Het gebruik van visuele inspectie bij activabeheer en kwaliteitscontrole
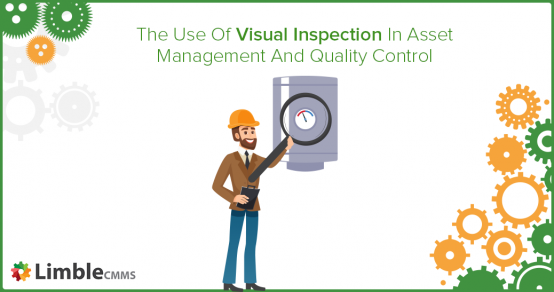
Visuele inspectie is een veel voorkomende techniek die wordt gebruikt door onderhoudsprofessionals bij fysiek asset management, evenals de laatste stap in de productielijn van verschillende goederen.
Terwijl ingenieurs voortdurend nieuwe manieren vinden om veelgebruikte repetitieve handelingen te automatiseren, bleken visuele inspecties in dat opzicht behoorlijk veerkrachtig, vooral op het gebied van apparatuuronderhoud.
In dit bericht proberen we visuele inspectie vanuit verschillende gezichtspunten te begrijpen. We bespreken zowel de basis als moderne use cases. Aangezien visuele inspectie wisselende resultaten kan opleveren vanwege de subjectieve aard, zullen we de zaken afronden met een overzicht van de stappen die u kunt nemen om het inspectieproces te standaardiseren.
De definitie van een visuele inspectie
Visuele inspectie is een zeer eenvoudige inspectiemethode die wordt gebruikt bij de kwaliteitscontrole van de productie en het onderhoud van activa. Het is de methode om gebreken of onvolkomenheden op te sporen met het blote oog en niet-gespecialiseerde inspectieapparatuur.
Vaak is er geen empirische formule voor het vinden van defecte producten of het inspecteren van een apparaat. Daarom speelt de ervaring van de persoon die visuele inspectie uitvoert een belangrijke rol bij het bepalen van de doeltreffendheid van het proces.
Het zoeken naar afwijkingen met het blote oog is de meest gebruikelijke methode van visuele inspectie. Maar het is niet noodzakelijkerwijs daartoe beperkt. Het gebruik van andere zintuigen voor inspectie valt ook onder de brede paraplu van visuele inspectie. Het basisprincipe is dat een ervaren persoon zijn zintuiglijke vermogens gebruikt om problemen te identificeren met objecten die ze inspecteren.
Ervaren professionals kunnen bijvoorbeeld de kwaliteit van materialen als hout en metaal beoordelen door het geluid dat ze produceren te beoordelen. Ze kunnen gewoon op het object kloppen en een oordeel vellen op basis van het geluid dat het produceert.
Op dezelfde manier kan een onderhoudstechnicus ruiken een gaslek, hoor dat er iets los zit in de asset, of zelfs voelt dat een apparaat meer trilt dan zou moeten of overmatige hitte uitstraalt. Allemaal tijdens het uitvoeren van een visuele inspectie .
Visuele inspecties bij fysiek asset management
Visuele inspectie is een integraal onderdeel van fysiek asset management. Onderhoudsprofessionals gebruiken het dagelijks als onderdeel van hun routine-onderhoudsactiviteiten.
Af en toe zal een organisatie machinebedieners opleiden om visuele inspecties uit te voeren in plaats van onderhoudstechnici. Deze praktijk wordt gewoonlijk autonoom onderhoud genoemd.
Regelmatige inspecties helpen onderhoudsteams om tekenen van slijtage op te sporen die tot apparatuurstoringen kunnen leiden. Kleine mankementen worden ter plaatse verholpen als de monteur de beschikking heeft over de juiste gereedschappen en onderdelen. Anders laten ze een notitie achter over het gedetecteerde probleem. De onderhoudsmanager of supervisor voegt later een nieuwe taak toe aan het preventief onderhoudsplan, zodat het probleem niet onopgelost blijft.
Hoewel ze erg handig kunnen zijn, hebben visuele inspecties een aantal nadelen. Machines moeten vaak worden stilgelegd zodat een monteur een visuele inspectie kan uitvoeren. Zoals u zich kunt voorstellen, vermindert dit de uptime van de apparatuur en kan dit nadelige gevolgen hebben voor de bedrijfsresultaten. Het andere probleem is dat visuele inspecties het probleem soms te laat kunnen ontdekken. Als u geluid, hitte of rook waarneemt, is de storing mogelijk al aan de gang.
Om deze problemen aan te pakken, gebruiken steeds meer organisaties sensoren en apparatuur voor conditiebewaking om de gezondheid en prestaties van activa in realtime te bewaken. Deze technologie stelt hen in staat om tekenen van verslechtering veel eerder op te merken dan anders mogelijk zou zijn. Dit wordt netjes weergegeven in de onderstaande afbeelding.
