Aluminium extrusieproces:een gedetailleerd overzicht
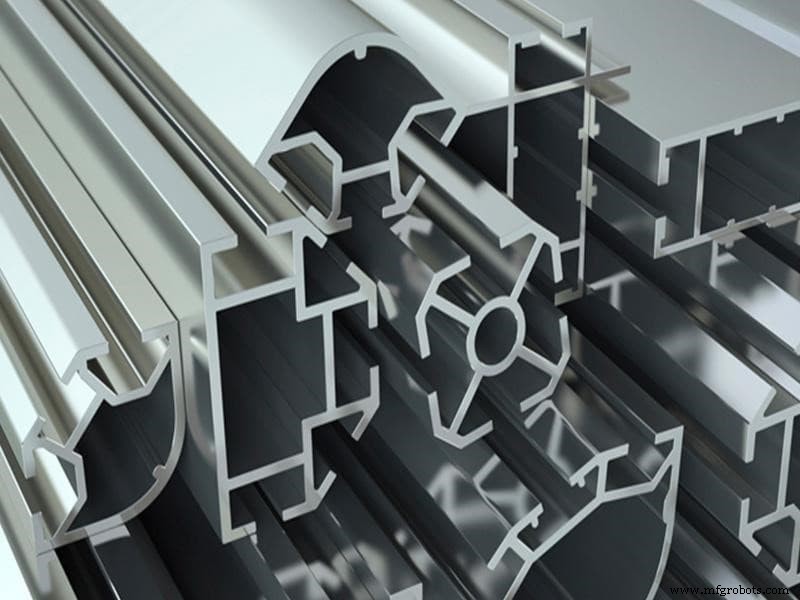
Aluminium extrusie is de laatste jaren steeds populairder geworden in productinnovatie en productie. Technavio meldde dat de wereldwijde vraag naar aluminiumextrusie tussen 2019 en 2023 met ongeveer 4% zou groeien.
Misschien heb je wel eens van deze fabricageprocedure gehoord en ben je benieuwd wat het is en hoe het werkt. Dit artikel gaat dieper in op de details van alles wat u moet weten over extrusie-aluminium.
Wat Ik s Aluminium extrusie ?
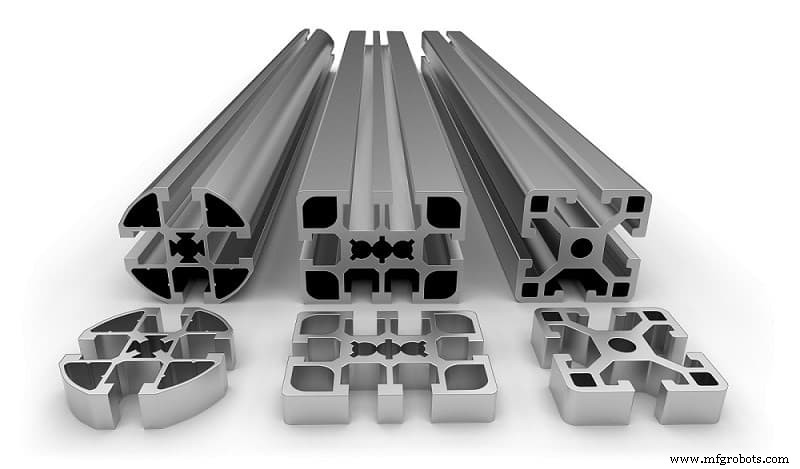
Aluminiumextrusie is een techniek om materiaal van een aluminiumlegering in een matrijs te persen met een vooraf bepaalde dwarsdoorsnedevorm. Een aanzienlijke ram duwt het aluminium via de matrijs en verlaat de matrijsopening. Het komt tevoorschijn in de exacte vorm van de dobbelsteen en wordt als dit gebeurt langs een uitlooptafel gesleept.
