Toekomstige composietproductie - AFP en Additive Manufacturing
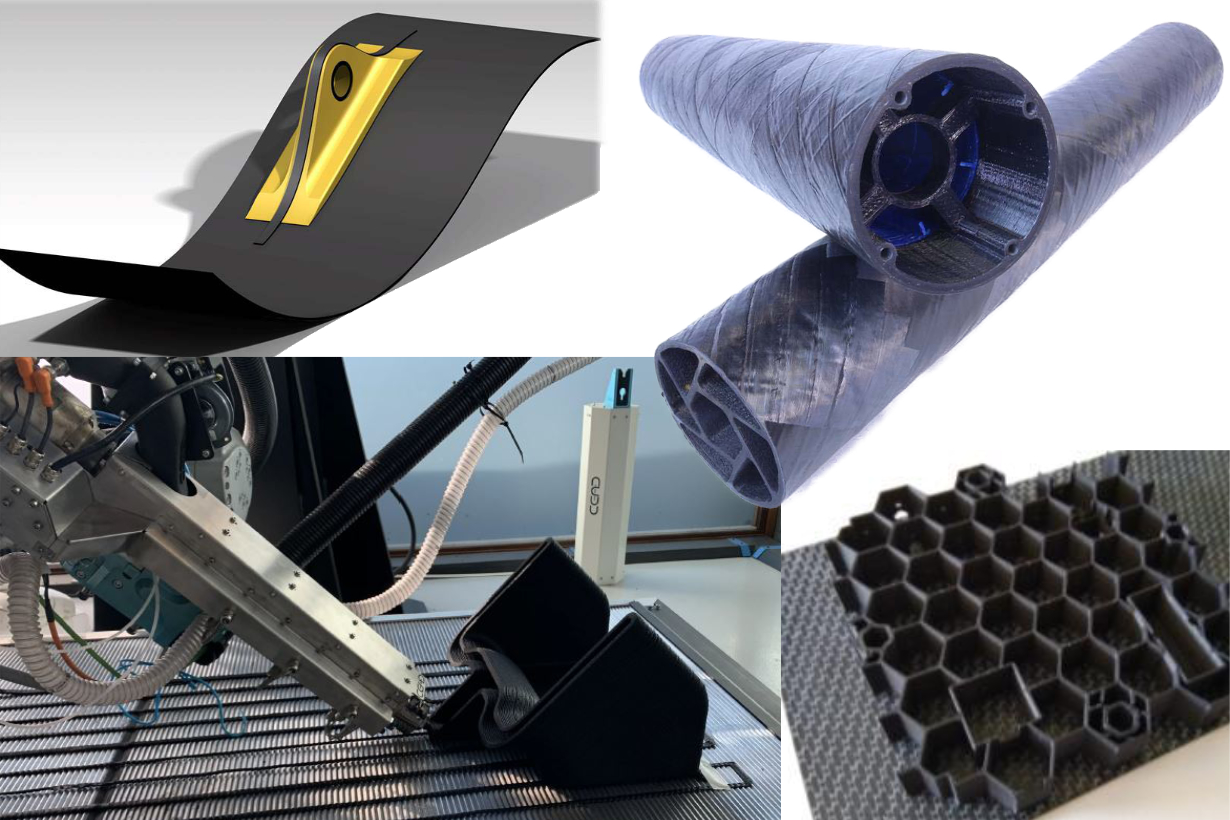
"Overdrukken" op vooraf gemaakte CFRP-oppervlakken en beugels (linksboven) , hybridiserende processen zoals 3D-printen en filamentwikkelen (rechtsboven) , 3D-printkernen op AFP-laminaten en AFP-skins op 3D-geprinte kernen (rechtsonder) en CEAD AM Flexbot 3D-printen op 45 graden (linksonder) . Photo Credit:TU München, voorzitter van Carbon Composites
In september woonde ik het virtuele symposium "FUTURE COMPOSITE MANUFACTURING – AFP &AM" bij, verwijzend naar geautomatiseerde vezelplaatsing (AFP) en additive manufacturing (AM). Dit symposium werd georganiseerd door de voorzitter van Carbon Composites (LCC) op Technische Universiteit van München (TUM, München, Duitsland). Bij het evenement was ook TUM's onderzoekspartner Australian National University (ANU, Canberra) aanwezig. Het symposium besprak de R&D-capaciteiten van composieten bij zowel TUM als ANU, evenals voltooide en lopende projecten met industriële partners, waaronder AFPT, Airbus, BMW, CEAD, DLR, Fraunhofer, GKN Aerospace, INOMETA, SGL Carbon en Victrex.
De samenwerking tussen TUM en ANU begon in 2010 met het AutoCRC-project voor de ontwikkeling van opslagtanks voor gecomprimeerd aardgas (CNG) van thermoplastische composieten. Gezamenlijke R&D is sindsdien voortgezet, inclusief de oprichting van het Australian Research Council's centre for Automated Manufacture of Advanced Composites (AMAC) en drie belangrijke aandachtsgebieden bij ANU:
