Lanxess Tepex composiet materiaal lichtgewichten luxe sedan laadruimte goed
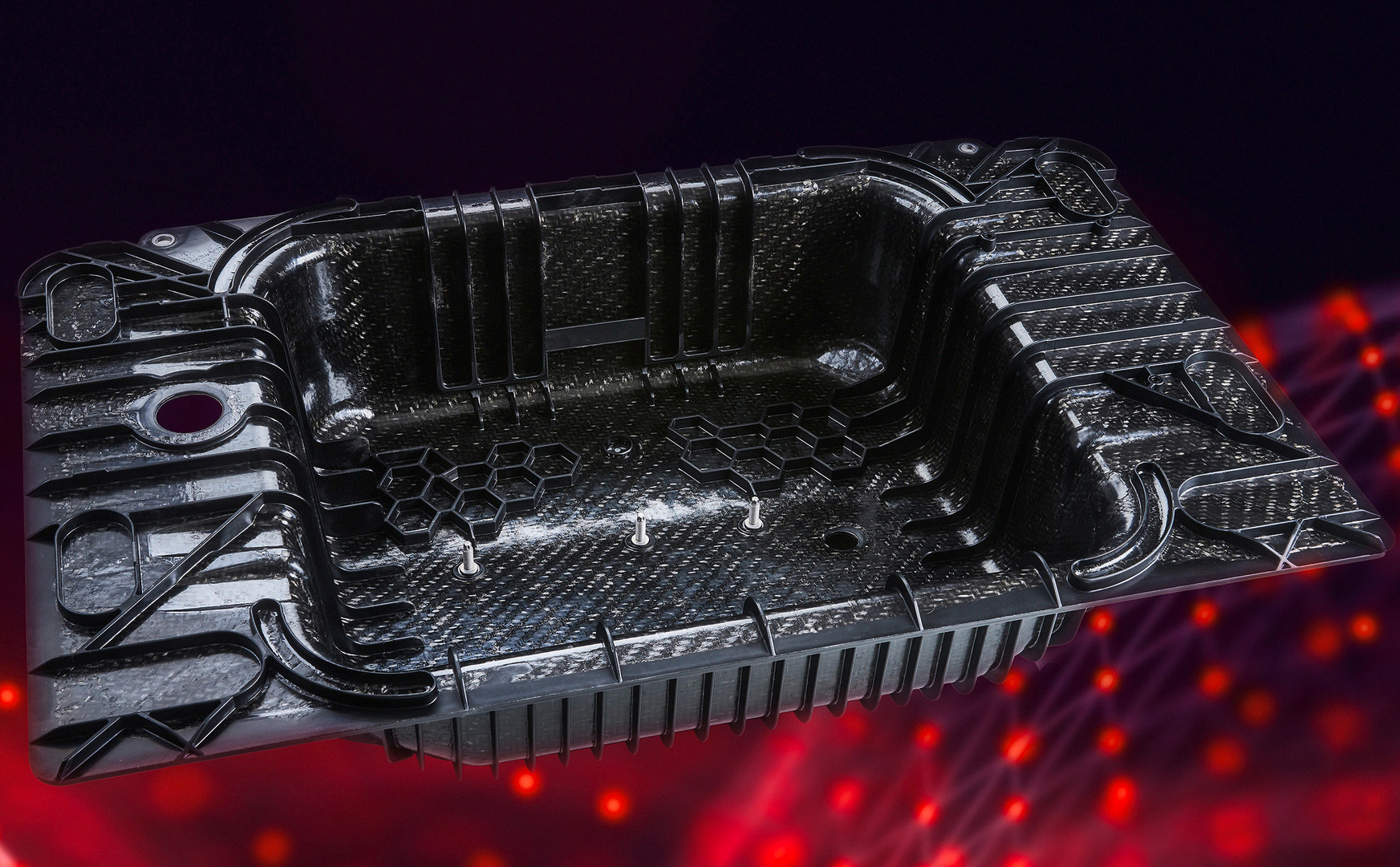
Lanxess (Keulen, Duitsland) heeft zijn Tepex dynalite continu vezelversterkte thermoplastische composietmaterialen toegepast bij de vervaardiging van de laadruimte die goed is geïnstalleerd in de luxe sedan van de Mercedes-Benz S-Klasse om plaats te bieden aan de 48V-poederaccu van het voertuig. Lanxess zegt dat de composietcomponenten bestand zijn tegen hoge mechanische belastingen en ongeveer 30% lichter zijn dan vergelijkbare componenten van plaatstaal.
