Het museum van de toekomst bouwen
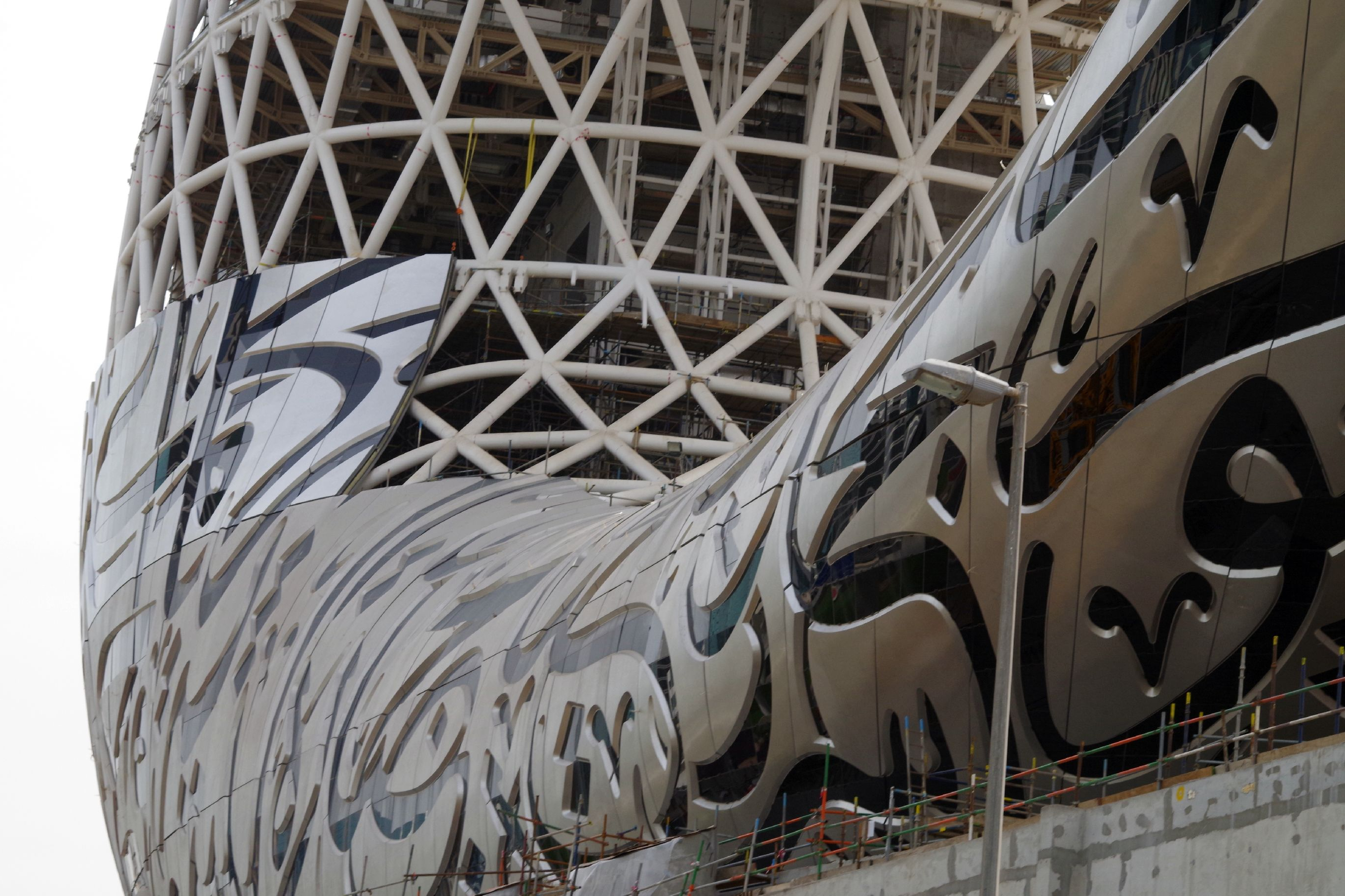
Het Museum van de Toekomst dat momenteel wordt gebouwd in Dubai, Verenigde Arabische Emiraten (VAE), is een van de meest complexe bouwwerken ooit gebouwd. Het 78 meter hoge gebouw herbergt zeven verdiepingen in een torusvormige schaal die bovenop een podium van drie verdiepingen ligt. De buitengevel van de torus bestaat uit 1.024 brandvertragende (FR) composietpanelen. Elk paneel is bekleed met roestvrij staal, heeft een unieke 3D-vorm en integreert ingegoten Arabische kalligrafie. Het vloeiende script vormt gedichten die de visie op de toekomst van Dubai beschrijven door Zijne Hoogheid Sheikh Mohammed bin Rashid Al Maktoum, vice-president en premier van de VAE en heerser van het emiraat Dubai. Ze dienen ook als ramen van het gebouw, werpen daglicht door het kolomvrije interieur en creëren 's nachts een dramatisch effect via 14 kilometer geïntegreerde led-verlichting.
Ontworpen door Sheikh Mohammed als een broedplaats voor innovatie en uitvinding, wordt het Museum van de Toekomst beschouwd als een van de meest geavanceerde gebouwen ter wereld, een plek waar mensen nieuwe technologieën kunnen ervaren en onderzoeken. Het is ook een symbool van architectuur die grenzen verlegt via digitaal ontwerp en gebruik van efficiëntere materialen. Parametrisch ontwerp werd gebruikt om de stalen diagrid te ontwikkelen - een raamwerk van 2.400 diagonaal kruisende stalen elementen - waaraan composietbetonvloerplaten en 17.000 vierkante meter composietbekleding zijn bevestigd, de laatste met behulp van 1 miljoen vierkante meter multiaxiaal glas en koolstofvezelversterkt epoxy prepreg.
Affan Innovative Structures uit Dubai leverde het composietontwerp voor de panelen, evenals de fabricage en ondersteuning voor installatie. "Dit is de eerste keer dat een dergelijk project is uitgevoerd", zegt de CEO van het bedrijf, Dr. Amer Affan. "En ook de eerste keer dat composietpanelen zijn gebruikt om meerdere gebouwfuncties te integreren via dergelijke complexe vormen."
