De ultieme CNC-bewerkingsgids

Computer Numerical Control (CNC)-bewerking is een modern, efficiënt en geautomatiseerd subtractief productieproces waarmee fabrikanten herhaalbare onderdelen van consistente kwaliteit kunnen maken van een breed scala aan materialen, waaronder kunststoffen, metalen en composieten. Tegenwoordig zijn CNC-gefreesde onderdelen te vinden in een groot aantal verschillende industrieën, van ruimtevaart tot automobiel tot medisch.
Het begin van CNC-technologieën is terug te voeren op een paar verschillende punten in de geschiedenis. De eerste moderne bewerkingsgereedschappen verschenen in 1775 toen industriëlen een kottergereedschap ontwikkelden waarmee fabrikanten stoommachinecilinders konden produceren met een meer consistente mate van nauwkeurigheid en precisie.
De technologische voorouders van moderne computers verschenen echter eerder in de eeuw, voortkomend uit de textielindustrie. In 1725 begon Basile Bouchon een systeem van geperforeerde gaten in papieren tape te gebruiken om gegevens te coderen. Decennia later, in 1805, verfijnde Joseph Marie Jacquard het proces en verruilde hij de papieren tape voor stevige ponskaarten. Wanneer ze in een reeks werden gebonden, gaven de ponskaarten aan hoe de stof aan het weefgetouw werd toegevoegd, waardoor het proces werd vereenvoudigd en een van de eerste voorbeelden van programmering werd geboden. Deze machine, het Jacquard-weefgetouw, is in zekere zin de voorloper van onze moderne computer- en automatiseringsoplossingen.
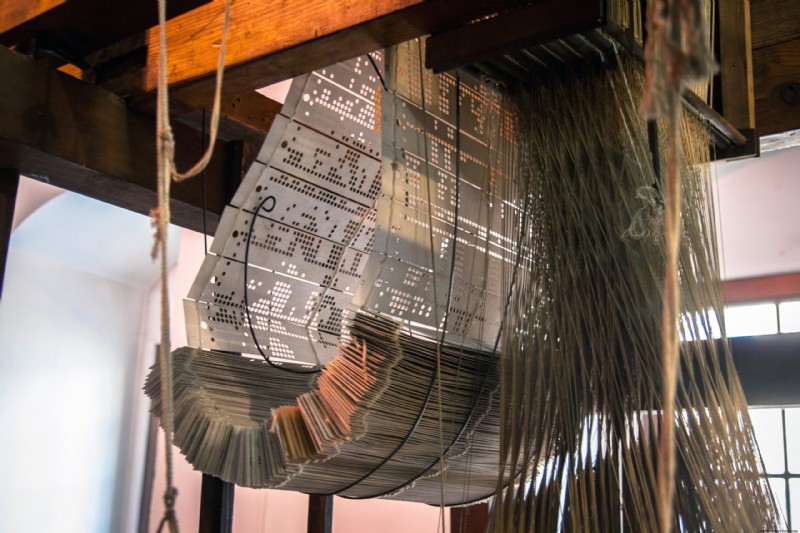
Deze gids voor alles wat met CNC-bewerking te maken heeft, laat zien hoe moderne CNC-bewerkingsprocessen werken, inclusief materiaalopties, ontwerpoverwegingen, kostenfactoren en meer. Blijf lezen of klik hier om de PDF te downloaden.
Soorten CNC-bewerking
Tegenwoordig zijn er verschillende technische processen opgenomen onder de paraplu van CNC-bewerking.
3-assige bewerking:frezen en draaien
Zodra de operator de bewerkingsinstructies invoert, zullen 3-assige CNC-machines de invoerbewerkingen uitvoeren door snijgereedschappen te gebruiken om langs drie assen te snijden:X (van links naar rechts), Y (van voren naar achteren) en Z (omhoog en omlaag). omlaag). CNC-frezen en CNC-draaien zijn twee veelvoorkomende voorbeelden van 3-assige bewerking.
3-assig CNC-frezen omvat het fixeren van het blok materiaal - ook wel het werkstuk of "blanco" genoemd - met een bankschroef of machinebed. Dit houdt het werkstuk stationair terwijl snijgereedschappen en roterende boren, bevestigd aan een centrale spil, sneden maken om materiaal te verwijderen en het uiteindelijke onderdeel vorm te geven. De 3-assige CNC-freesmachines zijn eenvoudig te programmeren en te bedienen en kunnen worden gebruikt om de meeste onderdelen te maken met eenvoudige geometrische ontwerpen.
Aangezien de snijgereedschappen en boren beperkt zijn tot drie assen, kunnen sommige ontwerpkenmerken of delen van de plano moeilijk te voltooien of te bereiken zijn (bijvoorbeeld onconventionele vormen of diepe, smalle holtes). Meerdere instellingen kunnen echter helpen het werkstuk te oriënteren zodat de machines deze functies kunnen bereiken. Terwijl bijna elke 3-assige bewerkingstaak meer dan één opstelling per onderdeel heeft, kunnen te veel opstellingen per onderdeel de productiekosten snel verhogen. Het verwerken van geometrisch complexe onderdelen kan bijvoorbeeld vereisen dat operators werkstukken handmatig herpositioneren, wat de verwerkingssnelheid kan beïnvloeden, arbeidsgerelateerde kosten kan verhogen en meer kansen op menselijke fouten kan creëren.
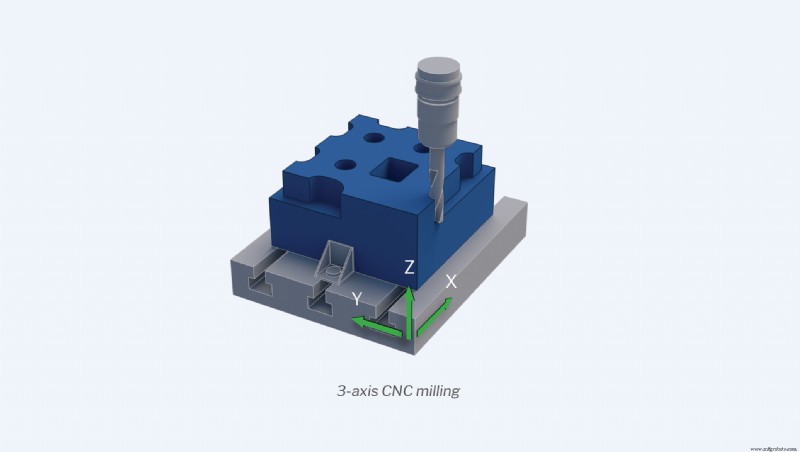
Het CNC-draaiproces werkt iets anders. De plano wordt bevestigd aan een roterende spil en een draaibank vormt vervolgens de binnen- en buitenomtrek van het stuk of boort gaten rond de middenas van het werkstuk. De belangrijkste ontwerpbeperking bij CNC-draaibanken is dat ze altijd rotatiesymmetrische onderdelen produceren. Het proces is daarom ideaal voor het vervaardigen van onderdelen zoals schroeven, schalen of stoelpoten. Voor dit soort ronde onderdelen kunnen draaibanken stukken sneller en tegen lagere kosten produceren dan CNC-freesmachines, vooral bij het produceren van onderdelen in grote volumes.
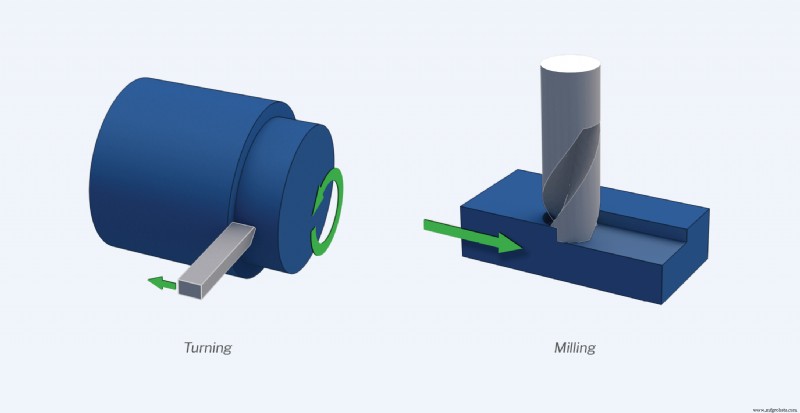
5-assige of meerassige bewerking
Meerassige bewerkingsprocessen geven de snijwerktuigen meer bewegingsvrijheid terwijl het werkstuk wordt gefreesd of gedraaid. 3-assige processen zorgen ervoor dat de blanco of het snijgereedschap kan draaien, maar niet beide. Bij 5-assige processen daarentegen kunnen zowel het werkstuk als het gereedschap tegelijkertijd draaien en bewegen langs de X-, Y- en Z-assen. 5-assige CNC-bewerking bespaart tijd en is ideaal voor het maken van complexe en nauwkeurige onderdelen zoals die worden aangetroffen in de medische, olie- en gasindustrie en de lucht- en ruimtevaartindustrie.
