De juiste pers kiezen
Perstechnologie — mechanisch, hydraulisch of servo — speelt vele rollen
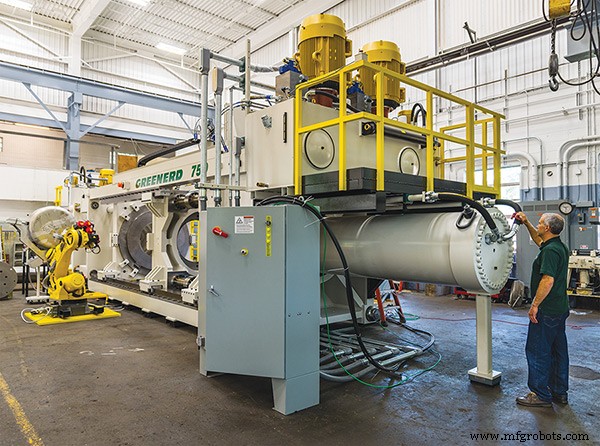
Er zijn keuzes in persen, wat een goede zaak is. Het debat is niet wat de beste is, maar welke het beste is voor de klus. Er zijn compromissen in kosten, functie en kwaliteit tussen de belangrijkste soorten persen die men zou kunnen kiezen.
Het is een vriendelijk debat en de kaarten liggen voor iedereen op tafel.
Snel overzicht van technologie
Volgens Stephanie Price, senior applicatie-ingenieur bij Promess Inc, Brighton, Mich., waarderen veel mensen in de industrie de voordelen van servoperstechnologie niet volledig. Omgekeerd stelt Mike Josefiak, werktuigbouwkundig ingenieur bij Greenerd Press &Machine, Nashua, N.H., dat een hydraulische pers voor sommige toepassingen de beste oplossing is. En Jim Landowski, vice-president van Komatsu America Industries LLC uit Chicago, zou je vertellen dat er nog steeds situaties zijn waarin een traditionele mechanische pers prima werkt.
Een mechanische pers zet de roterende beweging van een vliegwiel om in de lineaire beweging van de ram die in het werkstuk drukt. Zoals Landowski het beschreef, kun je je 'de cirkel voorstellen, met nul bovenaan en 180 onderaan. Een mechanische pers gaat van nul tot 180 en terug naar nul, of 360, in één continue beweging.” De slag heeft geen kracht aan de bovenkant en maximale kracht aan de onderkant, dus "afhankelijk van de matrijs kun je het materiaal op 160 graden of zo gaan duwen. Maar als het 180 wordt, is het onderdeel klaar, omdat je dia weer omhoog gaat."
Zoals Bob Southwell, executive vice president van AIDA-America, Corp. Dayton, Ohio, uitlegde, zijn de meeste servopersen versies van dezelfde opstelling, "behalve dat je een mechanische aandrijflijn aandrijft met een servomotor, in plaats van een vliegwiel met een koppelingsremmechanisme.” Een mechanische pers heeft een vaste slag en een constante snelheid. Maar "voeg er een servomotor aan toe en nu kun je het bewegingsprofiel programmeren. Je kunt vertragen, pauzeren, snel herstarten en verschillende dingen doen die nooit mogelijk waren met een standaard mechanische pers. Er is ook een versie met directe aandrijving (servomotor naar kogelomloopspindel), met betere koppelkarakteristieken dan de servomechanische hybride.
Een hydraulische pers combineert een set pompen, kleppen en slangen om de ram in contact te brengen met vloeistof onder druk. Hoewel deze aanpak voordelen heeft, is er niet het soort bewegingsbesturing dat hierboven wordt beschreven. Een servopers biedt dus extra mogelijkheden en lost een aantal problemen op die optreden bij puur mechanische of hydraulische persen.
Nieuwe materialen, nieuwe uitdagingen
Landowski merkte op dat de verschuiving naar geavanceerde legeringen, veroorzaakt door lichtgewicht auto's en andere factoren, de vraag naar servopersen stimuleert. Zoals hij het uitdrukte, "beschouw staal als een vloeistof, het moet stromen... Je bewerkt niet het materiaal, je werkt met het materiaal."