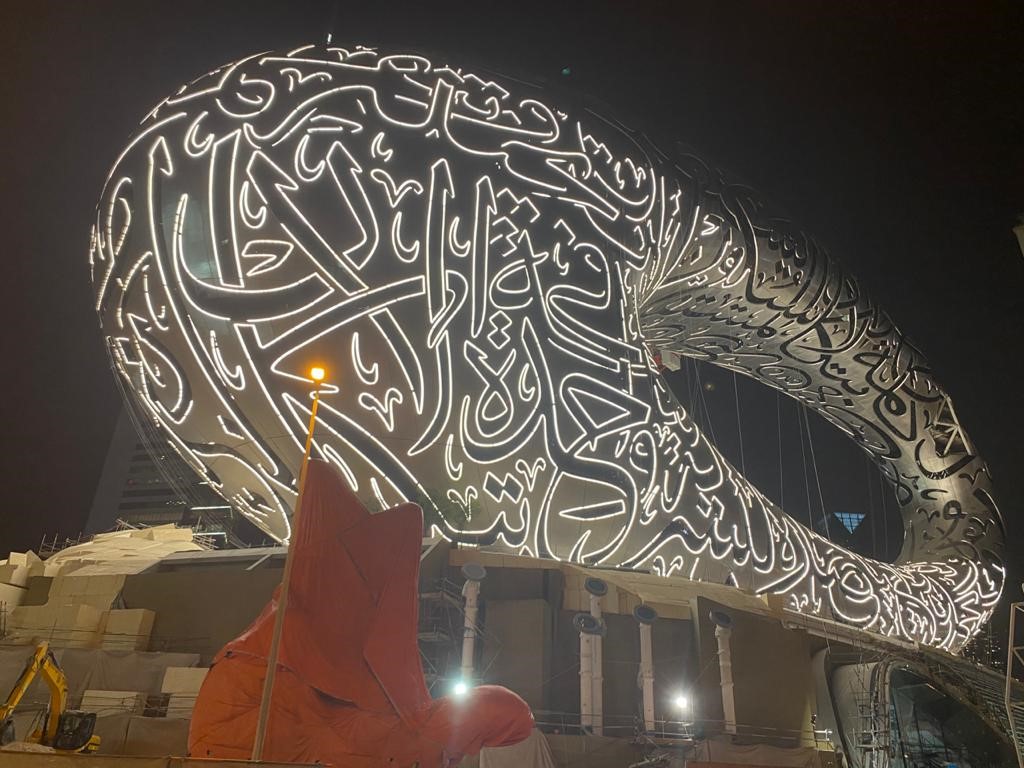
Hoofdarchitect Shaun Killa legt uit dat dergelijke complexe buitenkanten normaal gesproken regenschermen zijn, met daarachter een gebouw dat het waterdichtingssysteem bevat. "Dit vereenvoudigt de zaken omdat het een beetje meer vergevingsgezind is bij het maken van deze zeer driedimensionale vormen", merkt hij op. "In dit gebouw doet de envelop echter de waterdichting, de luchtdichtheid, de structuur en de verlichting." Affan geeft toe dat zijn bedrijf voor zo'n groots project klein is, "maar we hebben onze technische expertise gebruikt om iets unieks te bereiken en hebben laten zien hoe gebouwen in de toekomst zullen worden gebouwd."
Capaciteit in complexe, digitale ontwerpen
Affan Innovative Structures werd aanvankelijk gecontacteerd door het engineeringteam van Museum of the Future. "Er waren niet veel bedrijven die het benodigde werk voor de buitenbekleding konden doen", merkt Affan op. “De enige andere concurrent stelde een normale vliesgevel voor met aan de buitenzijde aluminium of RVS panelen.” Gordijngevels, die doorgaans worden gebruikt als aanvulling op een structureel stalen frame, zijn dun en gemaakt van aluminium frames die glas, metalen en/of dunne stenen buitenpanelen ondersteunen (zie “De bouwschil:FRP unitized gevels”). Dit werd door het engineeringteam afgewezen als te moeilijk en niet in staat om dezelfde uitstraling te geven als mogelijk was met een geïntegreerde, multifunctionele composiet paneelgevel. Zo werd de laatste, voorgesteld door Affan Innovative Structures, geselecteerd voor het project. "We hebben ook een unieke technologie waarmee we grote panelen kunnen maken," voegt Affan toe, "tot 3 meter breed en 9 meter hoog, gebogen in beide richtingen, wat minder voegen betekent."
Affan Innovative Structures was bij uitstek geschikt voor dit project. Het bedrijf, opgericht in 2004 door Dr. Affan, biedt complete kant-en-klare oplossingen — van conceptontwerp tot installatie en onderhoud van het gebouw — die zich richten op zeer technische uitdagingen. Het cv van het bedrijf omvat het complexe, geometrische aluminium scherm/bekleding voor het King Abdullah Sports City Stadium (Jeddah, Saoedi-Arabië), de samengestelde ingangsluifel en 64 glazen en stalen dakramen met ingewikkeld patroon voor de Yas Mall (Abu Dhabi, VAE) , het composiet buitendak voor het Sidra Hospital (Doha, Qatar) en vele andere uitdagende projecten. Dit vermogen in complexe staal-, glas- en composietconstructies zou precies zijn wat nodig was voor de multifunctionele composietbuitenkant van het Museum van de Toekomst.
"Binnen elk composietpaneel bevindt zich een systeem van vlakglas [panelen] in het Arabische schrift", legt Affan uit. "Het glas is bijna verzonken in de panelen, tot 200 millimeter diep." Deze uitsparing verandert niet alleen van de bovenkant van het gebouw, met minder uitsparing om waterophoping te voorkomen, naar de onderkant, waar verticale en ondersneden panelen diep kunnen worden verzonken zonder water op te sluiten, maar ook binnen elk paneel, schuin en afnemend om een geleidelijk, natuurlijk rand voor het script. "De locatie en randen van de uitsparing varieerden ook per locatie van het glas in het paneel, omdat het glas vlak was, maar de panelen waren gebogen", merkt Affan op. “Dit was alleen mogelijk met digitaal ontwerp en CNC-bewerking.” Deze precisie zou ook nodig zijn om ervoor te zorgen dat het script, dat van het ene paneel tot het andere varieerde, precies werd uitgelijnd op het moment dat de panelen werden geïnstalleerd, zodat de letters en woorden correct over de buitenkant van het gebouw vloeiden.
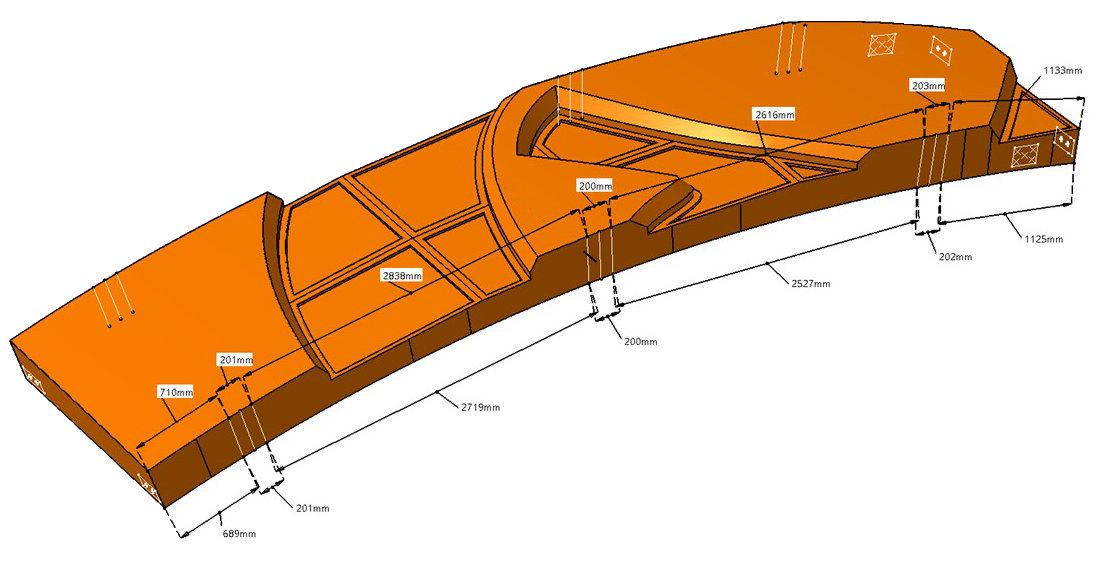
Voor Affan was de enige oplossing om het Arabische schrift en uitsparingen in elk composietpaneel te gieten. "Versterkingen zouden in nauwkeurig CNC-gefreesde mallen worden gelegd", legt hij uit. Toevallig is de CATIA-software (Dassault Systèmes, Vélizy-Villacoublay, Frankrijk) die Affan Innovative Solutions gebruikt om zijn CNC-machines aan te drijven ook het 3D CAD-programma dat door de lucht- en ruimtevaartindustrie wordt gebruikt om complexe vliegtuigen en composietstructuren te ontwerpen. Daarnaast is het team van 28 ingenieurs van Affan ook bedreven in Tekla BIM-software, Rhino 3D (Robert McNeel &Assoc., Seattle, Wash., VS) en AutoCAD van Autodesk. "We hebben alle tekeningen in CATIA gemaakt, evenals het laminaatontwerp, waardoor we in staat waren om dergelijke complexe bewerkingen uit te voeren", zegt Affan.
