Wat is extrusie? Verschillende soorten extrusieprocessen?
Het extrusieproces is een van de soorten bulkvormende processen waarbij werkmetaal door een matrijsgat wordt geperst of gecomprimeerd om een bepaalde vereiste dwarsdoorsnedevorm te verkrijgen.
In eenvoudige bewoordingen is extrusie een metaalbewerkingsprocedure waarbij metaal onder verhoogde druk door een matrijsgat wordt geperst om de dwarsdoorsnede samen te drukken.
Sinds de evolutie van het extrusieproces is de wereld afhankelijk geworden van extrusie om staven, buizen en secties te produceren in elke vorm, hol of massief.
Omdat deze bewerking het duwen of trekken van de knuppel door de matrijs inhoudt, zijn de krachten die nodig zijn om de knuppel te extruderen tamelijk groot. Hete extrusie is de meest gebruikelijke methode omdat de weerstand tegen metaalvervorming laag is bij hoge temperaturen, terwijl koude extrusie over het algemeen alleen op zachte metalen wordt uitgevoerd.
Geschiedenis:
Hoewel het concept van extrusie is geboren uit het vormingsproces. Het is vastgelegd dat in 1797 een ingenieur met de naam Joseph Bramah het extrusieproces patenteerde.
De proef omvatte het voorverwarmen van metaal en het vervolgens door een matrijsholte te dwingen om een pijp uit de knuppel te maken. Hij gebruikte een met de hand aangedreven zuiger om het metaal te forceren.
Bramah vond vervolgens het hydraulische proces uit na de uitvinding van extrusie. Vervolgens gebruikte Thomas Burr de technologie van hydraulische pers en basisextrusietechniek, waarbij de afzonderlijke technologieën werden gecombineerd om een pijp (hol) te produceren. Het werd toen ook gepatenteerd in het jaar 1820.
De technologie werd toen een basisbehoefte in de groeiende wereld, terwijl het proces niet kon werken op de harde metalen. In het jaar 1894 introduceerde Thomas Burr extrusie met koper en messinglegeringen, wat een evolutie in de extrusietechniek teweegbracht.
Sinds de uitvinding van de extrusietechniek is het proces geëvolueerd naar een verscheidenheid aan technieken die in staat zijn om een breed scala aan producten met complexe structuren te produceren tegen de laagst mogelijke kosten.
Classificatie of soorten extrusieprocessen:
Verschillende soorten extrusieprocessen :
- Hete extrusie
- Koude extrusie
- Warme extrusie
- Wrijving extrusie
- Micro-extrusie
- Directe extrusie
- Indirecte extrusie
- Hydrostatische extrusie en
- Impact extrusie Proces.
#1. Heet extrusieproces:
In dit Hete extrusieproces wordt de knuppel boven de herkristallisatietemperatuur bewerkt. Deze hete bewerking zorgt ervoor dat het werkstuk niet uithardt en zorgt ervoor dat de ram het gemakkelijk door de matrijs duwt.
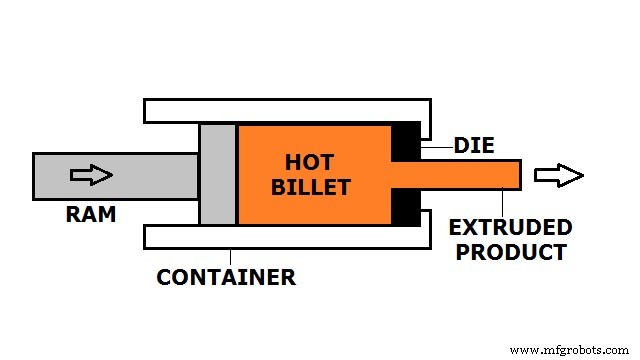
Hete extrusies worden over het algemeen uitgevoerd op horizontale hydraulische persen. De druk die bij dit proces betrokken is, kan variëren van 30 MPa tot 700 MPa. Om de hoge druk intact te houden, wordt smering toegepast. Olie of grafiet wordt gebruikt als smeermiddel bij extrusies bij lage temperaturen en glaspoeder wordt gebruikt bij extrusies bij hoge temperaturen.
