Swinburne University en CSIRO's Industry 4.0 Testlab for Composite Additive Manufacturing
Swinburne University of Technology (Melbourne, Australië) richt een Industry 4.0 Testlab op voor de fabricage van composietadditieven in samenwerking met het Australische National Science Agency, de Commonwealth Scientific and Industrial Research Organization (CSIRO, zie "Developing hogere kwaliteit, hogere sterkte, lagere kosten koolstofvezels"). De faciliteit is momenteel in aanbouw op de Clayton-site van CSIRO en zal in oktober 2020 worden voltooid.
Dit Industry 4.0-testlab voor composieten, ondersteund door de Australische federale overheid, is een van de zes in een Australisch nationaal netwerk, vergelijkbaar met het Labs Network Industrie 4.0 in Duitsland. Dit Testlab is de eerste nationale faciliteit in het op de staat gebaseerde netwerk waar het doel is om kleine en middelgrote ondernemingen (MKB's) in staat te stellen nieuwe technologieën en bedrijfsmodellen gecreëerd door Industry 4.0 te testen, waarbij aspecten van ontwerp tot economische haalbaarheid worden onderzocht, in een pre-competitieve omgeving met minimaal technisch en financieel risico. Elk Testlab heeft een onderscheidende productfocus. Voor Swinburne is dit additive manufacturing van composieten.
"Het Industry 4.0 Testlab for Composites in Swinburne zal een proces op proefschaal bieden om de productiecapaciteiten van Australië te verbeteren", zegt Bronwyn Fox, plaatsvervangend vice-kanselier van onderzoek en onderneming aan de Swinburne University. Fox kwam in 2015 bij Swinburne, aanvankelijk als directeur van Factory of the Future en vervolgens als directeur van het Manufacturing Futures Research Institute van de universiteit. Voordat ze bij Swinburne kwam werken, was ze onderzoeksdirecteur voor Carbon Nexus aan de Deakin University.
"Swinburne's Testlab zal de kenmerken van de productie van digitale composieten demonstreren in een immersieve omgeving", zegt Fox. “De processen op proefschaal zullen digitaal worden aangestuurd vanaf het ontwerp en de optimalisatie van het onderdeel tot aan het eindproduct. We zullen ook een digitale tweeling van het proces creëren en de grenzen van virtuele inbedrijfstelling verleggen.”
Deze composiet 4.0 hub wordt gehuisvest in een nieuw, op maat gemaakt gebouw. "Het gezamenlijke CSIRO/Swinburne Testlab is gericht op een wereldwijd eerste proces voor additive manufacturing van koolstofvezelversterkte composieten op industriële schaal", zegt Dr. Marcus Zipper, uitvoerend directeur van de Future Industries-divisie van CSIRO. "Dit maakt de locatie, in het hart van Clayton's additive manufacturing-gebied, uitstekend geschikt. Bij CSIRO draait alles om het creëren van kansen voor het mkb en het bredere innovatie-ecosysteem, en dit testlab is daar nog een voorbeeld van.”
Partners en proces
Er zijn veel belangrijke partners in het Industry 4.0 Testlab for Composites, met Siemens Australia (Bayswater, Victoria) was een van de eersten die in 2017 een subsidie voor digitaliseringssoftware van $ 135 miljoen aan Swinburne verleende. Dit biedt het Composites 4.0 Testlab een reeks geavanceerde PLM-software (product lifecycle management) en de Siemens cloudgebaseerde, open Internet of Things (IoT)-platform, MindSphere.
