Op snijden gebaseerd mechanisme voor verwijdering van één atomaire laag van monokristallijn koper:edge-radius-effect
Abstract
Het uiteindelijke doel van mechanisch snijden is om de minimale spaandikte terug te brengen tot een enkele atomaire laag. In deze studie wordt het op snijden gebaseerde enkelvoudige atomaire laagverwijderingsmechanisme op monokristallijn koper onderzocht door een reeks moleculaire dynamische analyses. De onderzoeksresultaten melden dat wanneer de snijdiepte afneemt tot atomaire schaal, de minimale spaandikte kan worden teruggebracht tot een enkele atomaire laag door mechanisch te snijden met behulp van gereedschap met afgeronde randen. Het materiaalverwijderingsgedrag tijdens het verwijderen van een enkele atomaire laag op basis van snijden vertoont vier kenmerken, waaronder spaanvorming door door schuifspanning aangedreven dislocatiebeweging, elastische vervorming op het bewerkte oppervlak, atomair sizing-effect en cutting-edge radius-effect. Op basis van dit inzicht wordt een nieuw snijmodel voorgesteld om het materiaalverwijderingsgedrag te bestuderen bij het op snijden gebaseerde verwijderingsproces van een enkele atomaire laag, significant verschillend van die voor nanosnijden en conventioneel snijden. De resultaten bieden theoretische ondersteuning voor het onderzoek en de ontwikkeling van de fabricagetechnologie op atomaire en bijna atomaire schaal.
Inleiding
Mechanisch snijden, als een van de belangrijkste subtractieve bewerkingsmethoden, is toegepast om onderdelen te produceren met een hoge oppervlaktekwaliteit [1, 2]. Er is een groot aantal theoretische en experimentele onderzoeken uitgevoerd om het onderliggende materiaalverwijderingsmechanisme op nanoschaal te verduidelijken om de basistheorie voor nanosnijden vast te stellen en te verrijken [3,4,5,6]. De onderzoeksresultaten dragen aanzienlijk bij aan de toepassing van nanometrisch snijden in de academische wereld en de industrie, waardoor de productie mogelijk wordt van hoogwaardige onderdelen die een complexe vorm en nanometrische oppervlaktekwaliteit vereisen [7, 8]. Er is echter nog steeds geen rapport over het mechanisme van materiaalverwijdering bij snijden op atomaire en bijna atomaire schaal (ACS), waardoor de voortgang van de ontwikkeling van de volgende generatie fabricagetechnologie ernstig wordt beperkt - fabricage op atomaire en bijna atomaire schaal ( ACSM), dwz Fabricage III [9]. Bovendien benadrukte de voortschrijdende ontwikkeling van apparaten op atomaire schaal ook de vraag naar verschillende bewerkingsprocessen om ACSM [10] te bereiken.
Bij conventioneel snijden op macroschaal is de snijdiepte aanzienlijk groter dan de snijkantradius, waar de materiaalverwijdering wordt gerealiseerd door materiaalafschuiving aangedreven spaanvorming [11,12,13]. Bij micro-/nanosnijden, aangezien de snijdiepte vergelijkbaar is met of kleiner is dan de snijkantstraal van het gereedschap, wordt de spaanvorming van extrusie geleidelijk domineren met een afname van de snijdiepte tot op nanoschaal, wat sterk wordt beïnvloed door de snijkantstraaleffecten [14,15,16] ,17,18,19]. Bij ACS-snijden, aangezien de snijdiepte verder wordt verlaagd tot bijna atomaire schaal en zelfs atomaire schaal, die veel lager is dan de snijkantradius, zou het effect van de snijkantradius onvermijdelijk het materiaalverwijderingsgedrag beïnvloeden.
Bovendien is de snijdiepte, in tegenstelling tot conventioneel snijden en micro/nano snijden, bij ACS-snijden niet alleen aanzienlijk lager dan de snijkantradius, maar ook vergelijkbaar of zelfs lager dan de radius van de werkstukatomen. Het praktische materiaalverwijderingsgedrag zou veranderen bij verschillende verhoudingen van snijdiepte tot atomaire straal van het werkstuk, wat wordt erkend als een nieuw dimensioneringseffect, d.w.z. atomair dimensioneringseffect [20]. Daarom moet bij ACS-snijden rekening worden gehouden met zowel het snijkantstraaleffect als het atoomgrootte-effect. Er is echter geen rapport over deze uiterst belangrijke kwestie in de studie van ACS-snijtechnologie.
Om die redenen worden in de huidige studie het atomaire sizing-effect en het edge-radius-effect op het op snijden gebaseerde enkelvoudige atomaire laagverwijderingsmechanisme onderzocht met behulp van moleculaire dynamica (MD) -modellering.
Dit document is gestructureerd door de volgende paragrafen. Hoofdstuk 2 introduceert de gebruikte methodologie, inclusief modellering en protocol, geschikte potentiële functie. Hoofdstuk 3 presenteert de analyseresultaten en relevante discussies. Sectie 4 bespreekt het gedetailleerde op snijden gebaseerde mechanisme voor het verwijderen van een enkele atomaire laag, onder de gekoppelde invloed van het geavanceerde effect en het atomaire sizing-effect. De onderzoeksbevindingen worden geconcludeerd in Sectie 5.
Methodologie
Simulatiemodel en protocol
Aangezien de snijdiepte afneemt tot atomaire of bijna atomaire schaal, is het inderdaad een uitdaging om het materiaalverwijderingsproces in de praktijk ervaringsgericht te observeren. In deze studie wordt een reeks MD-simulaties uitgevoerd om het op snijden gebaseerde verwijderingsmechanisme van een enkele atomaire laag te analyseren, waarbij nadrukkelijk het atomaire maateffect van het werkstuk en het cutting-edge radius-effect worden gefocust.
Figuur 1 toont de snapshots voor atomaire configuratie van het diamant-koper snijmodel, dat bestaat uit een enkelkristal koperen werkstuk en een diamantsnijgereedschap. De simulaties worden uitgevoerd op het (111) vlak van eenkristalkoper. De afmetingen van het werkstuk in x -[1 -1 0], y -[1 1 -2], en z -[1 1 1] richtingen zijn respectievelijk 27, 10 en 5 nm. Tijdens MD-simulaties worden de werkstukatomen verdeeld in respectievelijk grenslaagatomen, thermostatische laagatomen en Newtoniaanse laagatomen, zoals weergegeven in Fig. 1. De twee lagen aan de onderkant van het werkstuk, namelijk de grenslaag, worden vastgehouden over de MD-simulaties, om de mogelijke door snijden veroorzaakte positievertaling van het werkstuk te elimineren. De drie atomaire lagen naast de grenslaag zijn atomen van de thermostaatlaag. De temperatuur van de thermostatische laag wordt op 298 K gehouden door snelheidsaanpassingsmethoden. De overige werkstukatomen behoren tot de Newtoniaanse laag. In de huidige simulaties is de hellingshoek en vrijloophoek van het snijgereedschap 0° en 12°. De gedetailleerde modelparameters zijn samengevat in Tabel 1. Aangezien ACS-snijden bij voorkeur wordt uitgevoerd met een lagere snijsnelheid, wordt een snijsnelheid van 25 m/s in de richting [-1 1 0] gebruikt, rekening houdend met het effect van snijsnelheid en rekentijd kosten.
