3 tips voor het ontwerpen van een goed nauwkeurige kunststof mal
Wat betreft de functie van kunststof matrijzen en de bijzondere eigenschappen van het gieten van kunststof producten, waar moet op worden gelet bij het matrijzen maken wordt geïntroduceerd.
De functie van de kunststof mal is tweeledig:de geplastificeerde kunststof de gewenste vorm, kwaliteit, koeling en het uitwerpen van het kunststof onderdeel. De mal bepaalt de eigenschappen, vorm, maat en nauwkeurigheid van het uiteindelijke kunststof onderdeel. Daarom is het ontwerp van een geavanceerde en redelijke spuitgietstructuur is de sleutel om aan de kwaliteitseisen te voldoen, de productkwaliteit is stabiel en de beste economische voordelen worden bereikt.
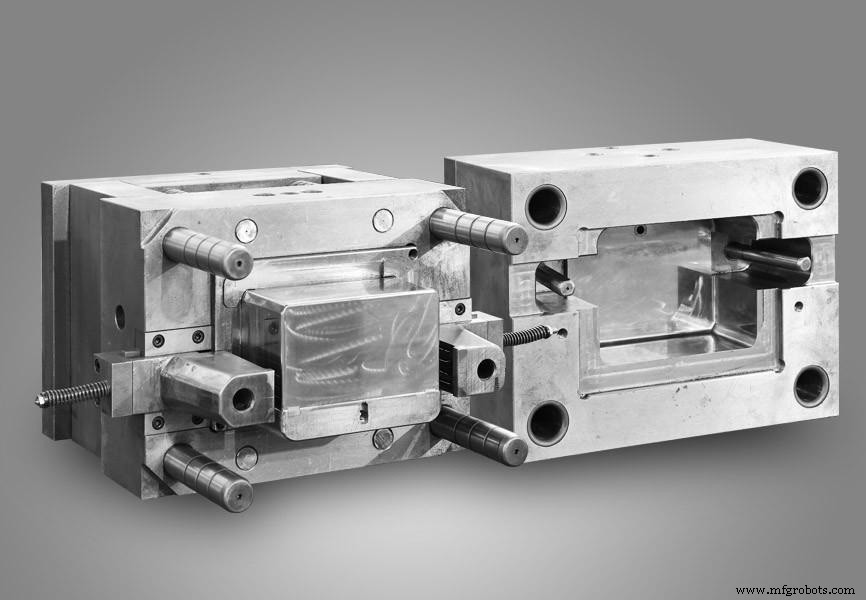
3 principes voor het ontwerpen van mallen
Om goed werk te leveren bij het ontwerpen van plastic matrijzen, moeten we de volgende principes begrijpen:
1. Redelijke selectie van scheidingsoppervlak
Om het product en het aggregaat uit de mal te kunnen verwijderen, moet de mal zijn voorzien van een scheidingsvlak. Het scheidingsoppervlak is een belangrijke factor bij het bepalen van de structuur van de matrijs. De instelling van het scheidingsoppervlak bepaalt de structuur en het fabricageproces van de matrijs, en beïnvloedt de vloei van de smelt en het ontvormen van de kunststof onderdelen. Het algemene selectieprincipe van het scheidingsoppervlak is om de kwaliteit van de plastic onderdelen te waarborgen, de vormstructuur te vereenvoudigen en het ontvormen te vergemakkelijken. Houd rekening met de volgende factoren bij het kiezen:
(1) Het mag niet op een opvallende plaats worden geplaatst en de vorm beïnvloeden. Scheidingsvlakken laten onvermijdelijk sporen achter op plastic onderdelen. Het is het beste om het gladde buitenoppervlak van het product niet te kiezen.