Het proces is een vrij eenvoudige techniek om op een fundamenteel niveau te begrijpen. De gebruikte kracht is vergelijkbaar met de kracht die wordt gebruikt bij het samenpersen van een tube tandpasta met uw handen. De tandpasta komt naar buiten in de vorm van de opening van de tube als je erin knijpt. De opening van de tube tandpasta heeft grotendeels hetzelfde doel als een extrusiematrijs.
Geschiedenis van aluminiumextrusie
Dit productieproces begon meer dan 100 jaar geleden. De extrusieprocedure werd voor het eerst ontwikkeld in 1797 door Joseph Bramah om loden pijpen te produceren. De procedure stond aanvankelijk bekend als "spuiten" en een handmatig proces totdat Thomas Burr de productie van de eerste hydraulische pers in 1820 voltooide. Alexander Dick creëerde het hete extrusieproces in 1894, dat nu in modern gebruik is. Dankzij de hete extrusietechniek gebruiken fabrikanten nu non-ferro legeringen in het extrusieproces. In 1904 was er een golf van aluminiumtoepassingen in de auto- en bouwindustrie nadat de eerste aluminium extrusiepers was gebouwd.
Tijdens de wereldoorlog nam de vraag naar het extruderen van aluminium enorm toe. Het vond gebruik in militaire toepassingen en de bouw van vliegtuigen. De behoefte aan geëxtrudeerd aluminium begon meer uit te breiden. Het maakt nu deel uit van ons dagelijks leven. Van de auto waarin u rijdt tot uw huishoudelijke artikelen, het zijn allemaal producten van dit effectieve productieproces.
Direct en Indirect Aluminium extrusieproces
Er zijn twee belangrijke soorten processen die worden gebruikt voor aluminium extrusies - direct en indirect. Het directe proces houdt in dat de matrijskop stationair wordt gehouden en dat de bewegende ram er metaal doorheen duwt. Aan de andere kant blijft de knuppel stationair in het indirecte extrusieproces. Het matrijssamenstel beweegt dan tegen die knuppel om de druk te creëren om het metaal door de matrijs te dwingen. Hier is een meer gedetailleerde kijk op beide processen.
Direct Aluminium extrusieproces
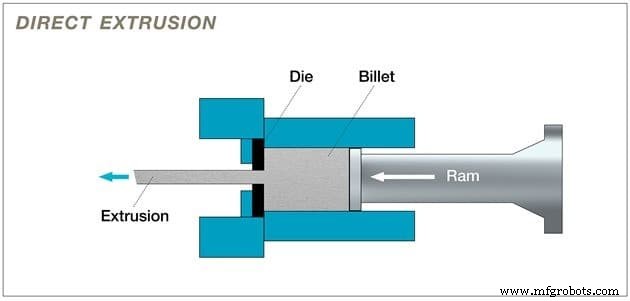
Directe extrusie is de meest gebruikte methode om aluminium te extruderen. De aluminium extruder plaatst de knuppel (verwarmd aluminium) in een verwarmde ommuurde container. Vervolgens dwingt een bewegende ram het metaal door de matrijs. Tijdens deze stap wordt er een zeer hoge hoeveelheid druk geproduceerd.
Machinisten plaatsen ook vaak blokken materiaal tussen de knuppel en de ram. Deze procedure voorkomt dat de ram en de verwarmde knuppel met elkaar in contact komen. Mensen noemen deze methode ook wel een voorwaarts extrusieproces, omdat de aluminium knuppel en de ram in dezelfde voorwaartse richting bewegen.
