Thermoplastische composieten:klaar om een stap voorwaarts te maken
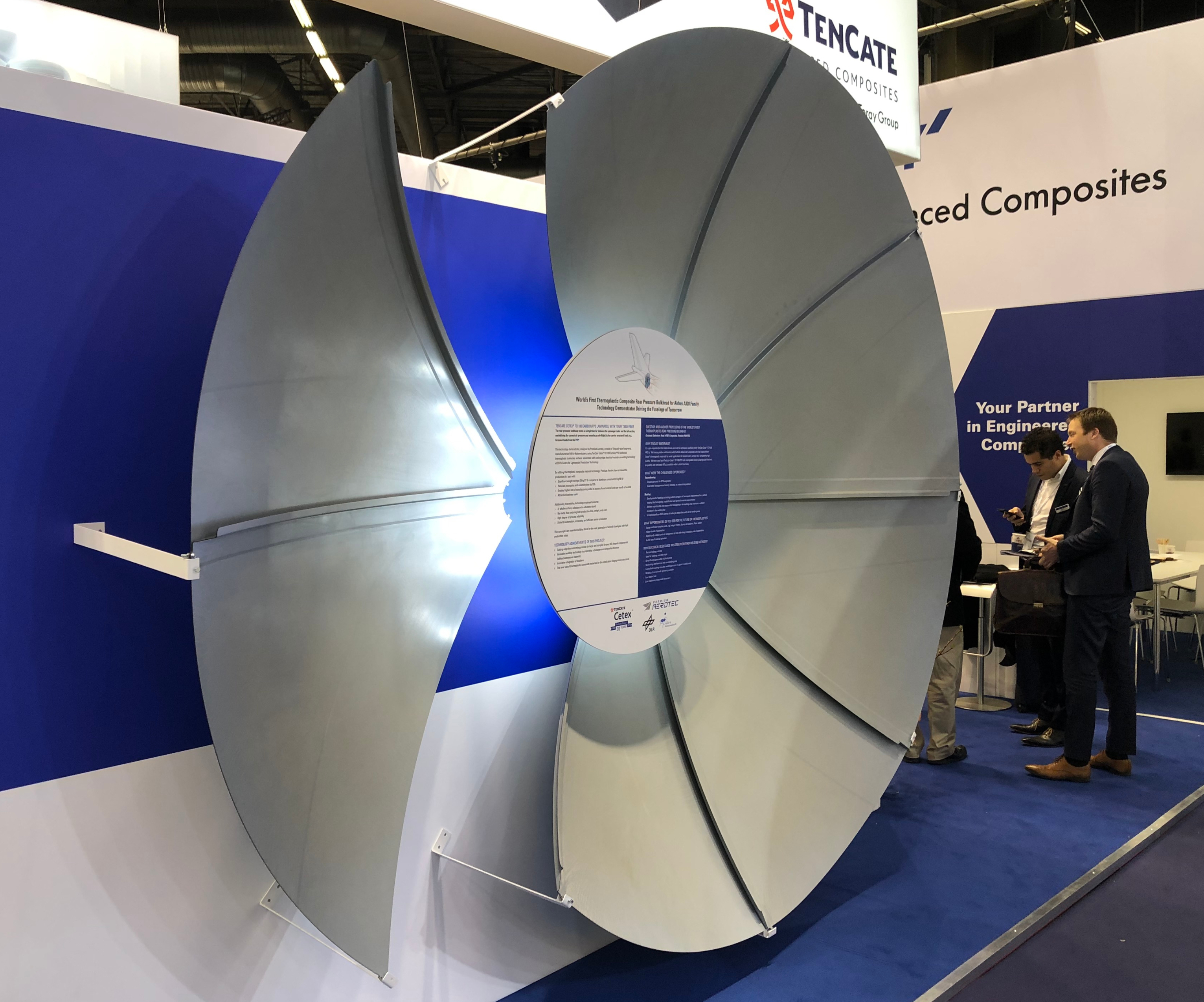

Thermoplastische composieten (TPC) zijn niet nieuw in de lucht- en ruimtevaartsector, maar de afgelopen jaren heeft het gebruik van thermoplasten in commerciële vliegtuigen een kantelpunt bereikt. Terwijl TPC's al enige tijd worden gebruikt voor kleinere onderdelen zoals clips en beugels, of kleinere interieurcomponenten, hebben thermoplasten geleidelijk hun weg gevonden naar grotere vliegtuigconstructies en lijken nu klaar om een grotere rol te spelen in de toekomst van commerciële vliegtuigen.