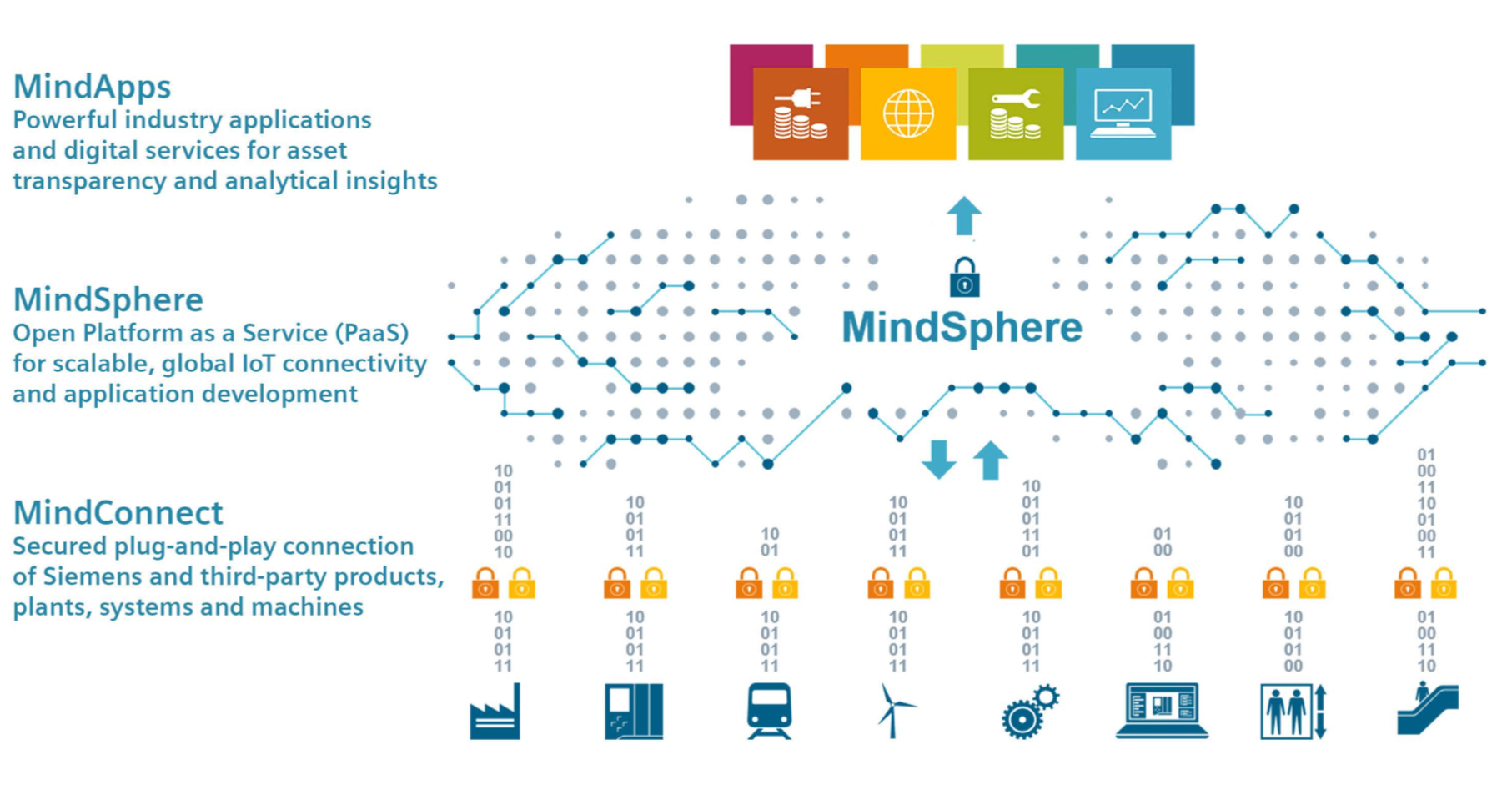
Volgens een presentatie van Siemens Australië waren er in augustus 2019 ongeveer 500 digitale apps/aanbiedingen binnen MindSphere en 1,4 miljoen aangesloten apparaten en systemen. "MindSphere stelt apparatuur van een breed scala aan fabrikanten in staat om met elkaar te communiceren", legt Fox uit in haar ICCM22-presentatie, "An Industry 4.0 Approach to the 3D Printing of Composite Materials". Dit artikel beschrijft hoe het Swinburne Industry 4.0 Testlab zal functioneren:
“Sensoren … stellen elke fase van de productielijn in staat om een grote hoeveelheid procesgegevens te verzamelen. Deze informatie wordt opgeslagen in een beveiligde lokale cloud en wordt ook onmiddellijk gebruikt om productiegegevens door te sturen en terug te koppelen naar andere machines in de lijn, waardoor een zichzelf aanpassend productieproces mogelijk wordt.
De voorgestelde lijn ... is ontworpen om productinspectie na elke fase van het productieproces mogelijk te maken. Ook worden de inspectiegegevens in de lokale cloud opgeslagen. Analyse van de grote datasets die in de cloud zijn opgeslagen, kan leiden tot de ontdekking van nieuwe en onverwachte correlaties tussen de staat van het eindproduct en de parameters van verschillende stadia van het productieproces, die op hun beurt kunnen worden gebruikt om het product te optimaliseren.”
