Niet langer de gieterij van je opa
Gieterijen blijven evolueren door innovatieve technologie en veiligheid op de werkplek toe te passen
Een gieterij is een industriële fabriek waar metaal wordt gesmolten en in specifieke vormen gegoten door het in een mal te gieten. Het proces zelf is al eeuwen oud. Tegenwoordig is ongeveer 90% van alle gefabriceerde goederen afhankelijk van metalen gietstukken voor onderdelen, waarbij auto's en vrachtwagens de grootste markt zijn. Aluminium, ijzer en staal zijn de meest voorkomende legeringen die in gieterijen worden verwerkt.

Geschiedenis van gieterijen
Generaties lang heeft de mensheid innovatieve manieren gevonden om grondstoffen uit de natuur te gebruiken - werken met metalen maakt al sinds de oudheid deel uit van de beschaving. Een breed scala aan artefacten is ontdekt door archeologen, van voorwerpen van aanbidding tot gereedschappen en oorlogswapens. In feite zijn de tijdperken van de menselijke geschiedenis vernoemd naar de vooruitgang in de metaaltechnologie:kopertijd, bronstijd en ijzertijd. Het oudst bekende gietstuk dat door historici is gevonden, is een koperen bijl, die werd ontdekt begraven met een mummie vanaf ongeveer 3300 voor Christus.
De gieterij en oven zijn afkomstig uit Mesopotamië en regio's van Irak en Syrië. Kleiafgietsels en hete vuurkorven werkten om koper, goud en zilver te smelten en vorm te geven. Deze primitieve gieterijen smolten koper en waren in staat om complexere vormen te creëren, maar pas toen tin werd geïntroduceerd, maakte de metaalbewerking een aanzienlijke vooruitgang. De toevoeging van tin verlaagde de temperatuur waarbij de twee metalen smolten en brons vormden - de eerste legering.
Door opeenvolgende eeuwen en generaties werden verschillende metaalbewerkings- en giettechnieken ontwikkeld en verloren, terwijl verschillende beschavingen opkwamen om het culturele en technologische landschap te domineren. Het is in de middeleeuwen waar de processen van het gieten van metaal in gieterijen voor het eerst werden gedocumenteerd. Vannoccio Biringuccio (1480-1539) staat bekend als de "vader van de gieterij-industrie", aangezien hij de auteur werd van de eerste handleiding over gieterijen, waaruit de technologie verder werd ontwikkeld.
De eerste officiële gieterij stond bekend als de "Canon Shop", die in 1479 in Moskou werd gebouwd. De 14e en 15e-eeuwse metaalgieterij-industrie in Europa werd bekend door de productie van bronzen en ijzeren klokken, kanonnen en kanonskogels.
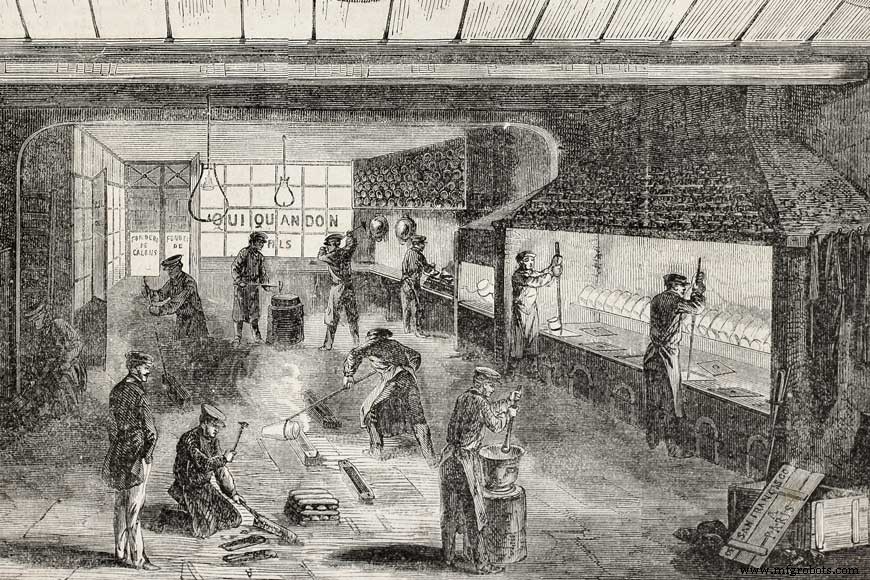
In Noord-Amerika groeide de metaalgietindustrie ter ondersteuning van de vooruitgang van kolonisten in de Nieuwe Wereld. Er waren meer geavanceerde en sterkere gereedschappen, hoefijzers en spoorrails nodig om aan de vraag van de zich ontwikkelende steden te kunnen voldoen.
