Wat is thermisch spuiten? - Typen en toepassing?
Tegenwoordig worden thermische spuitcoatings gebruikt in een aantal verschillende industrieën. Deze coatings bestaan uit draad en gesmolten poeder die worden blootgesteld aan plasma- of autogeenverbranding. Het vuur van het sproeiapparaat voedt het mengsel dat is verwarmd, en als het eenmaal op metaal is gespoten, behoudt het mengsel een stevige coating.
Thermische spuitcoatings worden gebruikt in een breed spectrum van vele nuttige toepassingen, waaronder het beschermen van vliegtuigen, gebouwen en andere constructies tegen extreme temperaturen, chemicaliën of omgevingscondities zoals vochtigheid en regen. In dit artikel zullen we bespreken wat thermisch spuiten is en hoe het te doen, en de toepassing en voordelen ervan.
Wat is thermische spuitcoating?
Thermische spuittechnieken zijn coatingprocessen waarbij gesmolten (of verwarmde) materialen op een oppervlak worden gespoten. De "grondstof" (coatingprecursor) wordt verwarmd door elektrische (plasma of boog) of chemische middelen (verbrandingsvlam).
Thermisch spuiten kan dikke coatings opleveren (diktebereik is ongeveer 20 micron tot enkele mm, afhankelijk van het proces en de grondstof), over een groot gebied met een hoge afzettingssnelheid in vergelijking met andere coatingprocessen zoals galvaniseren, fysische en chemische dampafzetting .
Coatingmaterialen die beschikbaar zijn voor thermisch spuiten omvatten metalen, legeringen, keramiek, kunststoffen en composieten. Ze worden in poeder- of draadvorm toegevoerd, verwarmd tot gesmolten of halfgesmolten toestand en versneld naar substraten in de vorm van deeltjes ter grootte van een micrometer.
Verbranding of ontlading van een elektrische boog wordt meestal gebruikt als energiebron voor thermisch spuiten. De resulterende coatings worden gemaakt door de ophoping van talrijke gespoten deeltjes. Het oppervlak mag niet significant opwarmen, waardoor brandbare stoffen kunnen worden gecoat.
De kwaliteit van een coating wordt meestal beoordeeld door de porositeit, het oxidegehalte, de macro- en microhardheid, de hechtsterkte en de oppervlakteruwheid te meten. Over het algemeen neemt de kwaliteit van de coating toe met toenemende deeltjessnelheden.
Naast originele uitrustingstoepassingen worden thermische spuitcoatings gebruikt om onderdelen die tijdens het gebruik versleten en beschadigd zijn te repareren en om de afmetingen van machinaal bewerkte onderdelen te herstellen. Thermische spuitcoatings worden gebruikt om de afmetingen van versleten of gecorrodeerde onderdelen, zoals drukrollen en ondermaatse lagers, te herstellen.
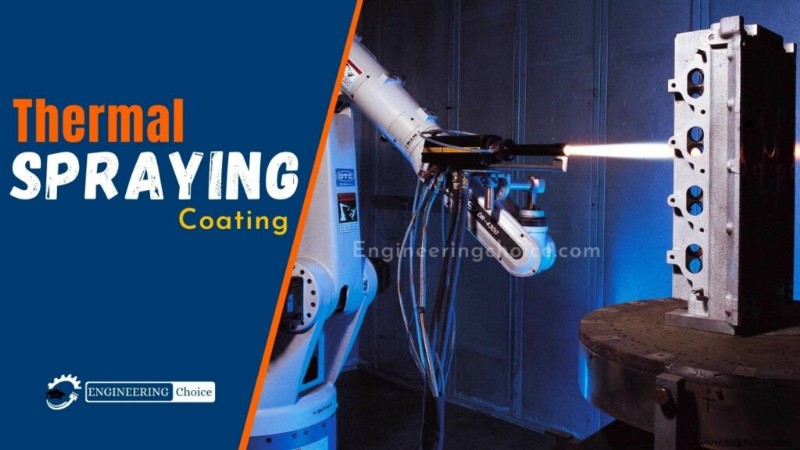
Hoe thermisch spuiten?
Thermisch spuiten is een algemene categorie van coatingprocessen waarbij een verbruiksartikel wordt aangebracht als een spray van fijnverdeelde gesmolten of halfgesmolten druppels om een coating te produceren.