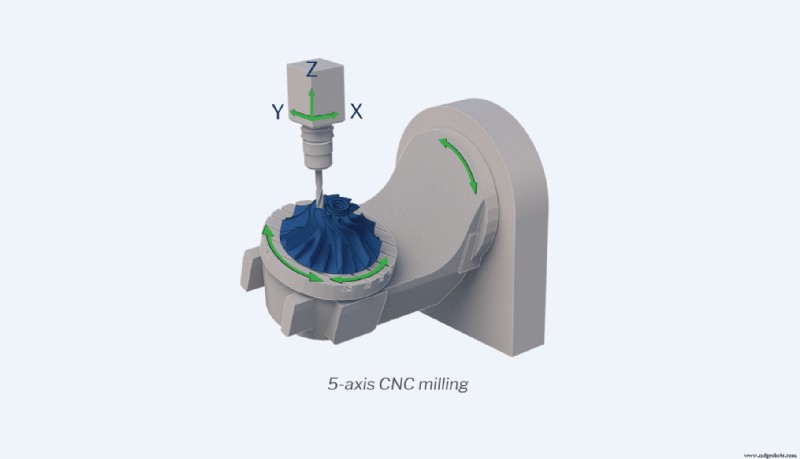
De meerassige CNC-bewerkingsfamilie omvat drie processen:
- Geïndexeerd 5-assig CNC-frezen: Tijdens geïndexeerde 5-assige freesbewerkingen kunnen de snijgereedschappen niet alleen langs de drie lineaire assen bewegen, maar tussen bewerkingen kunnen de bewerkingstafel en de gereedschapskop in twee richtingen draaien. Het meest opvallende voordeel van 5-assig frezen is dat de blanks niet meer handmatig hoeven te worden aangepast tussen snijbewerkingen, waardoor het mogelijk wordt om componenten met complexe geometrieën nauwkeuriger en efficiënter te maken. Geïndexeerde 5-assige bewerking is geweldig voor het vervaardigen van componenten zoals behuizingen, mallen en armaturen. Het proces valt ergens tussen 3-assig CNC-frezen en continue 5-assige CNC-bewerking (zie hieronder) in termen van snelheid, precisie en het vermogen om complexe geometrieën te verwerken.
- Continu 5-assig CNC-frezen: Continue 5-assige CNC-freesmachines kunnen tijdens elke bewerking zowel het snijgereedschap als het werkstuk gelijktijdig verplaatsen en roteren, waardoor onderdelen met extreem ingewikkelde geometrieën en gladde oppervlakken kunnen worden vervaardigd. Hoewel dit per onderdeel de duurste vorm van CNC-bewerking is, worden de kosten van continu 5-assig CNC-frezen doorgaans gecompenseerd door een verbeterde oppervlakteafwerking, snelheid en maatvastheid.
- Frezen draaien met live tooling: Bij het frezen worden elementen van CNC-draaibanken gecombineerd met freesgereedschappen. Het werkstuk is bevestigd aan een roterende spil terwijl snijgereedschappen materiaal uit de plano verwijderen. Door de elementen van CNC-draaibanken te combineren met freesgereedschappen, biedt frees-draaiende CNC een hoge mate van nauwkeurigheid en geometrische veelzijdigheid, waardoor het ideaal is voor het maken van onderdelen met losse rotatiesymmetrieën, zoals nokkenassen of centrifugaalcompressoren.
Het juiste type CNC-bewerking kiezen
Bij het selecteren van een productieproces voor uw onderdeel, moet u evalueren of het beter geschikt is voor 3-assige of 5-assige bewerking. Over het algemeen kunnen onderdelen met eenvoudiger ontwerpen snel en betaalbaar worden gemaakt met 3-assige machines, terwijl 5-assige machines beter zijn voor het maken van geometrisch complexe stukken met verhoogde snelheid en nauwkeurigheid.
Als u een klein budget heeft of alleen een vlak oppervlak hoeft te zagen, zijn 3-assige machines de juiste keuze. Behalve dat ze betaalbaarder zijn, zijn 3-assige machines eenvoudiger te programmeren, zodat u niet de kosten hoeft te maken van het werken met dure 5-assige programmeurs en operators. Bovendien is de voorbereidingstijd korter met 3-assige bewerking.
Als u een dieper onderdeel of een onderdeel met een complexe geometrie moet produceren, wilt u 5-assige bewerking gebruiken. Door 5-assige machines te gebruiken, kunt u het werkstuk van alle kanten bewerken zonder handmatige rotatie. Met 5-assige bewerking heeft u hogere opbrengsten, grotere nauwkeurigheid en grotere bewegingsvrijheid, evenals de mogelijkheid om grotere onderdelen sneller te vervaardigen.
Veelgebruikte CNC-materialen
Een van de voordelen van CNC-bewerking is dat het proces compatibel is met veel verschillende materialen, waarbij kunststoffen en metalen de twee meest voorkomende materiaalfamilies zijn. Hier zijn enkele van de kunststoffen en metalen die u waarschijnlijk zult tegenkomen.
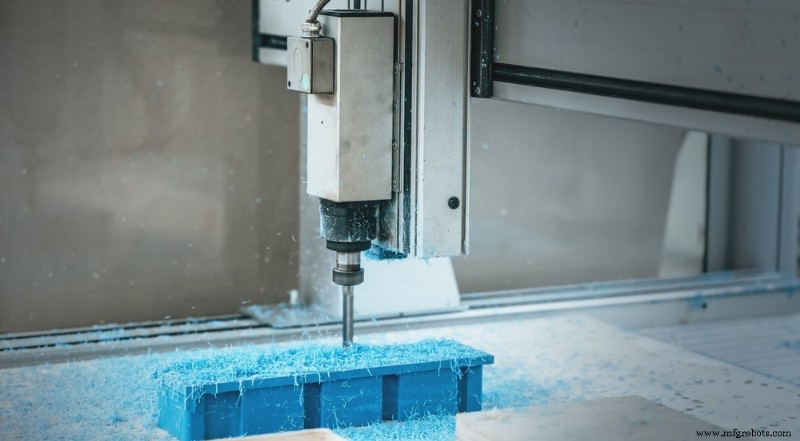
Hoogwaardige polymeren
- Acrylonitril-butadieen-styreen (ABS): ABS is een slagvast technisch thermoplast met uitstekende mechanische eigenschappen. Sterk en stijf met behoud van een zekere mate van flexibiliteit, ABS is opmerkelijk omdat het mechanisch sterk is, goede isolatie biedt en bestand is tegen slijtage en spanning.
- Hoge dichtheid polyethyleen (HDPE): HDPE, een van de meest veelzijdige thermoplastische polymeren die er zijn, is een flexibel en gemakkelijk te verwerken materiaal dat zeer goed bestand is tegen spanningsscheuren, chemicaliën en corrosieve stoffen, zelfs bij lage temperaturen. Het biedt ook een uitstekende slagvastheid. HDPE wordt vaak gebruikt om plastic flessen, pluggen, afdichtingen, isolatoren, leidingen en vele andere goederen te maken.
- Lage dichtheid polyethyleen (LDPE): Deze sterke, flexibele kunststof wordt voornamelijk gebruikt voor het maken van orthesen en protheses en is gemakkelijk te lassen en te smelten. Hoewel het een goede chemische weerstand biedt, is LDPE niet ideaal voor toepassingen die stijfheid, hoge structurele sterkte of weerstand tegen hoge temperaturen vereisen.
- Polyamide (PA) of nylon: Nylons zijn een familie van wrijvingsarme kunststoffen die zeer geschikt zijn voor het vervangen van metalen onderdelen, zoals lagers of bussen, vanwege de unieke combinatie van elasticiteit, stijfheid en stijfheid. Nylons kunnen worden versterkt met een reeks additieven om specifieke materiaal- en chemische eigenschappen te creëren of gecombineerd met andere kunststoffen voor betere prestaties en materiaaleigenschappen.
- Polyamide (PA) of nylon 30% GF: Glasvezels, een van de meest voorkomende additieven voor technische kunststoffen, verhogen de sterkte en stijfheid van nylon onderdelen aanzienlijk. Helaas verhogen deze vezels ook de brosheid van het materiaal en worden daarom alleen aanbevolen voor toepassingen waarbij geen hoge slagspanning of doorbuiging optreedt.
- Polycarbonaat (pc): Dit plastic wordt om een aantal redenen veel gebruikt:het is taai en toch licht van gewicht, het is een goede elektrische isolator en het is van nature hittebestendig. PC is van nature transparant en doorschijnend en neemt pigment goed op. Bovendien is PC bestand tegen verdunde zuren, oliën en vetten, maar gevoelig voor koolwaterstofslijtage en UV-stralen.
- Polyetheretherketon (PEEK): PEEK is een hoogwaardig polymeer met een unieke combinatie van mechanische eigenschappen en is bestand tegen chemicaliën, slijtage, kruip, vermoeiing, vloeistof en temperatuur. Dit materiaal is niet alleen recyclebaar en biocompatibel, maar ook lichtgewicht, sterk en onoplosbaar in alle gangbare oplosmiddelen. Net als nylon kan PEEK metaal vervangen bij CNC-bewerkingen. Veelvoorkomende toepassingen voor dit materiaal zijn zuigereenheden, kritische vliegtuigmotoronderdelen en tandheelkundige spuiten. Het is met name een van de duurdere CNC-bewerkingskunststoffen op de markt.