Hardere materialen vereisen fijne aanpassingen aan de ramsnelheid om "het materiaal correct te laten stromen, anders wordt het als taffy en begint uit elkaar te vallen." Hij zei bijvoorbeeld dat het vormen van een beker in een harde legering mogelijk een vertraging van 30 tot 15 IPM vereist in de loop van een slag van 3" (76,2 mm), met een nauwkeurige - en misschien variërende - veranderingssnelheid.
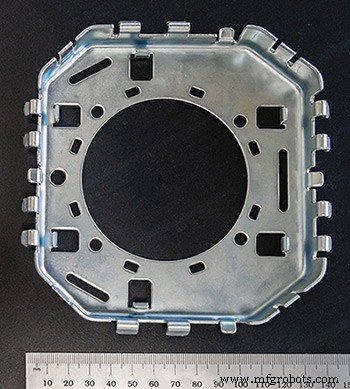
Alleen een servobesturing kan dit aan, aangezien de aanpassingen in milliseconden plaatsvinden.
Het belangrijkste voordeel van een servo, aldus Landowski, is de flexibiliteit om met verschillende metalen te werken door de materiaalstroom in te stellen. “Daarom laten we mensen binnenkomen om verschillende opties te proberen. Ik kan een goed of een slecht stuk maken door gewoon de snelheid van de dia te veranderen."
Southwell was het daarmee eens en meldde dat deze materiële uitdagingen hebben geresulteerd in een marktaandeel van ongeveer 80 procent voor servopersen in de Noord-Amerikaanse automobielindustrie. “De hogesterkte- en ultrahogesterktestalen en aluminiumsoorten zijn veel uitdagender om te vormen dan de materialen van tien tot vijftien jaar geleden. En het vermogen van een servo om het vormingsprofiel aan te passen, is buitengewoon gunstig gebleken voor het klantenbestand.”
Josefiak van Greenerd was het ermee eens dat servobesturing een voordeel heeft in responstijd versus hydrauliek, waarbij de respons wordt gedempt, maar zei dat hij "niet veel toepassingen had gezien waarbij dat niveau van controle in het bewegingsprofiel een wezenlijke invloed heeft op het al dan niet maken van een goed product." Maar hij erkende dat "restriking een goed voorbeeld is van een servo-only-functie. Naar de bodem gaan en dan binnen een fractie van een seconde weer toeslaan is niet iets wat je met hydrauliek kunt doen.”
Als je de snelheid niet hoeft te regelen, betoogde Landowski, heb je misschien geen servo nodig.
“Als je bijvoorbeeld sluitringen maakt, of kleine klinknagels of iets dergelijks, ga je de pers niet vertragen, je gaat de snelheid niet regelen. Je wilt zoveel mogelijk onderdelen maken, zo snel als je kunt.” Dat is waar een mechanische pers schijnt, zei hij. Het is ook waar hydraulische persen het minst geschikt zijn.
Servoveelzijdigheid in montage
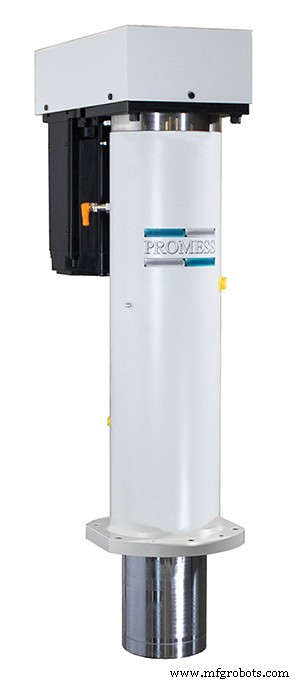
Southwell voegde eraan toe dat het vermogen van een servopers om gemakkelijk te herprogrammeren voor verschillende onderdelen een andere factor is in hun succes, zelfs in de autowereld met grote volumes.
“De meeste perssystemen zijn ontworpen om meerdere soorten onderdelen te verwerken. Ze zullen een uur lang een tool laten draaien, deze vervangen en een andere tool inrollen. Vrijwel niemand zet één pers op en runt hem gewoon... Ze kunnen onmogelijk concurrerend blijven. We verkopen veel systemen aan de OEM's via de Tier Ones en Tier Twos voor grote families van verschillende onderdelen of matrijzensets via een enkele druk op de knop.”