“Bij een crash mag de batterij niet door de niswand dringen of deze op enigerlei wijze beschadigen. Dit wordt gegarandeerd door de hoge sterkte en stijfheid van ons op stof gebaseerde composietmateriaal”, zegt Dr. Klaus Vonberg, applicatiedeskundige voor Tepex bij Lanxess. "Het composietontwerp zorgt er ook voor dat de laadruimte lekdicht is, waardoor het binnendringen en ontsnappen van vloeistoffen zoals water en batterij-elektrolyt wordt voorkomen."
De veiligheidscomponent is vervaardigd in een hybride vormproces met behulp van een blanco van ~110 x 80 centimeter die wordt geproduceerd door een watersnijmachine. De blank is gemaakt van op polyamide 6 (PA6) gebaseerde Tepex dynalite 102-RG600(2), dat is versterkt met twee lagen doorlopende glasvezelversterkte stoffen. Bovendien wordt de PA6 Durethan BKV60H2.0EFDUS060 van Lanxess gebruikt als materiaal voor ruginjectie om bevestigingsmiddelen te integreren en de ribben te versterken. Zestig procent van zijn massa bestaat uit korte glasvezels, zegt Lanxess, dat ook zijn sterkte en stijfheid optimaliseert voor gebruik met het Tepex-materiaal.
Het vormen (draperen) van de blanco wordt vervolgens uitgevoerd door een stempel, een zeer complex proces, zegt het bedrijf onder meer vanwege de hoge trekverhoudingen. Dit komt doordat het composietmateriaal niet plastisch uitzet zoals plaatwerk maar vervorming ondergaat als reactie op de beweging (drapping) van het vezelmateriaal, waardoor het composietmateriaal tijdens het vormproces continu van buitenaf moet worden aangevoerd. Als de beweging te groot is, kunnen de vezels het vormingsproces belemmeren, waardoor ze breken en de rest van het proces beïnvloeden.
Lanxess gebruikte ook een reeks virtuele rekenmodellen, waardoor het bedrijf het drapeerproces nauwkeurig kon simuleren — inclusief het bepalen van de optimale 3D-snijgeometrieën van de onbewerkte plaat en het vormingsgedrag — om de vormingseffecten beter te voorspellen en te analyseren en dienovereenkomstig te reageren.
“Voor de laadruimte hebben we ook bepaald wanneer de kritische afschuifhoek van de stof wordt bereikt tijdens het vormen, waar rimpels ontstaan en waar vezels beginnen te breken”, zegt Vonberg. "Onze berekeningen en simulaties hebben er ook voor gezorgd dat de afgeronde hoeken van het onderdeel bestand zijn tegen de verwachte belastingen." De lokale oriëntatie van de continue vezels zelf in componentgebieden met een uitgesproken 3D-contour (bijvoorbeeld in de afgeronde hoeken) werd ook gesimuleerd. Dit is een voorwaarde voor het nauwkeurig voorspellen van mechanisch gedrag in termen van integratieve simulatie. "Dit alles maakt deel uit van ons serviceaanbod onder het merk HiAnt waarmee we de ontwikkelingsexperts van onze klanten hebben ondersteund bij het goed ontwerpen van de laadruimte", zegt Vonberg.
Met het oog op de toekomst merkt Vonberg op dat Lanxess ook potentieel ziet in elektrische voertuigen (EV's). "Voor veiligheidsvoorzieningen zijn nu complete batterijsysteembehuizingen of componenten voor de opbergruimte beschikbaar onder de 'motorkap' - omdat ons lichtgewicht constructiemateriaal veel lichter is dan metaal en zo helpt om het bereik van EV's uit te breiden", besluit hij.
Hars
- Lanxess voegt twee nieuwe productielijnen toe voor composietmateriaal Tepex
- Lichtgewicht composiet rugleuning, ontwikkeld door Covestro en de Chinese autofabrikant GAC
- Continu-vezelversterkte thermoplastische composiet volledig gemaakt van natuurlijke hulpbronnen
- DIN 1725-1 klasse 3.0915 H28
- DIN 1725-1 klasse 3.0915 T6
- DIN 1725-1 klasse 3.0915 H16
- DIN 1725-1 klasse 3.0915 H1x
- DIN 1712-3 kwaliteit 3.0305 H14
- DIN 1725-1 klasse 3.3535 H1x
- EN 573-3 klasse AW-1050A
- DIN 1725-1 klasse 3.3535 T6