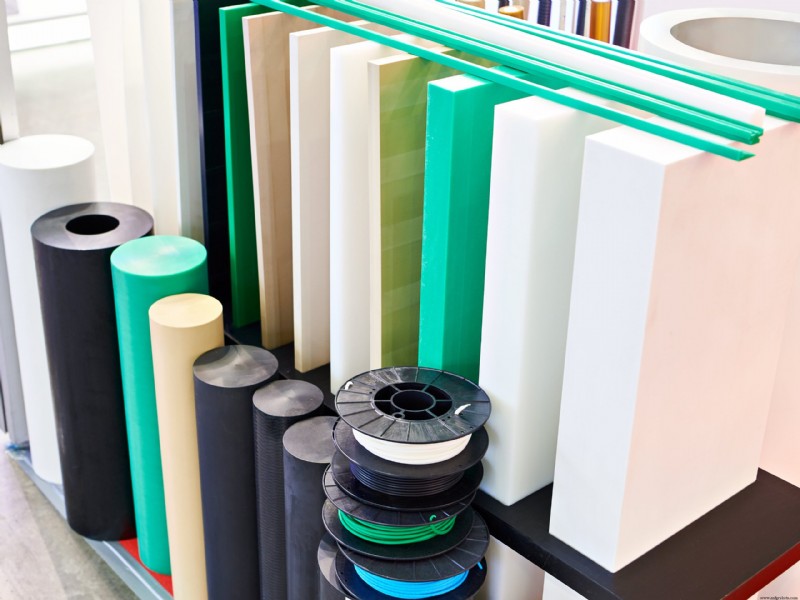
- Polyetherimide (PEI): PEI, algemeen bekend als ULTEM®, is een hoogwaardig kunststof- en productienietje. PEI is niet alleen sterk en gebruiksvriendelijk, maar is ook bestand tegen chemicaliën en vlammen en is bestand tegen extreem hoge temperaturen zonder zijn stabiele elektrische eigenschappen te verliezen. Om deze reden wordt PEI meestal gebruikt om producten te maken zoals printplaten, brillen, voedselbereidings- en sterilisatieapparatuur en vliegtuigonderdelen. Het is een van de weinige in de handel verkrijgbare amorfe thermoplastische polymeren die zijn mechanische integriteit bij hoge temperaturen behoudt.
- Polymethylmethacrylaat (PMMA): PMMA is een stijf thermoplastisch polymeer dat vaak acryl- of acrylglas wordt genoemd. Extreem breukvast, dit sterke en lichtgewicht materiaal is doorschijnend en bestand tegen weersinvloeden en UV-licht, waardoor het ideaal is voor toepassingen met weinig stress, zoals kassen, de afdekkingen van autolampen en richtingaanwijzers, of zonnepanelen. Het is echter belangrijk op te merken dat PMMA gevoelig is voor hoge temperaturen, schokken, slijtage en slijtage, en vatbaar is voor barsten onder zware belasting.
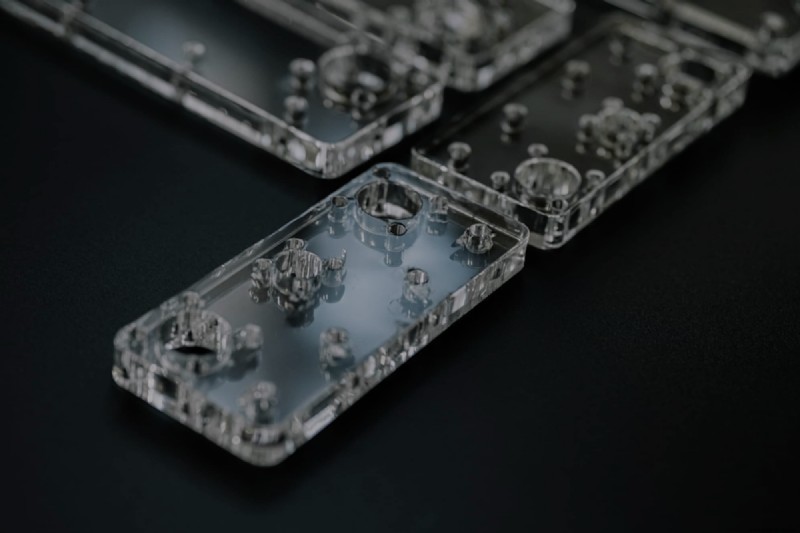
- Polyoxymethyleen (POM): Deze semi-kristallijne thermoplast van technische kwaliteit, algemeen bekend als Acetal of onder de merknaam Delrin®, biedt uitstekende maatvastheid, stijfheid en lage wrijving. Vanwege deze eigenschappen wordt acetaal vaak gebruikt om zeer nauwkeurige onderdelen te maken die worden gebruikt in toepassingen waar een hoge sterkte, duurzaamheid en een breed bedrijfstemperatuurbereik (-40 ° C tot 120 ° C) vereist zijn.
- Polypropyleen (PP): Deze kosteneffectieve kunststof is lichtgewicht, zeer goed bestand tegen chemicaliën in corrosieve omgevingen en bestand tegen de meeste organische oplosmiddelen, ontvettingsmiddelen en elektrolyten. Vergeleken met LDPE en HDPE heeft PP een lagere slagvastheid maar biedt het een betere treksterkte.
- Polytetrafluorethyleen (PTFE): PTFE, algemeen bekend als Teflon®, is een veelzijdig polymeer dat de voorkeur geniet vanwege zijn mechanische eigenschappen. Bestand tegen chemicaliën, temperatuur, licht, UV-stralen, water, weersinvloeden, vermoeidheid en hechting, wordt PTFE vaak aangetroffen in de coatings van anti-aanbakpannen, maar wordt ook gebruikt in halfgeleiders, pakkingen en zelfs sommige medische toepassingen. Hoewel PTFE een van de meest corrosiebestendige kunststoffen is, is het gevoelig voor kruipen en schuren.
- Polyvinylchloride (PVC): PVC is een van 's werelds oudste kunststoffen. Strak wit en stijf, PVC is een betaalbaar alternatief voor rubber waar al tientallen jaren veel vraag naar is. Met een sterke weerstand tegen licht, chemicaliën en corrosie, is PVC een populair materiaal in de gezondheidszorg, IT, transport, textiel en de bouwsector.
- Polyethyleen met ultrahoog moleculair gewicht (UHMW): UHMW, een taai, veelzijdig en zeer bewerkbaar plastic, kan worden gebruikt om onderdelen te maken met een hoge slijtvastheid en slijtvastheid, duurzaamheid en lage wrijvingscoëfficiënten. UHMW is doorgaans niet geschikt voor toepassingen met een hoge belasting of voor omstandigheden van meer dan 80 tot 100°C.
Metalen
Staalsoorten en roestvast staal, aluminium en zachte metalen zoals messing, brons, titanium en koper behoren tot de meest populaire bewerkbare metalen. Hoewel staal en aluminium het meest worden bewerkt, biedt elke familie van metalen een andere reeks fysieke eigenschappen en prijspunten.
- Aluminium: Aluminium zijn zachte, niet-magnetische metalen met een lage dichtheid die veel gemakkelijker te bewerken zijn dan staal. Vanwege hun lage treksterkte worden deze metalen vaak gelegeerd met andere materialen om de gewenste fysische eigenschappen te accentueren. Aluminium is over het algemeen ongeveer 1/3 van het gewicht van staal, wat betekent dat ze een betere sterkte-gewichtsverhouding bieden. Dit kan handig zijn bij het lichter maken van onderdelen. Ze zijn ook veel betere thermische en elektrische geleiders dan staal.
- Staal: Staalsoorten zijn metalen op ijzerbasis die zijn gelegeerd met koolstof en andere metalen, meestal met inbegrip van mangaan, fosfor of zwavel. Staal is over het algemeen sterker en duurzamer dan aluminium. Ze zijn echter ook zwaarder en moeilijker te bewerken zonder het gebruik van hardmetaal of ander speciaal gereedschap, wat de productiekosten kan verhogen.
- Roestvrij staal: Het belangrijkste verschil tussen staal en roestvrij staal is dat het laatste is gelegeerd met chroom in plaats van koolstof. Terwijl standaard staal gevoelig is voor roest en corrosie wanneer het wordt blootgesteld aan vocht en zuurstof, creëert het chroomgehalte in roestvrij staal een passieve chroomoxidelaag op het oppervlak van het metaal, waardoor wordt voorkomen dat het ijzer binnenin verder oxideert. Dit remt ook het vermogen van staal om elektriciteit te geleiden. Roestvast staal kan worden gelegeerd met andere metalen (waaronder molybdeen, nikkel of titanium) om de weerstand van een onderdeel tegen corrosie en hitte te vergroten.
- Zachte metalen: Zachte metalen zoals messing, brons, titanium en koper bieden een breed scala aan fysieke kenmerken die aantrekkelijk zijn voor specifieke toepassingen. Zachte metalen - vooral die met een hoog kopergehalte - kunnen echter moeilijker te bewerken zijn vanwege de hoge ductiliteit van koper. Het bewerken van zachte metalen kan bijdragen aan een verhoogde warmteontwikkeling op de snijplaats, grotere slijtage van het gereedschap en vreten (een gomachtige opbouw op de snijkant van het gereedschap). Met name titanium is ook minder stijf dan andere metalen en vereist daarom een stevige grip op het werkstuk om precisie en nauwkeurigheid te garanderen. Al deze factoren kunnen bijdragen aan hogere bewerkingskosten voor zachte metalen.