Het ontwerp was echter niet triviaal en moest voldoen aan verschillende structurele en windbelastingen. Zo zorgde de binnenkant van de torus voor een windtunneleffect, legt Affan uit. Deze panelen moeten tot 450 kg/m kunnen weerstaan 2 (92 lb/ft 2 ) van windbelasting. (Let op, de International Building Code vermeldt windbelastingen van 71 lb/ft 2 voor orkaangebieden met een hoog risico in West Palm Beach, Florida, VS). Ook de composietpanelen voor het Museum van de Toekomst zijn op maat gemaakt om het gewicht te minimaliseren. "De panelen gebruiken 9 tot 13 lagen, die variëren per locatie en belasting", zegt Affan. Hij voegt eraan toe dat het Composite Technology Center (Stade, Duitsland), een dochteronderneming van Airbus en een vaste partner via de handelsorganisatie CFK Valley ev (Stade, Duitsland), "een derde partij heeft gecontroleerd op ons laminaatontwerp, de doorbuiging en stijfheid berekeningen.”
Een extra complexiteit en innovatie is dat de panelen ook hun eigen bevestigingssysteem hebben geïntegreerd. "Aan de randen vormen 24 lagen de cassette-achtige bevestigingsgeometrie om te verbinden met het gebouw", legt Affan uit. Een cassettesysteem is een methode voor het bevestigen van buitenbekleding, oorspronkelijk ontwikkeld voor installaties van het type regenscherm. Hoewel typen en geometrieën variëren, maken cassettes doorgaans een vlak, regenbestendig buitenoppervlak mogelijk dat achter het dragende raamwerk van het gebouw wordt bevestigd. Voor de gevelpanelen van het Museum van de Toekomst waren er geen afzonderlijke stukken nodig om de cassetteranden te vormen, maar werden ze in elke mal machinaal bewerkt en zo geïntegreerd in elk composietpaneel.
Materialen, mallen en paneelfabricage
Hoewel de 10.000 vierkante meter aan composiet fabricageruimte van Affan Innovative Structures 16 harsinfusiemachines en acht op staal gebaseerde harsinfusietafels met glazen bovenkant van 3 meter bij 20 meter heeft, koos het ervoor om prepreg te gebruiken. Waarom? "Om de noodzakelijke FR-prestaties te bereiken, zijn veel additieven nodig, zodat de hars dik wordt en niet zal vloeien in de infusie", legt Affan uit. In dit geval was het additief aluminiumtrihydraat (ATH, zie “Brandbestendig zonder het gewicht”). Hij vervolgt:“Zo hebben we samengewerkt met Notus Composites [Ras Al Khaimah, VAE] om een FR epoxy prepreg te ontwikkelen. We gebruikten voornamelijk glasvezel, maar ook koolstofvezel in bepaalde secties waar er doorbuigingsproblemen waren.” Goedgekeurd door de Dubai Civil Defense, heeft Notus Composites EPFR-609 prepreg, in combinatie met NE11-FR oppervlaktefilm, voldaan aan de NFPA 285, EN13051-1 en ASTM E1098 en E84 klasse A brandvereisten (zie "Brandvertragende prepregs maken .. .” en “Beter, goedkoper afschermen van FRP-bouwmaterialen”).
Omdat externe metalen oppervlakken in Dubai in de zomer temperaturen van 80 ° C (176 ° F) kunnen bereiken, legt Affan uit, "we hebben de prepreg bij 120 ° C uitgehard om voldoende Tg (glasovergangstemperatuur) om doorbuiging van de kop te weerstaan. Zo werden de mallen machinaal vervaardigd uit een polyurethaanschuim dat bestand is tegen die hoge temperatuur, die duurder is. We hebben drie of vier verschillende soorten schuim geprobeerd, maar slechts één kon de temperatuur plus vacuümdruk weerstaan, en was toch zacht genoeg om gemakkelijk en snel CNC te bewerken.
De CNC-bewerking van elke mal duurde 12 tot 72 uur en elk van de 1024 composietpanelen had zijn eigen mal nodig . Alle vier de CMS (Zogno, Italië) 5-assige CNC-machines van Affan Innovative Structures - de grootste van 33 meter lang bij 13 meter hoog en 2,5 meter hoog - waren nodig om te voldoen aan de veeleisende productiesnelheid van het museum. "Als een [machine] defect was voor onderhoud, lieten we de andere parallel draaien", legt Affan uit.
Prepreg-lagen werden gesneden en gekit met behulp van een (Bulmer, Mehrstetten, Duitsland) automatische snijder. "We hebben geen kern in de panelen gebruikt omdat er in die tijd, in tegenstelling tot vandaag, geen schuimkernen waren die aan de FR-vereisten konden voldoen", zegt Affan. Zelfs met een dergelijke automatisering was het personeelsbestand van 250 medewerkers van het bedrijf, een totaal dat het in 2015 had bereikt, ook nodig om de productie te leveren, met een gemiddelde van vier panelen per dag. Teams van zes arbeiders, elk met een supervisor en een uitgebalanceerde set van vaardigheden om efficiënt te zijn, legden de panelen op. "Normaal gesproken zouden er twee of drie teams aan een project werken", merkt Affan op, "maar om aan dit productieschema te voldoen, hadden we op elk moment twintig teams aan het werk."