- Materiaalverbetering
- Materialen en coatings op nanoschaal voor verbetering van functionele eigenschappen van koolstofcomposieten
- Met grafeen verbeterde prepreg-tapes voor thermische en elektrische geleidbaarheid
- Laser-AFP
- Project met Ford om met composiet versterkt staal te ontwikkelen
- Digitale regeling van verwarmingsbias, b.v. processtabiliteit voor hoeken/3D-geometrieën
- Geavanceerde diagnostiek met röntgen-CT
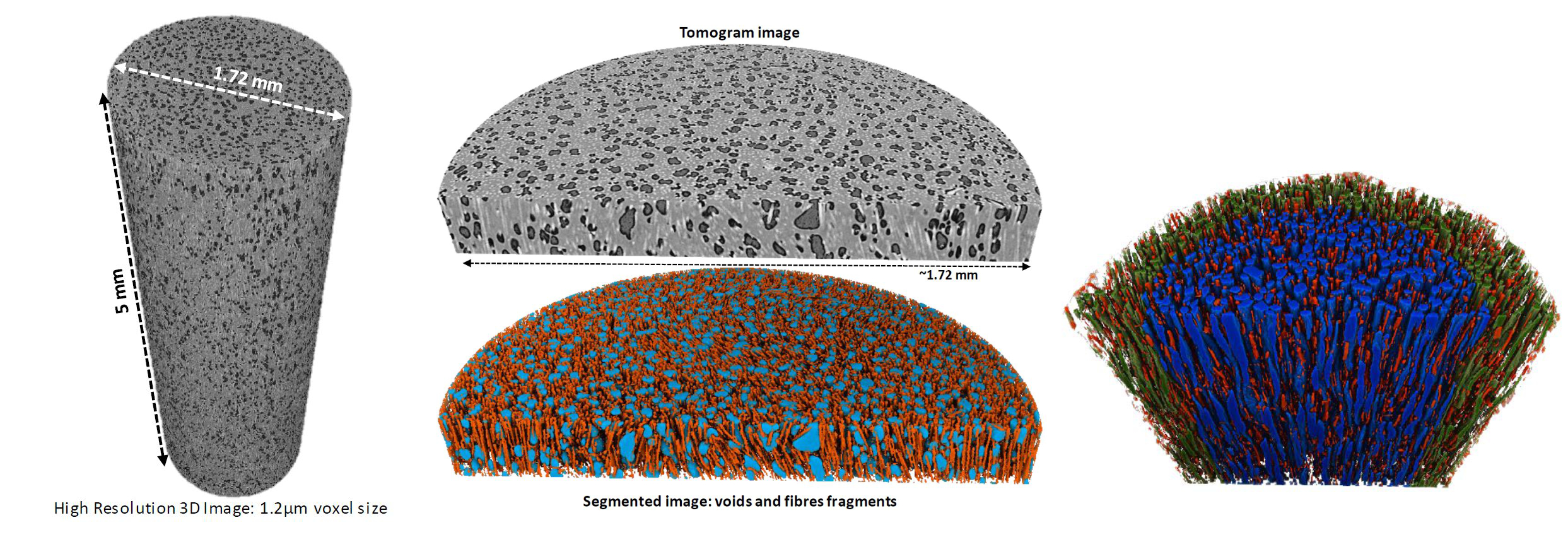
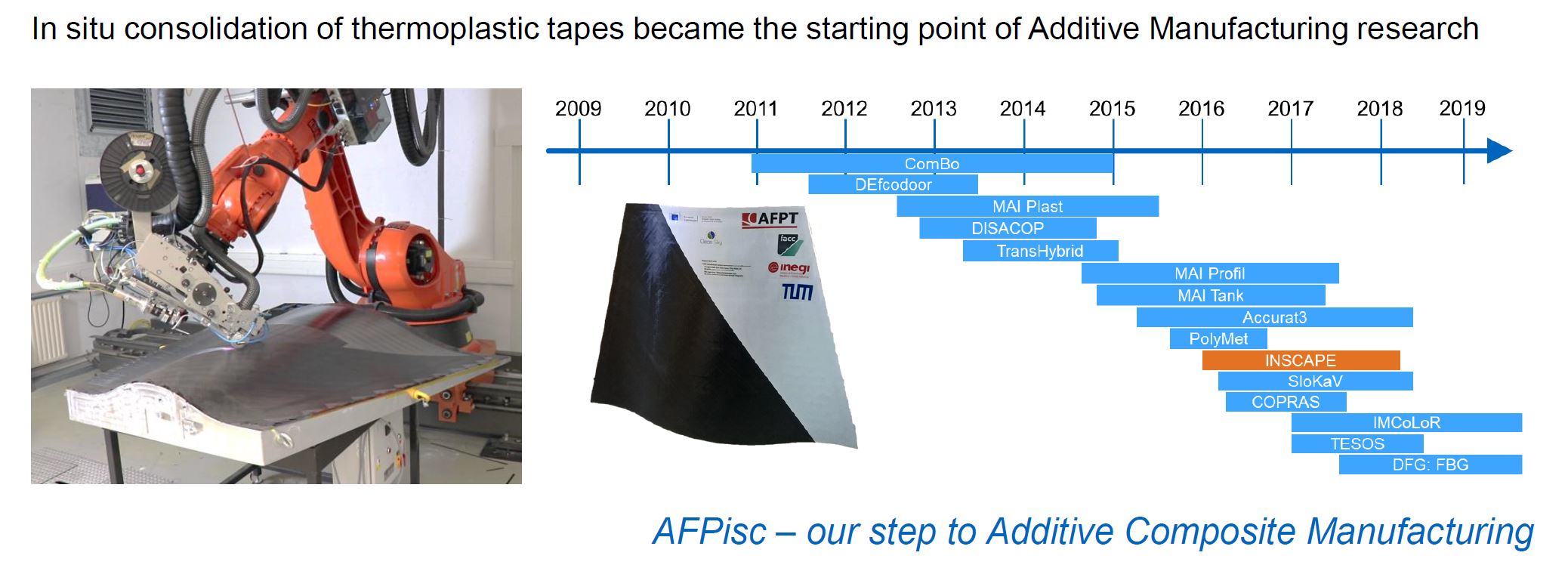
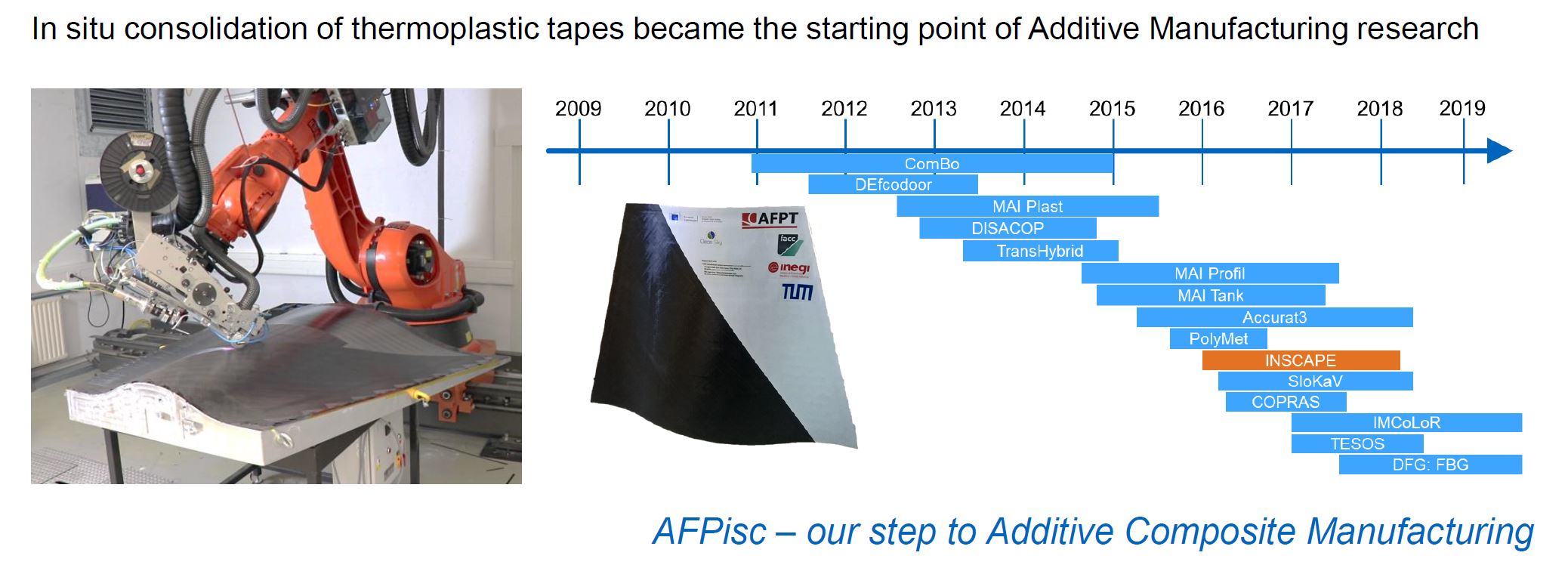
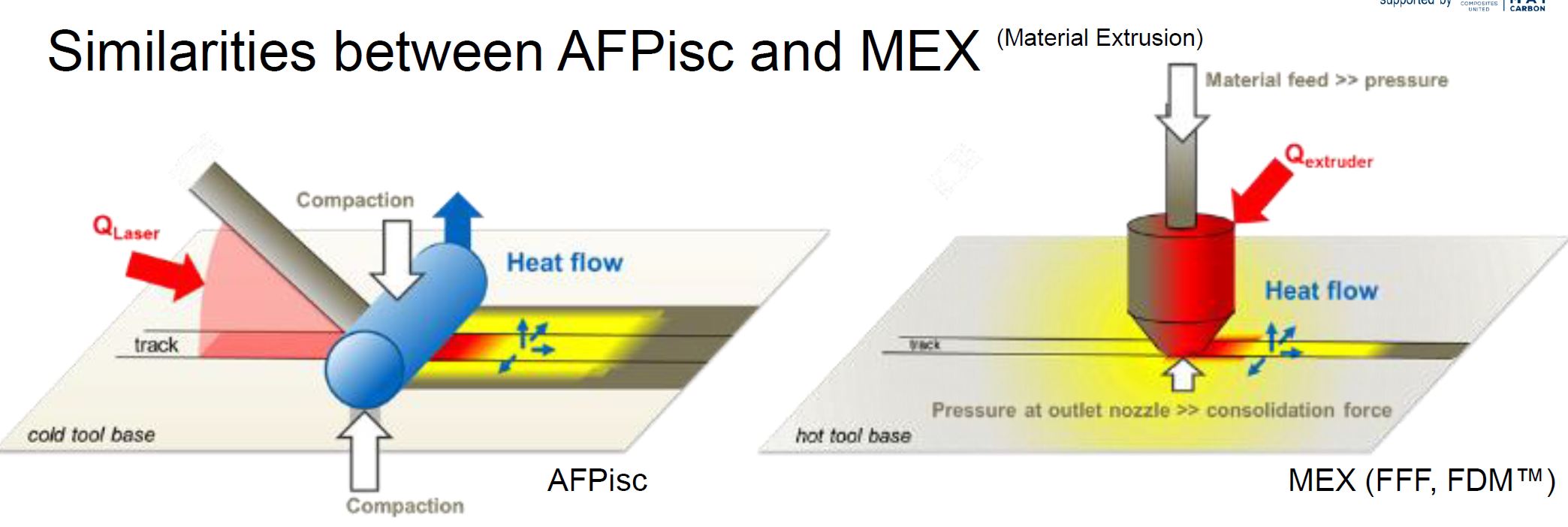
Hij besprak de overeenkomsten tussen materiaalextrusie (MEX), het meest gebruikte proces voor het 3D-printen van vezelversterkte composieten, en AFP ISC:
- Lokale, terugkerende warmtebehandeling
- Op lagen gebaseerd ontwerp en orthotrope materiaaleigenschappen
- Materiaalplaatsing langs 2D- en 3D-geprogrammeerde paden en thermische activering tussen lagen.
Drechsler besprak vervolgens de toekomstige behoeften aan composieten en hoe het combineren van AFP en MEX oplossingen zou kunnen bieden, waaronder op korte termijn in tooling en op langere termijn in hoogwaardige, lichtgewicht constructies die zowel kostenefficiënt als ecologisch duurzaam zijn.
Bij het schetsen van de mogelijkheden van LCC gaf Drechsler een overzicht van zijn MEX-apparatuur en van eerdere en lopende R&D-projecten op het gebied van additive manufacturing.