De veelzijdigheid van servopersen gaat veel verder dan eenvoudig programmeren en strekt zich uit tot delicate montagewerkzaamheden, zei Price van Promess.
Vasthoudend aan een autovoorbeeld, wees Price op het monteren van een deurscharnier. Ze legde uit dat een servopers zowel hoge precisie biedt als een inherente feedbacklus die in staat is om positie en kracht nauwlettend te volgen. Dus door het scharnier samen te drukken, kan Promess ook de resulterende weerstand in het gewricht meten, zodat ze ervoor kunnen zorgen dat de deur niet te gemakkelijk openzwaait en ook niet te stijf is om oncomfortabel te zijn voor de eigenaar van de auto.
Deze mogelijkheid om een bewegend onderdeel te activeren en krachten in realtime te meten, biedt ook de mogelijkheid om onderdeeltoleranties te verminderen, waardoor de onderdeelkosten worden verlaagd. Zoals Price heeft uitgelegd, worden ingenieurs zonder feedback tijdens de montage vaak gedwongen om te ontwerpen en te produceren met zeer nauwe toleranties om ervoor te zorgen dat onderdelen goed in elkaar passen.
“Ze gebruiken het feit dat de pers tot een bepaalde diepte is gegaan en gaan er op basis van hun krappe toleranties van uit dat het onderdeel correct is gemonteerd. Ze hebben geen handtekeninganalyse om dat te verifiëren.”
Met een servopers kunnen ze in plaats daarvan de toleranties losser maken en de gegevens tijdens het assemblageproces bekijken om te bepalen of wat ze samen hebben gedrukt, echt goed zit. Price zei dat de ingebouwde detectiemogelijkheden van hun servopersen in sommige gevallen hebben geleid tot verlagingen van het uitvalpercentage tot wel 50 procent.
Price wees er ook op dat als een toepassing extra detectie vereist (naast de feedback van de servomotor), deze eenvoudig te integreren is met hun systemen.
“We hebben klanten die negen tot tien verschillende drukopnemers gebruiken, of positieopnemers of externe loadcellen. We kunnen al die informatie opnemen om te begrijpen wat er in het proces aan de hand is, "zei hij. “En daar kunnen we tijdens het proces op inspelen. En omdat alles elektrisch is, is het heel eenvoudig in te stellen. Sluit gewoon een transducer aan op een digitale signaalconditioner. De controller kan dat signaal dan opnemen en gebruiken om een beslissing te nemen.”
Persen, controle en compromissen
Hydraulische persen zijn niet blind op dit gebied. Josefiak zei dat er bewegingscontrollers zijn speciaal voor hydraulische systemen met "extreem snelle scantijden die kijken naar de druk aan weerszijden van een hydraulische actuator. En dan kunnen we met behulp van snelwerkende druktransducers de daadwerkelijke kracht laten zien die op het werk wordt uitgeoefend.” Eén zo'n systeem werkt de krachtmeting bij in minder dan een milliseconde. Naar zijn mening zijn toepassingen die een snellere krachtmeting vereisen "weinig tussen".
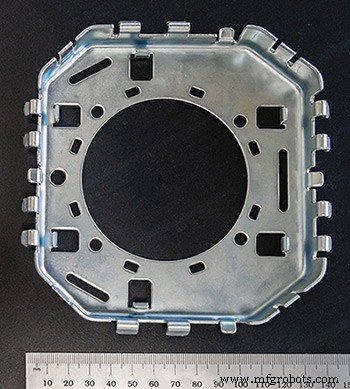
Volgens Southwell zijn servopersen veel beter dan hydraulische persen bij het maken van complexe onderdelen waarvoor een reeks matrijzen nodig is. Jaren geleden zou dit zijn gedaan door onderdelen met de hand over te brengen van pers naar pers, legde hij uit. Maar nu "de enige manier om te concurreren" is om onderdelen mechanisch over te brengen van podium naar podium binnen een enkele druk op de knop. Maar "wanneer je meerdere stations gebruikt om een onderdeel te maken, heb je last van excentrische belasting, wat erg nadelig is voor een hydraulische aandrijflijn."
Josefiak wierp tegen dat “off-center laden schadelijk is voor zowel mechanische als hydraulische systemen. Beide hanteren deze excentrische belastingen met de juiste constructie en geleiding van het stalen frame. We hebben systemen die gebruik maken van meerdere hydraulische cilinders om off-center laden mogelijk te maken die veel groter is dan een kant-en-klare servo-mechanische pers.”