In maart 2018 verwierf Toray Industries Inc. (Tokyo, Japan), 's werelds grootste koolstofvezelfabrikant, TenCate Advanced Composites (Morgan Hill, Californië, VS en Nijverdal, Nederland) voor € 930 miljoen (TenCate heeft sindsdien haar naam veranderd in Toray geavanceerde composieten). De verhuizing leek een poging te zijn om de thermoplastische capaciteiten van Toray te versterken ter voorbereiding op de volgende golf van ontwikkeling van commerciële vliegtuigen. Kort na die aankondiging kondigden Hexcel (Stamford, Conn., VS) en Arkema Inc. (King of Prussia, Pa., VS) een strategische alliantie aan om thermoplastische composietoplossingen voor de ruimtevaart te ontwikkelen, waarbij Hexcels vaardigheid in koolstofvezelproductie werd gecombineerd met Arkema's polyetherketonketon (PEKK) harsen expertise. En in de loop van het jaar leken verschillende andere stukjes van de thermoplastische puzzel op hun plaats te vallen.
In april 2018 onthulde Premium Aerotec GmbH (Augsburg, Duitsland) een demonstratiemodel voor een Airbus (Toulouse, Frankrijk) A320-drukschot dat het had ontwikkeld en vervaardigd met koolstofvezel in een thermoplastische matrix. De demonstrator, die uit acht gelaste segmenten bestaat, illustreert hoe de lasbaarheid van thermoplasten de potentie heeft om grotere vliegtuigonderdelen mogelijk te maken. (Meer informatie over Premium Aerotec's A320 drukschotdemonstrator).
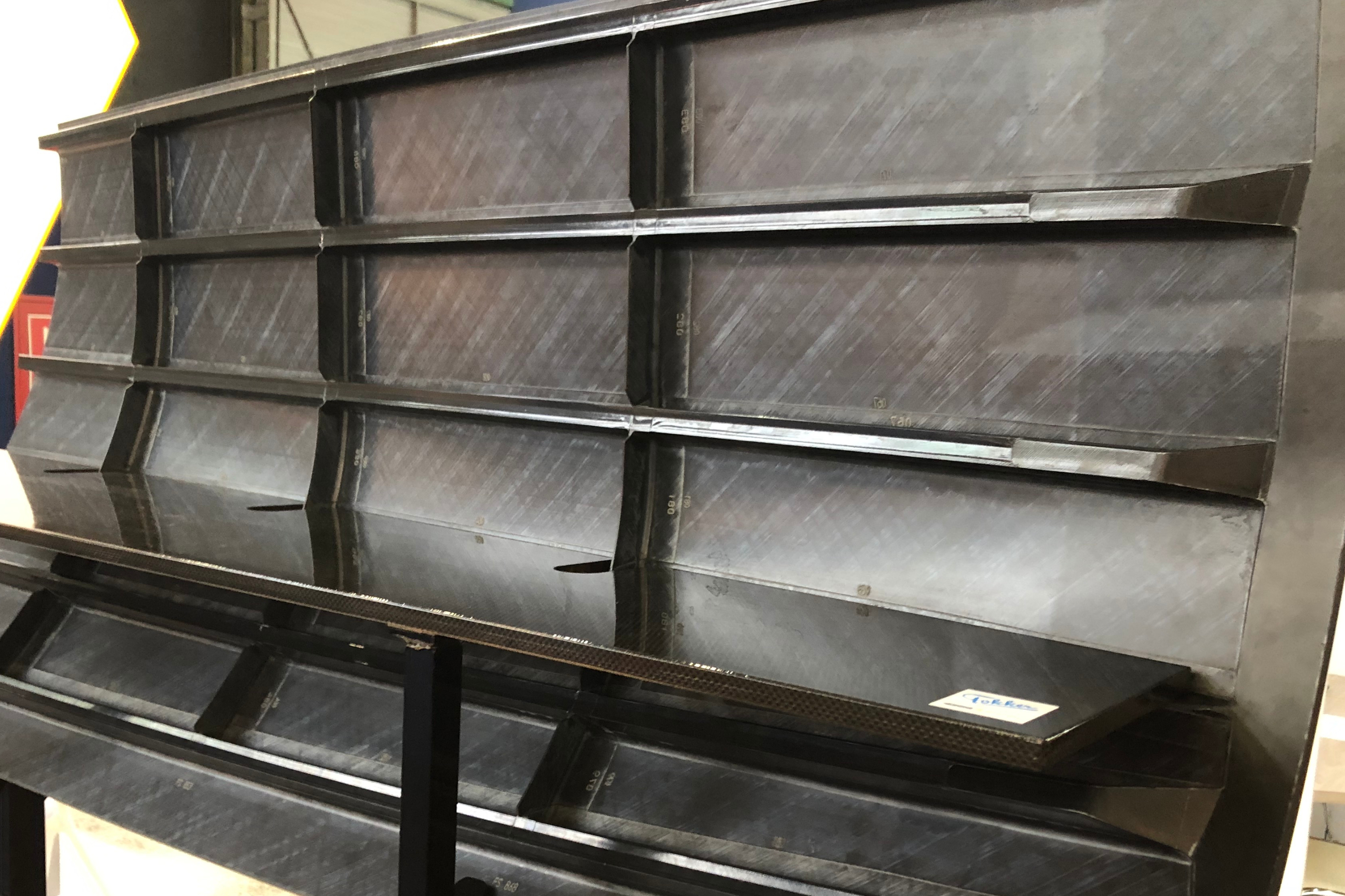
In augustus 2018 lanceerden Solvay (Alpharetta, Ga., VS), Premium Aerotec en Faurecia Clean Mobility (Columbus, Ohio, VS) IRG CosiMo (Industry Research Group:Composites for Sustainable Mobility), een consortium dat zich toespitst op de ontwikkeling van materialen en procestechnologieën gericht op het mogelijk maken van grootschalige productie van thermoplastische composieten voor de luchtvaart- en automobielmarkten. Het consortium combineert bedrijven uit de gehele procesketen van thermoplastische composieten, van materialen tot machines tot toepassingen in de auto- en ruimtevaart. (Lees hier meer over het IRG CosiMo-consortium).
