Hybride additieve gereedschappen op groot formaat:lichtere, snellere, goedkopere mallen voor grote onderdelen
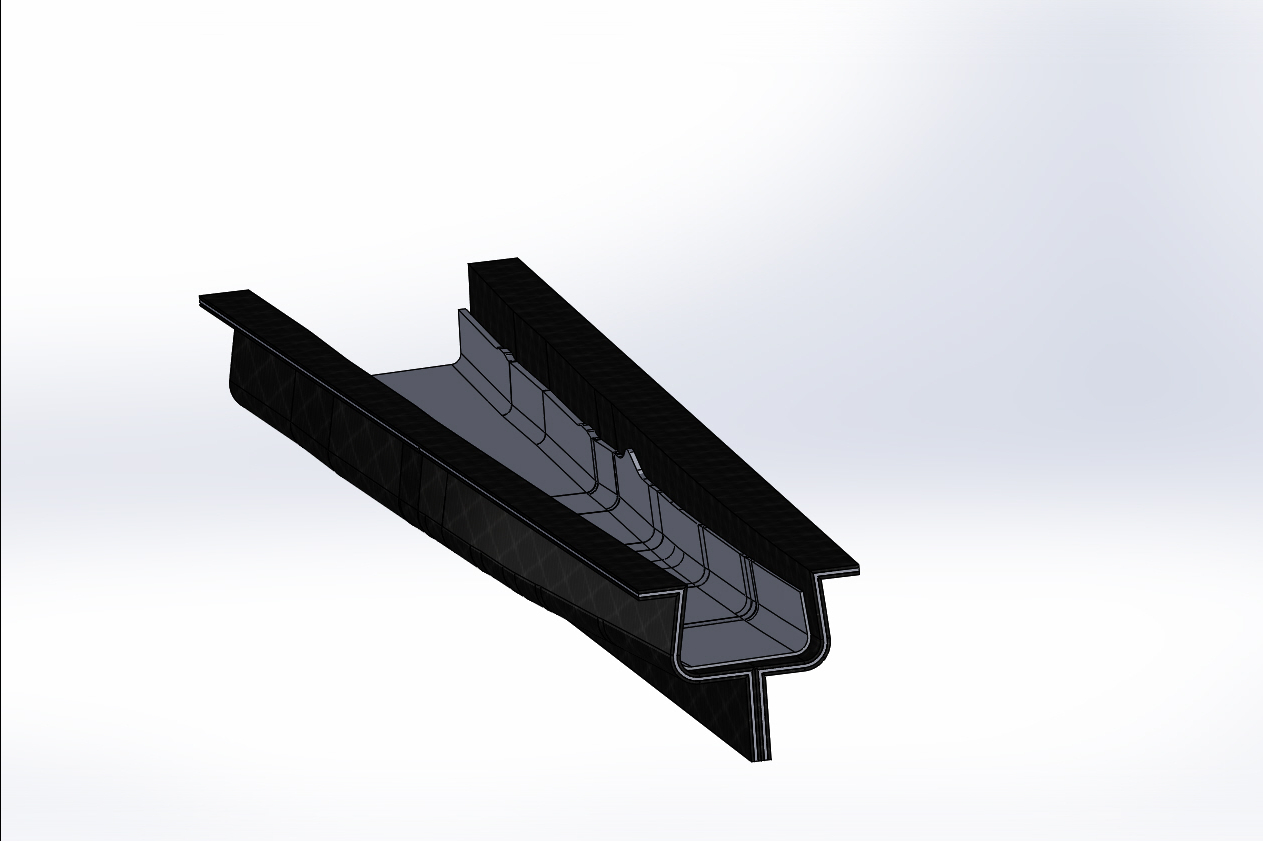
Al meer dan drie decennia omarmt de commerciële luchtvaart steeds meer composietmaterialen. In feite zijn meer dan de helft van de kritische structurele componenten van verschillende modellen van grote commerciële vliegtuigen tegenwoordig composieten. Aangezien het gebruik van deze materialen is toegenomen, zowel in termen van volume als grootte van onderdelen, is het steeds moeilijker geworden om gereedschappen te bouwen — met name betaalbare gereedschappen — om sneller prototypes te maken en deze onderdelen te vervaardigen. De vleugels van de A350 XWB van Airbus SE (Leiden, Nederland) zijn bijvoorbeeld elk 32 meter lang en 6 meter breed en vertegenwoordigen enkele van de grootste composiet luchtvaartconstructies die ooit zijn geproduceerd.
"Er zijn nu zulke baanbrekende productietechnologieën op de markt dat we grote stappen kunnen verwachten in de ontwikkeling van gereedschappen, die ons zullen helpen de uitdagingen aan te gaan waarmee we worden geconfronteerd bij de ontwikkeling van composiet vliegtuigcomponenten", merkt M. Pilar Muñoz Lopez op, ingenieur composietproductie bij Airbus' fabriek in Illescas, Spanje. "Het is van cruciaal belang voor ons om deze technologieën, mogelijkheden en beperkingen te onderzoeken, zodat we voorbereid kunnen zijn op de toekomst."
Aangezien tooling een aanzienlijk deel uitmaakt van de totale programmakosten voor aerostructure-onderdelen, en gezien de toenemende omvang van die onderdelen, zijn nieuwe tooling-opties met lagere kosten en doorlooptijden nodig. Airbus, Northrop Grumman Aeronautics Systems – Aerospace Structures Business Unit (Clearfield, Utah, VS) en de universiteit hebben onlangs een interessant onderzoek uitgevoerd naar hybride, additief vervaardigde (LFAM) gereedschappen voor prototypen en kleine productievolumes voor aerostructuren. van Dayton Research Institute (UDRI, Dayton, Ohio, VS) met bemoedigende resultaten.
Problemen met thermische uitzetting temmen
De meeste aerostructuren van koolstofvezelversterkte kunststof (CFRP) worden gemaakt van prepreg met epoxymatrix. Om dergelijke onderdelen te vormen, moet het gereedschap bestand zijn tegen uithardingstemperaturen in de oven of in de autoclaaf tot 180°C/356°F. Gezien de zeer lage (lineaire) thermische uitzettingscoëfficiënt (CLTE of CTE) van CFRP, is het ook van cruciaal belang om de CLTE's van gereedschap en vormmateriaal bij kamertemperatuur en verhoogde temperaturen zo goed mogelijk op elkaar af te stemmen. Dit zorgt ervoor dat matrijzen de afmetingen behouden, zodat de resulterende onderdelen ook voldoen aan de dimensionale vereisten. Om vervorming of spanning in de uiteindelijke constructies te voorkomen, is het ook belangrijk om het gebruik van gereedschapsmateriaal te vermijden dat sneller afkoelt dan het materiaal van het onderdeel. Als gevolg hiervan zijn de meest gebruikte gereedschappen om grote CFRP-aerostructuren te vormen, gemaakt van CFRP zelf of van Invar, een ijzerhoudende legering van nikkel en ijzer die bekend staat om zijn lage CLTE. Beide zijn kostbaar en kunnen aanzienlijke doorlooptijden hebben. Bovendien is Invar moeilijk en tijdrovend om te bewerken en zwaar om te verzenden. Hoewel stalen of aluminium gereedschappen de kosten kunnen verlagen, beperken hun relatief hogere CLTE-waarden het gebruik in veel toepassingen, vooral bij het vormen van grote of lange onderdelen.
