Plantentour:Holland Composites, Lelystad, Nederland
Foiling catamarans, gevels van gebouwen en meer. Holland Composites ligt op minder dan een uur rijden van Amsterdam en voert een breed scala aan zeer technische projecten uit in haar 4.500 m2 grote 2 faciliteit. Bron, alle afbeeldingen | Holland Composites
Holland Composites (Lelystad, Nederland) is gevestigd in een gebouw van 4.500 vierkante meter op minder dan een uur rijden van Amsterdam en richt zich op vier markten:marine/offshore, architectuur, duurzame energie en speciale projecten. Holland Composites gebruikt een mix van prepreg koolstofvezelversterkt polymeer (CFRP) en Nomex honingraat voor zwaarbelaste onderdelen, en harsinfusie en glasvezel voor de bouw en projecten met een lagere marge. "We zijn nog steeds in staat om hoge prestaties neer te zetten, zelfs met deze meer kosteneffectieve constructies, en we handhaven een lage overhead voor de onderdelen met behulp van geavanceerde materialen", zegt Sven Erik Janssen, co-managing partner van Holland Composites, samen met oprichter Pieterjan Dwarshuis. "Dit is uniek."
Het bedrijf exploiteert ook het merk DNA Performance Sailing en produceert foiling meerrompszeilboten, waaronder de 5,5 meter lange F1X-catamaran, de 11 meter lange TF10 trimaran en de 14 meter lange F4-catamaran. De 12 meter lange G4-catamaran is niet langer in productie, "maar het toont onze capaciteiten voor geavanceerde composiet jachtbouw en hoge prestaties", merkt Janssen op. “Deze boot is een dual-purpose foiling racer en familie cruiser met ligplaatsen, keuken en kop, maar haalt toch een snelheid van meer dan 35 knopen. Het vermogen om te foilen met een gewicht van meer dan 4.000 kilogram en slechts een bemanning van zes personen - er is nog steeds geen concurrentie op dit gebied, behalve de vele miljoenen dollars kostende America's Cups-jachten."
Marine naar weg- en luchtvervoer
Voordat de rondleiding begint, geeft Janssen een geschiedenis van het bedrijf en de composietconstructies die het produceert. Holland Composites werd in 1992 opgericht door Janssen en Dwarshuis, destijds studenten aan de Technische Universiteit in Delft (TU Delft, Nederland). Ze bouwden masten van koolstofvezel voor zeilcatamarans van Hobie, een jachttender van 18 meter lang met CFRP en Nomex-honingraat in 1993, en in 1994 een zeiljacht van 30 voet met verwerking van harsinfusie. “Tegen die tijd was alles wat we bouwden gemaakt van koolstofvezel met prepreg of infusie”, herinnert Janssen zich. Hij voegt er echter aan toe, omdat het bedrijf onderhevig was aan de typische ups en downs van de maritieme markt en eenmalige projecten:"We wilden diversifiëren, maar wilden in geavanceerde composieten blijven versus FRP [wat betekent dat minder geavanceerd, meer standaard glasvezel en polyesterhars].”
Het bedrijf begon met het onderzoeken van lichtgewicht oplossingen voor wegtransport en produceerde 35 vrachtwagenopleggers met een monocoque chassis van glas/koolstofvezelcomposiet, dat het gewicht met 3.500 kilogram verminderde. "De vrachtwagens vervoerden zware ladingen, zoals aardappelen, en zouden hun maximale gewicht bereiken voordat ze hun volume zouden vullen", legt Janssen uit. Holland Composites maakte ook koeltrailers, vult hij aan:“Maar we waren iets te vroeg; de markt was nog niet klaar — bedrijven waren nog niet in staat om de jaarlijkse winst te berekenen van het vervoeren van meer vracht en de onderhoudsbesparingen van de composiettrailers versus hun hogere initiële kosten.”
Ongeveer tegelijkertijd benaderde VRR (Rotterdam, Nederland), leverancier van luchtvrachtoplossingen op maat, het bedrijf. “Ze deden werk voor Airbus, Boeing en de luchtvaartmaatschappijen”, herinnert Janssen zich. "We hebben een vederlichte container ontwikkeld met een monocoque van koolstof/aramidevezelcomposiet, die vandaag de dag nog steeds niet kan worden geëvenaard in een laag gewicht", zegt hij. Hoewel Holland Composites er een paar duizend van maakte, raakte de markt al snel verzadigd met goedkope FRP-producten.
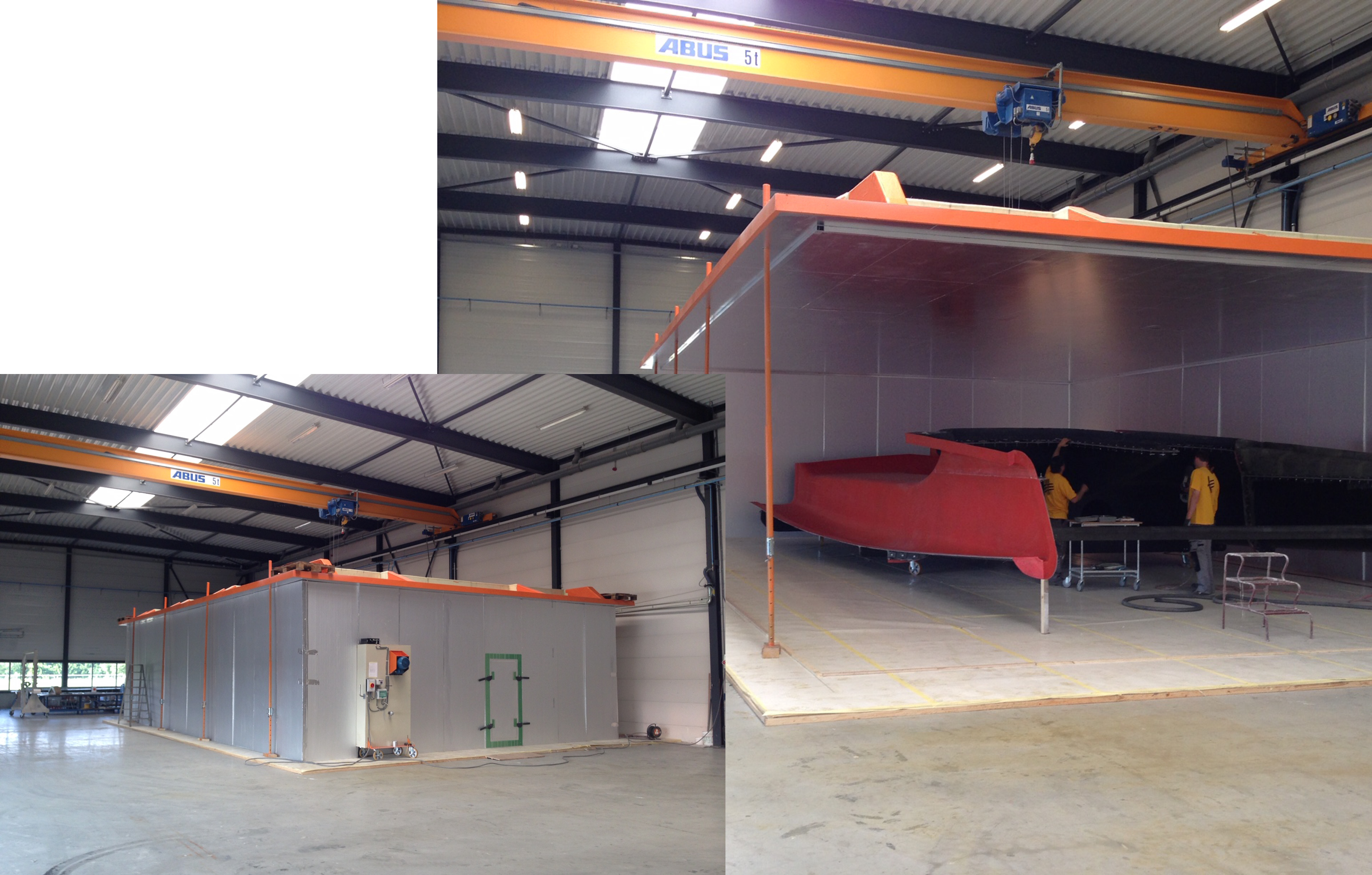
OOA-uitgeharde structuren. Grote koolstofcomposietstructuren voor het merk DNA Performance Sailing van foiling multihull zeilboten worden gehard in flexibele ovens (rechts) bestaande uit geïsoleerde panelen met verwarming en luchtcirculatie computergestuurd vanaf een buitenunit (inzet).