Solvay werkt sinds juni 2017 samen met GKN Fokker (Hoogeveen, Nederland) om de technologie vooruit te helpen en TPC's verder te gebruiken voor grote ruimtevaartconstructies. Het bedrijf startte met de productie van PEKK-polymeer in september 2017 en verdubbelde vervolgens zijn capaciteit voor gekwalificeerde UD-thermoplastische tape in 2018. Eerder in 2019 heeft Solvay een speciaal TPC-onderzoekslab in gebruik genomen in Alpharetta, Ga., VS, gericht op de ontwikkeling van materialen van de volgende generatie. Solvay is van plan eind 2019 te beginnen met de kwalificatie van een nieuwe UD-tapelijn.
Teijin Ltd. (Tokyo, Japan) heeft in januari 2019 aangekondigd dat zijn TENAX-koolstofvezel en koolstofvezel/thermoplastische unidirectionele voorgeïmpregneerde tape (TENAX TPUD) door Boeing (Chicago, Illinois, VS) is gekwalificeerd voor gebruik als intermediair geavanceerd composietmateriaal voor primaire structurele onderdelen (Lees hier het volledige nieuwsbericht).
Naarmate deze en soortgelijke technologieën en materialen vorderen, ontstaat geleidelijk een beeld van hoe de lucht- en ruimtevaartindustrie eruit zou kunnen gaan zien in de komende jaren en decennia. De rol van TPC's wordt een steeds groter onderdeel van dat plaatje.
Fabrikanten zijn geïnteresseerd in het profiteren van de fabricagevoordelen en snelle verwerkingstijden van thermoplasten, en in het gebruik van TPC's om grotere constructies zoals romppanelen en ribben te gaan maken. Bovendien hebben thermoplasten een hoge breuktaaiheid; goede mechanische eigenschappen; recycleerbaarheid; lage vlam, rook en giftigheid (FST), en kan bij kamertemperatuur worden bewaard. En naarmate OEM's en leveranciers van luchtvaartlagen meer vertrouwd raken met thermoplasten, worden ze gebruikt voor complexere onderdelen, gelaste assemblages en primaire constructies.
Volgens Steve Mead, managing director bij Toray Advanced Composites (voorheen TenCate), "zijn [grote vliegtuigbouwers] echt op zoek naar een materiaaloplossing die de snelheidscapaciteiten van aluminium en de gewichtscapaciteiten van op koolstofvezel gebaseerd materiaal heeft - een soort thermoplastische brug dat gat.”
Verwerkbaarheid van TPC's
Een groot deel van de reden waarom TPC's hun plaats vinden in vliegtuigprogramma's, is hun verwerkbaarheid. Omdat thermoplasten al volledig gepolymeriseerd zijn, hebben ze een hogere productiesnelheid dan thermoharders, die moeten worden uitgehard.
"Als je kijkt naar de hoeveelheid tijd die nodig is om vandaag een thermohardend onderdeel te maken en het vergelijkt met de hoeveelheid tijd die nodig is om een onderdeel van thermoplastisch composiet te maken, is [thermoplast] ongeveer 10 keer sneller", zegt Mike Favaloro, president en CEO van CompositeTechs LLC (Amesbury, Mass., VS), een adviesbureau voor de composietindustrie.
Een groot voordeel van thermoplastische geautomatiseerde vezelplaatsing (AFP) in vergelijking met thermohardende AFP - vooral gezien het ontbreken van een uithardingscyclus - zijn hogere productiesnelheden als gevolg van snellere verwerkingstijd. Er zijn kostenbesparingen te vinden bij in-situ laminering en out-of-autoclave (OOA) post-consolidatie. Bovendien zorgt het weglaten van de autoclaaf voor de ontwikkeling van grotere structuren.
David Leach, directeur bedrijfsontwikkeling voor ATC Manufacturing (Post Falls, Idaho, VS), erkent dat de kosten per eenheid van thermoplasten hoger zijn dan de kosten van thermoharders, maar stelt dat de prijzen van TPC-materiaal zullen dalen. Verder, zegt hij, biedt de efficiëntie van de verwerking de mogelijkheid om de kosten van vandaag te verlagen. De algemene consensus in de composietenindustrie is dat OOA-thermoplastische processen op dit moment kostenbesparingen bieden van meer dan 30 procent in vergelijking met thermoharders.