Veel onderzoeken in de publieke en private sector hebben additief vervaardigde gereedschappen geëvalueerd die zijn gedrukt in thermoplastische materialen en geconcludeerd dat ze mogelijk voordelen bieden, waaronder lagere kosten en kortere doorlooptijden om thermohardende laminaatcomposieten te produceren. Helaas heeft het op polymeren gebaseerde LFAM-gereedschap problemen zoals de porositeit van het gereedschap, wat kan leiden tot aanzienlijk vacuümverlies bij uithardingstemperaturen/-drukken. Om dit op te lossen, zijn extra gereedschapsvullingen en oppervlaktecoatings nodig. Een nog grotere uitdaging zijn de sterk anisotrope CLTE-waarden, dankzij de uitlijning van de vulstof in het vlak tijdens extrusie/printen, wat kan leiden tot uitzettings-/contractieverschillen die 5-10 keer groter zijn in de Z-as dan in de X- en Y-printassen. Dat maakt het een uitdaging om herhaalbaar en reproduceerbaar dimensionaal nauwkeurige onderdelen te verkrijgen, vooral wanneer onderdelen groot zijn, een hoge aspectverhouding hebben en/of complexe oppervlakken hebben.
"Iedereen die geïnteresseerd is in additieve gereedschappen, loopt tegen dezelfde problemen aan van porositeit en ongecontroleerde thermische uitzetting, maar er zijn maar weinig effectieve manieren om die problemen aan te pakken", legt Scott Huelskamp uit, UDRI-teamleider, geavanceerde ontwikkeling van fabricageprocessen, divisie structurele materialen. "Er zijn veel mensen die AM-tools willen gebruiken, maar ze wachten op iemand die deze problemen oplost."
Gezien het potentieel van AM om de gereedschapskosten en doorlooptijden te verlagen, heeft de industrie aanzienlijke inspanningen geleverd om uitbreidingsproblemen aan te pakken door nieuwe afdrukbare materialen, printerhardware-aanpassingen en innovatieve modelleringsbenaderingen te onderzoeken. Sommige groepen hebben bijvoorbeeld een "compensatiewaarde" ontwikkeld voor het ontwerpen van AM-tools om CLTE-verschillen aan te pakken. Huelskamp merkt echter op dat het bepalen van welke te gebruiken compensatiewaarde is moeilijk en foutgevoelig. Dergelijke benaderingen zijn ook niet effectief geweest voor gereedschappen met vrouwelijke holte en gereedschappen met vangfuncties over hun lengte die die-lock-omstandigheden creëren die onderdelen kunnen beschadigen tijdens thermische cycli in het gereedschap.
"Er is geen compensatiefactor die dat soort problemen gaat oplossen", voegt hij eraan toe. “Tot op heden heeft geen enkel AM-toolingonderzoek de behoefte aan lage, isotrope CTE-waarden bij verhoogde temperatuur volledig aangepakt. Zonder deze eigenschap zullen gereedschapsafmetingen en geometrieën altijd beperkt zijn, en grotere gereedschappen zullen lijden aan grotere maatfouten bij uithardingstemperaturen."
In een poging om nieuwe benaderingen uit te proberen voor het oplossen van LFAM-toolinguitdagingen, werd een project van 18 maanden uitgevoerd door verschillende aangesloten bedrijven onder auspiciën van het Institute for Advanced Composites Manufacturing Innovation (IACMI, Knoxville, Tenn., VS) en ondersteund door de VS Ministerie van Energie en Jobs Ohio (Columbus, Ohio). Het team werd geleid door UDRI en bestond uit Airbus en Northrop Grumman. Deze organisaties hadden eerder samengewerkt aan ander onderzoek, zowel binnen als buiten IACMI, en waren dus bekend met elkaars mogelijkheden.
“Brute-force” benadering
UDRI had al veel ervaring met AM-toolingstudies en is een actief lid van America Makes (Youngstown, Ohio, VS), het Amerikaanse AM-consortium. Daarnaast had het instituut voor de Amerikaanse luchtmacht onderzoek gedaan naar AM-structuren met metalen ruggen en heeft het samengewerkt met Cincinnati Inc. (Harrison, Ohio, VS), producent van Big Area Additive Manufacturing (BAAM)-printers, aan pure AM-tooling.
"We hadden ook met op maat gemaakte compounders gewerkt aan nieuwe grondstoffen voor 3D-printers, maar niets van wat we deden leek veel vooruitgang te boeken, en we wisten niet dat iemand anders meer succes had dan wij", herinnert Huelskamp zich. “Toen kwamen we op het idee om het probleem anders aan te pakken. Als we de manier waarop AM-materialen zich gedroegen niet konden veranderen of dat gedrag niet direct konden voorspellen , dan kunnen we ze misschien dwingen zich te gedragen zoals we wilden indirect .” Met wat Huelskamp een 'brute-force'-benadering noemt, stelde UDRI een hybride LFAM-onderzoek voor dat aerostructure-tooling zou produceren door conventionele toe te passen CFRP-gezichtshuiden tot thermoplastisch-composiet AM-kernen.
De doelstellingen voor het project waren eenvoudig:een goedkopere en snellere methode vinden om grote gereedschappen voor aerostructuren te maken. Het team zocht een optie die de kosten met 50% verlaagde en produceerde ten minste 10 acceptabele prototype- of kleine productieonderdelen voor latere tests
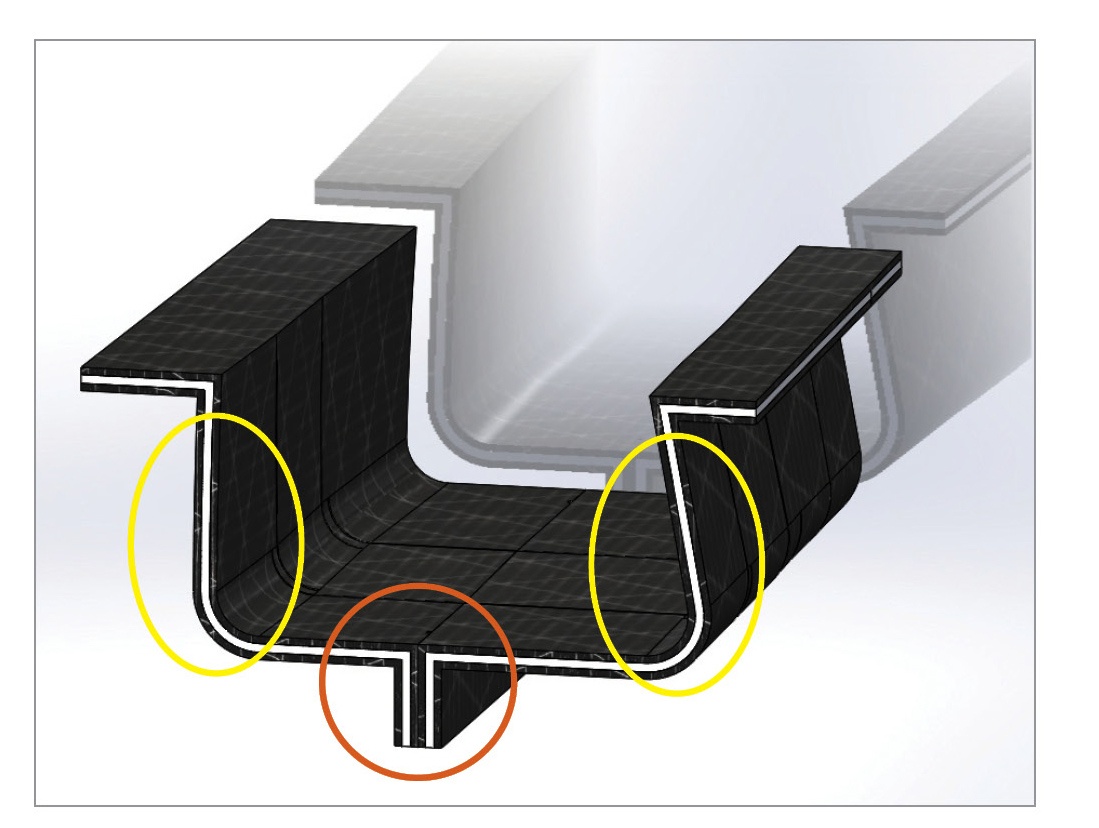
Het team besloot een sandwichstructuur te gebruiken om enkelzijdige gereedschappen te produceren voor een gedeelte van een generieke vleugelligger met behulp van gereedschapsgegevens van Airbus. Afgezien van het produceren van gereedschap om slechts een deel van de volledige C-spar te vormen - vanwege ruimtebeperkingen in de UDRI-faciliteit - zijn er geen grote ontwerpwijzigingen doorgevoerd.
