Waarom Origin One wordt gebruikt voor productieonderdelen voor 3D-printen
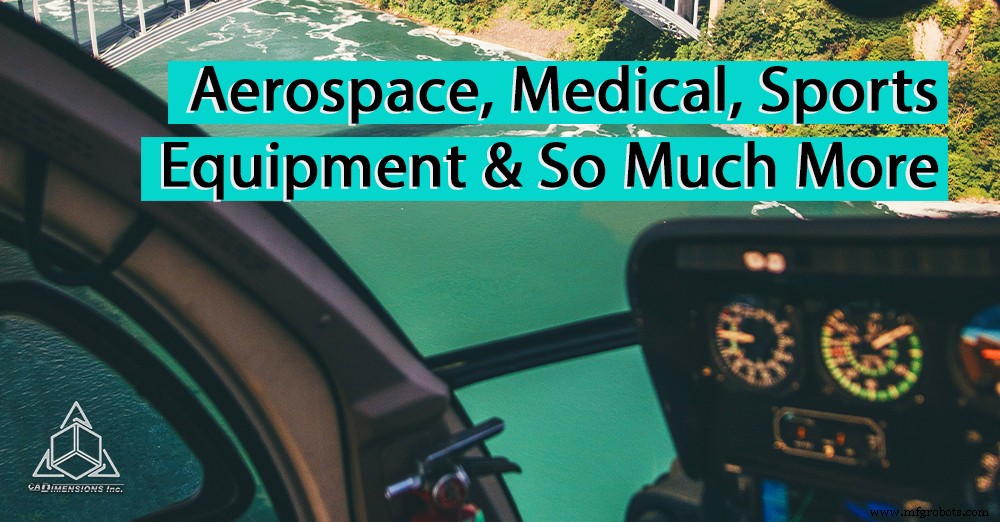
De Origin One is een nieuwe 3D-printer op harsbasis van Stratasys. Het is nu beschikbaar en eenheden zijn begonnen met verzending over de hele wereld. Stratasys is geen onbekende in het printen met harsproductieonderdelen. Hun Polyjet-technologie drukt al jaren zeer gedetailleerde visualisatiemodellen, nauwkeurige en gespecialiseerde winkelhulpmiddelen en medische modellen af. Dit is echter het eerste op btw gebaseerde harssysteem dat wordt toegevoegd aan de Stratasys-portfolio en het heeft een drastisch ander beoogde gebruik.
P3-technologie is geweldig voor productie-onderdelen
De Origin One wordt aangedreven door Programmable Photopolymerization-technologie, of P3. P3 gebruikt een 4K-projector om de hele laag bij elke cyclus gedeeltelijk uit te harden. De onderdelen worden vervolgens volledig uitgehard in een UV-kamer. Het heeft een uniek pneumatisch scheidingsmechanisme dat voorkomt dat onderdelen aan de bodem van het vat blijven kleven, wat een kritieke reden is waarom de Origin One uitblinkt in zowel grote, blokvormige onderdelen als zeer gedetailleerde, ingewikkelde onderdelen. Stratasys werkt samen met grote materiaalfabrikanten zoals DSM en Henkel om een breed scala aan hoogwaardige harsen te leveren. Nieuwe materialen worden voortdurend gecertificeerd door Stratasys en er is een Open Materials-licentie beschikbaar om de machine volledig te ontgrendelen voor onderzoek en testen.
Met supply chain-problemen die in alle sectoren hoogtij vieren, zijn bedrijven op zoek naar een kosteneffectieve, flexibele oplossing om te voldoen aan de steeds veranderende eisen van hun klanten. De Origin One is goed gepositioneerd om deze problemen op te lossen door eindgebruiksonderdelen van productiekwaliteit te leveren in een verscheidenheid aan materialen en een machine die gebruikers volledige controle over hun processen geeft. Meer materialen staan gelijk aan meer toepassingen. Dus hoe gebruiken bedrijven deze krachtige technologie?
Origin One Materials
Momenteel zullen er bij de lancering meer dan 12 materialen beschikbaar zijn, en er zullen er nog meer volgen. De toepassingen van de Origin One kunnen bijna eindeloos lijken. Gebruikers vinden regelmatig nieuwe en unieke manieren om deze machine te gebruiken. Een van de best presterende materialen op het gebied van mechanische eigenschappen is 3955 van het merk Loctite van Henkel. Het heeft een zeer hoge temperatuurbestendigheid (HDT> 300C), een hoge stijfheid en voldoet aan de vlam-, rook- en toxiciteitsnormen voor veeleisende toepassingen in de lucht- en ruimtevaartindustrie. Laten we eens kijken naar een bedrijf dat dit materiaal al gebruikt voor hun eindgebruiksonderdelen:TE Connectivity.
Lucht- en ruimtevaarttoepassing
TE Connectivity ontwerpt en produceert connectoren en sensoren voor ruwe omgevingen. Ze zijn toegewijd aan het creëren van een veiligere, duurzame, productieve en verbonden toekomst door oplossingen te bieden voor elektrische voertuigen, vliegtuigen, digitale fabrieken en slimme huizen. Vorig jaar benaderde een van hun bestaande aerospace-klanten hen met een verzoek dat ze niet wilden laten liggen:connectoren en houders voor een helikopter. Dit verzoek bracht unieke uitdagingen met zich mee, aangezien de connectoren nog nooit eerder waren ontworpen of geproduceerd. De tijdlijn en volumevereisten voor een houder van productiekwaliteit betekenden dat traditionele productiemethoden en ontwikkelingstijdlijnen ontoereikend waren voor zowel TE Connectivity als zijn klant. De materiaalkeuze was een andere hindernis. FDM 3D-printen zou de vereiste mechanische eigenschappen kunnen bieden, zoals hoge hitte- en vlamvertragende eigenschappen, maar zou niet kunnen voldoen aan de nauwkeurigheid van +/- 0,002 inch. Er was maar één oplossing om aan de strenge behoeften van hun klanten te voldoen:de Origin One.
