Nieuwe benaderingen voor het maken van onderdelen voor de oliepatch
Fracking heeft geleid tot grote veranderingen in de olievlek en grote veranderingen in de bewerking van onderdelen.
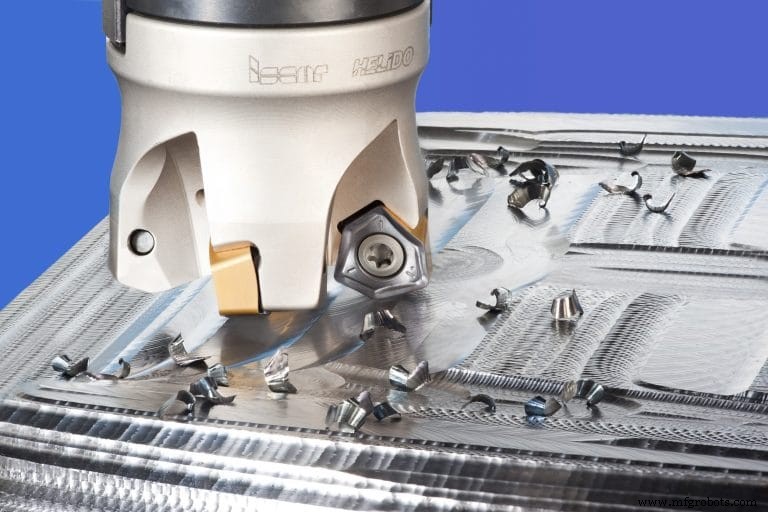
Rod Zimmerman van snijgereedschapfabrikant Iscar Metals woont in een aangename groene zone in een buitenwijk van Fort Worth. Maar binnen een halve mijl van zijn huis heeft een oliemaatschappij een verticaal gat van 2286 meter diep gezonken, van waaruit het negen zijlijnen heeft gespreid, elk ongeveer een halve mijl. Het pompt frackingvloeistof in deze leidingen bij 9.000 psi om het aardgas te extraheren. Het is een even goed voorbeeld als de alomtegenwoordigheid van de fracking-revolutie en de verbazingwekkende technologie die erbij betrokken is.
En hoewel de revolutie misschien niet letterlijk "overal" is, zei Salvatore Deluca, productmanager voor een andere fabrikant van snijgereedschap, Allied Machine &Engineering, dat de gigantische fracking-faciliteiten in zijn land "steden" worden genoemd. Behalve dat, in tegenstelling tot Dallas-Fort Worth, deze 'steden' in het verre Ohio liggen, een staat die voorheen niet bekend stond om zijn aardolie. Het is dan ook geen verrassing dat grote veranderingen in de olievlek hebben geleid tot grote veranderingen in het bewerken van onderdelen voor de olievlek.
Het Fracking-blok aanpakken
Zoals hierboven vermeld, wint hydraulisch breken (beter bekend als fracking) gas en olie terug uit schalieformaties door in de aarde te boren en een mengsel van water, zand en chemicaliën onder extreem hoge druk in het gesteente te injecteren. Om die druk te genereren, zijn gigantische pompen nodig, waarvan een belangrijk onderdeel het "vloeistofuiteinde" of "frackingblok" en zijn kleppen, zuigers en voeringen is.
De hoge druk en abrasiviteit van de slurry die door deze blokken wordt gepompt, veroorzaakt snelle slijtage en barsten. En aangezien operators van olievelden hoge druk moeten handhaven, zijn ze genoodzaakt om de vloeistofuiteinden om de paar dagen te vervangen, volgens Paul Best, een productspecialist bij Allied Machine, Dover, Ohio. Het beste is dat vloeistofuiteinden zijn vervaardigd uit massieve blokken staal en zijn over het algemeen ongeveer 3 "lang, 4" breed en 2-3 "(0,61-0,91 m) dik. Met complexe contouren, talrijke kanalen, drie tot vijf doorgaande gaten (elk tot 203,2 mm in diameter) en drie tot vijf kruisende kruisgaten, vereisen vloeistofuiteinden enorme hoeveelheden frezen, boren en draadsnijden.
