Fraunhofer IPT ontwikkelt thermoplastische composieten in waterstofopslag, motorbladen en meer
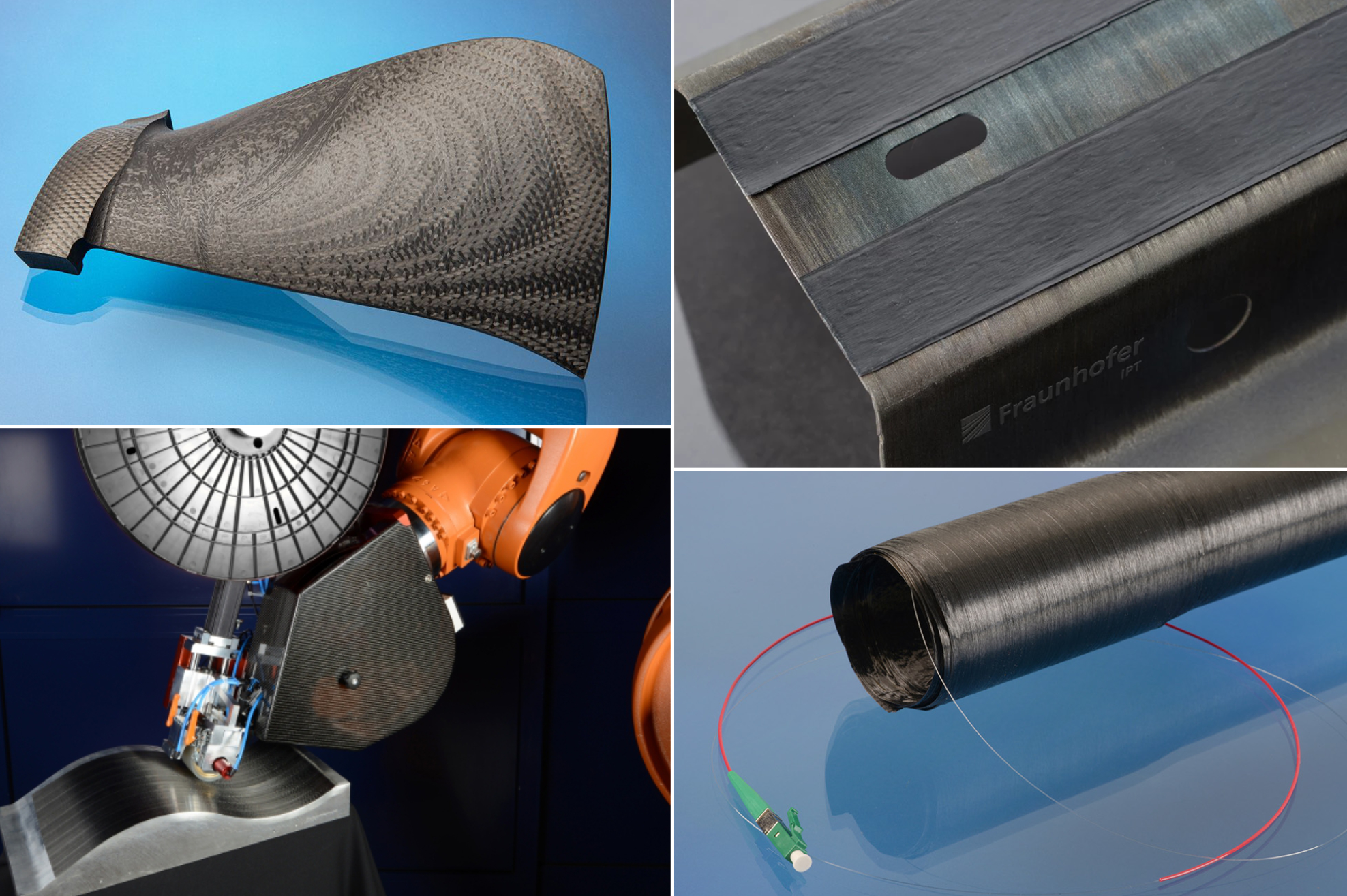
De ontwikkeling van Fraunhofer IPT omvat (met de klok mee van linksboven) ventilatorbladen van thermoplastische composieten voor vliegtuigmotoren, hybride composiet-metaalstructuren met behulp van laserstructurering en AFP, structurele gezondheidsmonitoring (SHM) van composieten en verwerkingssystemen voor thermoplastische composiettape, zoals de PrePro 2D- en PrePro3D-systemen gecommercialiseerd door Conbility. Fotocredits:Fraunhofer IPT
In december 2020 publiceerde ik een artikel over hoe het Fraunhofer Instituut voor Productietechnologie (IPT, Aken, Duitsland) volledig geautomatiseerde tape-legging en vorming ontwikkelt voor thermoplastische koolstofvezelversterkte polymeer (CFRP) ventilatorbladen voor vliegtuigmotoren. In-situ consolidatie (ISC) van thermoplastische composiettape, zo blijkt, is een onderwerp dat Fraunhofer IPT goed kent, aangezien deze technologie in het begin samen met ISC-pioniers Accudyne Systems Inc. (Newark, Del., VS) en Automated heeft geleid. Dynamics, nu Trelleborg Sealing Solutions Albany (TSS Albany, Niksayuna, NY, VS). [Voor meer informatie over deze ISC-pioniers, zie "Consolidering van thermoplastische aerostructuren op hun plaats, deel 1 en deel 2".] "De IPT is sinds 1988 actief in laser-assisted tape winding (LATW) en het blijft een van onze belangrijkste onderwerpen ”, legt Dr. Henning Janssen uit, hoofdingenieur en afdelingshoofd voor vezelversterkte kunststoffen en lasersysteemtechnologie bij Fraunhofer IPT. Hij merkt op dat de LATW-technologie veel is veranderd, vooral in de afgelopen 10-15 jaar. Deze blog geeft meer details over Fraunhofer IPT's ontwikkeling van LATW en van thermoplastische composieten in het algemeen, evenals waar het instituut de technologie in de toekomst ziet leiden.
Evolutie in het opwinden van lasertape