Saugus Iron Works was de eerste gieterij in de VS en werd in 1642 in gebruik genomen door Europese staalproducenten. Gevestigd in Lynn, Massachusetts, werd het bekend als de geboorteplaats van de Amerikaanse ijzer- en staalindustrie.
Ontwikkelingen in gieterijtechnologie
Gieterijprocessen ontwikkelen zich voortdurend om de kwaliteit van producten en productie-efficiëntie te verbeteren en te profiteren van nieuwe technologieën. Doorbraken in de ontwikkeling hebben aanzienlijke vooruitgang mogelijk gemaakt in het gieten van metaal op belangrijke momenten in de geschiedenis van de industrie.
Ovenontwikkelingen
De migratie van steenkool naar cokes als brandstof voor gieterijen werd ontwikkeld door Abraham Darby. Zijn innovatie in 1709 leidde tot een aanzienlijke verbetering van de efficiëntie en kosten, en maakte de bouw van veel grotere ovens mogelijk dan voorheen mogelijk was.
Koepeloven
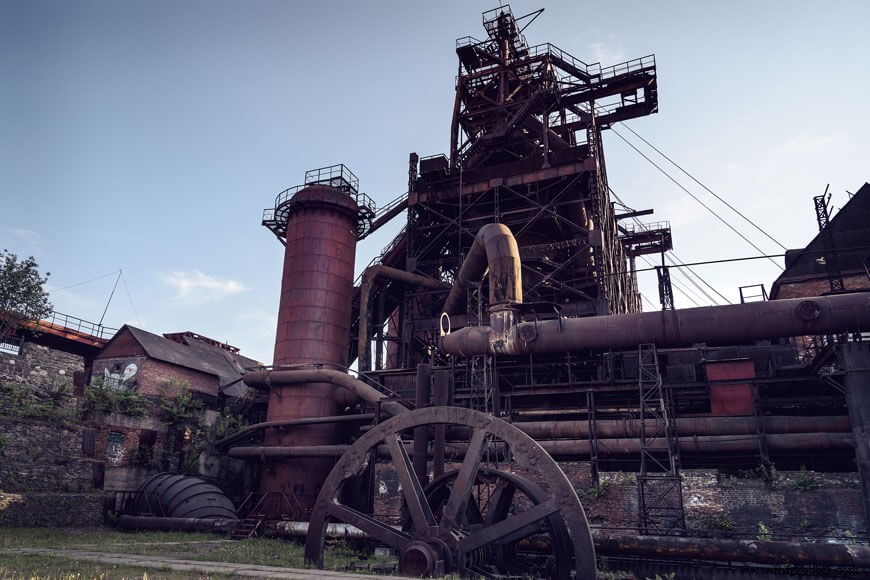
De Cupola-oven werd in 1720 ontwikkeld door de Fransman René-Antoine Ferchault de Réaumur. De koepelvormige structuur heeft een opening om de lading te voeden en scharnierende deuren aan de basis om de oven na uitschakeling te legen. Een cokesbed ondersteunt de smeltende metaal-, cokes- en kalksteenfluxlading boven de tuyeres (openingen waar lucht wordt toegevoerd). Hoewel de Cupola-oven ooit het gieterijlandschap domineerde, is deze nu grotendeels vervangen door efficiëntere elektrische inductie- en vlamboogovens.
Smeltkroes proces
In het 18e-eeuwse Engeland was Benjamin Huntsman de ondernemer achter de ontwikkeling van het smeltkroesproces. Dit was het eerste proces waarbij staal volledig kon worden gesmolten tot een uniform product na het gieten.