Er is een vrouwelijk gereedschap ontworpen om ervoor te zorgen dat de kritische onderdeelgeometrie werd gevormd met behulp van hardgereedschapsoppervlakken. Dit rondhoutkapgereedschap had een kleine binnenwaartse hoek die een negatieve trek veroorzaakte en een die-lock-toestand, omdat het een gereedschap uit één stuk was. Dit bracht onderzoekers ertoe het ontwerp aan te passen aan een split-tool die werd afgedicht met pakking / cordstock. Om het risico te verkleinen, begon het team met een subschaaltool van 0,6 meter/2,0 voet om het concept te bewijzen. Nadat het gereedschapsontwikkelingsproces en de prototypeonderdelen die op dat gereedschap waren geproduceerd waren getest en bleken te werken, bouwde het team een groter gereedschap van 3,3 meter lang om een groter deel van de ligger te vormen voor het testen van prototypen.
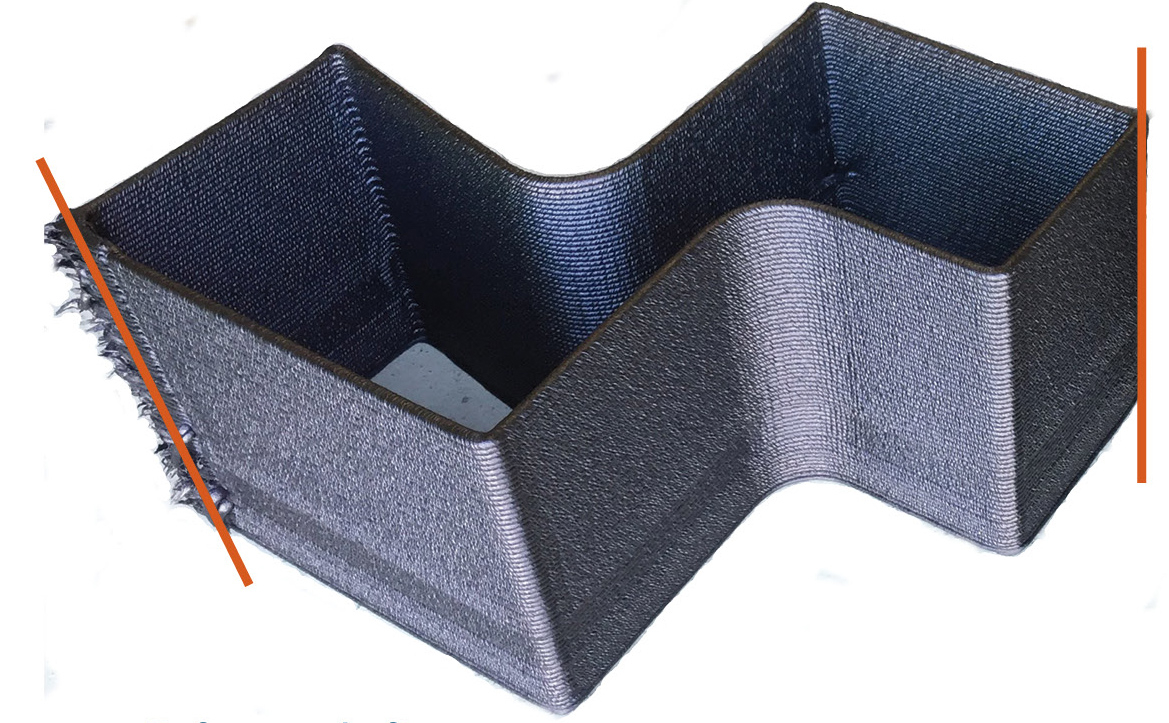
Omdat CFRP-tooling zo'n lage CLTE-waarde heeft, lichter is dan Invar en de tool was bedoeld voor productieonderdelen van prototypes/kleine volumes, besloot het team om CFRP-gezichtshuiden te gebruiken om de AM-kern te beperken. De huiden zijn gemaakt met Hextool M81 epoxy tooling prepreg van Hexcel (Corp., Stamford, Conn., U.S.).
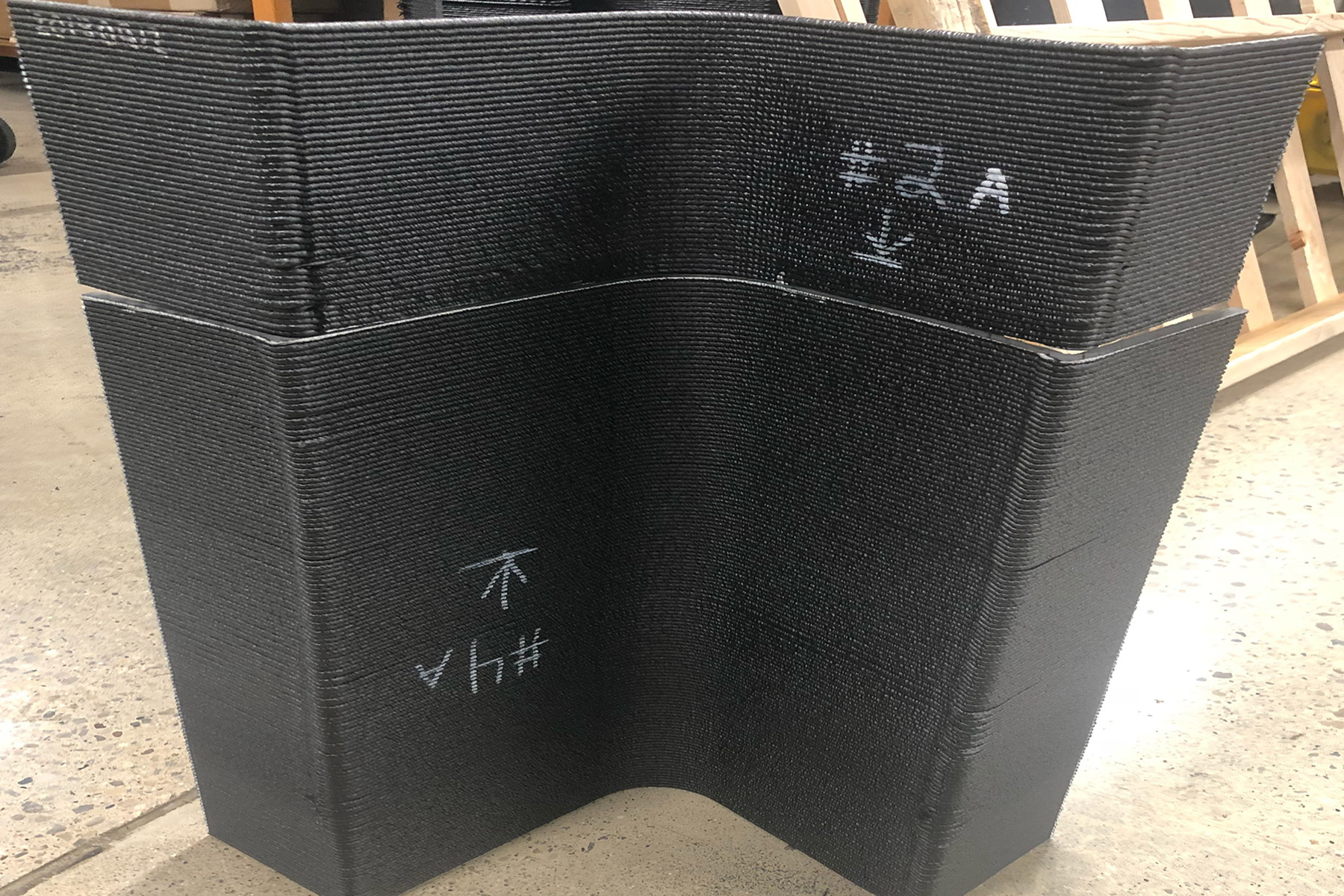
De bovenste afbeelding toont een gedeelte van de rechterhelft van de subschaal, BAAM-gedrukte tool met rode lijnen die snijlijnen aangeven na het afdrukken. De onderste afbeelding toont het rechterhelftgereedschap nadat de secties aan elkaar waren gehecht. Photo Credit:University of Dayton Research Institute.