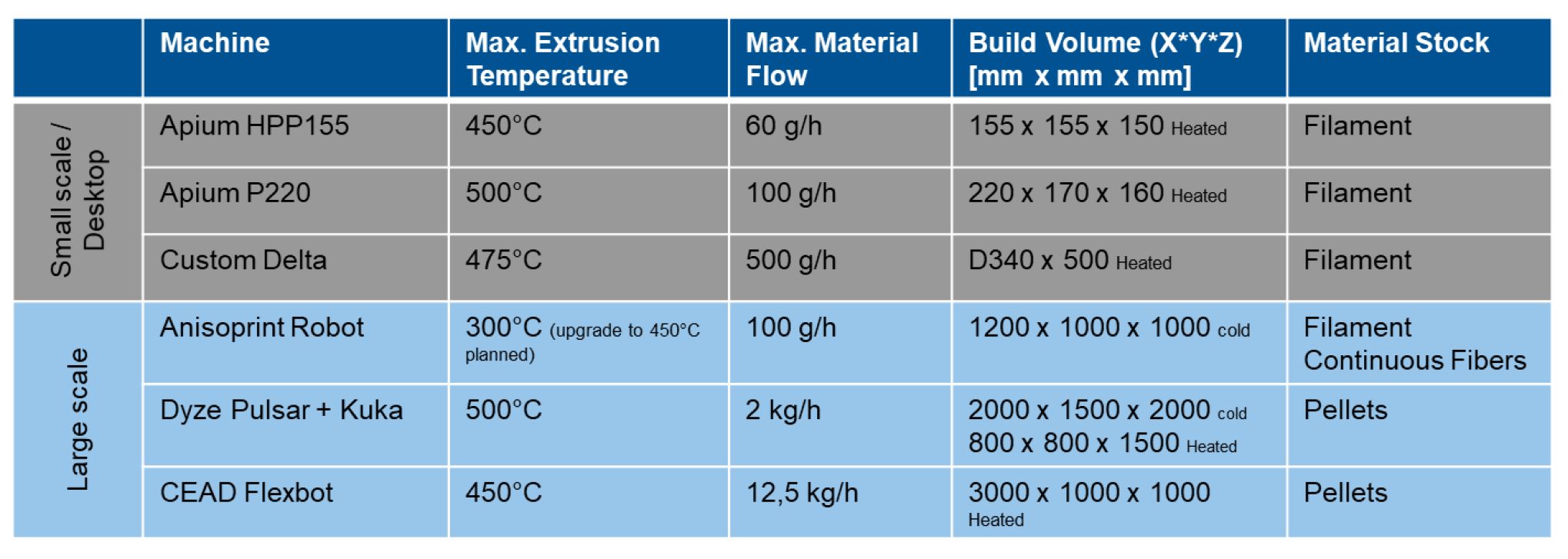
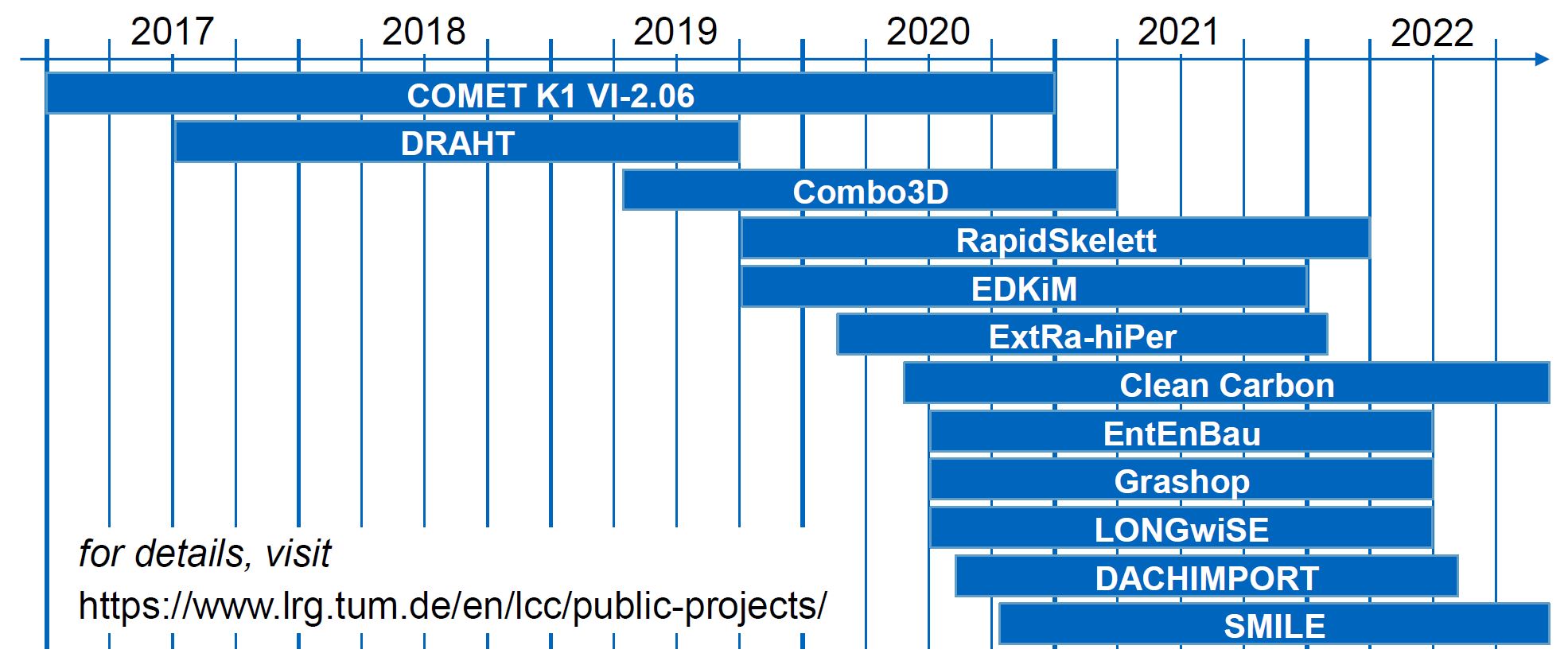
Met betrekking tot ISC AFP omvatten recente en lopende ontwikkelingen bij LCC:
- Een wikkelkop om de industrialisatie van constructies zoals drukvaten te ondersteunen, inclusief waterstofopslagtanks
- Gesloten regeling van laserstraalverwarming
- Een vloeistofgekoelde rol gebruiken voor consolidatie
- Karakterisering van banden om ISC te optimaliseren.
De ontwikkelingen van LCC op het gebied van MEX en 3D-printen werden de komende 2 dagen verder onderzocht in meerdere presentaties.
CEAD en grootschalig 3D-printen
De volgende presentatie na de keynote van Drechsler werd gegeven door Maarten Logtenberg, uitvoerend directeur van CEAD (Delft, Nederland). CEAD, opgericht in 2014, heeft commerciële systemen verkocht op basis van zijn Continuous Fiber Additive Manufacturing (CFAM)-technologie, zowel als een op een portaal gebaseerde gesloten cel (CFAM Prime) en een op een robot gebaseerd systeem (AM Flexbot). LCC is eigenaar van de laatste (zie bovenstaande tabel) en werkt samen met LCC aan verschillende projecten (zie CW artikelen over CEAD en zijn werk met TUM LCC).
Hoogtepunten van de presentatie van Logtenberg waren onder meer CEAD's ontwikkeling van hybride oplossingen die CNC-frezen, grote verwarmde printbedden (1,2 m x 3 m en 1,2 m x 2 m) en verwarmde roterende printbedden integreren. Het streeft ook naar nog grotere cellen en 45-graden printen, evenals het printen van vezelversterkte gereedschappen voor de seriële autoclaafproductie van commerciële vliegtuigonderdelen.