Elektrische boogoven
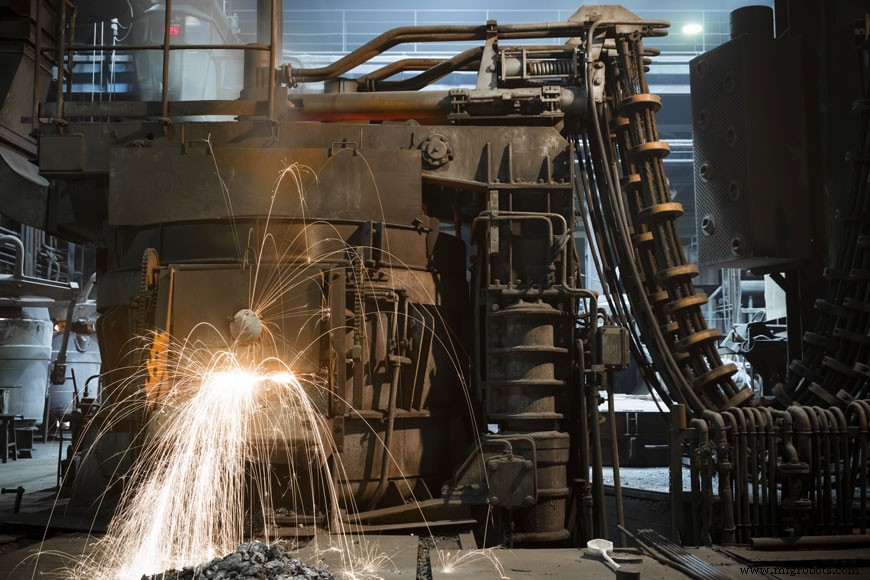
De introductie van commerciële elektriciteitsvoorziening heeft bijgedragen aan de uitvinding van elektrische boogovens. Grafietelektroden creëren de elektrische boog en leveren stroom als energiebron om ijzer te smelten. De eerste elektrische vlamboogoven werd in 1900 gemaakt door Paul Héroult uit Frankrijk. In 1907 werd een commerciële fabriek opgericht in de Verenigde Staten. Deze ovens zijn zuiniger bij lagere productiesnelheden en kunnen met tussenpozen worden gebruikt, waardoor metaalgieterijen meer flexibiliteit krijgen.
Elektrische inductieoven
Elektrische inductieovens gebruiken een wisselstroom met hoog vermogen die door een spoel vloeit om wervelstromen in het metaal te induceren en zo warmte te genereren, en worden tegenwoordig het meest aangetroffen in productiegieterijen.
Casting-ontwikkelingen
In de oudheid werd metaal gegoten in kleivormen. Een van de grote Assyrische koningen, Senacheribb, beweert de techniek van het gieten van brons en koper in kleivormen te hebben geperfectioneerd. Naarmate de tijd vorderde, transformeerden technologische ontwikkelingen het gietproces - van zandgieten tot elektromagnetische technologie.
Zandafgietsels
Vannochio Birringucio, gieter uit de late 15e en vroege 16e eeuw, schreef een boek over alle vormen van gieten en aanverwant werk. Het boek beschrijft het gebruik van zandgietwerk, de volgende grote fase van giettechnologie. Aanvankelijk zou zand worden gemengd met klei als bindmiddel zodat de mal zijn vorm zou behouden tijdens het gieten, maar in de loop van de tijd zijn er nieuwe soorten zand en bindmiddelen ontwikkeld.
Groen zand is een van de meest voorkomende materialen die tegenwoordig worden gebruikt. Historisch gezien bestond groen zand uit kwartszand, bentonietklei, water en zeekool. Zeekool wordt tegenwoordig echter niet meer vaak gebruikt en is vervangen door andere materialen. Hoewel gieten van groen zand nog steeds algemeen wordt gebruikt, worden "no-bake", chemische harding of cold-set-processen overheersend in de gieterijen van vandaag.