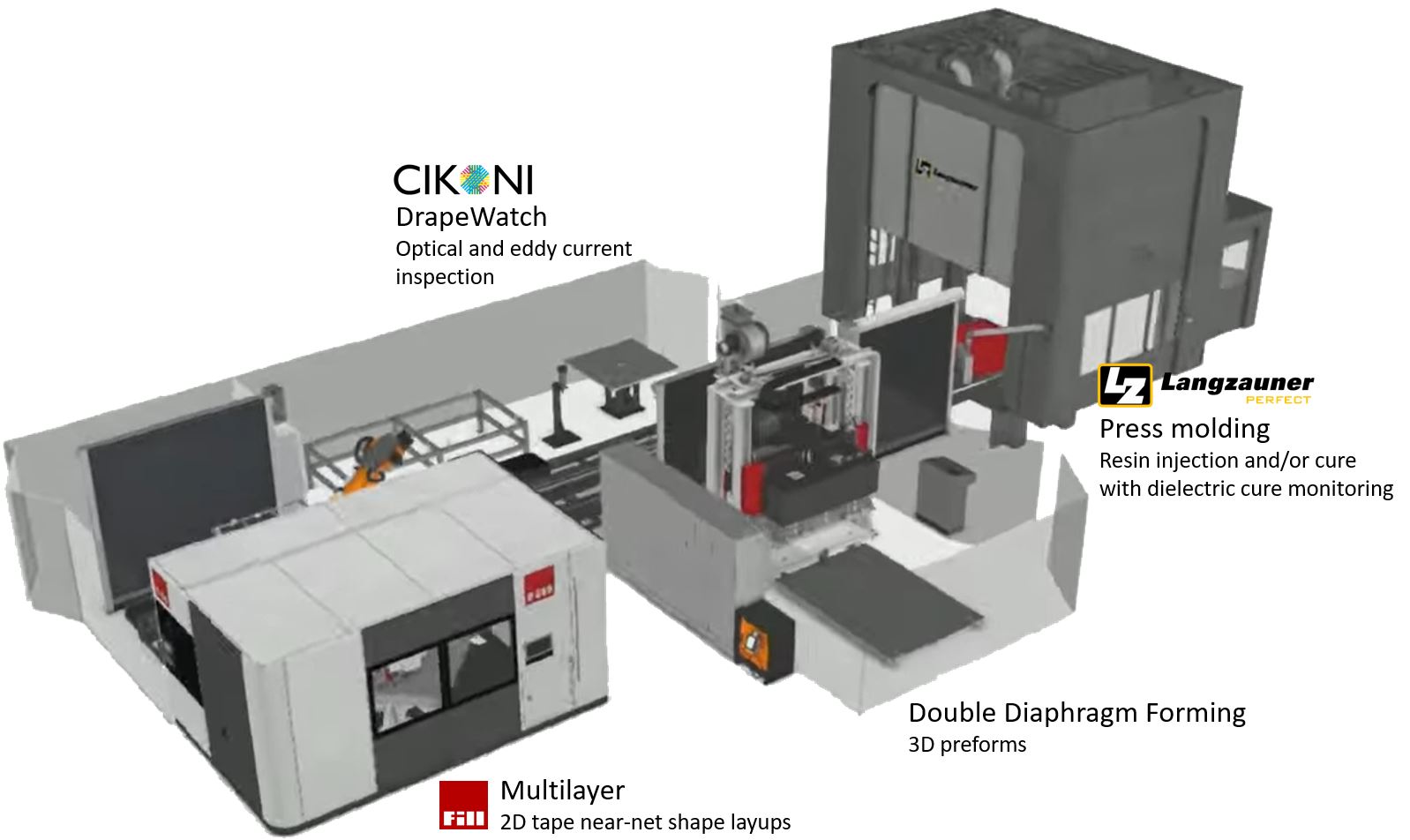
Fox wijst er ook op dat Industrie 4.0 composietproductielijnen niet kant-en-klaar kunnen worden gekocht. Zo ontwikkelde Swinburne een netwerk van leveranciers en eindgebruikers om het ontwerp en de ontwikkeling van zijn Composites 4.0 Testlab-apparatuur en -faciliteit te informeren. Partners die belangrijke componenten leveren, zijn onder meer:
VUL (Gurten, Oostenrijk) heeft het meerlagensysteem geleverd, dat nauwkeurig gesneden en georiënteerde, unidirectionele vezeltapes stapelt in bijna netvormen tot 1,6 bij 1,6 meter groot. Bijna netvormen die tape gebruiken, verminderen het schroot van meer dan 60% tot minder dan 10%. De banden worden vanaf spoelen op een roterende tafel gelegd, waarbij elke 15 seconden een laag wordt aangebracht. Fox merkt op dat Fill's Multilayer-machine tapes van thermohardende prepreg en towpreg kan opleggen, evenals droge vezels en thermoplast met een laag smeltpunt, zoals polyamide (PA). Er is lopende R&D voor hoogsmeltende thermoplasten zoals polyetheretherketon (PEEK) en polyetherketonketon (PEKK). "De Multilayer-machine maakt ook hybride materialen mogelijk, zoals het mengen van glas- en koolstofvezels en blends met natuurlijke vezels, enz.", voegt ze eraan toe.