“Toen we 30 jaar geleden begonnen, was lasertechnologie nog niet klaar voor de snelle verwerking van thermoplastische composieten”, zegt Janssen. “Je kunt je voorstellen dat je, zeker aan de besturingskant, alleen een analoge camera had. Nu hebben we veel betere technologie. Toen we bijvoorbeeld in 2008 een compacte laseropwindkop ontwikkelden, wat resulteerde in de oprichting van AFPT Duitsland (Dörth, Duitsland), moesten we een 16-pixel x 16-pixel camera gebruiken, die een beeldsnelheid bood van slechts acht beelden per seconde. Nu hebben we gemakkelijk 640 x 480 pixels en verwerken we 50 frames of meer per seconde.” Hij legt uit dat dit belangrijk is, "omdat met de laserbandwikkeling die we hebben ontwikkeld, een van de belangrijkste voordelen is dat je kunt naar het proces en verander ook de verwerkingskracht binnen milliseconden. Dat geeft je bijvoorbeeld een goed voordeel als je om complexe geometrieën heen gaat, zoals de koepel van drukvaten, waar de wikkelsnelheid vertraagt, en je het laserverwarmingsvermogen moet verlagen. U moet dan opnieuw afstellen terwijl de wikkeling weer op snelheid komt langs de tankcilinder. Dit was 15 jaar geleden niet mogelijk omdat de laser-, controlesysteem- en warmtebeeldtechnologieën niet gereed waren of te duur waren en ook niet zo krachtig als wat we nu hebben.
Janssen vervolgt:“Er is dus veel ontwikkeld aan de digitale kant. Nu leveren we bijvoorbeeld zoiets als een digitale tweeling, waarmee je al je sensorinformatie op het drukvat in kaart kunt brengen, zodat je het onderdeel zoals gefabriceerd kunt vergelijken met het digitale ontwerp om de kwaliteit van het onderdeel te beoordelen en de prestaties te voorspellen. Het gebruik van virtuele processensoren en modellen stelt ons ook in staat om de laminaatsterkte te voorspellen zoals gedefinieerd door de verwerkingsgeschiedenis.” Dit is belangrijk omdat LATW met thermoplastische tape gebruik maakt van snelle verwarming en koeling waarbij de materiaal- en onderdeeleigenschappen worden bepaald tijdens het wikkelproces zelf, vanwege het ontbreken van een thermische nabewerkingsstap, merkt hij op. Het is daarom van cruciaal belang om de mogelijkheid te hebben voor snelle procescontrole.
