Additieve productie voegt veelzijdigheid toe aan grote maritieme constructies
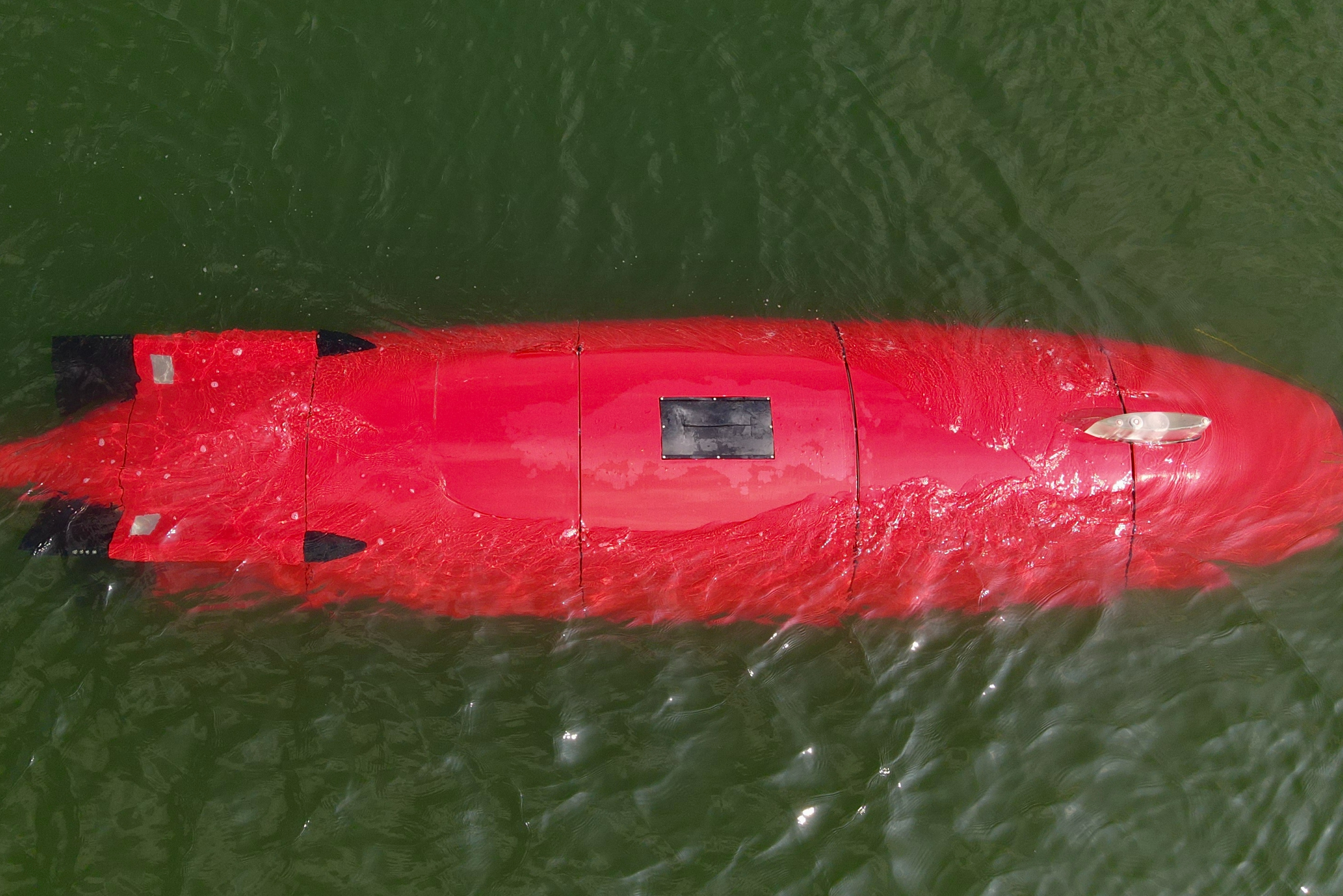
De mogelijkheid om snel verschillende iteraties van onderdelen te bouwen - zonder dure speciale gereedschappen te hoeven ontwikkelen of kopen - is de reden waarom additive manufacturing (AM) zo vaak wordt gebruikt bij het maken van prototypes van onderdelen. Naarmate de materialen en printtechnologieën echter blijven verbeteren, zijn meer bedrijven in staat om de snelheid en veelzijdigheid van AM uit te breiden naar onderdelen voor eindgebruik, met name voor kleine oplagen of eenmalige toepassingen waarbij de mogelijkheid om snel nieuwe ontwerpen te produceren een troef is .