Indirect Aluminium extrusieproces
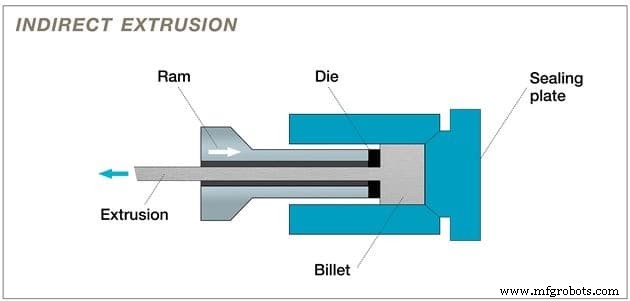
Indirecte extrusie, vaak bekend als achterwaartse extrusie, verschilt van het directe proces. Hier blijft de matrijs stil terwijl de knuppel en de container tegelijkertijd bewegen. Fabrikanten gebruiken een "stam" bij het uitvoeren van dit proces. Deze steel moet langer zijn dan de lengte van de container en houdt de ram op zijn plaats. Zo wordt de aluminium knuppel door de stationaire matrijs geduwd.
In tegenstelling tot de directe methode genereert deze methode minder wrijving voor een betere warmtebeheersing. De productkwaliteit voor indirecte extrusies is meestal consistenter. Dit kan te wijten zijn aan het feit dat de uitgeoefende kracht relatief stabiel blijft. De temperatuurconsistentie zorgt ook voor betere mechanische eigenschappen en korrelstructuur.
Stap- B y-Step Guide op Aluminium extrusie Proc dure
Stap 1 : Bereid je voor E xtrusie D dwz
Het eerste dat u moet doen, is een ronde matrijs bewerken. Aan de andere kant kun je een al beschikbare hebben. Verwarm vóór het extrusieproces de matrijs voor op ongeveer 450-500 0 C. Dit zorgt voor een gelijkmatige metaalstroom en maximaliseert de levensduur van de matrijs. Na het voorverwarmproces kunt u de matrijs vervolgens in de extrusiepers laden.
Stap 2 : Verwarm aluminium knuppel voor
De volgende stap is om de knuppel, een dik cilindrisch blok aluminiumlegering, uit een langwerpig stuk materiaal te snijden. Verwarm het vervolgens voor in een oven tot ongeveer 400-500 0 C. Dit proces maakt de knuppel kneedbaar genoeg om de bewerking uit te voeren. Het zorgt er ook voor dat het niet gesmolten is.
Stap 3 : Verplaats de B illet naar de E xtrusie P ress
Breng de knuppel na het voorverwarmen mechanisch over in de pers. U moet er echter voor zorgen dat u een smeermiddel toevoegt voordat u het in de pers laadt. Breng bovendien het lossingsmiddel aan op de extrusiecilinder. Dit proces voorkomt dat de ram en de knuppel aan elkaar hechten.
Stap 4 : Duwen B illet M ateriaal in de Extrusiepers Container
In dit stadium bevindt de kneedbare knuppel zich al in de extrusiepers. Hier kan de hydraulische ram ongeveer 15.000 ton druk uitoefenen. De druk duwt de kneedbare knuppel in de container. De aluminiummaterialen zetten vervolgens uit om de wanden van de container te vullen.
Stap 5 : Druk het geëxtrudeerde materiaal tegen de matrijs
Omdat aluminium materiaal nu de wand van de container vult, wordt het tegen de extrusiematrijs gedrukt. Op dit punt wordt voortdurend druk op het materiaal uitgeoefend. De enige richting is dus door de matrijsopeningen. Het komt uit de openingen van de matrijs in een volledig gevormde vorm.
Stap 6 : Doof de extrusies
Een trekker houdt de extrusie op zijn plaats na het tevoorschijn komen. De trekker beschermt het als het de pers verlaat. Terwijl de legering langs de tafel beweegt, wordt het profiel gelijkmatig afgekoeld door een ventilator of waterbad. Dit proces is aan het "blussen".
Stap 7 :Scheer de Extrusies tot tafellengte
Zodra de extrusie de volledige tafellengte bereikt, knipt u deze af met een hete zaag. Temperatuur is essentieel bij elke stap van het extrusieproces. Ondanks het afschrikken van de extrusie na het verlaten van de pers, is deze nog niet volledig afgekoeld.