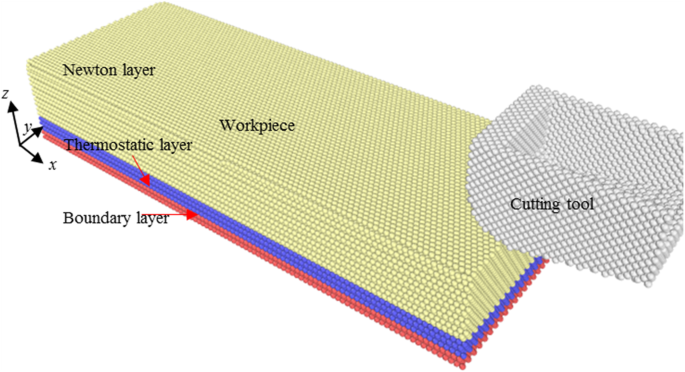
Simulatiemodel voor diamantslijpmodel
Potentiële functie
Het koper-diamant-snijsysteem omvat hoofdzakelijk twee soorten atomen, namelijk koper- en diamantatomen. In de MD-simulaties moeten de interatomaire interacties nauwkeurig worden beschreven om de rekennauwkeurigheid van simulatieresultaten te garanderen. Een redelijke selectie van potentiële functies is dus van cruciaal belang. In deze studie wordt de veelgebruikte potentiaalfunctie van de embedded atoommethode (EAM) gebruikt om de interatomaire interacties tussen koperatomen te beschrijven [21]. Morse-functie wordt toegepast om de interacties tussen koperatomen en diamantatomen (Cu-C) te berekenen, voornamelijk afhankelijk van de r.
$$ E={D}_0\left[{e}^{-2\alpha \left(r-{r}_0\right)}-2{e}^{\alpha \left(r-{r} _0\rechts)}\rechts] $$ (1)waar E en D 0 verwijzen naar het paar potentiële energie en cohesie-energie, α staat voor een constante, r 0 is de evenwichtsafstand, en r is de afstand tussen twee atomen. Voor Cu-C-interacties, D 0 is 0.087ev, r 0 is 0,205 nm [22], en α is 51.40 nm −1 . Voor de interacties tussen koolstofatomen in snijgereedschap (C-C) is de aanzienlijk sterkere bindingssterkte tussen diamantatomen dan koperatomen te verwaarlozen. Het snijgereedschap wordt tijdens de analyse als stijf beschouwd.
Definitie van snijdiepte
Zaagdiepte (a ) wordt gedefinieerd als de afstand tussen het hoogste punt van het werkstukoppervlak en het laagste punt van het snijgereedschap. De grootte van een werkstukatoom wordt meestal weergegeven door de atoomstraal (r w ). Zoals aangegeven in Fig. 2, wanneer de bovenste eerste atomaire laag van het werkstukoppervlak moet worden verwijderd, kan theoretisch de maximale snijdiepte als volgt worden verkregen:
$$ {a}_{\mathrm{max}}={r}_w+0.5\ast {d}_{layer} $$ (2)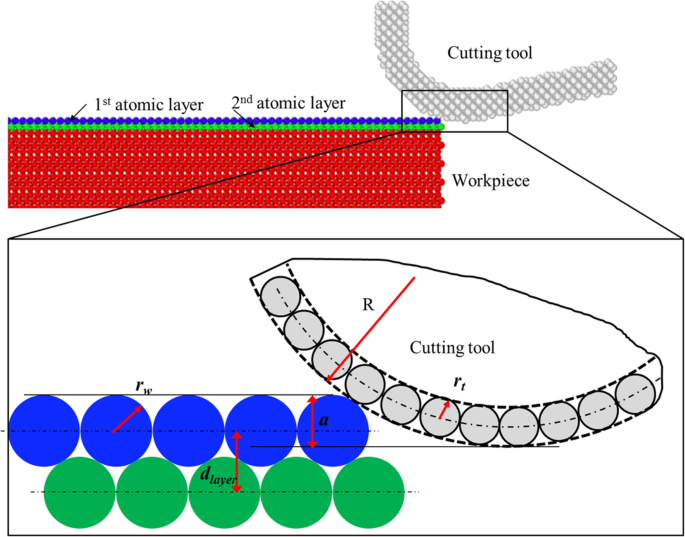
Schematisch diagram voor de definitie van de snijdiepte bij het verwijderen van een enkele atomaire laag
Hier, d laag vertegenwoordigt de afstand tussen de bovenste aangrenzende atomaire lagen op het werkstukoppervlak. In deze studie is alle analyse gebaseerd op het (111) oppervlak van een monokristallijn koperwerkstuk; daarom, de r w in verg. (2) verwijst naar de straal van koperatomen, namelijk 1,28 Å. De d laag is 2.087 Å. Wanneer een is groter dan a max , zal het laagste punt van het snijgereedschap in direct contact komen met de tweede atoomlaag en kan de materiaalvervorming en zelfs verwijdering veroorzaken. Daarom zijn in de huidige studie de gebruikte snijdiepten kleiner dan a max (2.32 Å).
Op basis van de bevindingen zal het fundamentele op snijden gebaseerde mechanisme voor het verwijderen van een enkele atomaire laag sterk worden gewijzigd bij verschillende combinaties van de verhoudingen van a naar R en een naar r w .
Resultaten en discussie
Volgens MD-resultaten hebben zowel het atomaire sizing-effect als het cutting-edge radius-effect het op snijden gebaseerde verwijderingsproces van een enkele atomaire laag sterk beïnvloed. In de volgende paragrafen, om het atomaire dimensioneringseffect en het gereedschapsrandradiuseffect duidelijk te beschrijven, wordt de verhouding van de snijdiepte (a ) naar atomaire straal van het werkstuk (r w ), a/r w , en die van de snijdiepte(a ) naar randradius(R ), a/R , zijn werkzaam. De analyseresultaten worden systematisch bestudeerd vanuit de aspecten spaanvorming, oppervlaktegeneratie, ondergrondse deformatie en atomair verplaatsingsgedrag. De bevindingen bieden gedetailleerde inzichten in de typische kenmerken van een op snijden gebaseerd mechanisme voor het verwijderen van een enkele atomaire laag.
Chipvorming
De analyseresultaten geven aan dat er vanwege het atomaire dimensioneringseffect van het werkstuk [20] twee kritische waarden zijn voor de verhouding van de snijdiepte (a ) naar atomaire straal van het werkstuk (r w ), namelijk kritische waarde 1 (C1 ) en kritische waarde 2 (C2 ), die het chipvormingsgedrag in verschillende gevallen verdeelde.
- een.
De verhouding van a/r w kleiner dan kritische waarde 1 (C1 ).
Figuur 3 toont de resultaten van MD-simulatie bij verschillende snijkantradiussen van het gereedschap bij een snijdiepte van ongeveer 1,1 Å. Hier is de verhouding van de snijdiepte (a ) naar atomaire straal van het werkstuk (r w ) is 0,781.
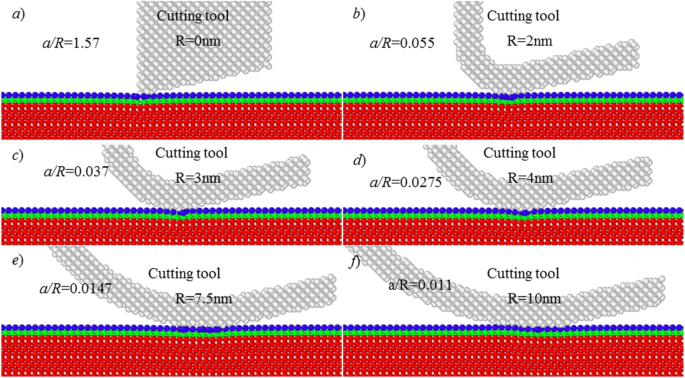
Simulatieresultaten bij een zaagdiepte van 1,1 Å
Ondanks de grotere snijkantstraal, vindt er elastische vervorming plaats op het bewerkte Cu (111) oppervlak. Er is geen spaanvorming en materiaalverwijdering tijdens het snijproces. De studie toont aan dat de snijdiepte groter moet zijn dan ongeveer 1,1 Å om materiaalverwijdering op Cu (111) oppervlak mogelijk te maken.
