Nieuwe Anodic Catalyst Support voor Direct Methanol Fuel Cell:Karakteriseringen en Single-Cell Performances
Abstract
Deze studie introduceert een nieuwe titaniumdioxide koolstof nanovezel (TiO2 -CNF) ondersteuning voor anodische katalysator in directe methanol brandstofcel. Het katalytische syntheseproces omvat verschillende methoden, namelijk de sol-gel-, elektrospin- en afzettingsmethoden. De gesynthetiseerde elektrokatalysator wordt vergeleken met andere drie elektrokatalysatoren met verschillende soorten ondersteuning. Al deze elektrokatalysatoren verschillen op basis van een aantal fysische en elektrochemische kenmerken. Experimentele resultaten tonen aan dat de TiO2 -CNF-ondersteuning gaf de hoogste stroomdichtheid bij 345,64 mA mgkatalysator −1 , wat overeenkomt met het 5,54-voudige van koolstofondersteuning, terwijl de vermogensdichtheid bijna het dubbele is van die van de commerciële elektrokatalysator.
Achtergrond
Een directe methanol-brandstofcel (DMFC) is een van de meest veelbelovende kandidaten voor een hernieuwbare energiebron. Het is een stroomopwekkingssysteem dat elektrische energie produceert door de energie van een chemisch vloeibare (methanol) brandstof direct om te zetten, zonder hulpapparatuur. DMFC's worden aangedreven door hun opwindende mogelijkheden in transport en stationaire toepassingen. Bovendien zijn onderzoekers ook van mening dat dit systeem een van de meest veelbelovende energiebronnen is voor veel mobiele en draagbare toepassingen, evenals een nieuw alternatief voor oplaadbare batterijtechnologie. DMFC's bieden veel voordelen, waaronder een kleinere systeemgrootte en -gewicht. Ze zijn ook schone energiedragers en verminderen de vervuiling. Ondanks deze voordelen worden ze echter ook geconfronteerd met problemen die hun commercialisering belemmeren. De meest uitdagende problemen zijn de slechte elektro-oxidatiekinetiek van methanol en lage systeemprestaties. De totale kosten moeten worden verlaagd en problemen zoals methanol-crossover, duurzaamheid, stabiliteit, warmte en waterbeheer moeten worden verbeterd om de DMFC succesvol te laten zijn [1,2,3].
De ontwikkeling van de DMFC begon tien jaar geleden met het creëren van veel oplossingen waarbij katalysatoren werden gebruikt. Een van de onderzoeken naar de verbetering van de DMFC-prestaties analyseerde verschillende ondersteunende structuren voor katalysatoren, waaronder koolstof nanovezel (CNF), koolstof nanobuis (CNT), koolstof nanodraad (CNW) en andere structuurlagen. De toevoeging van nieuw materiaal aan de katalysator, inclusief het creëren van een nieuwe hybride katalysator, is ook een trend geworden in de DMFC-evolutie [4,5,6]. Ondanks dit onderzoek bestaan er nog steeds problemen, vooral die met betrekking tot lage katalytische activiteit, stabiliteit en geleidbaarheid voor zowel elektronische als protonische werking.
Platina (Pt) is de beste katalysator voor zowel de waterstofoxidatiereactie (HOR) als de zuurstofreductiereactie (ORR). Ondanks dat het effectief is in elektrokatalysatortoepassingen [7,8,9,10], is Pt duur, wat meer onderzoek vereist om een nieuwe katalysator te vinden. Momenteel is bimetaal platina-ruthenium (PtRu) de beste katalysator voor DMFC. Het gebruik van deze katalysator verminderde de Pt-belading, wat de elektrokatalysatorkosten van DMFC verlaagde met een standaardverhouding van 1:1. De rol van Ru in deze bimetaalkatalysator is het verwijderen van het koolmonoxide (CO) van de actieve plaatsen voor de HOR, wat leidt tot een overtreffende trap van de CO-vergiftiging van de katalysator [11, 12]. Volgens een studie van Bock et al., vertoonde PtRu superieure katalytische activiteit in de DMFC, en het was duidelijk dat de katalytische prestatie sterk afhing van de verdeling van Pt- en Ru-sites op atomair niveau [13]. Het probleem van lage methanoloxidatie kan echter niet worden opgelost met behulp van de PtRu-katalysator, dus moet de katalysator verder worden gewijzigd om de brandstofcelindustrie te helpen.
Metaaloxiden zijn de meest prominente materialen die worden gebruikt om de elektrokatalyse van DMFC te verbeteren. Titaandioxide (TiO2 ), ook bekend als titania, is een anorganische stof die van nature stabiel, niet-ontvlambaar en zeer goed bestand is tegen corrosie. Titania is ook niet gecategoriseerd als een gevaarlijke stof door het Globally Harmonized System (GHS) van de Verenigde Naties (VN) voor de classificatie en etikettering van chemicaliën. Bovendien zijn de kristalstructuren van TiO2 zijn thermodynamisch stabiel en helpen een composietmateriaal te creëren met een goede elektrochemische en thermische stabiliteit [14]. De ladingsdragers uit de anataasvorm worden dieper in het bulkmateriaal geëxciteerd, creëren meer oppervlaktereacties en verbeteren stapsgewijs de katalytische activiteit [15]. Het elektronische gedrag van het materiaal wordt verbeterd wanneer de interactie tussen de TiO2 metaaloxide en het andere materiaal ontstaat. Deze verbetering kan ook de oxidatieactiviteit verbeteren door de CO-oxidatiepotentialen te verlagen [6]. Het gebruik van TiO2 als drager voor de metaalkatalysator beïnvloedt de reactiekinetiek en het reactiemechanisme [16]. TiO2 heeft alle eerder genoemde voordelen voor vele toepassingen in verschillende industrieën. Ondanks deze voordelen is het grootste probleem dat het wijdverbreide gebruik ervan voor brandstofceltoepassingen in de weg staat, de lage geleidbaarheid. Om dit probleem op te lossen, moeten hoge beladingen van een Pt-katalysator boven TiO2 samengesteld met een elektrisch geleidend materiaal, zoals N-gedoteerde koolstof, en het gebruik van substoichiometrische TiO2 zijn vereist [5].