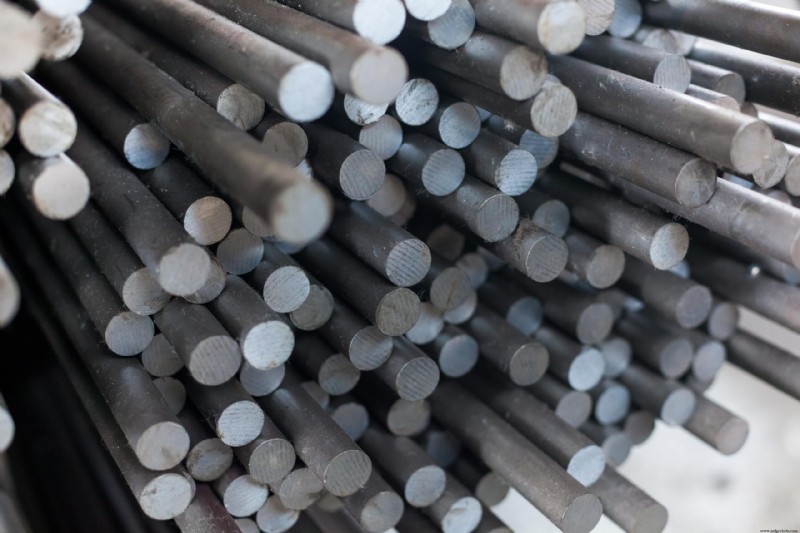
CNC oppervlakteafwerkingen en nabewerking
Nadat een onderdeel of component is bewerkt, moet het mogelijk een of meer afwerkingsprocessen ondergaan. Deze processen kunnen worden gebruikt om esthetische gebreken te verwijderen, het uiterlijk van een product te verbeteren, extra sterkte en weerstand te bieden, elektrische geleidbaarheid aan te passen en meer. Gangbare afwerkingsprocessen voor bewerkte onderdelen zijn anodiseren, poedercoaten en parelstralen. Het is echter ook gebruikelijk om onderdelen machinaal of gefreesd te laten als andere afwerkingen niet nodig zijn.
Algemene CNC-afwerkingsopties
- Anodiseren (aluminium): Anodiseren is een elektrochemisch proces waarbij aluminium- of titaniumlegeringen worden ondergedompeld in een elektrolytisch bad om de natuurlijke oxidelaag van een bewerkt onderdeel te verdikken om het dichter, elektrisch niet-geleidend en duurzamer te maken. Geanodiseerde afwerkingen beloven ook een goede dimensionale controle, waardoor ze het best kunnen worden gebruikt in hoogwaardige technische toepassingen, met name voor interne holtes en kleine onderdelen. Anodiseren biedt een van de meest esthetisch aangename afwerkingen voor CNC-gefreesde onderdelen, maar heeft een hogere prijs.
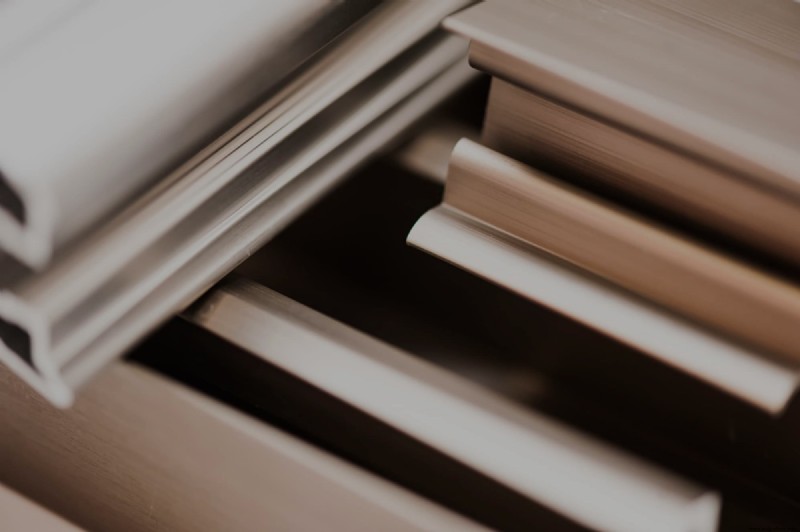
- Kralenstralen (metaal of plastic): Parelstralen maakt gebruik van een persluchtsysteem om miljoenen glasparels op het onderdeel af te vuren, waardoor gereedschapssporen en onvolkomenheden effectief worden verwijderd en kan worden gebruikt om een consistente korrelige, matte of satijnen oppervlakteafwerking te creëren. Parelstralen voegt geen chemische of mechanische eigenschappen toe en, in tegenstelling tot poedercoating die materiaal aan een onderdeel toevoegt, is het een reducerende afwerking, wat betekent dat het proces materiaal van het onderdeel verwijdert. Dit is een belangrijke overweging als uw onderdeel strikte toleranties heeft. Parelstralen is een van de meest betaalbare oppervlakteafwerkingen, maar moet handmatig worden uitgevoerd. De grootte en kwaliteit van de kraal zijn ook van invloed op de uiteindelijke afwerking.
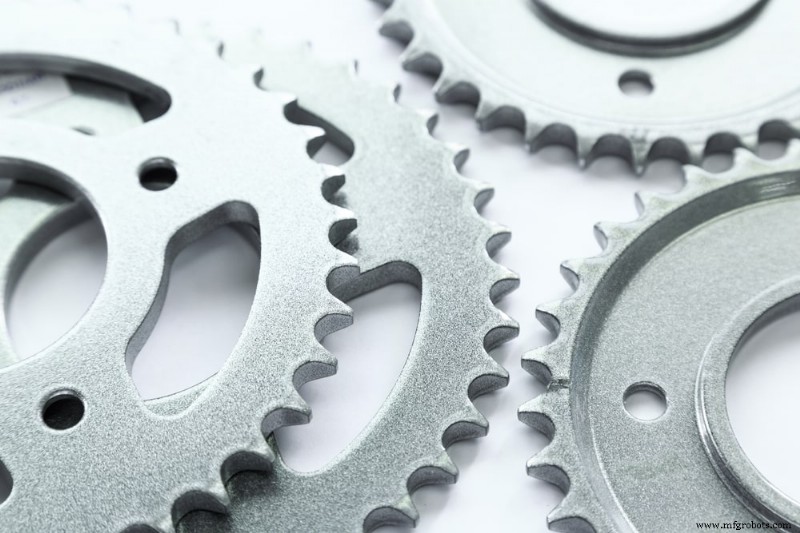
- Zwart oxide (staal, roestvrij staal, koper): Dit elektrochemische of chemische behandelingsproces creëert zwart ijzeroxide op het oppervlak van ferrometalen. Dit proces, ook wel zwart maken, oxideren of zwart passiveren genoemd, zet niet alleen een zwarte oxidelaag op het oppervlak van het metaal af. Integendeel, de chemische reactie tussen het ijzer in het metaal en de oxiderende zoutoplossing creëert een ijzeroxide genaamd magnetiet, dat een matzwart uiterlijk heeft. Dit proces verbetert de dimensionele stabiliteit en het esthetische uiterlijk van het onderdeel, terwijl de lichtreflectie van het oppervlak wordt verminderd, wat belangrijk is voor onderdelen die worden gebruikt in toepassingen met straling. Zwart oxiderend staal kan ook helpen bij het slijpen van gereedschappen zoals schroevendraaierpunten en boren.
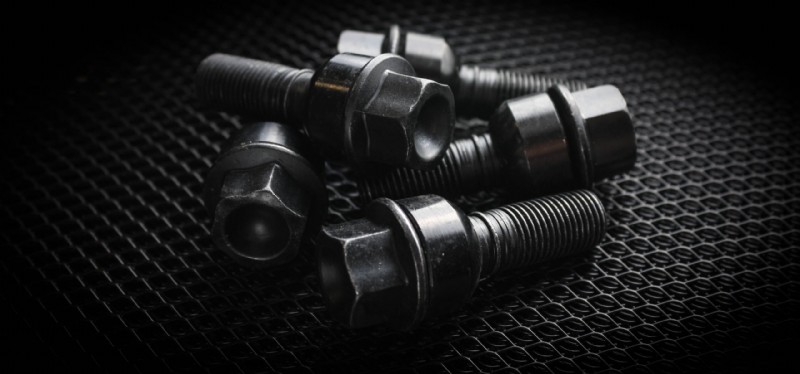
- Poedercoating (alle metalen): Poedercoaten is vergelijkbaar met spuiten. Het bewerkte onderdeel krijgt een grondlaag om het te beschermen tegen corrosie. Vervolgens wordt het onderdeel "gelakt" met een droge poedercoating uit een elektrostatisch spuitpistool en uitgehard in een oven die is verwarmd tot minimaal 200°C. Er kunnen meerdere lagen worden aangebracht om de dikte van de afwerking te vergroten, waardoor een dunne beschermende laag ontstaat op het onderdeel dat sterk, slijtvast en esthetisch aantrekkelijk is. Dit proces kan worden gecombineerd met parelstralen om de corrosieweerstand van het onderdeel te vergroten en een grotere uniformiteit in textuur en uiterlijk te creëren. In tegenstelling tot anodiseren is een gepoedercoate afwerking compatibel met alle metalen, is minder bros en biedt een grotere slagvastheid. Poedercoating geeft echter over het algemeen minder controle over de afmetingen dan een anodische afwerking en wordt niet aanbevolen voor gebruik in kleine componenten of interne oppervlakken. De hogere prijs van poedercoaten kan grotere productieruns ook duur maken.