Ook op het gebied van materialen zijn er ontwikkelingen geweest, zegt Janssen. "Twintig jaar geleden was er een beperkte hoeveelheid thermoplastische composiettape-materialen beschikbaar, zoals APC-2 van Cytec, nu Solvay (Alpharetta, Ga., V.S.)", legt hij uit. “Maar nu zijn veel meer materialen geschikt voor industriële toepassingen, en je hebt ook veel basismaterialen zoals polypropyleen (PP) versterkt met koolstofvezel en ook met glasvezel, evenals polyamide zes (PA6) bijvoorbeeld, dat wordt veel gebruikt in de auto-industrie. Er zijn nu ook toepassingen voor LATW die meer gericht zijn op massaproductie. Er is bijvoorbeeld een duw in de richting van retentiehulzen en andere onderdelen in elektromotoren. Dit zijn eenvoudige ringen of buizen van thermoplastisch composiet, maar in volumes van 10.000 tot 50.000 per jaar.”
ambliFIBRE, pijpen voor olie en gas
Een deel van de digitale besturing in LATW die Janssen hierboven beschrijft, is ontwikkeld in het project ambliFIBRE (2015-2018). "Er waren veel partners in dat project", zegt hij, "maar een daarvan was Baker Hughes (Newcastle, Engeland en Houston, Texas, VS) en we gebruikten onze LATW-apparatuur voor hun niet-metalen buizen." Merk op dat kort nadat ambliFIBRE in 2018 eindigde, Baker Hughes zijn joint venture met Saudi Aramco (Riyadh, Saoedi-Arabië) aankondigde om het gebruik van niet-metalen buizen uit te breiden, inclusief het mogelijke gebruik van met koolstofvezel versterkt plastic (CFRP).
Baker Hughes streeft er nu naar om de introductie van niet-metalen materialen in de energiesector te versnellen, en er zijn ook andere bedrijven die lasertechnologie voor pijpleidingen gebruiken, zoals Magma (Portsmouth, VK). (Zie “Thermoplastische leiding in opkomst in de diepzee” en “Magma Global levert hogedruk composiet stijgleiding…).
"Het is ook vrij gebruikelijk om lasertape-wikkeling te gebruiken voor stijgleidingen en stroomlijnen van thermoplastisch composiet", zegt Janssen. “Al is dat in andere branches nog niet algemeen bekend.” Hij voegt eraan toe dat veel van de recente aandacht voor LATW is geweest voor waterstofopslagtanks, maar de technologie heeft al een veel bredere toepassing.
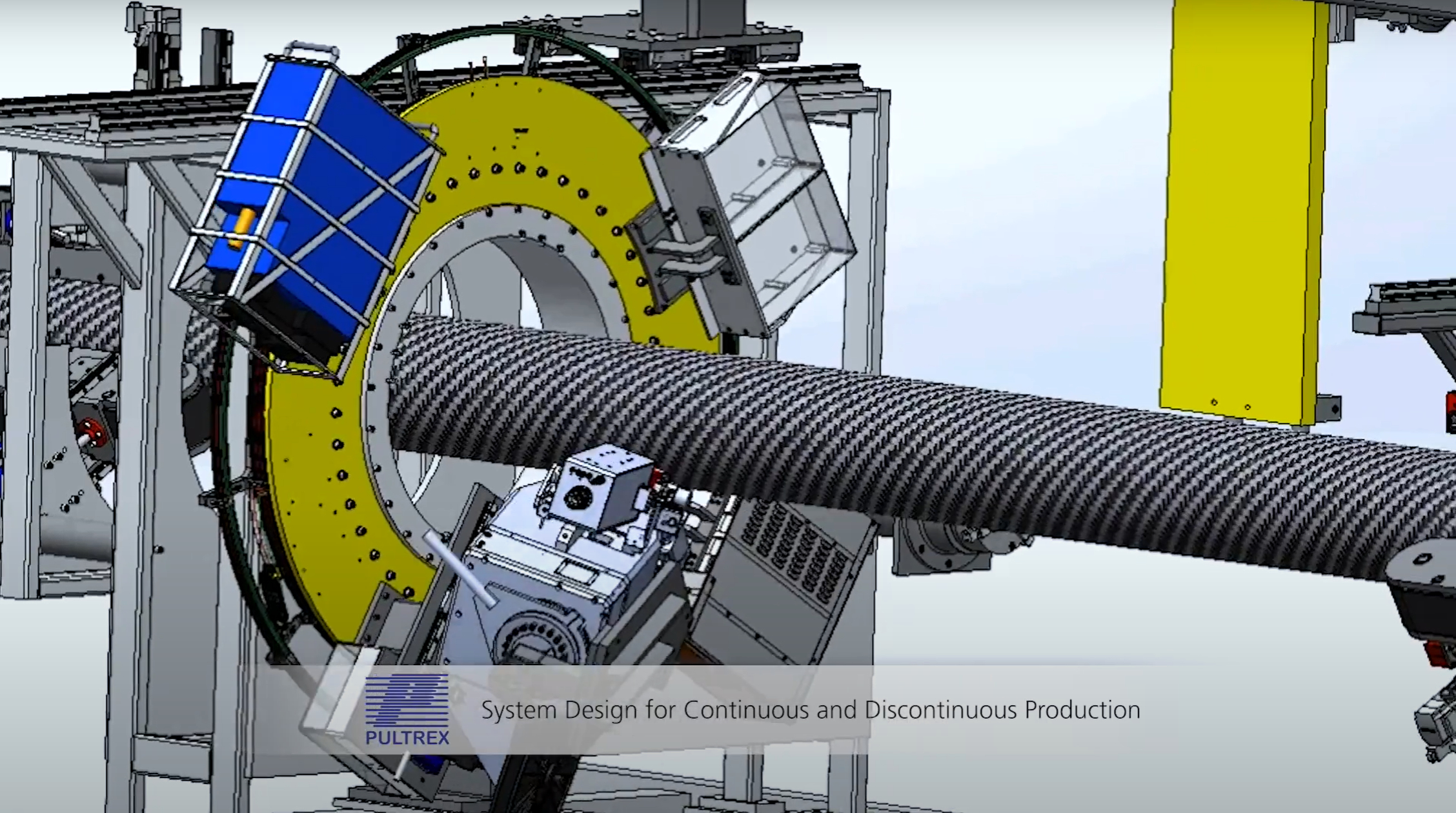
