PRACHTIG project ontwikkelt met succes een thermoplastische romphuid van 8,5 meter lang
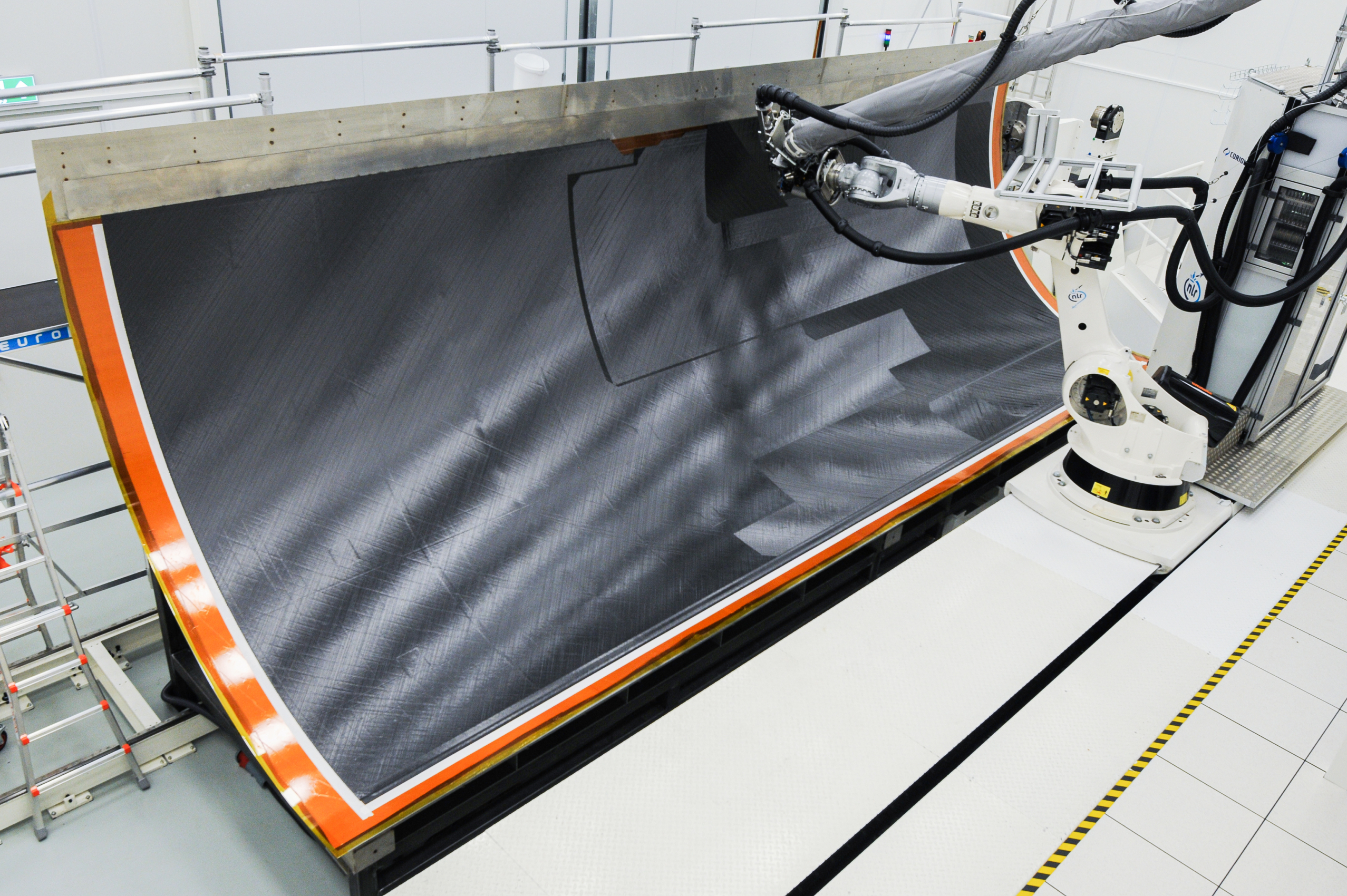
Als onderdeel van het Clean Sky 2-initiatief van de EU zoekt de lucht- en ruimtevaartindustrie naar een vluchtroute naar duurzaamheid, met name door de overgang van aluminium naar koolstofvezelversterkte composieten om vliegtuigstructuren te verbeteren en emissies sterk te verminderen. De Clean Sky 2 Multifunctional Fuselage Demonstrator (MFFD), is zo'n programma dat in 2017 begon en bestaat uit tientallen individuele projecten en werkpakketten (voor meer hierover, zie "Leren van LM PAEK-lassen voor Multifunctional Fuselage Demonstrator"). Met name het STUNNING-project (SmarT mUlti-fuNctionNal and INtegrated thermoplastic fuselaGe), dat het onderste rompgedeelte van de MFFD zal ontwikkelen, heeft onlangs een 8,5 meter lange romp van thermoplastische kunststof geproduceerd via geautomatiseerde vezelplaatsing (AFP ) (zie video hieronder).