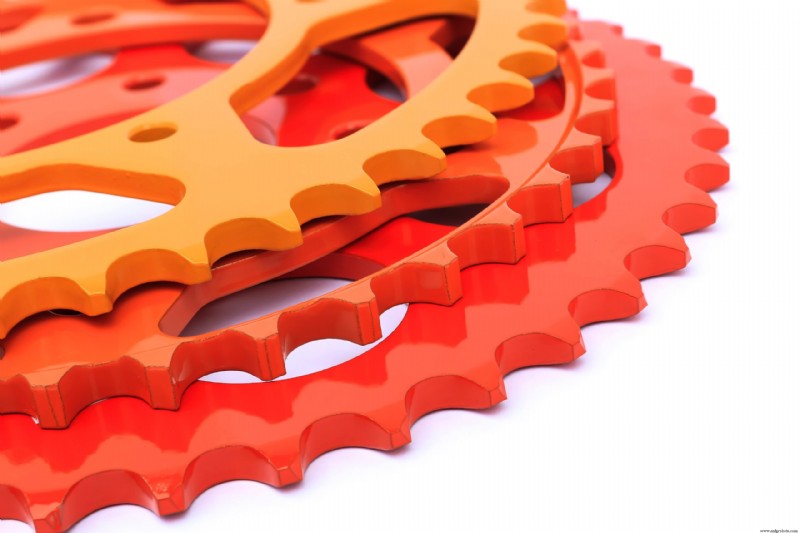
- Als machinaal bewerkt (metaal of plastic): Het niet toepassen van afwerkingsprocessen op bewerkte onderdelen wordt een "as-machined" of "as-milled" afwerking genoemd. Het onderdeel heeft kleine maar zichtbare gereedschapssporen en vlekken. As-machinaal bewerkte onderdelen hebben de kleinste maattoleranties en zijn uiterst betaalbaar om te produceren omdat nabewerking niet nodig is. Dit is ideaal voor toepassingen waarbij dimensionale integriteit belangrijker is dan esthetiek. Het is echter belangrijk op te merken dat zonder extra afwerking of beschermende coating, de oppervlaktehardheid van de machine ze vatbaar maakt voor inkepingen, schuren en krassen.
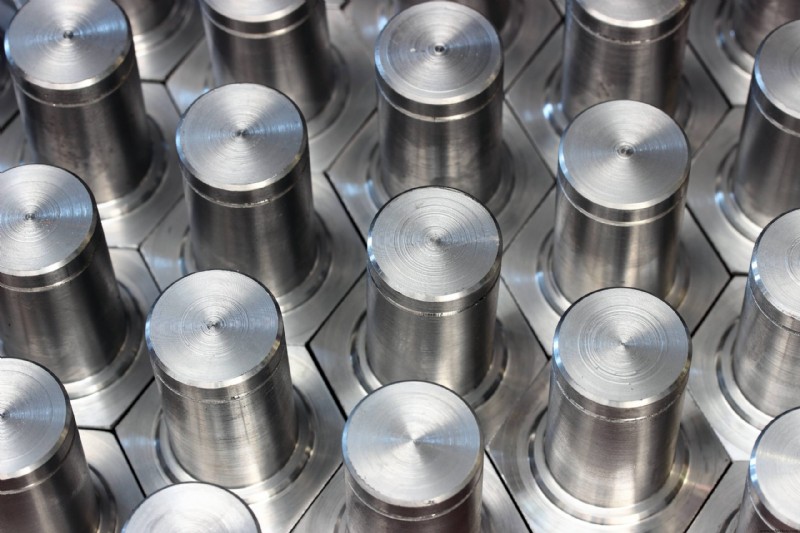
De juiste materialen en afwerking kiezen
Het selecteren van materialen en nabewerkingsopties voor uw onderdeel is sterk afhankelijk van hoe en waar uw onderdeel zal worden gebruikt. Belangrijke overwegingen bij het eindgebruik voor het selecteren van uw onderdeelmateriaal en oppervlakteafwerking zijn onder meer:
- Omgevingsfactoren: De omgevingsomstandigheden van de eindtoepassing van een bepaald onderdeel spelen een belangrijke rol bij het bepalen welke materialen en behandelingen ideaal zijn. Er moet rekening worden gehouden met factoren zoals hitte, kou, vlammen, UV-straling, blootstelling aan chemicaliën of autoclaveren en meer om de levensvatbaarheid van het onderdeel te garanderen.
- Elektrische factoren: Of een onderdeel geleidende of isolerende eigenschappen vereist, is een andere kritische overweging. Als u weet dat uw onderdeel elektriciteit moet geleiden, kunt u een geleidend materiaal zoals koper kiezen, terwijl een materiaal zoals Nylon 66 geschikt zou zijn bij het zoeken naar een goede isolator.
- Mechanische factoren: Onderdelen die bedoeld zijn om zware belastingen, slijtage of andere externe krachten te weerstaan, moeten zijn gemaakt van materialen die bestand zijn tegen die krachten. Door de meest wenselijke of noodzakelijke eigenschappen voor een onderdeel te identificeren, zoals flexibiliteit, slagvastheid, trek- of druksterkte, kunnen teams bepalen welke materialen het beste passen.
- Cosmetische overwegingen: Hoewel esthetiek voor sommige onderdelen van ondergeschikt belang kan zijn, is dit niet het geval voor veel consumentenproducten. Sommige onderdelen of toepassingen vereisen mogelijk materialen met bijzondere cosmetische opties als het gaat om kleur, transparantie of oppervlakteafwerking.
- Toleranties: Bij de fabricage wordt enige mate van variatie tussen onderdelen verwacht, en maattoleranties verwijzen naar het bereik van acceptabele variatie waarbinnen haalbare onderdelen moeten vallen. Nauwere toleranties zijn arbeidsintensiever en kostbaarder om herhaaldelijk te bereiken, maar kunnen noodzakelijk zijn op basis van hoe een onderdeel wordt gebruikt.
Ontwerpen voor CNC-bewerking
Het ontwerpen van een onderdeel van hoge kwaliteit dat zal presteren zoals verwacht, is slechts de helft van de uitdaging. U moet het onderdeel ook op een efficiënte en kosteneffectieve manier kunnen bewerken. Ontwerp voor maakbaarheid (DFM) is het procesraamwerk dat helpt bij het integreren van hoe een onderdeel wordt gemaakt met het onderdeelontwerp. DFM is van cruciaal belang voor de productie en beïnvloedt alles, van productietijdlijnen en -kosten tot operationele efficiëntie en de kwaliteit van het onderdeel zelf. De meest voorkomende ontwerpoverwegingen voor CNC-bewerking zijn:
Diepe zakken:
Functies zoals diepe of smalle zakken en sleuven vereisen langer gereedschap om goed te kunnen bewerken. Langere snijgereedschappen zijn echter gevoeliger voor breuk en zijn vaak minder nauwkeurig vanwege bewerkingstrillingen of geratel. Diepe functies vereisen doorgaans ook meerdere sneden om goed te kunnen bewerken, wat zowel de bewerkingstijd als de productiekosten verhoogt, vooral omdat er waarschijnlijk kleinere gereedschappen nodig zullen zijn om de nabewerkingsgangen te voltooien. Als sleuven of diepe zakken moeten worden bewerkt, probeer dan ofwel de diepte van het element zo veel mogelijk te verkleinen of het oppervlak van de dwarsdoorsnede van de zak te vergroten. De diepte van een zak of sleuf mag niet meer dan 3x de diameter van het kleinste benodigde gereedschap zijn.
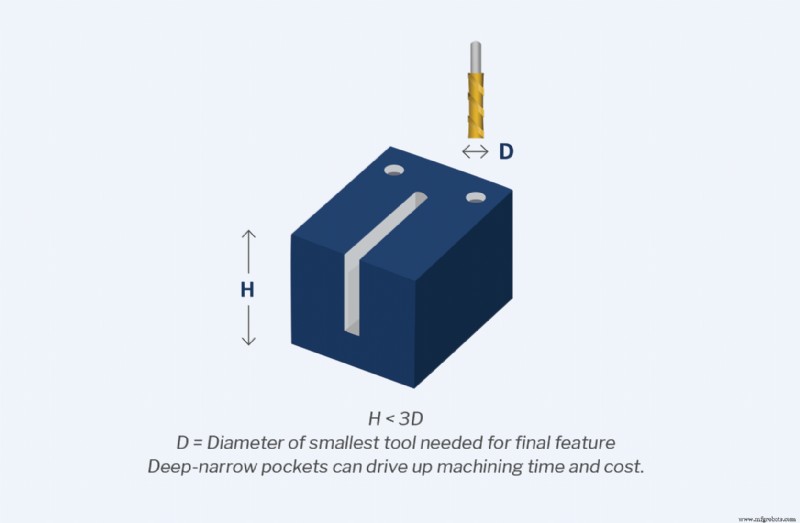
Smalle regio's:
Smalle kenmerken beperken de grootte van bruikbare snijgereedschappen. Dit kan een uitdaging vormen voor fabrikanten omdat lange gereedschappen met een kleine diameter gevoelig zijn voor klapperen en breken. Net als bij diepe kenmerken, moeten smalle gebieden niet minder zijn dan 3x de diameter van het kleinste snijgereedschap. Door de diepte van deze functies te minimaliseren, kunt u kortere snijgereedschappen met een grotere diameter gebruiken, waardoor het geratel van de machine wordt verminderd.