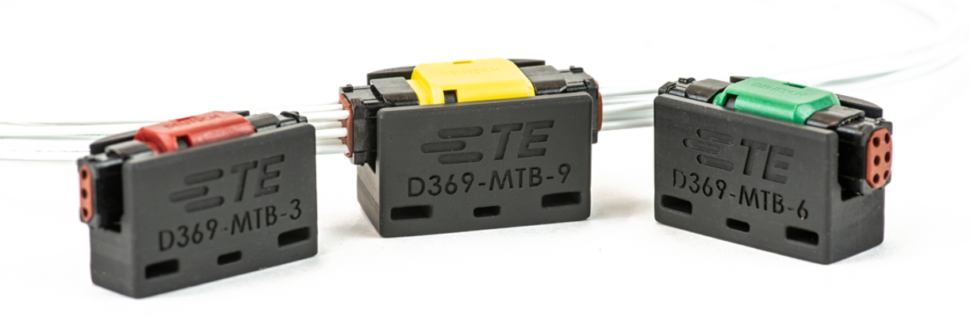
Tegenwoordig zien we dat de hardware, de software en de materialen van Stratasys echt samenkomen om de productieschaal voor ons werkelijkheid te maken. We zijn van mening dat dit ertoe bijdraagt dat TE Connectivity een flexibelere en kosteneffectievere partner wordt voor veel van 's werelds toonaangevende OEM's, in industrieën van auto's tot lucht- en ruimtevaart tot huishoudelijke apparaten, terwijl we werken aan een meer verbonden toekomst.
Mark Savage, Senior Manager, Additive Manufacturing van TE Connectivity
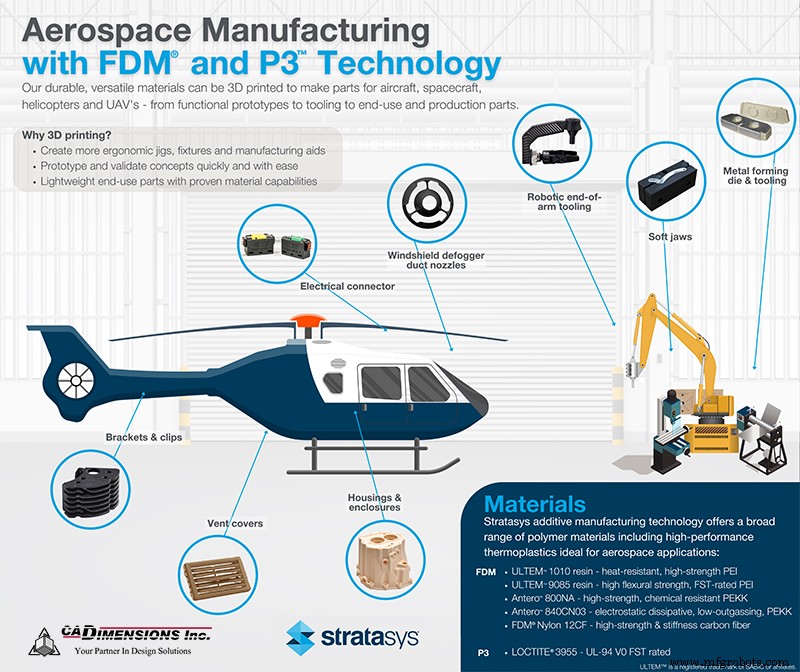
Klik hier om het volledige verhaal te lezen of bekijk de video!
Productieonderdelen voor medische toepassingen
Een andere branche die strenge eisen en voorschriften heeft waar de Origin One aan kan voldoen, is de medische industrie. Momenteel zijn er twee medische materialen van Henkel die kunnen voldoen aan de ISO 10993-5 en -10-normen voor biocompatibiliteit wanneer ze worden verwerkt met behulp van een gevalideerde workflow:MED412 en MED413. MED412 is matig flexibel, taai, heeft een grote slagvastheid en kan worden vergeleken met polypropyleen van medische kwaliteit. MED413 is een veelzijdig technisch materiaal dat het meest lijkt op ABS van medische kwaliteit. Deze materialen ontsluiten vele toepassingen binnen de ontwikkeling van medische hulpmiddelen.
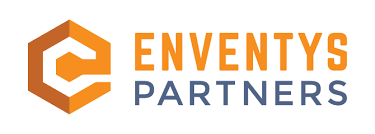
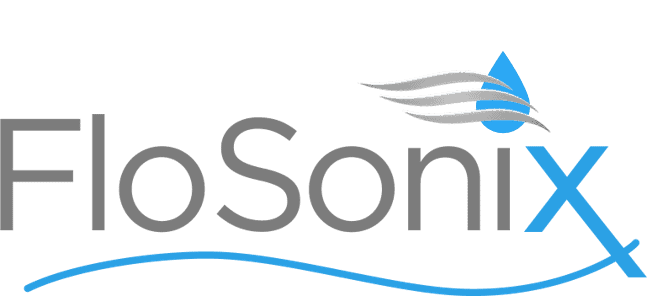
Een bedrijf dat al medische hulpmiddelen voor eindgebruik heeft geproduceerd met een combinatie van Origin-materialen, is Eventys Partners, een full-service productlanceringsbureau dat alle aspecten van productontwikkeling afhandelt. Ze hebben toegang tot verschillende productiemethoden, dus het komt niet vaak voor dat een bedrijf naar hen toekomt met een verzoek dat hun capaciteiten op de proef stelt. FloSonix, een toonaangevend apparaat voor de bestrijding van luizen, benaderde Eventys met een nieuw ontwerp voor een apparaat voor de behandeling van hoofdluis. In eerste instantie was Eventys stomverbaasd. Het handheld-apparaat vereiste biocompatibele en hittebestendige materialen, een lichtgewicht ontwerp en getextureerde handgrepen, allemaal met een esthetisch aantrekkelijk uiterlijk. FloSonix vroeg jaarlijks 200 tot 300 apparaten aan. De uitdaging was dat de onderdeelgrootte, het aantal en de ontwerpcomplexiteit te duur zouden zijn en moeilijk te realiseren met traditionele productiemethoden. Het eenvoudigweg ontwerpen en prototypen van het product zelf zou onbetaalbaar zijn geweest.