Quickstep (Sydney, Australië) is de grootste onafhankelijke fabrikant van geavanceerde composieten van luchtvaartkwaliteit in Australië en biedt uitgebreide expertise in zowel autoclaaf-uitgeharde als uit autoclaaf (OOA) composieten. Het gepatenteerde OOA-systeem van Quickstep, Qure, en de hoogwaardige versie voor lucht- en ruimtevaarttoepassingen, AeroQure, is een geavanceerd fabricageproces voor composieten dat aanzienlijke voordelen biedt ten opzichte van traditionele productietechnieken zoals uitharden in een autoclaaf, waaronder:
- Lage kapitaalkosten voor installatie
- Aanzienlijk kortere uithardingscyclustijden
- Verlaagd energieverbruik
- Ontwerpflexibiliteit om de materiaaleigenschappen van het eindproduct te halen of te verbeteren
- Mogelijkheid om complexe geïntegreerde onderdelen te produceren.
Qure gebruikt een circulerende warmteoverdrachtsvloeistof (HTF) onder druk om de mal te ondersteunen en het onderdeel snel te verwarmen en af te koelen. Verwerking met lagere druk (vacuüm plus tot 2,5 bar) maakt gereedschap tegen lagere kosten mogelijk. Snelle verwarming van de mal en het materiaal vermindert de procesviscositeit, waardoor de luchtafgifte en de vezelbevochtiging worden verbeterd. Lagere viscositeit verbetert de hechting aan honingraat- en schuimkernen, wat resulteert in een hogere afpelsterkte en minder kernverplettering bij het uitharden. De HTF zorgt voor superieure thermische controle, zelfs voor dikke laminaten die vatbaar zijn voor exotherme reacties.
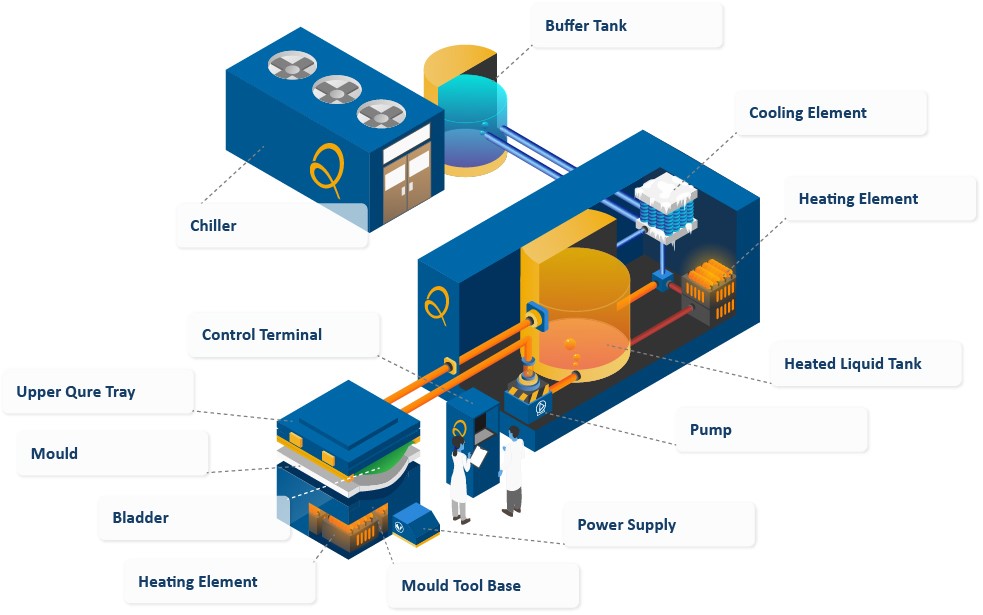
Langzauner (Lambrechten, Oostenrijk) levert een geautomatiseerde pers voor hoge temperaturen met een klemkracht tot 300 ton die geschikt is voor meerdere processen - van variaties van harsoverdrachtgieten (RTM) tot thermovormen. Het maakt injectie van hars in droge voorvormen mogelijk, gevolgd door uitharden of persvormen van thermohardende en thermoplastische prepregs.
De pers bereikt energie-efficiëntie/-besparingen via servohydrauliek en de hoogste nauwkeurigheid, zelfs bij asymmetrische belasting, door middel van een enkele zuigerbesturing. Een hoogwaardige infrarood (IR) oven verwarmt materialen snel tot de gewenste verwerkingstemperatuur en compenseert verschillende diktes met behulp van een individueel regelsysteem voor radiatoren. Een snelle overdracht van het voorverwarmde materiaal naar het persstation wordt verzekerd door een lineaire as. Het hogetemperatuurplaatverwarmingssysteem kan onderdelen vormen bij temperaturen tot ten minste 400 °C, waardoor geavanceerde thermoplasten zoals polyetheretherketon (PEEK) kunnen worden verwerkt.
De pers is ook geschikt voor dubbelmembraanframes (zie 2020-blog over dubbelmembraanvorming). De hoogste mate van digitalisering en monitoring wordt gegarandeerd door flexibele, robuuste en gebruiksvriendelijke software.