De knuppel krijgt een warmte tussen 0,5 Tm en 0,75 Tm om een kwaliteitsvolle werking te verkrijgen.
Hete extrusietemperaturen van enkele veelgebruikte materialen zijn zoals vermeld:
Materiaal | Temperatuur (˚C) |
Aluminium | 350 tot 500 |
Koper | 600 tot 1100 |
Magnesium | 350 tot 450 |
Nikkel | 1000 tot 1200 |
Staal | 1200 tot 1300 |
Titanium | 700 tot 1200 |
PVC | 180 |
Nylon | 290 |
Voordelen van heet extrusieproces:
- Vervorming kan worden gecontroleerd volgens de vereisten.
- De knuppel wordt niet verstevigd door verharding van het werk.
- Er zijn minder krachten nodig om te drukken.
- Materialen met voortijdige scheuren kunnen ook worden bewerkt.
Nadelen van heet extrusieproces:
- Slechte oppervlakteafwerking.
- De maatnauwkeurigheid kan in gevaar komen.
- Verkort de levensduur van de container.
- Mogelijkheid tot oxidatie van het oppervlak.
#2. Koude extrusie:
Het is het proces waarbij metaal wordt gevormd door er met een slak op te slaan. Dit slaan wordt bereikt met een pons of ram in een gesloten holte. De ram dwingt het metaal door de matrijsholte om de massieve knuppel in een stevige vorm te transformeren.
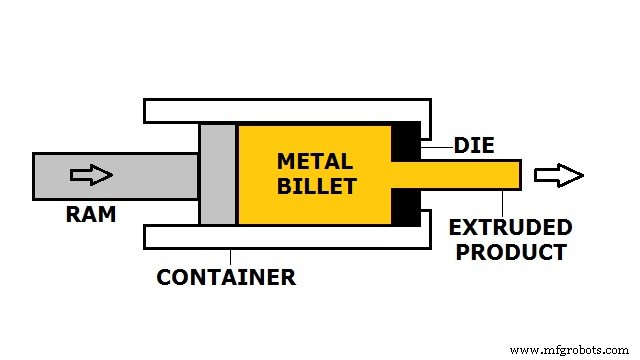
Hierbij wordt het werkstuk bij kamertemperatuur of iets boven kamertemperatuur vervormd.
Omdat de benodigde krachten te hoog zijn, wordt bij deze techniek een krachtige hydraulische pers gebruikt. De druk gaat tot 3000 MPa.
Voordelen:
- Geen oxidatie.
- Verbeterde sterkte van het product.
- Nauwere toleranties.
- Verbeterde oppervlakteafwerking.
- Hardheid is verbeterd.
Nadelen:
- Hogere krachten zijn vereist.
- Er is meer vermogen nodig om te werken.
- Niet-ductiele materialen kunnen niet worden bewerkt.
- Strain verharding van het materiaal dat wordt geëxtrudeerd is een beperking.
#3. Warm extrusieproces:
Warme extrusie is het proces waarbij een knuppel wordt geëxtrudeerd boven kamertemperatuur en onder de herkristallisatietemperatuur van het materiaal. Dit proces wordt gebruikt waar het materiaal moet worden voorkomen door microstructurele veranderingen die optreden tijdens het extrusieproces.
Dit proces is belangrijk om de juiste balans tussen vereiste krachten en ductiliteit te bereiken. De temperatuur van elk metaal dat bij deze bewerking wordt gebruikt, kan tussen 424 graden Celsius en 975 graden Celsius liggen.
Voordelen van een warm proces:
- Verbeterde kracht.
- Het verbeterde de hardheid van het product.
- Gebrek aan oxidatie.
- Er kunnen zeer nauwe toleranties worden bereikt.
Nadelen:
- Niet-ductiele materialen kunnen niet worden geëxtrudeerd.
- Een stuk verwarmingsapparatuur is extra.
#4. Wrijving extrusie:
Bij de frictie-extrusietechniek worden de knuppel en de container gedwongen tegen elkaar in te draaien, terwijl tijdens het werk tegelijkertijd de knuppel door de matrijsholte wordt geduwd om het gewenste materiaal te produceren.