Productiestappen
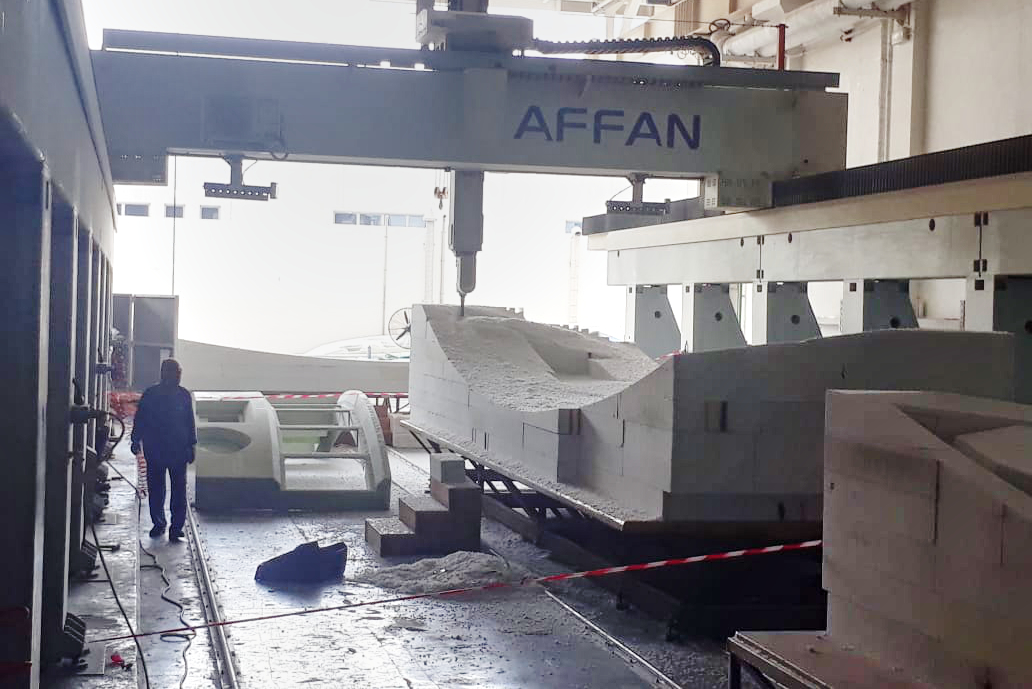
Stap 1Polyurethaanschuim wordt in precisiemallen gefreesd. Bron voor alle afbeeldingen van productiestappen | Affan innovatieve oplossingen
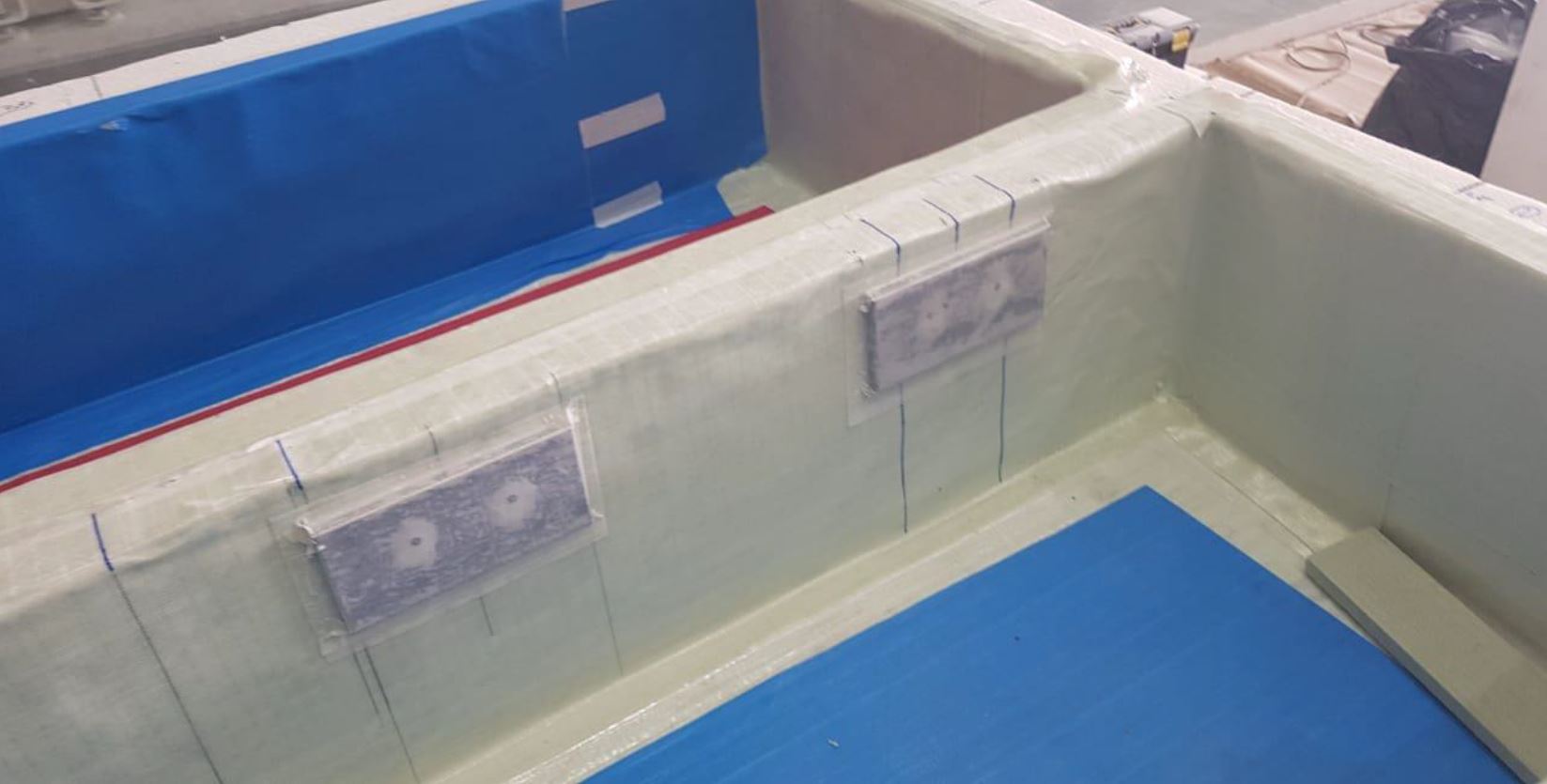
Stap 2Glasvezel/epoxy prepreg wordt met de hand in de mallen gelegd.
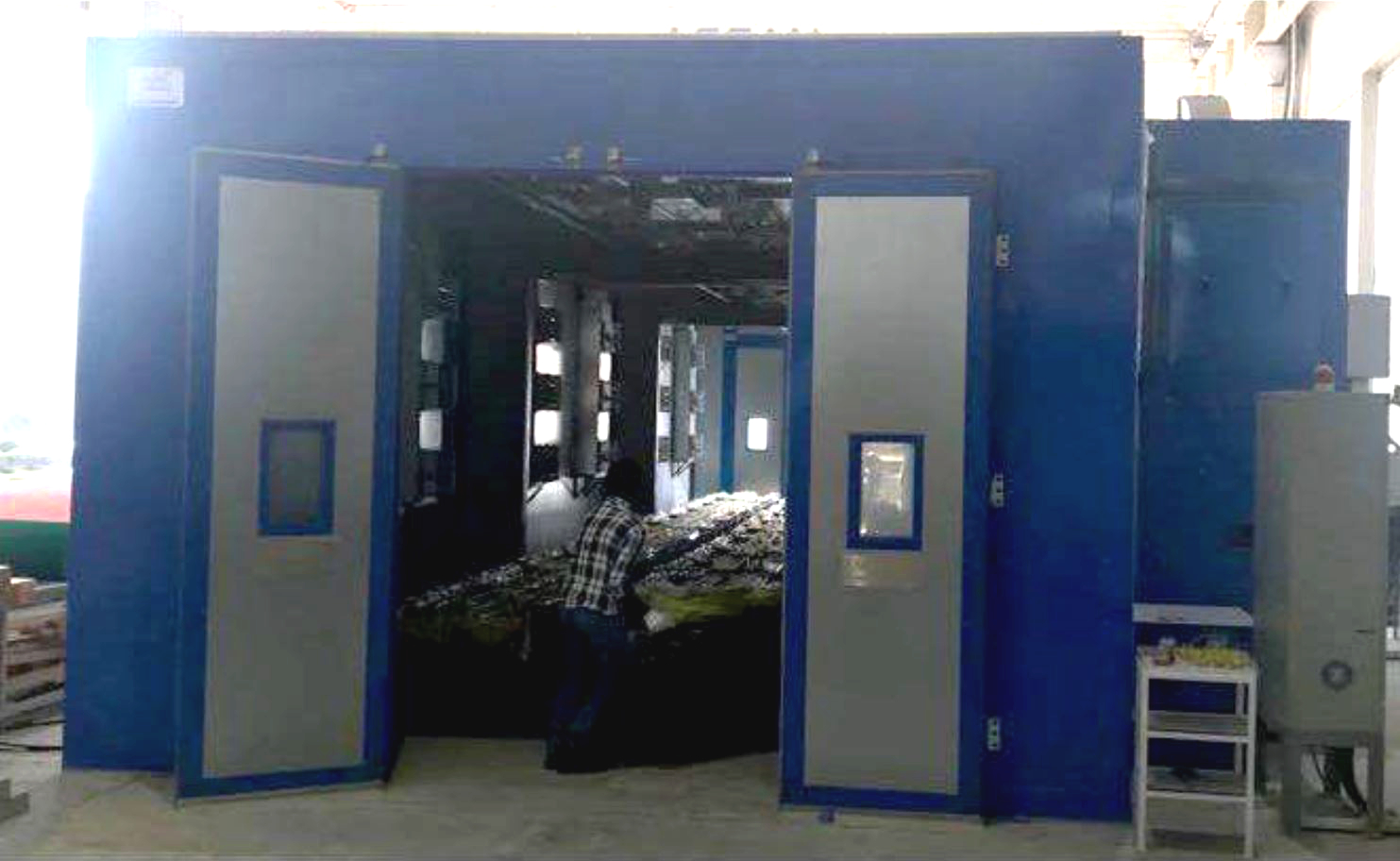
Stap 3Prepreg lay-ups worden vacuüm verpakt en gedurende 6 uur bij 120°C in een oven uitgehard.
