Geautomatiseerde productie van aerocomposieten:vloeibaar gieten of gelast thermoplast?
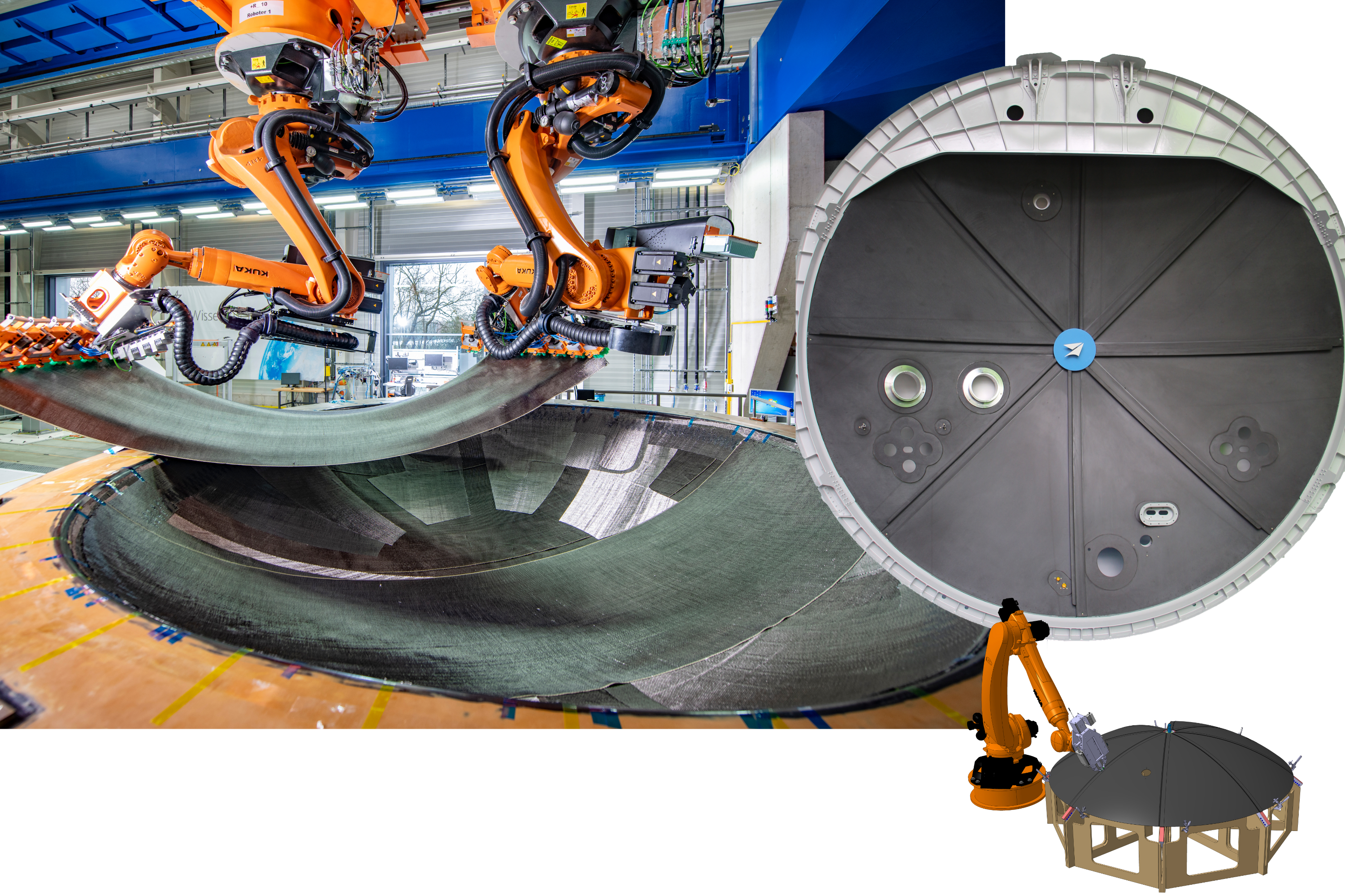
Terwijl OEM's en leveranciers de materialen en processen onderzoeken die de volgende generatie vliegtuigen mogelijk zullen maken, worden twee verschillende benaderingen gedemonstreerd. De eerste is het vloeibaar gieten van preforms van droge vezels, bijvoorbeeld te zien in Spirit AeroSystem's (Prestwick, Schotland) high-rate resin transfer molding (RTM) lijn voor Airbus A320 spoilers en ook in het door Airbus geleide Wing of Tomorrow (WOT) programma waarbij gebruik wordt gemaakt van geautomatiseerde plaatsing van non-crimp-stoffen (NCF) en vloeibare harsinfusie, gevolgd door uitharding buiten de autoclaaf (OOA) in een oven (zie "Hoge snelheid, geautomatiseerde RTM-lijn voor de ruimtevaart levert spoilers van de volgende generatie" en "Update:lagere vleugel skin, Wing of Tomorrow” respectievelijk.)
De tweede is thermoplastische composieten (TPC) die bijvoorbeeld worden gebruikt in de Clean Sky 2 Multifunctional Fuselage Demonstrator (MFFD), waar verstijfde huiden worden gemaakt met behulp van geautomatiseerde plaatsing van vezels - in-situ geconsolideerd voor de bovenste helft en autoclaaf-geconsolideerd voor de onderste de helft — gevolgd door montage door middel van lassen. Deze programma's gebruiken automatisering om de productiesnelheid en kwaliteit te verhogen en tegelijkertijd de kosten te verlagen. Maar hoe verhouden ze zich?
Het Duitse Aerospace Center (DLR) Institute of Structures and Design exploiteert het Center for Lightweight Production Technology (ZLP) in Augsburg. Van de vele composietproductieprojecten bieden PROTEC NSR en Fast Lane RPB een unieke kans om respectievelijk een vloeibaar gevormd thermohardend achterdrukschot (RPB) voor de Airbus A350 met twee gangpaden te vergelijken met een thermoplastische RPB voor de Airbus met één gangpad A320. Beide projecten werkten samen met de Tier 1-leverancier van deze structuren, Premium Aerotec Group (PAG, Augsburg, Duitsland), en demonstreerden automatisering terwijl de cyclustijd en -kosten werden geëvalueerd.
Vloeibaar gegoten TS-schot
"We zijn vele jaren geleden begonnen met PAG in het AZIMUT-project om handmatige processen voor de fabricage van composieten te analyseren", zegt Dr. Lars Larsen, hoofd assemblage- en verbindingstechnologieën bij ZLP Augsburg. "Onze eerste automatiseringsoplossing was voor layup, en daarna hebben we gewerkt om meer bewerkingen te automatiseren." Het belangrijkste doel van PROTEC NSR was om deze gespecialiseerde oplossingen voor RPB-productie te integreren in een enkel geautomatiseerd proces, legt Dr. Marcin Malecha, projectmanager voor PROTEC NSR bij DLR, uit.
