Geïndustrialiseerde continue vezelcomposietdruk in Delft
3D-printen van continu vezelversterkte composieten blijft zich uitbreiden en vooruitgaan. Er zijn veel nieuwe bedrijven en ontwikkelingen ontstaan sinds Markforged de Mark One continuous fiber 3D-printer in 2014 aankondigde. Ik heb op veel hiervan geblogd en ik zal doorgaan met het verkennen van het zich snel ontwikkelende landschap en de spelers voor CW lezers.
CEAD (Delft, Nederland) werd geïntroduceerd in Karen Mason's functie van maart 2019, "Moving continuous-fiber 3D printing into production". In deze blog geef ik meer details op basis van mijn interviews met mede-oprichter Maarten Logtenberg, waaronder waarom het bedrijf zijn extruder apart verkoopt en de visie van het bedrijf op de toekomst van continu printen op vezels.
Afdrukken met en zonder doorlopende vezel — in dezelfde afdruk
CEAD is samen met Logtenberg opgericht door Lucas Janssen. Zij waren de helft van het team dat het Nederlandse 3D-printerbedrijf Leapfrog oprichtte. "We hebben veel verschillende 3D-printmachines voor de industrie gemaakt", zegt Logtenberg. “Ik was de markt aan het verkennen en had het gevoel dat op grote schaal printen met materialen die geschikt zijn voor echt industriële toepassingen ontbrak. Je hebt meer kracht nodig dan alleen thermoplast.” Dit is wat printen met continue vezel oplevert. "Dus hebben we onze eigen technologie ontwikkeld, die we hebben gepatenteerd", vervolgt hij.
“We zien nog steeds behoefte aan prints met korte vezel en zonder vezel.” Dit is de reden waarom CEAD's Continuous Fiber Additive Manufacturing (CFAM) technologie maakt printen met continue vezel en . mogelijk met directe extrusie uit onversterkte of korte vezelversterkte korrels binnen dezelfde print . "We hoeven de printkop niet te vervangen", legt Logtenberg uit. “We leggen de continue vezel in het midden van de smelt, zodat beide tegelijk worden geëxtrudeerd. Maar ze gebruiken verschillende aandrijfsystemen. De continue vezel wordt door de printkop geduwd maar vooraf geïmpregneerd om de kwaliteit te garanderen.”
Reeds standaard in spuitgegoten en overmolded composieten, evenals compressiegegoten directe lange vezel thermoplastische (DLFT) composieten, directe extrusie van pellets/granulaatmaterialen is goedkoper voor industriële productie, zegt Logtenberg. "Deze materialen moeten worden gedroogd pre-print, en we hebben onze eigen droger ontwikkeld, die is aangesloten op de CFAM-machine.”
Net als bij overmolded thermoplastische composieten, wordt voor elke print hetzelfde polymeer gebruikt in zowel het voorgeïmpregneerde continue filament als de onversterkte of met korte vezel versterkte directe extrusie. Het bedrijf heeft een breed scala aan polymeren verwerkt, waaronder ABS, PC, PEEK, PET, PLA en PP. Ze onderzoeken nu PEKK en PAEK met laag smeltpunt.
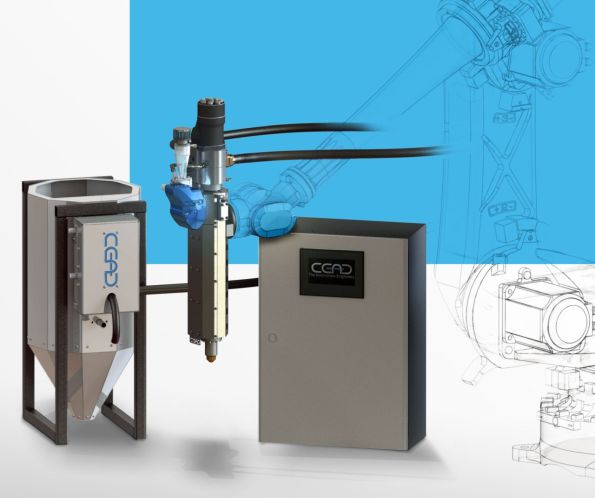
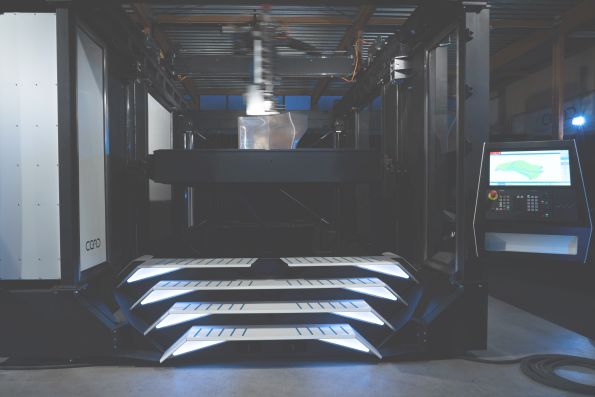
CEAD biedt een kleinere extrusiekop voor robotarmen (boven) en de CFAM Prime (onder) op een portaal gebaseerde machine met een bouwvolume van 4 m x 2 m x 1,5 m.