- b.
De verhouding van a/r w is groter dan C1, maar kleiner dan kritische waarde 2 (C2 ).
Wanneer de zaagdiepte groter is dan ongeveer 1,1 Å, namelijk de verhouding van a/r w groter is dan 0,781, vindt materiaalverwijdering plaats op het werkstukoppervlak. Zoals getoond in figuur 4, wordt een deel van het materiaal verwijderd van het werkstukoppervlak, maar een groter aantal atomen in de bovenste eerste laag blijft op het nieuwe bewerkte oppervlak achter, waardoor oppervlaktedefecten worden gevormd. Bovendien, als de straal van de rand toeneemt tot 7,5 nm, wordt de verhouding van a/R is 0,019. In een dergelijk geval is een deel van de atomen in de eerste atoomlaag in de tweede laag en zelfs in de derde atoomlaag geperst, zoals weergegeven in figuur 4e, wat moet worden toegeschreven aan de extrusie-actie van het snijgereedschap. Het geeft ook aan dat het effect van de gereedschapsrandradius invloed begint te krijgen op het materiaalverwijderingsproces, hoewel een continue materiaalverwijdering niet kon worden verkregen.
- c.
De verhouding van a/r w is groter dan C2 .
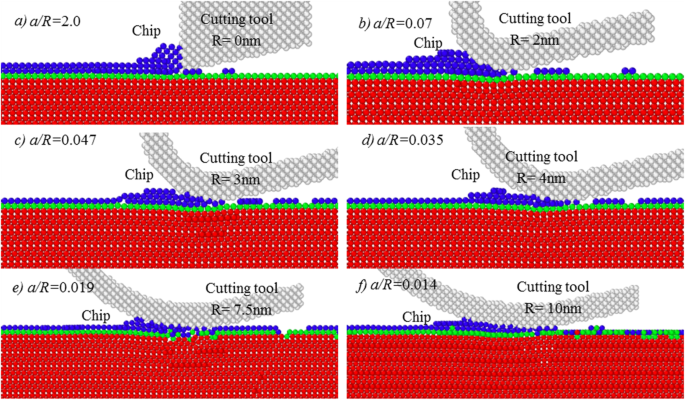
Simulatieresultaten bij een zaagdiepte van 1,4 Å
Figuur 5 toont de spaanvorming bij een snijdiepte van ongeveer 2 Å. Hier de verhouding van a/r w =2 Å/1,28 Å =1,563. Vergeleken met Fig. 3, met een toename van de snijdiepte tot 2 , konden de atomen in de beoogde atoomlaag continu en stabiel worden verwijderd door chipvorming. Het geeft aan dat de snijdiepte groter was dan de minimale chipdikte van monokristallijn koper, en de minimale chipdikte zou kunnen zijn tot een enkele atomaire laag met een snijdiepte van ongeveer 2 Å. Na het snijden werden de materialen in de eerste atoomlaag volledig verwijderd van het werkstukoppervlak.
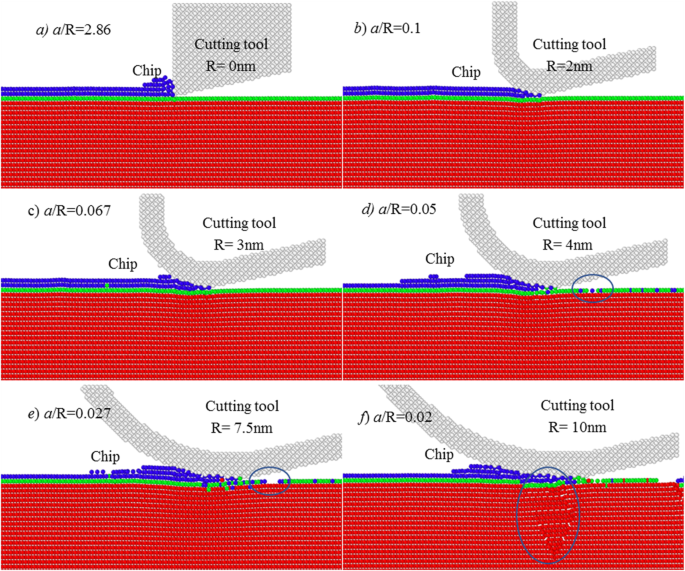
Simulatieresultaten van ACS-snijden op snijdiepte =2 Å
In figuur 5 kan echter ook worden opgemerkt dat door de toename van de verhouding van a/R , ondergaan de atomen in de eerste atoomlaag duidelijk verschillende verwijderingsprocessen, vooral de door snijden veroorzaakte vervorming op het bewerkte oppervlak. Bij de snijdiepte van 2 Å, wanneer scherp snijgereedschap wordt gebruikt, namelijk de verhouding van a/R is 5,70, er treedt slechts een lichte vervorming op op het bewerkte oppervlak. Naarmate de snijkantstraal toeneemt tot 3 nm, wordt de verhouding van a/R is 0,134, de amplitude van elastische vervorming was duidelijk toegenomen.
Wanneer de straal van de gereedschapsrand wordt vergroot tot 4 nm, zoals weergegeven in figuur 5d, zijn veel atomen binnen de beoogde eerste atoomlaag in de tweede atoomlaag geperst, waardoor het nieuwe bewerkte oppervlak wordt gevormd. Bij de gereedschapsrandradius van ongeveer 7,5 nm wordt een deel van de atomen in de eerste laag zelfs verspreid naar de derde atoomlaag. Wanneer de gereedschapsrandradius ongeveer 10 nm bereikt, treedt er een duidelijke elastische en plastische vervorming op, die ook kan worden bepaald in de volgende paragraaf 3.3.
Daarom hangt de op snijden gebaseerde verwijdering van een enkele atomaire laag niet alleen af van de verhouding van a/r w , maar ook de verhouding van a/R . Om verwijdering van een enkele atomaire laag te bereiken door mechanisch snijden, d.w.z. materiaalverwijdering op atomaire schaal, moet rekening worden gehouden met zowel atoomgrootte-effecten als het snijkantstraaleffect, significant verschillend van micro-/nanosnijden en conventioneel snijden op macroschaal.
Oppervlaktegeneratie
Een van de doelstellingen van het verwijderen van atomaire lagen op basis van snijden is het verkrijgen van een defectvrij bewerkt oppervlak met een ideale kristalstructuur. Het atomaire effect van het werkstuk op oppervlaktegeneratie bij ACS-snijden is recentelijk bestudeerd [20]. In de huidige studie worden de oppervlaktetopografie en oppervlaktesamenstelling van het nieuwe bewerkte oppervlak als volgt bestudeerd, om het snijkantstraaleffect op oppervlaktegeneratie bij ACS-snijden duidelijk aan te geven.
Oppervlaktetopografie
Figuur 6 toont de oppervlaktetopografieën van het bewerkte Cu (111)-oppervlak bij verschillende randstralen. Hierbij wordt een snijdiepte van 2 Å aangehouden. Zoals getoond in Fig. 6a, b, wanneer de straal van de gereedschapsrand kleiner is dan 3 nm, kunnen de Cu (111)-oppervlakken met een ideale kristallijne structuur worden verkregen. Wat betreft de defecten aan de linkerkant van het werkstukoppervlak, dit is te wijten aan de vervorming tijdens het snijden van het gereedschap. Tijdens het snijden in een vaste fase wordt er geen oppervlaktedefect gevormd op het bewerkte oppervlak.