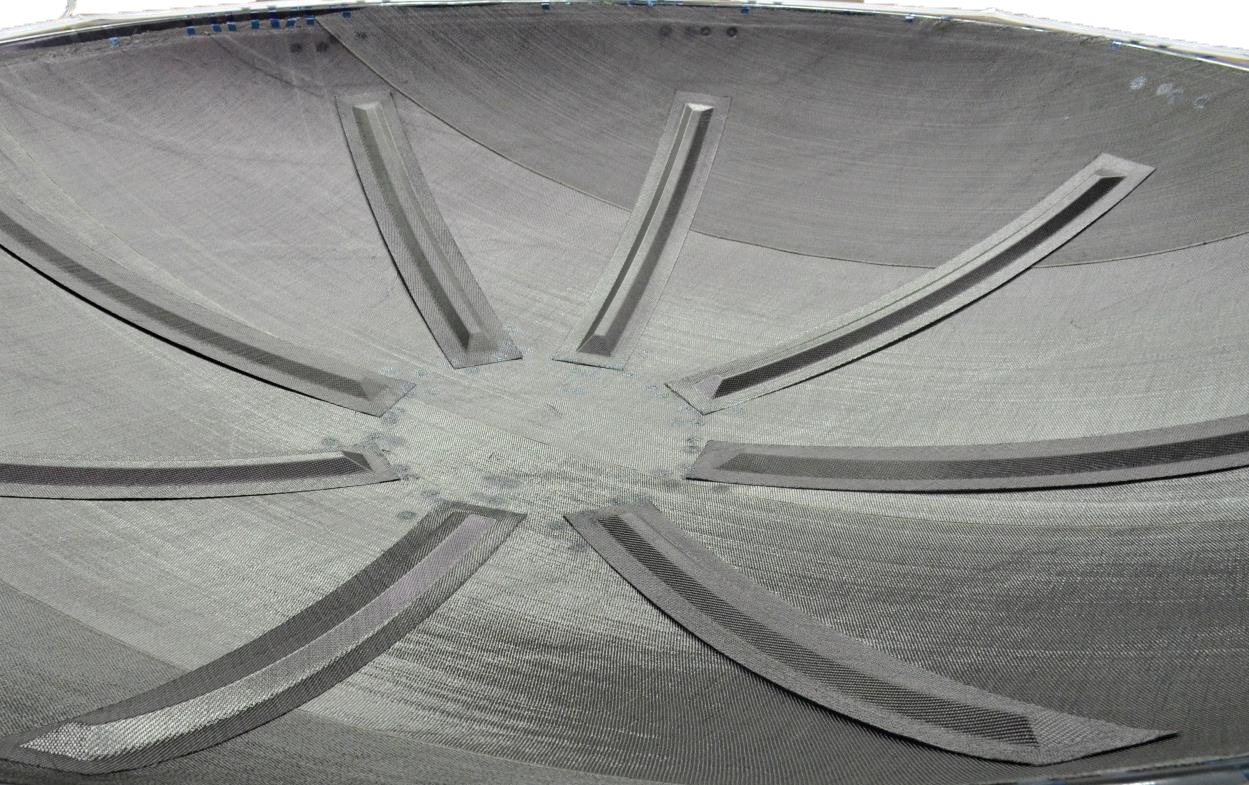
Preform en grijpers. De processtappen voor het maken van de droge voorvorm in vacuümzakken worden weergegeven in figuur 1 hieronder. Dit werd doordrenkt met RTM6-epoxyhars met behulp van het door Airbus gepatenteerde vacuümondersteund proces (VAP), dat gebruik maakt van een semi-permeabel membraan voor verminderde porositeit. De lay-out van de voorvorm bestond uit twee sets van 16 lagen met een lengte van maximaal 5 meter, waarbij gebruik werd gemaakt van de volledige breedte van 1,27 meter van de satijnen koolstofvezelstof met 5 harnassen. Ingebed tussen deze twee sets waren 25 complexvormige, versterkende stukken met afmetingen tot 1,5 bij 2,5 meter. Er werden acht stringers bovenop geplaatst.
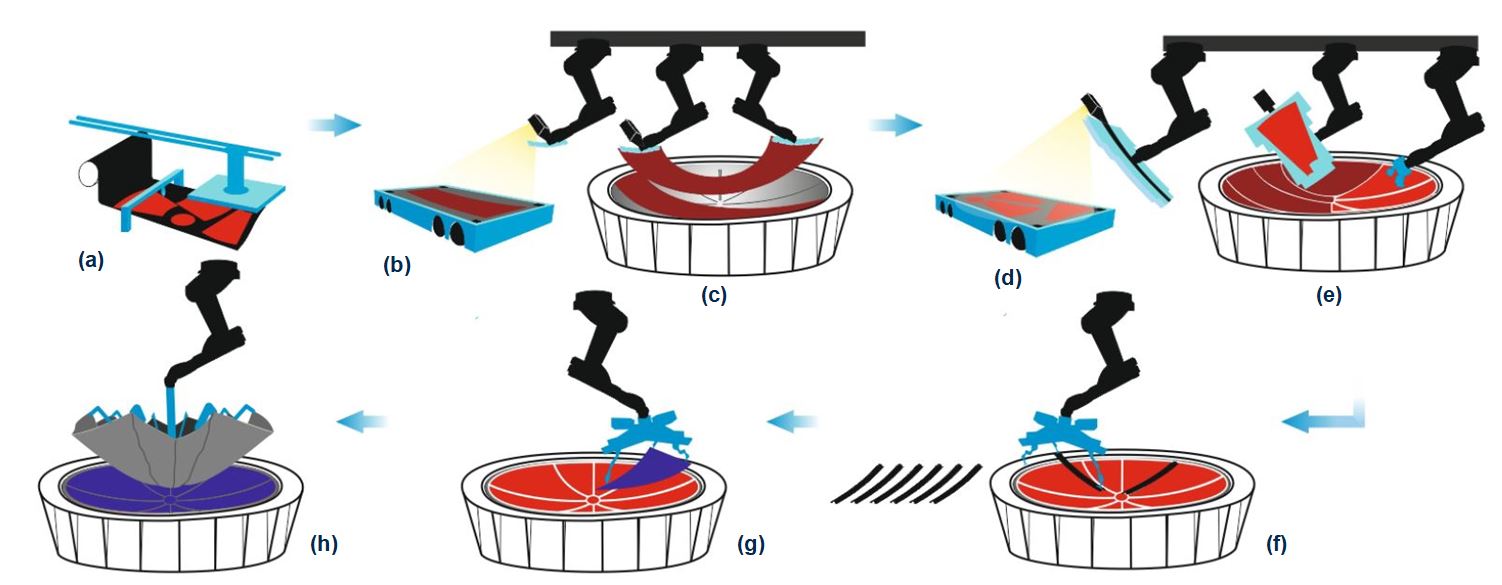
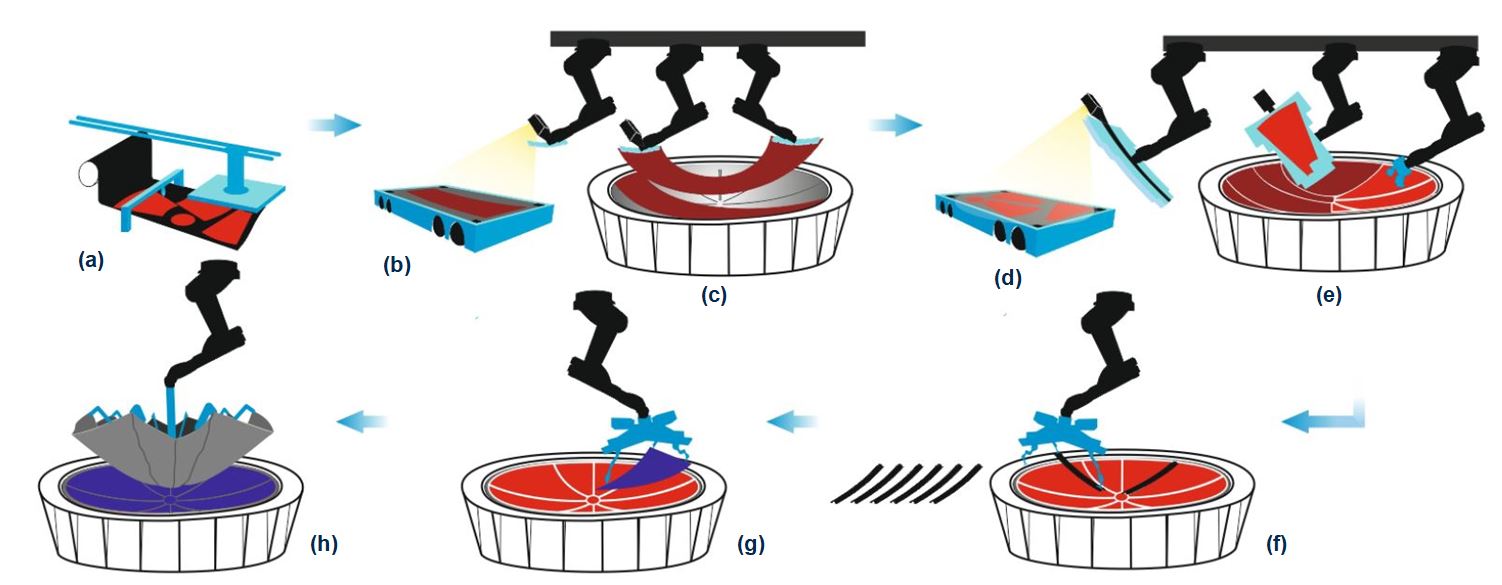
"Het ontwikkelen van gereedschappen en grijpers die de nodige precisie bij het draperen en hanteren konden bereiken, was een van de grootste uitdagingen", merkt Larsen op. Dit was deels te wijten aan de complexe mix van lagen waarvoor drie verschillende drapeermechanismen nodig waren:
- Aanbrengen van materiaal over de volledige breedte direct vanaf de rol die zich moet aanpassen aan de vorm van de mal.