Zimmerman, vice-president verkoop, West Zone voor Iscar, zei dat vloeistofuiteinden traditioneel zijn gemaakt van gelegeerd staal uit de 4000-serie, maar om slijtage tegen te gaan, proberen gebruikers "meer exotische legeringen zoals 17-4 PH roestvrij staal, super duplex roestvrij staal en 15-5 roestvrij.” Deluca schatte dat ongeveer de helft van de vloeistofuiteinden die hij nu ziet een variant is van een voorgehard roestvrij staal en het aandeel blijft groeien.
Gayle Vollmer, engineering services voor Hartwig in Houston (Okuma's dealer in het gebied) zei dat er ook een beweging is om hardere materialen te gebruiken voor de onderdelen van een fracking-blok die het meest vatbaar zijn voor slijtage, en een poging om fracking-blokken opnieuw te ontwerpen zodat meer componenten zijn gemakkelijk vervangbaar. Maar hij vermoedde dat de huidige vraag naar hoge productie dergelijk onderzoek op een laag pitje heeft gezet.
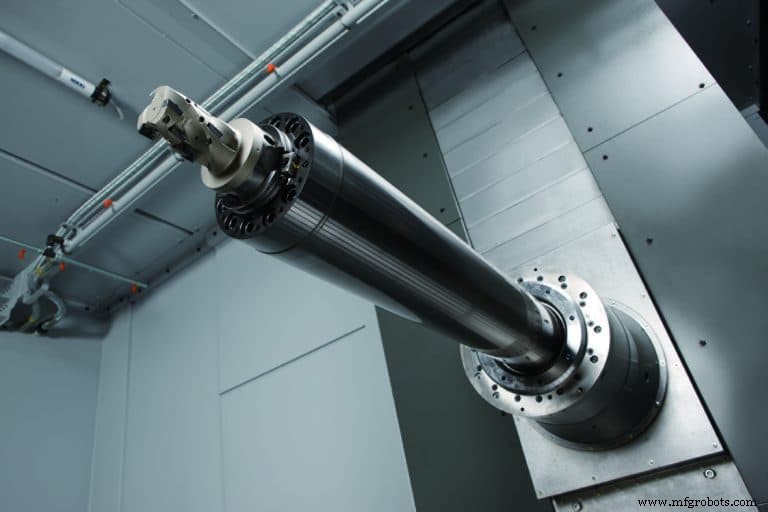
Of het nu is gemaakt van 4340 of een harder roestvrij staal, het aanpakken van een vloeistofuiteinde vereist vrijwel een grote kotterbank of een horizontaal bewerkingscentrum. Jason Schooley, regionaal verkoopmanager voor JTEKT Toyoda Americas, Arlington Heights, Illinois, zei dat het doel is om zoveel mogelijk bewerkingen uit te voeren in één machine, wat dubbel belangrijk is voor een onderdeel dat zo groot en moeilijk te verplaatsen is.
Schooley zei dat, hoewel saaie molens doorgaans grotere tafels hebben voor nog grotere onderdelen, horizontale machines zoals Toyoda's FH1250SX bijna vier keer sneller zijn. Dat is deels te danken aan een tandwielaangedreven spindel van 6.000 tpm (naar keuze 8.000 tpm of een spil met hoog koppel van 15.000 tpm) en een hoge voedingssnelheid van 1.654 ipm (42 m/min). De machine is gebouwd op een Meehanite gietijzeren basis voor maximale stijfheid met cilindrische rolgeleiders voor hogere snelheid, terwijl de dubbele kogelomloopspindelaandrijving op de Y- en Z-assen de bewerkingsstabiliteit tijdens zwaar snijden verhoogt.