BRON:CEAD
Verwarmingszones en portaal versus robot
Momenteel biedt CEAD de Robot-extruder aan, met vier verwarmingszones, en de op een portaal gebaseerde CFAM Prime machine, met een bouwvolume van 4 bij 2 bij 1,5 meter en 10 verwarmingszones in de extruder. “We zijn in 2017 begonnen met de ontwikkeling”, zegt Logtenberg. “De printkop is gebaseerd op een enkelschroefsextruder die vaak wordt gebruikt bij spuitgieten. Je hebt zones nodig om het materiaal geleidelijk te verwarmen, zodat je de grote hoeveelheid druk kunt uitoefenen die nodig is (50-60 bar) om zoveel materiaal te extruderen. De pellets worden overgebracht naar het vat, waar ze smelten, dan comprimeer je en duw je. Als je te snel opwarmt, bouwt de extruder geen druk op.”
Waarom de extruder/printkop apart verkopen? "Klanten wilden ook een kleinere extruder voor een robotarm om hun eigen machines te bouwen, maar zonder continue vezels, alleen directe extrusie", zegt Logtenberg. Waarom dan een portaal gebruiken voor de CFAM Prime? Het korte antwoord:nauwkeurigheid en snelheid. "Robots zijn erg goed in relatieve nauwkeurigheid", legt hij uit, "maar de manier waarop ze vanaf punt A bij punt B aankomen, is onnauwkeurig. Met 3D-printen moet je continu nauwkeurig bewegen om een hoogwaardig, afgewerkt onderdeel te creëren.”
"Het andere probleem is snelheid", vervolgt hij. “We wilden een hoge output voor industriële productie, maar ook met een hoge resolutie. Een robotarm die onze extruder gebruikt, kan met 4 m/min bewegen, wat erg snel is voor een robot, maar de portaalmachine kan met 60 m/min bewegen .”
Hoewel het portaal snelheid biedt, biedt een extruder op een robotarm nog steeds meerassig printen . "We zijn geïnteresseerd in het gebruik van meerassig printen om de huidige uitdaging met z-richtingseigenschappen [typisch voor afdrukken in plakjes] te overwinnen", erkent Logtenberg. “We hebben eerst het portaalsysteem ontwikkeld, maar hebben nu een nieuw besturingssysteem van Siemens dat dezelfde besturing biedt op een robotarm. Dus we ontwikkelen 5-assige machines . Het portaalsysteem is nog steeds sneller, maar dit nieuwe systeem biedt een echte meerassige plaatsing.” Hij stelt zich voor om de twee systemen te combineren, vergelijkbaar met de configuratie voor 5-assige CNC-freesmachines.
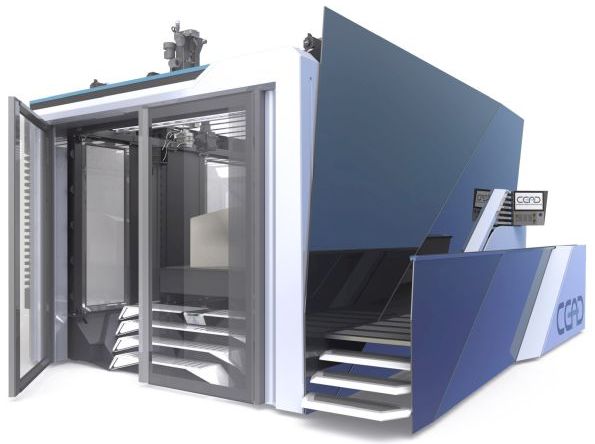
CFAM Prime-machine met gesloten kamer (onder ).