Marine blijft een kernkracht
In 1999 benaderde de Nederlandse Marine Holland Composites om sonardomes van massief glasvezelcomposiet voor onderzeeërs te produceren. “Deze werden traditioneel in twee helften gebouwd die aan elkaar werden gelijmd”, zegt Janssen, “maar de naad zorgt voor een verstoring in het ‘zichtveld’. We kregen de vraag om deze in één stuk te bouwen. Deze sonardomes zijn groot - 11,5 bij 3 bij 3 meter en 45 tot 110 millimeter dik - en moeilijk te infuseren, en bevatten 5.000 kilogram vinylester/epoxyhybridehars geleverd door Romar-Voss Composites (Roggel, Nederland). De afgewerkte constructie weegt 6.500 kilogram. Ze moeten stijf zijn en bestand zijn tegen dichtslaande lasten omdat ze zich aan de voorkant van de romp bevinden. “Ook de dichtheid en sonartransparantie van water moeten we afstemmen”, zegt Janssen. "We doen dit voor schepen van het type torpedobootjager voor een flink aantal zeestrijdkrachten over de hele wereld."
Aan het andere uiteinde van het gewichtsspectrum bevinden zich de DNA-performance foiling multihulls. “Onze kleine boten waren de eerste foiling catamarans in competitie”, zegt Janssen. Holland Composites produceert ook de composiet draagvleugelboten voor recordbrekende racejachten zoals MOD70's Team ARGO en Beau Geste . "We hebben een techniek in huis waarmee we zonder problemen echt zwaar belaste onderdelen kunnen maken, en een unieke eenmalige productiemethode voor deze zeer hoogwaardige folies", voegt hij eraan toe. "We werken met de beste zeilers ter wereld om het volgende niveau van foiling-prestaties te bereiken en alle foils te produceren voor de boten van de NACMA17 Olympische klasse."
Het lichtgewicht dekhuis van CFRP dat Holland Composites produceert voor service-/ondersteuningsvaartuigen voor windmolenparken van Windcat Workboats (zie "Composite dekhuizen verminderen gewicht") maakt gebruik van een met hars doordrenkte sandwichconstructie van CFRP-schuim voor stijfheid om een grote, open overspanning te bereiken zonder pilaren in de cabine. "Het monocoque dekhuis is licht genoeg om het op goede dempers te plaatsen om [het] te isoleren van motor- en golftrillingen in de romp", zegt Janssen. “Windcat staat bekend om zijn erg stille vaart, en de boten zijn geliefd bij de grote OEM's van windturbines. Al deze windparken moeten worden onderhouden, dus er is een nieuwe markt voor hogesnelheidscatamarans met een lengte van 50 tot 60 voet.”

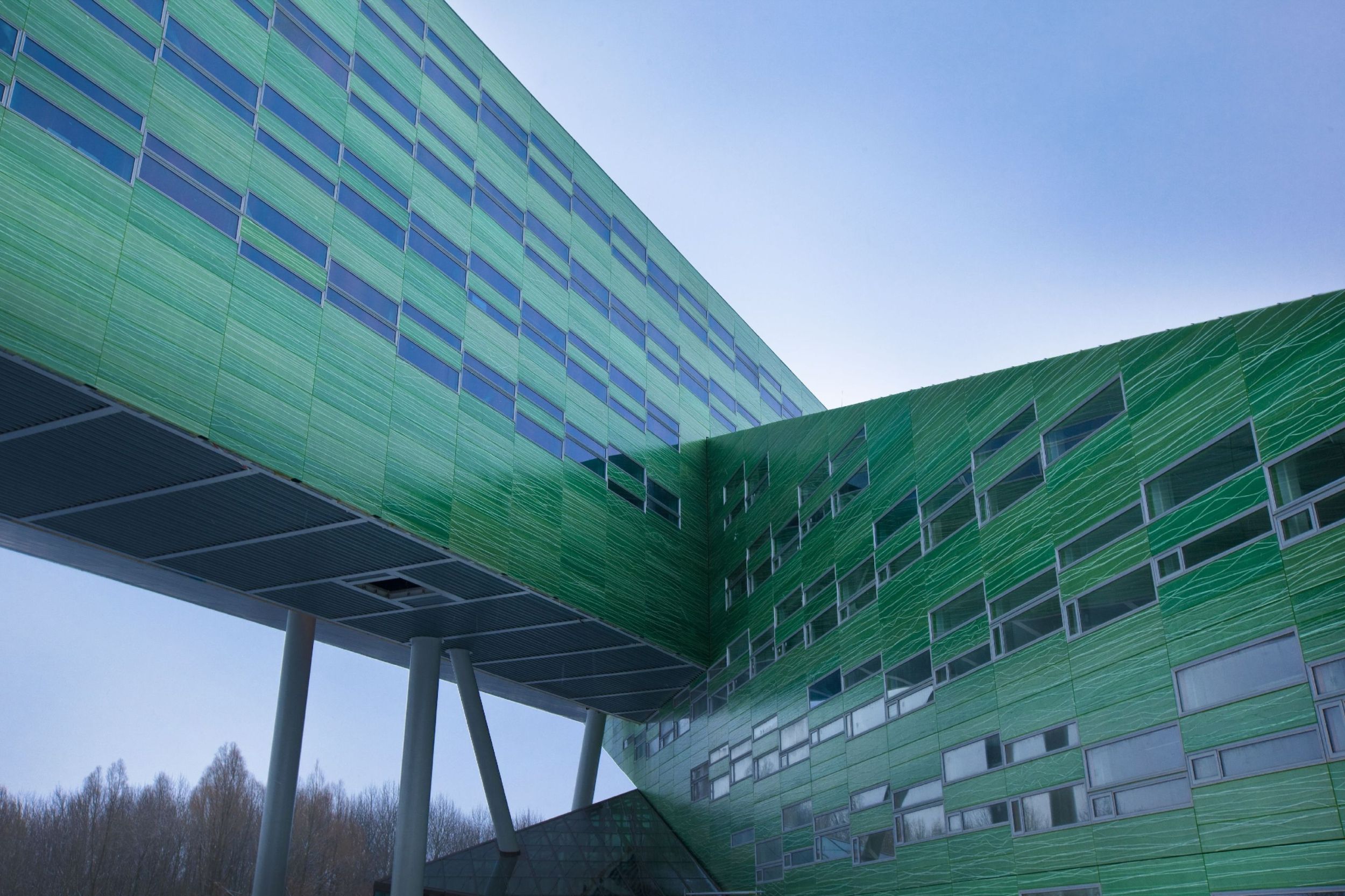
Holland Composites leverde de constructieve composietgevel voor de University of Groningen Life Wetenschappen bouwen, met behulp van hun doorschijnende RAFICLAD-paneelsysteem en grote (3,6 bij 3,3 meter) paneelafmetingen, waardoor gewichtsbesparingen en maximale thermische isolatie worden bereikt.