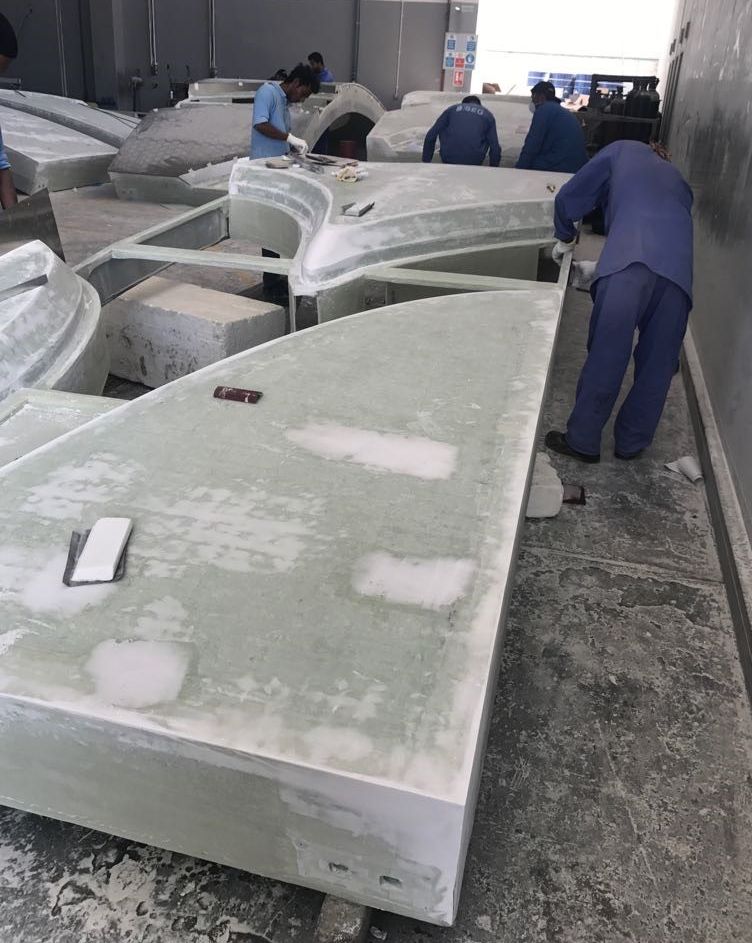
Stap 4Demoulded panelen worden voorbereid voor het verlijmen van roestvrijstalen afwerking.
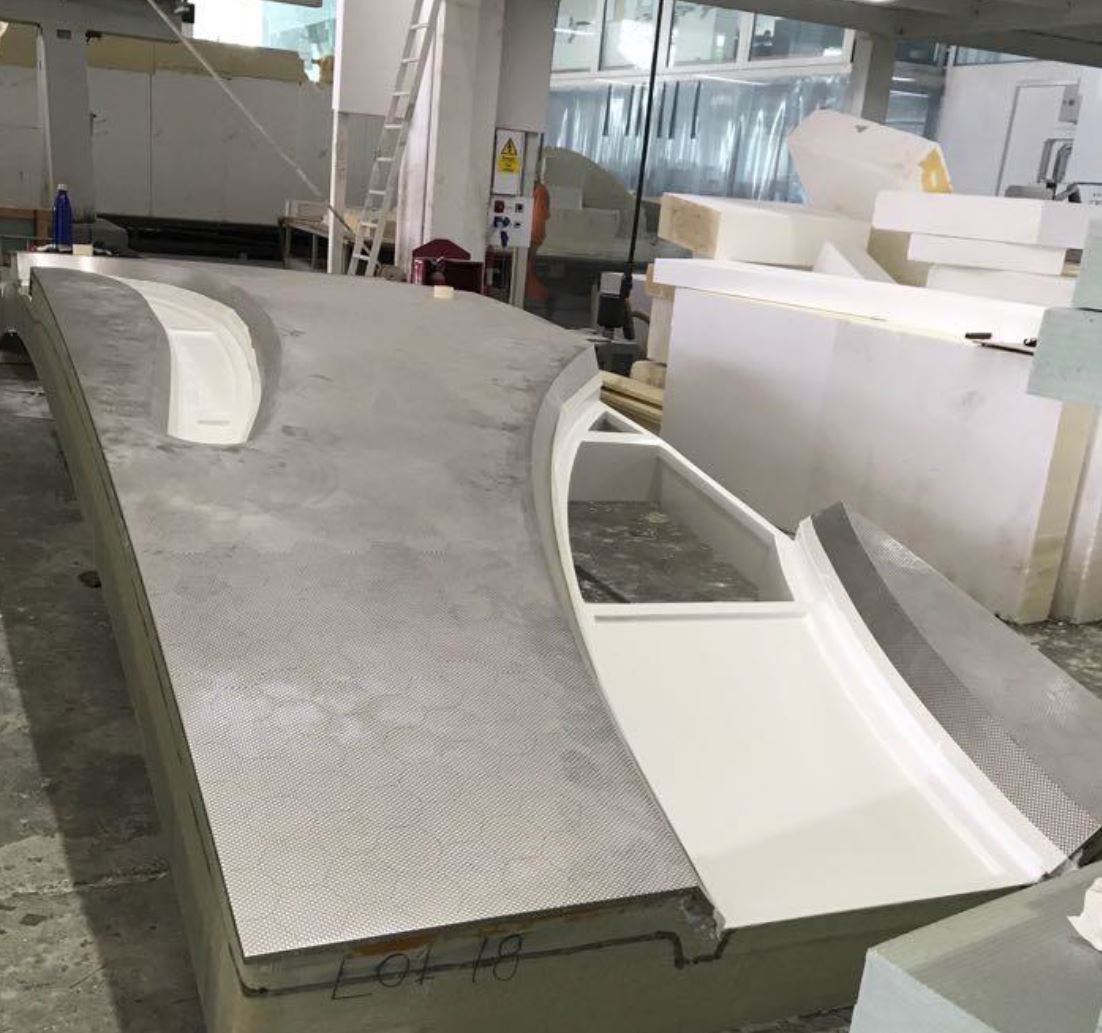
Stap 5Roestvrijstalen zeshoeken worden verlijmd en mechanisch bevestigd aan FRP-panelen.