De FH1250SW heeft ook een W-as voor diep boren en kotterbewerkingen. Hij voegde eraan toe dat de afgelopen jaren "een aantal machinebouwers hebben gekozen voor een ingebouwde U-askop" of een W-as, die respectievelijk parallel aan de X-as of Z-as rijden. Dit maakt het mogelijk om het draaipunt te wijzigen voor een vast draaigereedschap, een handige functie bij het snijden van grote boringen of andere grote contouren. Dat komt omdat vloeistofuiteinden niet alleen grote boringen hebben, de boringen zijn van binnen vaak "flesvormig", zodat ze niet zomaar kunnen worden geboord. Voor machines die geen ingebouwde U-as hebben, kunnen gebruikers een "feed-out" kop toevoegen die dezelfde functie vervult, D'Andrea is zo'n leverancier.
Er zijn nadelen verbonden aan het monteren van een grote kop op een roterende spil, waaronder mogelijke interferentie van onderdelen en incompatibiliteit met koelvloeistoftoevoer door de spil. De aftermarket-optie heeft ook een eigen externe schijf nodig en het is misschien niet mogelijk om de rig automatisch uit te schakelen zoals bij andere gereedschapswisselingen.
Maar Schooley zei dat interferentie geen probleem is bij frack-bloktoepassingen als de Z-asbeweging van de machine lang genoeg is om te voorkomen dat de opzetkop voorbij de meetlijn steekt. Met 1850 mm Z-asverplaatsing en 200 mm van spilneus tot dode band in het midden van de tafel, pakt de 1250-machine frackblokken aan zonder interferentie. Hij voegde eraan toe dat Toyoda de mogelijkheid om automatisch te wisselen voor zijn contourkoppen verder heeft ontwikkeld om "onze klanten te helpen voorop te blijven lopen in een industrie die zo vluchtig is als olie."
De ervaring van Schooley is dat de modulaire kottergereedschappen die verkrijgbaar zijn bij Innovative Tooling Solutions en anderen standaard worden geleverd met koelmiddel door de spil en veel winkels die frackblokken maken, gebruiken een speciale horizontale kotterbank met een contourkop om de boringen af te werken. Toyoda biedt ook horizontale bewerkingscentra met spilspil met een koppel van 1.560 ft-lb voor zware bewerkingen. Schooley zei dat de as met 4.000 tpm het bereik en de kracht combineert die nodig zijn voor kotteren en diep boren, waardoor werkstukken waarvoor voorheen twee bewerkingen nodig waren, op één machine konden worden voltooid. De roterende pallet met 360.000 posities van de machine biedt maximale flexibiliteit voor zware bewerkingen op een verscheidenheid aan werkstukken.
Okuma America Inc., Charlotte, N.C., heeft een programmeeroptie ontwikkeld, Turn-Cut genaamd, waarmee een horizontaal bewerkingscentrum een draaibank kan nabootsen bij het snijden van cirkelvormige en hoekige kenmerken op grote, ongebalanceerde onderdelen zonder een U-kop te gebruiken. Zoals Ted Winkle, de coördinator van het technische centrum van Okuma in Houston, uitlegde:"In plaats van het onderdeel te roteren, wat voor sommige grote onderdelen moeilijk of onmogelijk zou zijn, draai je het gereedschap rond het onderdeel. En in plaats van dat een U-kop het gereedschap uit het midden van de rotatie-as verplaatst, interpoleert Turn-Cut die assen in X en Y, terwijl het ook een enkelpunts draaigereedschap in Z voedt.”
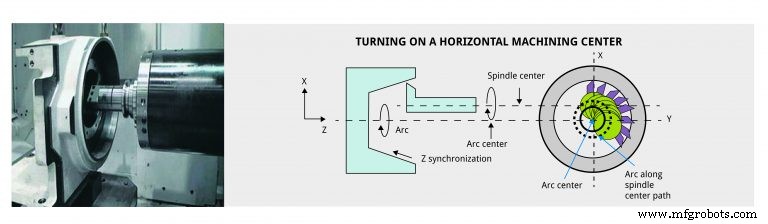
Winkle denkt dat Turn-Cut een grotere rol zal spelen in de olie- en gasindustrie voor onderdelen zoals fracking-blokken, omdat "naarmate boringen groter in diameter worden, er veel koppel nodig is om een solide gereedschap te laten draaien om een gat van dat formaat te maken. De mogelijkheid om te draaien, in tegenstelling tot een U-kop en al het dure gereedschap dat daarmee gepaard gaat, is een voordeel.”