Er is ook enige controverse over toepassingen die het gebruik van food-grade olie als smeermiddel vereisen. Landowski meldde dat "verschillende klanten zijn overgestapt van hydraulische naar servo-mechanische persen, uitsluitend vanwege het huilen van cilinders en het druppelen van de schuiven op het materiaal. Alle onderdelen moeten worden gereinigd nadat ze zijn gevormd om alle mogelijke verontreinigingen te verwijderen. Klanten hebben ons ook verteld dat het reinigen van food-grade smeermiddelen goedkoper is dan non-food grade vanwege FDA- of EPA-voorschriften.”
Josefiak zei dat ze bij een aantal projecten aan zowel de medische als de voedselveiligheidsnormen hebben voldaan "door de afdichting in hun persen aan te passen om olie van voedingskwaliteit te gebruiken in plaats van standaard industriële oliën." Terwijl Landowski verklaarde dat hun standaard kant-en-klare servopers geen aanpassingen nodig heeft, "alleen de food-grade olie voor de persaandrijving en het glijmiddel." Een klant “maakt rubberen stoppen voor reageerbuisjes. Elke druk van de pers levert 65 tot 75 rubberen stoppen op, en smeermiddelen die niet geschikt zijn voor voeding zouden dit specifieke proces ongeldig maken.”
Hydraulische verovert dieptrekken
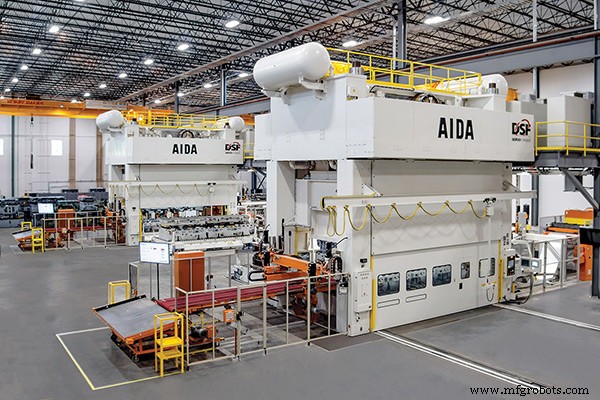
Volgens Southwell is “het voordeel van een hydraulische pers dat je de volledige tonnage- of krachtcapaciteit hebt gedurende de hele slag. Dus als het een pers van 200 ton is en je hebt een slag van 12 inch, dan kun je tijdens die slag 200 ton druk uitoefenen. Met een servopers die dezelfde mechanische excentrische aandrijflijn heeft als de originele mechanische pers, heb je een tandwieloverbrenging, de krukas of een centrale as en een centrale tandwielaandrijving. Er is een tonnage- of koppelkromme en de kracht die je kunt uitoefenen varieert afhankelijk van de hoek van de motoras vanaf de bodem.” Dit is niet het geval voor servopersen met directe aandrijving zoals die van Promess, maar deze systemen worden erg duur naarmate het tonnage toeneemt. Promess bereikt bijvoorbeeld een top van 1 MN (~100 ton) in een enkele cilinder.
De mogelijkheid om volledige kracht uit te oefenen door de hele slag, maakt hydraulische persen perfect voor dieptrektoepassingen, en Josefiak ging zelfs zo ver om te zeggen dat het "de enige optie is die echt logisch is".
Een recent voorbeeld dat hij noemde, is een project om 'relatief grote druktanks' te produceren. We hebben een geautomatiseerd systeem geïnstalleerd dat grote, platte blanco's in een dieptrekpers laadt met een werkslag van anderhalve meter.” Het systeem heeft meerdere operaties, legde hij uit. De eerste gebruikt een pers van 170 ton om twee helften van de tank te tekenen. Dit wordt gevolgd door een geautomatiseerde ponsmachine en stroomafwaarts trimmen en lassen. De sleutel hier, zei Josefiak, is dat zo'n werkende slag "niet iets is dat gemakkelijk kan worden gerepliceerd met een servopers. Dus diepe trek is een gebied waar hydrauliek nog steeds domineert. En dat is in heel wat sectoren. Het is meer het proces dan de industrie.”
