powder Bed Fusion te beschrijven.
Er worden ook enkele materiaalspecificaties ontwikkeld, waaronder normen voor titanium, nikkellegeringen, roestvrij staal, kobaltchroom.
Met name de Metal Powder Industries Federation (MPIF) heeft onlangs negen MPIF-standaardtestmethoden uitgegeven voor het karakteriseren van metaal-AM-poeders.
Gericht op ontwerpers, fabrikanten en gebruikers van metalen AM-onderdelen, is deze collectie het zoveelste teken van industrieën die de groeiende rol van 3D-metaalprinten in de productiewereld erkennen.
Kosten en snelheid
Ondanks de indrukwekkende vooruitgang die is geboekt, wordt 3D-printen op metaal nog steeds geplaagd door twee belangrijke beperkingen:kosten en snelheid.
“Er zijn tegenwoordig gewoon niet veel goede opties als je 3D-printen wilt gebruiken voor productie. Dit komt omdat systemen te traag zijn, de productiekosten te hoog zijn en de processen te complex zijn”, zegt Duncan McCallum, CEO van Digital Alloys.
De gemiddelde kosten van een metalen poederbedsysteem kunnen bijvoorbeeld variëren van $ 200.000 tot $ 2 miljoen. Dit is natuurlijk exclusief de materiaalkosten en eventuele nabewerkingsstappen die moeten worden genomen.
Naarmate metal AM steeds meer ingang vindt als productieoplossing, moet de technologie sneller en goedkoper om de acceptatie verder te versnellen.
Grote productie
Vanwege zijn geschiktheid voor hoogwaardige toepassingen met een klein volume, werd 3D-printen met metaal al vroeg geadopteerd door de lucht- en ruimtevaart en de medische industrie.
Echter, het potentieel van 3D-printen met metaal voor productie maakt het een opwindende technologie voor industrieën buiten deze bekende toepassingen.
Dat gezegd hebbende, blijft het verhogen van de productievolumes een belangrijke hindernis voor een bredere acceptatie van AM. Dit is met name het geval voor de auto-industrie die, afgezien van de race- en luxevoertuigensectoren, doorgaans hoge productievolumes vereist.
“De productievolumes van [Automotive] verschillen aanzienlijk van de volumes in de ruimtevaart of de medische sector”, zegt Harold Sears, Technical Leader for Additive Manufacturing van Ford Motor Company. “We moeten dus kijken naar systemen die onderdelen in minuten of seconden kunnen produceren in plaats van dagen en uren. Alles wat we kunnen doen om de technologie naar hogere bouwsnelheden te duwen, zal ons zeker ook helpen".
Hoewel verbeteringen op het gebied van hardware zullen helpen om de productievolumes verder te verhogen, is procesoptimalisatie een andere manier om hogere volumes te bereiken met 3D-metaalprinten.
Betatype heeft dit aangetoond met de creatie van koellichamen voor led-autokoplampen.
Door ontwerpoptimalisatie heeft het bedrijf een manier kunnen ontwikkelen om veel onderdelen in één gebouwschil te stapelen.
Deze aanpak heeft het mogelijk gemaakt om 384 onderdelen in één keer te produceren, waardoor de bouwtijd van 444 uur tot minder dan 30 uur is teruggebracht en de kosten van $ 39 zijn gedaald tot slechts $ 3.
Betatype gelooft dat het draaien van slechts 7 machines met dit geoptimaliseerde proces 1 miljoen onderdelen per jaar zou kunnen opleveren, wat overeenkomt met de eisen van de auto-industrie op het gebied van zowel volume als kosteneffectiviteit.
De toekomst van 3D-metaalprinten
Metaal 3D-printen heeft grote vooruitgang geboekt en heeft de 3D-printhype van het midden van de jaren 2000 overwonnen. Tegenwoordig zien we vooruitgang op elk gebied van de markt, van de ontwikkeling van nieuwe printprocessen tot snellere machines en een groter scala aan geschikte materialen.
Aan de investeringskant groeit de markt snel, aangezien grotere bedrijven investeren in en gespecialiseerde bedrijven verwerven en nieuwe spelers de markt betreden. Onlangs heeft printgigant Xerox een duidelijke stap gezet in metaal 3D-printen met de overname van metaal 3D-printing startup, Vader.
Wat zal de situatie over 10 jaar zijn, nu het landschap snel verandert? Hoewel moeilijk te voorspellen, is één ding duidelijk:3D-printen van metaal is goed op weg om een echt levensvatbare productie-oplossing te worden.
3d printen
- Vuurvaste metaalpoeders VS 3D-afdruktechnologie
- De Rapid Additive Forging-technologie van Prodways:een nieuwe benadering van het printen van metaal
- Waarom brengen gevestigde fabrikanten 3D-printen in huis?
- Overwegend wat nieuwe metaalprinttechnologie betekent voor AM
- Imperial College London onthult nieuwe metaalprintertechnologie
- Hoe kan 3D-printen het metaalgieten ten goede komen? Hier zijn 3 manieren
- Ontwikkelingsnormen voor 3D-printen:waar staan we vandaag? (update 2020)
- Stereolithografie en digitale lichtverwerking:waar zijn we vandaag?
- Wat zijn de voordelen van 3D-printen voor metaalbewerkers?
- Technologieoverzicht:wanneer u echt voor metaal 3D-printen moet gaan
- Direct Metal Laser Sintering (DMLS) 3D-printen:technologieoverzicht