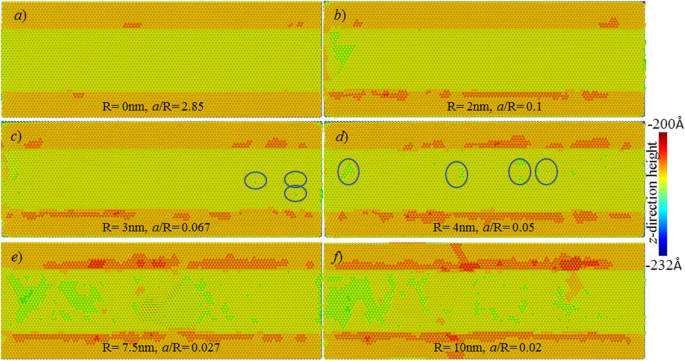
Effecten van gereedschapsrandradius op oppervlaktetopografieën. Atomen zijn gekleurd op basis van hun hoogte in de z-richting
Naarmate de straal van de gereedschapsrand toeneemt, worden echter geleidelijk veel defecten gevormd op het bewerkte oppervlak. Bij de randstraal van 4 nm worden veel putachtige defecten gevormd op het bewerkte oppervlak, zie figuur 6d. Verder, wanneer de straal van de gereedschapsrand gelijk is aan of groter is dan 5 nm, worden er een groot aantal oppervlaktedefecten gevormd, die de oppervlaktekwaliteit ernstig verslechteren. In een dergelijk geval is meer dan één laag atomen verwijderd van het werkstukoppervlak. Daarom kan worden vastgesteld dat bij een snijdiepte van 2 , wanneer de straal van de gereedschapsrand kleiner is dan 3 nm, verwijdering van een enkele atomaire laag kan worden bereikt op het oppervlak van Cu (111). Vanwege het snijkantstraaleffect is de verhouding van de snijdiepte (a ) naar randradius (R ) moet groter zijn dan één drempel om een defectvrij bewerkt oppervlak te bereiken via op snijden gebaseerde verwijdering van een enkele atomaire laag. Hier, de kritische waarde van de verhouding van a/R is [0.05, 0.067].
Oppervlaktesamenstelling
Figuur 7 toont de samenstelling van de bewerkte oppervlakken bij verschillende snijkantradii van het gereedschap en de snijdiepte van 2 Å. Hier zijn groene en blauwe atomen die van de eerste en tweede laag, terwijl de rode atomen die onder de tweede atoomlaag zijn. Zoals getoond in Fig. 7a, wanneer een scherp snijgereedschap wordt gebruikt, is de verhouding van a/R is 2,85, het bewerkte oppervlak bestaat alleen uit atomen in de eerste laag. Dit resultaat geeft aan dat de beoogde eerste atoomlaag grondig van het werkstuk is verwijderd. Bovendien betekent dit dat de materiaalverwijdering laag voor laag wordt uitgevoerd, waarbij de verwijderde materialen alleen afkomstig zijn van de beoogde eerste atomaire laag op het werkstukoppervlak.
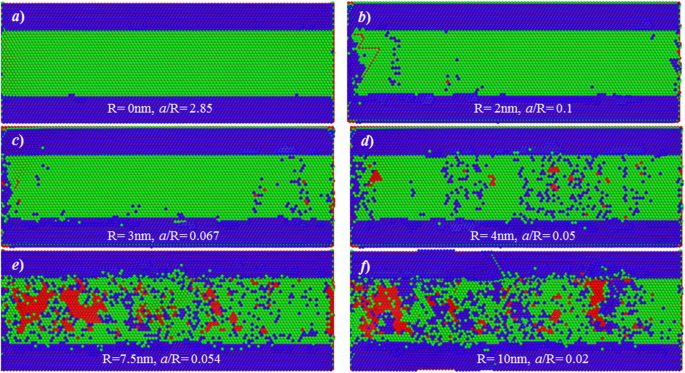
Oppervlaktesamenstelling van bewerkte oppervlakken. Atomen worden gekleurd op basis van het aantal atoomlagen
Wanneer de straal van de gereedschapsrand echter 2 nm en 3 nm is, zoals weergegeven in Fig. 7b, c, zijn de bewerkte oppervlakken samengesteld uit twee atomaire lagen (blauw en groen). Het geeft aan dat hoewel verwijdering van een enkele atoomlaag is bereikt, het proces voor het genereren van het oppervlak minimaal 2 atoomlagen omvat. Verder, wanneer de gereedschapsrandradius groter is dan 4 nm, is er een groot aantal atomen van de eerste atoomlaag op het bewerkte oppervlak, wat aangeeft dat veel atomen in de eerste laag zijn samengeperst om een nieuw oppervlak te genereren.
Daarom is met een toename van de snijkantradius de oppervlaktegeneratie sterk veranderd. Hieronder worden twee soorten mechanismen voor het genereren van oppervlakken samengevat:
- 1.
Laag-voor-laag :de beoogde eerste atomaire laag wordt volledig verwijderd om een nieuw bewerkt oppervlak te genereren. Alleen atomen in de eerste laag worden verwijderd tijdens het snijproces.
- 2.
Verwijderen van meerdere lagen :hoewel verwijdering van een enkele atoomlaag zou kunnen worden gerealiseerd, ondergaan de atomen in de beoogde atoomlaag twee typische verplaatsingsgedragingen. Een deel van de atomen zou tot een chip worden gevormd door door schuifspanning aangedreven dislocatiebeweging, terwijl andere in het bewerkte oppervlak zouden worden geëxtrudeerd onder invloed van een snijgereedschap. Het materiaalverwijderingsproces omvat minimaal twee atomaire lagen.
Ondergronds vervormingsmechanisme
Bij nanocutting is er tijdens het snijproces elastische en plastische vervorming op het bewerkte oppervlak. Nadat het snijgereedschap over het werkstukoppervlak is gegaan, veert het elastische gedeelte terug, terwijl het plastische vervormde deel tot blijvende vervorming zou leiden [1, 2]. Naarmate de snijdiepte afneemt tot atomaire schaal, wordt bij het snijden naar verwijdering van een enkele atoomlaag verondersteld dat er alleen elastische vervorming optreedt op het bewerkte oppervlak. Om dit te verifiëren, worden de vervormingstoestanden van het werkstuk tijdens en na het snijden geanalyseerd. Figuur 8 illustreert de defectstructuren in de ondergrond van het werkstuk bij verschillende snijkantstralen van het gereedschap. Hier worden de atomen gekleurd op basis van centro-symmetrieparameter (CSP) en worden de atomen met een CSP kleiner dan 3 weggelaten, die die met een perfecte FCC-structuur vertegenwoordigen.
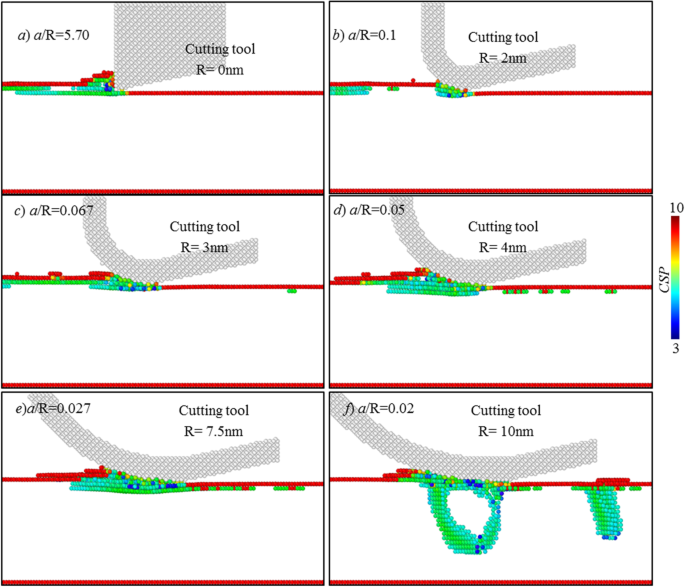
Oppervlaktesamenstelling van de bewerkte oppervlakken. Atomen zijn gekleurd op basis van hun CSP's
Wanneer de snijkantradius kleiner is dan 4 nm, wordt er geen ondergronddefect gevormd in het bewerkte oppervlak. Er is alleen elastische vervorming op het bewerkte oppervlak bij het snijden.