- Draperen van grote structuurlagen waar twee robots samenwerken, één per stofrand, om de doelgeometrie van de mal op te pakken en te creëren om ervoor te zorgen dat het zich zonder kreukels aanpast voordat u het plaatst.
- Accommodatie voor kleine, gevormde lagen tot 1,5 bij 2,5 meter .
“Voor de samenwerkende robots hebben we eindeffectors ontwikkeld die uit zes modules bestaan die door sferische verbindingen met elkaar zijn verbonden”, legt Larsen uit. "Hierdoor kan de eindeffector vervormen, op een manier die vergelijkbaar is met een slang, in overeenstemming met de doelgeometrie van de mal. Geïntegreerde verwarmingsapparaten activeren het bindmiddel in de stof terwijl het wordt getransporteerd en gevormd, en behoudt zijn 3D-vorm en positie zodra het is geplaatst."
Geautomatiseerde drapering en plaatsing
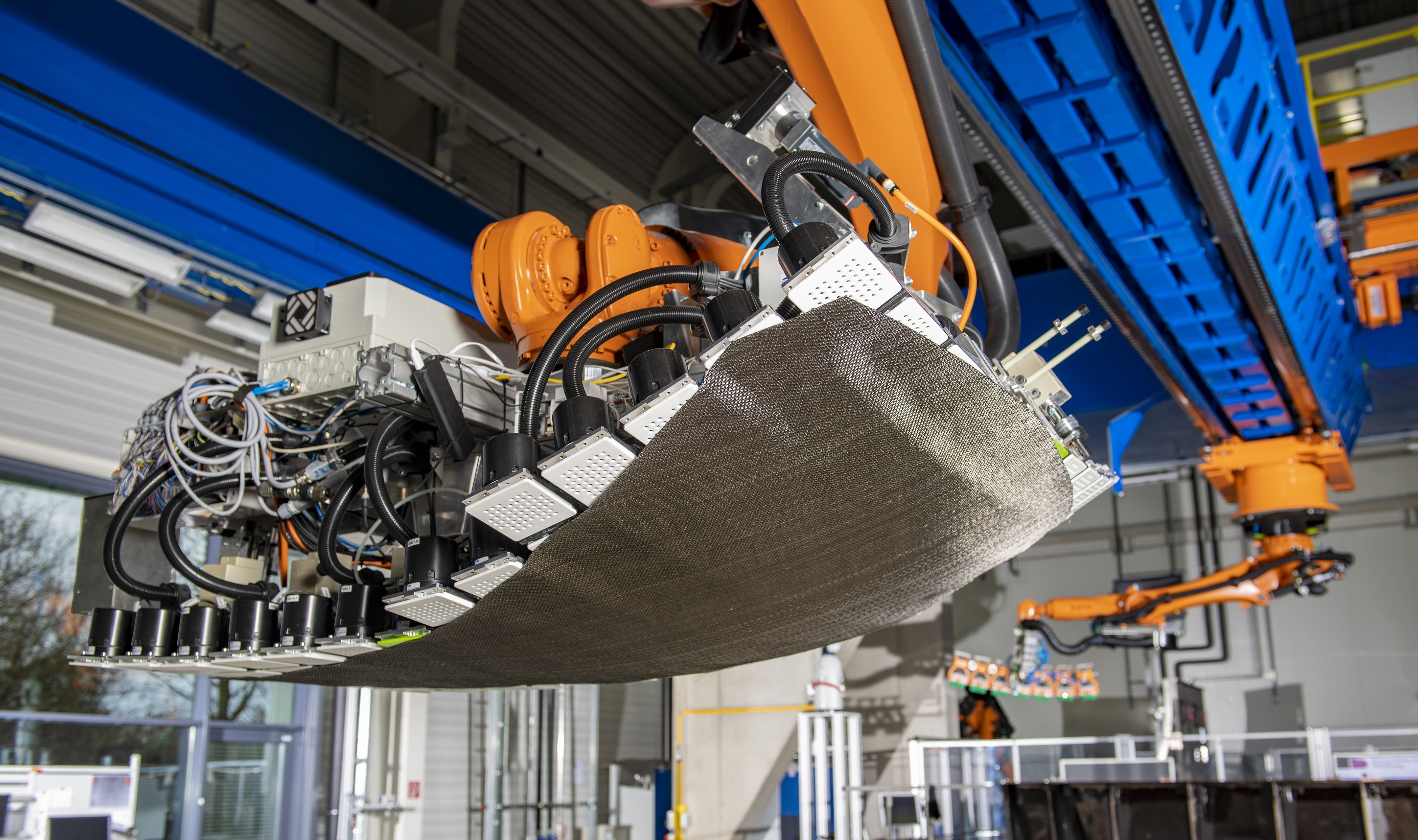
De eindeffector is voorzien van een grijper die 127 modules gebruikt die zijn uitgerust met vacuümzuiging om gesneden lagen stof op te pakken, vervolgens om te zetten in een 3D-vorm en ze vervolgens te verwarmen voordat ze in de mal worden geplaatst. Photo Credit:German Aerospace Center (DLR) Institute of Structures and Design
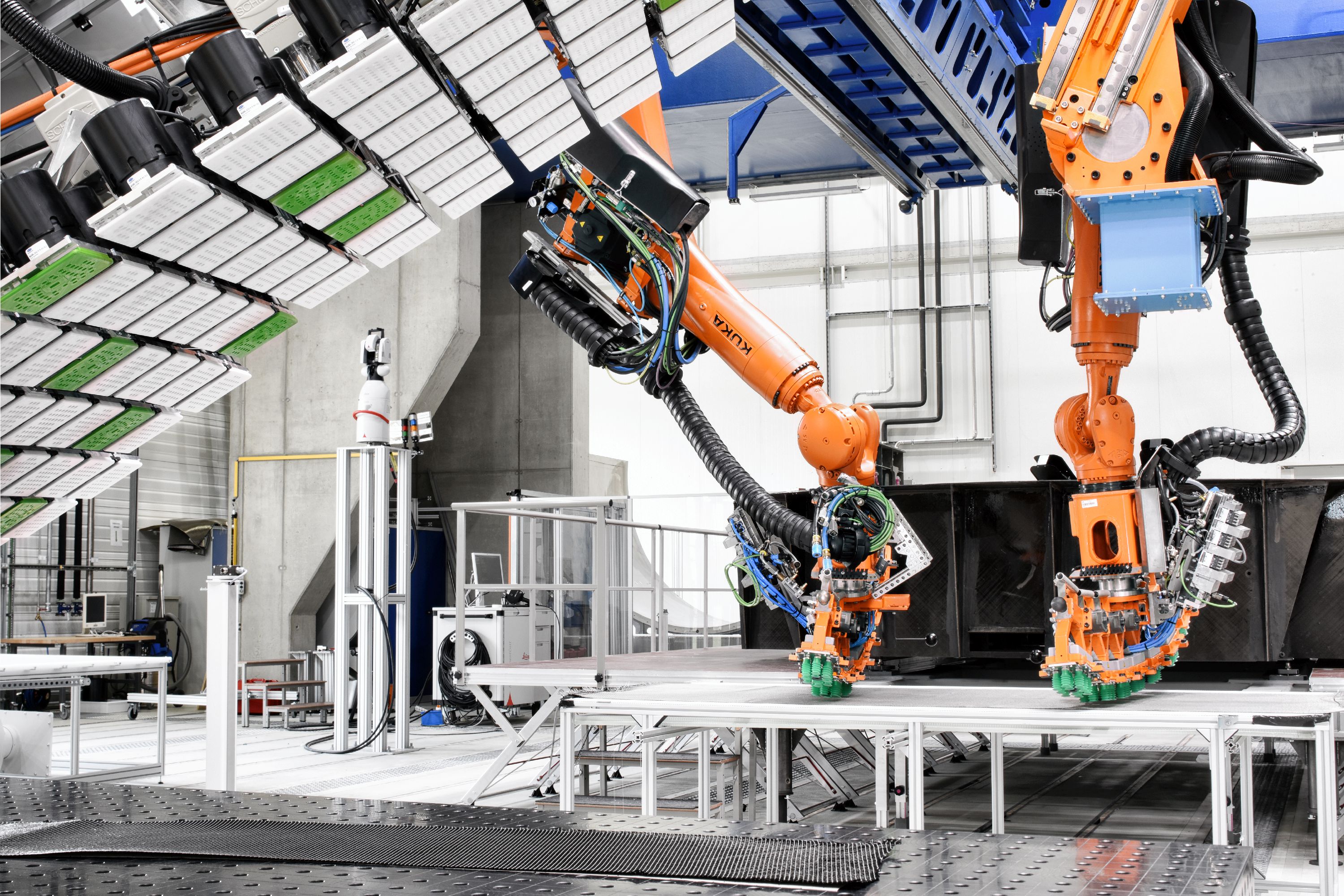
Hier zijn zowel de grijper met 127 modules (links) als samenwerkende robots (achtergrond) te zien. Photo Credit:German Aerospace Center (DLR) Institute of Structures and Design