Binnen het ambliFIBRE-project ontwikkelde Fraunhofer IPT digitale procesbesturingsmodellen voor discontinue (bijv. tanks) en continue bandwikkeling, bijvoorbeeld om leidingen van meerdere kilometers lang te produceren. Photo Credit:Fraunhofer IPT-video voor ambliFIBRE-project
“En wat wij bij Fraunhofer IPT bieden voor deze toepassingen is essentieel”, zegt Janssen. “Het is duidelijk dat we hier in ons instituut geen volledige productielijn voor continue pijpproductie hebben, maar wat we onze klanten wel bieden, is materiaaltesten en productkwalificatie. Er is bijvoorbeeld de testpiramide, gebaseerd op DNV-GL F114, beginnend met kwalificatie en testen van het polymeer en de vezels, en vervolgens opschalen naar de microstructuur van composietlaminaat of mesostructuur. We testen dus veel op couponniveau en schalen vervolgens op naar kleinere pijpen en representatieve pijpen, bijvoorbeeld omdat wikkelen je andere eigenschappen geeft dan persen of automatisch tape leggen (ATL).”
Hij merkt ook op:"Omdat je verschillende spanningen in je materiaal hebt, worden veel van deze composietmaterialen getest in kleinere buizen, bijvoorbeeld 2-3 inch tot enkele meters lang. Dus doen we deze tests en dan passen we ons procesbegrip toe voor de werkelijke lengte van het onderdeel, bijvoorbeeld 2-3 kilometer. En dat is heel interessant, omdat de verwerkingstijd bij die lengte een paar dagen kan bedragen, en je moet rekening houden met krimp en met andere factoren, zoals veranderingen in de temperatuur van de omgevingslucht, die een behoorlijke impact kunnen hebben.”
LATW in waterstofopslagtanks
Janssen zegt dat Fraunhofer IPT al sinds 2000 samenwerkt met olie- en gasbedrijven. "En toen, acht jaar geleden, kwamen we erachter dat dit bijna dezelfde technologie is die je nodig hebt voor waterstoftanks", herinnert hij zich. “En nu hebben we een groot initiatief voor waterstofproductie hier bij IPT en ook voor koolstofvezelcomposieten in brandstofcellen. We zetten een faciliteit van 80 miljoen euro op voor geautomatiseerde productie van brandstofcellen en investeren ook in een nieuwe, vrij grote wikkelfaciliteit zodat we onderdelen kunnen produceren tot 7 meter lang en 2,5 meter in diameter, die we ook zullen gebruiken voor grote drukvaten.”