Zoals getoond in Fig. 8, wanneer de snijkantradius gelijk is aan of groter is dan 4 nm, zijn er ondergrondse defecten geïnitialiseerd. Bovendien, naarmate de snijkantstraal groter wordt, neemt het aantal ondergrondse defecten aanzienlijk toe. Wanneer de randradius ongeveer 10 nm bereikt, is er één dislocatielus gevormd en deze kon niet verdwijnen na het snijden, zoals weergegeven in figuur 9e. Het geeft duidelijk de plastische vervorming aan die optreedt op het bewerkte oppervlak.
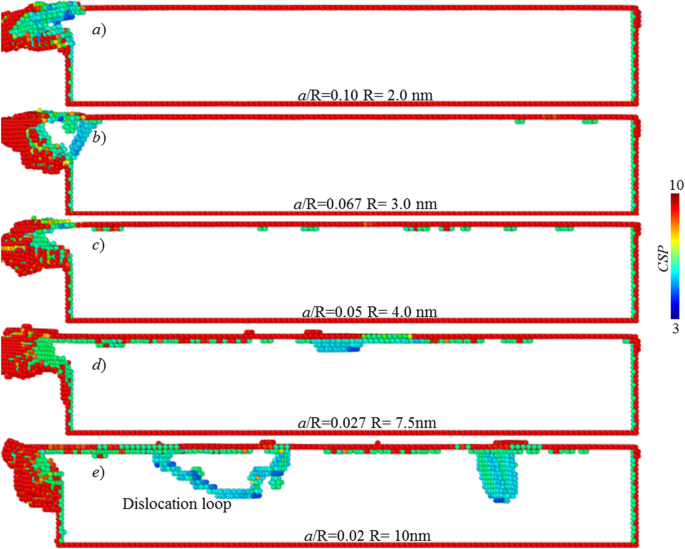
Ondergrondse defecten bij verschillende snijkantradii van het gereedschap. Atomen zijn gekleurd op basis van hun CSP's
Nadat het gereedschap over het werkstukoppervlak is gegaan, zou het elastisch vervormde gedeelte terugveren; zo worden delen van ondergrondse defecten vernietigd. Zoals weergegeven in Fig. 9a-c, was er ten slotte geen ondergronds defect, wanneer de gereedschapsrandradius 2 nm of 3 nm is.
Het plastisch vervormde gedeelte leidt tot een blijvende vervorming. Zoals getoond in Fig. 9, wanneer de gereedschapsrandradius 7,5 nm is, blijft er een klein aantal ondergrondse defecten over. Wanneer de gereedschapsrandradius 10 nm is, zijn de dislocatielus en stapelfout eindelijk aanwezig in de ondergrond van het werkstuk.
Op basis van bovenstaande analyse kan worden geconcludeerd dat om op snijden gebaseerde verwijdering van een enkele atomaire laag mogelijk te maken, plastische vervorming moet worden vermeden en dat alleen elastische vervorming op het verwerkte oppervlak is toegestaan. Het wordt beschouwd als een kenmerkend kenmerk van het op snijden gebaseerde proces voor het verwijderen van een enkele atomaire laag.
Atoomverplaatsingsgedrag
Volgens MD-trajectbestanden heeft dislocatiebeweging het op snijden gebaseerde verwijderingsproces van een enkele atomaire laag gedomineerd. Afbeelding 10 toont de simulatieresultaten met verschillende gereedschapsrandradiussen. Bij de randradius van 2 nm, onder invloed van het snijgereedschap, wordt alleen de eerste atomaire laag in de snijrichting geschoven om een chip te vormen, terwijl andere geïmmobiliseerd blijven. Het kan worden beschouwd als één dwarsdoorsnede van één randdislocatie.
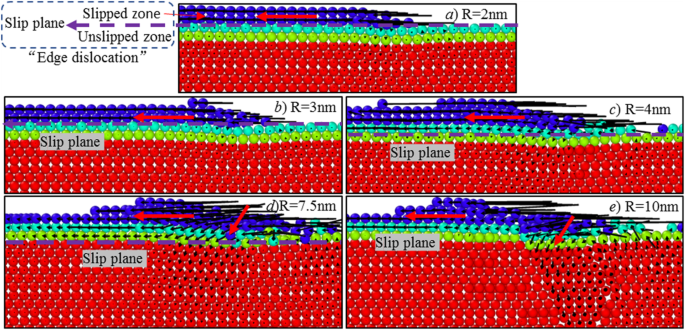
Atoomverplaatsingsgedrag bij verschillende geavanceerde radius
Naarmate de straal van de gereedschapsrand toeneemt, is een deel van het materiaal in de eerste atomaire laag in het bewerkte oppervlak gedrukt, waardoor de atomaire lagen onder de eerste laag gaan slippen. Bovendien, naarmate de straal van de gereedschapsrand toeneemt, heeft het aantal atomaire lagen die een materiaalslipproces ondergaan de neiging om te groeien. Wanneer de gereedschapsrandradius 4 nm is, behalve de eerste atomaire laag, geleidt de tweede atomaire laag ook materiaalslip langs de snijrichting, zoals geïllustreerd in Fig. 10. Wanneer de gereedschapsrandradius 7,5 nm is, terwijl het snijgereedschap voortbeweegt, de bovenste drie atomaire lagen op het werkstukoppervlak zijn in de snijrichting geschoven. Verder, wanneer de gereedschapsrandradius wordt vergroot tot 10 nm, is een groot aantal materialen geperst om een nieuw bewerkt oppervlak te vormen; er treedt plastische vervorming op (zie afb. 10e) op het werkstukoppervlak, die ook in afb. 9 kan worden bepaald.
Figuur 11 toont het slipproces van de beoogde atomaire laag langs de snijrichting. Het gebied van de slipzone wordt voortdurend vergroot terwijl het snijgereedschap naar voren beweegt. Bij de snijafstand van 17,5 nm heeft de slipzone een maximale waarde bereikt. Vervolgens worden de materialen in de slipzone continu tot spaanders gevormd; het volume van de chip is ook verhoogd.
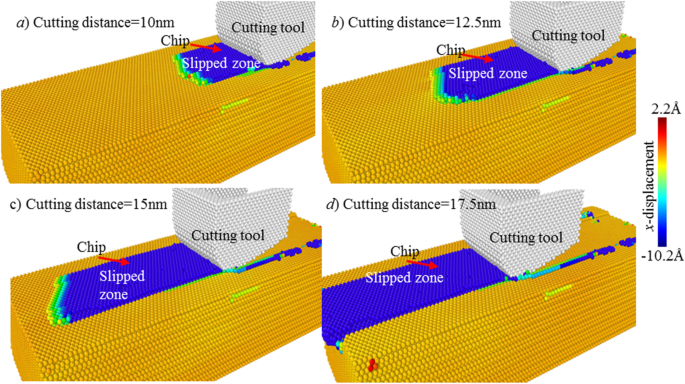
Slipproces van de beoogde atomaire laag bij een snijkantstraal van 2 nm. Atomen zijn gekleurd op basis van hun atomaire verplaatsingswaarden in de x-richting
Over het algemeen zijn, zoals blijkt uit de analyse in secties 3.3 en 3.4, naarmate de straal van de gereedschapsrand toeneemt, zowel het ondergrondse vervormingsmechanisme als het atomaire verplaatsingsgedrag sterk veranderd. Bij verschillende snijkantstralen van het gereedschap hebben verschillende aantallen atomaire lagen de neiging om langs de snijrichting te glijden, terwijl verschillende vervormingsregimes optreden op het bewerkte oppervlak, zoals samengevat in tabel 2. Bovendien kan worden gevonden dat in de op snijden gebaseerde verwijdering van een enkele atomaire laag proces, wordt de chipvorming bepaald door door schuifspanning aangedreven dislocatiebeweging, die aanzienlijk verschilt van de chipvorming bij conventioneel snijden en nanosnijden. Het kan ook worden beschouwd als een kenmerkend kenmerk van op snijden gebaseerde verwijdering van een enkele atomaire laag.