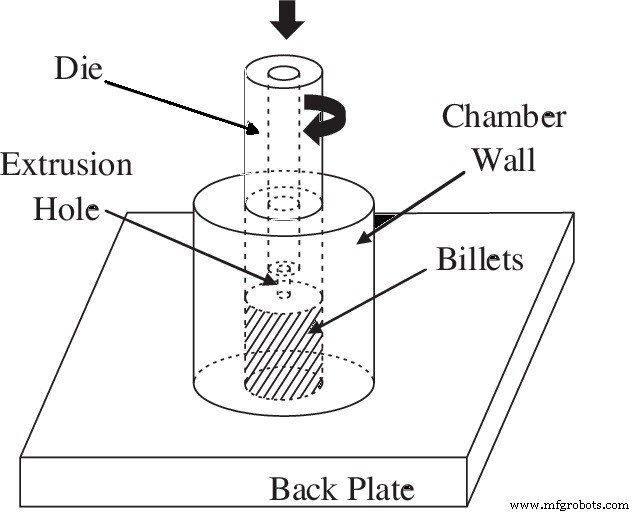
Het proces wordt beïnvloed door de relatieve rotatiesnelheid tussen de knuppel en de matrijs. De relatieve roterende beweging van de lading en de matrijs heeft een significante invloed op het proces.
Ten eerste resulteert dit in het genereren van een groot aantal schuifspanningen waardoor de knuppel plastisch vervormt. Ten tweede wordt er een grote hoeveelheid warmte gegenereerd tijdens de relatieve beweging tussen de knuppel en de matrijs, dus voorverwarmen is niet nodig, waardoor het proces efficiënter wordt.
Het kan substantieel geconsolideerde draad, staven, buizen en andere niet-cirkelvormige metaalgeometrieën rechtstreeks genereren uit een verscheidenheid aan voorloperladingen, zoals metaalpoeder, vlok, bewerkingsafval (spanen of spanen) of vaste knuppels.
Voordelen van wrijvingsproces:
- Geen verwarming nodig.
- Het ontstaan van schuifspanningen resulteert in een verbeterde vermoeiingssterkte van het product.
- Elk type materiaal kan als knuppel worden gebruikt, waardoor dit proces economisch is.
- Lage energie-input.
- Betere weerstand tegen corrosie.
Nadelen van wrijving Proces:
- Verwachte oxidatie.
- Hoge initiële instellingen.
- Complexe machines.
#5. Micro-extrusieproces:
Door de nomenclatuur wordt duidelijk dat dit proces betrekking heeft op de productie van producten in het submillimeterbereik.
Net als bij extrusie op macroniveau, wordt de knuppel hier door de matrijsopening gedwongen om de verwachte vorm op de knuppel te genereren. De uitvoer past door een vierkant van 1 mm.
Voorwaartse of directe en achterwaartse of indirecte micro-extrusie zijn de twee meest fundamentele technieken die in dit tijdperk worden gebruikt om micro-elementen te produceren.
Voorwaartse micro-extrusie heeft de ram die de knuppel naar voren drijft en de knuppel beweegt in dezelfde richting, terwijl bij achterwaartse micro-extrusie de ram en knuppel in tegengestelde richtingen bewegen.
Micro-extrusie wordt veel gebruikt bij de productie van componenten voor resorbeerbare en geïmplanteerde medische apparaten, variërend van bioresorbeerbare stents tot systemen voor gecontroleerde afgifte van geneesmiddelen.
Terwijl op mechanisch gebied de toepassing op grote schaal kan worden waargenomen bij de productie van kleine tandwielen, kleine pijpen, enz.
Voordelen van microproces:
- Er kunnen zeer complexe doorsneden worden gemaakt.
- Kleine elementen kunnen worden geproduceerd.
- Verbeterde geometrische toleranties.
Nadelen :
- Het is een uitdaging om een kleine dobbelsteen en een container te maken om aan onze behoeften te voldoen.
- Er is een bekwame werker nodig.
