Een 3D-geprinte Tesla-turbine ontwerpen — deel 2
Inleiding
Dit is de tweede aflevering van een tweedelige serie waarin de aanpassing van een machinaal bewerkte Tesla-turbine met Markforged-onderdelen wordt beschreven. In de eerste aflevering introduceerden we Tesla Turbines, bespraken we welke onderdelen zich goed leenden voor 3D-printen en vervingen we de turbinebehuizing door een Markforged onderdeel. Nu gaan we het andere gedrukte onderdeel van onze turbine-retrofit aanpakken:het lagerhuis.
Het Tesla Turbine Lagerhuis
Terwijl het turbinehuis het assamenstel omringt, raakt het het niet aan. In plaats daarvan, een tussenstuk genaamd de lagerbehuizing, bouten op de turbinebehuizing en houdt de asconstructie vast met twee perfect concentrische lagers. Door de rotoren aan de zijkant van het lagerhuis uit te kantelen, zorgden de oorspronkelijke ontwerpers ervoor dat de machinist die het originele onderdeel draaide, gemakkelijk de concentriciteit van de lagergaten kon verifiëren. Dit is van cruciaal belang. Bij 24.000 tpm kan een verkeerde uitlijning in de turbinerotoren leiden tot een catastrofale storing. In het aluminium huis (zoals het oorspronkelijk was bewerkt) was de tolerantie voor elk van deze lagerpassingen +0/-.0004”. Extreem nauwe toleranties zorgen ervoor dat de perspassingen goed zitten zonder zo strak te zijn dat ze de rotatie van het lager belemmeren. Hoewel dit onderdeel kan worden vervaardigd op een Markforged-machine, is het een veel grotere taak dan het turbinehuis.
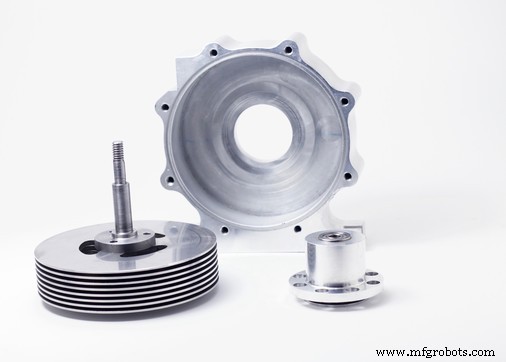
Wijzigingen in ontwerp van additieve fabricage
Hoewel dit onderdeel zeker kan worden afgedrukt, vormt het om een paar redenen een aanzienlijk grotere uitdaging dan het turbinehuis. Ten eerste moeten de lagerpassingen nauwkeurig en concentrisch zijn; de toleranties kunnen echter iets losser zijn vanwege de verminderde oppervlaktehardheid van Onyx. Dit is een verhulde zegen, aangezien het behalen van een tolerantie van +0/-.001” veel realistischer is dan wat vereist is voor aluminium. Ten tweede moesten we zowel borgringgroeven als overhangende flenzen nauwkeurig kunnen printen. Deze beide vereisten aanzienlijk ondersteunend materiaal dat van moeilijk bereikbare plaatsen kon worden verwijderd zonder het onderdeel te beschadigen. Gelukkig kunnen met onze afpelbare steunen gemakkelijk borgringgroeven en flenzen worden bedrukt. Ten derde moesten we aanzienlijke vezels in de onderdelen passen, vooral rond de lagers. Als het onderdeel vervormd zou zijn, zou elke precisie die we bereikten met lagerpassingen teniet worden gedaan. Het onderdeel is groot genoeg om zes vezelringen om elk lager te passen; dit is voldoende ondersteuning.
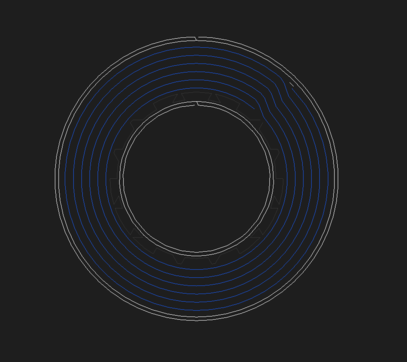
De behuizing afdrukken
Op al onze machines is het mogelijk om krappe toleranties aan te halen. Om het te bewijzen, hebben we besloten om twee versies van het lagerhuis te printen:één op de Mark Two Enterprise en één op de Mark X met laser dimensionale verificatie.