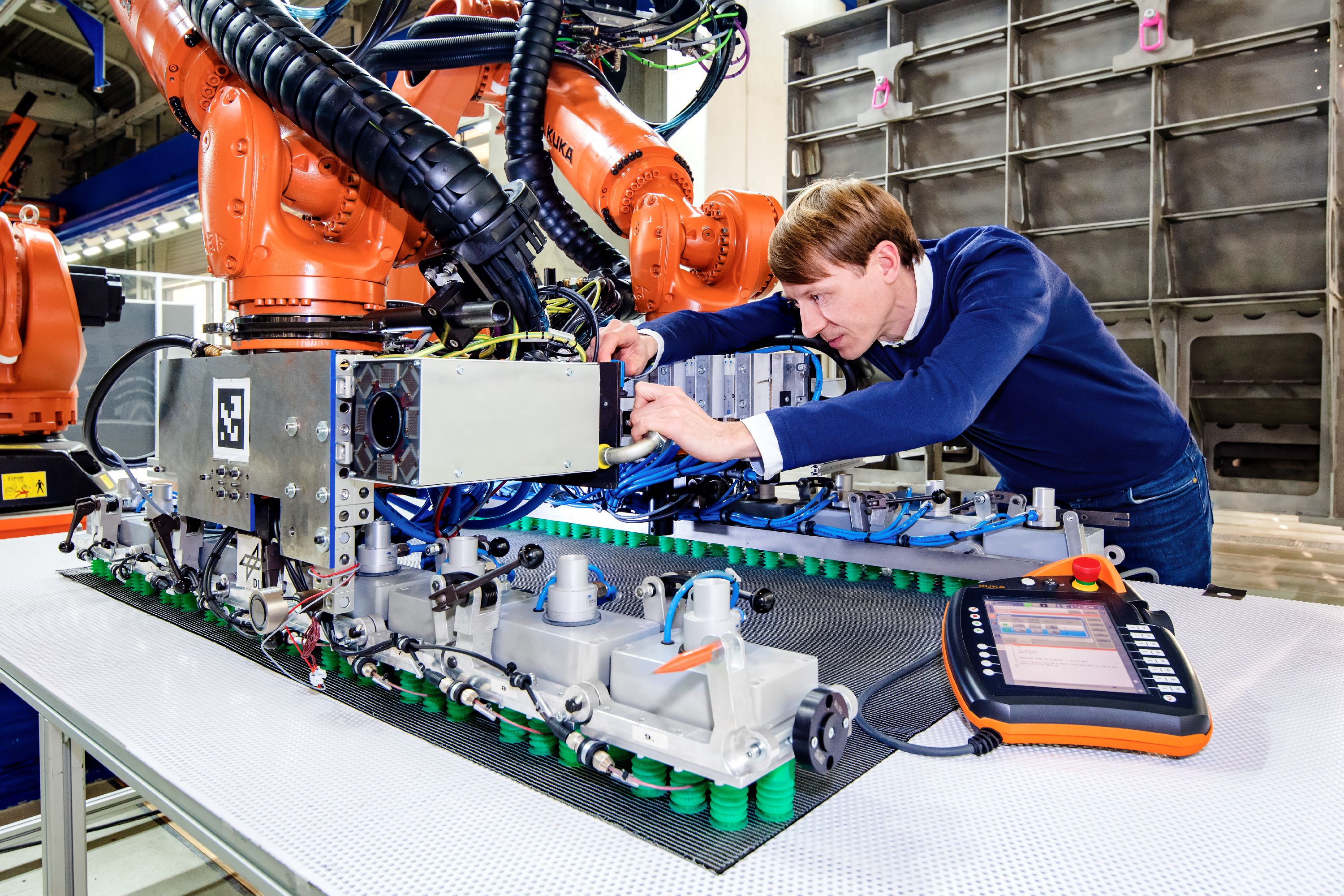
Voor de samenwerkende robots zijn end-effectors ontwikkeld die zes modules bevatten die door sferische verbindingen met elkaar zijn verbonden. Photo Credit:German Aerospace Center (DLR) Institute of Structures and Design

Elke robot pakt een rand van de grote stoflaag op. Ze werken vervolgens samen terwijl ze de laag transporteren om de vereiste doelgeometrie te creëren voordat de stof in de mal wordt geplaatst. Photo Credit:German Aerospace Center (DLR) Institute of Structures and Design
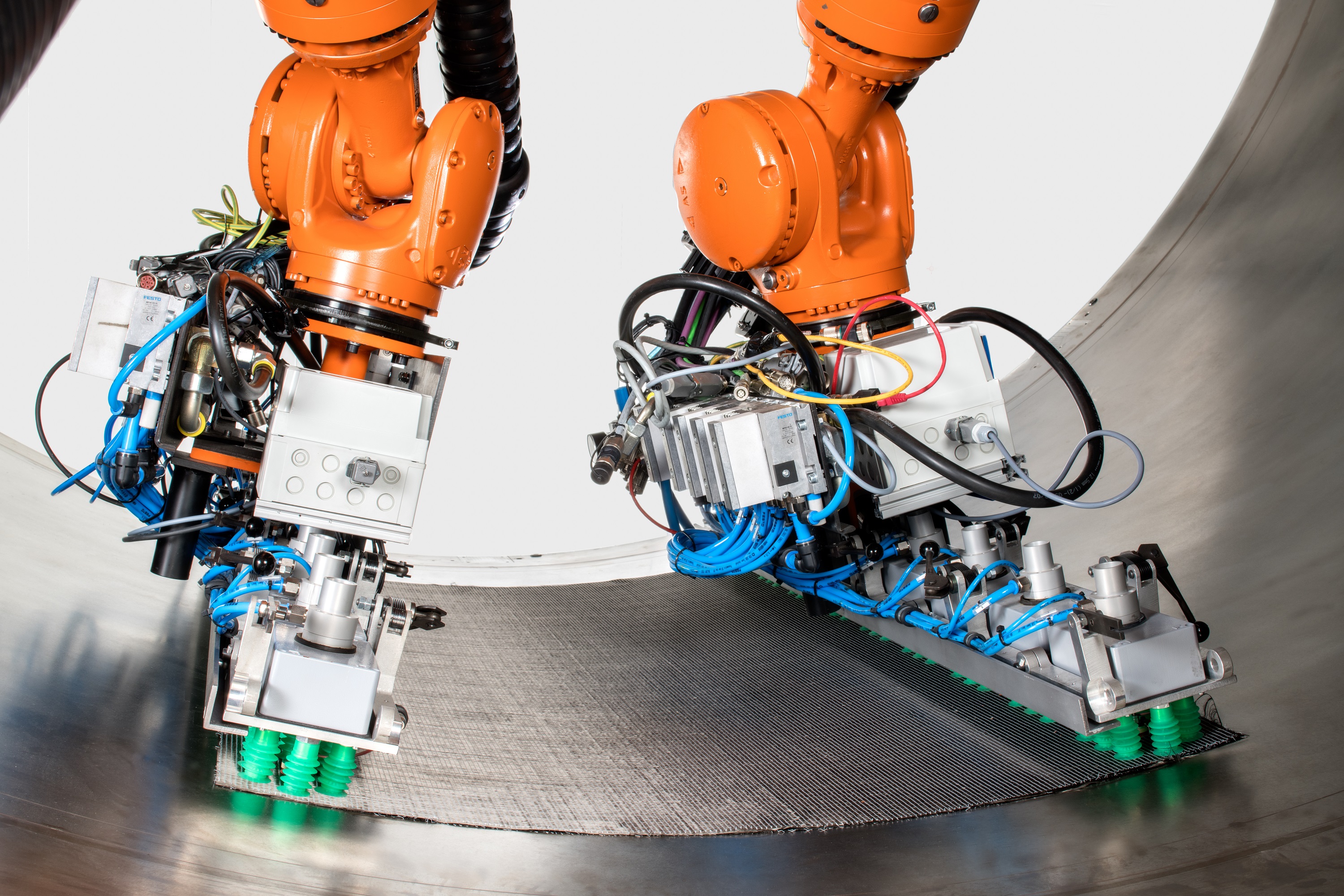
Photo Credit:German Aerospace Center (DLR) Institute of Structures and Design
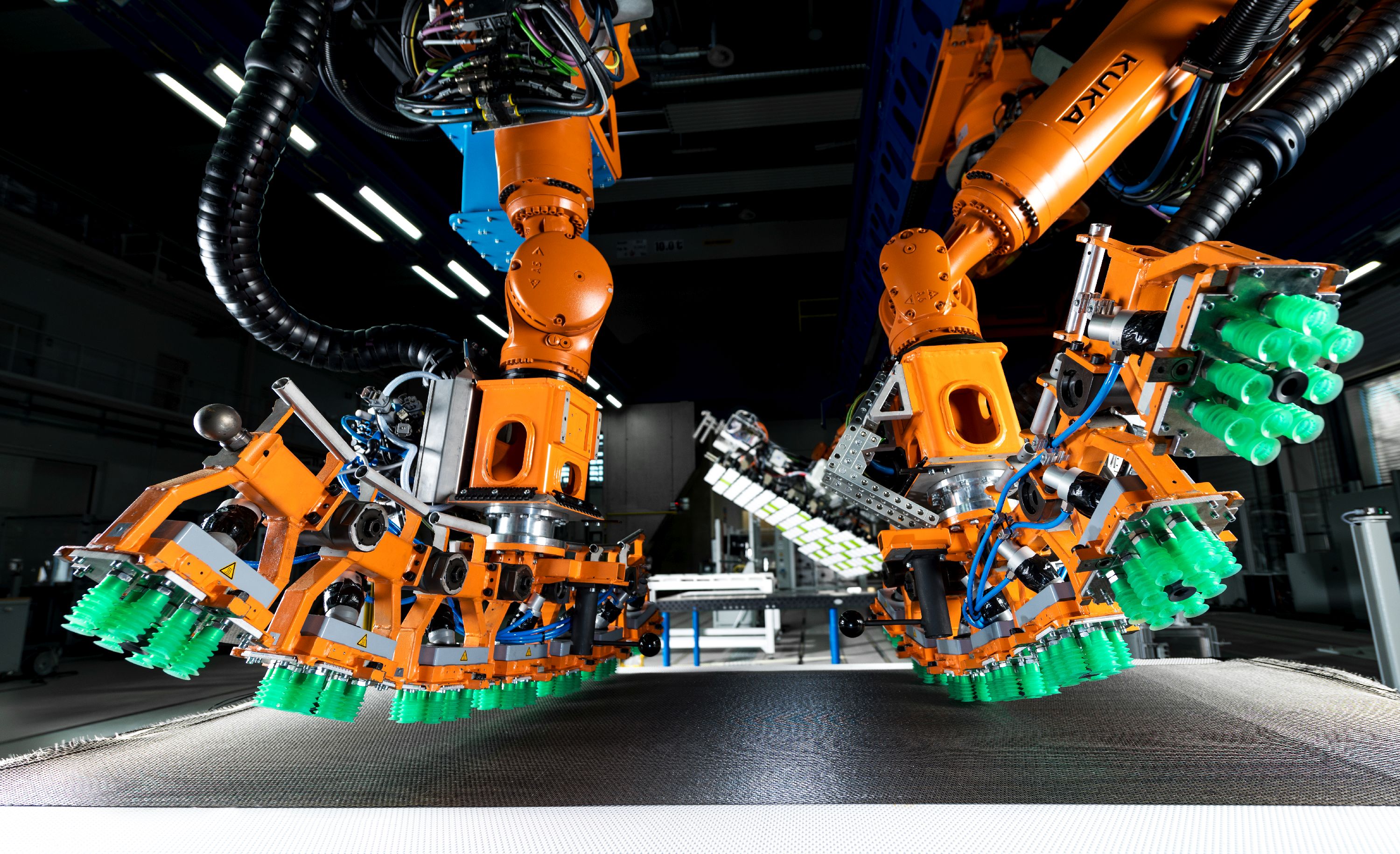
Close-up van de collaboratieve robot-eindeffectors. Photo Credit:German Aerospace Center (DLR) Institute of Structures and Design
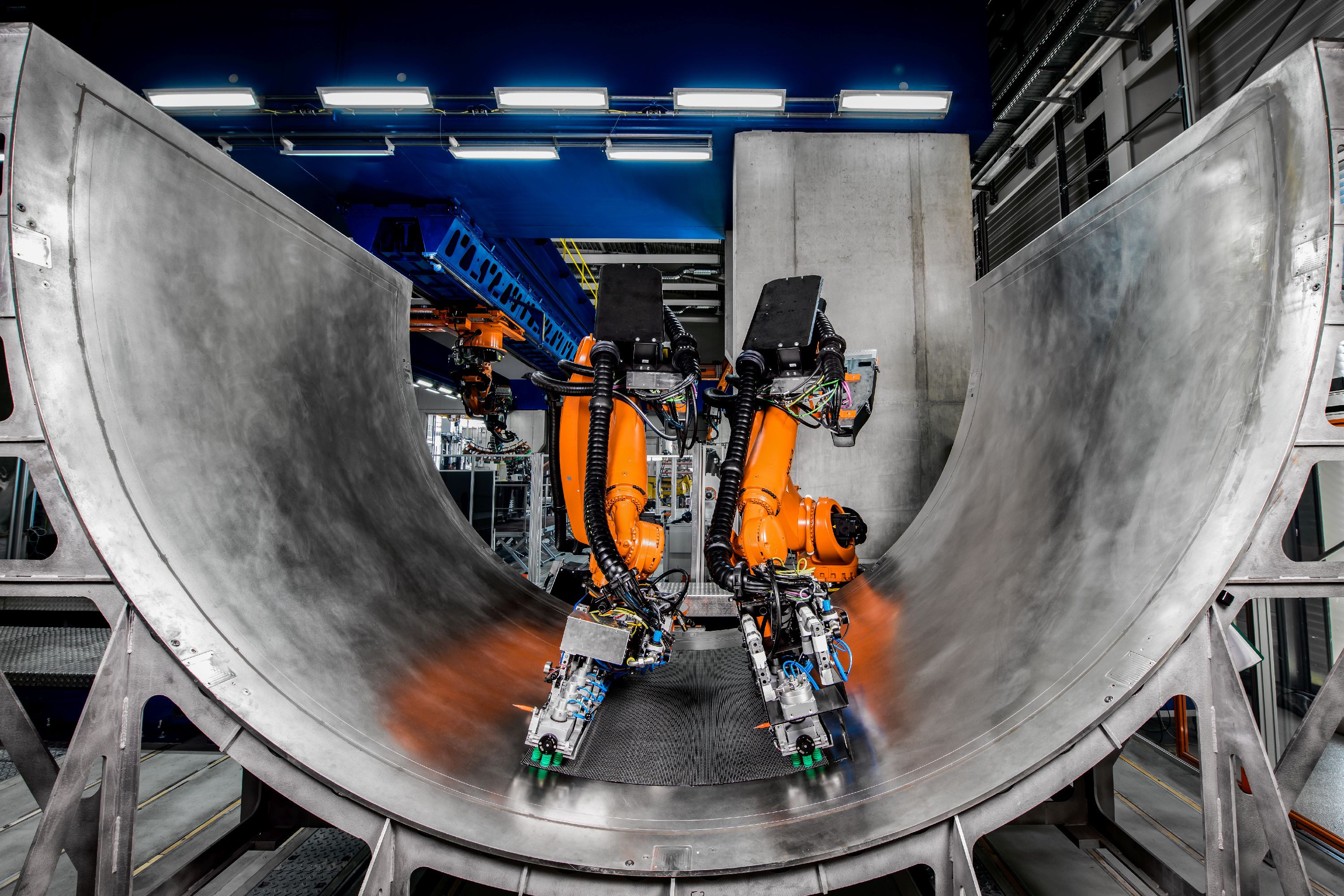
Dit systeem dat DLR in eerste instantie ontwikkelde voor een A320-achterdrukschot, is nu ook gedemonstreerd voor een romppaneel en is ontworpen om flexibel te zijn voor een verscheidenheid aan grote aerostructuren, op basis van hun digitale ontwerpbestanden, zonder de robots opnieuw te leren. Photo Credit:German Aerospace Center (DLR) Institute of Structures and Design