Onlangs hebben twee bedrijven aangetoond dat composiet AM-technologieën oplossingen kunnen bieden voor het aanpassen van grote maritieme constructies zoals autonome onderwatervoertuigen (AUV) en motorboten.
Grootformaat 3D-printen voor aanpasbare AUV-productie
Autonome onderwatervoertuigen zijn een soort onbemand robotvoertuig dat onder water kan reizen zonder fysieke verbinding met een boot of afstandsbediening van een menselijke operator, en zijn vaak uitgerust met camera's of sensoren voor verschillende gebruikssituaties in defensie, oceaanonderzoek of offshore-onderzoekstoepassingen. Meestal bestaan de buitenrompen van AUV's uit één groot metalen drukvat, of ze zijn gemaakt van thermogevormd plastic of composieten. Voor beide opties is echter de ontwikkeling en aanschaf van speciale gereedschappen vereist, wat duur kan zijn en de hoeveelheid maatwerk die voor AUV-klanten mogelijk is, beperkt. AUV-fabrikant Dive Technologies (Quincy, Mass., V.S.) heeft ontdekt dat composiet 3D-printen veel van de beperkingen van traditionele productie oplost.
In 2018 besloten de mede-oprichters van Dive Technologies, Bill Lebo, Jerry Sgobbo en Sam Russo, om hun eigen bedrijf op te richten om een nieuwe, meer capabele AUV te ontwerpen en te lanceren die voldoet aan de eisen van de klant voor een lang uithoudingsvermogen en een groot laadvermogen.