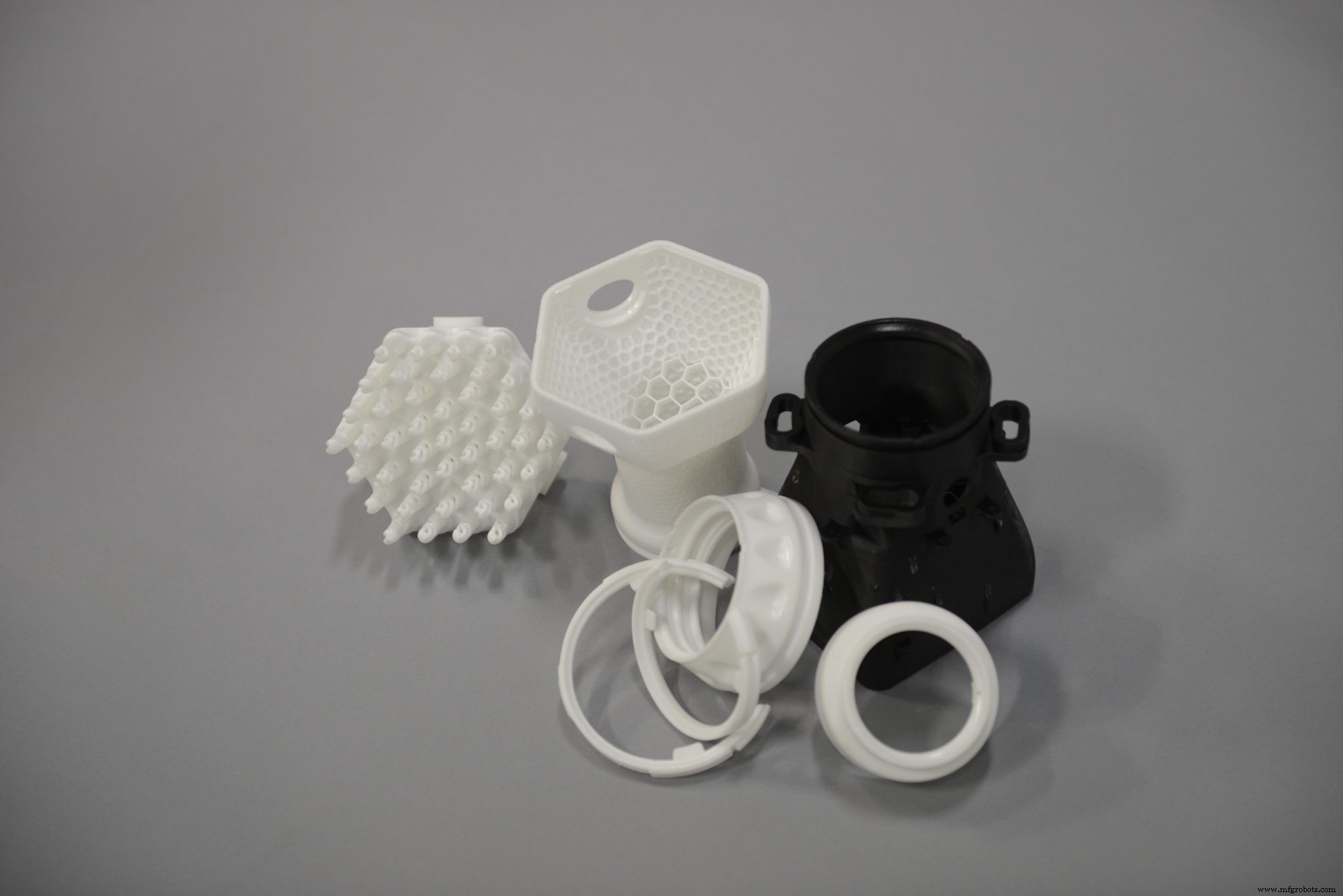
Eventys was dus op zoek naar een oplossing die voldeed aan hun behoeften op het gebied van prototyping en productie voor eindgebruik. Het team was in staat om het FloSonix-handheld-apparaat van idee naar productie te brengen met slechts één Origin One-printer en had slechts één extra printer nodig om aan de jaarlijkse vereiste inventaris van FloSonix te voldoen.
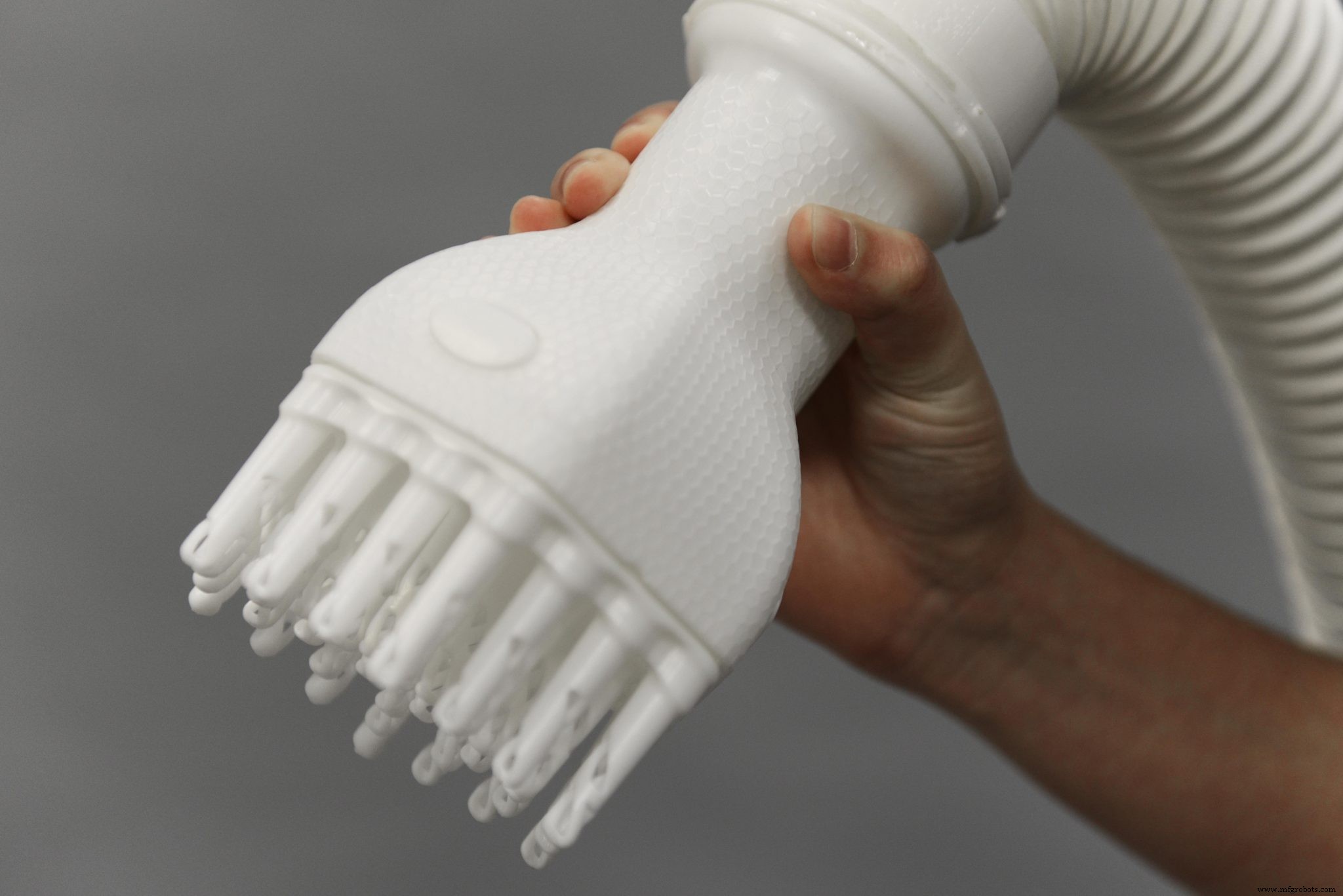
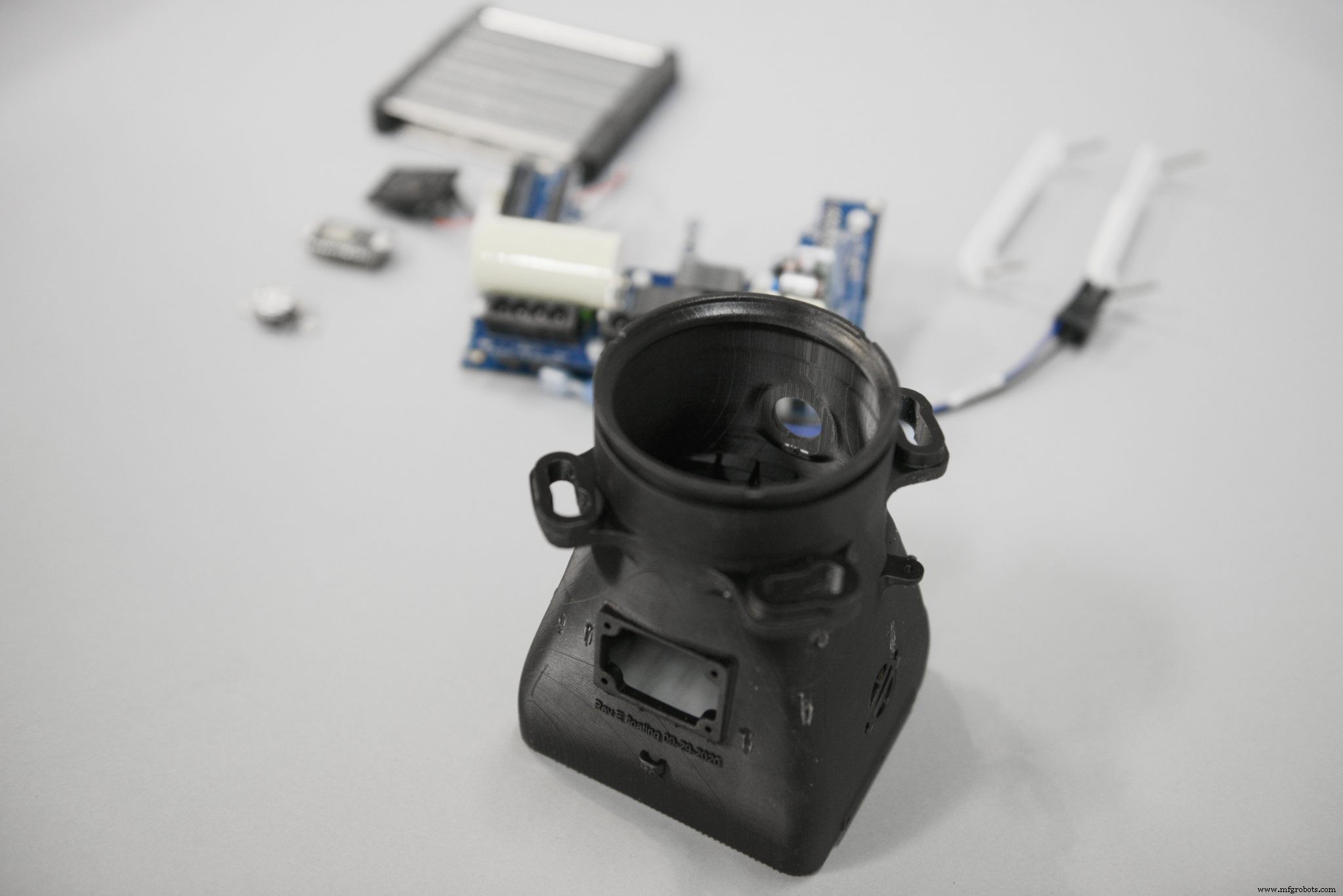
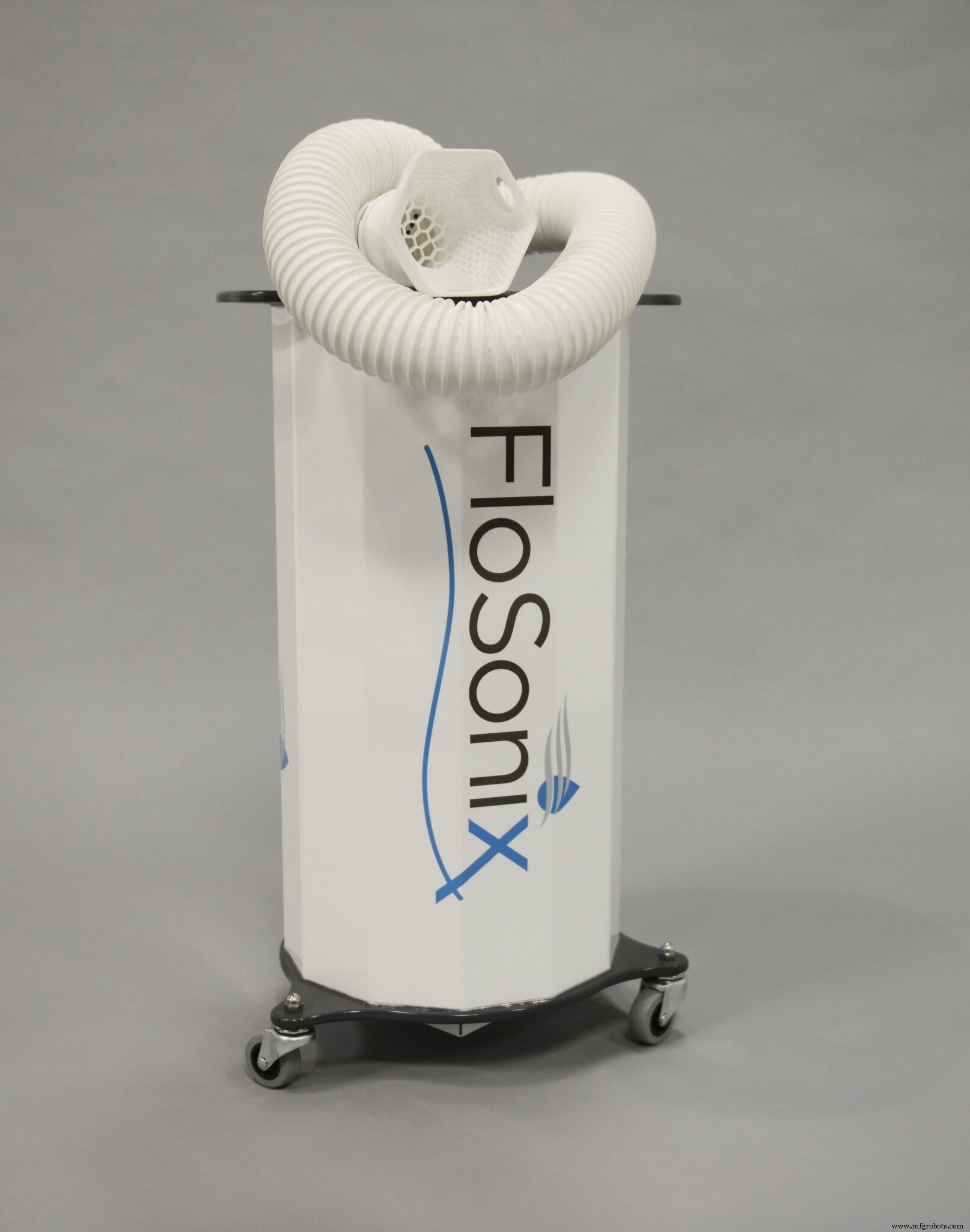
De Origin One heeft ons in staat gesteld om ons niet alleen aan te passen aan veranderende toeleveringsketens, maar onze ontwikkeling in fasen te plannen; zo verfijnen we het product in de toekomst vaak graag, maar niet meteen. Additive manufacturing stelt ons in staat om stapsgewijs