Het materiaalformaat was een mat van 2.000 gram per vierkante meter gehakte koolstofvezel geïmpregneerd met Hexcel's 8552 geharde epoxy. Dit materiaal wordt vaak gebruikt voor composietgereedschappen vanwege de bijna isotrope eigenschappen, die machinale bewerking mogelijk maken zonder gereedschapsbeweging die anders zou kunnen worden veroorzaakt door restspanningsrelaxatie.
Aangezien de kern zou worden afgedrukt op een BAAM 1000-printer van Cincinnati Inc. bij Additive Engineering Solutions (Akron, Ohio, VS), en aangezien UDRI en Cincinnati aanzienlijke ervaring hadden met het werken met het thermoplastische polyetherimide (PEI) voor hoge temperaturen, kozen ze 20% korte koolstofvezelversterkte PEI (Thermocomp EX004EXAR1 Ultem) van SABIC, (Riyadh, Saoedi-Arabië) om een bijna netvormige kern te printen. (De aanwezigheid van koolstofvezels stabiliseert het polymeer tijdens het printen en voorkomt dat het inzakt; in de afgewerkte structuur verminderen de vezels CLTE in de printrichting.) Om de kosten laag te houden, functioneerde de kern als de tooling master en werden de gezichtshuiden direct gelamineerd tot de kern zonder lijm, maar met enige aanpassing aan het kernoppervlak dat valt onder intellectueel eigendom (IP) dat tijdens het project is ontwikkeld. Die aanpak was effectief, zonder delaminatie, zelfs niet na meerdere thermische cycli.
Gecondenseerde productie
Bij conventionele fabricage van CFRP-gereedschappen voor aerostructuren wordt eerst een goedkope master gemaakt. Dit omvat meestal het aan elkaar lijmen van blokken gereedschapsbord in een oven of autoclaaf, en vervolgens het machinaal bewerken van de monolithische structuur tot de gewenste onderdeelgeometrie. Het gereedschapsmateriaal wordt vervolgens op de master gelegd, in zakken gedaan en in een autoclaaf uitgehard. Na het uit de vorm halen en opruimen wordt een rugstructuur aan het gereedschap gehecht en wordt het gereedschapsoppervlak opnieuw machinaal bewerkt om een goede geometrische tolerantie en oppervlakteafwerking te garanderen.
Met hybride AM-tooling ontwikkelde het team een gecondenseerd productieproces om de doorlooptijd en kosten te verminderen. Eerst werd een bijna netvormige kern (toolmaster) 3D-geprint (in korte koolstofvezel / PEI). Vervolgens werd prepreg van CFRP-gereedschap rechtstreeks op beide zijden van de kern gelamineerd (met warme debulks tussen laag één, vier en zeven volgens de aanbevelingen van de leverancier). De hele structuur werd vervolgens vacuüm verpakt en geautoclaveerd.
Gecondenseerd fabricageproces voor subschaal C-spar-tool.
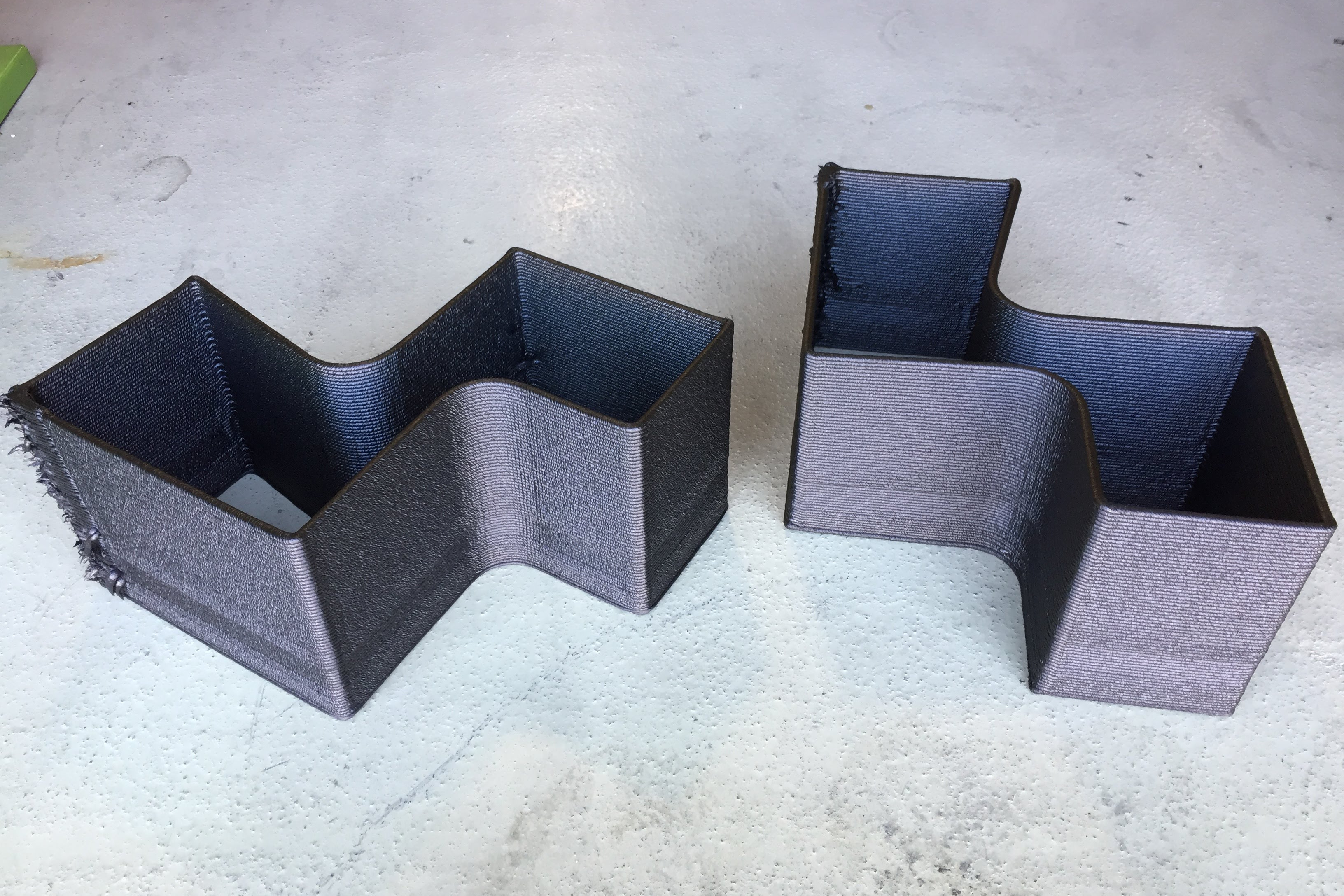
Stap 2:Knip de BAAM-afdruk door het midden en in de linker- en rechterhelften.