STUNNING wordt geleid door GKN Fokker (Papendrecht, Nederland) met belangrijke partners Diehl Aviation (Laupheim, Duitsland), Netherlands Aerospace Centre (NLR, Amsterdam, Nederland) en de Technische Universiteit Delft (TU Delft, Delft, Nederland). Het project heeft tot doel geautomatiseerde assemblageprocessen, thermoplastische fabricage- en lastechnologieën, geïntegreerde ontwerp- en fabricageontwikkeling en geavanceerde elektrische systeemarchitecturen verder te ontwikkelen.
“Waarschijnlijk de helft van de lucht- en ruimtevaartindustrie in Europa is betrokken bij het MFFD-project, aangezien we echt graven in het onderzoeken van verschillende productietechnieken, allemaal met het oog op duurzaamheid”, beschrijft Joachim de Kruijk, senior R&D composieteningenieur bij het NLR. “Bij het onderzoeken van de verschillende productieopties en materialen, geloven we dat de beste manier om dit doel van een duurzamere rompstructuur te bereiken, is om de nieuwe generatie thermoplastische materialen te gebruiken. We zien dat een dergelijk materiaal een verandering in de fabricagebenadering en ontwerptechnieken mogelijk kan maken die kunnen resulteren in veel lichtere vliegtuigen, wat betekent dat er minder brandstof wordt verbruikt en dat er minder CO2 wordt uitgestoten. en GEENx, en dat alles met behoud van de kracht en veiligheid die we verwachten van traditionele aluminium vliegtuigen.”
Een aantal moderne vliegtuigen, zoals de Airbus A350 XWB en de Boeing 787 Dreamliner, gebruiken al thermohardende composietmaterialen bij de constructie van onderdelen en beugels en zelfs de huid van de romp, merkt Clean Sky op. In het STUNNING-project kregen experts van GKN Fokker en NLR echter de opdracht om te ontwerpen voor fabricage die een hoge productiesnelheid van grote, structurele onderdelen voor vliegtuigen mogelijk maakt.
"Een van de echte verbeteringen die het gebruik van thermoplasten biedt, is dat dit materiaal tijdens het fabricage- en assemblageproces, in tegenstelling tot thermoharders, meerdere keren kan worden verwarmd en opnieuw verwarmd om uniformiteit en hechting te garanderen", legt De Kruijk uit. “In STUNNING was een van onze doelstellingen om te laten zien hoe de verschillende processen kunnen worden gecombineerd om zowel structurele als niet-structurele componenten te bouwen voor volledige integratie. Om dit te doen, wilden we de hele onderste helft van een romp bouwen om niet alleen inzicht te krijgen in de maakbaarheid van de huid van het vliegtuig, maar ook in de substructuren zoals de verstijvers voor onder de huid en andere structurele stukken zoals vloerbalken , evenals delen van de cabine, de systemen en zelfs laaddeuren.”
Met deze verheven doelen in het achterhoofd, gingen de medewerkers op zoek naar het testen van hun verschillende fabricagetechnieken om de talrijke onderdelen en constructies te bouwen die in een romp moesten worden geïntegreerd. Voor het NLR betekende dit het testen van zijn kennis en productiecapaciteiten met het grootste deel van allemaal, de onderbuik van de rompstructuur. Met behulp van zijn eigen, ultramoderne AFP-machine zou het NLR zijn doel hebben bereikt door de onderste helft van de romphuid te bouwen - een enkel stuk, met een lengte van 8,5 meter lang en een diameter van 4 meter - zei om het grootste bekende thermoplastische stuk ooit gemaakt te zijn.
Dit was geen geringe prestatie, zegt Clean Sky. Hoewel composietmaterialen zoals thermoharders in toenemende mate worden gebruikt in de vliegtuigbouw, zijn grote thermoplastische onderdelen relatief nieuw in het veld, wat ook betekent dat het in vergelijking iets duurder kan zijn. Maar volgens De Kruijk is dat gewoon tegen de nominale waarde, want de voordelen wegen ruimschoots op tegen de prijs.