te itereren zonder dat we mallen opnieuw hoeven te snijden, opnieuw moeten bewerken of overmatige oude voorraad moeten weggooien; dit bespaarde ons zowel tijd als kapitaal die normaal op het spel zouden staan tijdens herontwerpen.
TJ Root, Senior Design Engineer bij Eventys Partners
Klik hier om het volledige verhaal te lezen!
Productie-onderdelen gedijen in ijskoude omgevingen in sportuitrustingtoepassingen
Bij de Origin One houdt het niet op bij lucht- en ruimtevaart en medisch. Een andere industrie die de waarde van op maat gemaakte, 3D-geprinte onderdelen van productiekwaliteit heeft erkend, is sportuitrusting. Technologische verbeteringen zijn essentieel om het concurrentievermogen in de wereld van sportuitrusting te behouden, maar fabrikanten hebben moeite om gelijke tred te houden met de veranderende eisen van de klant.
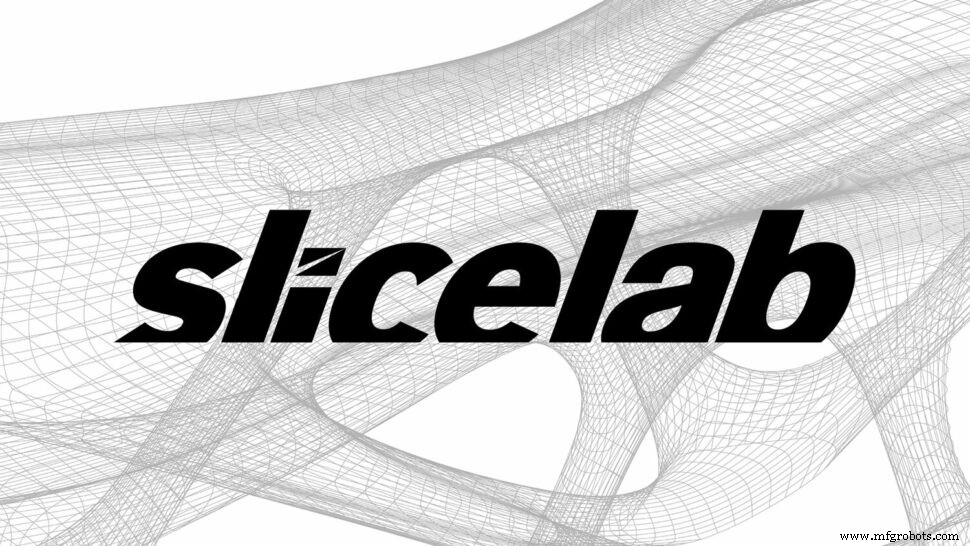
De ontwerpstudio's van Slicelab en f=f gingen, in samenwerking met de teams Stratasys Origin One en Henkel Loctite, de uitdaging aan om een integraal onderdeel van snowboardbindingen opnieuw uit te vinden:de hoge rug. De hoge rug is een stuk van een snowboardbinding die de onderkuit van de rijder ondersteunt, wat hem helpt het snowboard te sturen. Hoe beter het ontwerp van het onderdeel, hoe meer controle de rijder heeft. De Origin One was een duidelijke keuze vanwege zijn vermogen om verlengde bruggen en steile uitsteeksels te printen zonder in te boeten aan kwaliteit. Een interne tralieondersteuningsstructuur maakte een variabele flexibiliteit door het hele onderdeel mogelijk, wat onmogelijk zou zijn om te bereiken met spuitgieten.