Stap 8 :Cool Extrusies tot kamertemperatuur
Wanneer het knipproces is voltooid, worden de extrusies overgebracht naar een koelvlak van de uitlooptafel. De profielen blijven daar tot ze op kamertemperatuur komen. Als ze eenmaal op kamertemperatuur zijn, wordt er uitgerekt.
Stap 9 : Verplaatsen Extrusies naar de brancard en Strek ze uit naar Uitlijning
U zult in dit stadium enkele wendingen in de vormen opmerken en u moet dit corrigeren. Om deze correctie uit te voeren, heeft u een brancard nodig. Houd elk profiel mechanisch aan beide uiteinden vast en trek eraan totdat ze volledig recht zijn. Dit proces brengt ze in specificatie.
Stap 10 :Verplaatsen Extrusies naar de afwerkzaag en Snijd ze tot lengte
Nu de extrusies recht en gehard zijn, kunt u ze overzetten op een zaagtafel. Op dit punt kun je ze in specifieke lengtes snijden, voornamelijk tussen 8-21 ft. Nadat het zaagproces voorbij is, kun je ze naar een oven verplaatsen om ze op de juiste temperatuur te laten rijpen (T5 of T6).
Stap 11 :Uitvoeren Secundair O peraties (H eet behandeling, V afkorting, en S oppervlak F eindigend)
Nadat het extrusieproces is voltooid, kunt u profielen met warmte behandelen om hun eigenschappen te verbeteren. Het volgende wat na de warmtebehandeling is om ze te fabriceren als het nodig is om hun afmetingen te corrigeren. oppervlakteafwerking toevoegen zou ook helpen hun uiterlijk en corrosiebestendigheid te verbeteren.
Met welke vormen kan worden gemaakt Aluminium extrusie ?
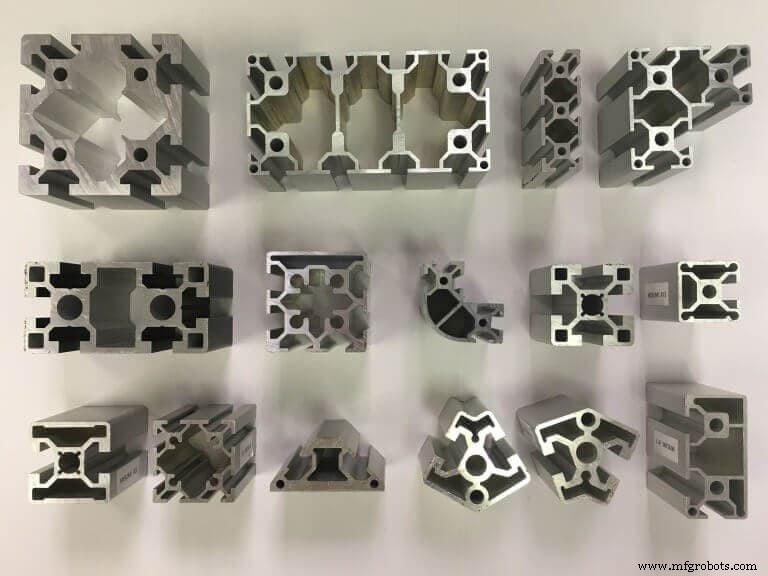
Er zijn vier belangrijke soorten geëxtrudeerde vormen, en dat zijn:
Bent u op zoek naar op maat gemaakte geëxtrudeerde onderdelen met aangepaste vormen? Laat RapidDirect het sourcingproces voor u regelen. Onze beschikbare aluminium extrusieprocessen zijn de beste die u kunt vinden. We combineren geavanceerde machines met een professioneel technisch team om eersteklas productiediensten op maat te leveren.
We kunnen ook verschillende oppervlakteafwerkingsopties bieden voor uw eindproducten. Wat je keuze ook is, je kunt er zeker van zijn dat we leveren. We zorgen ook voor constante tests in elke productiefase om ervoor te zorgen dat u alleen het beste krijgt. Upload vandaag nog uw ontwerpbestand en ontvang direct een offerte.