Snijkracht
Invloed van Edge Radius-effect
Afbeelding 12 toont het effect van de snijkantstraal op de gemiddelde snijkrachten bij een snijdiepte van 2 Å. Hier de tangentiële en normale componenten van snijkrachten, namelijk F t en F n , worden vergeleken. Zoals geïllustreerd, voor een scherp snijgereedschap, is de verhouding van a/R is 2,85, en de F t van 16,4 nN is duidelijk kleiner dan F n van 23,7 nN. Naarmate de snijkantstraal van het gereedschap toeneemt, worden beide F t en F n zijn vergroot. Echter, de F n heeft veel grotere groeiamplitudes vertoond dan F t . Het geeft duidelijk aan dat naarmate de straal van de gereedschapsrand toeneemt, de normale snijkracht een groter effect zou hebben op het materiaalverwijderingsproces bij het ACS-snijproces. Wanneer de straal van de gereedschapsrand echter groter is dan ongeveer 3 nm, kon verwijdering van een enkele atomaire laag niet worden bereikt. Een grotere normale snijkracht zou dus niet nuttig zijn om op snijden gebaseerde verwijdering van een enkele atomaire laag mogelijk te maken, en bij voorkeur zou een lagere normale snijkracht moeten worden aangenomen.
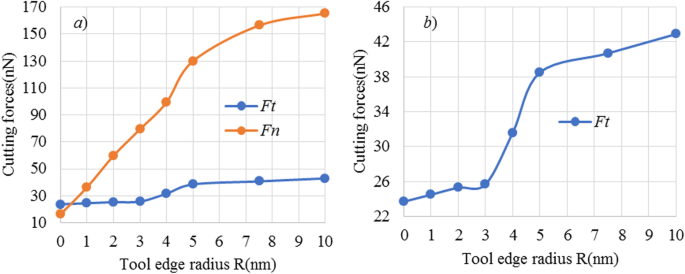
Plot van snijkrachten versus snijkantradius bij snijdiepte van 2 Å
Aangezien de normale snijkrachten de drukspanning leveren om elastische en/of plastische vervorming op het bewerkte oppervlak mogelijk te maken, zouden de tangentiële snijkrachten de afschuifspanning leveren aan de spaanvorming. Daarom kan worden geconcludeerd dat spaanvorming bij het verwijderen van een enkele atomaire laag op basis van snijden voornamelijk moet worden aangedreven door de tangentiële snijkracht. In Fig. 12b is ook te zien dat de F t heeft drie soorten veranderingen vertoond, die verder leiden tot verschillende oppervlaktetopografieën (zie Fig. 6), waaronder de volgende:
Wanneer de gereedschapsrandradius kleiner is dan ongeveer 3 nm, namelijk de verhouding van a/R is 0,067, de F t blijft ongeveer ongewijzigd en is altijd kleiner dan 25 nN, naarmate de randstraal groter wordt. In dat geval wordt slechts één atomaire laag van het werkstukoppervlak verwijderd.
Wanneer de gereedschapsrandradius 3 nm en 5 nm is, zijn de verhoudingen van a/R zijn 0,04 en 0,067, terwijl F t is duidelijk verhoogd tot ongeveer 38,5 nN. Dientengevolge wordt meer dan één atomaire laag van het werkstukoppervlak verwijderd, maar er wordt een klein aantal oppervlaktedefecten gevormd.
Wat betreft de randradius groter dan 5 nm, F t convergeert ook geleidelijk naar een constante waarde. In dit geval wordt meer dan één atoomlaag verwijderd. Er worden echter grote aantallen oppervlaktefouten gevormd op het werkstukoppervlak en de ondergrond.
Er kan worden geconcludeerd dat een zeer lage tangentiële snijkracht het mogelijk zou maken om op snijden gebaseerde enkelvoudige atomaire laag te verwijderen met een redelijke snijrandstraal, zoals 2 nm. Op zijn beurt kon de verwijdering van een enkele atomaire laag niet worden gerealiseerd, ondanks de grotere tangentiële snijkracht.
Invloed van het atoomformaateffect
Figuur 13 geeft verder de grafiek van snijkrachten versus snijdiepte bij een snijkantradius van 2 nm. Er kan worden vastgesteld dat bij de snijkantradius van 2 nm, naarmate de snijdiepte toeneemt, zowel de normale snijkracht als de tangentiële snijkrachten veranderingen in drie fasen hebben ondergaan. Er zijn duidelijke veranderingen bij een snijdiepte van ongeveer 1,1 Å en 1,6 Å. De corresponderende verhouding van zaagdiepte (a ) naar atomaire straal van het werkstuk (r w ) zijn 0,055 en 0,080, de bovengenoemde twee kritische waarden van a/r w , C1 en C2, zoals weergegeven in Sectie 3.1.
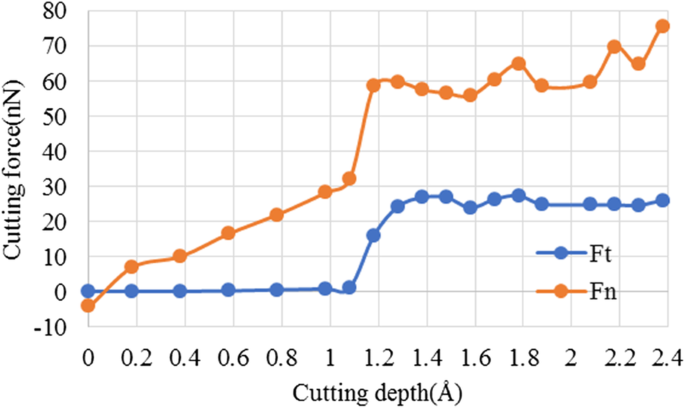
Plot of cutting forces versus cutting depth at edge radius of 2 nm
When cutting depth is smaller than 1.1 Å, namely, the ratio of a/r w is less than 0.055, F t is always 0 nN, while F n is linearly increased to about 32 nN. However, the cutting forces could not enable plastic material deformation and removal on the workpiece surface. Consequently, there is only elastic deformation on workpiece surface, as shown in Fig. 3.
When the cutting depth is larger than 1.1 Å, but smaller than 1.6 Å, the ratio of a/r w is more than 0.055 but less than 0.080. If this case, F t has greatly increased from 0 nN to about 25 Nn, while F n further increased to about 58 nN. The cutting forces are larger enough to enable material removal on workpiece surface. At the cutting depth of 1.4 Å, there is chip formation and material removal on workpiece surface. But the stable and continuous material removal could not be realized and many defects are formed on the processed surface, as shown in Fig. 4.
When the cutting depth is larger than 1.6 Å, both F t en F n are large enough to enable continuous material removal on workpiece surface. Consequently, chip is stably formed over the workpiece surface, and the targeted atomic layer is continuously removed via chip formation, forming a new processed surface, as shown in Fig. 5b and Fig. 6b.
Overall, both cutting-edge radius effect and atomic sizing effect have an influence on cutting force in cutting-based single atomic layer removal process, thereby changing the material removal and surface generation process.