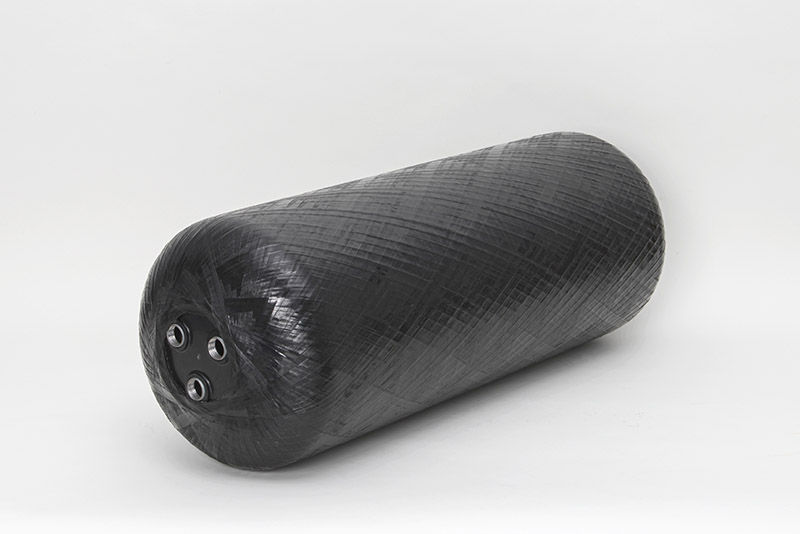
LATW met thermoplastische composiettapes is nog niet state-of-the-art voor de productie van drukvaten, zegt Janssen, “omdat de chemie van de thermoplasten, evenals de verwerking en duurzaamheid ervan nog allemaal worden onderzocht. Maar onze sterke overtuiging is dat de lage permeabiliteit, taaiheid en recycleerbaarheid die thermoplasten bieden belangrijk is.” Hij ziet ook mogelijkheden voor thermoplasten in type V-drukvaten, die volledig van composiet zijn maar geen afzonderlijke thermoplastische voering gebruiken. "Deze kunnen een toekomstige oplossing bieden voor sommige mobiele waterstofopslagtoepassingen, zoals brandstofcel-elektrische vrachtwagens."
“We zien ook dat conventionele thermoset filamentwikkeling is beperkt wat betreft minimale wikkelhoeken”, zegt Janssen. “Je moet bijvoorbeeld rond de koepels gaan in spiraalvormige lagen met niet veel minder dan een vezelhoek van 10°. Je kunt dus geen 0°-versterking in een conventionele filamentgewikkelde tank plaatsen.” Hij stelt echter:“in de klassieke LATW wordt de binnenkomende thermoplastische prepreg direct aan het substraat gelast, zodat je alle kanten op kunt gaan, wat je veel meer ontwerpvrijheid geeft. We lopen momenteel projecten met partners uit de auto-industrie om thermoplastische drukvaten voor waterstofopslag te ontwikkelen die veilig, energiezuinig en gemakkelijk te recyclen zijn.”
Thermoplastische composiet ventilatorbladen
Fraunhofer IPT heeft een zeer sterke achtergrond in turbomachines, zegt Janssen. “We hebben hier in Aken de International Center for Turbomachinery Manufacturing, of ICTM, een pre-competitieve gemeenschap waar we samenwerken met de motorfabrikanten en hun leveranciers in pre-competitieve R&D-projecten om productietechnologie te ontwikkelen en te verbeteren.”
Hij merkt op dat de afgelopen 20 jaar de focus vooral lag op het bewerken van titanium of nikkelgebaseerde legeringen voor geavanceerde producten van de compressiesectie en turbines, zoals de geïntegreerde schijf (blisk). Terwijl in het koude gedeelte onderdelen van composietmaterialen - zoals koolstofvezelcomposiet ventilatorbladen - werden in de jaren negentig door GE ontwikkeld en zijn nu in gebruik in de GE90 en GEnx. "Nu worden keramische matrixcomposieten (CMC) echter gezien als materialen van de volgende generatie voor het hete gedeelte van straalmotoren", zegt Janssen, "waardoor hogere temperaturen bij minder gewicht mogelijk worden voor meer efficiëntie."
“Het vervaardigen van onderdelen uit composieten in vergelijking met metaal is heel anders”, vervolgt hij. “In metaal begin je met een massa materiaal en leidt het onderdeel af door subtractieve bewerking, meestal machinale bewerking, zodat het ontwerp niet zo afhankelijk is van de fabricage. Bij composieten is het precies andersom, daar is altijd een soort generatief proces voor nodig. Dus hebben we besloten dat we nieuwe strategieën voor ventilatorbladen zullen aanpakken vanuit een productieperspectief.”