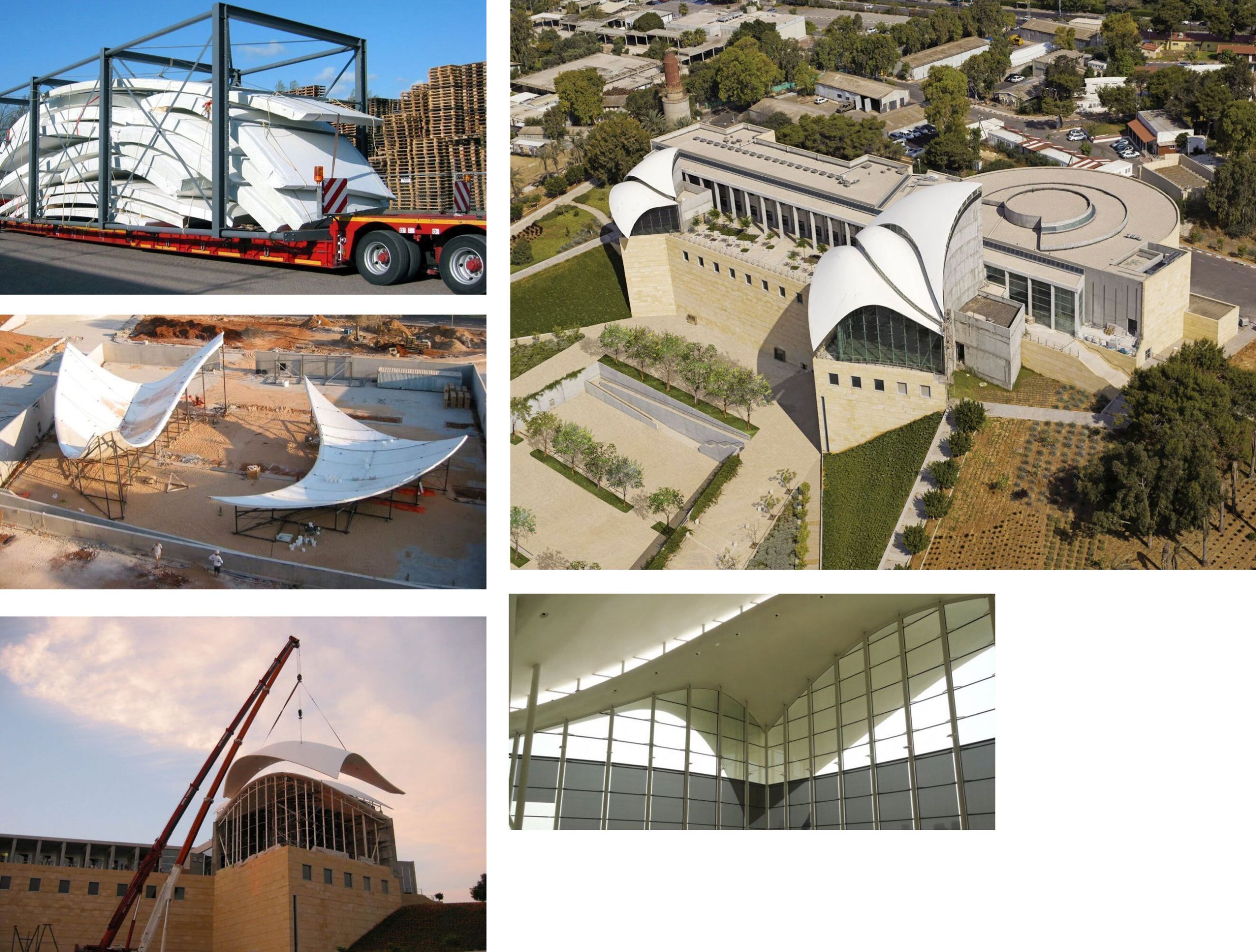
Vijfenzeventig composietsecties van 40 bij 60 meter werden naar Israël verscheept, aan elkaar gelamineerd en op hun plaats gehesen om de vleugelachtige daksecties voor het Yitzak Rabin Center in Tel Aviv te creëren.
"Alles wat we doen is structureel"
Voor het Yitzak Rabin Center (Tel Aviv, Israël) werd het bedrijf gevraagd om vleugelachtige dakconstructies te bouwen die te zwaar zouden zijn als ze van beton waren gemaakt. “We hebben weer de grootst mogelijke secties gemaakt”, zegt Janssen. Vijfenzeventig secties van 40 bij 60 meter werden met hars doordrenkt met behulp van glasvezel en vinylesterhars op epoxybasis en vervolgens verscheept naar Israël. Ter plaatse werden deze ondersteboven in mallen gelegd om ze aan elkaar te lamineren tot “vleugeldaken” met een maximale overspanning van 31 meter. Janssen merkt op dat het project structureel zeer uitdagend was. “Deze panelen zijn 200 tot 300 millimeter dik en houden de glazen gevel bij elkaar, inclusief een uitkraging van 11 meter. Het composietmateriaal is bestand tegen alle krachten, waardoor je de mogelijkheid hebt om dergelijke vrijhangende dakoverspanningen te ontwerpen.”
De Fletcher Hotel-toren is een ander dergelijk project, voltooid in 2012-2013. Het begon als een winkelcentrum naast een snelweg, maar vereiste een aanzienlijke akoestische demping in de structuur nadat de beslissing was genomen om het gebouw om te bouwen tot een high-end hotel. “Het betonskelet kon niet veel extra belasting aan, dus werden we geroepen om een lichtgewicht oplossing te bieden”, zegt Janssen. Holland Composites bedacht composietpanelen van 8,5 bij 3 meter waarop de glazen gevel kon worden bevestigd. "Het glas hangt eigenlijk aan onze panelen, wat helpt om de last te dragen", benadrukt hij. “Vervolgens bevestigden we onze panelen aan het betonskelet. Deze combinatie van het glas voor de composiet sandwichpanelen met de luchtspleet ertussen zorgt voor een enorme akoestische barrière.” Elk composietpaneel was aan één kant verfklaar voor binnenmuren en afgewerkt met UV-bestendige coatings aan de glazen buitenzijde.
“Dit was ook een heel snelle manier om bekleding te monteren op een rond gebouw”, zegt Janssen. “We hebben de complete gevel in één stap gemonteerd en een isolatie R-waarde behaald van 8, wat twee keer de beoordeling is van normale buitenmaterialen voor gebouwen.” Voortbouwend op dit idee, zegt Janssen dat hij gelooft dat energieneutraliteit van cruciaal belang is voor toekomstige bouwconstructies. "Er is niet veel energie nodig om de gebouwen te verwarmen die onze structurele composietbekleding gebruiken, dus onze aanpak is zeer efficiënt om een netto-nulvoetafdruk te bereiken. BREEAM is de Nederlandse certificering voor energie-efficiëntie en de eerste twee gebouwen die dit hebben behaald, gebruiken onze composieten.”