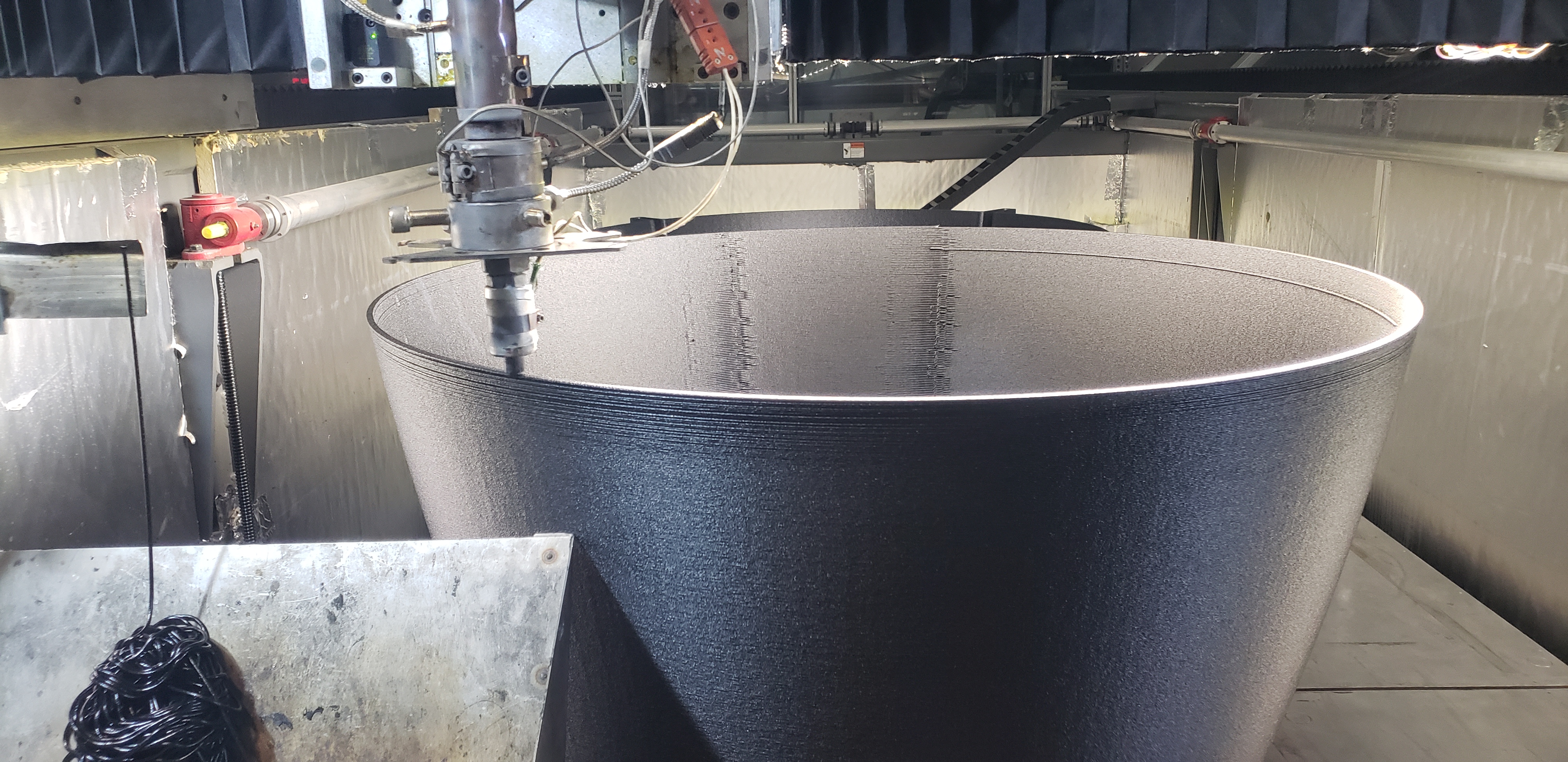
Wat zij en hun team hebben ontwikkeld, is de DIVE-LD, een 19 voet lange, 4 voet diameter commerciële AUV die in staat is om tot 6000 meter te duiken en tot 500 mijl te reizen, met een laadvermogen van maximaal 1 kubieke meter. Oorspronkelijk ging het team ervan uit dat de uiteindelijke structuur van zijn voertuig thermogevormde kunststoffen zou gebruiken voor de buitenromp. Om het ontwerp te onderzoeken en te testen, sprak Dive Technologies met Oak Ridge National Laboratory (ORNL, Oak Ridge, Tenn., V.S.) over het gebruik van 3D-printen voor rapid prototyping. Via ORNL maakte het Dive-team kennis met Additive Engineering Solutions (LFAM), specialist op het gebied van additieve fabricage in groot formaat (AES, Akron, Ohio, VS), en begon het samen met het AES-team aan een productieproces voor zijn AUV-rompvormen.
Tijdens het werken aan de 3D-geprinte prototypes realiseerde Dive Technologies zich echter het potentieel voor LFAM om snel afgewerkte te produceren. componenten, niet alleen prototypes. Niet alleen voldeden de 3D-geprinte prototypecomponenten beter dan verwacht aan de onderdeelvereisten, maar het gebruik van AM voor productievoertuigen zou ook de gereedschapskosten besparen, Dive in staat stellen om sneller eindproducten te produceren dan met traditionele methoden en een nieuw, hoger niveau van snelle aanpassing voor klanten.