Factoren die van invloed zijn Aluminium extrusie
Hoewel extrusie van aluminium een effectief productieproces is, zijn er enkele factoren die de uiteindelijke resultaten van het proces beïnvloeden. Het is het beste om deze factoren in gedachten te houden om het succes van uw project te garanderen.
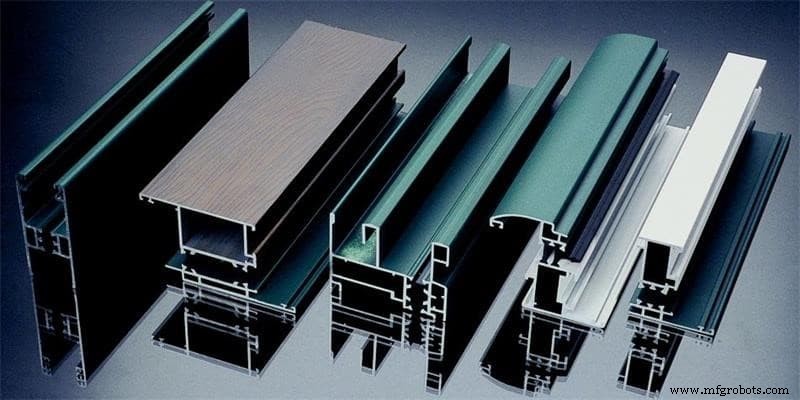
Geëxtrudeerd S hapes
De vorm zou bepalen hoe gemakkelijk en duur het zou zijn om een onderdeel te extruderen. Extrusie kan een breed scala aan vormen produceren, maar er zijn enkele beperkingen. Eenvoudige massieve vormen zouden bijvoorbeeld veel gemakkelijker en sneller te extruderen zijn dan halfholle. Ze zouden ook minder duur zijn - in het algemeen geldt dat hoe complexer de vorm, hoe uitdagender en duurder het is om te extruderen.
Extrusie S pist
Als algemene regel is de extrusiesnelheid direct gecorreleerd met de metaaldruk en temperatuur in de container. De snelheid, druk en temperatuur moeten dus correct worden geassocieerd om een stabiel proces te behouden en een constant geëxtrudeerd segment te genereren.
Billet T emperatuur
De beste knuppeltemperatuur is er een die acceptabele tolerantie en oppervlaktecondities biedt. Tegelijkertijd zorgt het voor de kortst mogelijke cyclustijd. Het is altijd ideaal om knuppelextrusie te hebben bij de laagst mogelijke temperatuur die het proces kan toestaan.
Te hoge temperaturen zouden het metaal vloeibaarder maken. Dit zou ervoor zorgen dat het metaal weerstand biedt aan het binnendringen van vernauwde gebieden. Hierdoor kunnen de vormafmetingen onder de gewenste toleranties vallen. Evenzo kunnen te hoge temperaturen het metaal scheuren bij scherpe hoeken en dunne randen.
Extrusie R atio
De extrusieverhouding van elke vorm is een goede indicator van hoeveel mechanisch werk er zal plaatsvinden tijdens de extrusie. Wanneer de extrusieverhouding van een sectie laag is, zal mechanisch werk aan de delen van de vorm die de meeste metaalmassa bevatten minimaal zijn. Aan de andere kant zal er behoefte zijn aan meer druk wanneer er een hoge extrusieverhouding is. De druk zou het metaal door kleinere openingen dwingen en er zal extreem mechanisch werk nodig zijn.
Druk op O peration
De gedachte aan winstgevende persbewerking maakt het gewicht per voet relevant in aluminium extrusies. Zoals je zou verwachten, vereist het extruderen van lichtere secties meestal kleinere persen. Er zijn echter nog enkele andere factoren die persen met een grotere capaciteit zouden kunnen vergen. Een grotere, dunwandige holle vorm is een typisch voorbeeld.