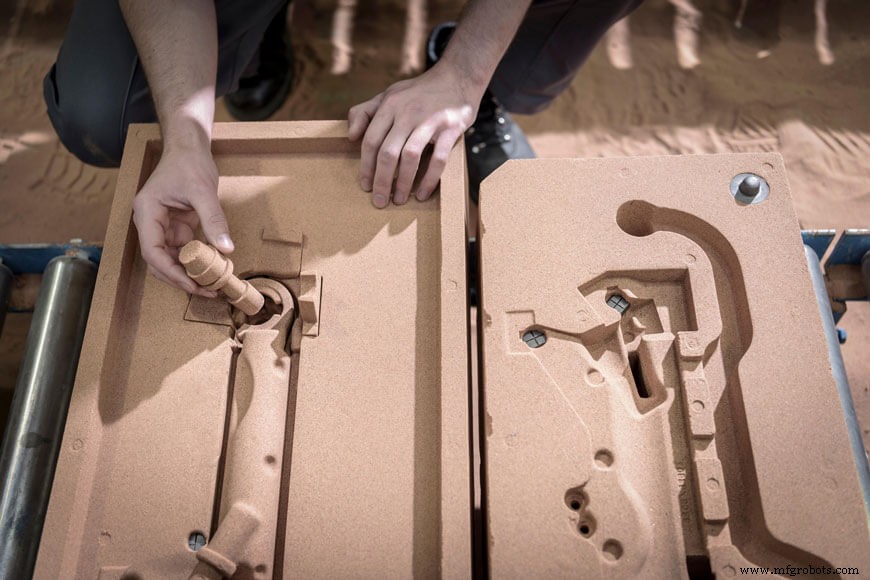
Spuitgieten
Spuitgieten en investeringsgieten zijn moderne technieken waarbij gebruik wordt gemaakt van nieuw beschikbare materialen om de kwaliteit van de gietafwerking en de productiekosten te verbeteren. Spuitgieten wordt gekenmerkt door het onder hoge druk persen van gesmolten metaal in een vormholte. Afhankelijk van het type metaal dat wordt gegoten, wordt een hete- of koudekamermachine gebruikt. Spuitgietstukken staan bekend om hun goede oppervlakteafwerking en dimensionale consistentie.
Continu casten
Misschien wel de belangrijkste vooruitgang in het gietproces is de introductie van de continugietmachine. Gesmolten metaal wordt in een mal gegoten en langzaam teruggetrokken om ononderbroken stukken gestold metaal te creëren. Het grote voordeel van deze koolstofstaalgietmethode is de eliminatie van enkele van de stroomafwaartse verwerkingsstappen. Deze halffabrikaten kunnen gemakkelijker door walsen worden omgezet in eindproducten.
Permanente schimmels
In de 21e eeuw maakten gietprocessen een nieuwe sprong voorwaarts door de introductie van elektromagnetische technologie. Een inductiespoel is gewikkeld rond een watergekoelde mal met wisselstroom die elektromagnetische velden genereert.
Deze elektromagnetische velden gaan door het koelende metaal en veroorzaken de vorming van wervelstromen in het gesmolten metaal, wat resulteert in twee positieve resultaten:
- Het contact tussen het koelmetaal en het matrijsoppervlak is "zacht" en geeft een betere afwerkingskwaliteit. Bij standaard watergekoeld gieten vormt zich door “hard” contact met de mal een dikke huid met grove microstructuur. Deze huid wordt vóór het walsen weggefreesd, wat resulteert in aanzienlijke productverspilling en hogere kosten.
- De homogeniteit van het metaal is sterk verbeterd met een vermindering van korrelgrensscheidingen.
Kwaliteitsontwikkelingen
Sir Henry Bessemer was de vernieuwer achter nieuwe technieken om koolstof en overtollige zuurstof uit het gesmolten staal te verwijderen, wat culmineerde in de uitvinding van de converter. Bessemer ontdekte dat het blazen van zuurstof door het gesmolten metaal een reactie veroorzaakte met koolstof en silicium in het materiaal, waarbij onzuiverheden werden verwijderd maar ook het materiaal werd verwarmd om het gieten gemakkelijker te maken.
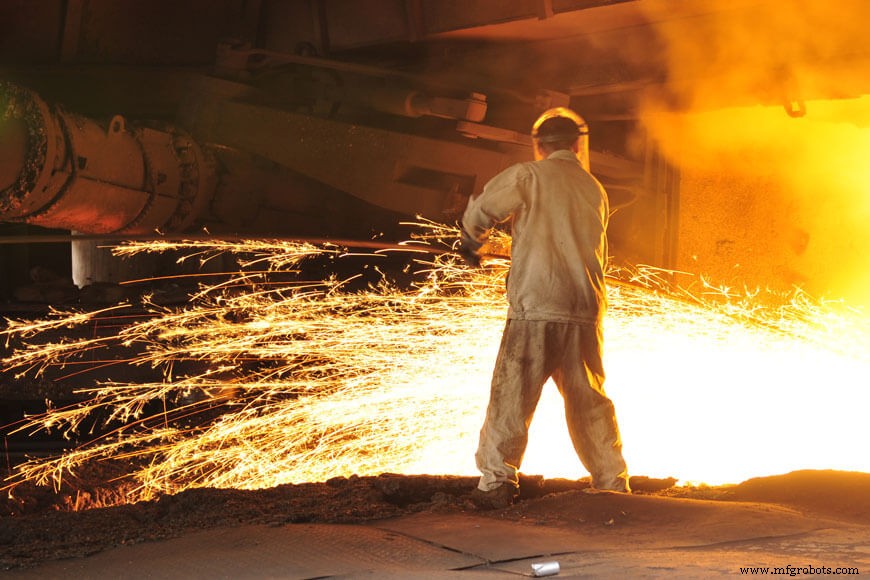
Converters worden nu gebruikt voor fijne mate van kwaliteitscontrole door nauwkeurige koolstofgehalteverhoudingen in te stellen en legeringen en andere additieven toe te voegen voor de specifieke vereiste producteigenschappen. In een vlamboogoven kan zuurstof in het bad worden geïnjecteerd om koolstof en vele andere elementen en onzuiverheden te "verbranden". Hierdoor wordt het initiële bad zo schoon mogelijk en kan de gieterij de smelt tot de perfecte inhoud legeren. Bij inductiesmelten kan de gieterij alleen beginnen met een bad dat is gemaakt van de input of het gesmolten schroot - de chemische inhoud van het schroot moet overeenkomen met de chemie van het bad dat de gieterij aanvankelijk gebruikt.