#6. Directe of voorwaartse extrusie:
Bij het directe extrusieproces wordt eerst een metalen knuppel in de container geplaatst. De container heeft een voorgevormd matrijsgat. Een ram wordt gebruikt om de metalen knuppel door het matrijsgat te drijven en het product wordt vervaardigd.
Bij dit type is de richting van de metaalstroom dezelfde als die van de bewegingsrichting van de ram.
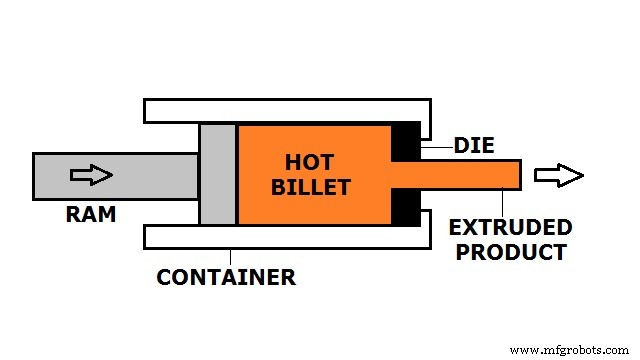
Wanneer de knuppel wordt gedwongen om naar de matrijsopening te bewegen, wordt een grote hoeveelheid wrijving geproduceerd tussen het oppervlak van de knuppel en de containerwanden. Het bestaan van wrijving vereist een aanzienlijke toename van de ramkracht, waardoor meer vermogen wordt verbruikt.
In dit proces is het extruderen van brosse metalen zoals wolfraam en titaniumlegeringen moeilijk omdat ze tijdens het proces breken. De trekkrachten tijdens het hele proces zorgen ervoor dat er snel microscheurtjes ontstaan, wat resulteert in breuken.
Het extruderen van brosse metalen zoals wolfraam- en titaniumlegeringen is moeilijk omdat ze tijdens het proces breken. Trekkrachten zorgen ervoor dat er snel microscheurtjes ontstaan, wat resulteert in breuken.
Ook versterkt de aanwezigheid van een oxidelaag op het oppervlak van de knuppel de wrijving. Deze oxidelaag heeft de potentie om gebreken te veroorzaken in het geëxtrudeerde product.
Om dit probleem te verhelpen, wordt een dummyblok tussen de ram en de werkbalk geplaatst om de wrijving te verminderen.
Buizen, blikken, bekers, kleine tandwielen, assen en andere geëxtrudeerde goederen zijn voorbeelden.
Sommige delen van de knuppel blijven altijd aan het einde van elke extrusie. Het wordt de kont . genoemd . Het wordt van het product verwijderd door het direct voorbij de uitgang van de matrijs te snijden.
Voordelen van direct proces:
- Het proces is in staat om langere werkstukken te extruderen.
- Verbeterde mechanische eigenschappen van het materiaal.
- Goede oppervlakteafwerking.
- Koude en warme extrusies zijn mogelijk.
- Mogelijkheid om continu te werken.
Nadelen van direct proces:
- Broze metalen kunnen niet worden geëxtrudeerd.
- Grote kracht en hoge vermogensbehoefte.
- Mogelijkheid tot oxidatie.
#7. Indirecte of achterwaartse extrusie:
Bij dit achterwaartse extrusieproces blijft de matrijs stationair, terwijl de knuppel en container in combinatie bewegen. De matrijs is op de ram gemonteerd in plaats van op de container.
Het metaal stroomt door het matrijsgat aan de kant van de ram in de tegenovergestelde richting van de beweging van de ram terwijl het wordt samengedrukt door de ram.
Wanneer de knuppel wordt samengedrukt, zal het materiaal tussen de doorn en dus de matrijsopening passeren.
Aangezien er geen relatieve beweging is tussen de knuppel en de container, wordt er geen wrijving geregistreerd. Dit tilt het proces op boven het directe extrusieproces, waardoor de gebruikte ramkracht kleiner is dan bij de directe extrusie.
Om de matrijs stationair te houden, wordt een "steel" gebruikt die langer is dan de lengte van de container. De kolomsterkte van de steel bepaalt de uiteindelijke en maximale extrusielengte.