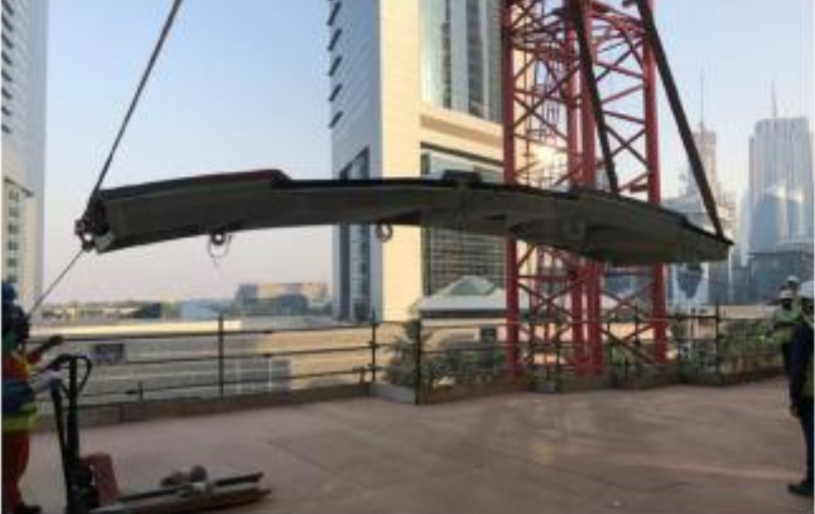
Stap 6 Afgewerkte panelen worden opgetild voor installatie.
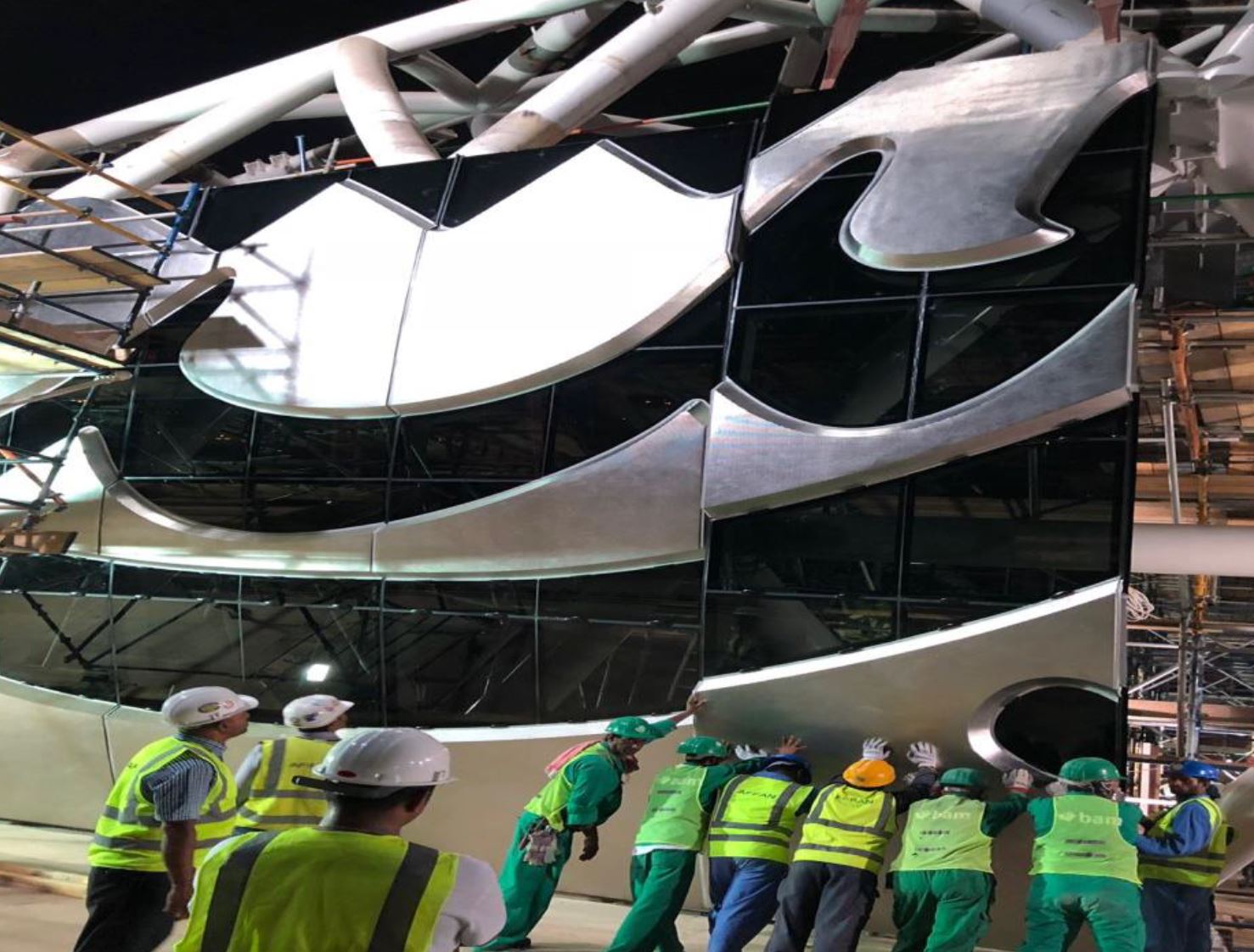
Stap 7Elk paneel wordt aangepast via een unieke 3D “universele verbinding”.
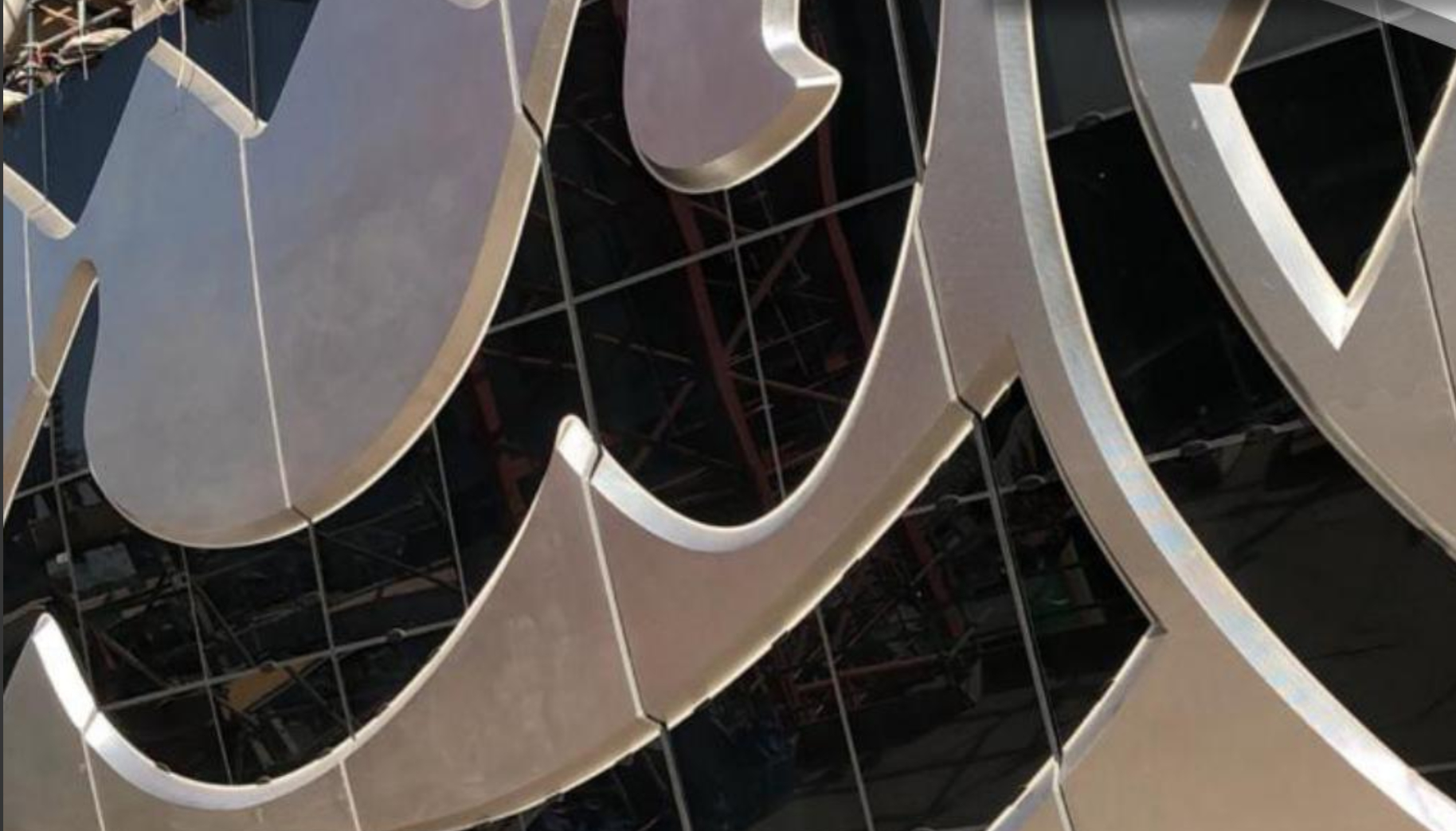
Stap 8Elk paneel wordt aangepast via een unieke 3D "universele voeg" om een soepel uitgelijnde buitengevel te verkrijgen.