"Thermoplastieken vinden hun weg naar programma's, zelfs nadat vliegtuigen in productie zijn gegaan", merkt Leach op. "Het is een bewijs van de kostenvoordelen van thermoplasten."
Het potentieel van hoogwaardige matrixpolymeren gaat verder dan wat momenteel op de markt beschikbaar is. Doug Brademeyer, hoofd van Ultra-Polymers Materials bij Solvay, zegt dat het bedrijf zowel intern als met partners werkt aan de ontwikkeling van op maat gemaakte polymeren die zijn aangepast aan de verschillende fabricageprocessen.
"We zijn enthousiast over deze PAEK-oplossingen op maat en kunnen deze snel commercialiseren in onze wereldwijde activa, op basis van de behoeften van de klant", zegt Brademeyer.
Laag smeltend PAEK
Met vliegtuig-OEM's en leveranciers die strijden om hogere productiesnelheden en kortere cyclustijden, is verwerkbaarheid van cruciaal belang. Polyetheretherketon (PEEK) is al lang het favoriete thermoplastische polymeer omdat het de grootste database heeft en het meest gekwalificeerd is. Maar volgens Favaloro biedt low-melt polyarlyetherketon (LM PAEK) enkele voordelen, vooral voor geautomatiseerde verwerkingsmethoden zoals ATL.
"PEEK is verwerkbaar via stempelvormen en continu gieten, maar LM PAEK verwerkt bij een lagere temperatuur, heeft een lagere werkviscositeit die een betere geautomatiseerde verwerking mogelijk maakt, en heeft een lagere mate van kristalliniteit waardoor de resterende vormspanningen worden verminderd", zegt hij."Het uiteindelijke doel is om een ATL-machine te gebruiken om [de tape] neer te leggen en ermee klaar te zijn - je hebt de juiste mate van kristalliniteit, een goed venster en goede neerlegsnelheden nodig."
LM PAEK heeft een breed procesvenster van 350-385ºC. Ter referentie:de verwerkingstemperaturen van polyfenyleensulfide (PPS) variëren van 330-350°C, terwijl de verwerkingstemperaturen van polyetherketonketon (PEKK) en PEEK respectievelijk 380°C en 400°C zijn.
"Het materiaal heeft zoveel grip gekregen vanwege de verwerkbaarheid", zegt Scott Unger, technisch directeur bij Toray Advanced Composites. Toray Advanced Composites werkte samen met Victrex (Lancashire, V.K.) om Cetex TC1225 te produceren, een unidirectionele tape met LM PAEK.
"De bedoeling met de ontwikkeling van TC1225 was om een product te creëren dat gemakkelijk kan worden verwerkt bij temperaturen die dicht bij die van PPS liggen, een gunstige kostenpositie heeft voor de eindgebruiker en de mechanische en vloeistofbestendige eigenschappen van PEEK heeft", zegt Unger. "Met TC1225 LM PAEK heb ik het gevoel dat we al deze doelen hebben bereikt."
Cetex TC1225 wordt momenteel gekwalificeerd door het National Center for Advanced Materials Performance (NCAMP, Wichita, Kan., V.S.). Bovendien zegt Toray dat er twee belangrijke op vliegtuigbouwers gebaseerde kwalificaties in de maak zijn voor het materiaal, evenals een aantal kwalificatieprogramma's op basis van opkomende markten zoals luchttaxi's en stedelijke luchtmobiliteit.
Tapes die LM PAEK gebruiken, leveren naar verluidt verbeterde neerlegsnelheden op. Tim Herr, directeur van Aerospace SBU bij Victrex, zegt:"De uitvalpercentages die we kunnen bereiken voor zowel in-situ AFP als geconsolideerde AFP buiten de autoclaaf zijn ongekend." Hij geeft aan dat 60 meter per minuut kan worden gehaald op oven-geconsolideerde panelen; 20 meter per minuut is naar verluidt mogelijk met in-situ consolidatie.
Wat de kwaliteit betreft, beweert Unger dat PAEK met een laag smeltpunt de mogelijkheid biedt om dezelfde laminaatkwaliteit te krijgen met in-situ plaatsing van vezels als met een met vezels geplaatst laminaat dat door een ovenconsolidatie na plaatsing van de vezels is gehaald.
Composieten verlijmen
De lasbaarheid van TPC's is een groot voordeel van het materiaal voor gebruik bij het ontwikkelen van vliegtuigen. Fusion bonding/lassen biedt een alternatief voor mechanische bevestiging en het gebruik van lijmen, beide methoden die worden gebruikt voor het verbinden van thermohardende composietdelen.