Josefiak zei dat hydrauliek ook "het zeer goed doet in situaties met een zeer lange cyclustijd, waar we een zeer laag stroomverbruik kunnen beheren bij een consistente druk over het bedgebied en relatief goedkoop vanuit het oogpunt van kapitaalkosten." Compressievormen is een belangrijk voorbeeld. "Meestal is persen een combinatie van tijd, temperatuur en druk die een materiaal in een vorm vormt", legt Josefiak uit. De pers zou een relatief dun materiaal onder druk tegen een positieve of negatieve matrijsvorm houden. “De duur kan zo kort zijn als vijf seconden, of zo lang als twee uur. En heel vaak ... proberen we een constante temperatuur van de plaat over het werkgebied van ongeveer 300 tot 700 graden te handhaven, en proberen we een zeer consistente druk over het werkgebied te regelen." Dat zorgt ervoor dat het materiaal dat wordt gevormd overal uniform is. De techniek wordt gebruikt voor zaken als autobedliners (inclusief de nieuwe composiet bedliners) en automotive headliners gemaakt van tapijtachtig materiaal. Een ander voorbeeld dat hij noemde is "poederverdichting voor het maken van aluminiumoxide slijpstenen."
Kostenoverwegingen
In het algemeen overtreft de kapitaalinvestering voor een servopers die van traditionele mechanische of hydraulische persen. Maar er zijn bedrijfskosten en gerelateerde factoren waarmee u rekening moet houden die deze vergelijking bijna nutteloos maken. Bovendien zijn niet alle persen van een bepaald type gelijk, zelfs niet voor hetzelfde tonnage/koppel.
Laten we beginnen met het energieverbruik. Een hydraulische pers moet de leidingen onder druk houden om de ram naar behoefte te verplaatsen, en dat betekent dat de pompen door de cycli moeten lopen. Dat is ongunstig in vergelijking met een servopers, die alleen elektriciteit gebruikt als de ram beweegt. Volgens Landowski levert dat een energiebesparing van ongeveer 50 procent op met een servopers, afhankelijk van de grootte van de machine. Price verwees naar een onderzoek van de Universiteit van Kassel, waaruit bleek dat de servopers 90 procent efficiënt is in energieconversie, tegenover 57 procent voor het vergelijkbare hydraulische systeem. Southwell zei dat Honda hun eigen systemen bestudeerde en de bevinding publiceerde dat servopersen een besparing van 30 procent op het werkelijke stroomverbruik opleverden.
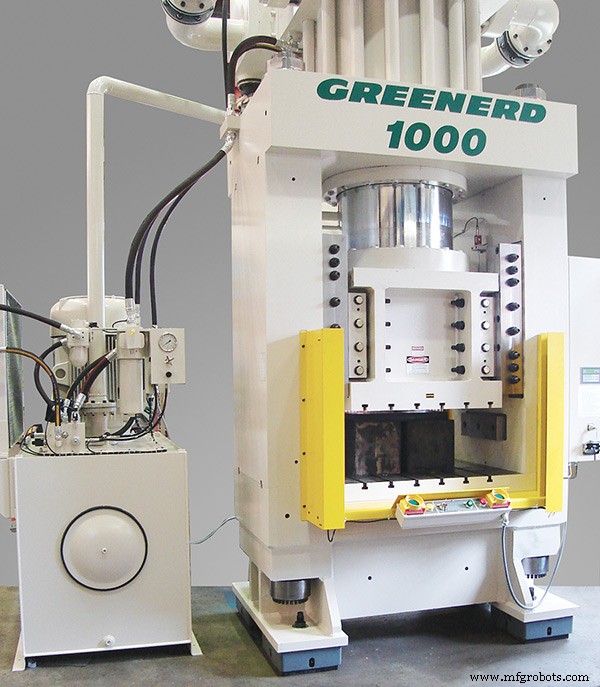
Southwell gaf ook aan dat sommige AIDA-persen een "100 procent op condensatoren gebaseerd energiebeheersysteem" gebruiken. Dit slaat de benodigde werkenergie op in condensatoren, die worden opgeladen tijdens het niet-werkende deel van de slag. Dit "vermindert de piekbelasting enorm", legde hij uit, in vergelijking met een mechanische of hydraulische pers, die een "enorme piek heeft wanneer ze voor het eerst worden ingeschakeld". De huidige stroomafname van AIDA is "redelijk vlak. Uw werkelijke piekstroom kan dus slechts 20 tot 30 procent zijn van de piekbelasting van mechanische of hydraulische systemen. Dat is cruciaal, want energiebedrijven moeten de stroom die ze aan de klant leveren, afstemmen op de piekbelasting.”