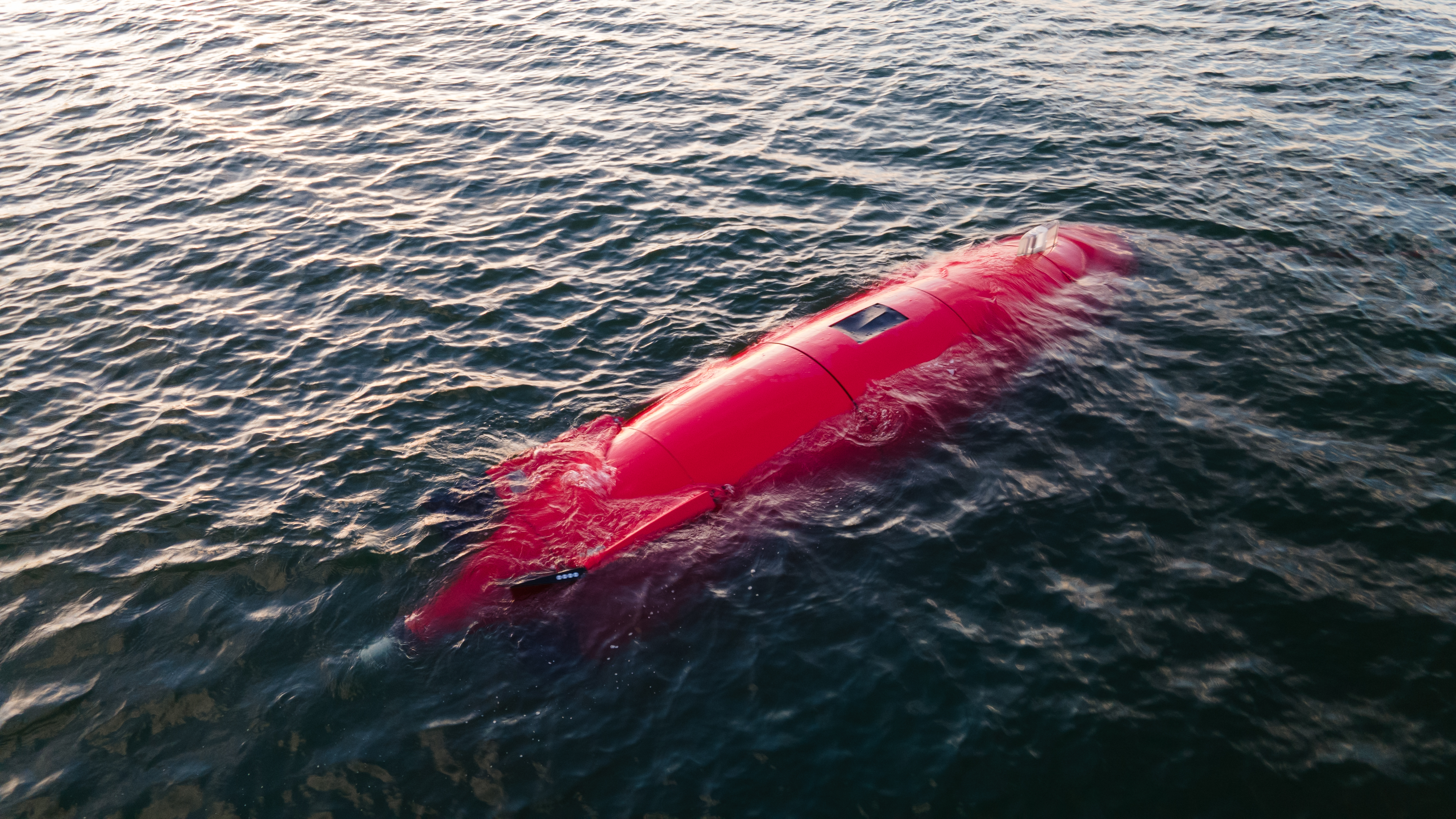
De buitenromp van de DIVE-LD bestaat uit negen buisvormige stroomlijnkappen die zijn bedrukt met een van de vier Cincinnati Inc. (Cincinnati, Ohio, VS) Big Area Additive Manufacturing (BAAM) 3D-printers van AES. Deze stroomlijnkappen zijn gedrukt van met gehakte vezels gevulde ABS geleverd door Sabic (Riyadh, Saoedi-Arabië). Volgens de mede-oprichter en VP van AES, Andrew Bader, kan AES alle onderdelen voor een complete romp in minder dan twee dagen printen. Eenmaal geleverd aan Dive, worden de 3D-geprinte stroomlijnkappen mechanisch bevestigd met vier bevestigingsmiddelen per stroomlijnkap en gecoat om een glad, hydrodynamisch buitenoppervlak te produceren. Na succesvolle eerste tests in 2020, bouwt Dive dit voorjaar de eerste voertuigen van klanten en zal de eerste bestelling in juni 2021 leveren.
Volgens Russo is AM een kernonderdeel geworden van de waardepropositie van Dive Technologies voor toekomstige voertuigen en producten. De samenwerking met Dive is ook een grote stap voor AES en composiet 3D-printen. Bader voegt toe:"Als mensen denken aan 3D-printen, denken ze meestal aan prototypes, armaturen en tooling, dus dit laat zien waartoe 3D-printen in staat is."
Om meer te lezen over Dive Technologies en AES, lees "Grootformaat 3D-printen maakt gereedschaploze, snelle productie voor AUV's mogelijk."