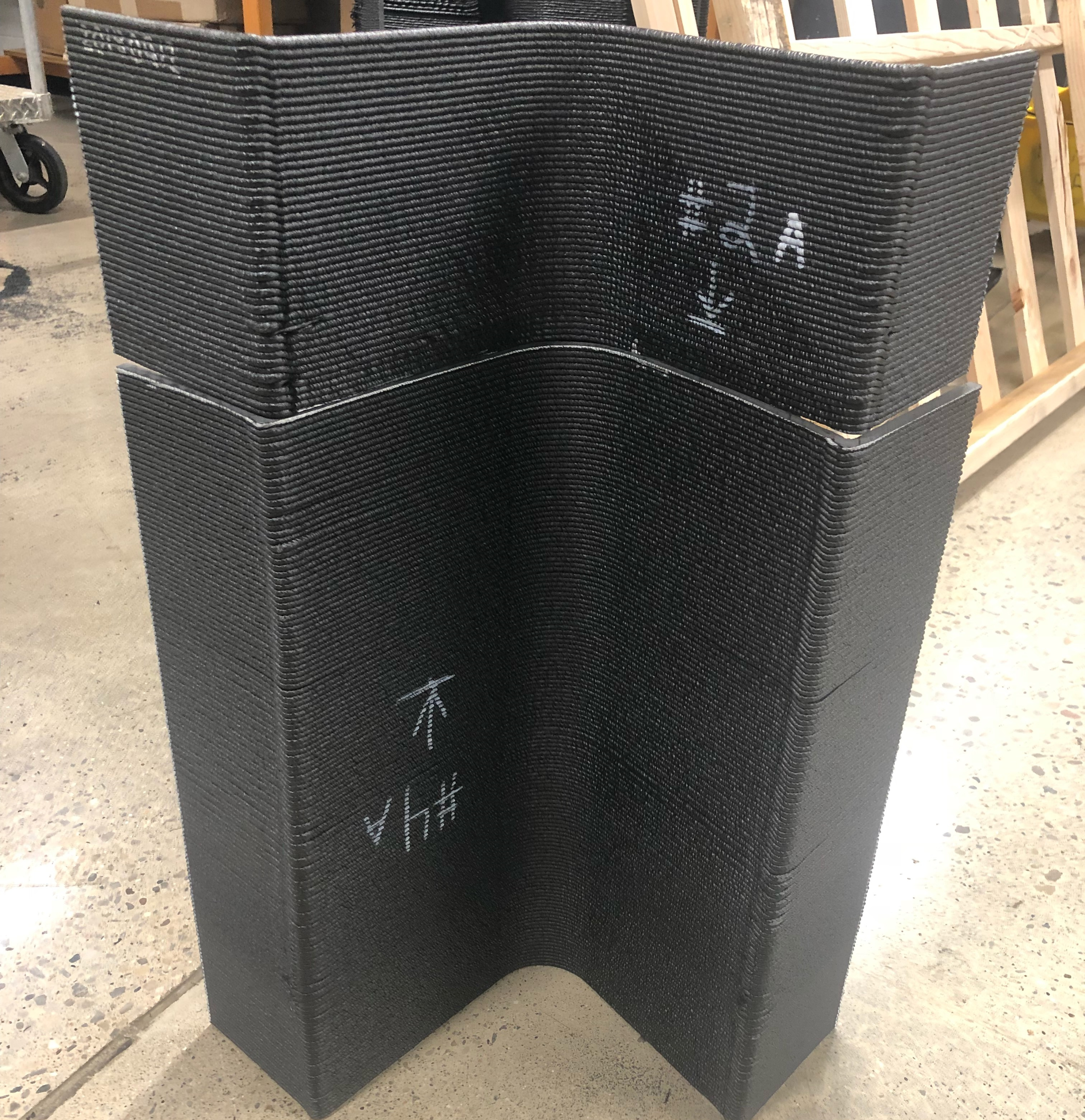
Stap 3:Bond BAAM-print om de gewenste lengte te bereiken en laat uitharden.
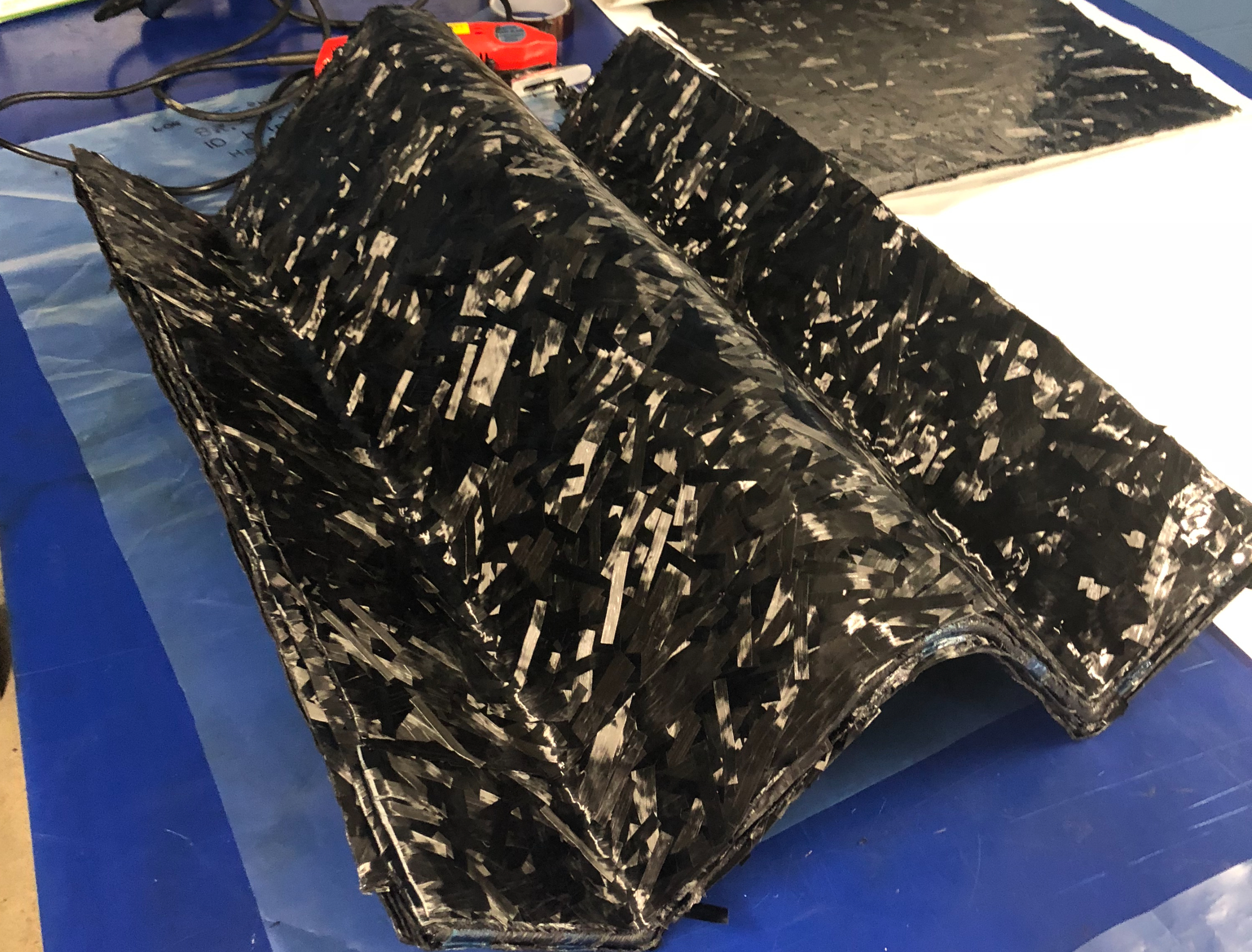
Stap 4:Lamineer de prepreg van het gereedschap aan beide zijden van de kern met hete debulks volgens de instructies van de fabrikant.