NETZSCH (Selb, Duitsland) zal in-mold uithardingsbewakingstechnologie leveren, waardoor de composietproductie kan worden gecontroleerd op basis van materiaalgedrag.
Plataine (Israël) biedt digitaliserings-, optimalisatie- en digitale tweelingsoftware voor de fabricage van composieten die het mogelijk maakt om gereedschappen, onderdelen en grondstoffen te volgen, digitale tweelingen te creëren en machinesensorgegevens te analyseren om de productie van onderdelen te optimaliseren. Plataine heeft een breed scala aan samenwerkingsverbanden met leiders en leveranciers in de composietindustrie, waaronder Siemens.
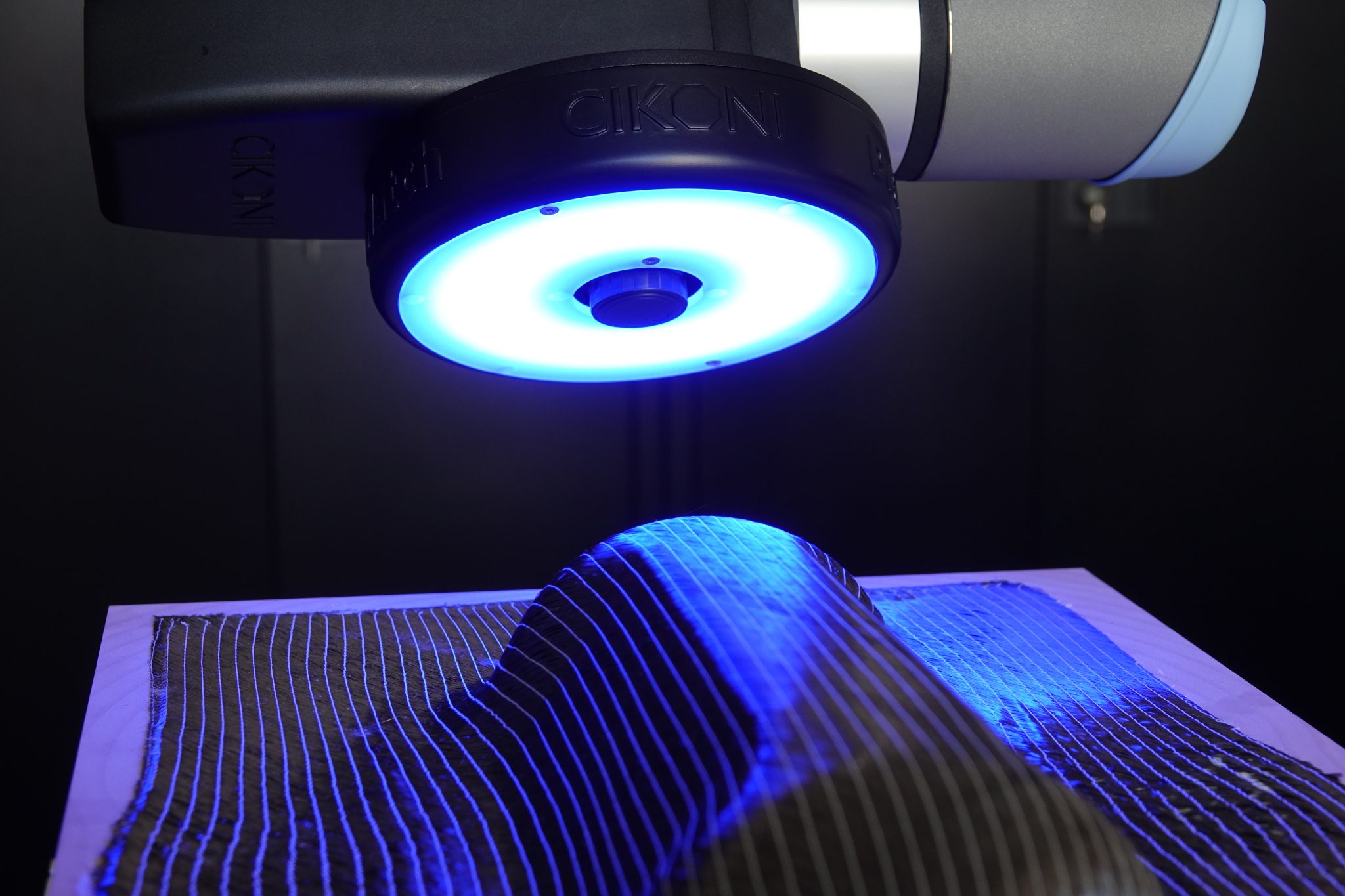
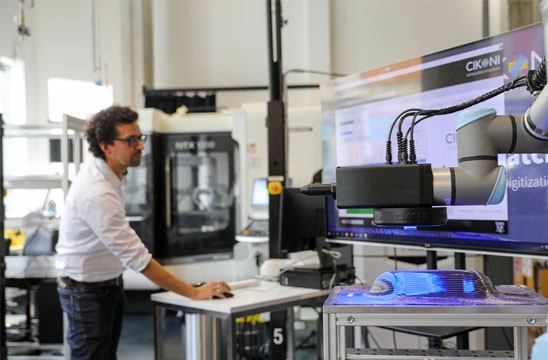
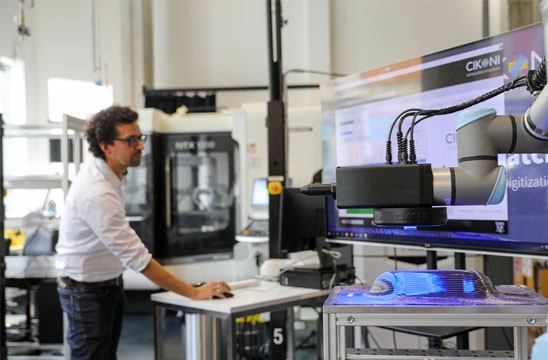
CIKONI (Stuttgart, Duitsland) heeft het DrapeWatch-systeem geleverd voor inline inspectie en digitalisering van zowel preforms als geconsolideerde onderdelen. Dit robotgebaseerde 3D-analysesysteem kan hiaten, verkeerde uitlijningen en onregelmatigheden identificeren. Het combineert een visuele sensor voor gedetailleerde oppervlakte-inspectie met een EddyCurrent-sensor voor interne defecten en diepgaande materiaalanalyse. Gegevens worden geanalyseerd door de kunstmatige intelligentie-algoritmen van het systeem om vroegtijdige detectie van defecten te bieden en dure herhalingen te voorkomen. Een interface naar eindige-elementenanalyse (FEA) maakt export van vezelhoekresultaten naar simulatiemodellen mogelijk voor evaluatie van de impact van defecten op de prestaties van onderdelen. Het modulaire systeem kan ook worden uitgebreid door de integratie van thermografie-, ultrasone of laserscanapparatuur.
Medio 2020 wordt de apparatuur van Fill en Langzauner geïnstalleerd. "Fill heeft experimenten voor ons gedaan", merkt Fox op, "en we hebben personeel naar Oostenrijk gestuurd voor training op bepaalde onderdelen en voor training in digitalisering. Zodra alle procesapparatuur in gebruik is genomen, zullen we de RFID-technologie (radiofrequentie-identificatie) van Plataine gebruiken en opschalen naar het nieuwste edge computing-platform, PlataineEdge, dat realtime analyse en communicatie tussen machines mogelijk zal maken.”