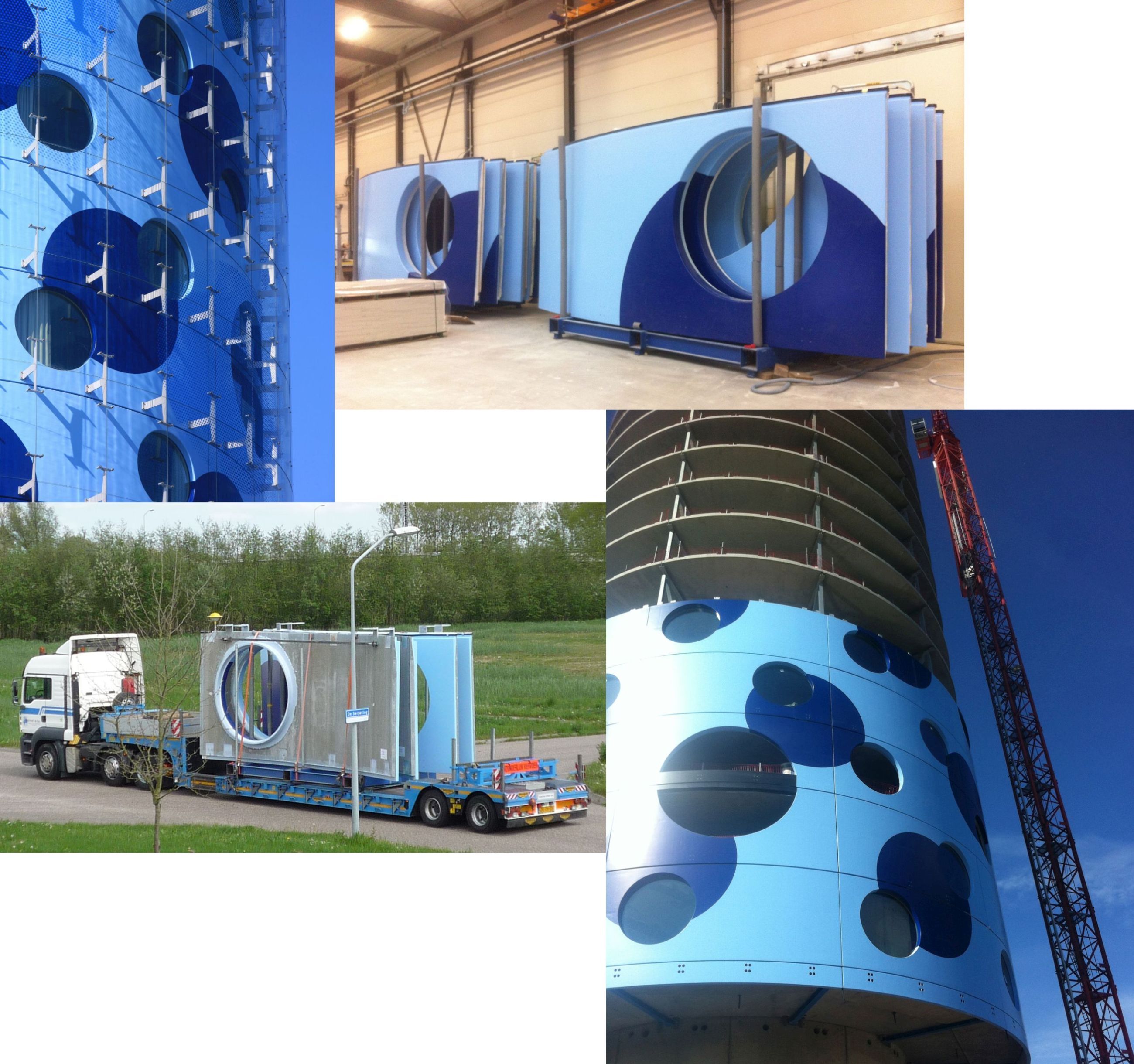
Voor het Fletcher Hotel realiseerde Holland Composites een esthetische, geluidsreducerende buitenkant door gebogen composietpanelen aan het betonskelet van het gebouw te bevestigen, waaraan de glazen gevel kon worden bevestigd zonder overmatige eigenlast toe te voegen.
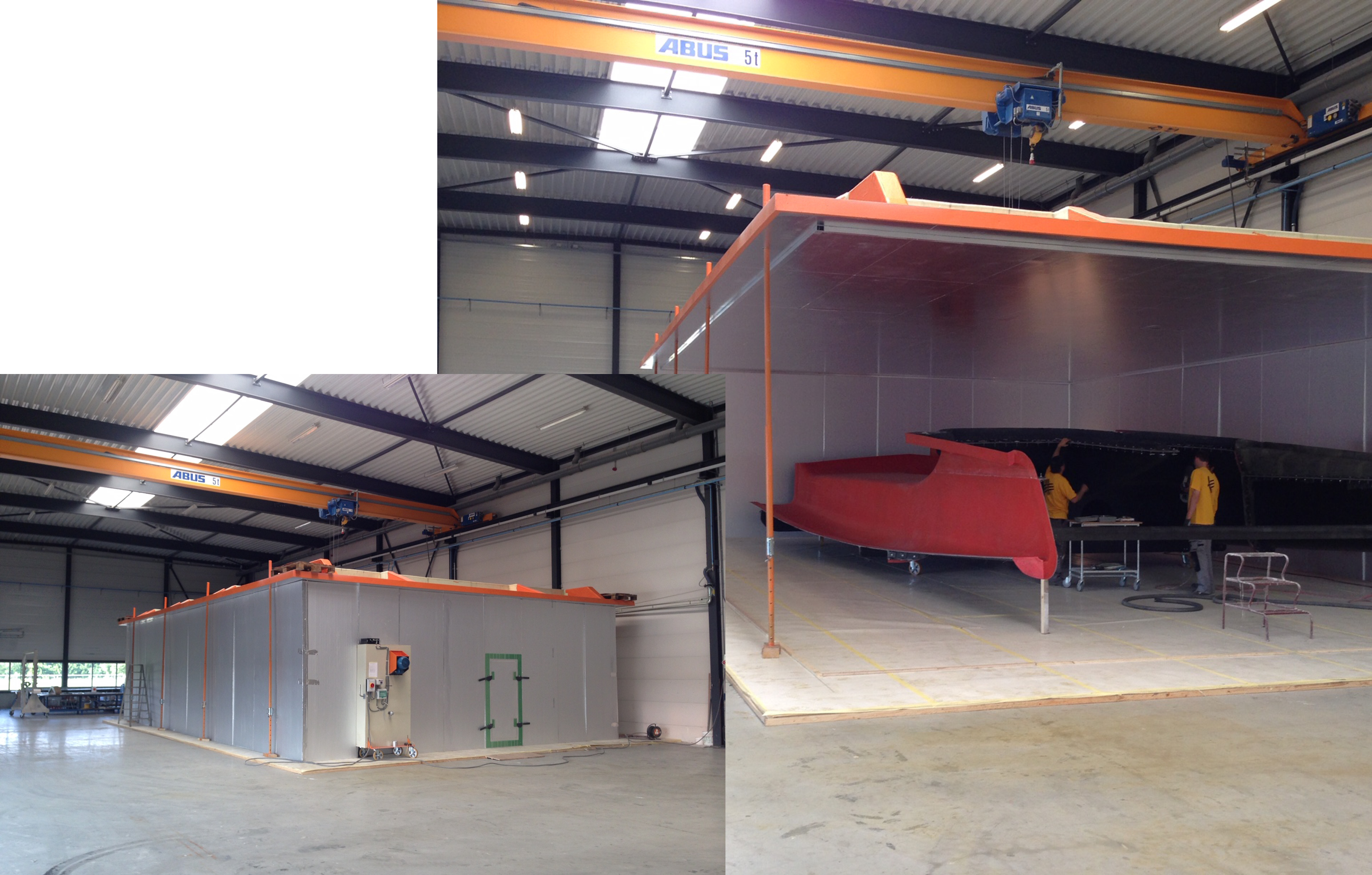
Janssen noemt het Stedelijk Museum voor hedendaagse kunst in het centrum van Amsterdam het hoogtepunt van de technische bouwprojecten van Holland Composites (zie “Groot museum, grote bouwwerken”). "Het was een extreme oefening in het beheersen van thermische uitzetting en illustreert wat we doen." Holland Composites heeft ook pionierswerk verricht met aardbevingsbestendige structurele gevels, die nu in bepaalde delen van Nederland nodig zijn, legt Janssen uit, omdat de bodem is gedestabiliseerd door hydrofracturering (fracking). Het Wiebengagebouw in Groningen heeft een aardbevingsbestendige gevel die zonder storing 30 centimeter kan verschuiven. "Typisch staal en beton kunnen dit soort bewegingen niet aan", voegt hij eraan toe.