Doordat de knuppel in combinatie met de container beweegt, worden alle wrijvingskrachten eenvoudig geëlimineerd.
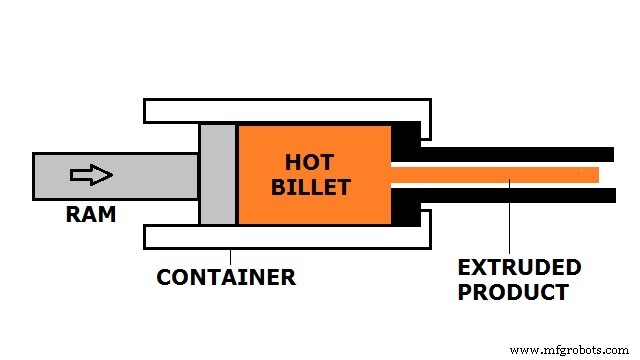
Voordelen van indirecte processen:
- Er is minder extrusiekracht nodig.
- Kleinere doorsneden kunnen worden geëxtrudeerd.
- Vermindering van wrijving met 30%.
- Verbeterde bedieningssnelheid.
- Er wordt zeer weinig slijtage geregistreerd.
- Extrusiefouten of grofkorrelige ringzones zullen minder snel optreden omdat de metaalstroom consistenter is.
Nadelen van indirecte processen.
- Dwarsdoorsnede van het geëxtrudeerde materiaal wordt beperkt door de maat van de gebruikte steel.
- Mogelijkheid van restspanningen na extrusie.
- Onzuiverheden en defecten beïnvloeden de oppervlakteafwerking en maken het product compromitterend.
#8. Hydrostatische extrusie:
Bij het hydrostatische extrusieproces wordt de knuppel omgeven door vloeistof in de container, die door de voorwaartse beweging van de ram tegen de knuppel wordt gedrukt. Er is geen wrijving in de container vanwege de vloeistof en er is zeer weinig wrijving bij het matrijsgat.
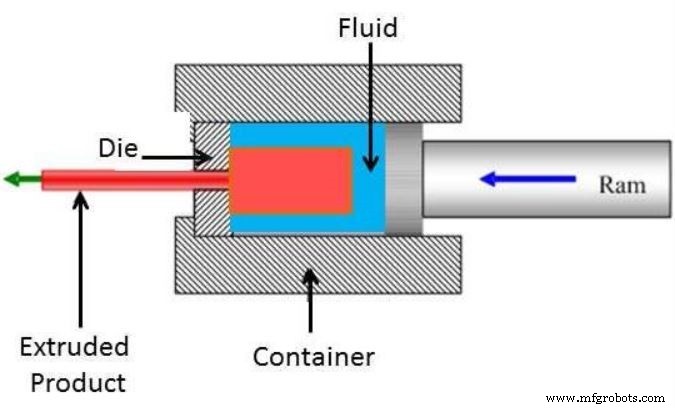
De knuppel raakt niet verstoord bij het vullen van de boring van de houder, aangezien deze wordt onderworpen aan uniforme hydrostatische druk. Dit resulteert met succes in een knuppel met een enorme lengte-diameterverhouding, zelfs draadspoelen kunnen feilloos worden geëxtrudeerd of een ongelijke dwarsdoorsnede.
Het belangrijkste verschil tussen hydrostatische en directe extrusie is dat er geen direct contact is tussen de container en de knuppel tijdens hydrostatische extrusie.
Werken bij hoge temperaturen vereist het gebruik van gespecialiseerde vloeistoffen en processen.
Wanneer een materiaal wordt onderworpen aan hydrostatische druk en er geen wrijving is, neemt de taaiheid ervan toe. Als gevolg hiervan kan deze methode worden gebruikt op metalen die te broos zijn voor typische extrusiemethoden.
Deze benadering wordt gebruikt op ductiele metalen en maakt hoge reductieverhoudingen mogelijk.
Voordelen:
- Geëxtrudeerde goederen hebben een uitstekende oppervlaktepolijsting en zijn maatvast.
- Geen sprake van wrijving.
- Geminimaliseerde krachtvereisten.
- Er blijven geen knuppelresten achter in het proces.