Een ander onderdeel van de visie voor Swinburne's Composites 4.0 Testlab is om flexibele productie mogelijk te maken die zich zeer snel kan aanpassen aan veranderende eisen van de industrie:
“In een typische productielijn vereist een productwijziging of -aanpassing aanzienlijke aanpassingen aan de apparatuur en handmatige interventies. Om een dergelijke productverandering winstgevend te laten zijn, is dus een minimale batchgrootte van het nieuwe product vereist. In de Industry 4.0-visie daarentegen maken slimme fabrieken het mogelijk om individuele klantvereisten en zelfs eenmalige artikelen winstgevend te produceren. Zo'n fabriek kan namens de klanten en leveranciers gemakkelijk inspelen op last-minute wijzigingen. Een van de belangrijkste doelstellingen van de voorgestelde productielijn is dan ook om verschillende producten te kunnen produceren met minimale of geen handmatige tussenkomst.” — Fox en Subic, "An Industry 4.0 Approach to the 3D Printing of Composite Materials"
ARENA2036 en links naar wereldwijde waardeketens
Naast het leveren van een gedigitaliseerde fysieke composieten 4.0-fabriek, zal Swinburne ook het personeel van de volgende generatie opleiden. Dit laatste wordt mogelijk gemaakt door een subsidie van $ 1 miljoen per vier jaar van het Global Innovation Linkages Program van Australië. Een belangrijke partner in dit initiatief is ARENA2036, het industriegedreven, on-campus R&D-programma van de Universiteit van Stuttgart, dat zichzelf omschrijft als "Het zeer flexibele onderzoeksplatform voor mobiliteit en productie van de toekomst". Ondersteund door het federale ministerie van Onderwijs en Onderzoek (BMBF, Bonn, Duitsland) en gerund als een geregistreerde vereniging met 38 leden uit de wetenschap en industrie, beschikt ARENA2036 over een "STARTUP AUTOBAHN" en een gebouw van 10.000 vierkante meter, waarvan 4.700 vierkante meter is een open productiehal met een 16 meter hoog plafond en een industriële kraan van 10 ton. Swinburne is lid geworden van ARENA2036 in 2018.