BRON:CEAD
Koeling en controle
Een van de problemen bij 3D-printen is het beheersen van krimp van de kunststofmatrix. Hoewel de CFAM Prime aanvankelijk gebruik maakte van infrarood (IR) verwarming, beheerd met input van thermische camera's, geeft Logtenberg toe dat dit systeem ongelijkmatige verwarming produceerde bij het printen van complexe vormen. “We gebruikten nog steeds een afgesloten printkamer en ontwikkelen nu een verwarmd printbed ," hij zegt. "Dit zorgt voor meer gelijkmatige warmte en we zullen nog steeds thermische camera's gebruiken om het systeem te bewaken en te beheren. Als u hetzelfde onderdeel twee keer met een tussenpoos van zes maanden print, heeft u hetzelfde temperatuurprofiel en dezelfde omstandigheden in de printkamer.”
Logtenberg merkt op dat de CFAM Prime zoveel materiaal extrudeert dat er veel energie in zit. “Het is dus moeilijk om het snel genoeg af te koelen om de print stabiel te houden. Je wilt de lagen afkoelen om ze stabiel te maken tijdens het printen.”, voegt hij eraan toe. Hoe wordt deze koeling bereikt? "Met geforceerde lucht, en veel", zegt Logtenberg. Hij merkt op dat het toevoegen van warmte in het printbed en de gesloten printkamer deel uitmaakt van het beheersen van kromtrekken. “Je legt warme lagen op koele lagen. Maar je wilt het materiaal boven zijn Tg houden, die voor sommige materialen meer dan 150°C is, maar toch stabiel om erop te printen.” Zelfs met dit proces merkt Logtenberg op dat er altijd enige thermische spanning in het onderdeel zal zijn. "Je kunt een aantal stappen na het proces uitvoeren om de spanning uit het onderdeel te halen."
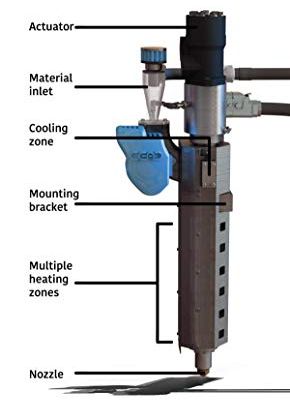
Robotextruder met meerdere verwarmingszones.
BRON:CEAD
CEAD gebruikt Siemens-systemen om zijn machines te besturen. “Deze zijn goed doordacht en kunnen complexe uitdagingen in het proces en de materialen aan”, legt Logtenberg uit. CEAD schreef zijn eigen software achter het Siemens-systeem om een eenvoudige gebruikersinterface te bieden. “De machine draait op G-code, wat ook de standaard is voor industriële freesmachines”, merkt hij op. “Dit geeft vrijheid bij het programmeren van de onderdelen. Het kan open source slicers gebruiken, maar ook Siemens NX , wat een krachtige softwaretool is.”
Logtenberg zegt dat de klant kan kiezen hoe complex hij/zij wil gaan. “Onze aanpak is erg open source , waardoor verschillende soorten printsoftware kunnen worden gebruikt. Dus als de klant een heel vereenvoudigde afdruk wil, druk je gewoon op een knop. Maar het is ook mogelijk om meer geavanceerde software te gebruiken. Dan moet de klant echter wel de kennis hebben om dit te gebruiken. Onze visie is om mensen te laten beslissen wat ze willen gebruiken en dan we ondersteunen ze .” Logtenberg merkt op dat CEAD aan bedrijven verkoopt, niet aan consumenten. "Dus we hebben de mogelijkheid om meer ondersteuning te bieden."
Gedrukte onderdelen en eigenschappen
"Je kunt het verschil voelen tussen onderdelen die zijn bedrukt met doorlopende vezels en onderdelen die zijn bedrukt met gehakte vezels", merkt Logtenberg op. “Maar we hebben nog geen eigenschappen getest.” Dat is de volgende taak, nu de ontwikkeling van de machine en de eerste lancering zijn voltooid. "Dit jaar zullen we werken aan het volledig karakteriseren van de materialen en het ontwikkelen van datasheets met druksterkte, stijfheid, enz. Voor elke materiaalcombinatie", voegt hij eraan toe.