Discussions About Cutting-Based Single Atomic Layer Removal Mechanism
As per above analysis, both atomic sizing effect and cutting-edge radius effect have a great influence on the cutting-based single atomic layer removal mechanism. As summarized in Table 3, depending on the ratio of cutting depth to workpiece atomic radius(a/r w ) and the ratio of cutting depth to edge radius(a/R ), there are minimum 5 typical cases of material deformation and removal behaviours in cutting-based single atomic layer removal process. In this section, the fundamental material deformation and removal mechanism of each case is summarized.
In conventional machining, as cutting depth is significantly larger than the cutting-edge radius, the cutting-edge radius effect can be ignored. As the cutting depth is decreased to nanoscale, which is comparable or lower than the edge radius, the edge radius effect can be no longer ignored. In nanocutting, the material removal process is dominated by the extrusion deformation, which is greatly influenced by cutting-edge radius. As the cutting depth is further decreased to atomic scale, except for cutting-edge radius effect, a new sizing effect, atomic sizing effect [20] has a great influence on material removal.
As shown in Fig. 14, in the cutting-based single atomic layer removal process, there are two portions involving in cutting, i.e., nanometric cutting edge and the lowest cutting tool atoms (B ). Such two portions could be coupled to enable single atomic layer removal. The size of cutting edge, regarded as ‘nano-tool,’ is described by edge radius (R ). The cutting edge is the envelope curve of the outermost atoms in cutting tool. Regarding the lowest atoms, as ‘atomic-tool,’ it is described by workpiece atomic radius (r w ). The cutting-based single atomic layer removal is the results of the coupled actions of nano-tool and atomic-tool on workpiece material.
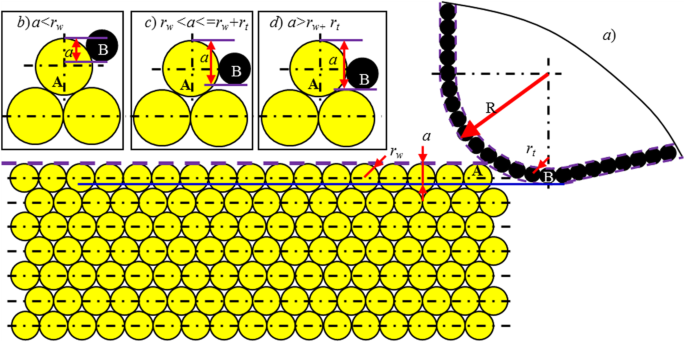
Schematic diagram for cutting-based single atomic layer removal
Firstly, depending on the ratio of cutting depth (a ) to the workpiece atomic radius (r w ), i.e., a/r , there are three kinds of material deformation behaviour in ACS cutting process.
- 1.
The ratio of a/r w is smaller than critical value 1(C1 ).
As shown in Fig. 15, chip formation does not occur, but elastic deformation does occur on the workpiece surface. During cutting process, after workpiece passes the lowest point of cutting tool, the elastically deformed part would recover completely. Consequently, no material deformation and removal occurred on the topmost surface. In such case, the tool edge effect could be ignored. This ratio could be affected by material properties (case 1).
- 2.
The ratio of a/r w is larger than C 1 , but smaller than critical value 2 (C2 ).
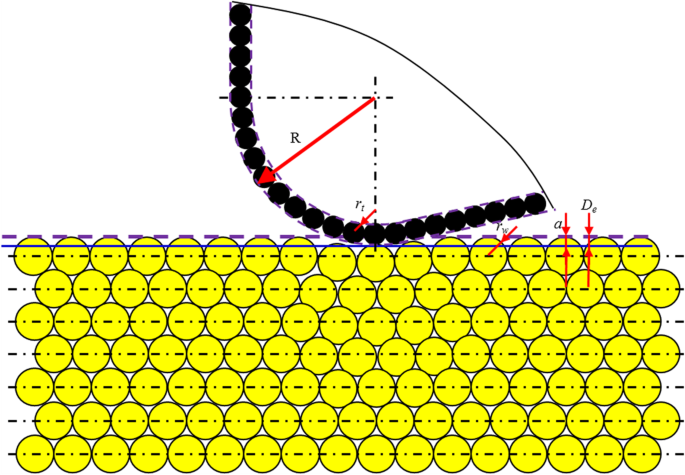
Schematic illustration of cutting-based single atomic layer removal at the ratio of a/rw smaller than C1
As the ratio of the cutting depth to atomic radius (a/r w ) increases to be larger than C1 but smaller than critical value 2(C2 ), there is material removal on the workpiece surface, but it is noncontinuous. In such case, only part of material within targeted atomic layer is formed into chip by shear stress-driven dislocation motion, while others are remained on the workpiece surface. When cutting tool passes over the workpiece surface, the surface quality of the processed surface is seriously deteriorated (case 2) (Fig. 16).
- 3.
The ratio of a/r w is larger than critical value 2 (C2 ).
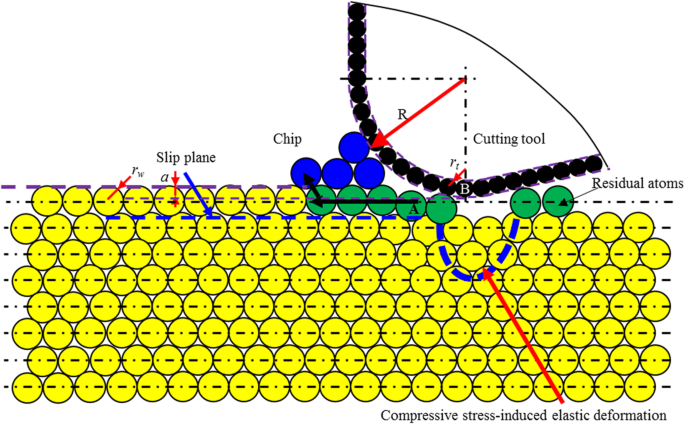
Schematic illustration of cutting-based single atomic layer removal at a/rw larger than C1 and smaller than C2
When the ratio of cutting depth to atomic radius (a/r w ) increases to be larger than critical value, there is a continuous material removal by chip formation during cutting process. In such case, the edge radius effects can no longer be ignored. For ACS cutting process, the maximum cutting depth is subnanometer order. At such extremely low cutting depth, regardless of the nominal rake angle, the effective rake angle is always largely negative. The negative rake face can produce the necessary shear stress to enable chip formation by dislocation motion and the compressive force to enable the elastic and/or plastic deformation on the processed surface.
Depending on the ratio of cutting depth (a ) to tool edge radius (R ), different kinds of elastic and/or plastic deformation process occur on the workpiece surface. There are two threshold values of a/R , namely, threshold value 1 (T 1 ) and threshold value 2 (T 2 ), leading to different material removal processes.
- a.
The ratio of a/R is larger than threshold (T 1 ).
As shown in Fig. 17, there is one atomic slip plane. The workpiece material below this plane would have an elastic deformation. As for the materials above this slip plane, it undergoes a plastic deformation by dislocation motion. A part of materials is also formed into chip by shearing stress-driven dislocation motion, while the other undergoes dislocation slip. After the workpiece passes the lowest point of the cutting tool, the elastically deformed part recovers completely (case 3).
- b.
The ratio of a/R is lower than threshold 1 (T 1 ), but larger than threshold 2 (T 2 ).