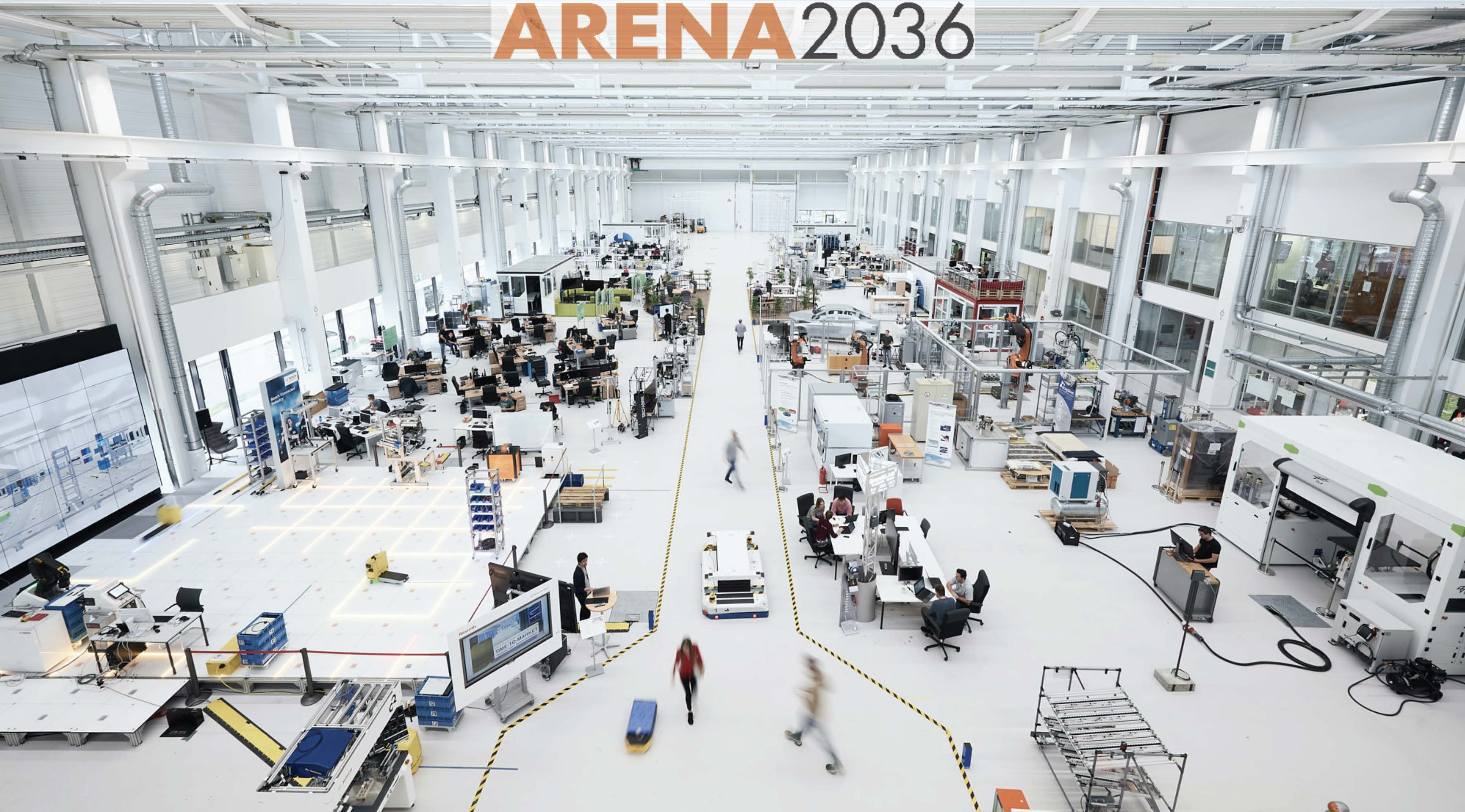
Swinburne's Composites 4.0 Testlab en ARENA2036 werken samen via een programma van 3,6 miljoen dollar, ondersteund door de Global Innovation Linkage (GIL)-regeling van de Australische regering voor de productie van Industrie 4.0 van grootschalige, lichtgewicht composieten met een focus op een specifieke productietechnologie die mogelijk wordt gemaakt door flexibele gereedschapssystemen en digitale tweelingtechnologie. Het bevat:
- R&D en commercialisering, het faciliteren van gezamenlijke start-ups.
- Gezamenlijke werving, co-supervisie en uitwisseling van promovendi
- Gezamenlijke onderzoeksworkshops en symposia.