Het onderscheidt zich door zijn vermogen om coatings van metalen, cermet, keramiek en polymeren af te zetten in lagen met een aanzienlijke dikte, typisch 0,1 tot 10 mm, voor technische toepassingen. Vrijwel elk materiaal kan worden afgezet, zolang het maar smelt of plastisch wordt tijdens het spuiten. Op het substraatoppervlak vormen de deeltjes 'splats' of 'bloedplaatjes' die in elkaar grijpen en zich ophopen om de coating te geven.
De afzetting versmelt niet met de ondergrond of moet een vaste oplossing vormen om een hechting te bereiken. Dit is een belangrijk kenmerk van thermisch spuiten in vergelijking met veel andere coatingprocessen, met name booglassen, hardsolderen en lasercoatingprocessen.
De verbinding tussen een thermisch gespoten coating en het substraat is voornamelijk mechanisch en niet metallurgisch of versmolten. De hechting aan de ondergrond hangt af van de staat van de ondergrond, die vóór het spuiten schoon en opgeruwd moet zijn door middel van gritstralen of machinale bewerking.
Thermische spuitprocessen worden al vele jaren op grote schaal gebruikt in alle belangrijke sectoren van de machinebouw voor de bescherming en terugwinning van componenten. Recente apparatuur- en procesontwikkelingen hebben de kwaliteit verbeterd en het potentiële toepassingsbereik voor thermisch gespoten coatings uitgebreid.
Soorten thermische spuitcoatingprocessen
Er worden verschillende varianten van thermisch spuiten onderscheiden:
- Plasma spuiten
- Detonatie spuiten
- Draadboogspuiten
- Vlamspuiten
- Hoge snelheid oxy-fuel coating spuiten (HVOF)
- Hoge snelheid luchtbrandstof (HVAF)
- Warm spuiten
- Koud spuiten
- Spuiten en zekeren
Bij klassieke (ontwikkeld tussen 1910 en 1920) maar nog steeds veel gebruikte processen zoals vlamspuiten en draadboogspuiten, zijn de deeltjessnelheden over het algemeen laag (<150 m/s) en moeten grondstoffen worden gesmolten om te worden afgezet.
Plasmaspuiten, ontwikkeld in de jaren 70, maakt gebruik van een plasmastraal op hoge temperatuur die wordt gegenereerd door boogontlading met typische temperaturen>15.000 K, waardoor het mogelijk is om vuurvaste materialen zoals oxiden, molybdeen, enz. te spuiten.
Hier bespreken we de 5 meest voorkomende processen om thermische spuitcoatings in detail te genereren:
1. HVOF (High-Velocity Oxy-Fuel Spraying)
HVOF is een proces waarbij gebruik wordt gemaakt van een toorts die ervoor zorgt dat de vlam zich verspreidt wanneer het mondstuk wordt gebruikt. Dit zorgt voor een snelle versnelling die de deeltjes in het mengsel versnelt. Het eindresultaat is een uitzonderlijk dunne coating die gelijkmatig wordt aangebracht. Ondanks dat hij dun is, is deze coating sterk en hecht hij goed. De weerstand tegen corrosie is beter dan die van plasmacoatings, maar het is niet goed geschikt voor hoge temperaturen.
2. Verbrandingsvlamspuiten
Spuiten met verbrandingsvlam is een uitstekende optie voor oppervlakken die niet zijn ontworpen om extreme stress aan te kunnen. De coating die het resultaat is van dit proces hecht zich niet sterk aan het oppervlak omdat het spuitmechanisme wordt aangedreven door een lagere vlamsnelheid.
De vlam wordt gegenereerd via zuurstof die is gecombineerd met brandstof, waardoor het mengsel zal smelten. Spuiten met verbrandingsvlammen is populair voor toepassingen met een lage intensiteit vanwege de lage kosten.
3. Plasmaspuiten
Plasmaspuiten maakt gebruik van de plasmatoorts als het belangrijkste hulpmiddel voor het verwarmen en spuiten van de coating. Nadat het poedermateriaal is omgesmolten, wordt het vervolgens op het product geplaatst op een manier die vergelijkbaar is met het spuiten met verbrandingsvlammen.