Het bepalen van het gehalte aan holtes en het vezelvolume maakt ook deel uit van dit karakteriseringswerk. “Ons vezelgehalte is momenteel niet zo hoog”, geeft Logtenberg toe. “Als je de gehakte vezelkorrels gebruikt, heb je bijvoorbeeld 30 gewichtsprocent vezels. Door de continue vezel toe te voegen, komt daar nog maar 10% bij, omdat de totale output en het volume groot zijn.”
Hoe zit het met verdichting om de inhoud van lege ruimtes te verminderen? “Het mondstuk zelf verdicht de laag”, zegt Logtenberg. “Je moet de juiste laaghoogte versus breedte hebben. Als je dat goed hebt, krijg je een goede hechting tussen de lagen.” Hij legt uit dat de verhouding tussen hoogte en breedte moet in het juiste bereik zijn om compressiekracht in de afgedrukte laag toe te staan en voldoende warmte om een goede fusie in de lagen te krijgen. “Bij een bedrukte laag van 5 mm hoog en 5 mm breed zal er bijvoorbeeld bijna geen compressiekracht zijn”, merkt hij op. “Voor een laag van 5 mm hoog heb je een breedte van 10 mm nodig.”
CEAD verbetert continu de CFAM Prime-printkwaliteit, zegt Logtenberg. “We hebben veel interne software ontwikkeld om dynamisch te printen.” Hij legt uit dat er problemen waren in de hoeken omdat de extruder materiaal naar buiten duwt terwijl de machine moet vertragen om richting te draaien. “Dat probleem hebben we nu opgelost. We blijven onze tracking ontwikkelen met behulp van sensoren, de dynamiek en de laagtemperatuur, bijvoorbeeld om de procescontrole te verbeteren .”
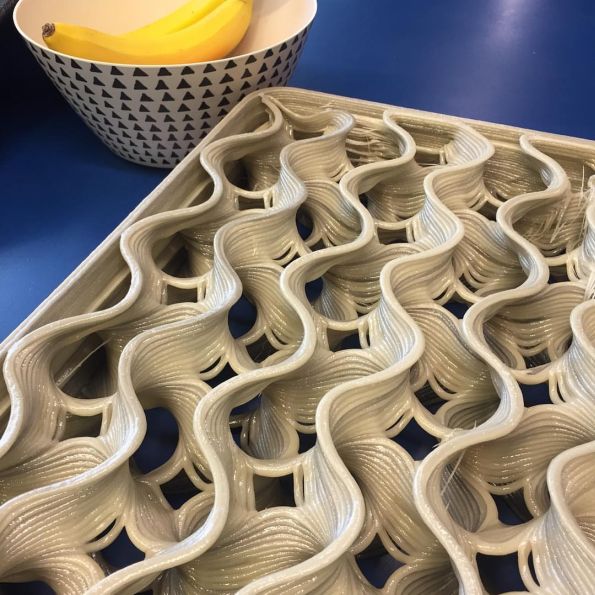
Complexe vormen afdrukken met CFAM Prime.
BRON:CEAD Instagram, maart 2019
Machines voor de scheepvaart en de bouw
Logtenberg zegt dat de eerste doelen voor de industriële productiecapaciteit van CEAD Prime de maritieme en bouw- en infrastructuurmarkten zijn, omdat de geprinte composietonderdelen goed genoeg zijn om direct te worden gebruikt voor eindservice. De eerste klanten zijn inderdaad Royal Roos (Rotterdam, Nederland), een bedrijf voor waterbouwkunde en constructie, en Poly Products (Werkendam, Nederland), een fabrikant van composieten die werkzaam is in de sectoren scheepvaart, architectuur, industrie, recreatie en transport.
Dat gezegd hebbende, wordt de CFAM Prime ook gebruikt om mallen te printen, vooral voor maritieme constructies. "Daarom zijn we verder gegaan met de robotarm", zegt Logtenberg, "en hebben we CNC-frezen toegevoegd , net als de LSAM-machine [van Thermwood], maar een beetje kleiner en goedkoper.”