Vorige volgendeVoor de kleine, gevormde lagen tot 1,5 bij 2,5 meter werd een tweede soort grijper ontwikkeld die gebruik maakt van 127 modules uitgerust met vacuümzuiging voor het oppakken. "Deze grijper pakt materiaal in 2D-staat op en buigt het vervolgens naar de doelgeometrie", legt Malecha uit. “Het moet beslissen welke van de 127 modules het stevig vasthoudt en welke het laat schuiven om de 2D-laag om te zetten in een 3D-vorm. Het lijkt dus erg op hoe handen werken om te draperen. We hebben veel geëxperimenteerd en ervaring opgedaan over waar te houden en waar te lossen. Kracht kan worden aangepast door hoe intens de modules grip op het materiaal hebben.”
Inline inspectie. Optische sensoren in de modulaire grijpers bewaakten het drapeerproces. Na het plaatsen van een laag, inspecteert een eindeffector die een Leica T-Scan (Hexagon Manufacturing, Cobham, U.K.) en een cameragebaseerd vezelhoekmeetsysteem van Profactor (Steyr, Oostenrijk) combineert op kwaliteit. "We hebben eerst de vezelhoeken gemeten en vergeleken met het CAD-bestand", zegt Malecha, "en daarna hebben we de randen van elk stuk gemeten en de positie vergeleken met het CAD-bestand."
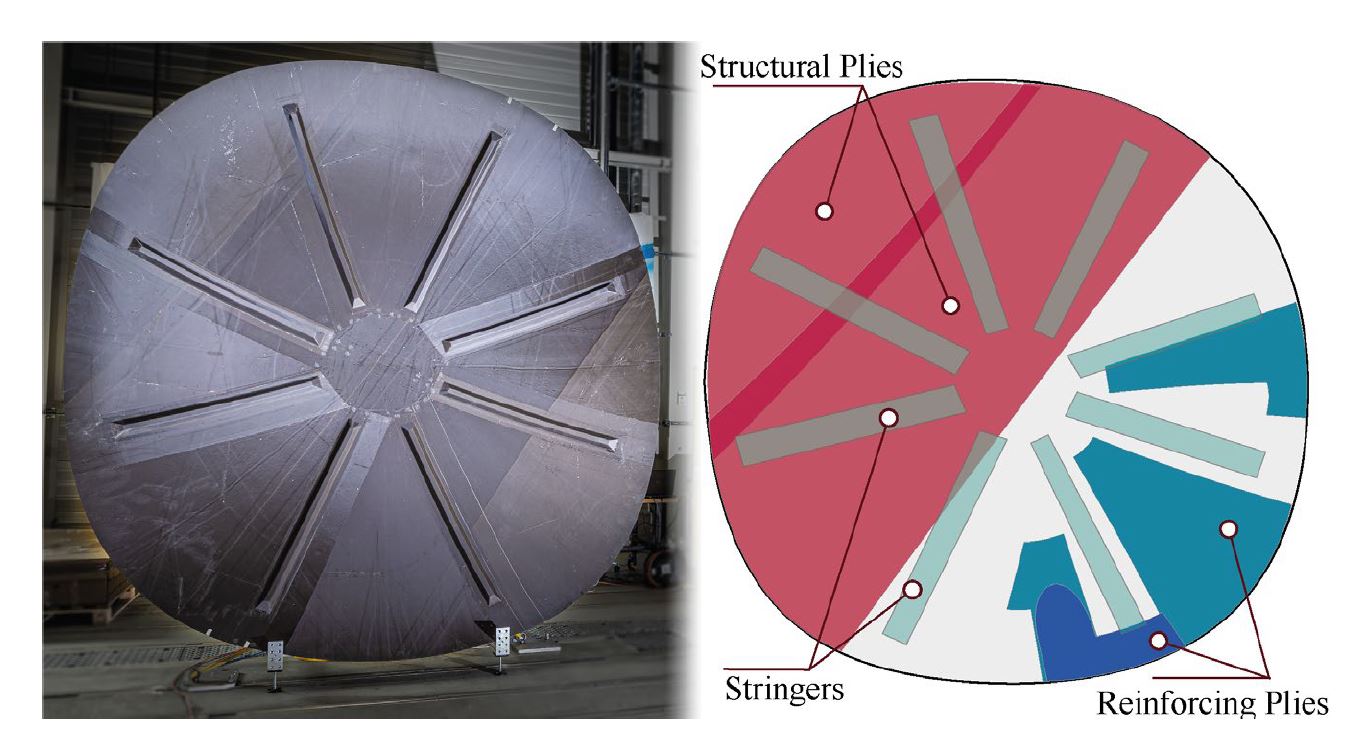
Stringers en vacuümzakken. Na het voltooien van de preform werden er acht verstijvers (stringers) bovenop bevestigd. Voor deze taak is de Multi Kinematic Gripper ontwikkeld en ook gebruikt om de vacuümzakhulpstoffen