De coatings die het resultaat zijn van plasmaspuiten, kunnen enkele micrometers dik tot enkele millimeters dik zijn. Hoewel het poeder het meest gebruikte materiaal is, worden ook metalen en keramiek gebruikt. Het plasmaspuitproces is erg populair vanwege zijn aanpassingsvermogen.
4. Vacuüm plasmaspuiten
Vacuümplasmaspuiten gebeurt in een gecontroleerde omgeving, maar maakt gebruik van lage temperaturen. Dit handhaaft het vacuüm en vermindert tegelijkertijd schade aan het materiaal. Er kunnen verschillende gascombinaties worden gebruikt om de benodigde druk voor het spuiten te krijgen.
Vacuümplasmaspuiten wordt gebruikt voor zaken als autobumpers, het dashboard of behuizingen voor buitenspiegels. Dit proces kan ook worden gebruikt voor de voorbehandeling van polyethyleen vormstukken, wat zorgt voor hechting van epoxylijmen op waterbasis.
5. Tweedraads elektrisch boogspuiten
Deze spuitmethode maakt gebruik van een boogpunt dat wordt gecreëerd tussen twee draden die elektrisch geleidend zijn. Smelten zal plaatsvinden op het punt waar de draden aansluiten. De boog zorgt voor verwarming, wat op zijn beurt afzetting en smelten veroorzaakt, vergelijkbaar met het sproeien van verbrandingsvlammen dat wordt gebruikt met een toorts.
Voor het spuiten van de coatings wordt perslucht gebruikt. Deze procedure is populair vanwege de kosteneffectiviteit en zal doorgaans aluminium of zink als basismateriaal gebruiken.
Voordeel van thermisch gespoten coatings
Enkele voordelen van thermische spuitcoatings zijn:
- Verlaagde kosten. De kosten voor het repareren van het onderdeel zijn lager dan het kopen van een nieuw onderdeel. Vaak gaat de coating zelfs langer mee dan het oorspronkelijk gebruikte materiaal.
- Lage warmte-inbreng. Op enkele uitzonderingen na laat het thermische spuitproces de thermische geschiedenis van het onderdeel met rust.
- Veelzijdigheid. Bijna elk metaal, keramiek of plastic kan thermisch worden gespoten.
- Diktebereik. Afhankelijk van het materiaal en het spuitsysteem kunnen coatings worden gespoten van 0,001 tot meer dan 1 inch dik. De dikte varieert meestal van 0,005-0,1 inch.
- Verwerkingssnelheid. De spuitsnelheden variëren van 3-60 lb/hr, afhankelijk van het materiaal en het spuitsysteem. Typische tarieven voor materiaaltoepassing zijn 1/2 -2 lb materiaal per vierkante voet per 0,01-inch dikte.
Nadelen van thermische spuitcoatings
- Verbergt het substraat – aangezien thermische spuitcoatings in veel gevallen zo efficiënt zijn, is het onmogelijk om te zeggen van welk materiaal het substraat is gemaakt na het coatingproces, tenzij er strikte gegevens worden bijgehouden. Neem voor meer informatie hier contact op met Green Leaf Business Solutions.
- Kan effectiviteit niet precies beoordelen – als de thermische spuitcoating eenmaal is aangebracht, is het vaak moeilijk om precies te bepalen hoe goed de coating is aangebracht, behalve door een visuele beoordeling.
- Dure installatie – sommige methoden van thermische spuitcoatings vereisen zeer dure apparatuur, wat kan resulteren in hoge initiële installatiekosten.
Productieproces
- Wat is een saaie machine? - Soorten en toepassingen?
- Wat is sinusbalk? - Hoofdsom, typen en toepassing
- Wat is laserlassen? - Werken, typen en toepassingen?
- Wat is extrusie? - Werken, typen en toepassingen
- Wat is thermisch spuiten? - Typen en toepassing?
- Rolling Process:Types, Werken, Terminologie en Toepassing
- Wat is smeedproces, bediening, typen, toepassing, voor- en nadelen?
- Wat is polijsten, kenmerken en soorten polijsten?
- Wat is technische tolerantie, typen en pasvorm?
- Wat is lasersnijden? – Werking, Soorten &Toepassing
- Wat is stempelen? - Typen, bediening en toepassing