Stephen Heinz, productontwikkelingsdirecteur bij Solvay, zegt:“Verbinden en lassen spelen een belangrijke rol in de toekomst van assemblage en hebben het potentieel om kosten te besparen en de betrouwbaarheid van aerostructuren te verbeteren. Bedrijven als GKN Fokker nemen het voortouw bij het demonstreren van lassen.”
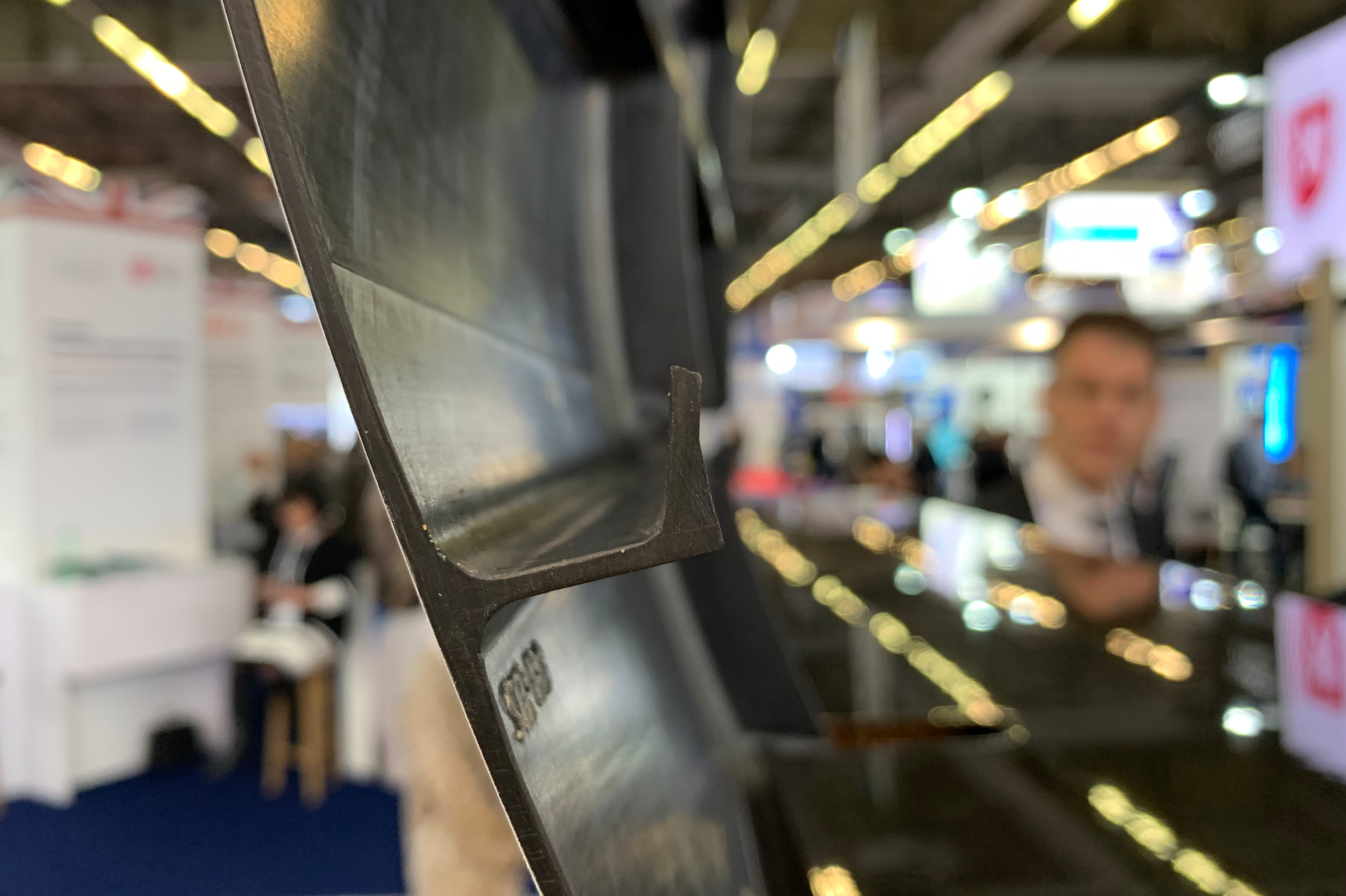
GKN Fokker (Hoogeveen, Nederland) werkt al geruime tijd aan de ontwikkeling van TPCwelding, nadat hij in de jaren negentig begon te experimenteren met weerstandslassen van thermoplasten. Het bedrijf gebruikt thermoplastische lasprocessen om toonaangevende interne ribben en huiden te verbinden. Op JEC World 2019 toonde het bedrijf een gebiedsgeregeerd thermoplastisch composiet romppaneel vervaardigd met Solvay's APC (PEKK-FC) UD-tape. Het panel is het resultaat van een gezamenlijk R&D-project tussen GKN Fokker en Gulfstream Aerospace (Savannah, Ga., V.S.). Het onderdeel is naar verluidt het goedkoopste composietpaneel, dankzij de eenvoudige "stomp-verbonden" orthogrid-versteviging en volledig gelaste frames.