Hoewel het een uitdaging is om de talloze vereisten te balanceren met kosten en planning bij het bouwen van constructies, merkt Janssen op dat brandwerendheid momenteel het grootste probleem is. “Verkeerde implementaties van composieten hebben de composietindustrie een slechte naam bezorgd wat dat betreft”, legt hij uit. "We gebruiken nu alleen brandwerende materialen voor deze bouwprojecten en voeren brandtesten uit volgens goedgekeurde voorschriften."
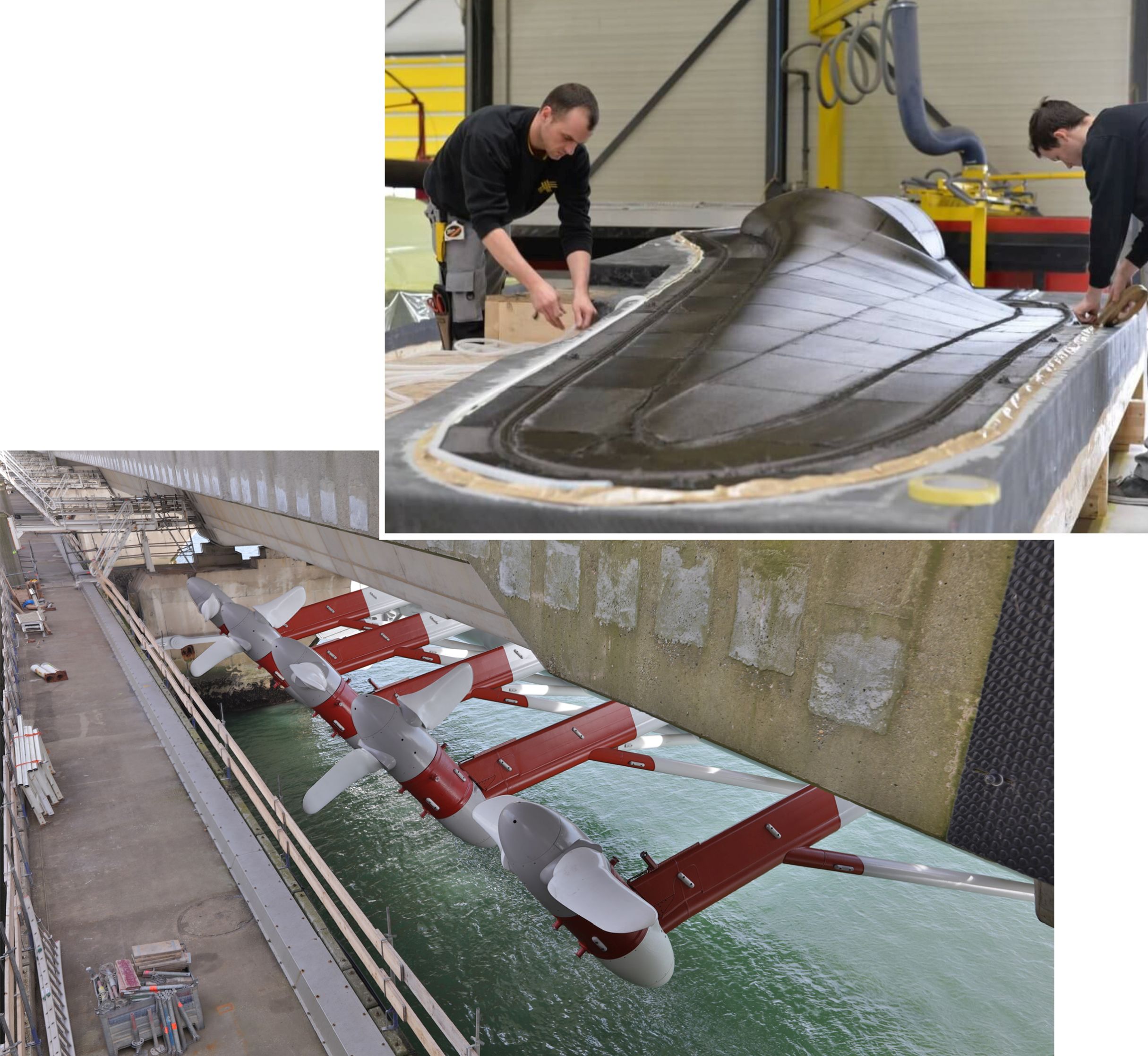
Holland Composites bouwt bladen voor getijdenturbinegeneratoren met behulp van koolstofvezel prepreg, uitgehard in een autoclaaf, om de grote belastingen op deze lage snelheid, hoog koppel constructies aan te kunnen.
Offshore en hernieuwbare energie
Holland Composites heeft ook langlopende contracten in de offshore olie- en gasindustrie. “Composieten bieden hier niet alleen een laag gewicht en corrosiebestendigheid, maar zijn ook gemakkelijk te repareren”, zegt Janssen. “Offshore-platforms en -schepen mogen geen uitvaltijd hebben. Reparatie van metalen constructies vereist echter lassen en vonken, dus de productie moet worden stopgezet vanwege brandgevaar. We kunnen composieten patchen zonder deze verstoring.” Het bedrijf heeft nieuwe klanten die om dergelijke producten vragen voor een verscheidenheid aan offshore constructies.