- De materiaalstroom is gelijkmatig.
Nadelen:
- Bij gebruik bij hoge temperaturen moeten speciale vloeistoffen en procedures worden gebruikt.
- Elke knuppel moet vóór het werk worden voorbereid en aan één kant taps toelopen.
- Het is moeilijk om de vloeistof te bevatten.
#9. Impact extrusie:
Impactextrusie is een andere belangrijke methode voor het produceren van geëxtrudeerde metalen profielen. In tegenstelling tot het traditionele extrusieproces, waarbij hoge temperaturen nodig zijn om het materiaal zacht te maken, wordt bij impactextrusie vaak gebruik gemaakt van koude metalen knuppels. Deze knuppels worden onder hoge druk en efficiëntie geëxtrudeerd.
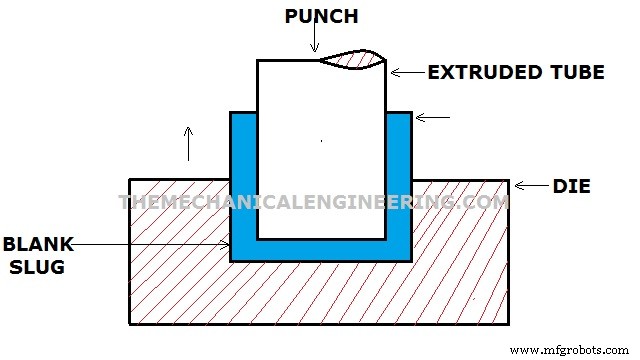
Een op geschikte wijze gesmeerde slak wordt in een matrijsholte geplaatst en met een stoot in een enkele slag geraakt tijdens een conventionele slagextrusiebewerking. Hierdoor stroomt het metaal terug rond de stempel door een opening tussen de matrijs en de stempel.
Dit proces werkt beter met zachtere materialen zoals lood, aluminium of tin.
Dit proces wordt altijd in koude toestand uitgevoerd. Het achterwaartse impactproces zorgt voor zeer dunne wanden. Maak bijvoorbeeld tandpastatubes of batterijboxen.
Het wordt uitgevoerd in een sneller tempo en met kortere slagen. In plaats van druk uit te oefenen, wordt slagdruk gebruikt om de knuppel door de matrijs te extruderen. Impacting daarentegen kan worden uitgevoerd door voorwaartse of achterwaartse extrusie, of een combinatie van beide.
Voordelen:
- Grote verkleining.
- Snel proces. Verminderde bewerkingstijd tot 90%.
- Verhoogde productiesnelheid.
- Verhoogde tolerantie-integriteit.
- Tot 90% besparing op grondstoffen.
Nadelen:
- Er is een zeer hoge drukkracht vereist.
- De grootte van de knuppel is een beperking.
Factoren die de extrusiekracht beïnvloeden:
De volgende factoren zijn van invloed op de extrusiekracht:
- Werktemperatuur.
- Ontwerp van de apparatuur, horizontaal of verticaal.
- Type extrusie.
- De verhouding van extrusie.
- Hoeveelheid vervorming.
- Wrijvingsparameters.
Extrusieproces Toepassing of gebruik:
- Het wordt veel gebruikt bij de productie van buizen en holle buizen. En wordt ook gebruikt om plastic voorwerpen te maken.
- Het extrusieproces wordt gebruikt om kozijnen, deuren, ramen, enz. in de auto-industrie te produceren.
- Het metaal Aluminium wordt in veel industrieën gebruikt bij constructiewerk.
Industriële technologie
- Wat is aansnijden? - Proces, werken en typen
- Wat is smeden? - Definitie, proces en typen
- Wat is extrusie? - Werken, typen en toepassingen
- Wat zijn de verschillende soorten buisbuigen?
- Wat zijn de verschillende soorten onderhoudspersoneel?
- Wat zijn de verschillende soorten lassen?
- Wat zijn de verschillende soorten prototypes?
- Wat zijn de 4 soorten fabricageprocessen?
- Verschillende soorten elektrisch booglasproces
- Verschillende soorten plaatbewerkingsprocessen
- Verschillende soorten afwerkingsprocessen