"Met thermoplasten kan een orthogrid sterk worden vereenvoudigd door het raster met de huid te 'stompen'", legt Arnt Offringa, hoofd Thermoplastic Composites Technology Development bij GKN Fokker, uit. "Het raster bestaat nu uit eenvoudige, platte voorvormen die samen met het huidlaminaat worden samengevoegd tot een goedkope, integraal verstijfde schaal. Frames worden op het rooster gelast. Deze lassen worden onder afschuiving belast, waardoor het mogelijk is om alle bouten weg te laten.”
Terwijl gelaste thermoplastische constructies al enige tijd in luchtcafts worden gebruikt, lijkt de technologie nu geschikt voor gebruik in primaire constructies. Mike Favaloro is van mening dat lucht- en ruimtevaartfabrikanten en OEM's meer vertrouwen krijgen in TPC's, met name met procesbeheersing. "Over een horizon van 10 jaar zullen we zien dat het veel meer wordt aangenomen", zegt hij.
Lees meer over lastechnologie in het artikel van Ginger Gardiner "Las van thermoplastische composieten."
Zonder gereedschap
Een andere innovatie aan de horizon die een versnelling van het gebruik van thermoplasten mogelijk zou kunnen maken, is de fabricage van composieten zonder gereedschap. Het concept, zoals de naam al aangeeft, maakt traditionele mallen en gereedschappen overbodig en vervangt ze door robotica.
Lucht- en ruimtevaartfabrikant General Atomics Aeronautical Systems Inc. (GA-ASI, San Diego, Californië, VS) ontwikkelt een dergelijk proces voor de fabricage van thermoplastische composietstructuren. Composite Automation LLC (Cape Coral, Fla., V.S.), met apparatuur van Mikrosam (Prilep, Macedonië) werkte samen met GA-ASI om de automatisering te ontwikkelen. Het proces maakt gebruik van twee 6-assige robots die samenwerken om thermoplastische tape te plaatsen. Eén robot bestaat uit een standaard unidirectioneel tape-plaatsingssysteem dat laserverwarming biedt om in-situ consolidatie van het thermoplastische materiaal uit te voeren. De tweede robot biedt ondersteuning en werkt tegenover de geautomatiseerde tapelaag (ATL) om een beweegbaar gereedschapsoppervlak te bieden waartegen de ATL tape plaatst. (Zie voor meer informatie "General Atomics Aeronautical ontwikkeling van gereedschapsloze thermoplastische composieten.")
Recyclebaarheid
Een ander voordeel van TPC's is de recyclebaarheid. Omdat thermoplastische polymeren kunnen worden omgesmolten en omgevormd, kijken verschillende bedrijven naar TPC's als een manier om materialen te hergebruiken.
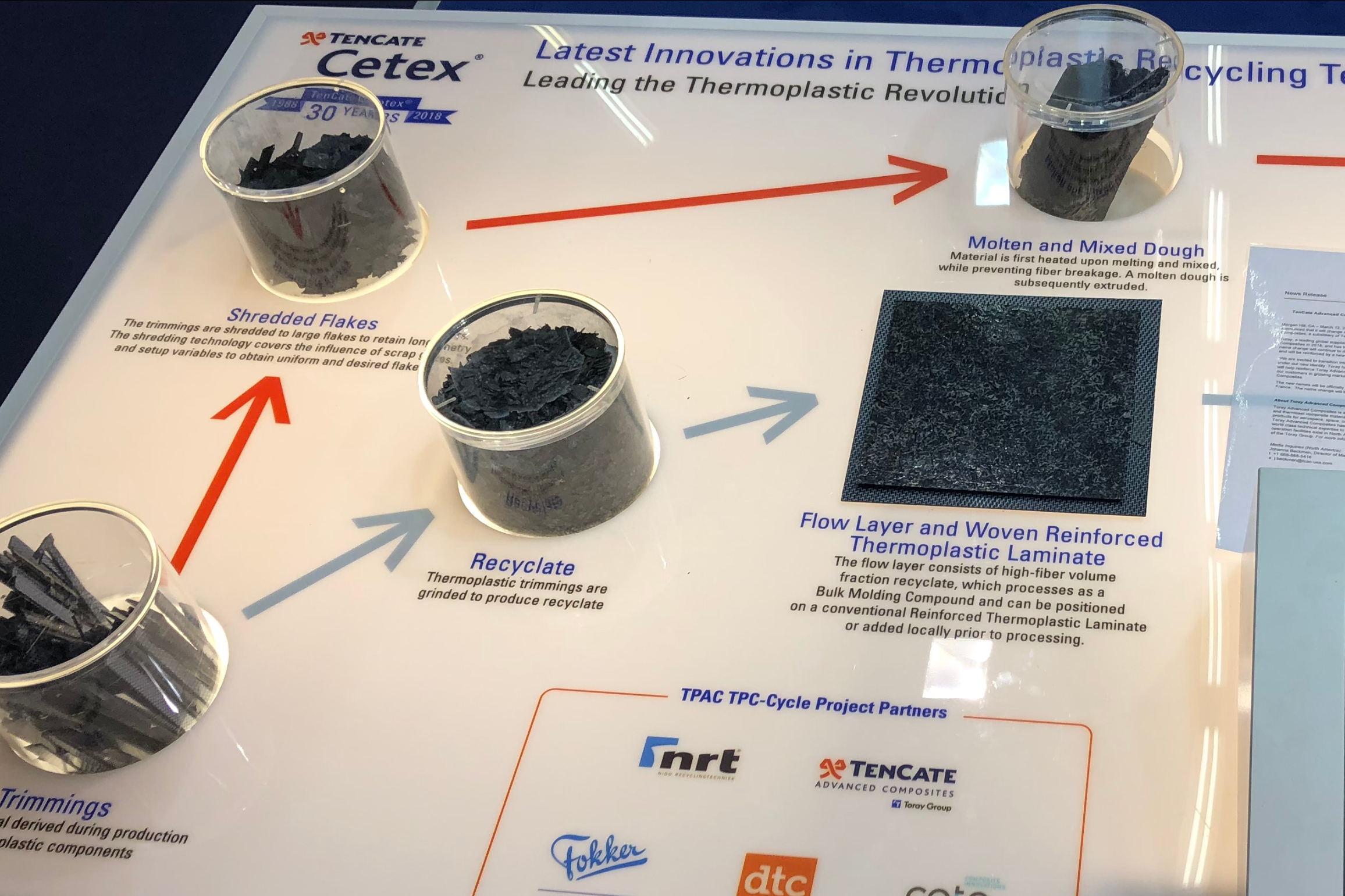