(2) Er zal daardoor geen doorzakking worden gevormd. Dat wil zeggen dat de keuze van het scheidingsoppervlak bevorderlijk moet zijn voor ontvormen en dat het trekmechanisme van de zijkern zoveel mogelijk moet worden vermeden. Voor dit doel moet het scheidingsoppervlak worden gekozen op de grootste maat van het plastic onderdeel. Zie afbeelding 1. Aangezien er aan beide uiteinden van de slangverbinding weinig doorhangende secties zijn, wordt de "scheidingslijn voor verticale scheiding" gebruikt.
(3) Het moet zich op een plaats bevinden waar verwerking gemakkelijk is. Zoals getoond in figuur 2, bevindt de scheidingslijn van het handvat van de tandenborstel zich op het oppervlak met de maximale breedte van het product, en het gevormde product kan gemakkelijk uit de vorm worden gehaald. Of de lijn voor het passen van de mal is consistent met de vormcurve en de verwerking is eenvoudig. De scheidingslijn die wordt getoond in figuur 3(a) is in een fasevorm, wat het moeilijk maakt om mallen te maken en gegoten producten te verwerken. Fig. 3(b) gebruikt rechte lijnen of gebogen oppervlakken om de verwerking te vergemakkelijken. Figuur 4 is de scheidingslijn van het strijkijzer.
Uit de bovenstaande analyse blijkt dat het ontwerp van het scheidingsoppervlak gebaseerd moet zijn op de gebruiksvereisten van de plastic onderdelen, de prestaties van de plastic onderdelen, de technische parameters van de injectiemachine en de matrijsverwerking.
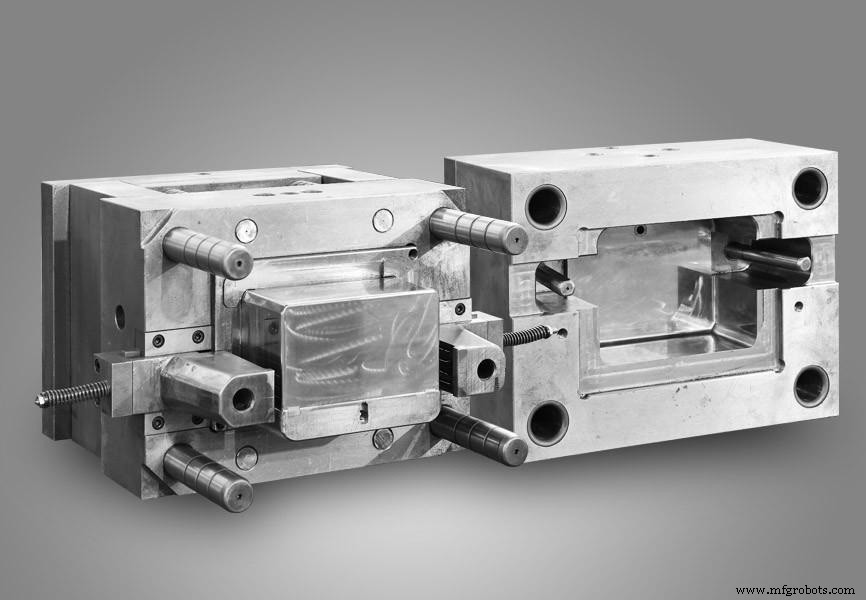
2. Redelijke selectie van scheidingsoppervlak
Om het product en het aggregaat uit de mal te kunnen verwijderen, moet de mal zijn voorzien van een scheidingsvlak. Het scheidingsoppervlak is een belangrijke factor bij het bepalen van de structuur van de matrijs. De instelling van het scheidingsoppervlak bepaalt de structuur en het fabricageproces van de matrijs, en beïnvloedt de vloei van de smelt en het ontvormen van de kunststof onderdelen. Het algemene selectieprincipe van het scheidingsoppervlak is om de kwaliteit van de plastic onderdelen te waarborgen, de vormstructuur te vereenvoudigen en het ontvormen te vergemakkelijken. Houd rekening met de volgende factoren bij het kiezen:
- Grootte van raster
De diepgangshoek varieert afhankelijk van het rastertype, de grootte en de grootte van het totale oppervlak van het rastergedeelte. Wanneer de rastersteek (P) kleiner is dan 4 mm, moet de diepgangshoek ongeveer 1/10 zijn; als de grootte van het rastersegment (C) groter is, moet de diepgangshoek worden vergroot; als de roosterhoogte 8 mm overschrijdt, moet de trekhoek worden vergroot. Als de afmeting van het roostersegment (C) groot is, maak dan een rooster van minder dan 1/2H in de holte van de beweegbare malzijde van het vormproduct.