Vorige volgendeLay-ups werden met de hand gelegd, vacuüm verpakt en gedurende 6 uur uitgehard in ovens van 20 meter lang, 8 meter breed en 3 meter hoog. “Elke CNC-machine had zijn eigen oven”, zegt Affan. “We hebben niet veel panelen per uithardingscyclus gebundeld. In plaats daarvan, toen elk paneel klaar was, hebben we het onmiddellijk uitgehard om een zo hoog mogelijke productiestroom te behouden. Vervolgens hebben we de panelen uit de vorm gehaald en een 3D-scanner gebruikt om ervoor te zorgen dat het as-made paneel overeenkwam met het CATIA-bestand. Volgens ons totale kwaliteitscontrolesysteem moesten we bij elke stap in het proces de digitale bestanden controleren.”
Afgewerkte panelen kregen vervolgens de roestvrijstalen buitenafwerking. "Het roestvrij staal wordt op elk paneel gelijmd en vervolgens bevestigd met mechanische bevestigingsmiddelen, wat een kunst op zich is", zegt Affan. “Het metaal werd in kleine zeshoeken gesneden om over de 3D-panelen te draperen. Het zeshoekige raster varieerde deel tot deel, afhankelijk van de hoeveelheid kromming. Hoewel we ervaring en vertrouwen hebben in verlijming, bestaat er geen risico dat een enkele zeshoek uit elkaar valt tijdens de levensduur van het gebouw. Dus elke zeshoek moest worden bevestigd - er waren maar liefst 200 tot 300 bijlagen nodig voor een enkel paneel. " De afgewerkte panelen werden vervolgens naar de locatie gestuurd om te worden geïnstalleerd.
NASA-ondersteunde, probleemloze installatie
De installatie is feitelijk voltooid door bouwbedrijf BAM International (Gouda, Nederland) van het gebouw. "We hebben alleen supervisors geleverd voor installatie om te helpen bij het omgaan met de panelen", merkt Affan op. "De manier waarop ze worden opgetild, is de sleutel. De panelen zijn zo ontworpen dat ze sterk genoeg zijn voor ieders specifieke positie in het gebouw. Ze moeten echter op een specifieke manier worden opgetild, via minimaal twee hijspunten, net als bij het ophangen van cassettes bij meer traditionele bouwmethoden.”
Er was nog een ander probleem waarvoor Affan als geen ander gekwalificeerd was om het op te lossen. “Om ervoor te zorgen dat elk paneel op de staalconstructie kan zitten en toch het gladde oppervlak vormt, hadden we de mogelijkheid nodig om het paneel in diepte, oriëntatie en kromming in 3D aan te passen – met andere woorden, een soort universele verbinding met drie vrijheidsgraden . In 1985 werkte ik als student bij NASA in Californië aan demping van ruimtestationconstructies. De sleutel was om elke structuur te kunnen verplaatsen en aan te passen wanneer de shuttle aanmeert, zodat trillingen snel worden gedempt, een beetje zoals ruisonderdrukking. Ik heb dezelfde technologie gebruikt voor de bevestiging en afstelling van het paneel tijdens de installatie.”
Omdat de panelen ook voor de waterdichte afdichting van het gebouw zorgden, mochten er geen openingen tussen de panelen zijn. "De panelen konden niet direct tegen elkaar aanliggen, of ze zouden kunnen barsten", zegt Affan, die uitlegt dat vanwege een hoge belasting van 1,5 ton op de vrijdragende 6 e vloer tentoonstellingsruimte, de staalconstructie beweegt daadwerkelijk. "We hielden een nauwkeurig gespreide opening tussen de panelen en deze werd opgevuld met een speciale pakking." Deze pakking, zacht genoeg om uit te zetten, maar toch stijf genoeg om belasting te weerstaan, zorgde voor afdichtingsfunctionaliteit terwijl het de esthetische uitstraling van het gebouw mogelijk maakte.
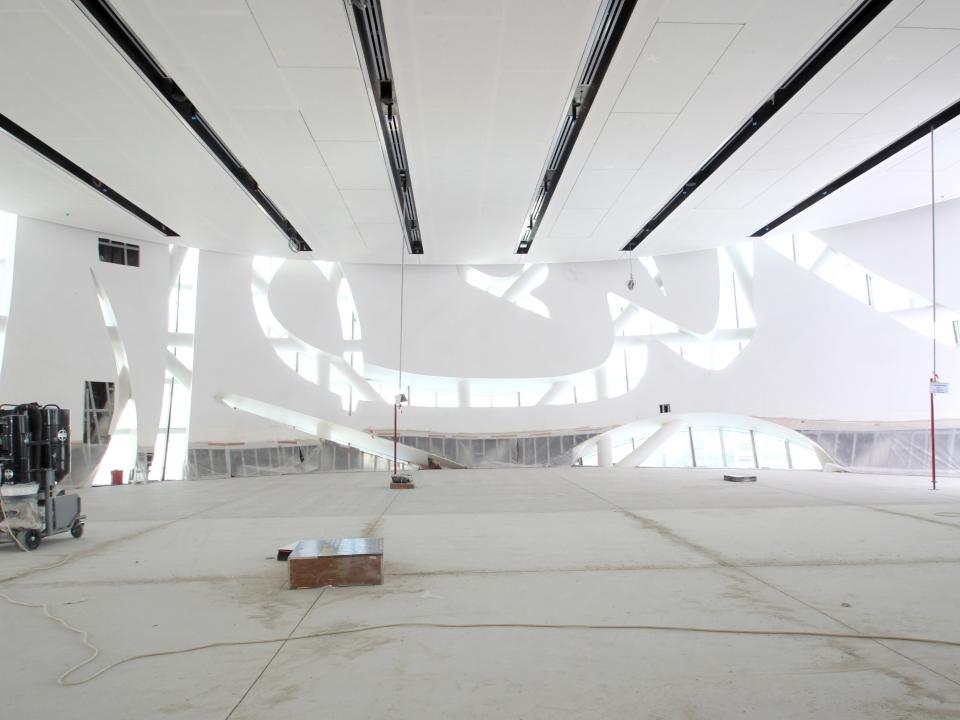
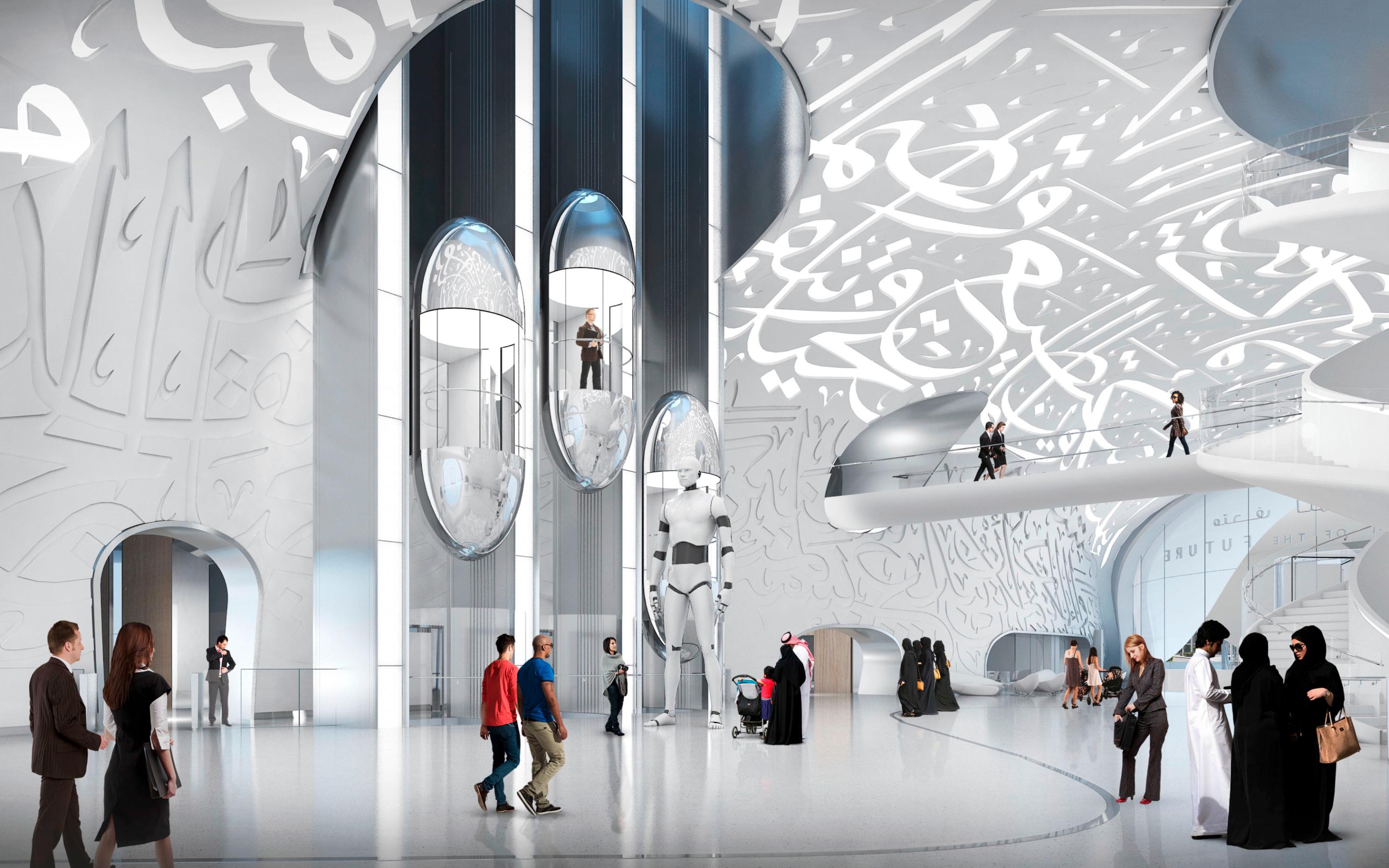