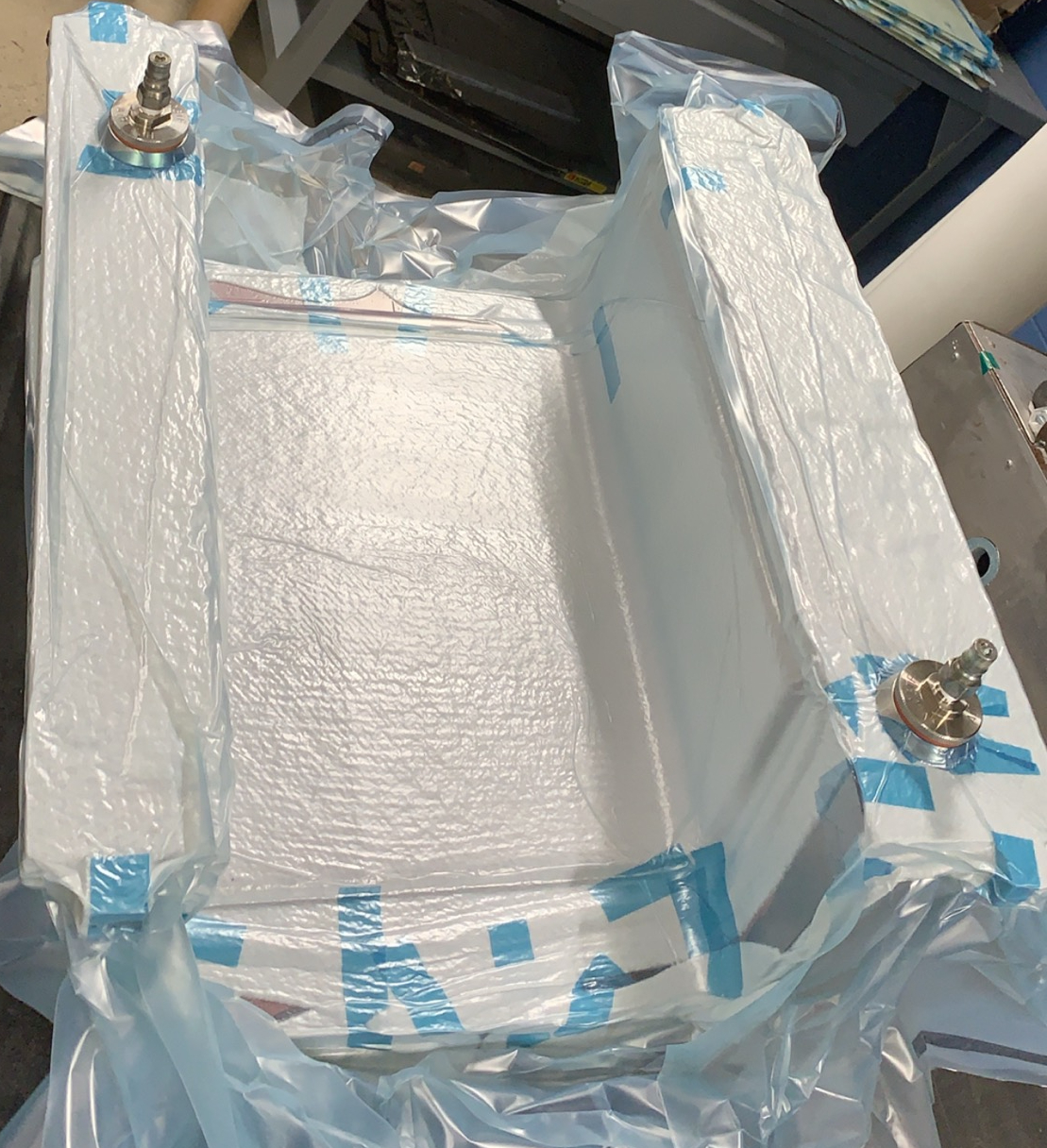
Stap 5:Vacuümzak en uitharden in autoclaaf.
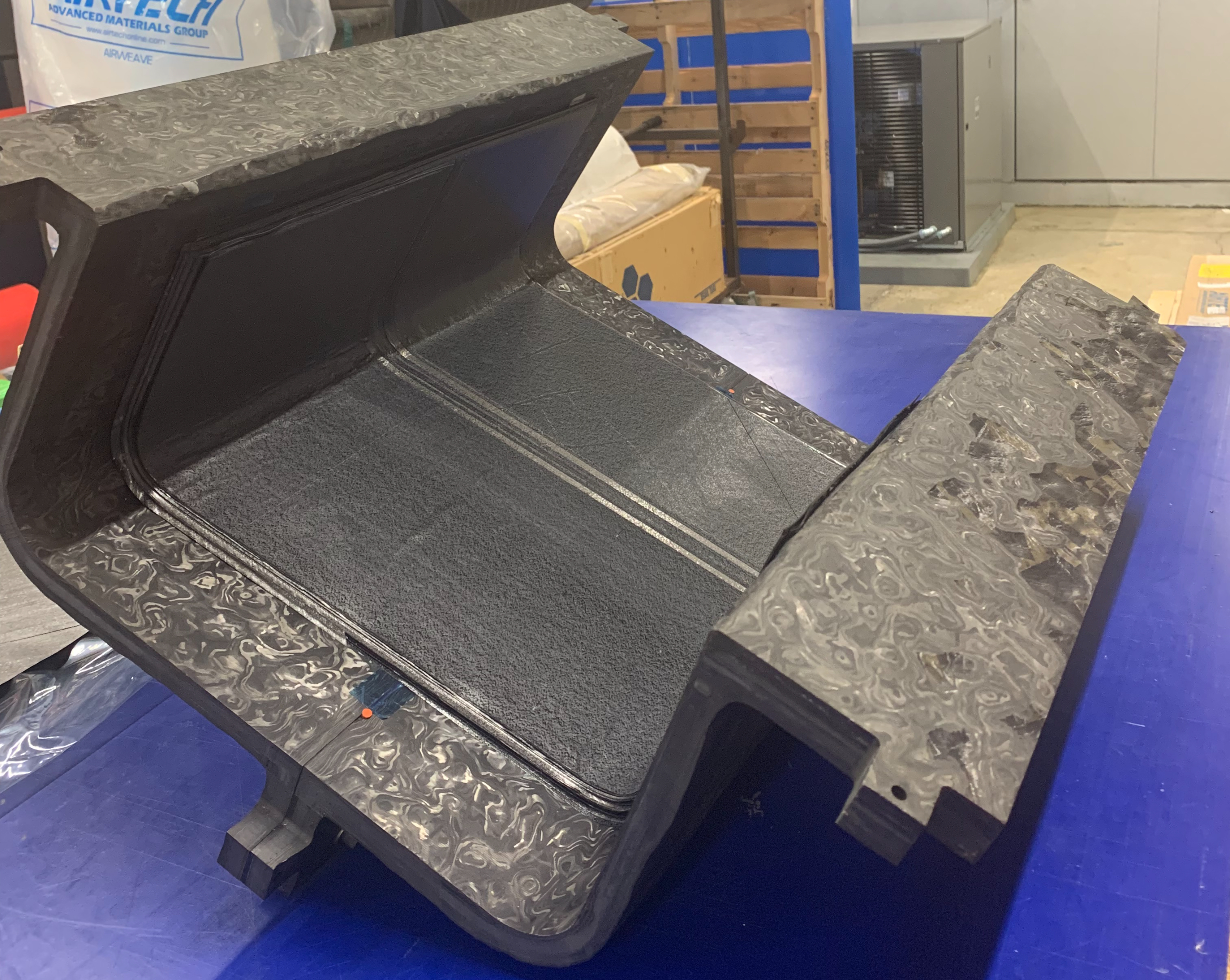
Stap 6:Machinaal uitgehard gereedschap om de uiteindelijke afmetingen en oppervlakteafwerking te bereiken.