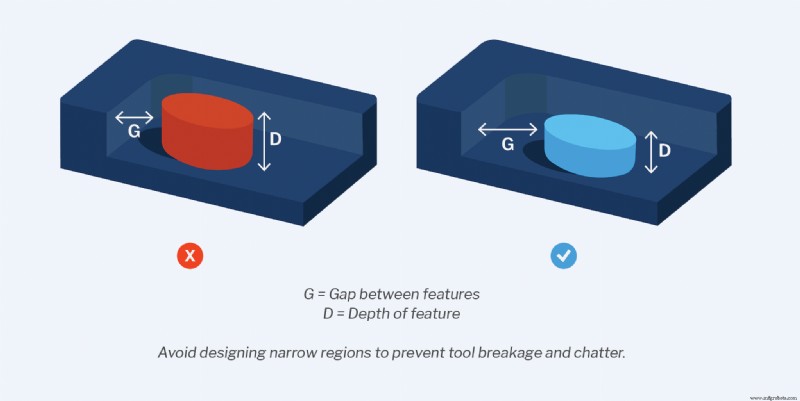
Scherpe binnenhoeken:
CNC-vingers zijn cirkelvormig, wat het moeilijk maakt om scherpe interne hoeken te bewerken omdat de bits een hoekradius achterlaten. Hoewel er methoden zijn om scherpe interne hoeken te bewerken, zijn deze processen vaak kostbaar. Over het algemeen moeten scherpe binnenhoeken worden vermeden voor bewerkte onderdelen. Interne hoekradii moeten ook groter zijn dan de radius van het beoogde snijgereedschap. Door interne radii groter te ontwerpen dan het snijgereedschap, kan de machine een vloeiende overgang tussen muren creëren. Daarentegen zal een interne radius die even groot is als het snijgereedschap de machine dwingen om een plotselinge richtingsverandering uit te voeren, wat resulteert in een minder gladde afwerking.
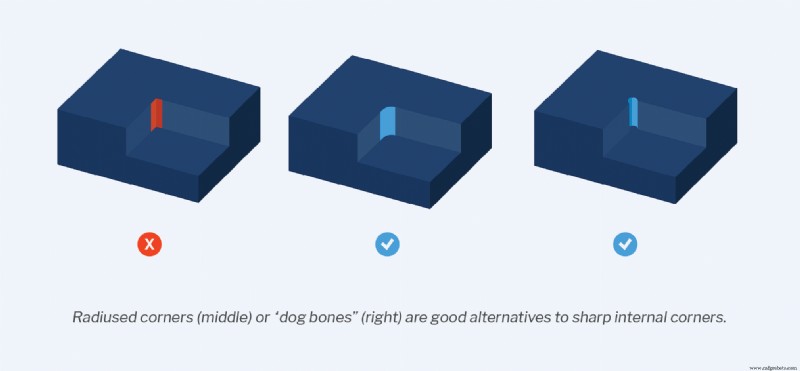
Ontoegankelijke functies:
Functies zoals verzonken gaten - die openen in een andere zak of zakken met negatieve tocht - kunnen een grote uitdaging vormen voor productieteams. Deze ontwerpkenmerken nemen aanzienlijk meer tijd in beslag om te bewerken, omdat het moeilijk kan zijn om het snijgereedschap toegang te geven. Het is van cruciaal belang ervoor te zorgen dat snijgereedschappen vrij toegang hebben tot alle functies van een onderdeel zonder te worden geblokkeerd door een andere functie.
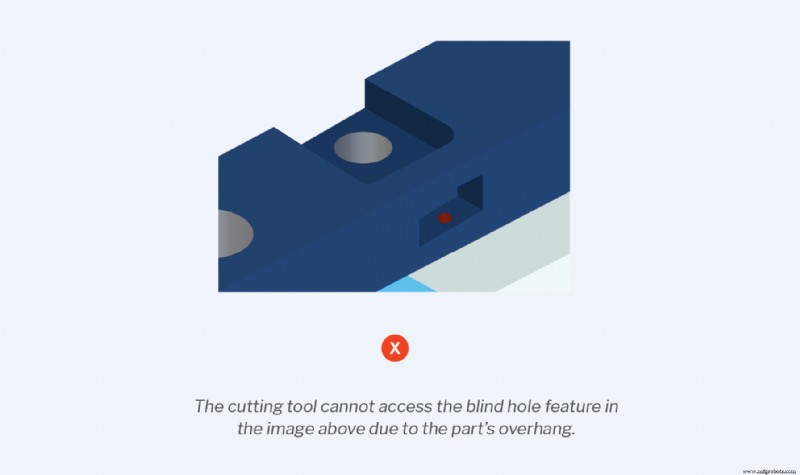
Buitenfilets:
Buitenfilets, of afgeronde hoeken langs de bovenrand van pockets, nokken, sleuven en andere kenmerken, vereisen aangepaste snijgereedschappen die worden ondersteund door een nauwkeurige machinale opstelling - een koppeling die snel duur kan worden. Het afschuinen of afschuinen van de buitenranden kan deze kosten helpen voorkomen.
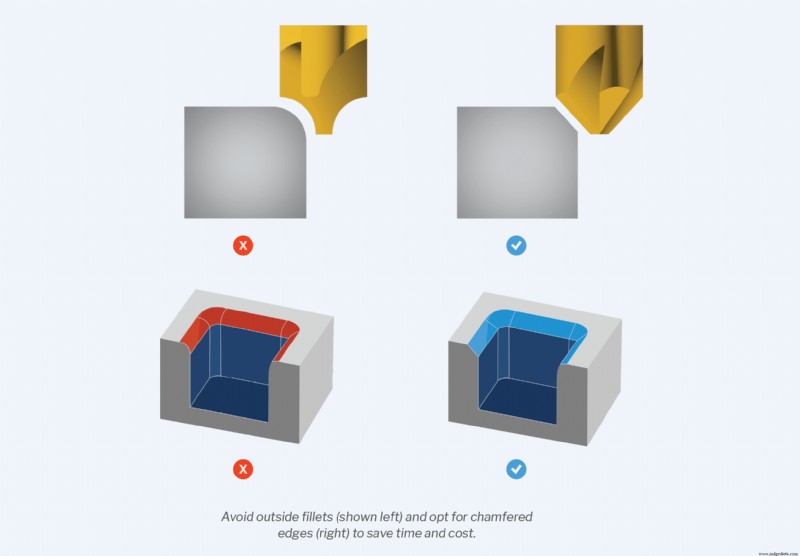
Wanddikte:
Dunne wanden kunnen problemen veroorzaken voor zowel metalen als plastic onderdelen en moeten waar mogelijk worden vermeden. Dunne metalen wanden zijn bijvoorbeeld gevoeliger voor klapperen, wat een negatieve invloed heeft op de nauwkeurigheid van het onderdeel en de oppervlakteafwerking. Kunststof onderdelen met dunne wanden hebben ook meer kans om krom te trekken of zacht te worden. De minimale wanddikte voor metalen onderdelen moet 0,03” (0,762 mm) en 0,06” (1,524 mm) zijn voor plastic onderdelen.
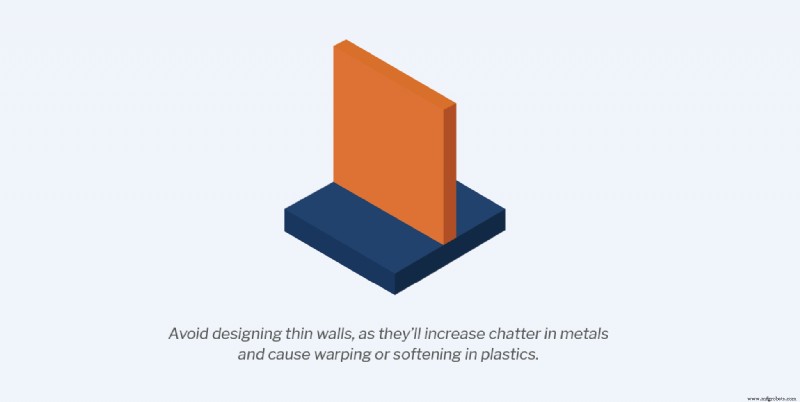
Gaten met platte bodem:
Gaten met een vlakke bodem zijn niet alleen moeilijk te bewerken, maar ze veroorzaken ook vaak moeilijkheden bij latere bewerkingen. Over het algemeen moeten productteams blinde gaten met vlakke bodems vermijden in plaats van standaard spiraalboren, die gaten maken met kegelvormige bodems.
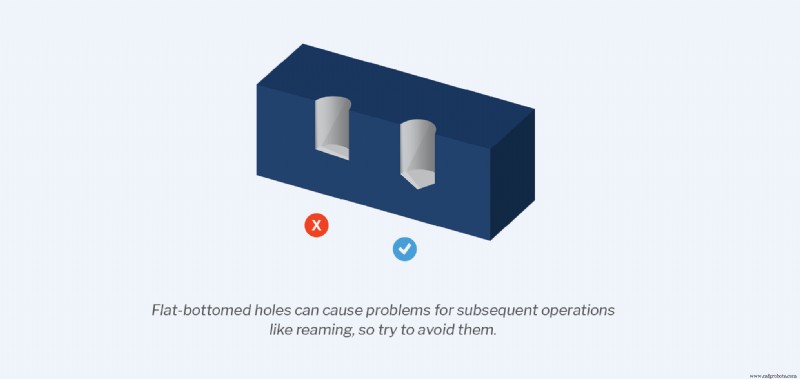
Onderdelen met schroefdraad:
Bij het bewerken van interne of externe schroefdraad zijn er een paar verschillende ontwerpoverwegingen.
Voor binnendraad:
- Voeg een verzinking toe aan het einde van interne draden.