Het heeft ook bladen voor getijdenturbines vervaardigd. Het oogsten van getijdenenergie is nog nieuw, zegt Janssen, maar de eerste projecten zijn afgerond en de resultaten zijn indrukwekkend. “Getijdenturbines bieden een betrouwbare energiebron”, legt hij uit. "De getijden zijn er altijd, vergeleken met wind en zon, dus je kunt het vermogen betrouwbaar voorspellen, wat van cruciaal belang is voor energiebedrijven." Holland Composites gebruikt voor deze bladen geautoclaveerd carbon prepreg omdat de belasting enorm is. “De bladen bewegen met een lage snelheid maar met een hoog koppel”, zegt Janssen. "Je wilt dat de rotorsnelheid maximaal wordt omgezet in de motor om vermogen te produceren, dus de turbinefabrikanten hebben sterke maar efficiënte constructies nodig die zijn gevormd om zoveel mogelijk energie uit getijdenbewegingen te halen."
Elke turbine heeft twee bladen van 3 meter lang die 18 millimeter dik zijn. Er zijn vijf turbines per getijdengenerator. "De belasting van deze turbinebladen wordt beschreven als gelijk aan een sleepboot van 13.600 pk die op volle kracht vooruit gaat", zegt Janssen, "maar de klant heeft ook bladen nodig die stijf, lichtgewicht en onderhoudsarm zijn met een goede weerstand tegen vermoeiing voor duurzaamheid. Staal zou te zwaar zijn geweest, waardoor de generatoren minder efficiënt zouden zijn.” Holland Composites maakt alleen de bladen; stroomlijnkappen, neuskegel en niet-structurele bekleding zijn gemaakt door FRP-fabrikanten.
Toekomstgerichte faciliteit
De tour begint in de lay-upruimte, met een grote lay-uptafel, onderdelen voor de DNA-prestatiezeilboten en een verscheidenheid aan CFRP-folies die worden klaargemaakt voor installatie. Het plafond is hier laag vanwege een entresol voor materiaalopslag. Dit komt uit op een productievloer met een hoog plafond, met een Zünd (Altstätten, Zwitserland) geautomatiseerde snijmachine net buiten het opstelgebied. De snijplotter heeft een snijbereik van 5,7 bij 2,8 bij 0,3 meter voor het verwerken van prepreg, droge vezels en schuimmaterialen tot 25 millimeter dik.
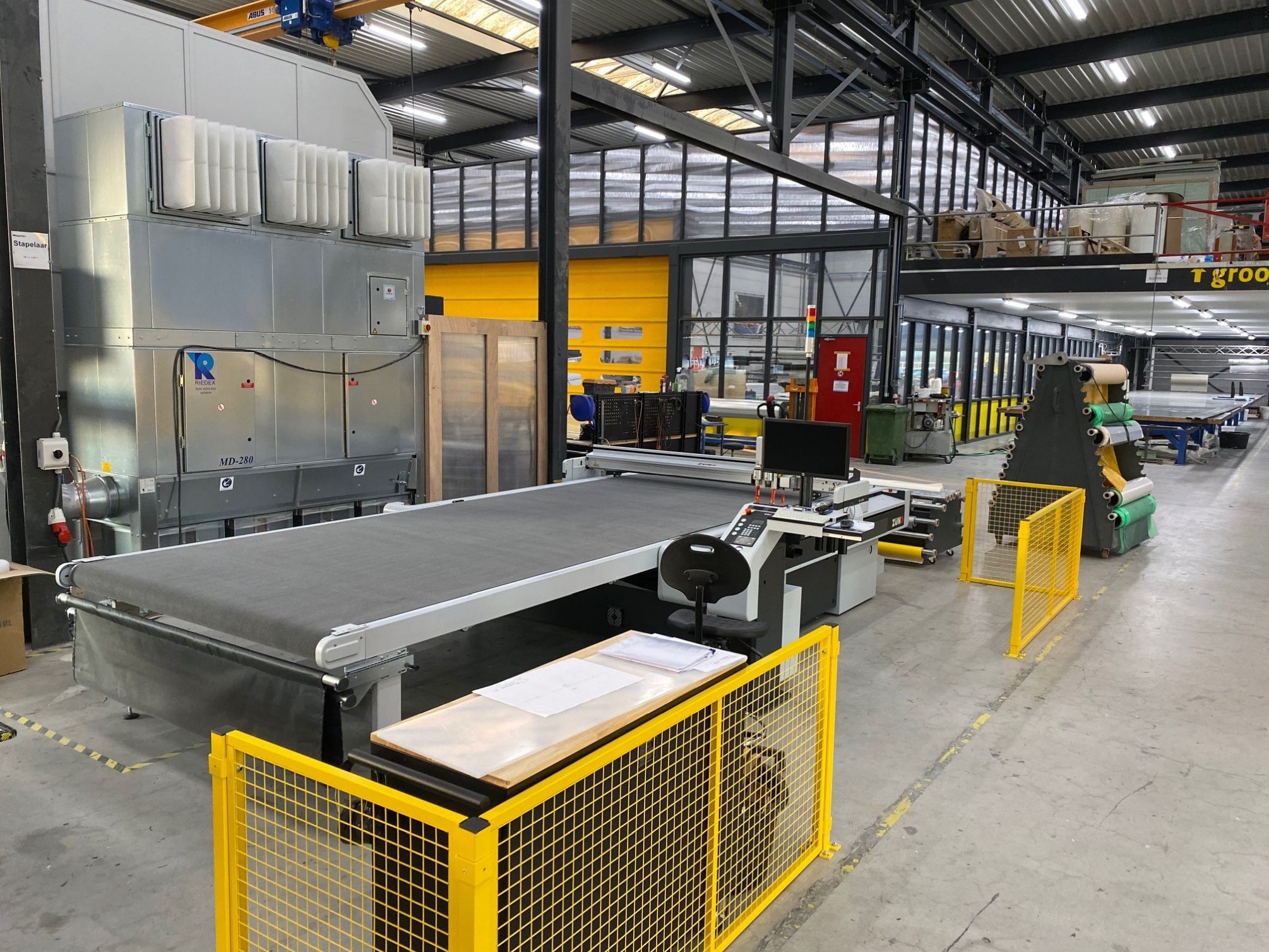
De Zünd-automaat op de voorgrond levert snijverstevigingen en schuim aan de opstelruimte, die rechts achterin te zien is, met de mezzanine voor materiaalopslag erboven. Het omsloten gereedschapsgebied ligt achter de gele roldeur, hier gezien achter de zijkant van het CMS bewerkingscentrum, dat naast de Zünd snijtafel staat.
Als we ons omdraaien van de Zünd-frees, lopen we naar een met glas omsloten gereedschapsruimte die grenst aan het opstelgebied. Bij binnenkomst via een gele oproldeur zijn er meerdere gereedschappen in bewerking en worden onderdelen onder vacuümzakken uitgehard. “We maken onze eigen mallen”, zegt Janssen. "Voor CFRP-onderdelen gebruiken we CFRP of aluminium voor het gereedschap, evenals ventilatiegaten voor luchtcirculatie in het gereedschap, wat helpt om een gelijkmatige uitharding over het onderdeel te garanderen."