Dergelijke oplossingen zijn een voordeel, merkt Affan op. “Omdat we uit een constructieve achtergrond komen, zijn we in staat om veel materialen te combineren. Dit is erg belangrijk. Composieten zijn slechts één materiaal dat we gebruiken. Dit was niet zomaar een samengesteld project.” De resultaten spreken voor zich. “De installatie is goed verlopen; er waren helemaal geen problemen”, zegt Affan, die opmerkt dat er geen manier was om te controleren of het paneel zou passen, behalve om ervoor te zorgen dat het in overeenstemming was met het digitale bestand. "We hebben nog geen paneel gehad dat niet past of dat de verkeerde vorm heeft of het woord verkeerd is gespeld", getuigde projectmanager Bauly van Buro Happold in een BBC-artikel van Elizabeth Bains.
Toekomstige modulaire constructie
“We hebben het hele proces samen geleid”, vult Affan aan. “Teamwork binnen ons bedrijf zelf stond ook centraal; ontwerp- en lay-upgroepen moesten op elkaar afstemmen. We hebben nog nooit zo'n groot werk gedaan als dit, en het was een uitdaging, maar we houden van uitdagingen."
Helaas heeft COVID-19 zijn tol geëist. "We hebben deze klus net voor de pandemische lockdown afgerond", zegt hij. “Nu zijn we met minder dan 30 mensen. Het is verwoestend. Maar dit heeft iedereen geraakt, niet alleen ons.” En toch ziet Affan hoop voor de toekomst en voor de rol die composieten zullen spelen bij het bereiken van de duurzaamheid en innovatie die de wereld nodig heeft in de bouw. “Vooral in Dubai en de GCC (Gulf Cooperation Council) willen mensen nieuwe ideeën uitproberen. Het toont de toekomst van architectuur en constructie.”
Die toekomst, benadrukt hij, zal zijn voor degenen die modulaire constructiesystemen kunnen gebruiken, “en COVID-19 versnelt dit eigenlijk. Bedrijven bouwen modules in en sturen die naar de site. Dit zal zich ontwikkelen omdat het inefficiënties van de locatie naar een fabriek verplaatst, waardoor de controle en kwaliteit toenemen. Ter plaatse coördineer je alle mensen. Het is tijdverspilling, wachten op andere onderaannemers. Daarnaast ben je afhankelijk van het weer en werkonderbrekingen. Fabricage in een fabriek elimineert dit alles. Omdat ze sterk, licht en duurzaam genoeg zijn om gemakkelijk te vervoeren en te installeren, maken composieten dit type modulaire constructie mogelijk en kun je elke gewenste vorm maken.”
Affan merkt op dat modulaire constructie al jaren wordt gebruikt op cruiseschepen, waarbij elke cabine vooraf is gemaakt, compleet met verwarming/airconditioning, elektrische en sanitaire systemen, en vervolgens als LEGO-blokken in het stalen frame van het schip wordt gemonteerd. “Stel je voor hoeveel tijd je bespaart als elke module al is uitgerust. We zijn nu aan het kijken naar een project om op deze manier met composiet een hoogbouw te maken”, zegt hij. "Als je FR-harsen hebt, heb je de onderdelen die voorheen van metaal waren niet nodig." Onder verwijzing naar een Marriott-hotel dat op deze manier is gebouwd en vorig jaar in New York City is voltooid, voegt Affan eraan toe:"dat gebouw was van staal en hout, maar we kunnen het in composieten bouwen."
Hars
- Cloudbeveiliging is de toekomst van cyberbeveiliging
- De toekomst van snijsoftware
- Edge computing:de architectuur van de toekomst
- De toekomst van fabrieksonderhoud visualiseren
- De toekomst van datacenters
- Betere toeleveringsketens bouwen voor de toekomst
- Slimme gebouwautomatisering en de toekomst van vastgoedontwikkeling in steden
- Bouwen aan de toekomst van werknemerservaring met intelligente automatisering
- Hoe Tech Mahindra de fabriek van de toekomst bouwt
- De toekomst van 3D-printen in de maakindustrie
- Is 3D-printen de toekomst van productie?