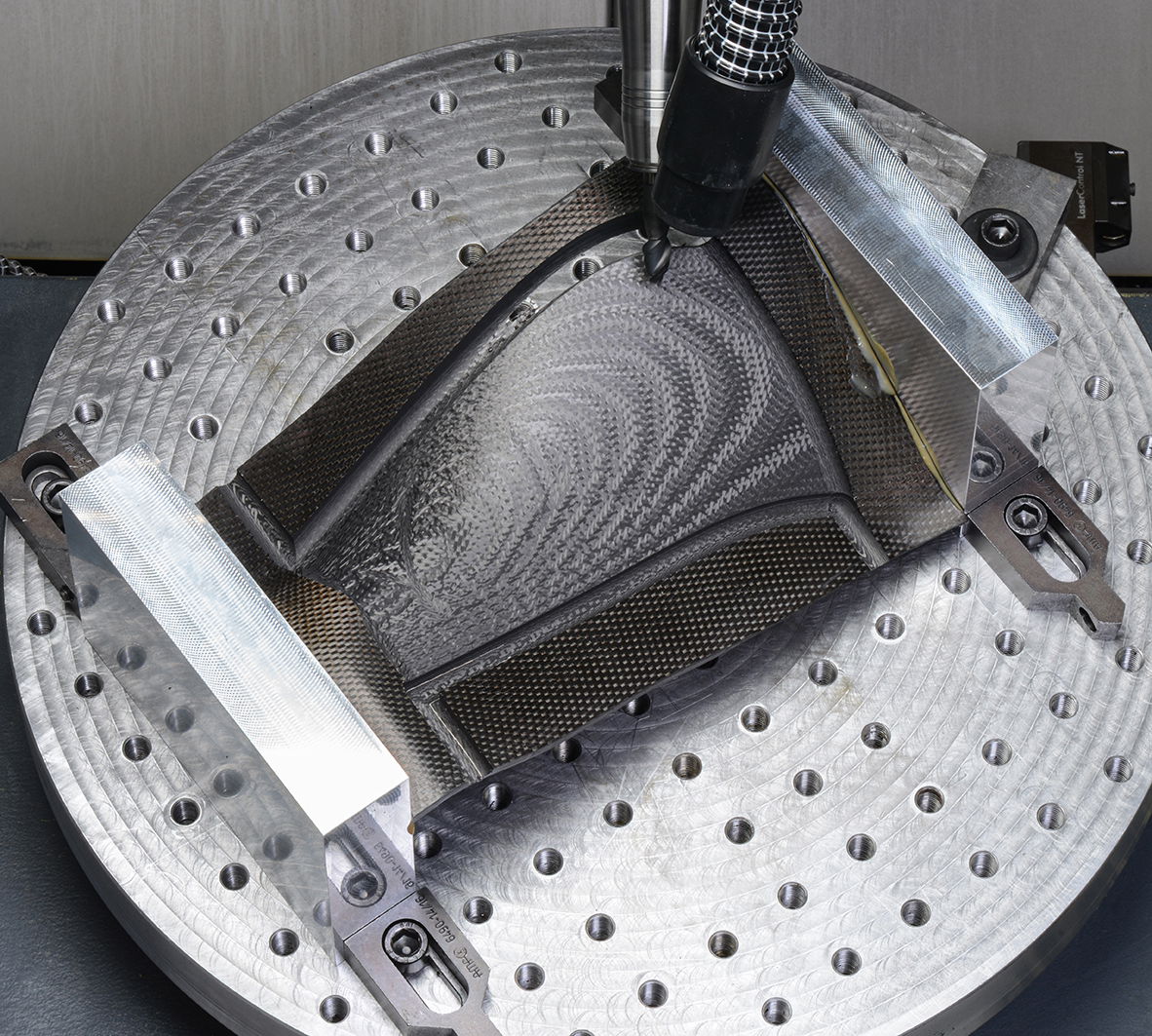
Hij wijst ook op de gemeenschappelijke onderneming Clean Sky 2, waarin Fraunhofer de Eco-Design-activiteiten leidt. Fraunhofer IPT richt zich op het eco-ontwerp voor motoren, inclusief levenscyclusanalyse en evaluatie van de milieu-impact. “Daarom zijn we gaan kijken naar thermoplastische composieten”, legt hij uit. "Tot nu toe bevinden we ons op een zeer lage TRL [technologiegereedheidsniveau]. Voorlopig gaat de ontwikkeling over het vervaardigen en uitproberen van verschillende procesroutes, zoals bijna netvorm lay-up en een beetje thermovormen - wat meer een kalibratiestap is - en dan de afwerking in termen van bewerking. Er staat ons dus nog heel wat werk te wachten.”
Ondertussen breidt Fraunhofer IPT zijn expertise in het bewerken van metalen onderdelen van vliegtuigmotoren uit naar composieten, met behulp van zijn digitale technologie om de bewerkingsparameters op elk blad te bewaken en te beoordelen. Maar is het niet het doel van composieten om van dergelijke subtractieve productie over te stappen naar meer additieve productie voor minder afval? “Ja, maar voor sommige procesroutes is machinale bewerking vereist om te voldoen aan maattoleranties”, zegt Janssen. "Waar we nu aan werken, is bijna net zo goed."