Vorige volgendeTijdens het uitharden van het laminaat werd een goede hechting bereikt tussen de PEI-kern en de epoxyhuid, dus lijm was niet nodig. Niet alleen zijn de CFRP-huiden niet-poreus en duurzamer dan de AM-kern, ze beperken ook fysiek de beweging van de kern tijdens temperatuurschommelingen vanwege hun veel lagere CLTE-waarden. Slechts een enkele behandeling en een enkele bewerking — beide grote kosten tijdens traditionele gereedschapsproductie — waren nodig om de uiteindelijke afmetingen en oppervlakteafwerking te bereiken. Er was ook geen backing nodig, dankzij de sandwichstructuur en de vorm van het gereedschap, inclusief retourflenzen aan de bovenkant van de mal voor laterale stijfheid en een boutverbinding in het midden van de mal voor verticale stijfheid - waardoor een verlijmingsoperatie wordt geëlimineerd.
Eerste uitdagingen
Onderzoekers stonden voor verschillende beheersbare uitdagingen met het nieuwe proces.
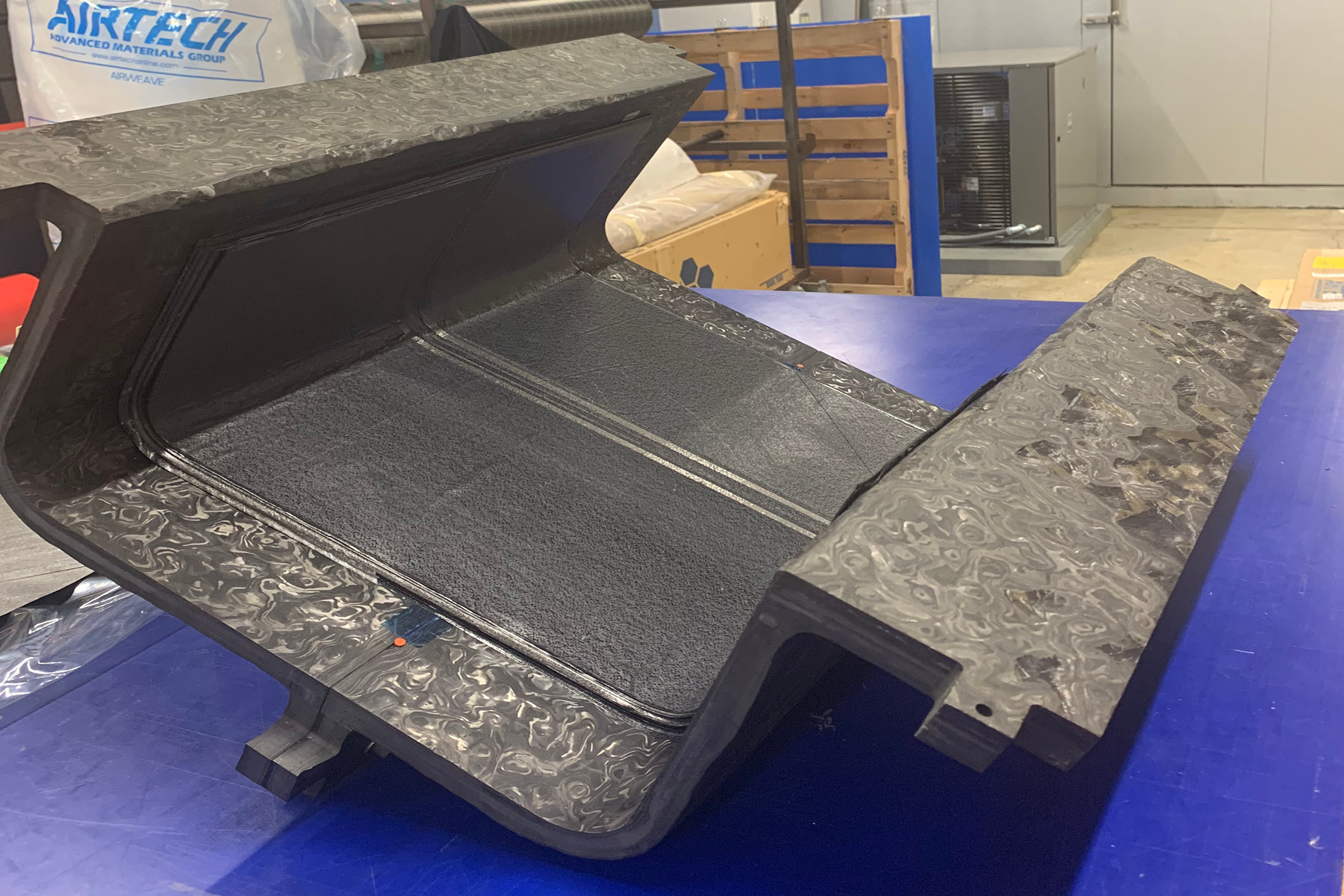
Om de fabricage op de BAAM te vergemakkelijken, was de voorkeursrichting voor de fabricage van de kern het afdrukken van de doorsnede als een verticale constructie. Dat was geen probleem voor het gereedschap van 0,6 meter; voor het grotere gereedschap was 3,3 meter echter groter dan de BAAM 1000 verticaal kon afdrukken. Vanwege de beperkingen van de afdrukruimte op de Z-as van de printer, hebben onderzoekers ervoor gekozen om beide subschaalgereedschappen over hun lengte te halveren en ze vervolgens opnieuw te splitsen in linker- en rechtersecties (om problemen met ondersnijding van de spar-cap aan te pakken en het uit de vorm halen te vergemakkelijken).