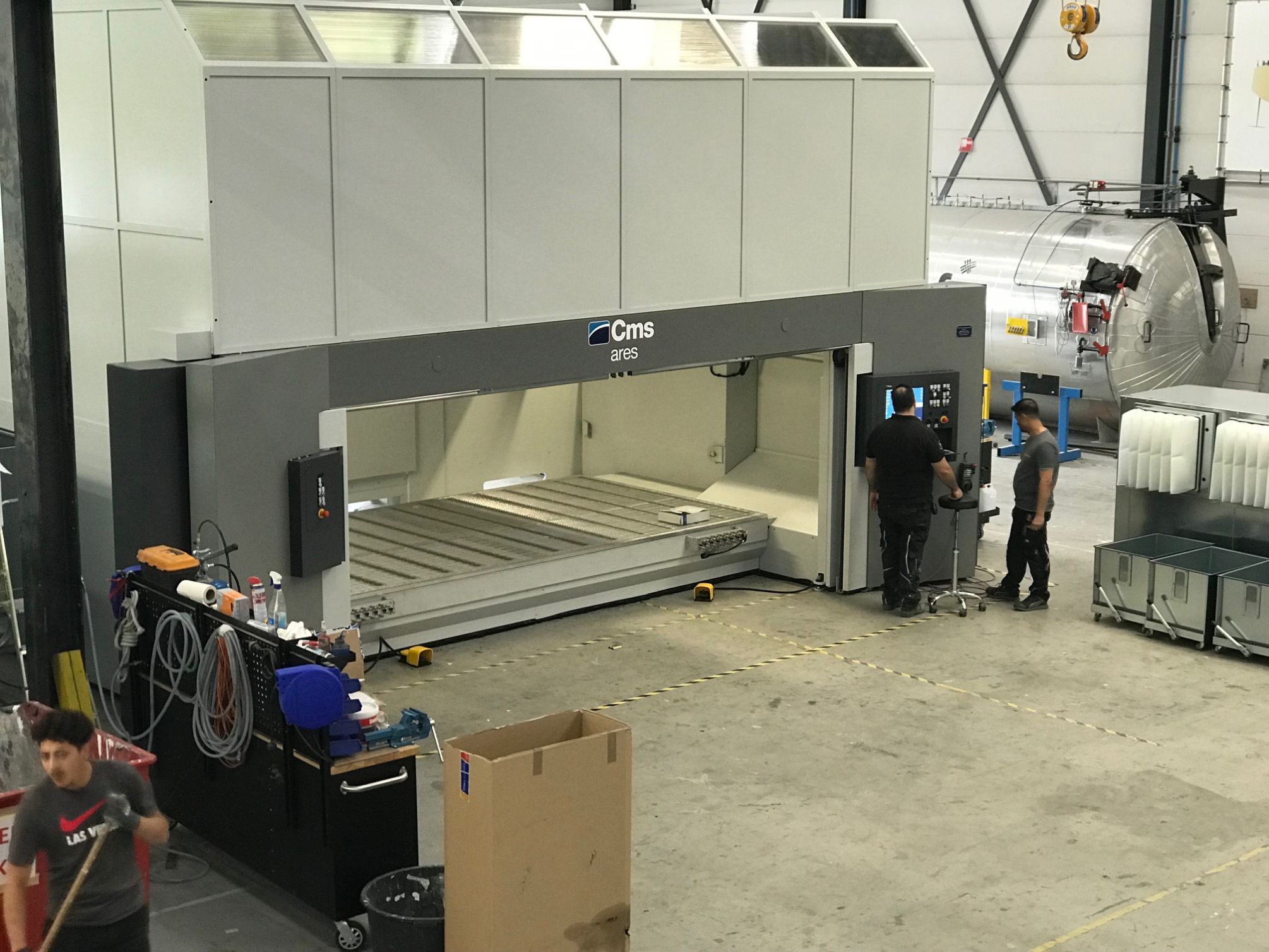
Het CMS-bewerkingscentrum bevindt zich tussen de snijtafel aan de linkerkant (uit het zicht) en de autoclaaf (uiterst rechts, tegen de muur).
Als we de gereedschapsruimte weer verlaten, passeren we het 5-bij-2-bij-1,8 meter 5-assige CNC-freescentrum (CMS SpA, Zogno, Italië) en zien we de autoclaaf van 6,5 bij 2,2 meter (Tankbouw Rootselaar, Nijkerk, Nederland). “We genezen doorgaans bij 125° C met een druk van 6 bar”, merkt Janssen op.
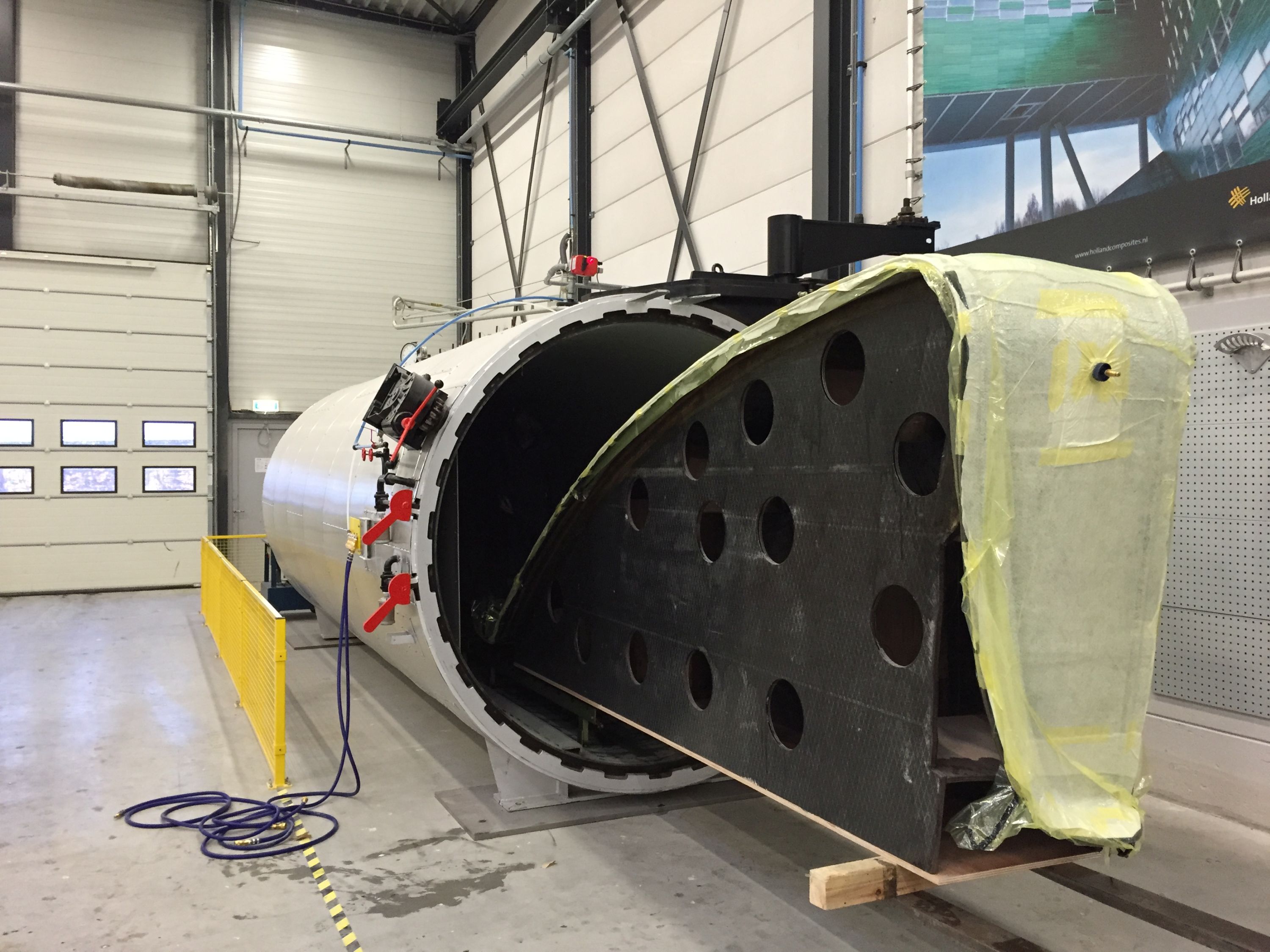
De autoclaaf is hieronder ook te zien met een CFRP-gereedschap (let op gaten voor luchtventilatie) en grote CFRP-folie die wordt uitgehard onder een vacuümzak voor een prestatiegerichte meerrompszeilboot.