Meet- en regelontwikkelingen
In combinatie met vooruitgang in productiemethoden, is er vooruitgang geboekt in de laboratoriumtestmethoden van gesmolten metaal terwijl de productie nog steeds aan de gang is. Monsters kunnen worden getrokken uit converters en geanalyseerd met behulp van spectrometers of röntgenfluorescentie-analyse. Deze realtime feedback van de chemische samenstelling biedt fabrikanten de mogelijkheid om aanpassingen aan te brengen voordat ze worden gegoten, waardoor kostbare tijd en middelen worden bespaard als gevolg van herbewerking.
Hoewel een ervaren operator oppervlaktedefecten en potentiële gebreken in het gegoten product met het blote oog kan oppikken, heeft de verbetering van niet-destructieve testmethoden klanten meer zekerheid gegeven over de integriteit van het product:
- Dye Penetrant en Fluorescent Powder kunnen in penetrerende olie worden gesuspendeerd en op het oppervlak van het voltooide gietstuk worden aangebracht. Oppervlaktebarsten en gebreken zijn direct zichtbaar bij het aanbrengen van de ontwikkelaar of in aanwezigheid van ultraviolet licht.
- Radiografische inspectie is de meest effectieve methode voor het identificeren van interne gaten, scheuren of insluitsels. De cast wordt blootgesteld aan straling van een röntgenbuis en het beeld dat op de radiografische film wordt gemaakt, geeft veranderingen in de dichtheid van de cast aan. Het voordeel van deze methode is dat de röntgenfoto dient als een permanente registratie, die het product gedurende zijn hele levenscyclus kan begeleiden voor kwaliteits- en veiligheidscontrole.
- Liquid Dye Penetrant Inspection (LPI) kan kleine scheurtjes, poriën of andere oppervlakte-imperfecties in zowel ferro- als non-ferro gietstukken vinden die met het blote oog moeilijk te zien zijn. LPI gebruikt een gekleurde kleurstofolie-oplossing op het oppervlak van het gietstuk dat zijn weg vindt naar de oppervlaktedefecten. Zodra een speciale ontwikkelaar is aangebracht, worden de gebreken duidelijk zichtbaar.
- Magnetic Particle Inspection (MPI) helpt bij het identificeren van de locatie van oppervlaktediscontinuïteiten in ferrometaal. Het kan ook wijzen op ondergrondse defecten als de magnetiserende kracht voldoende is om een lekveld aan het oppervlak te produceren. In deze test wordt een magnetische flux geïnduceerd in ferromagnetisch materiaal. Elke abrupte discontinuïteit in zijn pad resulteert in een lokaal fluxlekveld. Als fijnverdeelde deeltjes van ferromagnetisch materiaal in de buurt worden gebracht, bieden ze een pad met lage reluctantie naar het lekveld en nemen ze een positie in die ruwweg de effectieve grenzen schetst. Het te inspecteren gietstuk wordt gemagnetiseerd en het oppervlak ervan wordt bestrooid met het magnetische poeder. Een luchtstroom met lage snelheid blaast het overtollige poeder weg, waardoor het defect wordt omlijnd door de resterende poederdeeltjes. Het poeder kan worden aangebracht terwijl de magnetiserende stroom vloeit (continue methode) of nadat de stroom is uitgeschakeld (restmethode). Het kan droog of gesuspendeerd worden aangebracht in een licht petroleumdestillaat vergelijkbaar met kerosine.