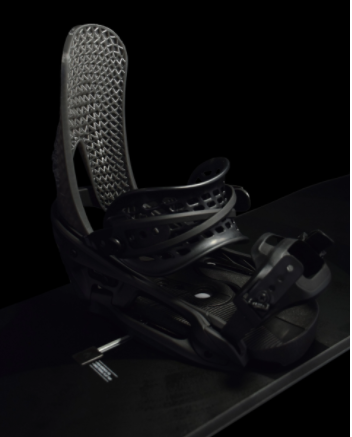
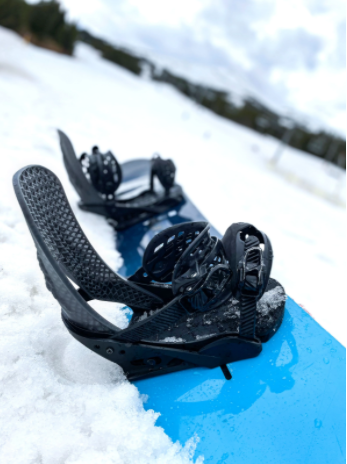
Het materiaalteam van Origin One werkte rechtstreeks samen met Slicelab en f=f om ontwerp-iteraties op te lossen, een perfecte print te garanderen en het juiste high-impact, flexibele, esthetische materiaal te selecteren. Ze gingen voor Henkel Loctite's IND 3172, die een uitstekende slagvastheid en matige flexibiliteit heeft. De echte test was toen een van de oprichters van Slicelab, Diego Taccioli, een van hun hoge ruggen installeerde, de dag ervoor op zijn snowboard printte en de hellingen van Breckenridge Resort in Colorado betrad. Ze presteerden precies zoals gewenst.
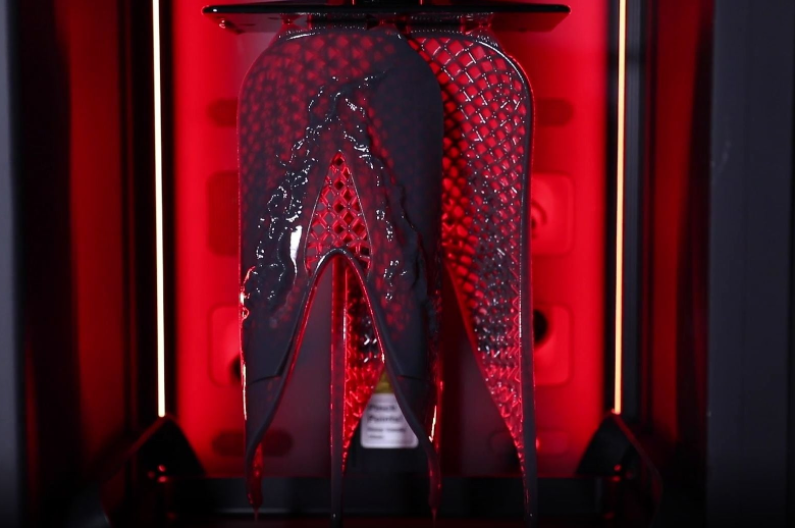
Nu additieve productie is waar het nu is, is het mogelijk om te voorspellen dat er in de toekomst minder hardwarecomponenten of maataanpassingsfuncties in producten hoeven te worden ingebouwd. Door de mechanische eigenschappen van het materiaal in parametrische software in te pluggen, kunnen we eenvoudig een paar inputs aanpassen om geometrie te genereren voor elk type verschil in prestaties waarnaar we op zoek zijn, of het nu een informele dag rijden of een intense poederdag is .
Diego Taccioli, mede-oprichter van Slicelab
Klik hier om het volledige verhaal te lezen of bekijk het afgedrukt!
Extra toepassingen
De bovenstaande casestudy's zijn uitstekende voorbeelden van hoe de Origin One tegenwoordig wordt gebruikt voor productieonderdelen voor eindgebruik, maar de toepassingen reiken ver achter bij die drie. Hier zijn enkele voorbeelden van andere toepassingen, allemaal afgedrukt op de Origin One van Stratasys.
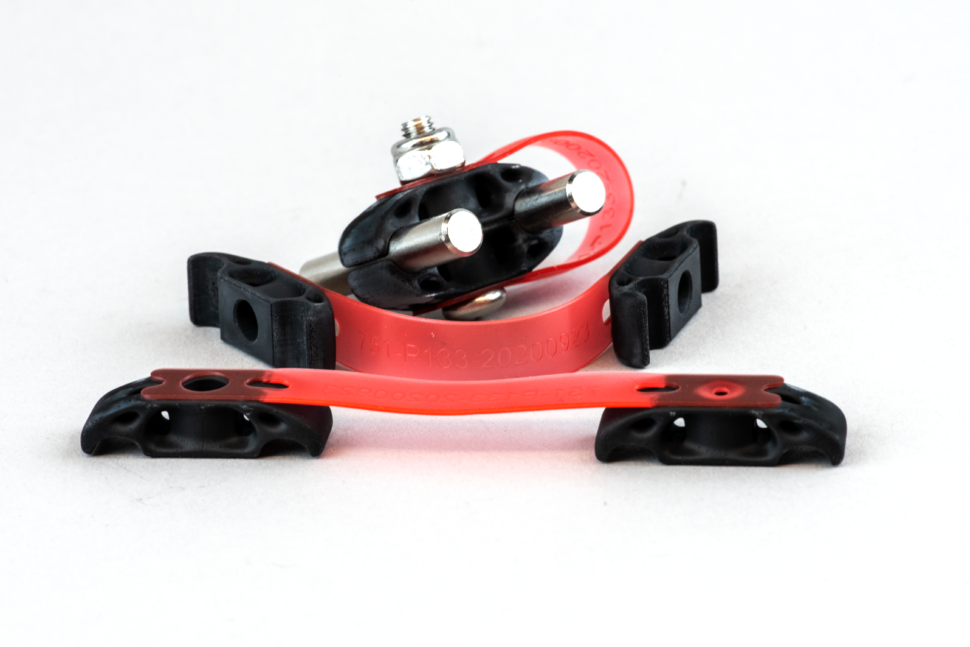
F16 hydraulische kabelklem voor vliegtuigen
Ontworpen als onderdeel van de Advanced Manufacturing Olympics van de US Air Force RSO. Dit onderdeel vereiste een strikte nauwkeurigheid terwijl het bestand was tegen hoge en koude temperaturen, trillingen, ontvlambaarheid en blootstelling aan chemicaliën. Dit ontwerp dat op de Origin One is afgedrukt, is twee keer zo sterk als het origineel en is 5% lichter geworden.