De muur naast de autoclaaf snijdt het productiegebied in twee helften en loopt over de lengte van het gebouw langs de gereedschapsruimte. We draaien ons om en gaan door een deur naar de tweede helft van de Holland Composites-faciliteit, die een waterstraalsnijmachine bevat (8-bij-2-bij-0,5 meter snijbereik), verschillende ovens met afmetingen tot 15 bij 10 -bij-3,5 meter, en de 19-bij-12-bij-3,5 meter spuitcabine van het bedrijf. "Momenteel produceren we grote panelen voor een project in Qatar en een reeks CFRP dekhuizen voor de Windcat-boten", zegt Janssen.
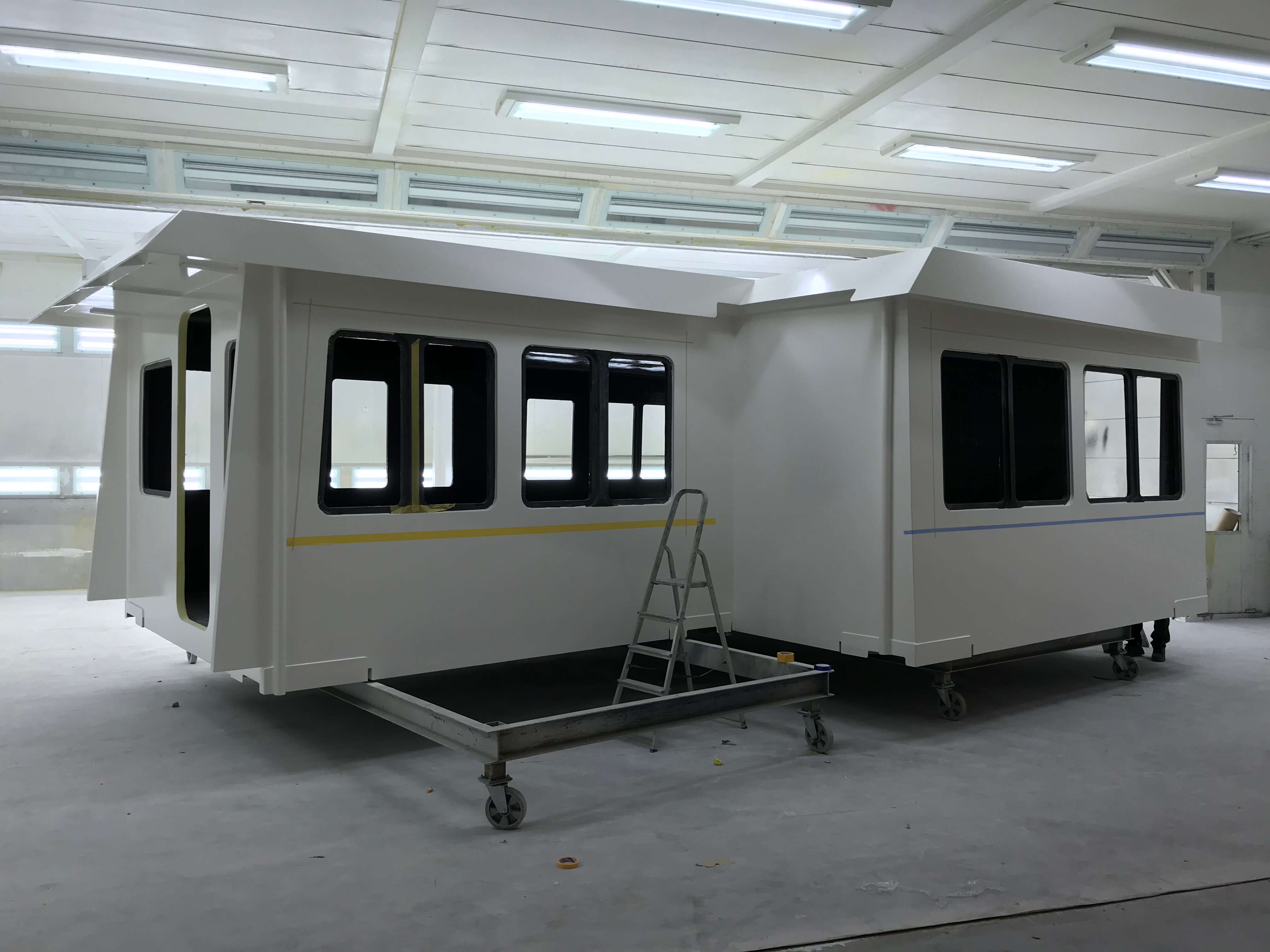
De CFRP-dekhuizen die Holland Composites produceert voor catamarans van Windcat Workboats worden geverfd in de spuitcabine van 19 bij 12 bij 3,5 meter van het bedrijf.
De nieuwste installatie van Holland Composites is een Massivit 3D (Lod, Israel) 1800 Pro printer met een bouwvolume van 145 bij 111 bij 180 centimeter. “We zijn partners die innoveren in het 3D-printen van mallen met behulp van drie printkoppen, waarvan er twee de huid van een sandwich printen en de middelste nozzle de infill- of roosterstructuur ertussen print”, legt Janssen uit. “We zullen in toekomstige ontwikkelingen vezelversterkt materiaal gebruiken, maar voorlopig kunnen we nauwkeurige gereedschappen printen met minimaal freeswerk. We gebruiken veel minder materiaal en zien zeer snelle matrijsproductietijden. We hebben nu een complete procesketen, met de mogelijkheid om in korte tijd van ontwerp en mallen naar geverfde onderdelen te gaan.”
Hij merkt op dat het bedrijf nog steeds onderzoekt hoe het meer gebruik kan maken van automatisering om zijn producten verder te ontwikkelen, maar zonder de kosten op te drijven. “Het komt neer op vindingrijkheid. We voelen ons aangetrokken tot zeer complexe problemen die maar weinig anderen durven aan te pakken, maar als botenbouwers hebben we altijd heel creatief moeten zijn met beperkte middelen. Voor wat we doen in composieten, zien we veel kansen in de toekomst.”
Hars
- Fabrikanten bezoeken United Safety for Plant Tour, Best Practice Discussion
- CompositesWorld SourceBook 2022
- Problemen oplossen met thermovormen van thermoplastische composieten
- De evolutie van additieve composieten
- Thermoplastische composieten:structurele bumperbeugel
- Composieten als versterkingen voor het lichaam
- CAMX 2020-voorbeeld
- Nederland presenteert de expertise op het gebied van composieten op JEC World 2019
- TPAC en TPRC ontwikkelen recyclingproces voor thermoplastische composieten
- Thermoplastische composieten lassen
- Hoogwaardige composieten in Israël