Een dergelijk recyclinginitiatief, dat wordt uitgevoerd door het Thermoplastic Composites Application Centre (TPAC, Enschede, Nederland) en het Thermoplastic Composites Research Centre (TPRC, Enschede, Nederland), is gericht op hergebruik van productieschroot van TPC-verwerking, van inzameling tot versnippering en herverwerking tot aan de toepassing. Het TPC-Cycle-project werkt aan de ontwikkeling van een betaalbare, milieuvriendelijke recyclingroute voor high-end, high-volume markten - en dit alles terwijl een materiaal wordt geproduceerd dat zoveel mogelijk van de mechanische eigenschappen van de originele thermoplastische materialen behoudt. Het project beschikt over korte cyclustijden, productie van netvormen en zou de productie van complexe vormen mogelijk maken.
De samenwerking omvat verschillende industriële partners in de waardeketen, van materiaal, productie, ontwerp en toepassing, waaronder GKN Fokker, Toray Advanced Composites, Cato Composite Innovations (Rheden, Nederland), Dutch Thermoplastic Components (Almere, Nederland) en Nido RecyclingTechniek (Nijverdal , Nederland).
Het juiste materiaal voor de juiste klus
Dus te midden van het lawaai van opwinding over deze materialen, rijst de vraag:zijn TPC's aangekomen? Tier 1 en Tier 2 lucht- en ruimtevaartleveranciers investeren in thermoplasten. Er is meer interesse en investering van kleinere en middelgrote leveranciers. Consortia zoals IRG CosiMo kijken naar zowel de lucht- en ruimtevaartmarkt als de automobielmarkt om procestechnologieën vooruit te helpen om grootschalige productie te realiseren.
"Het is de Trifecta", zegt Mead, "OEM's investeren, mensen in machines investeren, het juiste materiaal is ontwikkeld. Alle componenten van het recept komen samen.”
Wat betekent dit alles in groter verband als het gaat om het gebruik van materialen in vliegtuigen van de volgende generatie? Er zijn tenslotte talloze materialen die strijden om een plek in het vliegtuig van de toekomst, en de innovatie vertraagt niet - thermohardende composieten blijven evolueren; aluminium en titanium zullen een rol blijven spelen.
"Omdat vliegtuigbouwers een kwalificatiebasis ontwikkelen met thermoplasten, hebben ze nu een keuze", zegt Unger. "En die keuze zal gebaseerd zijn op het selecteren van het juiste materiaal voor een bepaalde toepassing dat voldoet aan de productiesnelheid en kostenvereisten voor het onderdeel of de constructie in kwestie. Als je kijkt naar de toekomstige commerciële luchtvaart, denk ik dat je vliegtuigbouwers het juiste materiaal voor de juiste taak zult zien gebruiken. Als een materiaal de meest geschikte structuur mogelijk maakt voor de laagste kosten en voldoet aan de vereisten voor de opbouwsnelheid van het programma, zal het zijn weg naar het vliegtuig winnen."