Materiaal: Henkel 3955
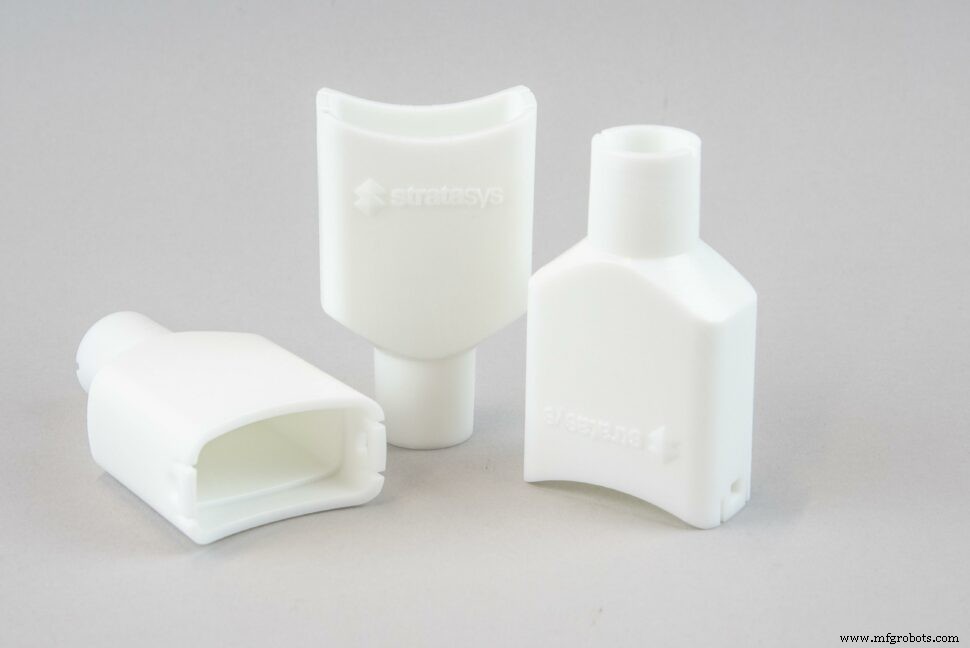
Adapter voor ademhalingsapparatuur
Gebruikt om de luchtstroom in een ademhalingsapparaat te bevorderen en vereiste biocompatibele eigenschappen. Het wereldwijde tekort aan beademingsapparatuur als gevolg van COVID-19 zorgde voor een grote vraag naar kritieke productieonderdelen met korte doorlooptijden.
Materiaal: Henkel MED413
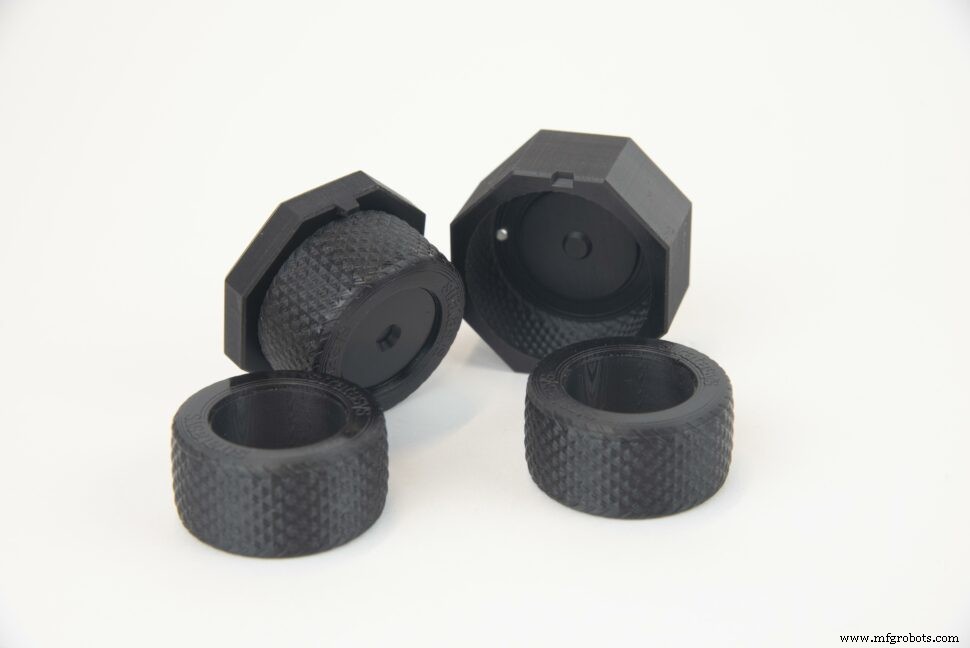
PU-wielvorm
Vorm voor een wiel van elastomeer polyurethaan, compatibel met een verscheidenheid aan lossingsmiddelen en urethaanchemicaliën, vormen hebben meer dan 1.500 onderdelen geproduceerd (en nog steeds) zonder schimmeldegradatie.