Continue fiber AM en automatisering voor veelzijdig motorbootontwerp
Sinds Moi Composites (Milaan, Italië) in 2015 zijn proces voor continue vezelproductie (CFM) patenteerde, heeft hij een reeks toepassingen onderzocht voor zijn op depositie gebaseerde, continu-vezel 3D-print CFM-technologie. Kenmerken van CFM zijn onder meer de aangepaste ontwerpsoftware van Moi Composites, het gebruik van robotarmen, UV-uitharding en "hybride" productie - meer traditionele composietlaminering bovenop een 3D-geprinte structurele kern. Onlangs heeft het bedrijf zijn CFM-technologie gedemonstreerd als een oplossing voor een kosteneffectiever, sneller en innovatiever ontwerp van maritieme constructies, door middel van een demonstratiemotorboot genaamd MAMBO.
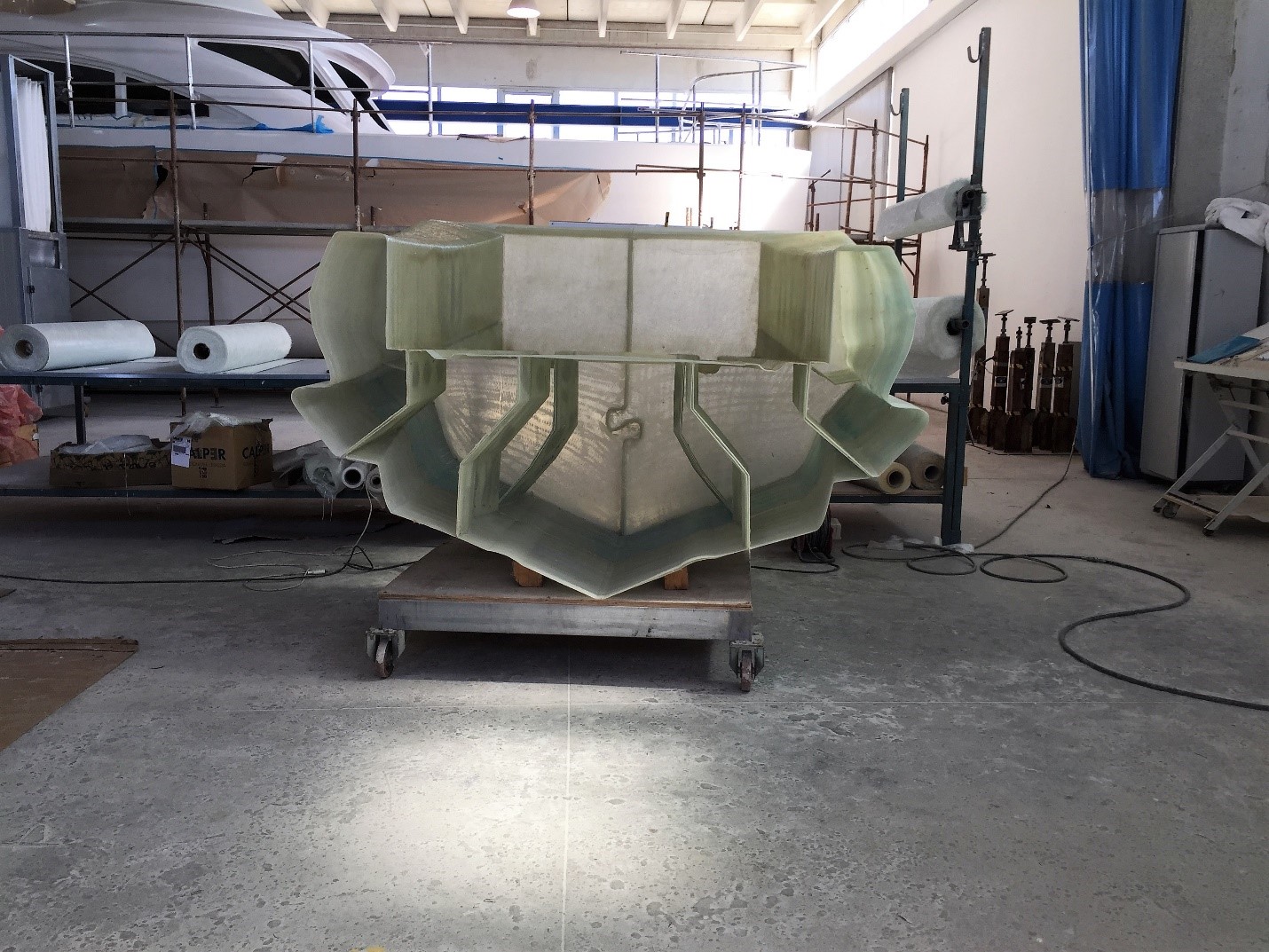
Volgens Gabriele Natale, mede-oprichter van Moi Composites, woonden hij en mede-mede-oprichter Michele Tonizzo de Genoa Boat Show in 2017 bij en realiseerden zich dat de gereedschapskosten en traditionele glasvezelinfusieprocessen die voor veel bootrompen worden gebruikt, het vermogen van bootontwerpers om nieuwe en meer complexe ontwerpen. Natale erkent dat hun vormloze 3D-printtechnologie met continue vezels een ondersteunende oplossing zou kunnen zijn en zegt:"Van daaruit begonnen we een plan te ontwikkelen en begonnen we partners binnen de maritieme industrie te ontmoeten."