aan te brengen. Deze grijper bestaat uit drie kleine en onafhankelijke 6-graden-van-vrijheid (DOF)-robots en een stijve arm, allemaal gemonteerd op de middenflens van een industriële 6-DOF-robot. Hulpmaterialen voor vacuümzakken - peel-ply, geperforeerde lossingsfilm en harsstroommedia (hulpmaterialen aan de kant van het gereedschap) - werden voorgesneden en vooraf verbonden, ontworpen voor waar ze werden geplaatst. "Ze hoefden niet te worden gedrapeerd, ze moesten gewoon worden geplaatst", merkt Malecha op. Het geprefabriceerde semi-permeabele membraan werd op een semi-automatische manier aangebracht via een eindeffector met een "paraplu-achtig" mechanisme, terwijl het plaatsen van plakband en buitenste vacuümzak handmatig bleef maar ook geautomatiseerd kon worden.
Cyclustijd en kosten. Voor Malecha was de grootste uitdaging het bouwen van het modulaire, op kunstmatige intelligentie (AI) gebaseerde fabricage-uitvoeringssysteem (MES) om de procesketen te bewaken en te beheersen. "We moesten databeheersystemen bouwen die heel verschillende processen konden samenbrengen en deze vervolgens via de MES via één gegevensuitwisselingspoort kunnen besturen", legt hij uit. "We kunnen ze meteen gebruiken wanneer ze nodig zijn, waardoor meer flexibiliteit en breder gebruik mogelijk is in plaats van een strikte productieorder te volgen."