Josefiak wierp tegen dat er in een omgeving met een hoge productie weinig of geen inactieve tijd is, dus "het maakt echt niet zoveel uit" dat de hydraulische pompen continu draaien. En "in systemen met lange stilstandtijden van 10 minuten of meer, kunnen we een 'softstart'-motorbesturing installeren die de motor uitschakelt om energie te besparen." Interessant is dat, hoewel deze optie slechts 2 tot 3 procent van de systeemkosten toevoegt, Josefiak meldde dat er nooit een sterke vraag naar is geweest. Hij voegde eraan toe dat het overschakelen van een pomp met vast debiet naar een pomp met variabel debiet ook "ons energieverbruik bij inactiviteit drastisch kan verlagen". Maar dat is weer een optie die in de VS nog de norm moet worden.
Met al zijn pompen, kleppen, leidingen en slangen wordt hydraulische technologie vaak gezien als complexer en onderhoudsintensiever dan op servo gebaseerde systemen. Price zei dat hun servopersen niet meer dan tweemaal per jaar moeten worden gesmeerd van de kogelomloopspillen - en zelfs dat is zeer voorzichtig. Omgekeerd, houd hydraulische leidingen maandenlang onder hoge druk, cyclus na cyclus, en vroeg of laat zal er iets gaan lekken of een subonderdeel zal het begeven. Het tegenargument, zei Josefiak, is dat “niemand NPT-fittingen meer gebruikt. Er is een reeks metaal-op-metaal afdichtingen en afdichtingen in O-ringstijl, gebouwd met betere materialen, die lekkage veel beter onder controle hebben.” Bovendien, zei hij, zijn de afzonderlijke componenten relatief goedkoop en gemakkelijk te repareren, terwijl "reparaties aan een servosysteem dramatisch duurder zijn."
Dit laatste punt brengt ons bij het onderwerp van het correct dimensioneren van de componenten voor de taak. Het is waar dat als je een servomotor binnen een paar jaar doorbrandt, je een hoge reparatierekening krijgt. Maar Price zei dat hun systemen routinematig 20 jaar draaien zonder dergelijke storingen, omdat ze zijn ontworpen met een veiligheidsfactor van 2,5×. De aandrijvingen zijn zo gedimensioneerd dat ze in de continue stroom van de servomotor werken, in plaats van in de piek, zodat de pers het onderdeel voor onbepaalde tijd kan vasthouden zonder oververhitting en uitval.
Evenzo hebben de kogelomloopspindels een dynamisch draagvermogen van 2,5× de kracht van de pers. Zo heeft de kogelomloopspindel in een Promess 40 kN pers een dynamisch draagvermogen van 134 kN en een statisch draagvermogen van 320 kN. Price zei dat van een dergelijk systeem kan worden verwacht dat het meer dan 22 jaar storingsvrij zal werken bij een taak met een gemiddelde kracht van 30 kN, met 16 cycli/min gedurende 14 uur/dag. Vergelijk dat met slechts 32 weken voor een kogelomloopspindel met een dynamische belasting van 40 kN; zelfs bij een vermogen van 80 kN zou het systeem minder dan vijf jaar meegaan.
Automatisering Besturingssysteem
- ips voor het kiezen van de juiste CNC-reparatieservice
- Robotische lassystemen:de juiste kiezen
- 5 tips voor het kiezen van het juiste orderbeheersysteem
- De juiste hydraulische klemmen kiezen om de cyclustijden te verkorten
- De juiste laser kiezen
- De juiste CNC-plasmatafel kiezen
- De juiste uitrusting voor landschapsarchitectuur kiezen
- De juiste verzekering kiezen voor uw zwaar materieel
- De juiste compacte apparatuur kiezen voor uw boerderij
- De juiste fabrikant kiezen in plaats van een grote fabrikant
- De betekenis van het kiezen van het juiste EDM-draadmateriaal