Aan de andere kant is Turn-Cut niet goedkoop omdat het extra software vereist voor gespecialiseerde versnelling, vertraging en synchronisatie, plus glazen schalen en kogelomloopkoeling. Maar u krijgt een betere precisie voor een verscheidenheid aan onderdelen met deze functies en het vergroot de kans dat u onderdelen in één opstelling kunt afwerken.
Schooley wierp tegen dat de techniek veel herhaalde bewegingen vereist in hetzelfde gebied van de kogelomloopspindels en geleidingen (hoe kleiner de diameter, hoe meer dit zou gebeuren) en dit zou de levensduur van de machine kunnen verkorten.
Aan de andere kant, zei Winkle, zou je, tenzij je deze mogelijkheid vaak op onderdelen van dezelfde grootte gebruikt, geen overmatige beweging in hetzelfde gebied hebben. En als u de mogelijkheid niet vaak nodig hebt, zou u de hoge kosten van een U-as niet kunnen rechtvaardigen, dus Turn-Cut zou een logischere optie zijn. Zoals bij elke functie van bewerkingsmachines zijn er compromissen.
Horsepower Heaven
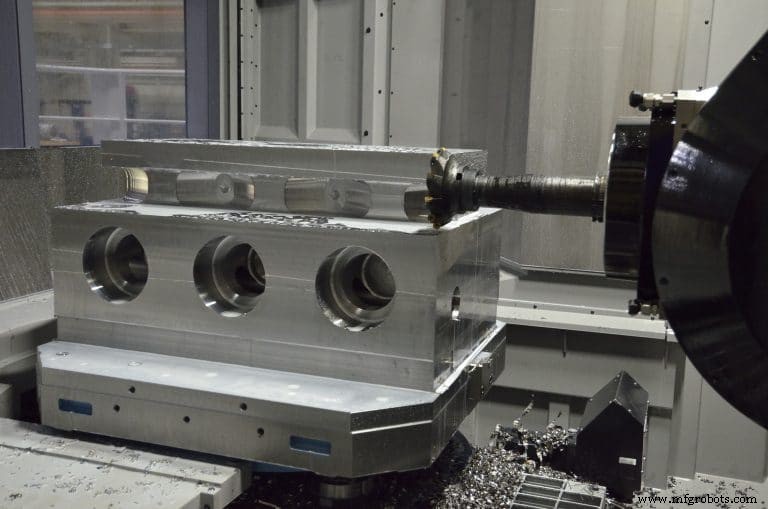
Voor Makino Inc., Mason, Ohio zijn de T1- en T2- vijfassige horizontale bewerkingscentra de "go-to"-platforms voor onderdelen zoals fracking-blokken. David Ward, productmarketingmanager, zei dat beide machines direct aangedreven spindels hebben die "ideaal zijn voor de uitdagende roestvaste en hooggelegeerde staalsoorten die in deze industrie worden gebruikt."
De T1 heeft een HSK100 12.000 tpm spindel met 143 pk en een nominaal koppel van 740 ft-lb. De grotere T2-spil maakt gebruik van een HSK125-interface voor radiale stijfheid. De T2-spil met 4.000 tpm levert 200 pk en een nominaal vermogen en koppel van 1.107 ft-lb.
Ward voegde eraan toe dat beide spindels hun maximale koppelwaarden tot 1.000 tpm behouden. "Door de maximale koppelwaarden tot op dit punt uit te voeren, zorgt het ervoor dat de spil kan profiteren van nieuwe ontwikkelingen in de snijgereedschaptechnologie, zoals wisselplaatcoatings bij hoge temperaturen."