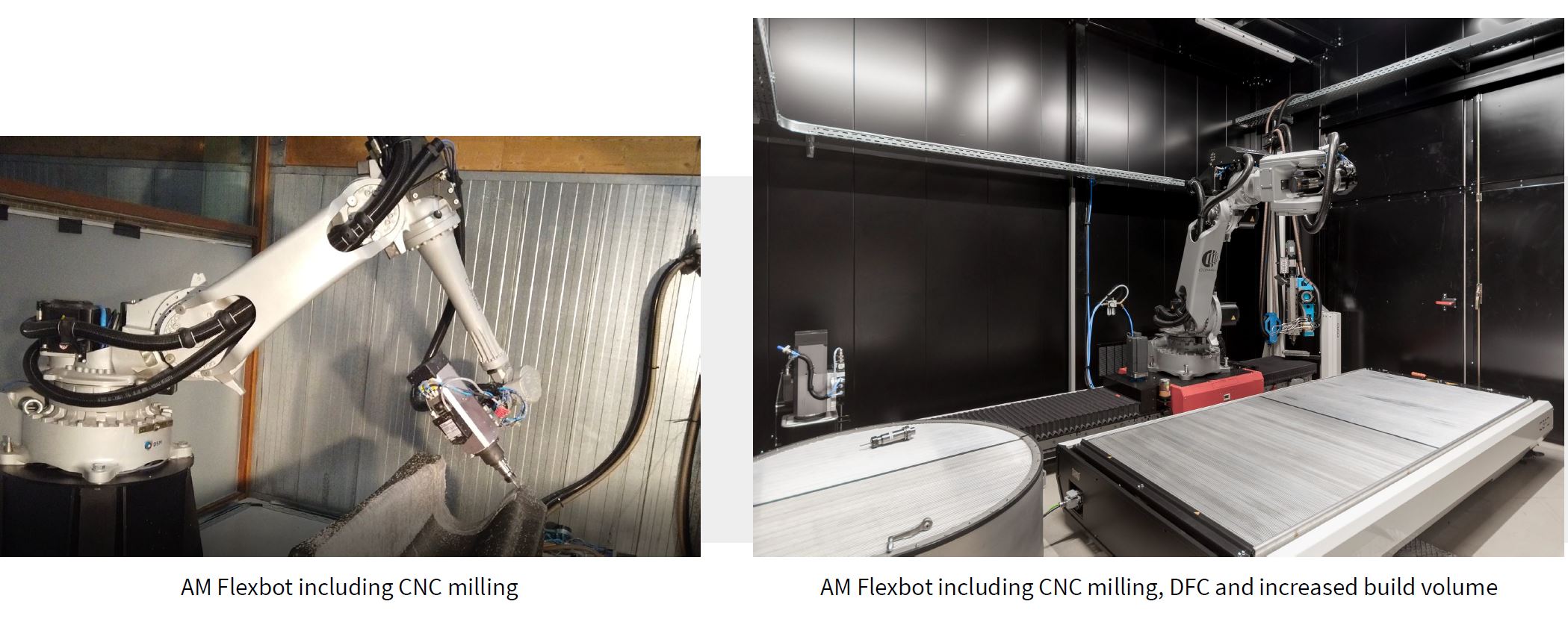
Logtenberg merkte op dat een van de belangrijkste uitdagingen voor 3D-geprinte autoclaafgereedschappen thermische uitzetting is en dat gereedschappen die veel groter zijn dan 4 meter de neiging hebben om te veel uit te zetten (zie "Hybride, grootformaat additieve gereedschappen"), waardoor het moeilijk is om voldoende te compenseren via gereedschapsontwerp . De oplossing die hij naar voren bracht, is om de gehakte vezelversterking die tot nu toe meestal wordt gebruikt te vervangen door continue vezels die zijn afgezet door systemen zoals AM Flexbot.
Dit pad voorwaarts werd ondersteund in de presentatie, "Introductie van 3D-geprinte spoorversterkers voor composietflapproductie ” gegeven door Thomas Herkner bij GKN Aerospace in München, Duitsland. Deze 3D-geprinte CFRP-versterkers worden gebruikt als tooling bij de productie van CFRP-landingskleppen voor de Airbus A350 en A330. Hoewel dit succesvolle programma bij GKN wel gebruik maakte van gehakte vezelversterking, toonde Herkner een routekaart voor verdere ontwikkeling, waaronder het gebruik van continue vezels in 3D-geprinte tooling en, uiteindelijk, in de vliegtuigonderdelen zelf.
Dit pad voorwaarts werd goed uitgelegd door LCC-onderzoek Patrick Consul in een recente CW-blog:
Consul presenteerde ook op het TUM-symposium, over procesontwerp voor grootschalige, op extrusie gebaseerde AM. Hij besprak hoe de hieronder getoonde glas- en faseovergangen de grootste verandering in materiaaleigenschappen vertegenwoordigen van gehakte vezelversterkte pellets die worden gesmolten en geëxtrudeerd in 3D-printsystemen zoals CFAM en AM Flexbot.
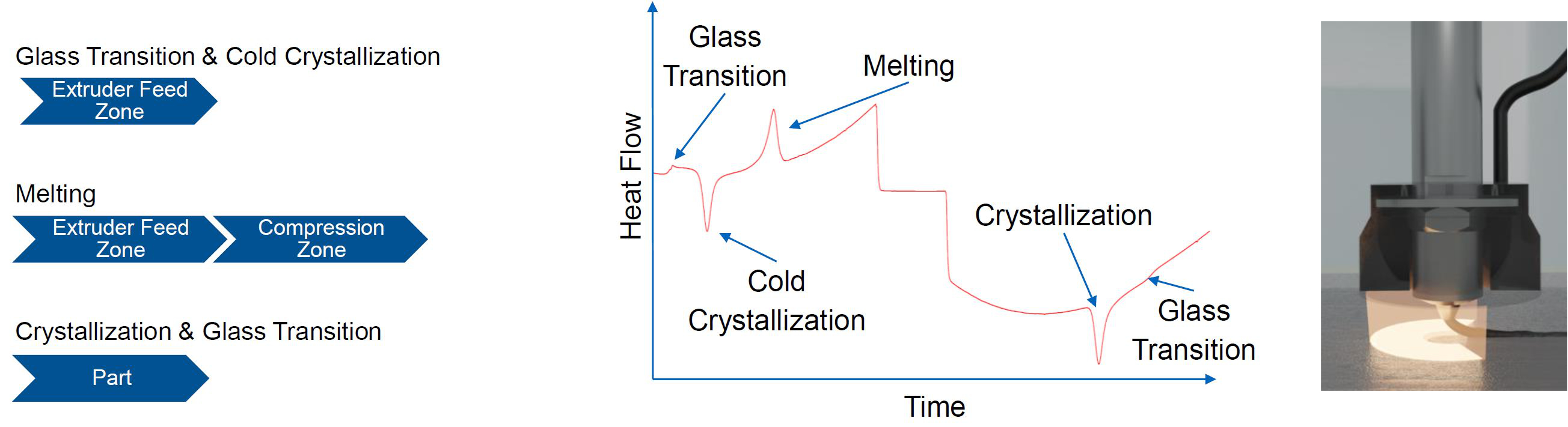
Het werk van Consul heeft geanalyseerd hoe MEX-parameters zoals polymeerviscositeit en extrusietemperatuur en koppel de kristalliniteit in het geprinte composiet beïnvloeden, wat op zijn beurt het vermogen beïnvloedt om lagen aan elkaar te lassen tijdens 3D-printen. Naast deze laag-op-laag hechting heeft Consul ook de vezeluitlijning en restspanning in de geprinte lagen onderzocht. Een oplossing die werd gepresenteerd, was het gebruik van een laser om het substraat voor te verwarmen tijdens het printen - tegenwoordig veel gebruikt in ISC AFP van thermoplastische composieten - en zo kennis over te dragen van AFP naar AM. Bij de eerste experimenten werd gebruik gemaakt van een ring van bestuurbare laserdiodes.
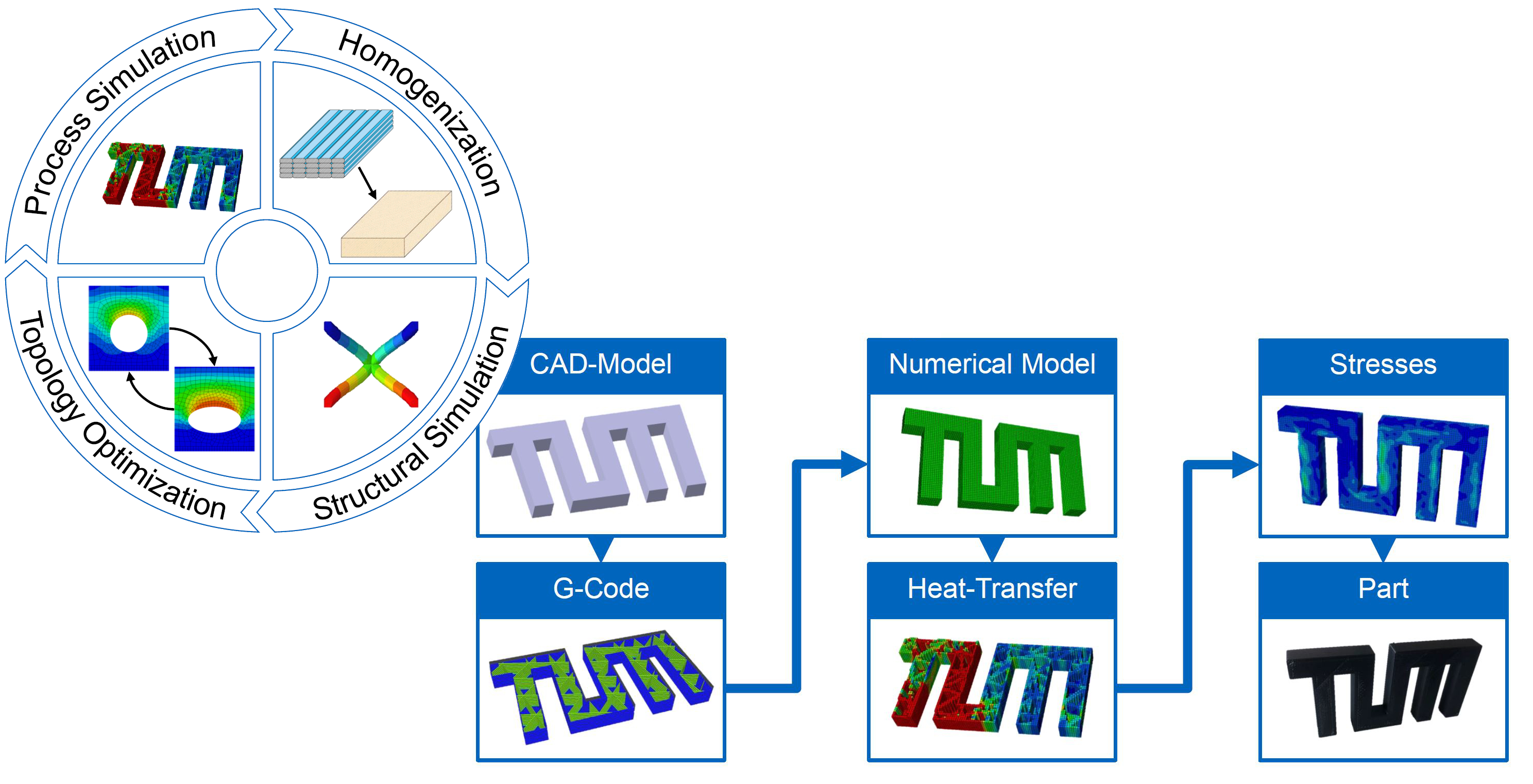
Collega van de consul, Matthias Feuchtgruber, presenteerde later op de dag en ging verder van procesontwerp en materiaalkarakterisering naar het ontwikkelen van een virtuele procesketen voor composieten AM.