De resulterende MAMBO-boot is 6,5 meter lang x 2,5 meter breed, met een droog gewicht van ongeveer 800 kilogram, uitgerust met een navigatiesysteem, kurkvloeren, witleren stoelen en een motor van 115 pk. Moi Composites werkte samen met de maritieme ontwerpstudio MICAD (Lecce, Italië) aan het structurele ontwerpconcept voor de boot, dat organische vormen combineert in zijn structurele elementen, geïnspireerd op de beroemde Arcidiavolo-catamaran van Sonny Levi. Autodesk (San Rafael, Californië, VS) Fusion 360 CAD en NETFABB additive manufacturing-software werden gebruikt bij het ontwerp en de vloeistofdynamische analyse van de componenten.
De romp en het dek van de boot, gedrukt van unidirectioneel E-glas geleverd door Owens Corning (Toledo, Ohio, V.S.) en vinylesterhars, werden ontworpen om te worden vervaardigd in 50 afzonderlijke secties van verschillende afmetingen. De helft van de secties werd geprint in de faciliteit van Moi Composites in Milaan, en de andere helft in de Advanced Manufacturing Facility (ACF) van partner Autodesk in Birmingham, VK Moi Composites' CFM 3D-printtechnologie en dubbele Kuka (Augsburg, Duitsland) robots werden gebruikt bij beide faciliteiten. Volgens Dominique Müller, onderzoeksmanager van het additive manufacturing-team bij Autodesk, zorgde het CFM-systeem in het technologiecentrum van Autodesk ervoor dat de boot snel kon worden geprint en dat de Autodesk ook beter kennis kon maken met de technologie die Moi op afstand bestuurde met behulp van Autodesk-software . De totale printtijd voor alle componenten was ongeveer twee maanden.
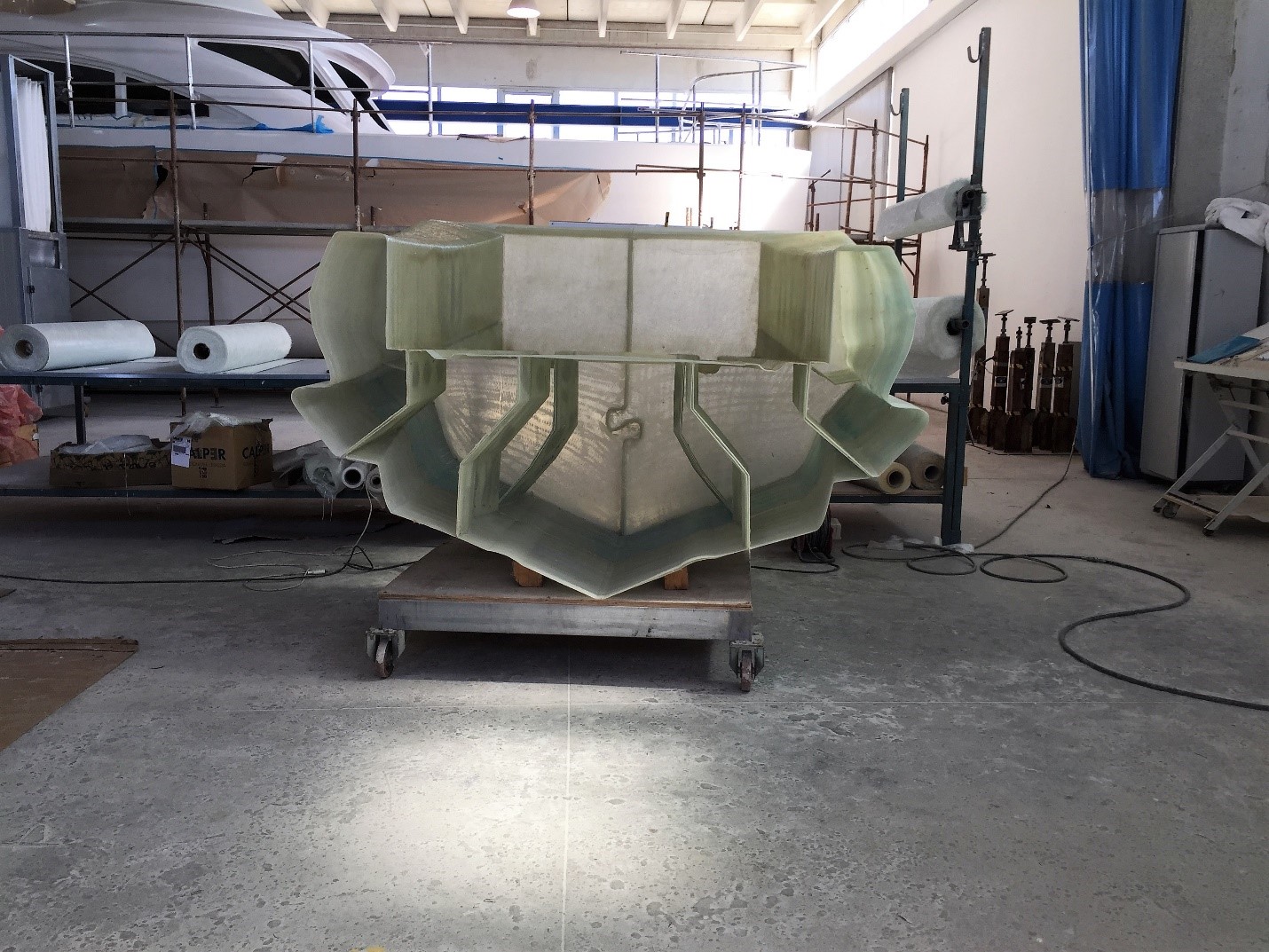