De PROTEC NSR-technologie werd gevalideerd door in januari 2019 een demonstratiemodel op ware grootte te produceren en medio 2019 een volwassenheidsniveau van TRL 5-6 te bereiken. Vergeleken met de huidige state-of-the-art bij PAG, verkort deze geautomatiseerde procesketen de cyclustijd van het aanbrengen van opgerolde stof met 58% en de pick-and-place van gesneden lagen met 50%. De fabricagekosten voor deze bewerkingen werden met respectievelijk 11,5% en 31% verlaagd.
Thermoplastische RPB
"Dit project begon in 2018 met PAG en Institut für Verbundwerkstoffe (IVW, Kaiserslautern, Duitsland) om te laten zien wat er mogelijk is met thermoplastische composieten in grote onderdelen en primaire structuren", legt Dr. Stefan Jarka, projectmanager voor Fast Lane RPB en expert op lastechnologieën bij ZLP Augsburg. “Een RPB is niet echt primair, omdat de mechanische eisen niet zo hoog zijn als een vleugel of romp, maar het laat zien wat er mogelijk is voor grote, platte, licht gebogen constructies. In slechts vier maanden tijd hebben we een demonstrator A320 RPB ontwikkeld als voorbeeld van hoe je een bestaande aluminium structuur kunt omzetten in thermoplastische composieten.”
Deze demonstrator gebruikte Cetex koolstofvezel (CF) weefsel/polyfenyleensulfide (PPS) organoplaat (Toray Advanced Composites, Nijverdal, Nederland) en weerstandslassen. Een weerstandselement tussen de twee te lassen oppervlakken genereert warmte en blijft in de gelaste structuur. GKN Fokker (Hoogeveen, Nederland) gebruikt deze techniek al tientallen jaren om landingsgesteldeuren en vaste voorranden van vliegtuigen te produceren. Voor deze A320 RPB gebruikte het ZLP-team een CF-weerstandselement in plaats van conventioneel roestvrijstalen gaas.
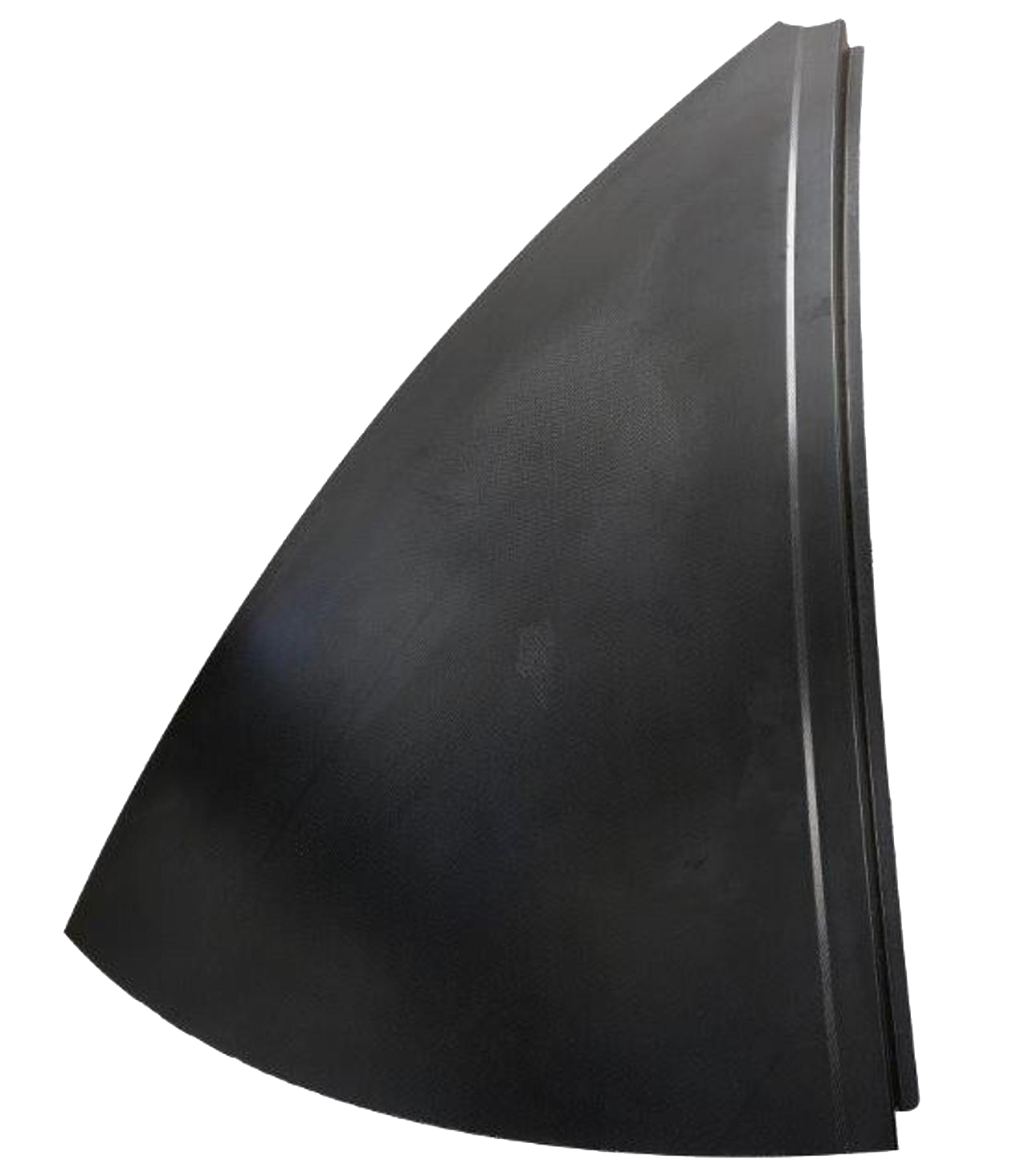
"De thermoplastische composiet RPB zou dezelfde prijs of goedkoper zijn, maar het materiaal is veel duurder", merkt Larsen op. Lagere productiekosten als gevolg van automatisering waren dus essentieel, evenals het gebruik van acht identieke bloembladsecties. "Deze secties waren nodig om de dubbel gebogen vorm van het onderdeel te vormen", legt Jarka uit. “Thermovormen als één onderdeel zou een zeer grote pers vergen die te duur zou zijn. Zo werden acht kleinere secties geperst door de IVW met behulp van aangepaste metalen gereedschappen en we assembleerden deze met behulp van geautomatiseerd lassen. Het automatiseringsniveau voor thermoplastisch persvormen is hoger dan voor thermohardende composieten. Je gebruikt meestal aangepaste metalen gereedschappen, waarbij een hoge maar constante temperatuur het belangrijkste probleem is, maar dit maakt de geautomatiseerde perscyclus ook erg snel.”
De algemene processtappen voor de demonstrator RPB worden getoond in Fig. 2. "Het lasproces dat we gebruikten was niet nieuw", zegt Jarka, "maar moest verder worden ontwikkeld om de 1,5 meter lange [en 40 millimeter lange brede] naden voor het onderdeel met een diameter van 3 meter en integreren een kwaliteitscontrolesysteem. Componenten werden eerst op de juiste positie gefixeerd met behulp van een positioneringsmal en vervolgens werd elektrische energie toegepast om de plasticsmelt in de laszone te genereren.”