Alexander Matschinski presenteerde vervolgens de integratie van eindeloze vezels in composieten AM, waarbij hij de onderstaande grafiek presenteerde, die de basis werd voor de gewijzigde grafiek die ik gebruikte in CW ’s Next-Gen Supplement-artikel over 3D-printen met continue vezels. Matschinski besprak ook het ontwerp van AM-structuren met continue vezels en de toekomstige ontwikkeling van "overprinten" op kant-en-klare CFRP-onderdelen en -oppervlakken.
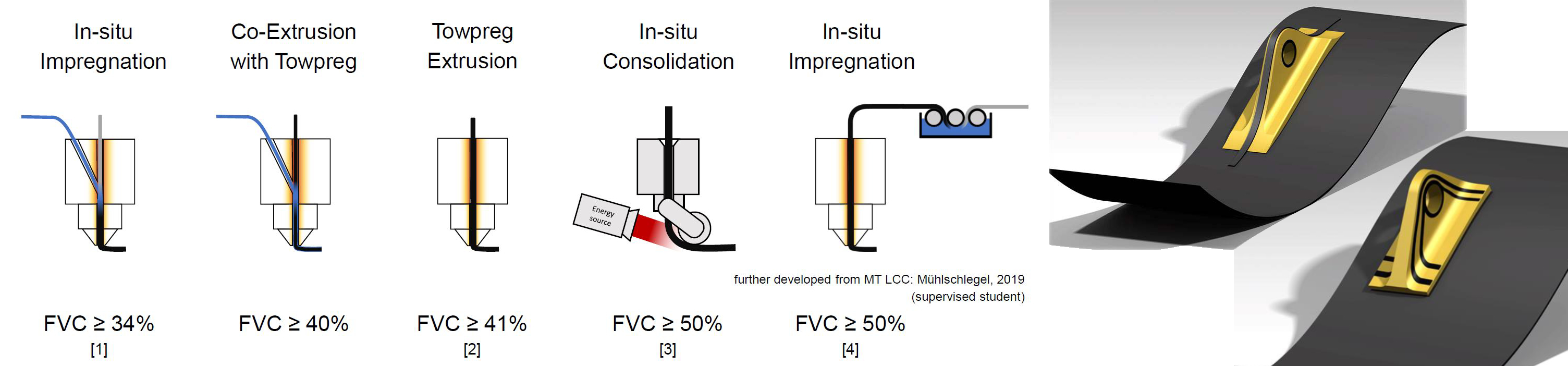
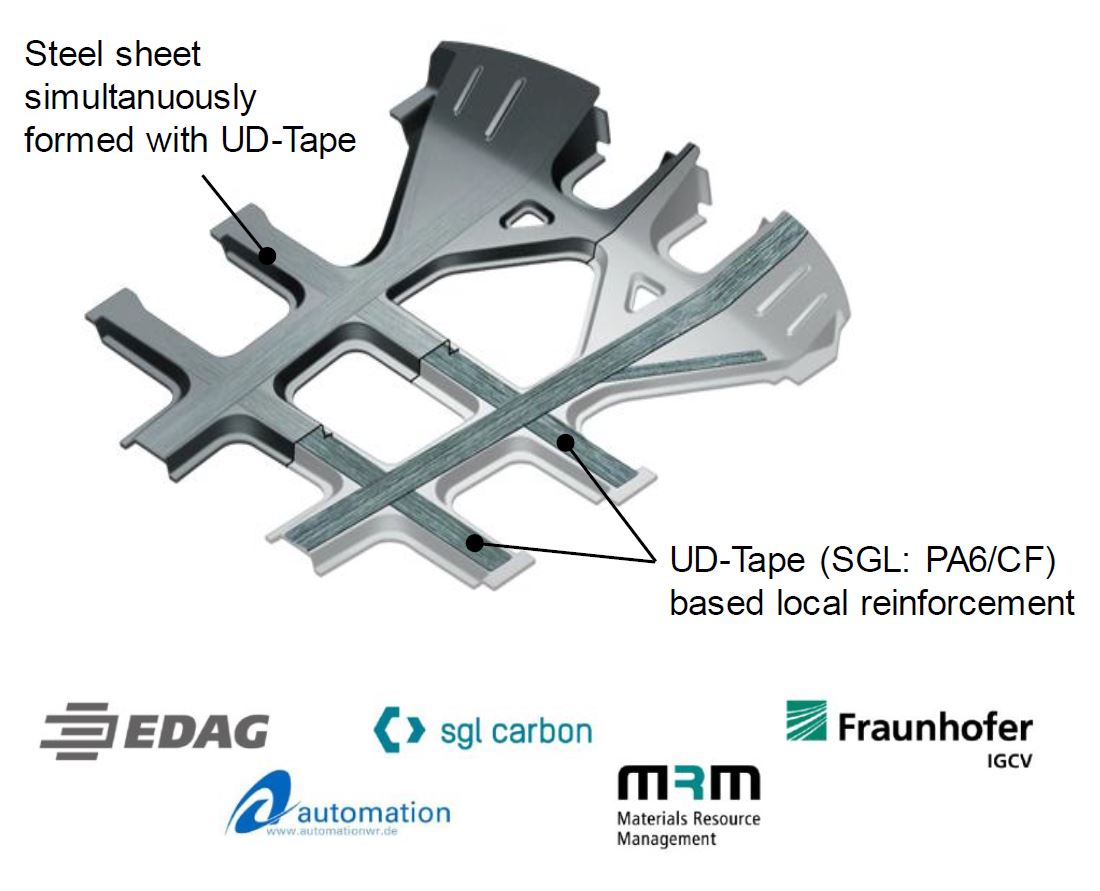
Andere interessante toepassingen van continue vezels werden getoond door Dr.Christopher Ebel bij SGL Carbon, waaronder het versterken van stalen bodemconstructies voor auto's, het verminderen van het aantal onderdelen van 37 naar 9 en het verminderen van het gewicht met 41%. Een ander concept was 3D-wikkeling met behulp van towpreg geïmpregneerd met snap-cure epoxyhars voor voor belasting geoptimaliseerde constructies. Deze digitaal gestuurde aanpak begint met vereenvoudiging van complexe belastingen en topologie-optimalisatie, gevolgd door geautomatiseerde productie. Resulterende onderdelen kunnen gebruik maken van vormvergrendeling van inzetstukken in constructies, waardoor belasting kan worden ingevoerd zonder verlies van stijfheid. De nieuwste 3D-metaalprintprocessen kunnen voor dergelijke inserts worden gebruikt, waardoor de efficiëntie van de laadbehandeling verder wordt geoptimaliseerd en de kosten worden verlaagd.