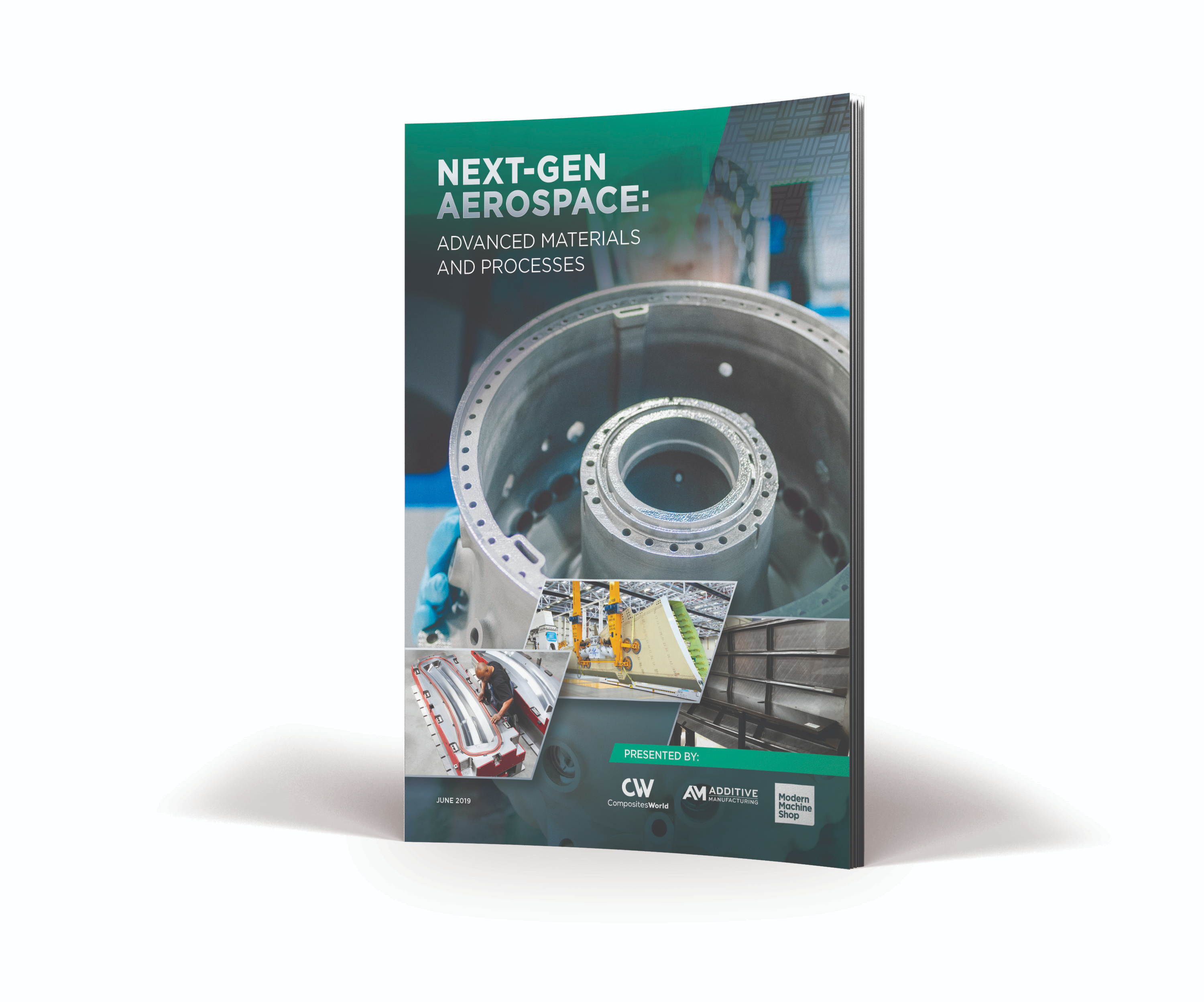
De volgende generatie lucht- en ruimtevaartfabricage
Aangezien de commerciële luchtvaartindustrie naar verwachting in de komende 20 jaar zal verdubbelen, zijn nieuwe technologieën en ongekende productiesnelheden nodig om aan de vraag naar passagiers- en vrachtvliegtuigen te voldoen.
Leer meer over de materialen en processen die de volgende generatie vliegtuigen zullen vormen in een verzameling verhalen van CompositesWorld, Modern Machine Shop en Additieve productie , beschikbaar om gratis te lezen of te downloaden . Download het hier.
Hars
- Covestro verhoogt investeringen in thermoplastische composieten
- Thermoplastische composieten bij Oribi Composites:CW Trending, aflevering 4
- Problemen oplossen met thermovormen van thermoplastische composieten
- Thermoplastische composieten:structurele bumperbeugel
- Toray Advanced Composites breidt mogelijkheden voor thermoplastische composieten uit
- Teledyne CML Composites investeert in verwerkingscapaciteit voor thermoplasten
- ACMA lanceert Thermoplastic Composites Conference 2020-programma
- Thermoplastische deur een primeur voor autocomposieten
- Thermoplastische composieten:schilderachtig uitzicht
- CAMX 2018 preview:TenCate Advanced Composites
- Thermoplastische composieten lassen