De bedrukte onderdelen werden verscheept naar de Catmarine-scheepswerf in Miggiano, Italië, waar ze in elkaar werden gezet en gelijmd. In een hybride fabricageproces vergelijkbaar met wat Moi heeft gebruikt met protheses en andere onderdelen, werd de hele romp vervolgens gelamineerd via handmatige lay-up met een extra glasvezel/polyester-laag gevuld met PVC-schuim, dat volgens Natale in dikte varieert langs de structuur. Nadat de romp en het dek volledig waren gemonteerd, geschuurd en gecoat, hebben de partners van Moi Composites de boot uitgerust met voortstuwing, navigatie en andere systemen om de boot af te maken.
De eerste proefvaarten en stabiliteitstests op zee werden uitgevoerd in de herfst van 2020, waarbij MAMBO tot 26 knopen reikte; Moi Composites is van plan om de proefvaarten in de zomer van 2021 voort te zetten en te werken aan de certificering van de boot.

“Additive manufacturing, digitalisering en automatisering kunnen de creatie van nieuwe concepten en futuristische projecten versnellen, want voor elke boot die je wilt ontwerpen, moet je een nieuwe mal maken. Met behulp van deze technologie kunt u uw 3D-model eenvoudig aanpassen en opnieuw afdrukken. Dit is perfect, vooral voor kleine of eenmalige boten”, zegt Natale.
Lees voor meer informatie over MAMBO "MAMBO test de wateren voor het 3D-printen van grote mariene constructies."
Hars
- 5 gemeenschappelijke productieprocessen voor additieven
- Additieve productie versus subtractieve productie
- Voordelen van additieve fabricage
- Een onderzoek naar workflows voor additieve productie
- Additive Manufacturing Technologies:het nabewerkingsbedrijf dat de toekomst van de productie vormgeeft
- Henkel biedt materiaalplatform voor additieve productie
- NCAMP publiceert eerste kwalificatieprogramma voor additieve fabricage
- Alliantie voor duurzame thermoplasten en additive manufacturing in Colorado
- 5 technologieën die de productie verstoren
- Additieve productie in elektronica
- Additieve productie in de lucht- en ruimtevaart