Met deze sensoren kunnen organisaties geavanceerde onderhoudsstrategieën uitvoeren, zoals condition-based onderhoud en predictief onderhoud. Dergelijke strategieën verminderen de noodzaak van visuele inspecties, maar maken ze verre van achterhaald. Sensoren zijn nog vrij duur en kunnen alleen specifieke tekenen van verslechtering detecteren. Het betekent dat handleiding testmethoden zoals visuele inspecties zijn niet alleen noodzakelijk, maar ook een meer kosteneffectieve optie, vooral voor goedkope activa.
Visuele inspecties bij kwaliteitscontrole
Visuele inspectie is de oudste niet-destructieve testmethode (NDT) voor kwaliteitscontrole. In zijn oorspronkelijke vorm wordt visuele inspectie gebruikt om het oppervlak van een object te observeren en te zoeken naar scheuren, krassen, verkeerde uitlijning, corrosie en andere fysieke defecten.
Grote merken, vooral die die dure producten produceren, hebben veel te verliezen als ze een hele reeks defecte producten op de markt brengen. Visuele inspectie is een geweldige manier om items met duidelijke gebreken snel uit te filteren.
Autofabrikanten zoals Rolls-Royce hechten bijvoorbeeld extreem veel belang aan de pasvorm en afwerking van elk onderdeel dat in hun auto's wordt gebruikt. Uit hun interne onderzoek blijkt hoe ongeveer 70% van alle defecte componenten worden afgewezen vanwege afwijkingen gevonden tijdens visuele inspectie .
Dit wil niet zeggen dat visuele inspecties alleen voorbehouden zijn aan luxegoederen. Een goed tegenvoorbeeld komt uit de voedingsmiddelen- en drankenindustrie. Hier worden visuele inspecties uitgevoerd om er zeker van te zijn dat er geen vreemde voorwerpen in het product zitten, dat de verpakkingen uniform en goed afgesloten zijn en dat de producten niet verkeerd geëtiketteerd zijn. Vanwege het vrij eenvoudige karakter van deze inspecties, beginnen veel voedselproducenten machine vision-systemen te gebruiken voor kwaliteitscontrole.
Een voorbeeld van een geautomatiseerd visueel inspectiesysteem ( Afbeeldingsbron )
In het algemeen kan visueel testen voor kwaliteitscontrole op drie verschillende manieren worden gedaan:
- Willekeurige steekproeven: Kwaliteitscontroles worden uitgevoerd op willekeurig geselecteerde producten. Producten kunnen direct aan de productielijn worden gecontroleerd op duidelijke visuele gebreken. Complexere inspecties (zoals het testen van het interieur van een product) worden meestal uitgevoerd in speciale testruimtes.
- Volledig handmatige bemonstering: Alle producten worden handmatig gecontroleerd. Dit kan fysiek zwaar werk zijn met veel repetitieve handelingen. Om de gezondheid en productiviteit van de werknemers die de inspecties uitvoeren te maximaliseren, moeten organisaties ernaar streven de nodige hulpmiddelen en ergonomische uitrusting te leveren.
- Geautomatiseerde visuele inspectie: Producten worden geïnspecteerd met behulp van camera's, beeldverwerkingsmethoden en machine learning-algoritmen. Meer hierover verderop in het artikel.
De geautomatiseerde systemen voor visuele inspectie lijken meer grip te krijgen naarmate de particuliere sector branchespecifieke oplossingen ontwikkelt. Het valt nog te bezien hoe snel fabrikanten deze technologie zullen adopteren.
Moderne visuele inspectietechnieken
Incrementele technologische verbeteringen in camerakwaliteit en machine learning beginnen onze manier van denken over visuele inspecties te veranderen. Onderhoudstechnici hebben nu de mogelijkheid om visuele inspecties uit te voeren op gevaarlijke en moeilijk bereikbare plaatsen, terwijl ze mijlenver verwijderd zijn van de objecten die ze inspecteren. Kwaliteitscontrolespecialisten hebben daarentegen steeds meer toegang tot geautomatiseerde visuele inspectieoplossingen.
Visuele inspecties op afstand voor onderhoud van bedrijfsmiddelen
Tegenwoordig kunnen technici robots en drones gebruiken om anders ontoegankelijke gebieden te bekijken. We hebben het over het inspecteren van objecten op grote hoogte, zeer kleine ruimtes, gevaarlijke plaatsen zoals opslagtanks en dergelijke.