Winkle merkte op dat de olievlek wordt gedomineerd door CAT 50-machines, maar was het ermee eens dat het gezichtscontact van de HSK- en BIG Plus-interfaces een voordeel zou zijn "als je een lange overhang hebt. Maar aangezien de meeste bewerkingskrachten axiaal zijn, maakt het niet veel uit welk "spiltype" u kiest. Zolang het maar vet is. "Het naderen van een frackblok met een ISO 40 spindelmachine zou een oefening in nutteloosheid zijn", zei hij.
Bronnen waren het erover eens dat hogedrukkoelvloeistof essentieel is voor het verwijderen van warmte en spanen in veel olie- en gastoepassingen, of zoals Iscar's Zimmerman het uitdrukte, "bijna ongeacht de toepassing. Wanneer u diep in een boorgat aan een vloeistofuiteinde werkt, is het van cruciaal belang om de spanen weg te spoelen en dat is moeilijk. Een met koelmiddel gevoede frees is verreweg de beste keuze voor dergelijke toepassingen.”
Dus als de machine niet met deze mogelijkheid werd geleverd, voegen gebruikers deze toe met eenheden van leveranciers zoals ChipBLASTER. "Ik zou niet eens overwegen om vandaag een freesmachine te kopen zonder hogedrukkoelmiddel door de spil", zei Zimmerman. "Het is een gamechanger voor zowel frezen als boren." De enige uitzondering is een situatie waarin u de koelvloeistof niet naar de snijkant kunt richten. In dat geval "werkt koelvloeistof soms tegen je en is het beter om machinaal te drogen om thermische scheuren van de wisselplaten te voorkomen", zei hij.
Deluca zei dat machinebouwers op deze vraag hebben gereageerd, zodat hij nu vaak machines aantreft met een door OEM geleverde pomp die 1.000 psi levert bij 20 gpm. Ward zei dat Makino's T1 26 gpm levert bij 1.000 psi, terwijl de T2 dezelfde druk levert bij 53 gpm.
Vooruitgang snijgereedschap
Hoewel je misschien dol bent op een monster met een hoog vermogen voor je fracking-blokken, zei Deluca van Allied Machine dat ze steeds vaker voor de tegenovergestelde uitdaging staan:de noodzaak om grote gaten te boren met machines die zijn gericht op frezen waar de spilsnelheden hoger zijn, maar het aantal pk's maximaal is bij 40 tot 50.
"De bedrijven die deze onderdelen maken, zijn meestal klein tot middelgroot en zijn meestal niet toegewijd aan het maken van frack-blokken", zei hij. “En veel mensen zijn wantrouwend om zich op deze markt te concentreren en een half miljoen dollar uit te geven aan een machine voor een industrie die als een achtbaan draait. Dus moesten we
een gereedschap ontwikkelen dat een gat met een diameter van 4″ kan snijden met veel hogere spilsnelheden en veel lagere voedingssnelheden dan onze traditionele boorproducten.”
De uitdaging bij het boren van frackingblokken gaat verder dan de grootte van de benodigde gaten. "Onderbroken sneden zijn inherent aan de productie van vloeibare eindblokken, omdat de dwarsgaten loodrecht op bestaande gaten worden geboord", zegt Allied Machine's Best. “Vanwege de resulterende vorm van de kruisende gaten blijven de buitenranden van de boor in de snede zitten, terwijl de binnenrand dat niet doet. Dit kan de boor destabiliseren, wat het gereedschap kan vernietigen en de integriteit van het frackingblok kan beschadigen.”
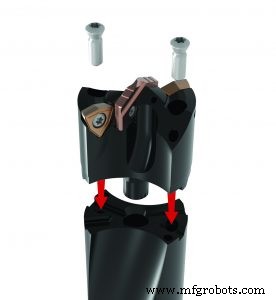
Als de klant bezuinigt door materiaal te gebruiken dat niet met warmte is behandeld, kan de boor aanzienlijke variaties tegenkomen. Deluca van Allied zei dat normaal gesproken betekent dat een operator het proces constant moet controleren of een catastrofale boorfout riskeert binnen enkele seconden nadat hij een zak in het gietstuk heeft geraakt, waardoor een onderdeel waar je uren in hebt gestoken, zou kunnen vernielen. Winkels ervaren ook materiaalvariaties van blok tot blok, waardoor het moeilijk is om de perfecte boor- en bedrijfsparameters te kiezen.