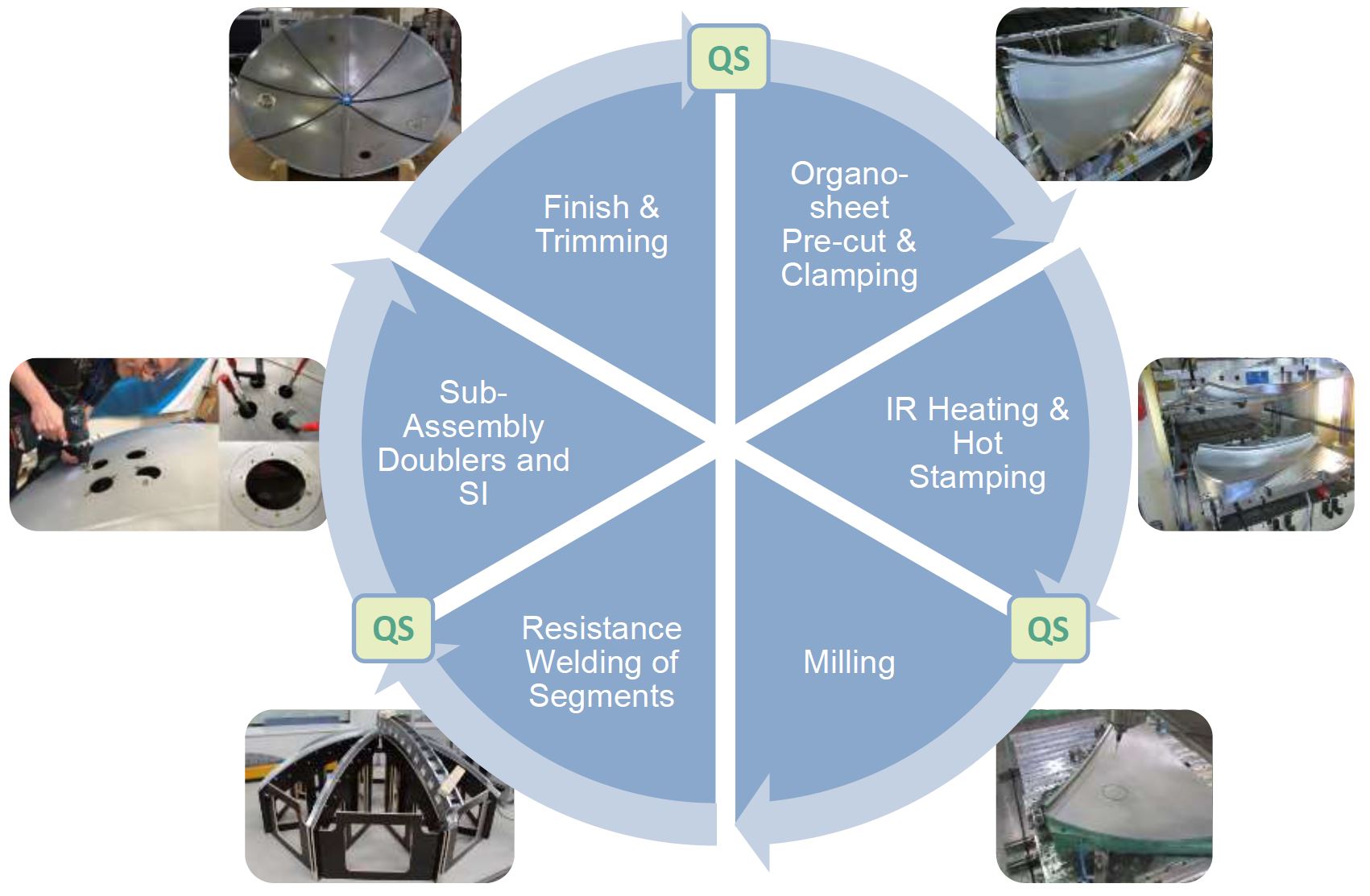
Afb. 2. Thermoplastische RPB-processtappen
Processtappen die werden gebruikt om acht secties (onderkant) van door een stempel gevormde CF/PPS-organoplaat te produceren die vervolgens werden samengevoegd via weerstandslassen om een demonstrator A320-schot te vormen. Photo Credit:German Aerospace Center (DLR) Institute of Structures and Design
QA integreren. "We hebben thermografie geprobeerd, zowel met flitslamp als met ultrasoon geactiveerd, maar het is niet zo eenvoudig om de laszone hiermee te meten", legt Jarka uit. "Thermografie is erg snel, maar het vertelt je niet gemakkelijk of je een goede consolidatie hebt." In plaats daarvan gebruikten ze een standaard testopstelling om meerdere gelaste monsters te maken, waarbij stroom, spanning en temperatuur werden gemeten. “Vervolgens hebben we ze gecontroleerd met ultrasoon testen (UT) en correlaties gemaakt tussen procesparameters en een goede consolidatie”, zegt Larsen. “Als we goede parameters hebben, dan hebben we een goede rol. We hebben ook een processimulatie gebouwd om de gegevens die we tijdens het lassen verkrijgen te vergelijken met de initiële baseline die we hebben vastgesteld.”
Automatisering en cyclustijd. "Het hele proces was erg snel, op de schaal van auto-onderdelen", zegt Jarka. "We hebben TRL 3 behaald in onze beoordeling van 2019 en zijn sindsdien uitgegroeid tot TRL 4. We zullen eind 2021 TRL 6 bereiken." Vóór de pandemie had PAG aangegeven dat het de thermoplastische RPB in 2021 in productie zou nemen. Hoewel de toekomst nu minder duidelijk is, wordt de thermoplastische RPB nog steeds gezien als de "romp van morgen", waardoor het gewicht van 41 naar 35 kilogram kan worden verminderd. en montagetijd met 75% en de totale kosten van onderdelen met meer dan 10%.
TS- en TP-composieten vergelijken
"De thermoplastische processen zijn zo snel dat je goedkoper kunt zijn dan aluminium en zelfs een productiesnelheid van 100 vliegtuigen per maand kunt halen", zegt Jarka. “De RPB is een goede toepassing voor thermoplastisch lassen maar ook voor automatisering”, zegt Malecha. "De droge vezel, vloeibaar gevormde RPB is duurder om te automatiseren."
“Maar die automatisering is interessant omdat je echte winst zou kunnen behalen door slechts enkele deelprocessen te automatiseren”, zegt Larsen. "Door bijvoorbeeld de hulpapparatuur te automatiseren, konden we het vacuüm verpakken in ongeveer een uur voltooien, ongeveer 10 keer sneller dan het handmatige proces." Hij geeft echter toe dat de kosten een groot obstakel vormen om een dergelijke verbetering door te voeren. “De kosten van de digitale tools, robots en ontwikkeling zijn te hoog voor één onderdeel, zoals de RPB. Maar als we een modulaire aanpak zouden kunnen ontwikkelen waarbij je dit systeem voor veel onderdelen zou kunnen gebruiken, dan zouden deze kosten breder kunnen worden gespreid, waardoor het betaalbaar wordt als het wordt berekend met minder tijd en arbeid.” ZLP heeft dit inderdaad bereikt, zoals uitgelegd in CW ’s juli 2020-functie:"Composieten 4.0:digitale transformatie, adaptieve productie, nieuwe paradigma's."
"Er zijn nog niet veel vergelijkingen tussen thermohardende en thermoplastische composietstructuren", zegt Malecha. "Maar we beginnen thermohardende en thermoplastische processen te vergelijken." Hij merkt op dat het volgende doel is om aan te tonen dat thermoplastische laslijnen de eigenschappen hebben die nodig zijn voor vliegtuigvleugels en rompen. En die prestatie moet ook worden aangetoond voor bijvoorbeeld grote, geïntegreerde vloeibaar gegoten vleugels. Dit is precies wat de MFFD- en WOT-programma's hebben willen bereiken. En we wachten op hun resultaten, evenals die van vele andere Clean Sky 2- en EC-projecten, om de volgende stappen voorwaarts te laten zien.
Hars
- Blog:Spuitgieten van vloeibaar siliconenrubber
- EconCore thermoplastische honingraatpaneelproductietechnologie
- Karl Mayer lanceert productielijn voor thermoplastische UD-tapes
- INEOS Styrolution gaat productielocatie bouwen voor StyLight thermoplastisch composiet
- Herone-productietechnologie wint JEC Innovation Award
- Thermoplastische overgegoten thermoharders, cyclus van 2 minuten, één cel
- LANXESS breidt productiecapaciteit voor continue vezelversterkte thermoplastische composieten uit
- Airtech lanceert materialen voor vacuümzakken op hoge temperatuur voor thermoplastisch gieten
- Finex-proces voor de productie van vloeibaar ijzer
- Geautomatiseerde productie van olie-boorkoppelingen
- Geautomatiseerd vanaf het begin