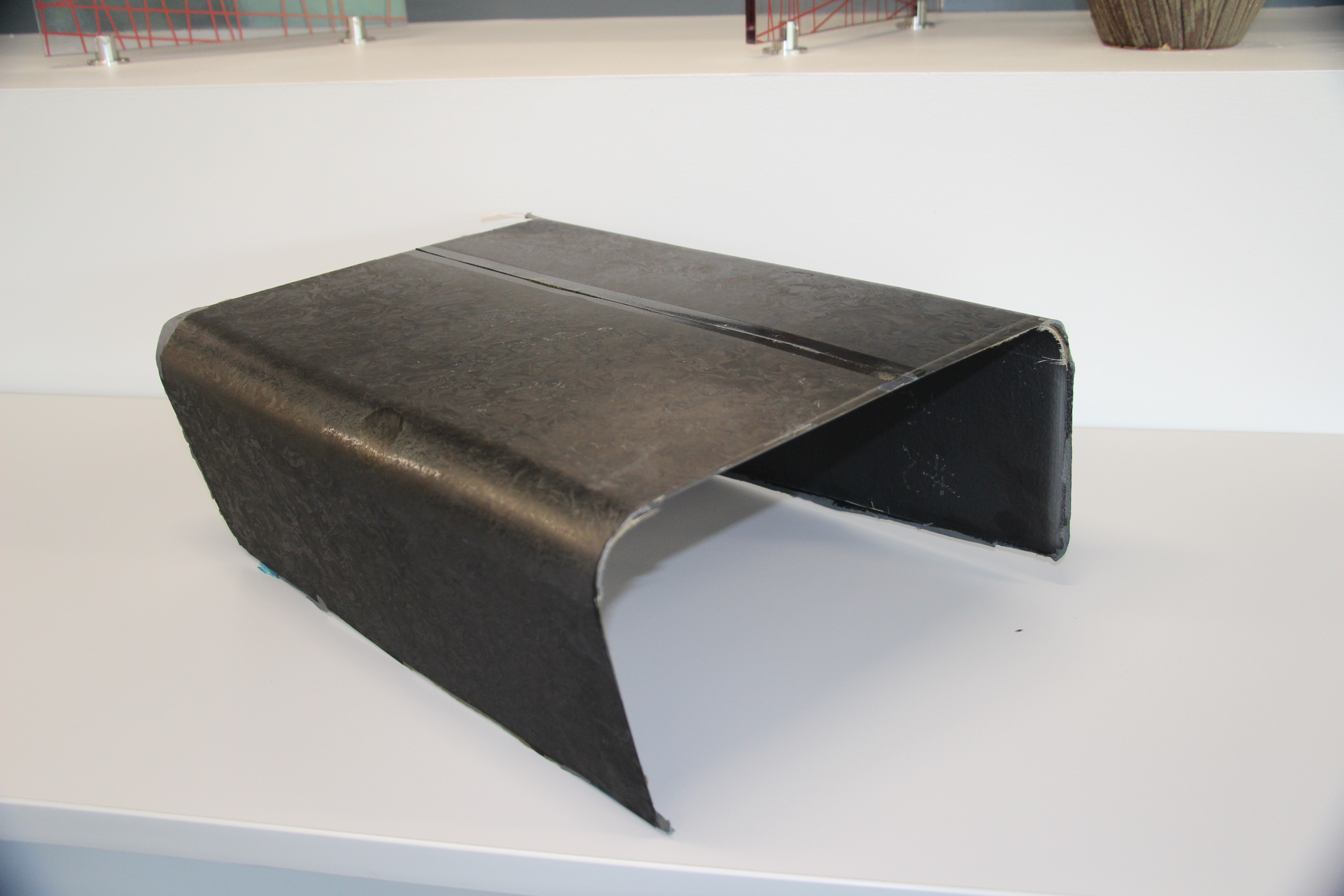
Om de afdrukefficiëntie te verhogen, werden gereedschapsdelen rug aan rug bedrukt en vervolgens in rechter- en linkerstukken gesneden. Om de lengte van 3,3 meter te bereiken, werden de twee rechtersecties aan elkaar gehecht, gevolgd door de twee linkersecties met Loctite EA9394 epoxylijm van Henkel Corp. (Rocky Hill, Conn., V.S.). Het team liet de AM-kern onbewerkt, omdat het van cruciaal belang was voor het bereiken van lage gereedschapskosten en korte doorlooptijden, evenals voor het creëren van een mechanische koppeling tussen de AM-kern en de CFRP-huiden aan elke kant. De achterkant van elke gereedschapshelft was gelamineerd met vijf lagen prepreg, terwijl de voorkant was gelamineerd met negen lagen om extra materiaal te verschaffen dat tijdens de bewerking na uitharding kon worden verwijderd.
Voorlopige resultaten
Naast het regelen van CLTE van de AM-kern, zorgde de prepreg voor een putvrij oppervlak dat de vacuümintegriteit handhaafde zonder dat er afdichtmiddel/coating nodig was. Deze aanpak was zo succesvol dat het gebruik van een uit meerdere delen bestaand gereedschapsontwerp, afgedicht met een pakking, mogelijk maakte, wat volgens onderzoekers niet eerder was aangetoond in AM-gereedschap dat bij hoge temperaturen wordt gebruikt. Bovendien werd de gereedschapsmassa aanzienlijk verminderd; de subschaaltool was een derde van het berekende gewicht voor een vergelijkbaar Invar-ontwerp. Niet alleen zijn lichtere CFRP-gereedschappen gemakkelijker te hanteren en op rekken op te slaan, maar ze vereisen ook kortere opwarm-/afkoelcycli in de autoclaaf. Bij een gereedschap om de volledige C-spar te vormen, kan dat gewichtsvoordeel het verschil maken tussen onder of overschrijding van de limieten voor het portaal/kraangewicht in sommige productieruimten.
Belangrijk is dat de kosten van het hybride gereedschap van 0,6 meter werden berekend tijdens de fabricage, met behulp van industriestandaard arbeidstarieven, op $ 24.136 USD met een verdeling van ongeveer 50/50 tussen bewerkingskosten en print-/lamineerkosten. Daarentegen werd een identieke Invar-tool genoteerd voor $ 46.775 USD - een besparing van bijna 50%. De kosten voor het gereedschap van 3,3 meter zijn niet compleet, maar zullen naar verwachting een besparing van ongeveer 30% opleveren op basis van kosten/lengte-eenheid, aangezien materiaal-/drukkosten lineair worden geschaald, maar bewerkingskosten een schaalvoordeel hebben dat de impact ervan vermindert. De hybride aanpak leverde tools op die voldeden aan de operationele prestatie-eisen van Airbus en Northrop Grumman en wordt beschouwd als een levensvatbaar alternatief voor Invar voor rapid-prototype of low-use tooling. Onderzoek naar de standtijd maakte geen deel uit van deze studie, maar zou waarschijnlijk aanzienlijk verder reiken dan de 12 cycli die werden aangetoond.
Het programma werd verlengd van 18 naar 30 maanden, maar er zijn nog steeds gebieden waar meer onderzoek nodig is, zoals inzicht in hoe de uiteindelijke as-gedrukte kerngeometrie verschilt van die voorspeld in CAE-modellen. Het team wil ook de voorspellende nauwkeurigheid verbeteren, zodat er voldoende lagen worden toegevoegd op kritieke gebieden om ervoor te zorgen dat er tijdens de bewerking geen perforatie optreedt. Toch beschouwde het team dit als een succesvol project met aanzienlijke kansen voor toekomstige LFAM-tooling.
"Northrop Grumman kijkt ernaar uit om een 3 meter lang spar-demonstratieonderdeel te bouwen met behulp van het 3,3 meter lange hybride gereedschap gebouwd door UDRI en ons eigen geautomatiseerde verstijvervormingsproces (ASF) om de duurzaamheid en dimensionale stabiliteit van het gereedschap te evalueren," voegt toe Vern Benson, technisch medewerkster van Northrop Grumman.
Hars
- Evonik, Evolve Additive Solutions om 3D-printmaterialen voor STEP-proces te ontwikkelen
- Henkel biedt materiaalplatform voor additieve productie
- Essentium en Lehvoss werken samen om materialen voor additieve productie te ontwikkelen
- Nieuw, hittegestabiliseerd nylon 6 voor hybride en elektrische aandrijflijnen
- Trelleborg kondigt nieuwe distributeur voor gereedschapsmaterialen aan
- UAMMI, Impossible Objects bouwen samengestelde onderdelen voor de Amerikaanse luchtmacht
- Victrex en Bond-partner voor 3D-printen van PAEK-onderdelen
- AeroLas onderzoekt nieuwe spintechnologie voor thermoplastisch hybride garen
- Tips voor 3D-printvormen
- Doorlooptijden voor grote onderdelen minimaliseren
- De fabricage en bewerking van metalen onderdelen voor brandstofinjectiesystemen