Inspectie van magnetische deeltjes
Magnetische deeltjesinspectie (MPI) is een soort niet-destructief onderzoek waarbij magnetische flux wordt gebruikt om eventuele oppervlaktedefecten te bepalen. Kijk hoe een werknemer niet-destructieve tests uitvoert op een olie- en gaslasverbinding.
- Ultrasoon testen (UT) identificeert interne defecten door middel van geluid door gebruik te maken van hoogfrequente akoestische energie die naar een gietstuk wordt overgebracht. UT maakt onderzoek van het dwarsdoorsnede-oppervlak van een gietstuk mogelijk en wordt daarom beschouwd als een volumetrische inspectiemethode. De hoogfrequente akoestische energie reist door het gietstuk totdat het het tegenoverliggende oppervlak, de interface of het defect raakt. De interface of het defect weerspiegelt delen van de energie die worden verzameld in een ontvangende eenheid en weergegeven voor de analist om te bekijken. Het patroon van energieafbuiging kan de locatie en grootte van een inwendig defect aangeven, evenals de wanddikte en het aantal knobbeltjes van nodulair gietijzer. UT vereist kennis en ervaring voor een nauwkeurige interpretatie van resultaten, wat de inspectiekosten verhoogt.
Veiligheidsontwikkelingen
Werken in een gieterij is een gevaarlijk beroep. Er zijn tal van chemische, mechanische en temperatuurgevaren die moeten worden beheerst om mogelijke schade aan werknemers te voorkomen.
Een van de belangrijkste gebieden die de veiligheid van werknemers heeft verbeterd, is de mechanisering van de industrie.
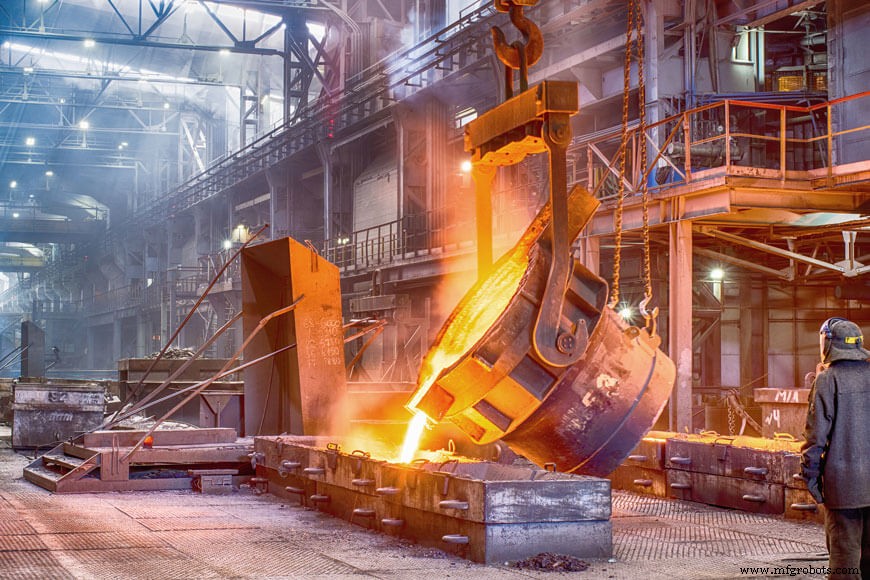
Voorheen werden pollepels gemanipuleerd, opgepakt en verplaatst over het gieterijterrein. Vervolgens werden er pollepels met tandwielen geïntroduceerd, waardoor een operator de pollepel op afstand kon bedienen en besturen in plaats van naast het vat met gesmolten metaal te staan. Er werden kranen geïntroduceerd om gietlepels in positie te brengen om te storten, maar het lawaai van de productieomgeving en de beperkingen van het zicht zorgden er nog steeds voor dat kraanmachinisten kwetsbaar waren voor het veroorzaken van incidenten. Proceskranen zijn de nieuwste ontwikkeling waarbij pollepels op vooraf ingestelde rupsbanden met liften lopen, waardoor de kans wordt geëlimineerd dat een machinist zich onder normale bedrijfsomstandigheden in het pad van de bewegende pollepel bevindt.
De toekomst van gieterijen
Toekomstige technologietrends
Efficiëntie is de belangrijkste drijfveer achter technologische vooruitgang in gieterijen. Er is een sterke focus op het verminderen van het energieverbruik door de nadruk op duurzame productie en de daarmee gepaard gaande verlaging van de kosten. Een kleinere beroepsbevolking in gieterijen zal ook de kans op verwondingen verminderen en de productie optimaliseren.