Hij wijst erop dat het ontwerp dat momenteel wordt ontwikkeld een 0,75-inch dik thermoplastisch laminaat is aan de wortel en slechts 2 millimeter dik aan de punt. “En dan zijn er nog verschillende ontwerpstrategieën, die we samen met de ontwerpingenieurs bespreken. Heeft u ook een autoclaaf of een perstrap voor dat soort zeer zwaar belaste onderdelen? Dit zal ook een rol spelen met betrekking tot de interne spanningen, omdat we weten dat dit blad een beetje draait tijdens het draaien. En natuurlijk is vogelaanvaring een belangrijk punt.” Voor dat laatste ziet Janssen de verhoogde taaiheid van thermoplasten als een enabler, en hij wijst erop dat PPS-composieten (polyfenyleensulfide) juist om deze reden worden gebruikt in vleugelvoorranden.
Toekomstige toepassingen voor thermoplastische composieten
Ik vroeg naar de mogelijkheid om thermoplastische composieten te gebruiken in motorgondels , die misschien een oplossing zou kunnen bieden voor vier recente blade-out-incidenten, waarbij, zoals gemeld in een Aviation Week van maart 2021 artikel:
"... schade veroorzaakt door bladfragmenten die delen van de motorkap of gondel raakten, veroorzaakte een reeks gebeurtenissen waardoor grote stukken structuur, waaronder delen van motorinlaten en ventilatorkappen, braken weg." Bij alle vier de ongevallen liep de romp van het vliegtuig schade op en bij Southwest Flight 1380 in april 2018 raakte een van de ruiten los, waardoor een passagier om het leven kwam.
“Er is enige interesse vanuit de industrie om thermoplastische composieten in motorcompartimenten toe te passen”, zegt Janssen, “dit is echter een langetermijnontwikkeling.” Een probleem voor een dergelijke ontwikkeling is certificering door luchtvaartautoriteiten, een ander gebied waarop Fraunhofer IPT actief is. “We bespreken nu met certificeringsinstanties hoe we de certificeringsinspanningen kunnen helpen verminderen door digitaal te bewijzen dat nieuwe productieprocessen voldoen aan de huidige en evoluerende normen. Dat is dus een nieuwe manier van denken. In de productie van de 21e eeuw zijn er zoveel gegevens beschikbaar, het gaat niet alleen om het certificeren van één proces of één ontwerp door te testen, en dan is dat bevroren." Met andere woorden, de nadruk van vandaag op Industrie 4.0 en Composites 4.0 is dat sensoren en AI-enabled software continu gegevens zullen verzamelen en intelligentie zullen ontwikkelen die vervolgens de productie continu zal optimaliseren en, op zijn beurt, die intelligentie terugsturen in de digitale draad om ontwerpen te verbeteren. Dit is inderdaad heel anders dan de productie van vandaag.