- Verminder het aantal threads waar mogelijk. De meeste spanning van een onderdeel valt eigenlijk op de eerste drie threads, dus het aantal verhoogt
- van threads levert afnemende opbrengsten op.
- Gebruik standaardformulieren en -formaten.
- Kies voor grove draden om de kosten laag te houden.
Voor externe threads:
- Neem een afschuining op in alle schroefontwerpen.
- Vermijd het afsluiten in de buurt van de schouder van gebieden met grote diameters.
- Gedraaide buitendraad moet een reliëfgroef hebben.
- Gebruik kortere uitwendige schroefdraad, tenzij het onderdeel specifiek een hoge schroefdraadsterkte vereist.
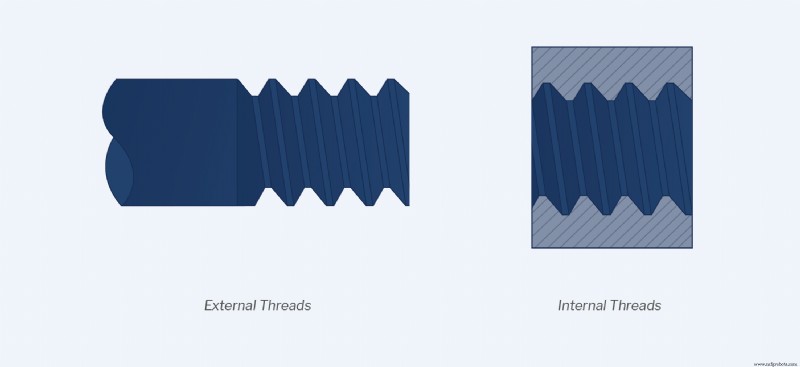
Boor in- en uitgangen:
Als het oppervlak van een werkstuk niet loodrecht op de as van een boor staat, zal de boorpunt afdwalen wanneer deze in contact komt met het materiaal. Om ongelijkmatige uitgaande bramen te minimaliseren en het braamverwijderingsproces te stroomlijnen, moet u ervoor zorgen dat de gatkenmerken begin- en eindvlakken hebben die loodrecht op de booras staan.
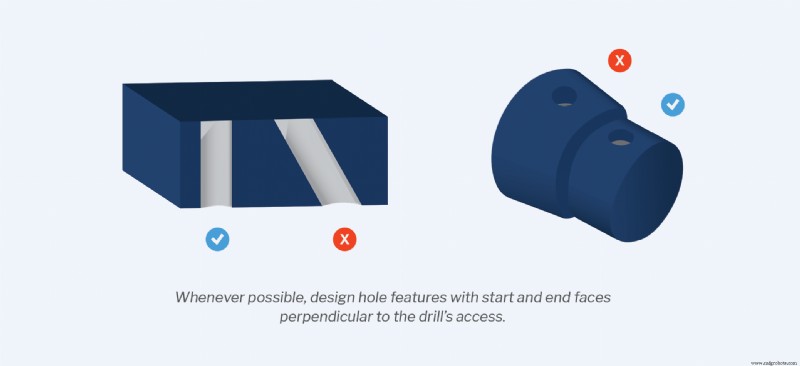
Een checklist om kosten te verlagen
Onderdelen met complexe ontwerpen of fabricageprocessen kunnen een aantal stroomafwaartse effecten hebben. Complexiteit kan de bewerkingstijd en -kosten verhogen, kansen op fouten introduceren en het voor eindgebruikers moeilijk maken om het exacte gebruik van componenten of onderdelen te begrijpen. Door te scheiden welke kenmerken en ontwerpkenmerken essentieel zijn voor de levensvatbaarheid van het onderdeel, en die welke wenselijk maar niet-kritiek zijn, wordt onnodige complexiteit uit het ontwerp en de bewerkingsbewerkingen van een onderdeel verwijderd.
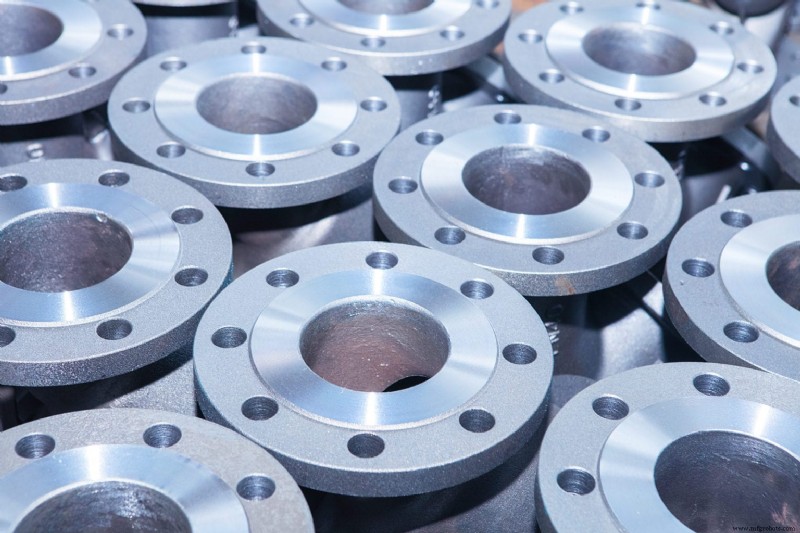
Hoewel de meeste CNC-bewerkingstaken meer dan één instellingsoriëntatie vereisen, wilt u het aantal oriëntaties per onderdeel tot een minimum beperken. Als u bijvoorbeeld een werkstuk drie keer moet omdraaien voordat de snijgereedschappen toegang hebben tot alle functies, zal dit de kosten verhogen, omdat bij elke opstelling het onderdeel opnieuw moet worden gemonteerd en de machine op nul moet worden gezet om de juiste assen, en het uitvoeren van een nieuw G-code programma. Machines met 5 assen zullen in dit opzicht beter in staat zijn, omdat ze meer functies kunnen bereiken zonder dat er meerdere instellingen nodig zijn, hoewel dit afhankelijk is van de geometrie van een bepaald onderdeel.
Het minimaliseren van het aantal benodigde snijgereedschappen is een andere manier om de kosten te verlagen. As much as possible, try to keep radii consistent so that fewer tools are needed to machine internal corners. Likewise, avoid very small details where possible. Smaller cutting tools aren’t able to cut as deep into the workpiece and are also more prone to breaking. Typically, the smallest internal features that can be machined are 0.0394” (1mm), though holes can go as small as 0.0197” (0.5mm).
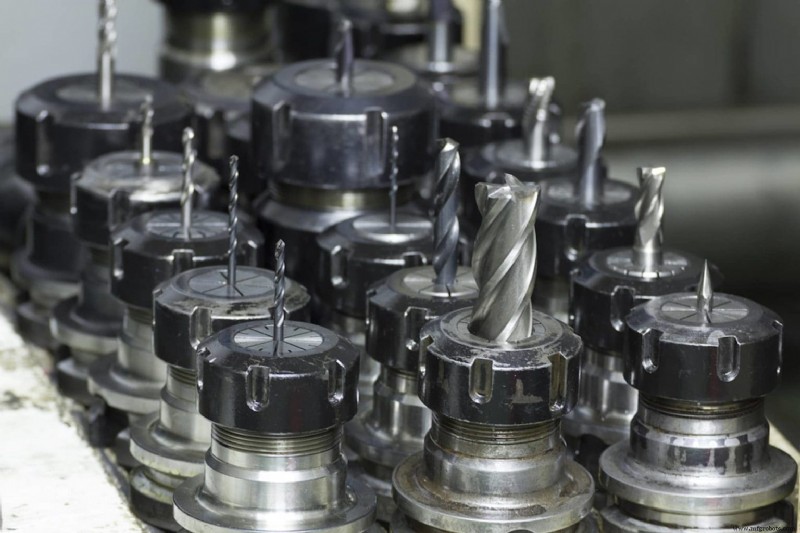
Choose your critical dimensions thoughtfully. Not every dimension requires inspection or is critical to the viability of the part, so focus your attention on those that are most essential. Determining how precise specific features need to be will allow you to adjust tolerances accordingly, reduce costs, and streamline the manufacturing process. Make sure that tolerances are still within machineable limits, adhere to given standards, and account for tolerance stacking.
Avoid over-dimensioning your part, as well. Unclear part drawings defeat the purpose of geometric dimensioning and tolerancing, which is to clarify and streamline communication. At Fast Radius, we recommend that you align drawing datums with the CNC coordinate system, as using consistent datum reference frames between machining and measurement systems is more likely to ensure parts are accurately located.
If possible, ensure all datums — points, surfaces, or axes used as references for measurement — reference the same setup. If a datum was machined in a previous setup, it becomes more difficult to hold tight tolerances after a setup change. Finally, be conscious about your datums. Choosing reference datums that are easy to measure from will ease manufacturing.