Verbeteringen in de automatisering en een verschuiving naar computersimulaties, zoals simulatiesoftware voor stolling, zullen de afhankelijkheid van de gieterij-industrie van arbeid verminderen en de nauwkeurigheid en efficiëntie verbeteren. Computerondersteunde processimulatie biedt procesmodellen die nu voldoende volwassen zijn. Hierdoor kunnen gieterijingenieurs de virtuele wereld gebruiken ter voorbereiding op de echte wereld, waardoor het aantal proefversies wordt geminimaliseerd.
De coördinatenmeetmachine (CMM) brengt een nieuw niveau van precisiemeting naar de werkvloer in de verspanende industrie. Inspectie van gaten, sleuven, gelaste onderdelen en vervormingen kan snel worden uitgevoerd, waardoor de cyclustijd aanzienlijk wordt verkort. De gescande gegevens worden vervolgens gecombineerd met tactiele resultaten in grafische rapporten voor eenvoudige interpretatie. De CMM is een drijvende kracht in het verhogen van de productiviteit en het verschaffen van praktisch inzicht.
Toekomstige markttrends
De gieterijmarkt werd het afgelopen decennium gedomineerd door consolidatie in grote conglomeraten. Schaalvoordelen zijn een belangrijke drijfveer voor deze trend en zullen zich waarschijnlijk in de nabije toekomst voortzetten. Kleinere en minder efficiënte operaties zullen blijven stilvallen vanwege het concurrentievermogen van de markt.
Toekomstige milieu- en veiligheidstrends
Recycling van metalen is een van de succesverhalen van duurzame ontwikkeling, maar er blijft een behoefte bestaan om het duurzame gebruik van andere producten die betrokken zijn bij het metaalgietproces te ontwikkelen. Er zullen nog steeds nieuwe manieren worden gevonden om slakken en gebruikt vormzand te gebruiken om gelijke tred te houden met de constante vooruitgang op het gebied van regelgeving op het gebied van afvalverwijdering.
Snelle vooruitgang in robottechnologie heeft deuren geopend om de blootstelling van mensen aan gevaarlijke situaties te verminderen. Innovators in robottechnologie voor industriële omgevingen ontwikkelen robotachtige werkcellen die volledig geautomatiseerd zijn en geen menselijke tussenkomst op de werkplek vereisen.
Gieterijen en hun voortdurende evolutie
Metaalgieten maakt al sinds de oudheid deel uit van de menselijke samenleving en groeit alleen maar in gebruik en vooruitgang met de dag.
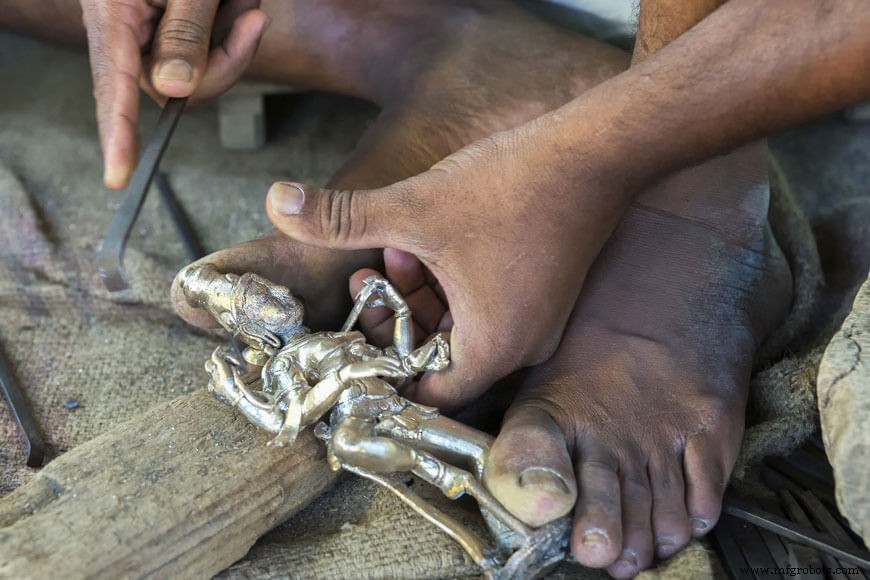
Tegenwoordig beïnvloeden gegoten metalen producten ons leven op verschillende manieren. Auto-onderdelen, keukengerei, gereedschap en vele andere producten voor dagelijks gebruik zijn allemaal het resultaat van de fabricageprocessen van gieterijen.