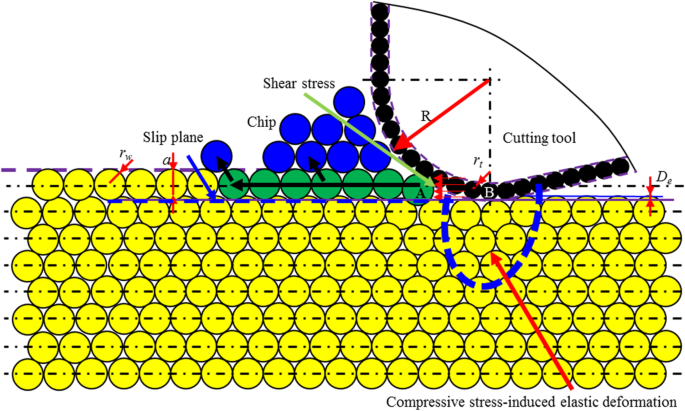
Schematic illustration of cutting-based single atomic layer removal at a/rw larger than C2 and a/R larger than T1
Under the action of cutting edge, minimum two atomic layers undergo dislocation slip, while elastic deformation occurs on the processed surface, as shown in Fig. 18. The cutting edge provides a force to generate the shear stress to enable chip formation by dislocation motion and compressive stress to induce elastic deformation on the processed surface. In such case, part of material within the targeted atomic layer is formed into chip by dislocation motion, while the other is extruded into other atomic layers to form new processed surface. It also drives the slip of other atomic layers on the workpiece surface, leading to the negative dislocation climb. After workpiece material passes the lowest point of the cutting tool, the elastic portion springs back (case 4).
- c.
The ratio of a/R is lower than threshold 2 (T 2 ).
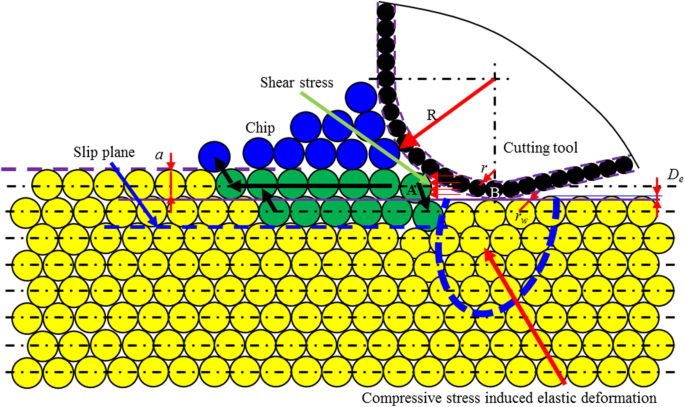
Schematic illustration of cutting-based single atomic layer removal at a/rw larger than C2 , a/R larger than T2 , smaller than T1
As the ratio of a/R decreases to lower than T 2 , there is either no chip formation or extremely small volume of chip formation, but elastic-plastic deformation occurs on the processed surface, as shown in Fig. 19. After workpiece material passes the lowest point of cutting edge, the elastic deformed part springs back. The plastic deformed part (Δ ) leads to lasting deformation. Such ratio is related with material properties, tool geometry and process conditions (case 5).
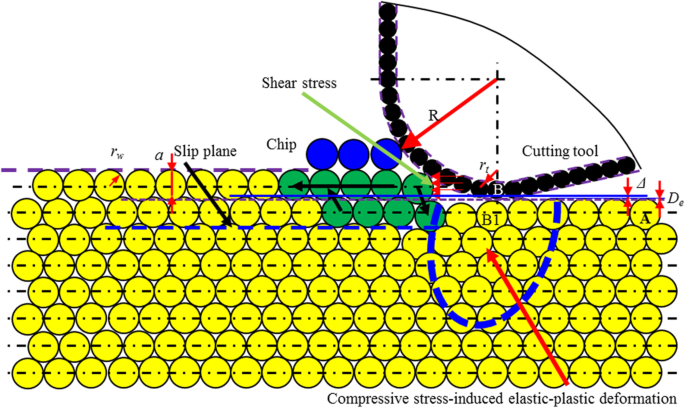
Schematic illustration of cutting-based single atomic layer removal at a/r larger than C2 and a/R lower than T2
Conclusies
In the present study, both of atom sizing effect and cutting-edge radius effect are analysed to investigate their influence on chip formation, surface generation, subsurface deformation, and atomic displacement behaviour during the cutting of monocrystalline copper towards single atomic layer removal. The following conclusions can be drawn.
- 1.
A new model is proposed to describe the underlying material deformation and removal mechanism in the cutting-based single atomic layer removal process, which exhibits four characteristics, including chip formation by dislocation motion, elastic deformation occurring on the processed surface, atomic sizing effect, and cutting-edge radius effect.
- 2.
Both of atomic sizing effect and cutting-edge radius effect have a great influence on the material deformation and removal during the cutting process of monocrystalline copper towards single atomic layer removal. With a specific ratio of cutting depth to workpiece atom radius (a/r w ) and that of cutting depth to edge radius (a/R ), cutting-based single atomic layer removal could be achieved on Cu (111) surface.
- 3.
Chip formation is affected by the ratios of a/r w and a/R . There is a chip formation only when the ratio of a/r w is larger than one critical value (C1) and the ratio of a/R is smaller than one threshold value (T1). Moreover, chip formation is mainly dependent on the shear stress-driven dislocation motion, significantly different from the extrusion-dominated chip formation in nanocutting and shearing-dominated chip formation in conventional machining.
- 4.
Single atomic layer removal can be achieved via layer-by-layer removal and multi-layer removal. The former one refers to that the targeted atomic layer could be either fully removed from workpiece surface. The latter one means that the first atomic layer is partly removed while the remaining materials are pressed into other atomic layers, forming a new processed surface.
- 5.
There is only elastic deformation occurring on the processed surface during ACS cutting process, different from the elastic-plastic deformation in nanocutting. It can be regarded as one characteristic feature in ACS cutting.
- 6.
Depending on the combined effect of atom sizing effect and cutting-edge radius effect, there exist five cases of material deformation and removal processes during the cutting-based single atomic layer removal, i.e., no workpiece material is removed (case 1), workpiece materials are non-continuously removed (case 2), a part of materials is formed into chip while others undergoes material slip via dislocation motion (case 3), a part of materials within the targeted atomic layer is formed into chip while others are extruded into other atomic layers to form new processed surface (case 4), and the elastic deformed part springs back, while the plastic deformed part leads to a lasting deformation (case 5).
Beschikbaarheid van gegevens en materialen
Authors declare that the materials, data, and associated protocols are available to the readers, and all the data used for the analysis are included in this article.
Afkortingen
- ACS:
-
Atomic and close-to-atomic scale
- ACSM:
-
Atomic and close-to-atomic scale manufacturing
- MD:
-
Moleculaire dynamiek
Nanomaterialen
- Geavanceerde atoomlaagdepositietechnologieën voor micro-LED's en VCSEL's
- Synergistische fotokatalytische adsorptieverwijdering van het basismagenta-effect van AgZnO/polyxometalaten nanocomposieten
- De antibacteriële polyamide 6-ZnO hiërarchische nanovezels vervaardigd door afzetting van atoomlagen en hydrothermische groei
- Fotokatalytische eigenschappen van Co3O4-gecoate TiO2-poeders bereid door plasma-versterkte afzetting van atoomlagen
- Fermi-niveau-afstemming van ZnO-films door middel van supercyclische atoomlaagafzetting
- Onderzoek naar het effect van het beïnvloeden van richting op het schurende nanometrische snijproces met moleculaire dynamiek
- Afhankelijkheid van dikte van grensvlak- en elektrische eigenschappen in atoomlaag afgezet AlN op c-vlak GaN
- Atomaire laagafzetting bij lage temperatuur van SiO2 met behulp van koolstofdioxide
- silicium nanodraad heterojunctie zonnecellen met een Al2O3 passiveringsfilm vervaardigd door atoomlaagafzetting
- TiO2-nanomembranen vervaardigd door atomaire laagafzetting voor supercondensatorelektrode met verbeterde capaciteit
- Enkel verstek zagen vergeleken met dubbele verstekzaag