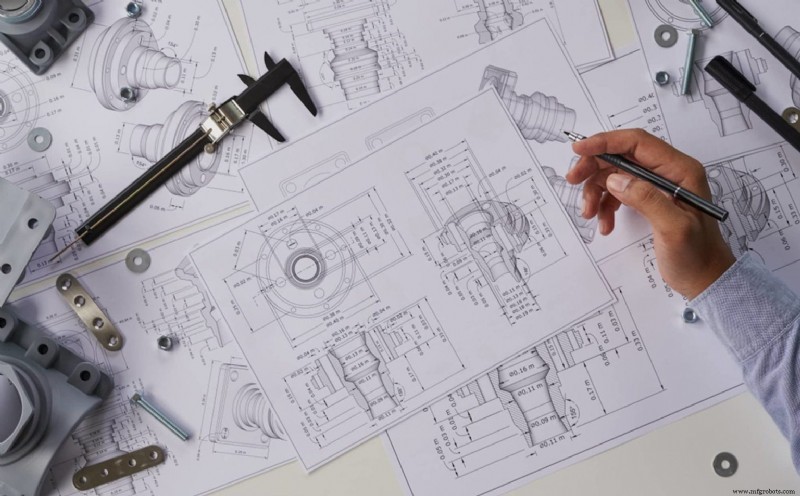
4. Tailor inspection levels
Similar to balancing your tolerances, strategically applying the right inspection levels can help reduce costs and optimize the production processes. Typical inspection options may include a visual inspection of the part, checking part dimensions using hand tools, or a first article inspection (FAI) where the first manufactured part is checked to ensure all requirements have been met. More in-depth inspections require more time and labor, which increases manufacturing costs.
Increasing the number of parts that you inspect will also increase the cost of production, so it’s important that you select the right sampling plan to ensure confidence across the entire order. At Fast Radius, our default sampling rate is based on ANSI ASQ Z1.4 Level 2.
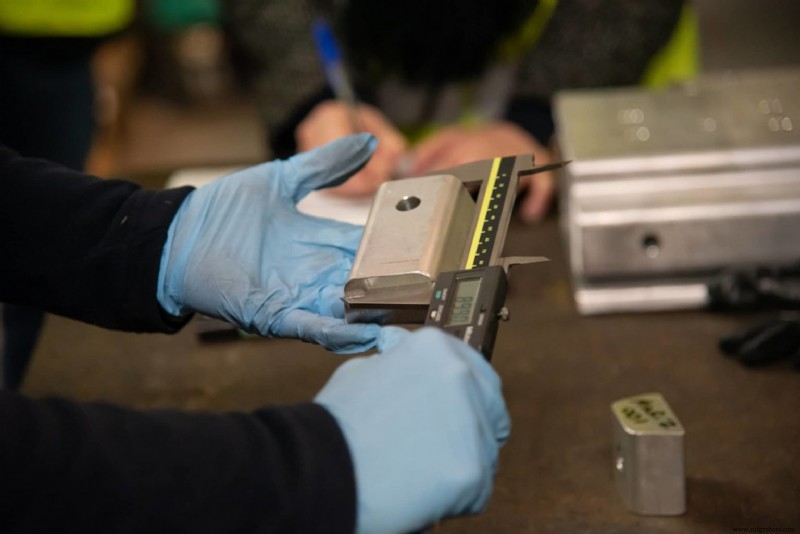
5. Design to common stock sizes
Designing parts to common stock sizes can help streamline the manufacturing process by minimizing the amount of material that needs to be removed from the workpiece. For example:if it’s acceptable for a part surface to retain its stock finish — that is, if the surface can be rougher than 125 μin Ra — and it does not need to be machined, you have an opportunity to reduce machining time without sacrificing part quality.
This is why knowing the common stock sizes for various materials is important. Metals, for instance, are typically available in a number of stock forms, including sheets, rods, bars, or tubes, which can be purchased according to dimensions like length, width, thickness, and diameter.
Keep in mind that metric sizes are more commonly available in Asia, while imperial sizes are more commonly available in the U.S.
6. Minimize deformation risk
Removing a large amount of material from a workpiece can cause the material to deform. This requires additional processing during machining to prevent deformation, leading to higher costs. Plastics have a higher risk of deformation than metals.
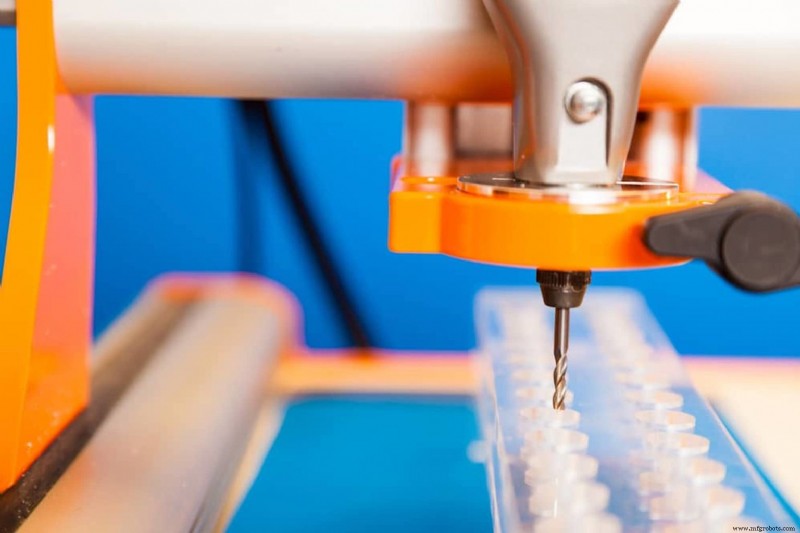
7. Choose your material carefully
The material you pick has a significant impact on the overall cost of your part. For example, metals are generally more expensive than plastics. Avoid over-engineering your parts and consider whether a specific grade or material certificate is required for the part. If a generic material can fulfill the part’s requirements or multiple materials can be accepted, select the less expensive material to keep costs low.
The machinability of the material should also be taken into consideration. Steels, for example, are typically more difficult to machine, which leads to higher costs because steel parts take longer to machine and increase wear-and-tear on cutting tools.

Common applications for CNC machining
Many industries rely on CNC machining processes to produce reliable, accurate parts that meet precise specifications and regulatory requirements, including the aerospace, automotive, medical device, electronics, and commercial parts manufacturing sectors.
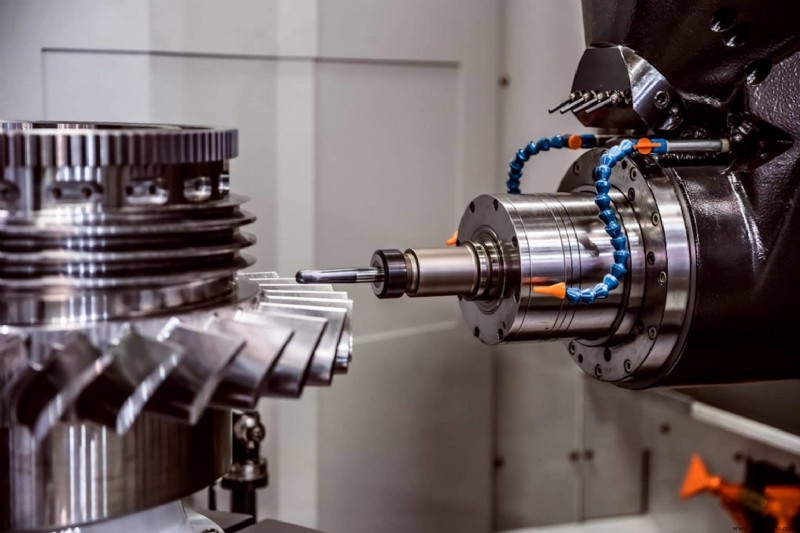
Aerospace parts are held to high quality, testing, and regulatory standards in order to ensure proper function, fit, and safety. CNC machining is an excellent fit for creating plastic and metal parts with extremely tight tolerances that satisfy the aerospace manufacturer’s need for an incredible degree of precision and a range of highly specialized parts. The same is true for automotive components.
CNC machining can also be used to create a variety of medical devices, from implants to surgical implements to components for medical electronics.
Care and precision are critical when producing these sorts of devices and tools, as they are held to additional safety standards and requirements. Semiconductors and electronics components also have incredibly stringent precision requirements and tolerance standards, given their size and complexity. As a process, CNC machining has few material limitations, allowing it to be used with conductive materials like silicon. Many commercial parts — from aluminum castings and extrusions to steel and plastic parts — can also be machined.
Another common application for CNC machining is tooling, or the process of creating the various components, tools, machinery, and master patterns that will be used in production. Tooling is an integral part of every manufacturing and molding process and encompasses items like molds, jigs, and fixtures.
Starting your CNC machining project with Fast Radius
At Fast Radius, we make it simple and straightforward to get quality parts through our CNC machining service. To get started, visit os.fastraidus.com, upload your part designs, and you’ll receive instant DFM feedback. The site also allows you to manage designs and orders from a single, intuitive interface.
When you choose Fast Radius, you’re choosing to work with a seasoned group of experts. You’ll receive the full support of our team of engineers, customer success managers, account executives, and others across the business. We’ll also leverage options for domestic and international CNC machining to ensure that your project is carried out as efficiently as possible, without sacrificing quality.
Contact us today to experience the Fast Radius difference or click here to download our comprehensive guide as a PDF.
Klaar om uw onderdelen te maken met Fast Radius?
Start uw offerteIndustriële technologie
- De essentiële gids voor 5-assige CNC-bewerking
- CNC-bewerking in de auto-industrie
- Een gids voor het kiezen van het beste CNC-materiaal voor bewerking
- Wat is AIaaS? De ultieme gids voor AI as a Service
- De ultieme gids voor onderhoudsbeheer
- Koude elektriciteit:ultieme basisgids
- Circuit Trace - De ultieme gids
- De kosten van CNC-bewerking
- De complete 5-assige CNC-freesmachinegids
- De toekomst van CNC-bewerking
- 5-assige CNC-bewerking:de complete gids