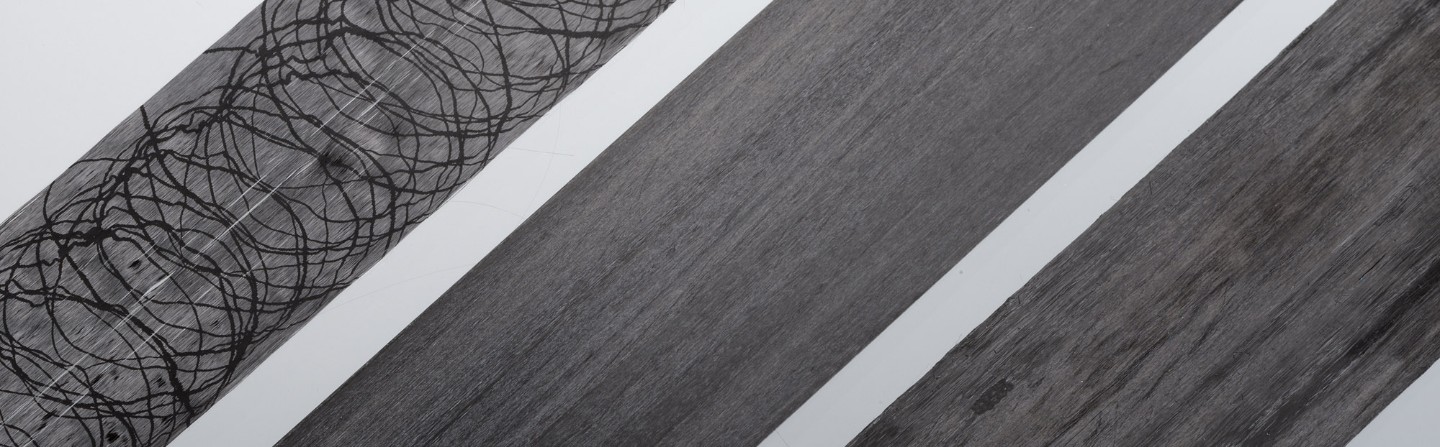
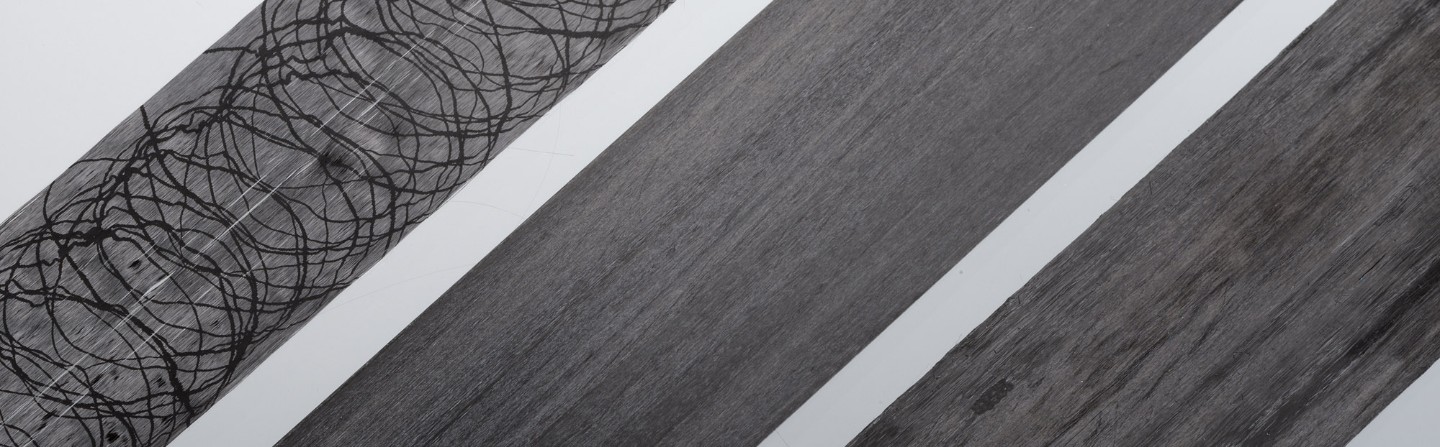
Het werk van Fraunhofer IPT met betrekking tot certificering, zegt Janssen, "zou kunnen helpen nieuwe technologieën mogelijk te maken, zoals thermoplastische composieten voor motoronderdelen - dat wil zeggen, als alle aspecten, inclusief technologie, ontwerp en risicobeheer, in overweging worden genomen." Hij stelt dat thermoplastische composieten een enorm potentieel bieden om de belangrijkste uitdagingen in een variëteit te helpen overwinnen van industriële sectoren, en merkt op dat Fraunhofer IPT eraan werkt om de verwerkingscomplexiteit van thermoplastische composieten te overwinnen, bijvoorbeeld door gebruik te maken van nieuw beschikbare digitale productiemethoden. "Bovendien kan het potentieel van thermoplastische composieten pas volledig worden benut als de volledige levenscyclus - inclusief hergebruik en recycling - wordt overwogen", zegt Janssen. “Zo werkt Fraunhofer IPT ook aan mechanische recycling van thermoplastische composieten. We zien dat het mogelijk zal zijn om hoogwaardig gerecycled materiaal te realiseren door zowel rekening te houden met de gegevens die tijdens de productie worden gegenereerd als met de gegevens die worden gegenereerd tijdens de hele levenscyclus van composietcomponenten.”
Hars
- Covestro verhoogt investeringen in thermoplastische composieten
- 2021 Beste lasergraveerder voor mesbladen en mesgrepen
- RECONTRAS-project valideert het gebruik van microgolven en laserlassen om recyclebare composieten te verkrijgen
- OTOMcomposite ontwikkelt software voor de productie van Composites 4.0 met behulp van laserondersteunde tapeplaatsing en -wikkeling
- Problemen oplossen met thermovormen van thermoplastische composieten
- Thermoplastische composieten:structurele bumperbeugel
- STELIA Aerospace Composites verbetert waterstofopslag
- TPAC en TPRC ontwikkelen recyclingproces voor thermoplastische composieten
- Thermoplastische composieten lassen
- Consortium thermoplastische composieten streeft naar productie in hoog volume voor Automotive en Aerospace
- RTP Company ontwikkelt lichte en sterke thermoplastische verbindingen