Afbeeldingen of video's kunnen vanaf een externe locatie worden bekeken, zelfs duizenden kilometers verwijderd van de locatie van de inspectielocatie - vandaar de naam visuele inspectie op afstand. De vastgelegde gegevens zijn op twee verschillende manieren toegankelijk:
- Livestream: Robots of drones kunnen gegevens van de locatie doorgeven aan het basisstation waar de inspecteur de live feed kan bekijken. In dit geval kan de robot of drone ook vanaf de remote terminal worden bestuurd. Het kan alleen worden gebruikt in gevallen waarin er constante draadloze communicatie is tussen de apparatuur die wordt gebruikt en het basisstation.
- Opgeslagen gegevens :In extreem afgelegen of gevaarlijke gebieden waar geen draadloze communicatie mogelijk is, worden video's en afbeeldingen opgeslagen en later geanalyseerd.
Een bijkomend voordeel van dit soort inspecties is dat de afbeeldingen en video's eenvoudig kunnen worden gedeeld tussen technici en andere relevante teamleden, zonder dat ze fysiek aanwezig hoeven te zijn op de inspectielocatie. Deze samenwerking kan zeer nuttig zijn bij het oplossen van complexe problemen of wanneer er behoefte is aan contact met gespecialiseerde experts.
Geautomatiseerde visuele inspecties (AVI) voor massaproductie
Geautomatiseerde visuele inspectie (AVI) gebruikt computervisie en kunstmatige intelligentie om visuele inspecties op producten uit te voeren in plaats van kwaliteitsinspecteurs. Deze technologie heeft tot doel de behoefte aan menselijke tussenkomst voor inspectie in grootschalige geautomatiseerde fabrieken drastisch te verminderen.
Cognitieve visuele inspectie-oplossing van IBM ( Afbeeldingsbron )
Foxconn, een van de grootste elektronicafabrikanten ter wereld, gebruikt AVI in hun productiefaciliteiten. We zullen ze als voorbeeld gebruiken om kort te beschrijven hoe deze technologie zou moeten werken.
Stel dat Foxconn moederborden maakt voor de nieuwste iPhone. Een ideaal voorbeeld van het moederbord wordt gemaakt en geïnspecteerd door een menselijke visuele inspecteur. Na goedkeuring wordt dit model geüpload naar de database en kan het algoritme het als benchmark gebruiken. Enkele voorbeelden van defecte modellen worden ook naar de server geüpload en gebruikt om algoritmen te leren specifieke afwijkingen te herkennen.
De rest van de moederborden komt uit de geautomatiseerde assemblagelijn en gaat onder de camerasystemen voor de AVI door. Meerdere afbeeldingen van het product worden vanuit verschillende hoeken vastgelegd. De vastgelegde afbeeldingen worden vergeleken met de benchmarkafbeeldingen die zijn opgeslagen met behulp van machine learning-algoritmen. Enkele van de vergeleken factoren kunnen zijn:
- grootte en vorm van verschillende elementen
- soldeerlocaties
- componentenlocaties
- ontbrekende componenten
- connectoren
- kleurafwijkingen
Het product komt door de keuring als het voldoende dicht bij de benchmark ligt.
Op het eerste gezicht lijkt deze technologie een perfecte oplossing. Het belangrijkste idee achter automatisering is immers om routinematige en alledaagse taken over te laten aan machines, zodat werknemers zich kunnen concentreren op creatieve probleemoplossing. Het is een goed idee, maar er zijn nog veel beperkingen die moeten worden aangepakt voordat het een standaard wordt in de industriële ruimte.
De beperkingen van geautomatiseerde oplossingen
Er zijn twee belangrijke belemmeringen voor de invoering van automatisering bij visuele inspectie.
De eerste zijn technologische beperkingen . Hoewel AI-onderzoekers grote vooruitgang hebben geboekt, zijn de inspectie-algoritmen verre van perfect. Ze hebben veel voorbeelden nodig van goede en defecte producten, zodat ze kunnen leren hoe ze verschillende afwijkingen met voldoende succes kunnen detecteren. Bovendien vinden machines het moeilijk om met reflecterende oppervlakken te werken. Dit zou het werken met de meeste metalen in een fabriek elimineren. Zulke minieme verschillen kunnen nog niet worden vastgelegd door de algoritmen, maar mensen kunnen dat gemakkelijk doen.
De tweede factor zijn de kosten . Om een geautomatiseerd inspectiesysteem te implementeren, moet er aanvullende apparatuur zijn, zoals beeldverwerkingsmachines, netwerktools, computerhardware, enz. Deze hardwarekosten, naast de softwarekosten, maken het voor veel organisaties nog steeds onbetaalbaar.
In de loop van de tijd zouden de kwaliteit en prijs van geautomatiseerde visuele inspectiesystemen moeten dalen en zouden we een bredere acceptatie moeten zien.