Allied is deze uitdagingen aangegaan met een tool van de volgende generatie, de APX. Het heeft een harder carbidesubstraat en een gepatenteerde coating om de schok van het raken van een zak te weerstaan. "Je mag het gereedschap afbreken en je krijgt een gil," zei Deluca, "maar je zult nog steeds in staat zijn om het gat af te maken."
Hij voegde eraan toe dat Allied de problemen van cross-hole boren aanpakte door een wiper aan het inzetstuk toe te voegen om de stabiliteit te verbeteren, plus slijtkussens om extra stabiliteit te bieden wanneer de piloot een lege ruimte of een cross-hole verlaat. “We raden ook aan om de voeding lichter te maken en dezelfde snelheid aan te houden bij het boren van gehoekte uitgangsgaten, zodat het gereedschap niet weg wil duwen of lopen. Het is meestal niet nodig bij het boren van de hoofdlijn of de dwarsgaten, maar er is maar zoveel techniek die je in een gereedschap kunt stoppen om de extreem onderbroken snede van de schuine gaten te compenseren.”
Voor frezen zei Zimmerman dat de HeliDo H600 dubbelzijdige zeshoekige wisselplaat van Iscar buitengewoon goed werkt voor dit type materiaal. "We bieden ook de Mill 4 Feed aan, een vierkante, enkelzijdige wisselplaat met een positievere geometrie voor een zachtere snede die minder pk's vereist."
Zijn belangrijkste boodschap is dat, aangezien Iscar zich al lang inzet voor de olie- en gasindustrie en alleen ervaren machinisten inhuurt, het het optimale proces voor een klant kan ontwikkelen en uit een breed scala aan gereedschappen kan kiezen. "We hebben veel soorten voermolens en kunnen een voermolen optimaliseren op basis van de toepassing, het materiaal en de machine, rekening houdend met de stijfheid, het aantal pk's en het koppel."
Multitasking en automatisering
Het is waarschijnlijk dat 9.500 lb fracking-blokken er niet toe leiden dat iemand "automatisering" denkt, maar Makino en andere bouwers bieden oplossingen waarmee één operator meerdere machines kan bedienen. Voor frackblokken betekent dat over het algemeen een roterende palletwisselaar die in minder dan een minuut schakelt tussen een onbewerkt gietstuk en een afgewerkt onderdeel. Daarna heeft de operator voldoende tijd om het voltooide stuk te verwijderen.
Met cyclustijden van enkele minuten bevinden fracking gun tubes zich aan de andere kant van het spectrum. En aangezien ze een "eenmalig gebruik" zijn, zei Vollmer, "zijn de productiesnelheden astronomisch. Elke dag worden er duizenden gemaakt.”
Als gevolg hiervan is het onderdeel ideaal voor automatisering en hebben Hartwig en Okuma samengewerkt om verschillende opties te bieden. Deze omvatten robots voor laden/lossen en staafaanvoersystemen zoals die worden gebruikt voor kleine onderdelen op draaimachines in Zwitserse stijl, behalve dat ze hier diameters van 2-4″ verwerken. De snelste benadering voert het materiaal in een machine met dubbele spil, waarbij het ene uiteinde wordt bewerkt en het onderdeel vervolgens rechtstreeks in de subspil wordt gevoerd om aan het andere uiteinde te werken.
Vollmer zei dat de onderdelen draaien, draadsnijden en wat frezen vereisen, idealiter met behulp van live tools voor de laatste, een functie die door Winkle wordt aangeduid als "een van de grootste veranderingen in de branche in de afgelopen jaren". Fracking en gestuurd boren zijn opnieuw een grote reden voor die overgang.
Voor veel van de grotendeels cilindrische onderdelen die nodig zijn in de huidige "down-hole" -bewerkingen, heeft de ideale draaibank echter meer dan live gereedschap en een of twee revolvers. Het heeft een draaibare kop en meerassige freesmogelijkheden zoals Okuma's MULTUS frees-draai-serie.