Door de eeuwen heen heeft technologie dramatische vooruitgang geboekt om de consistentie en kwaliteitscontrole van gegoten metalen producten te verbeteren, terwijl de arbeidsveiligheid van werknemers is verbeterd en de kosten zijn verlaagd door grotere efficiëntie. Een studie van de geschiedenis van gieterijen onthult uitstekende ondernemers, ingenieurs, innovators en probleemoplossers die elk een rol hebben gespeeld bij de ontwikkeling van deze industrie.
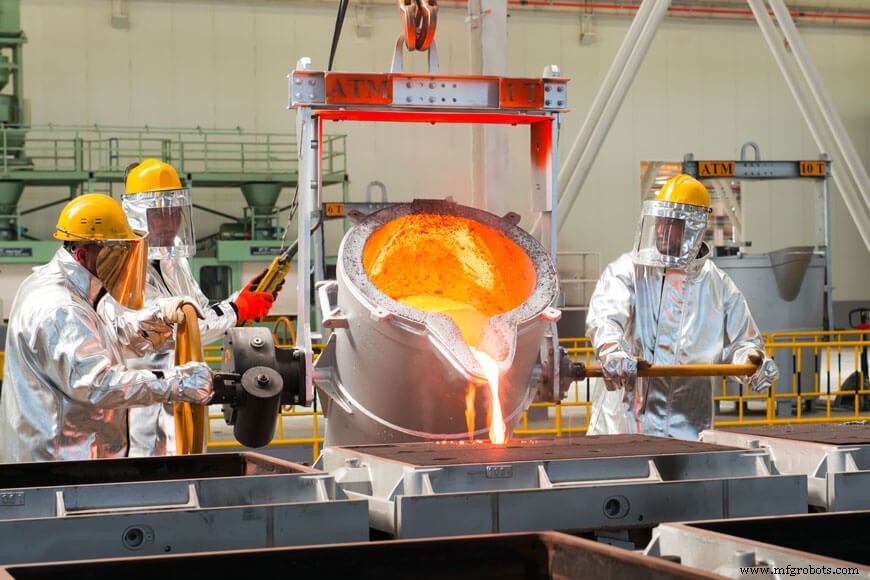
De economische druk van de wereldmarkt blijft een omgeving creëren die innovatie, consistentie en efficiëntie beloont. De komende decennia zullen ongetwijfeld opwindende nieuwe technologieën opleveren, zoals het gebruik van big data en robotica, en nieuwe bedrijfsmodellen door fusies en upgrades. Wereldwijde trends in de richting van duurzame productie zullen leiden tot verbeteringen op het gebied van milieu en veiligheid in de industrie, wat zowel werknemers als gemeenschappen ten goede zal komen.
Referenties
- Industriële metalen gietstukken. "Geschiedenis van metaalgieten"
- Het gratis woordenboek. "Gieterij-industrie"
- Waupaca gieterij. "Metaalgietgeschiedenis"
- Amerikaanse National Park Service. "Saugus Iron Works National Historic Site"
- Encyclopedie Britannica. "Koepeloven"
- De Amerikaanse Stichting voor Syrische Studies. "De context van uitvindingen in de antieke wereld"
- Het ijzer- en staalinstituut van Japan. “Staaltechnologie van de laatste 100 jaar”
- Amerikaanse Foundry Society. "Castings in onze wereld"
- Metaaltechnologieën. "Geschiedenis van metalen gietstukken"
- AMAG. “EMC-technologie verhoogt kwaliteit en kostenefficiëntie”
- TP Gietstukken. "Gieterij-industrie:korte geschiedenis en definitie"
Productieproces
- Guillotine
- Silicium
- Scharnieren voor uw plaatwerkbehuizingen
- 5 manieren om uw plaatwerkonderdelen te verbeteren
- 5 manieren om uw metalen onderdelen corrosiebestendig te maken
- Uw gids voor het knippen van metaalproductieprocessen
- 5 belangrijke vragen om uw metaalleverancier te stellen
- Corrosie in uw metalen apparatuur voorkomen
- Hoe u uw boormachine gebruikt om metaal te boren?
- Wat is een gieterij?
- Wanneer werd de metaalbewerkingsdraaibank uitgevonden?