3. Uniforme wanddikte
De wanddikte van kunststof onderdelen is een belangrijk constructief element, dat wordt bepaald door de gebruikseisen en proceseisen en heeft een grote invloed op het proces. Daarom is het erg belangrijk om de wanddikte van kunststof onderdelen redelijk te kiezen.
In termen van technologie, als de wanddikte te klein is, is de stromingsweerstand van het plastic in de holte groot en is het moeilijk te vormen, vooral voor complexe vormen en grote plastic onderdelen, die vatbaar zijn voor vulfouten of verhoog de injectiedruk; de wanddikte is te groot. , verhoogt niet alleen de kosten, maar verlengt ook de koeltijd, verlengt de vormcyclus, vermindert de productie-efficiëntie en is vatbaar voor defecten zoals krimpgaten en bellen. De wanddikte moet overal uniform zijn, maar vanwege de structuur van het plastic onderdeel, of de wanddikte moet tijdens het vormen worden gewijzigd en de wanddikte moet om economische redenen op de juiste manier worden aangepast. Bij het bepalen van de wanddikte moet met de volgende punten rekening worden gehouden:
- Structurele sterkte.
- ontvormkracht.
- kan het effect gelijkmatig verspreiden.
- voorkom barsten van het ingebedde metalen onderdeel (de thermische uitzettingscoëfficiënt van het vormmateriaal is anders dan die van het metalen materiaal en er ontstaan gemakkelijk scheuren bij het krimpen).
- De structuur belemmert de doorstroming en voorkomt onvoldoende vulling. De waarden van wanddikte (t) voor mogelijke vulafstand (L) voor verschillende vormmaterialen zijn samengevat in Tabel 1. De keuze van wanddikte is afhankelijk van het type kunststof en de grootte van het vormdeel. Voor kleine plastic onderdelen van thermohardende kunststoffen is de wanddikte 1,5 ~ 2,5 mm, voor grote, 3,2 ~ 8 mm, en het plastic met een slechte vloeibaarheid neemt de grotere waarde, maar over het algemeen niet meer dan 13 mm. Thermoplasten hebben een goede vloeibaarheid en zijn gemakkelijk te vormen dunwandige plastic onderdelen, meestal 1 ~ 4 mm, en de dunste kan 0,25 mm bereiken.
Beste fabrikant van plastic matrijzen in China - JTR
JTR is professioneel in een groot aantal CNC-bewerkingsdiensten, voor het maken van matrijzen zijn we meer dan alleen professioneel, we hebben er tientallen jaren ervaring in en onze klanten komen uit veel verschillende landen. Bij JTR kunt u gratis matrijsontwerpadvies krijgen van ons ontwerpteam. Vraag gerust om hulp.
Industriële technologie
- 5 tips voor het ontwerpen van plaatwerk
- Plaatwerkontwerp:tips en trucs
- Rol van fabrikanten van kunststof spuitgietmatrijzen
- 5 ontwerptips voor RIM
- Ontwerptips voor gietvormen
- Ontwerptips voor polyurethaangieten
- 4 tips voor het ontwerpen van magazijnstellingen
- Tips voor snelle lay-out
- Ontwerptips voor spuitgieten
- Stereolithografie (SLA) 3D-printontwerptips
- Polyjet 3D-printontwerptips