Hoe het visuele inspectieproces te standaardiseren
Door elk proces te standaardiseren, wordt het herhaalbaar en verifieerbaar. Maar een probleem met de standaardisatie van visuele inspecties is dat een groot deel van het werk erg subjectief van aard is en vrij moeilijk als checklist te verpakken.
Standaardisatie-inspanningen in onderhoud
Onderhoudsactiviteiten worden vaak gestandaardiseerd door middel van schriftelijke standaardwerkprocedures, veiligheidsrichtlijnen (zoals LOTO) en onderhoudschecklists. Visuele inspecties kunnen tot op zekere hoogte op dezelfde manier worden aangepakt.
Aangezien onderhoudstechnici al moeten weten hoe ze elementaire visuele inspecties moeten uitvoeren, kunnen er alleen schriftelijke richtlijnen worden opgesteld voor complexe apparatuur waarvoor de juiste inspectie meerdere stappen vereist.
Het proces van standaardisatie kan er ongeveer zo uitzien:
- Noteer alle activa die regelmatig visueel worden geïnspecteerd.
- Breng de betreffende te controleren gebieden in kaart.
- Noteer de acties die moeten worden ondernomen afhankelijk van het gevlekte teken van verslechtering.
- Maak een stroomdiagram op basis van de bovenstaande informatie.
- Maak een onderhoudschecklist voor de aanwijzingen die moeten worden geïnspecteerd.
- Voeg indien mogelijk de checklist en het stroomschema toe aan uw CMMS-systeem. Als u een mobiel CMMS heeft, hebben technici snel toegang tot die informatie op hun smartphone en tablet, wat hun workflow aanzienlijk kan versnellen.
- Bekijk deze stroomdiagrammen en checklists af en toe en werk ze bij.
Een asset kan een miljoen verschillende problemen hebben, maar het doel van een directe visuele inspectie is om te zoeken naar veelvoorkomende tekenen van slijtage.
Onderhoudschecklists moeten altijd worden opgesteld door ervaren technici die bekend zijn met de interne werking van de apparatuur in hun vestiging. Meestal zijn dat dezelfde mensen die verantwoordelijk zijn voor het opleiden van nieuwe technici. Dit is perfect, aangezien nieuwe technici het meeste uit deze standaardisatie-inspanningen zullen halen.
Standaardisatie-inspanningen voor kwaliteitsbeheer
De sleutel tot het standaardiseren van visuele inspecties in kwaliteitsmanagement ligt in het trainingsproces dat het volgende moet omvatten:
- zeer duidelijke richtlijnen over wat als een defect wordt beschouwd
- wat te doen met een defect product
- wanneer en hoe speciale visuele inspectietools te gebruiken
- met wie contact opnemen voor grensgevallen (vragen om een second opinion)
- hoe en waar nieuwe anomalieën op te merken
- andere speciale richtlijnen die moeten worden gevolgd op de fabrieksvloer
Zelfs daarna zullen er gevallen zijn waarin de subjectiviteit van het proces geschillen veroorzaakt. Een kleine kras op het product kan voor de ene inspecteur een deal-breaker zijn, terwijl de andere het als goed om te gebruiken zou markeren. Een zekere mate van inconsistentie is onvermijdelijk, maar kan worden geminimaliseerd door standaardisatie.
Inspecteer weg
Het zal nog een tijdje duren voordat technologie een geschikte vervanging wordt voor menselijke ogen en oordeel. En er zal nog veel meer nodig zijn voordat dezelfde technologie toegankelijk wordt voor kleine en middelgrote bedrijven.
Tot die tijd blijft deze eenvoudige activiteit een cruciaal onderdeel van assetmanagement en kwaliteitscontrole, uitgevoerd door opgeleid personeel.
Zoals altijd, als je vragen hebt, kun je een discussie starten in de reacties hieronder. Als je meer wilt weten over het onderhoud en de betrouwbaarheid van apparatuur, bekijk dan de nieuwste artikelen op de Limble-blog.
Onderhoud en reparatie van apparatuur
- Navigeren door de modernisering van het onderhoud en beheer van faciliteiten
- De voordelen van strategisch vermogensbeheer
- Kwaliteitscontrole is de eerste stap naar motorbetrouwbaarheid
- Kwaliteitsborging in MRO-materiaalbeheer
- Hoe het industriële internet activabeheer verandert
- Waarom is het nu de tijd om software voor onderhoud en activabeheer te kopen
- IoT en verbonden activa - een revolutie in het activabeheer
- De uitdagingen en kansen van de "All Digital" voor het kwaliteitsmanagementsysteem (QMS)
- De impact van visueel beheer in de branche
- De basisprincipes van kwaliteitscontrole en inspectie bij CNC-bewerkingen
- Het bemonsteringsplan in kwaliteitscontrole