"De onderdelen die nodig zijn voor zowel het boren als de voltooiingsfase zijn veel complexer dan bij traditionele verticale putten", legt Winkle uit. “Je moet kleppen kunnen openen en sluiten om van productiezone te wisselen. Onderdelen hebben hydraulisch leidingwerk en elektronische bewakingsapparatuur.”
Dit vereist kruisgaten en ingewikkelde gefreesde functies op de OD en ID, dus de machines hebben vijfassige positionering en negen of zo assen van machinebeweging nodig om een onderdeel aan het ene uiteinde te snijden en van spindels te wisselen om het andere te bewerken.
Draden zijn een andere uitdaging. Winkle zei dat er letterlijk honderden soorten zijn en dat de toleranties krap zijn:"Plus 1,5 gij, minus niets." Dat komt omdat in olie en gas draden niet alleen onderdelen bij elkaar houden, "ze moeten perfect afdichten en enorme trekspanningen doorstaan van de gigantische reeks onderdelen die kilometers diep in het gat gaan", zei Winkle. “En ze hebben te maken met thermische uitzetting en schokbelasting. Deze afdichtende en dragende component bestaat in geen enkele andere industrie.”
Het snijden van deze draden vereist een stevige machine en een opstelling die bestand is tegen klapperen. Kyle Downs, directeur projectmanagement en marketing voor SMW Autoblok, Wheeling, Illinois, zei dat dit allemaal gecompliceerd wordt door het feit dat “inkomend materiaal erg inconsistent is. Het automatiseren van het centreren van gehaakte, gebogen en/of langwerpige buizen kan worden bereikt met twee scenario's, ofwel een 3+3 automatisch centrerende en compenserende boorkop, of een compenserende boorkop en een op de losse kop gemonteerde centreeroplossing, die meestal ook een boorkop is .”
Ten slotte voegt de toevoeging van lasermetaalafzetting aan metaalverwijderingsmachines nieuwe mogelijkheden toe, zoals geïllustreerd door Okuma's nieuwe LASER EX-serie. Als u bijvoorbeeld een onderdeel had met slechts een paar uitstekende kenmerken, zou u die kenmerken aan het hoofdgedeelte kunnen toevoegen in plaats van de kenmerken uit een grotere voorraad te halen. Dat is potentieel een enorme besparing in bewerkingstijd.
Winkle voegde eraan toe dat je ook verschillende materialen kunt samensmelten, bijvoorbeeld door Inconel en roestvrij staal te combineren, wat "nooit mogelijk is met puur subtractieve technologie. Het gewricht is net zo sterk of sterker dan wanneer het uit massief zou worden gefreesd,” zei hij.
Dat heeft onmiddellijk potentieel in olie en gas voor het toevoegen van de slijtplaten die nodig zijn op boorassemblages of voor het toevoegen van de zijvinnen die worden gebruikt om te voorkomen dat pijp de binnendiameter van een putmantel schraapt terwijl deze door een bocht in een gerichte put beweegt. Okuma biedt ook de mogelijkheid om een zone van materiaal tot ongeveer 50 Rockwell te harden met dezelfde laser met een ander diafragma.
Automatisering Besturingssysteem
- Nieuwe certificering voor de Lubrication Elite
- Pleidooi voor neuromorfe chips voor AI-computing
- Een nieuwe kijk op slimme productie voor het nieuwe normaal
- Als data de nieuwe olie is, wie is dan uw raffinaderij?
- Voor supply chains is klantervaring de nieuwe onderscheidende factor
- Uw supply chain toekomstbestendig maken voor het nieuwe normaal
- De pandemie leidt tot een nieuw model voor besluitvorming in de toeleveringsketen
- De nieuwe golf van uitdagingen voor fabrikanten van industriële apparatuur
- Top 5 Stromag-onderdelen voor uw booreiland
- De juiste machineonderdelen vinden:advies voor ingenieurs
- Bedankt voor de herinneringen!