Mark Two Behuizing
Om nauwe toleranties op de Mark Two af te drukken, moeten we onafhankelijk gemeten eenheidstests gebruiken. We hebben unit-tests expliciet besproken in een eerdere blogpost; ze zijn ongelooflijk handig om ons in staat te stellen strakke toleranties te printen zonder een gesloten lusontwerp. Voor het lagerhuis abstraheren we elk van de twee lagerpassingen op ringen en drukken we tests met meerdere eenheden af. Na elke testafdruk van elke eenheid meten we de interne diameter zo nauwkeurig mogelijk (het meten van interne 3D-geprinte cirkels met remklauwen kan behoorlijk moeilijk zijn) en passen we de afmetingen van onze onderdelen aan in CAD. Na twee keer herhalen met elke lagerpassing, nemen we elke nieuwe dimensie op in het volledige onderdeel en drukken het af. Pas na het meten en valideren van het volledige onderdeel proberen we de hardware te plaatsen. Als alles volgens plan werkt, passen de lagers goed op elkaar en kunnen we het lagerhuis op het turbinehuis installeren.
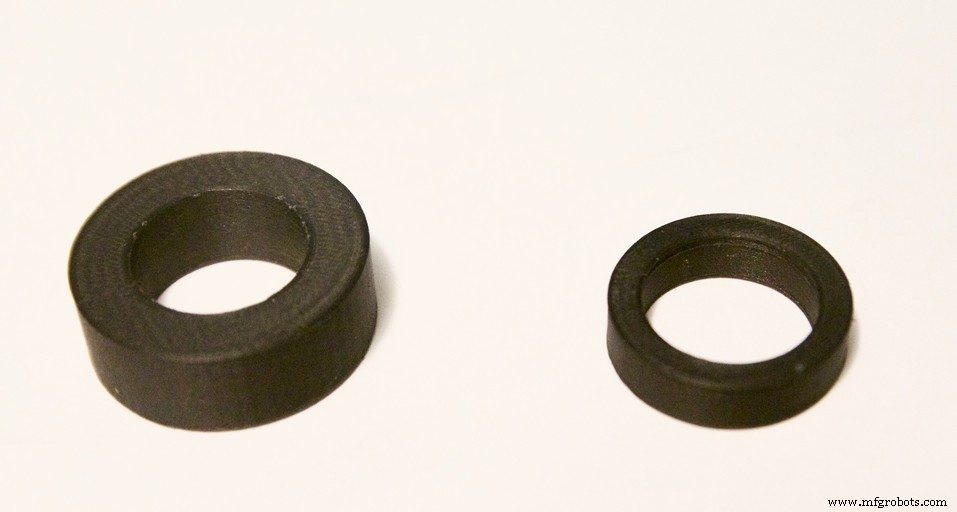
Mark X-behuizing
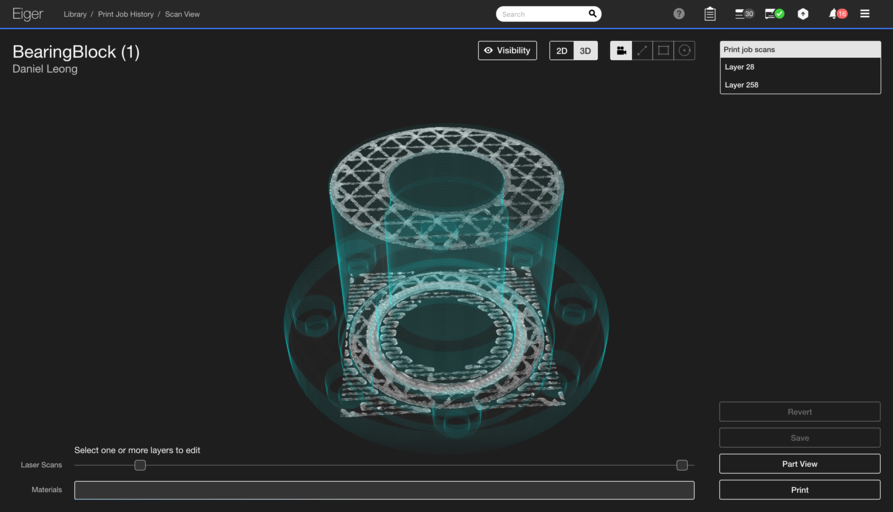
Omdat dimensionale zekerheid op de Mark X nog steeds door mensen wordt gevalideerd, kunnen we niet zomaar een perfect onderdeel afdrukken. De laserdimensionering stroomlijnt ons proces echter enorm. In plaats van unit-tests te gebruiken (die weliswaar geweldig zijn, maar toch het risico lopen de tolerantie niet te verifiëren omdat de unit-test met intolerantie-afmetingen nog moet worden gerepliceerd), printen we het hele onderdeel met een laserscan op lagen die elk van de twee kritische lagerpassingen. Dit stelt ons in staat om tijdens het printen te controleren of elk van de lagers past zonder remklauwen te gebruiken. Hoewel we erin slaagden om beide toleranties bij de eerste poging te bereiken (waardoor een herdruk niet nodig was), zou het missen van een van beide toleranties hebben geleid tot een eenvoudige herdimensionering en herdruk. Deze workflow is hands-off en veel eenvoudiger dan het gebruik van unit tests.