Materiaal: Henkel IND403
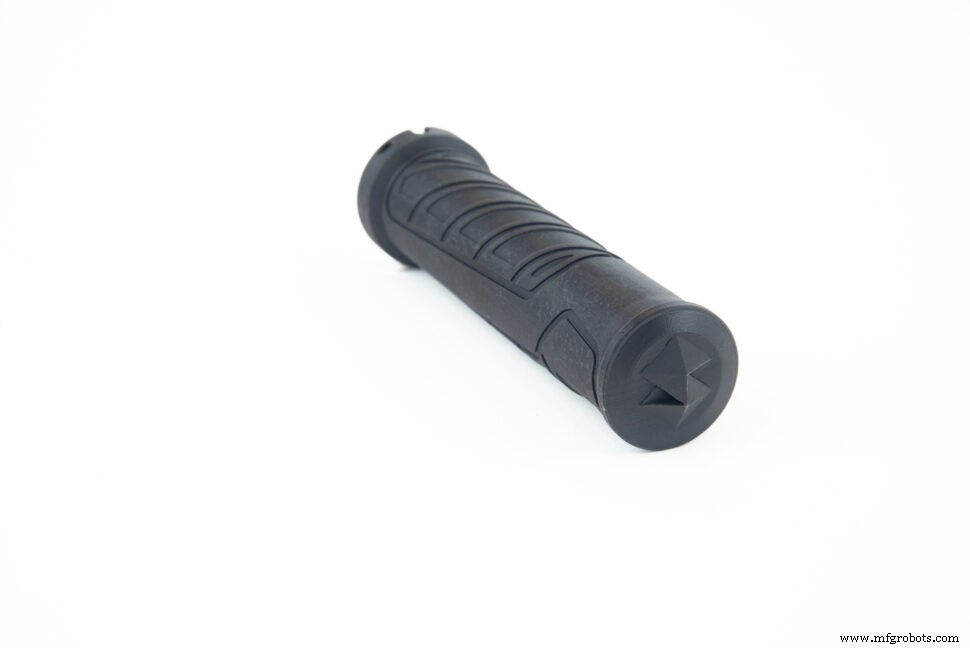
Greep fietsstuur
Stuurgrip die schokabsorptie, flexibiliteit en dempingseigenschappen vereist om de mechanische schokken en trillingen te absorberen die optreden tijdens het fietsen in een duurzaam, UV-stabiel materiaal.
Materiaal: Henkel IND402
The Bull Rider:90% van de productie-onderdelen zijn 3D-geprint op de Origin One
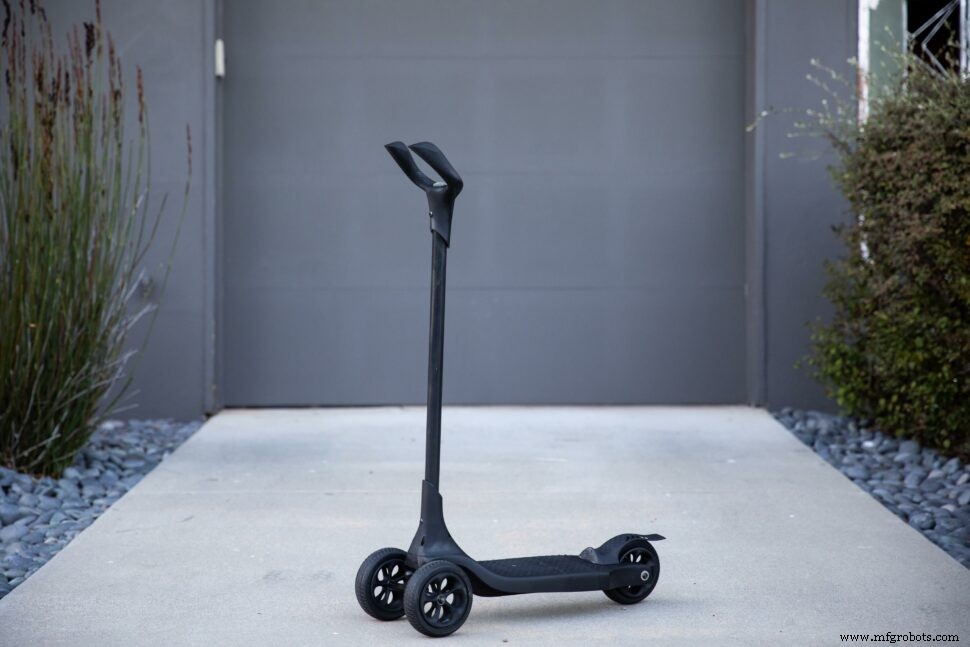
En tot slot, een van mijn persoonlijke favoriete projecten die tot nu toe uit de Origin One komen, de Bull Rider. Het nieuwe Stratasys Dura56-materiaal van Loctite werd op de proef gesteld om een functionele, duurzame kickscooter te creëren waarbij meer dan 90% van de massa van de scooter uit 3D-geprinte onderdelen bestaat. Het Origin One-team werkte samen met Slicelab en in slechts 81 dagen gingen ze van de eerste brainstorm, drie iteraties en creëerden vervolgens met succes een afgewerkt product. Alle onderdelen werden in minder dan 48 uur geprint met 3 printers.
Bekijk deze infographic voor meer informatie, of bekijk de video om hem in actie te zien!
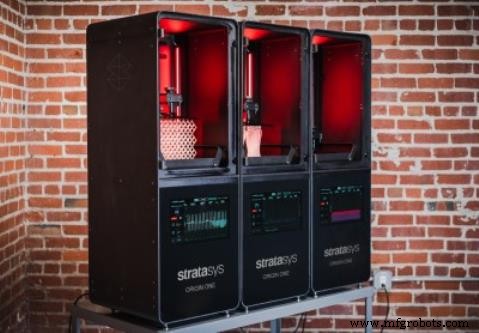
Behaal een uitzonderlijke nauwkeurigheid.
Lees meer over deze geweldige technologie en bereik een uitzonderlijke afdrukkwaliteit
Oorsprong Een3d printen
- Waarom CT-scanning een belangrijk onderdeel wordt van succesvol 3D-printen
- Emiraten adopteren 3D-printtechnologie voor vliegtuigonderdelen
- Is 3D-printen klaar voor de productie van eindonderdelen?
- Nabewerking voor industrieel 3D-printen:de weg naar automatisering
- Waarom is 3D-printen zo aantrekkelijk voor investeerders?
- Applicatie Spotlight:3D-printen voor turbineonderdelen
- Waarom 3D-printen en software cruciaal zijn voor digitale transformatie
- Waarom glasvezeldoek wordt gebruikt voor het maken van surfplanken
- Stratasys Origin One:een 3D-printer voor productieonderdelen
- 10 waterbestendige opties voor uw 3D-geprinte onderdelen:materialen en nabewerking
- Traceerbaarheidspraktijken voor de productie van onderdelen voor precisiebewerking