“Omdat het nieuwer is en vanwege zijn eigenschappen, zijn thermoplasten iets duurder dan thermoharders. Maar er zijn een aantal onderscheidende factoren die het gebruik van het nieuwe materiaal de moeite waard maken. Thermoplasten zijn bijvoorbeeld iets lichter dan thermoharders omdat het een taaier matrixmateriaal is en beter bestand is tegen stootschade, wat belangrijk is”, legt De Kruijk uit. “Buiten dat is echter de manier waarop het materiaal kan worden gebruikt in de productie. Om verschillende onderdelen of stukken thermoplast met elkaar te verbinden, hoeft u alleen maar het materiaal te verhitten om het aan elkaar te lassen. Dat betekent dat we ons ontdoen van de honderdduizenden bevestigingsmiddelen die conventionele vliegtuigen bij elkaar houden, wat ongetwijfeld zal leiden tot meer dramatische gewichtsbesparingen.”
Een ander onderwerp waar het NLR onderzoek naar heeft gedaan, is het inspecteren, onderhouden en repareren van vliegtuigen die zijn gemaakt van thermoplasten. Vanaf nu is het gebruik van grote composietonderdelen in vliegtuigen enigszins beperkt, wat betekent dat er veel minder gegevens en praktijk zijn op het gebied van inspectie, onderhoud en herstelbaarheid.
“Momenteel werken we aan de ontwikkeling van technologie voor een aantal niet-destructieve inspectietechnieken [NDI] om vliegtuigen te inspecteren, zoals thermografie en shearografie, maar die technologie is nog in ontwikkeling. Momenteel passen we ultrasone inspectie toe om te controleren op defecten en problemen, maar dat kan een tijdrovend proces zijn”, stelt De Kruijk. “De huidige inspectie en het onderhoud van conventionele vliegtuigen verloopt echter ook traag. Vanwege de aard van thermoplasten, met de mogelijkheid om opnieuw te worden verwarmd en aan elkaar te worden gelast, zien we dat onderhoud veel sneller kan worden gedaan dan aan traditionele vliegtuigen. Stelt u zich eens voor hoeveel tijd er kan worden bespaard door niet elke klinknagel in de hele constructie afzonderlijk met de hand te hoeven controleren.”
Vanwege de grootte van de uiteindelijke huid werden twee segmenten geproduceerd. Met de voltooiing van de lay-up van het tweede 90-graden segment van de onderste romphuid, is de volgende stap het consolideren en samenvoegen van de twee 90-graden segmenten van de onderste romphuid tot een 180-graden romphuidsegment. Om dit te doen, is echter naar verluidt een zeer grote autoclaaf nodig die in staat is om de overmaatse stukken zowel te passen als te verwarmen om ze samen te voegen. Omdat zo'n autoclaaf in Nederland niet bestaat, gaan de twee helften naar Duitsland voor integratie. Het proces zou eind juni plaatsvinden.
“Ervan uitgaande dat we deze twee delen van de romp in juni kunnen verbinden, verwachten we dat we tegen de zomer de geconsolideerde huid terug bij het NLR kunnen hebben om het gedetailleerde NDI-proces te starten om het succes te testen en te verifiëren en de kwaliteit van de de hele onderhuid van de romp”, illustreert De Kruijk. "Daarna zullen we het naar onze partners bij GKN Fokker verzenden, waar de verschillende onderdelen die in het STUNNING-project zijn ontwikkeld, volledig kunnen worden geassembleerd en geïntegreerd."
Voor een volledige samenvatting van het MFFD-project, zie "Vooruitgang met de Multifunctional Fuselage Demonstrator (MFFD)." Bekijk voor meer informatie over inductielassen dit webinar gepresenteerd door GKN Fokker.
Dit project heeft financiering ontvangen van de Clean Sky 2 Joint Undertaking (JU) onder subsidieovereenkomst nr. 945583. De JU ontvangt steun van het Horizon 2020-onderzoeks- en innovatieprogramma van de Europese Unie en de Clean Sky 2 JU-leden anders dan de Unie.
Hars
- Verbluffende mode leveren door snelle productie
- Een data-analyseproject starten in de productie
- Fraunhofer IPT ontwikkelt thermoplastische composieten in waterstofopslag, motorbladen en meer
- Clean Sky 2 FUSINBUL-project ontwikkelt full-scale drukschotten van koolstofvezel
- RECONTRAS-project valideert het gebruik van microgolven en laserlassen om recyclebare composieten te verkrijgen
- DLR Institute of Structures and Design vergroot de maturiteit van thermoplastische composiet rompstructuren
- Consortium streeft naar oplossingen voor thermoplastische composietstructuren van koolstofvezel
- Thermoplastische deur een primeur voor autocomposieten
- NCC en Surface Generation werken samen om thermoplastische overmolding-mogelijkheden te demonstreren
- Snelle productie van op maat gemaakte samengestelde blanks
- RTP Company ontwikkelt lichte en sterke thermoplastische verbindingen