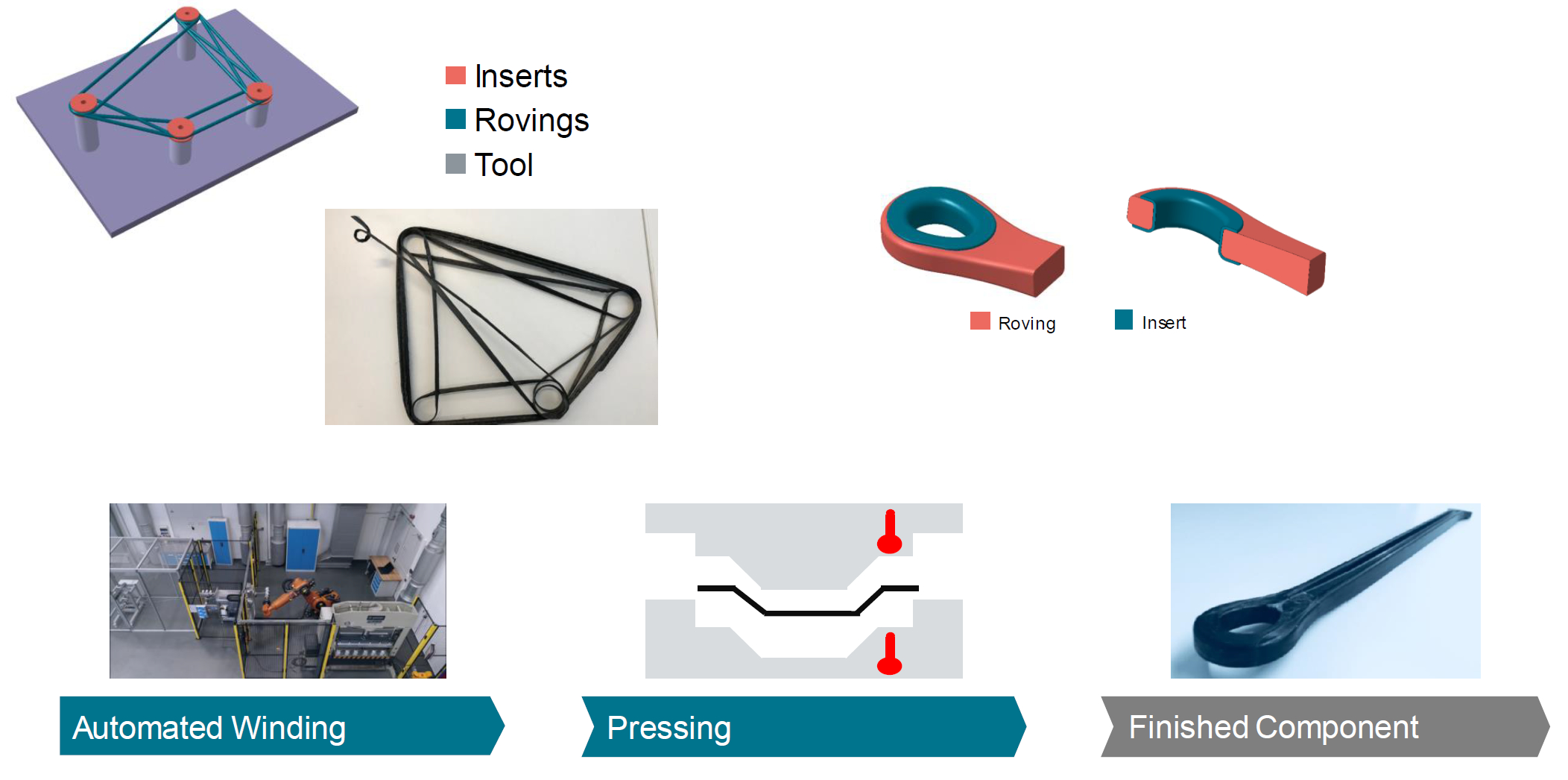
Sebastian Nowotny van DLR besprak het combineren van 3D-printen met ISC AFP van thermoplastische composieten, inclusief 3D-printen op AFP-laminaten en AFP op gedeeltelijk open 3D-geprinte structuren. De eerste experimenten omvatten het 3D-printen van een kern op een vooraf gemaakte CFRP-huid en vervolgens AFP/tape die bovenop de 3D-geprinte kern wordt gelegd. Er werden monsters gemaakt en vervolgens onderworpen aan een trekproef om de hechting van huid tot kern te evalueren.
Titel diavoorstelling
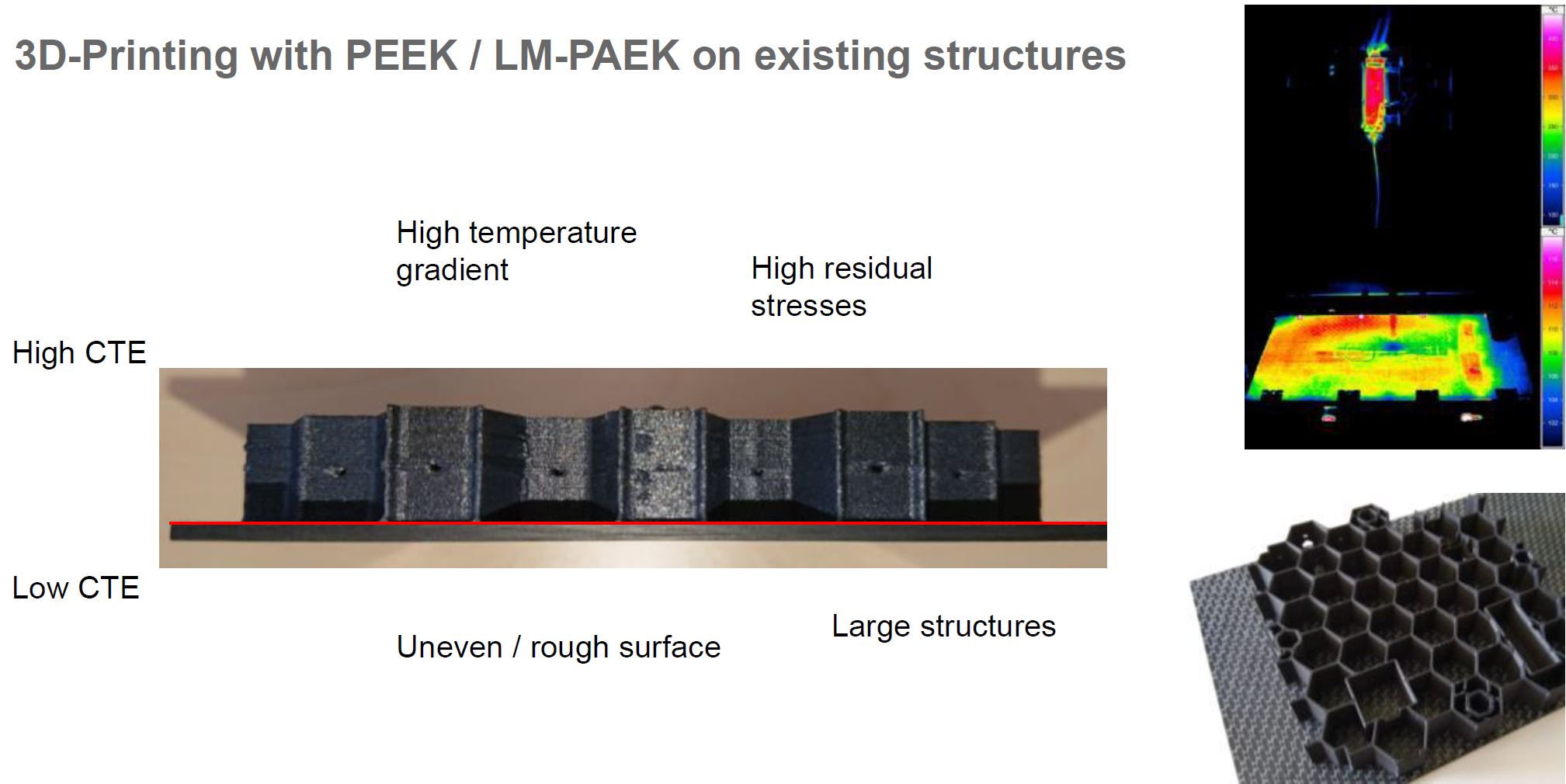
Fotocredits:Sebastian Nowotny, DLR, TUM Symposium september 2020
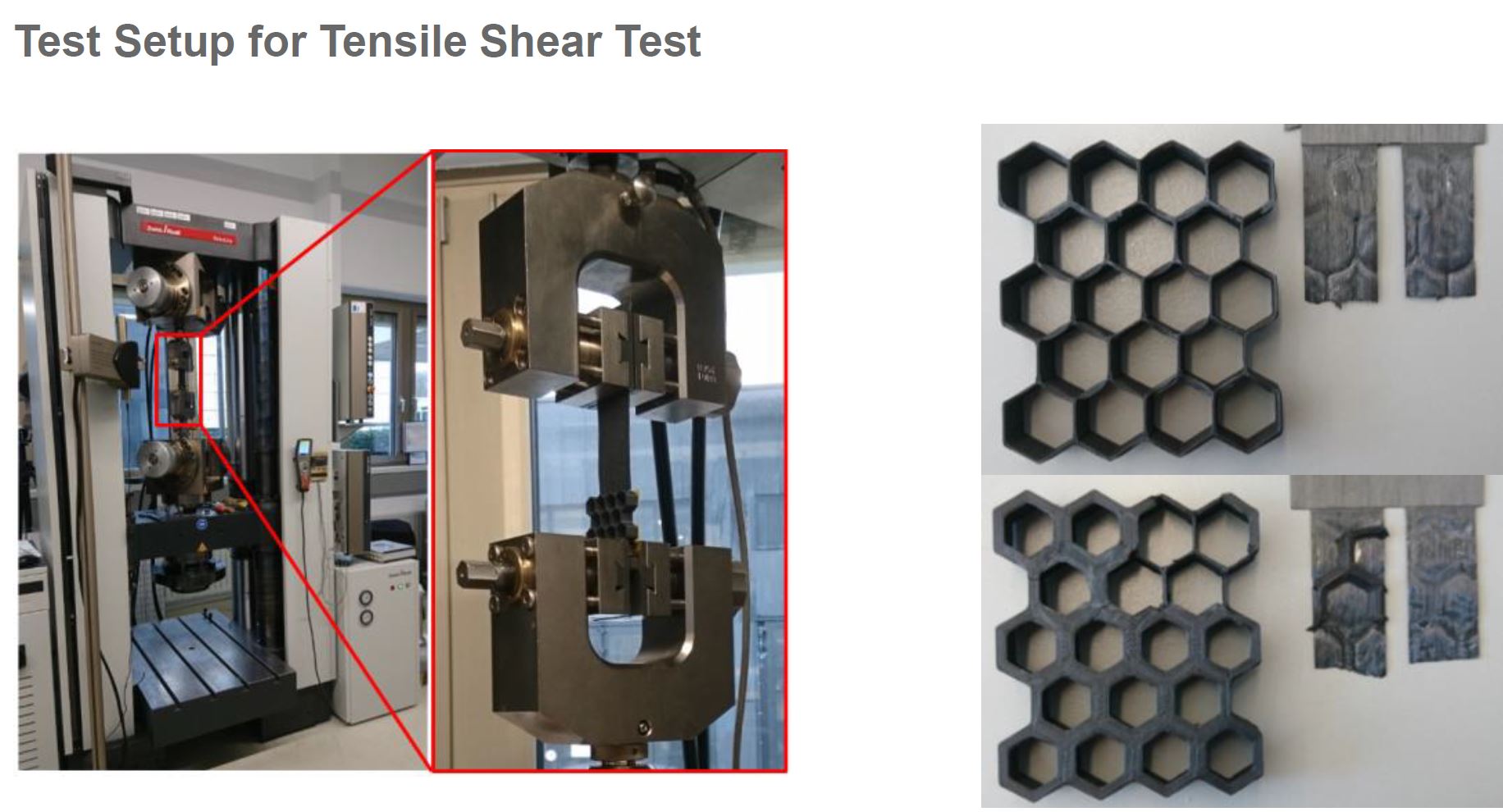
Trekkrachttesten van coupons gemaakt met hybride 3D-printen en AFP. Fotocredits:Sebastian Nowotny, DLR, TUM Symposium september 2020
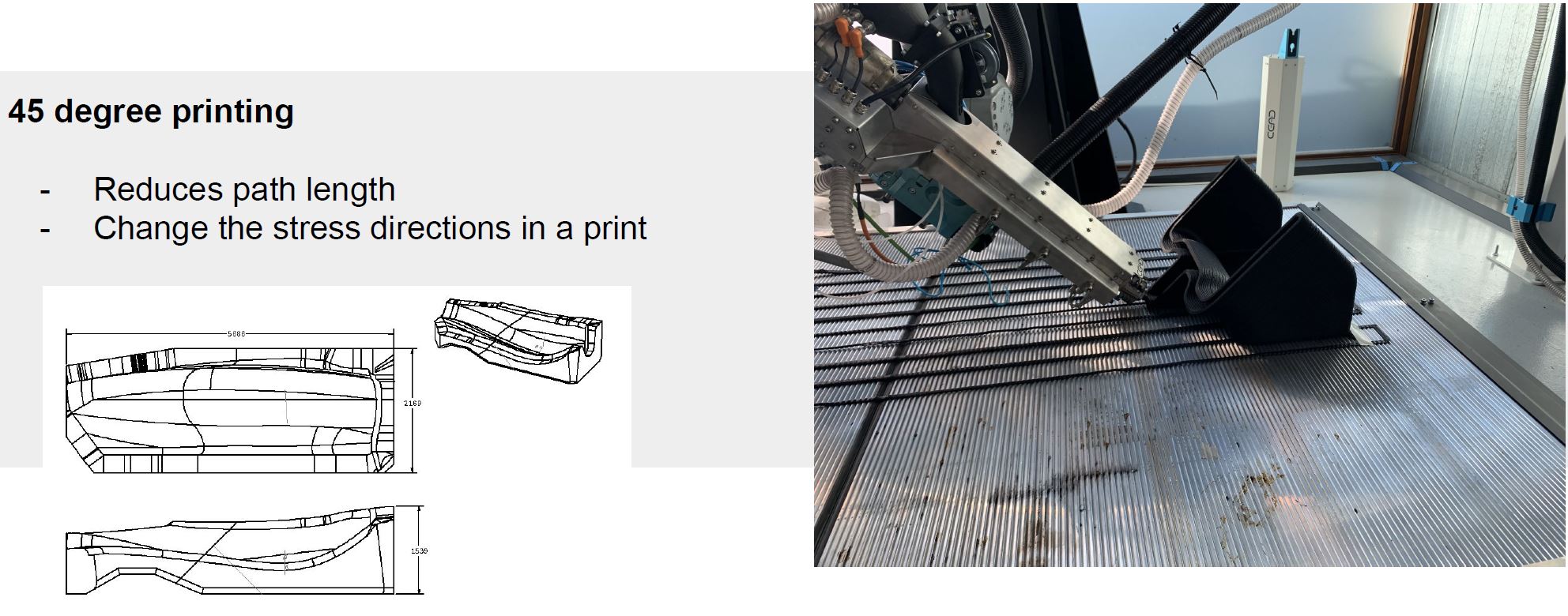
Fotocredits:CEAD, TUM Symposium september 2020
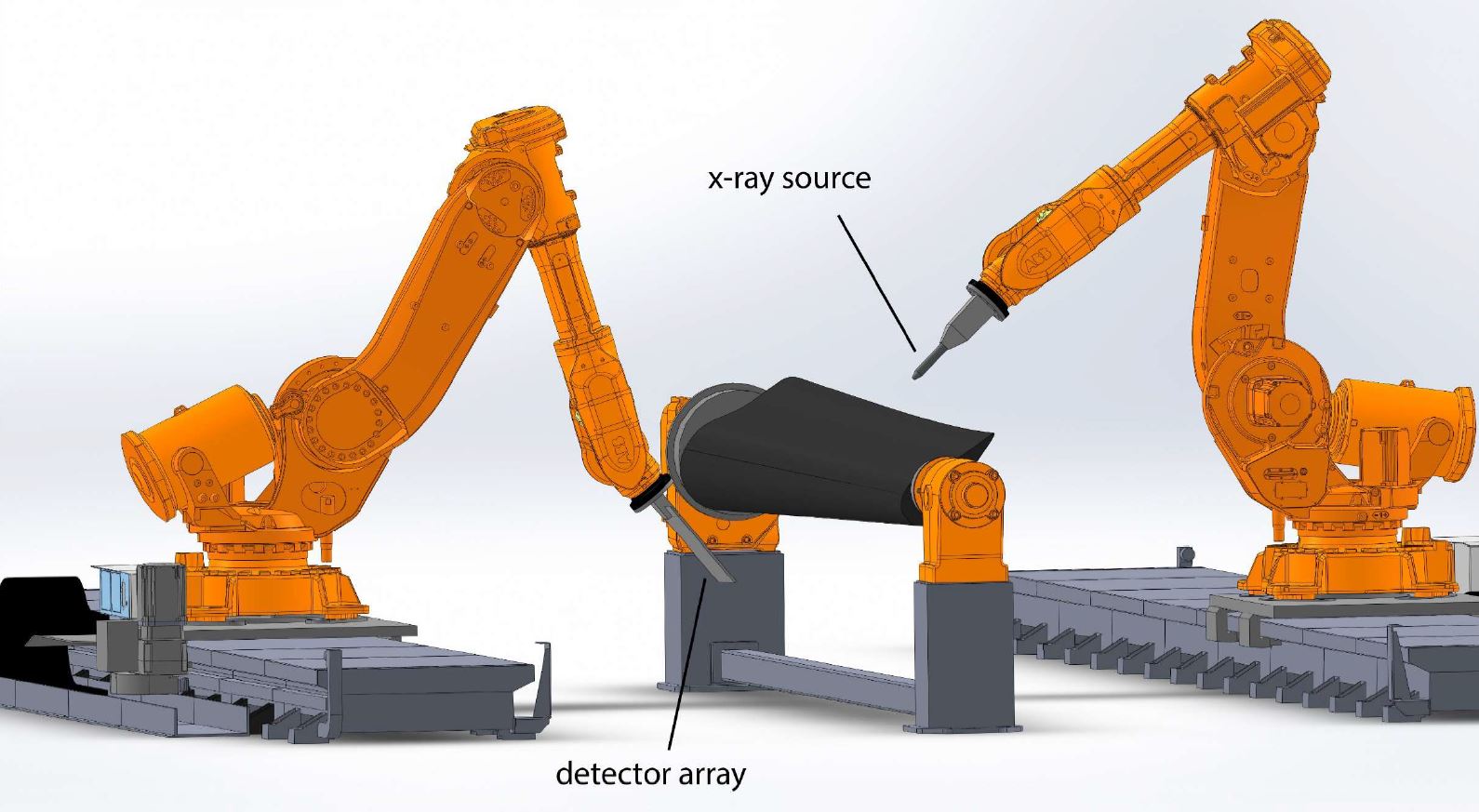
Toekomstige toepassing van computertomografie tijdens de productie van composieten. Photo Credit:Australian National University, TUM Symposium september 2020
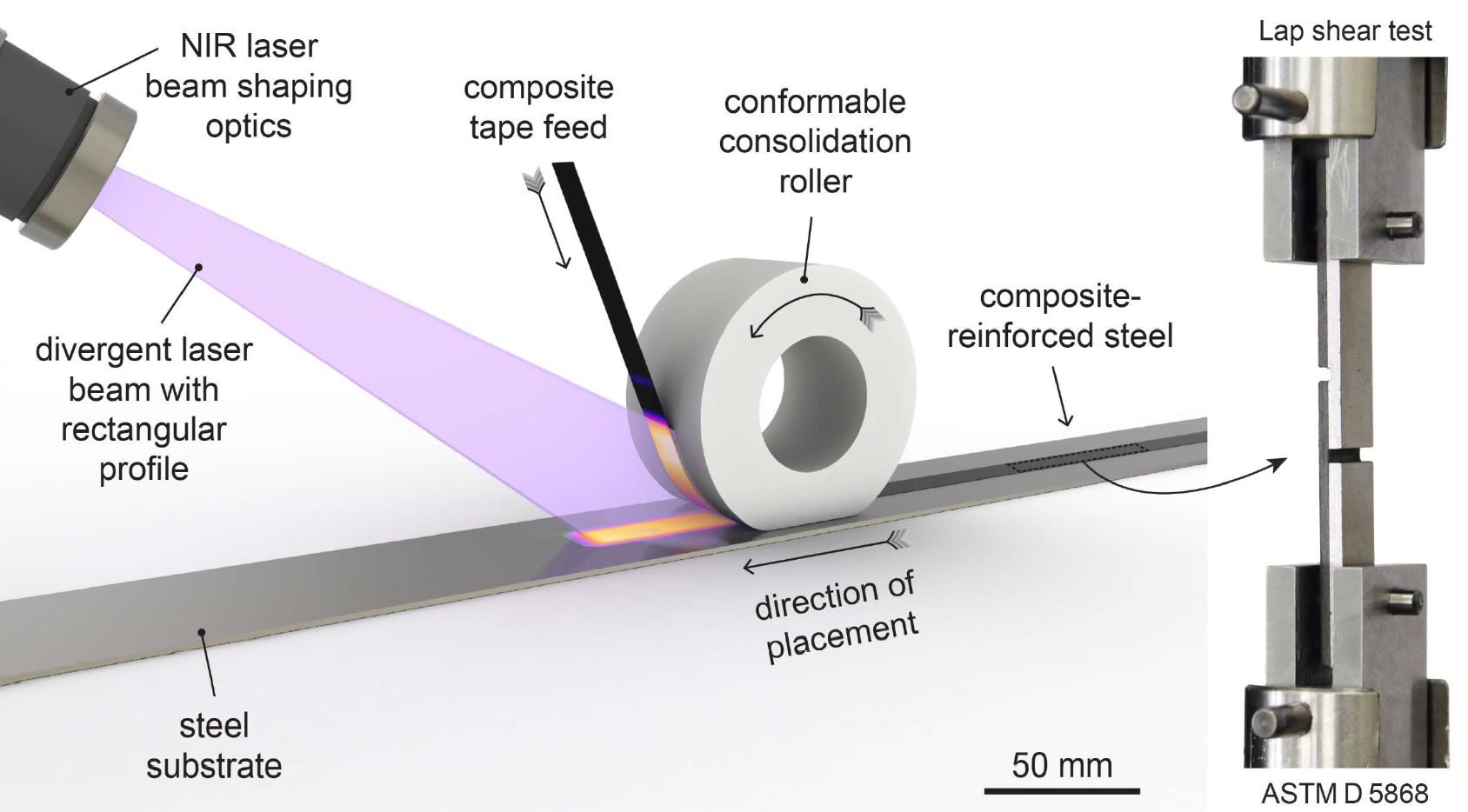