"In de EU is de bouwsnelheid voor marine gedaald", zegt hij. “Omdat de arbeid zo duur is, gaat de productie naar China. Dus we proberen een manier te vinden om te concurreren. We kijken ook naar andere markten, zoals de automobiel-, lucht- en ruimtevaart en ander transport.”
De respons in de scheepvaart- en bouwmarkt was goed. "We doen veel projecten om te laten zien wat de machine kan", zegt Logtenberg. “Na de lancering afgelopen najaar verliep de verkoop trager dan we hadden gewild. Maar nu gaat het goed, met versnelde projecten en machine-ontwikkelingen.”
Voor deze nieuwe markten verkent CEAD nieuwe materialen. Het test bijvoorbeeld een materiaal van SABIC op brandweerstand en praten met treinfabrikanten . Met de mogelijkheid om continue glasvezel te printen, kan CFAM ook worden gebruikt om te printen met draad en/of sensoren ? “We zijn dit aan het onderzoeken”, zegt Logtenberg. "We werken samen met een bedrijf om staalvezel in te bedden , die ook geleidend is.”
Toekomstvisie
Veel in de traditionele composietenindustrie vragen zich af hoe 3D-geprinte continue vezelcomposieten kunnen concurreren met conventionele composieten wanneer ze zo'n laag vezelgehalte hebben en zo'n groot potentieel voor delaminatie tussen de geprinte lagen. "Zeker, sterkte in de z-richting is een van de meest uitdagende dingen voor 3D-geprinte composieten", beaamt Logtenberg. “We concurreren momenteel niet met conventionele composieten. We denken dat we in de toekomst kunnen concurreren met conventionele composieten omdat onze productie volledig geautomatiseerd is, maar we hebben nog een lange weg te gaan. Op dit moment is het een aanvulling op de huidige productiemethoden, waardoor het flexibiliteit biedt en ontwerp- en productiemogelijkheden opent.”
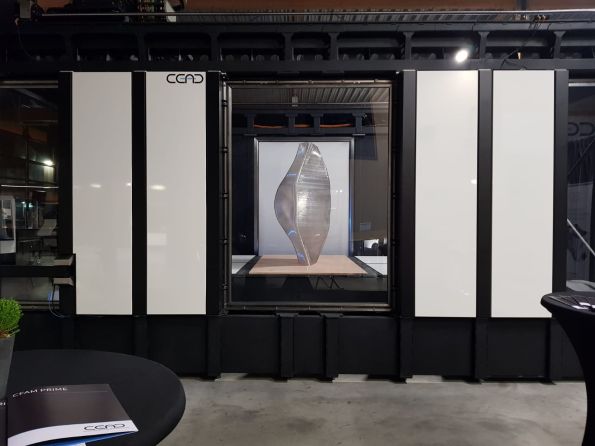
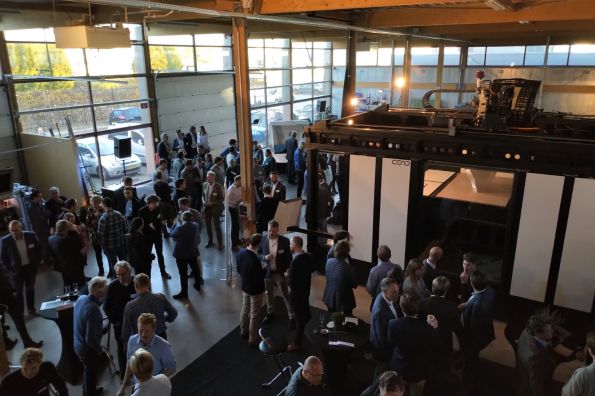
De CFAM Prime-machine bij zijn lancering in 2018.
BRON:CEAD
Hars
- Inzicht in composiettechniek en koolstofvezel
- De economie van 3D-printen
- 3D-printen van een koolstofvezel drone – deel 2
- Impossible Objects werkt samen met BASF voor composiet 3D-printen
- Continue vezelproductie vervaagt de grens tussen 3D-printen en AFP
- Covestro lanceert Maezio thermoplasten met continue vezels
- Continuous Fiber Manufacturing (CFM) met moi-composieten
- SD Mines composietmateriaal gedemonstreerd tijdens composiet brugwedstrijd
- 3D-print composieten met continue vezels
- Samengestelde materialen:waar ze te vinden zijn op NPE2018
- 3D-printen van composietmaterialen:een inleidende gids