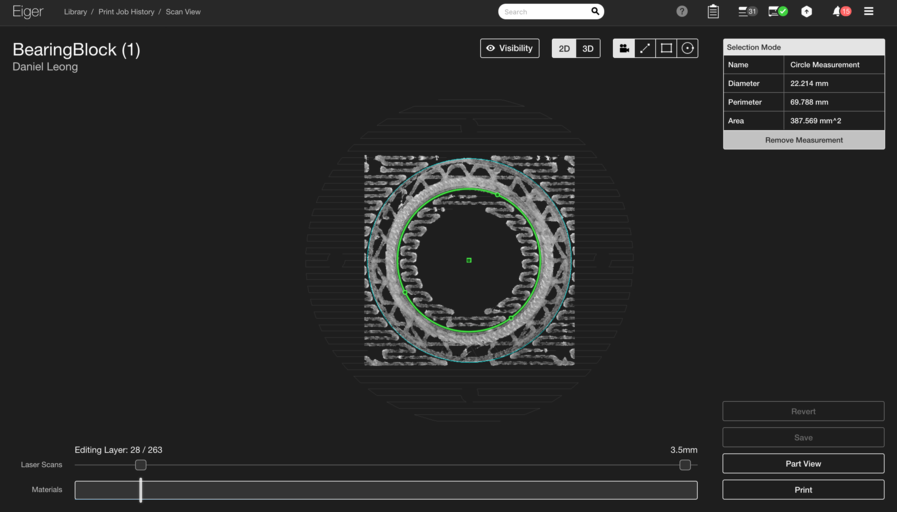
Conclusie
Hoewel complex, bleek de lagerbehuizing een geweldige toepassing van 3D-printen met strikte toleranties. We hebben gevalideerd dat we een functioneel onderdeel konden printen met weinig ontwerpwijzigingen op zowel de Mark Two als de Mark X. Beter nog, de behuizingen werken onderling uitwisselbaar; beide laten de turbinerotor vlekkeloos draaien.
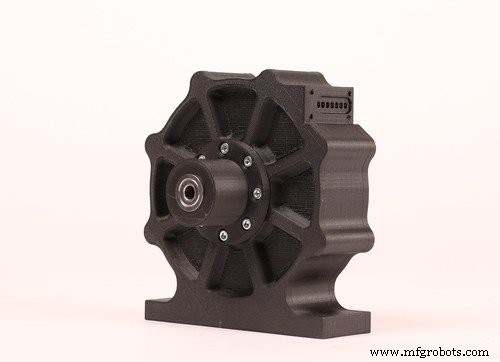
Wilt u meer toepassingen van dergelijke Markforged-machines zien? Volg ons op Facebook, Twitter, Instagram en Linkedin voor meer updates!
3d printen
- De 10 beste tips om te overwegen bij het ontwerpen van uw FDM-onderdeel
- Metalen 3D-printtoepassingen (deel 2)
- Een 3D-geprinte Tesla-turbine ontwerpen – deel 1
- In-process inspectie:3D-geprinte onderdelen verbeteren
- Een deel van de week – 3D-geprinte schokdemper
- Markforged 3D-geprint onderdeel:spoeldispenser
- Een 3D-geprinte drone maken - deel 3
- 3D-geprinte extreme drones
- Maatnauwkeurigheid van 3D-geprinte onderdelen
- Hoe krijg je sterkere 3D-geprinte onderdelen
- Inspectiemethode voor 3D-geprinte onderdelen (deel 3)