Ondanks het lage gewicht per voet, kan het perstonnage dat nodig is om het te extruderen hoger zijn. De factor heeft vergelijkbare effecten als de extrusieverhouding. Een grotere factor maakt het moeilijker om het onderdeel te extruderen. Dit heeft dus gevolgen voor de persproductie.
Tong R atio
De tongverhouding is ook belangrijk bij het bepalen van de extrusieprestaties van een onderdeel. U kunt de tongverhouding van een extrusie bepalen door de kleinste opening naar de leegte te kwadrateren. Bereken vervolgens het hele gebied van de vorm en deel de opening in het kwadraat door dit gebied. Hoe hoger de tongverhouding, hoe uitdagender het zou zijn om het onderdeel te extruderen.
Wat zijn de toepassingen van Aluminium extrusie s ?
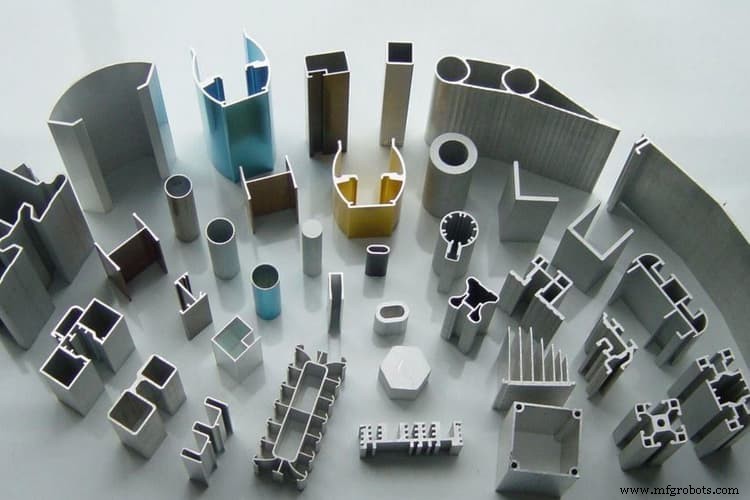
De materiaaleigenschappen maken extrusie-aluminium tot een effectief productieproces voor verschillende industrieën. De sterkte-gewichtsverhouding en treksterkte van het materiaal maken het ideaal voor het extruderen van motorblokken, panelen, transmissiehuizen, dakrails, chassis van voertuigen en andere onderdelen.
Het extruderen van aluminium produceert ook onderdelen voor autoradiatoren, condensorbuizen, airconditioners, kernreactoren en koelapparatuur in de elektronica. Geëxtrudeerde aluminium buizen kunnen draden en coaxkabels huisvesten, omdat het niet-magnetisch is. De corrosie- en roestbestendige eigenschappen van aluminium materiaal maken het ook geschikt voor buitentoepassingen. Bovendien zijn aluminium extrusies sterk reflecterend. Zo helpen ze producten te beschermen tegen licht, infraroodstraling en radiogolven.
Aluminium extrusie :een belangrijk productieproces
Het aluminium extrusieproces is essentieel voor het produceren van onderdelen met aangepaste dwarsdoorsnedeprofielen. Het proces is best interessant, en je kunt verschillende vormen van producten krijgen die je kunt verhitten, fabriceren en afwerken volgens specificatie. RapidDirect biedt de beste aluminium extrusiediensten voor het gewenste resultaat. Neem vandaag nog contact met ons op en laten we uw project tot leven brengen. U kunt uw ontwerpbestand ook uploaden op ons digitale offerteplatform voor directe offertes en een transparant bestelproces.
Industriële technologie
- Aluminium
- Aluminiumfolie
- FDM vs SLA - Uitsplitsing van 3D-afdrukproces
- Aluminium versus standaard PCB's
- De geschiedenis en toekomst van aluminium extrusie
- De basis van kunststofextrusie:proces, materialen, toepassingen
- Wat is storingsonderhoud?
- Is aluminium duurzaam?
- EN AW-5005
- AA 7075 T7
- Extrusieproces begrijpen