Ontwikkelingswerk met behulp van laser AFP om hybride CFRP-metaalstructuren te creëren. Photo Credit:Australian National University, TUM Symposium september 2020
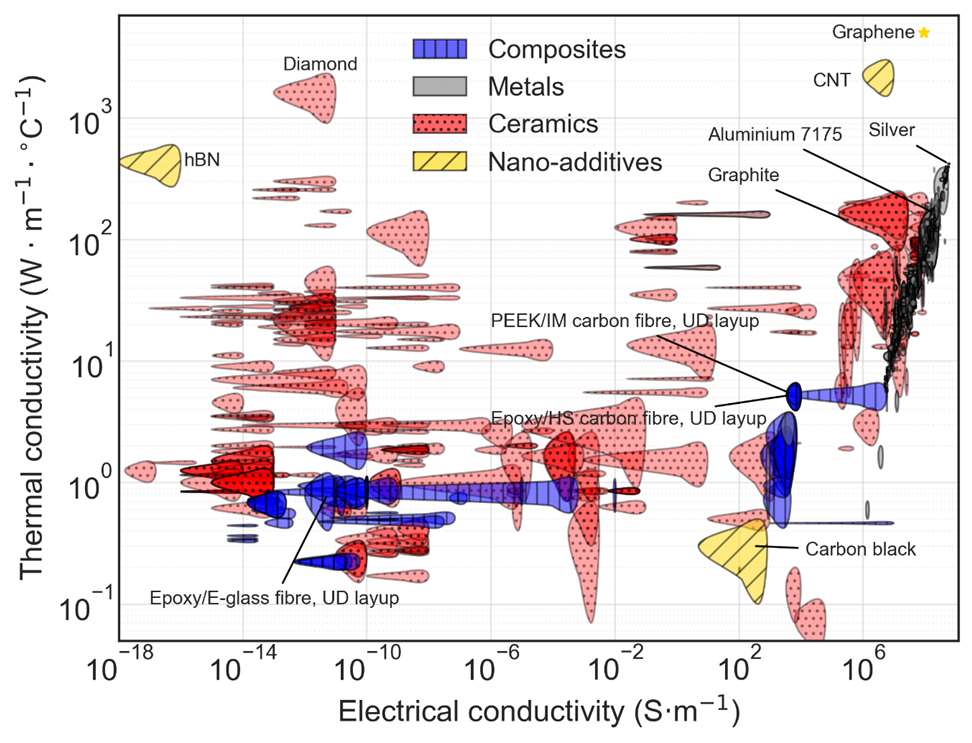
Met grafeen verbeterde prepreg-tapes voor thermische en elektrische geleidbaarheid. Photo Credit:Australian National University, TUM Symposium september 2020
Vorige volgendeChristian Weimer, hoofd materialen voor Airbus Central Research &Technology, besprak continu vezelprinten als onderdeel van het evoluerende technologielandschap, gericht op een lager gewicht met lagere kosten en meer duurzaamheid die moet worden bereikt voordat composieten een plaats krijgen in toekomstige vliegtuigen. Hij benadrukte dat echt efficiënte 3D-composieten het volgende moeten gebruiken:
- De juiste grondstoffen en tussenproducten – vezels, halffabrikaten
- Efficiënte processen en interfaces – AM-thermoplasten, spuitgieten
- Aangepast ontwerp en maatvoering – integraal, volledig geoptimaliseerd voor 3D-belasting)
- Oppervlak en functionaliteit – ESN (elektronisch serienummer), SHM (structurele gezondheidsmonitoring)
Hij besprak ook de behoefte aan bio-afgeleide vezels en harsen om de dringende doelstellingen op het gebied van klimaat en milieuduurzaamheid te halen.
Het TUM-symposium bevatte nog veel meer presentaties, waaronder samenvattingen van werk bij ANU, en ze waren allemaal erg interessant om te laten zien hoe composieten vooruitgaan en hoe de LCC, in samenwerking met partners over de hele wereld, zich blijft voorstellen wat composieten kunnen bereiken en onze industrie vooruit helpen.
Hars
- Is hybride productietechnologie de toekomst van additieve productie?
- Introductie van AM Fridays en Additive Podcast
- Additive Manufacturing met composieten in de lucht- en ruimtevaart en defensie
- Essentium en Lehvoss werken samen om materialen voor additieve productie te ontwikkelen
- Robotica en de toekomst van productie en werk
- AMRC en Prodrive werken samen om de productie van recyclebare composietcomponenten te bevorderen
- PES-additief verhoogt de weerstand tegen breuk en microscheurtjes in epoxycomposieten
- Alliantie voor duurzame thermoplasten en additive manufacturing in Colorado
- Wat is additieve productie? - Soorten en werking?
- Automatisering en de toekomst van digitale productie?
- Additieve productie in de geneeskunde en tandheelkunde