Deze samenwerking voorziet ook in gezamenlijke R&D-projecten met het Fraunhofer Institute for Manufacturing Engineering and Automation en het Institute for Industrial Engineering (Fraunhofer IPA en IAO, Stuttgart), inclusief stages voor promovendi bij het Institute for Aircraft Design (IFB) aan de Universiteit van Stuttgart in relevante Industrie 4.0-gebieden. "Het GIL-project is een belangrijke mijlpaal voor geavanceerde composietprocessen en ook voor de samenwerking van SUT, Universiteit van Stuttgart en ARENA2036", zegt professor Peter Middendorf, directeur van de IFB. "We zijn er trots op een partner te zijn in het project zelf en om twee andere onderzoeksprojecten aan te kondigen die worden ondersteund door de Duitse regering en die rechtstreeks verband houden met GIL."
"We zullen een nieuw cohort van digitaal vaardige gezamenlijke PhD-studenten opleiden tussen Swinburne en de Universiteit van Stuttgart", zegt Fox. “We zullen niet alleen Composite 4.0-processen verder ontwikkelen, maar ook wereldwijde partnerschappen aangaan en nieuwe producten creëren die vanuit Australië kunnen worden geëxporteerd, met name in nieuwe mobiliteitsmarkten. Door deze internationale samenwerkingen zal Swinburne's Industry 4.0 Testlab het Australische MKB actief verbinden met wereldwijde waardeketens. We hebben dit al aangetoond met onze partner Imagine Intelligent Materials en we kijken ernaar uit om dit uit te breiden naar andere Australische innovators.”
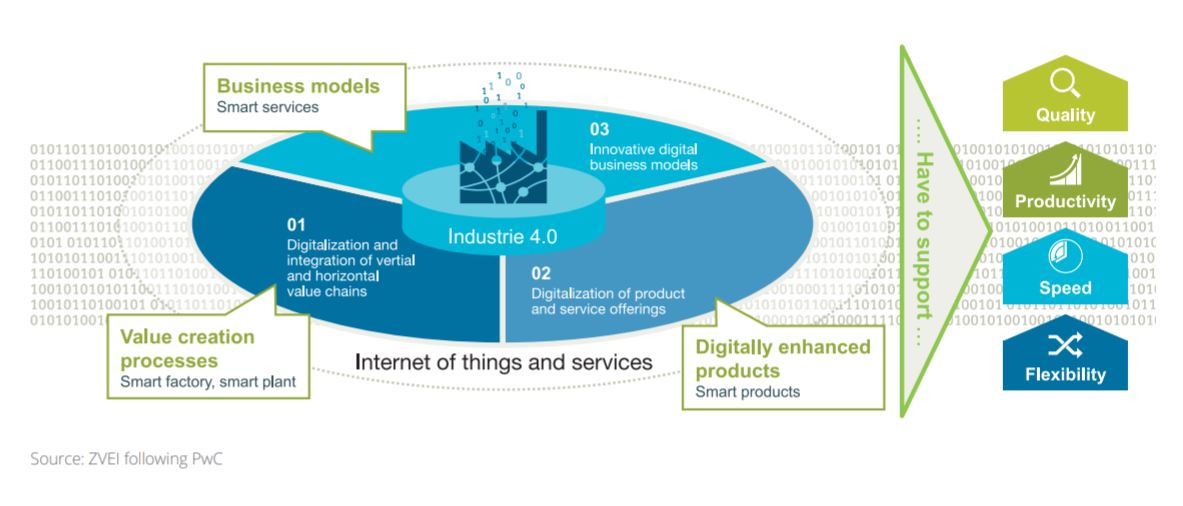
"De internationale concurrentie zal hevig zijn in de snel naderende digitale productie van de toekomst", zegt Fox. "Daarom is onze ontwikkeling van deze composieten 4.0-capaciteit en personeel nu zo belangrijk."
Het Industry 4.0 Testlab for Composite Additive Manufacturing aan de Swinburne University wordt in december 2020 gelanceerd. Blijf op de hoogte van CW voor toekomstige updates en lees onze functie van juli 2020, "Composieten 4.0:digitale transformatie, adaptieve productie, nieuwe paradigma's", samen met de vijf online zijbalken:
- Composieten 4.0:digitale tweeling versus digitale draad
- Zero-projectupdate
- Composieten 4.0:waar te beginnen?
- Geen businesscase voor het aanleren van robots
- Composites 4.0-architectuur en ontologie
Hars
- De waarde van additieve productie in de auto-industrie
- Additive manufacturing en spuitgieten — een nieuwe visie op productielevenscycli
- Introductie van AM Fridays en Additive Podcast
- Henkel biedt materiaalplatform voor additieve productie
- Essentium en Lehvoss werken samen om materialen voor additieve productie te ontwikkelen
- High-Flow POM voor de medische en zorgsector
- Alliantie voor duurzame thermoplasten en additive manufacturing in Colorado
- Wat is additieve productie? - Soorten en werking?
- De zaak voor 3D-printen in de productie
- Top 5 logistieke uitdagingen en oplossingen voor de maakindustrie
- Onderzoek van Protolabs en Censuswide suggereert dat de productie niet klaar is voor Industrie 4.0