Deze studie rapporteerde de synthese en karakterisering van titaniumdioxide-koolstof nanovezel (TiO2 -CNF) afgezet op een platina-ruthenium (PtRu) katalysator voor de DMFC-toepassing. Het doel van de studie was om de samengestelde elektrokatalysator te synthetiseren met TiO2 in een nanovezelstructuur die het vergiftigingseffect van de katalysator kan verminderen terwijl de katalytische activiteit wordt verbeterd om de DMFC-prestaties meer te verbeteren dan de commerciële PtRu/C-elektrokatalysator. TiO2 -CNF werd bereid door elektrospinnen, gevolgd door carbonisatie; ten slotte werd PtRu gedeponeerd met een annotatie van PtRu/TiO2 -CNF. Om de voorbereide PtRu/TiO2 . te karakteriseren -CNF composiet elektrokatalysator met verschillende dragers, röntgendiffractie (XRD), Brunauer-Emmett-Teller (BET), scanning elektronenmicroscoop (SEM) en transmissie-elektronenmicroscoop (TEM) werden gebruikt. De prestaties van de elektrokatalysator werden geëvalueerd door middel van cyclische voltammetrie (CV), elektrochemische oppervlakte (ECSA), Tafelanalyse, chronoamperometrie (CA) en DMFC-enkele cel. Alle prestatie-informatie werd vergeleken met verschillende andere ondersteuningen, waaronder C, CNF en TiO2 . Op basis van de experimentele resultaten werd het effect besproken van het gebruik van het metaaloxide als drager om de katalytische activiteit in de DMFC te verbeteren.
Methoden
Materialen
Titaanisopropoxide (TiPP, 97%) werd verkregen van Sigma-Aldrich Co., Ltd. Poly(vinylacetaat) (PVAc (Mw 500.000)), dimethylformamide (DMF (99,8%)) en azijnzuur (99,7%) werden ontvangen van Sigma-Aldrich Co., Ltd. Ethanol (99,8%) werd gekocht bij R&M Chemical Reagents. Deze chemische reagentia werden gebruikt voor de bereiding van nanovezels. De afzetting omvatte een Pt-precursor, H2 PtCl6 (40% inhoud), van Merck, Duitsland, en een Ru-voorloper, RuCl3 (gehalte van 45-55%) en reductiemiddel, natriumboorhydride (NaBH4 , 96%), van Sigma-Aldrich Co., Ltd. De commerciële katalysatordrager voor C, CNF en TiO2 nanopoeder werden respectievelijk verkregen van Cabot Corporation, Cheap Tubes Inc. en Sigma-Aldrich Co., Ltd. De gedetailleerde eigenschappen voor de katalysatordrager zijn weergegeven in tabel 1. Alle chemische reagentia werden zonder verdere zuivering gebruikt.
Voorbereiding van de TiO2 -CNF
TiO2 -CNF werd gesynthetiseerd met behulp van de sol-gel-methode en elektrospintechniek. De PVAc (11,5 gew.%) oplossing werd bereid door het polymeer 1 uur op te lossen in DMF bij een temperatuur van 60 °C en werd een nacht continu geroerd. 50 gew.% TiPP en een paar druppels ethanol en azijnzuur werden in de PVAc-oplossing gemengd en met een homogenisator geroerd totdat het mengsel homogeen was. De gemengde oplossing werd gevoed vanuit een injectiespuit met een roestvrijstalen naald voor de elektrospintechniek met een constante snelheid van 0,1 ml h −1 , een aangelegde spanning van 16 kV en een afstand van 18 cm tussen de punt en de collector. De elektrospun nanovezel werd 5 uur bij kamertemperatuur gedroogd en bleef 8 uur stabiliseren bij 130 ° C. De vezel werd gecarboniseerd met behulp van een buisoven bij 600 ° C gedurende 2 uur in een stikstofatmosfeer. De gecalcineerde vezel onderging vervolgens een proces om de grootte te controleren met behulp van een vijzel en stamper voordat deze verder in dit onderzoek werd gebruikt.
Voorbereiding van de composiet elektrokatalysator
Alle elektrokatalysatoren werden gesynthetiseerd met behulp van de depositiemethode door chemische reductie van NaBH4 . De 20 gew.% PtRu met de atomaire verhouding 1:1 wordt geladen op verschillende katalysatordragers, die gesynthetiseerde drager zijn, TiO2 -CNF, en nog eens drie commerciële dragers, C, CNF en TiO2 . Een mengsel van gedeïoniseerd water (DI-water) en isopropylalcohol (IPA) werd aan het dragermateriaal toegevoegd en 30 minuten gesoniceerd. De voorlopers werden in het dragermengsel gemengd en werden nog 30 min continu geroerd totdat de oplossing goed gemengd was. De pH-waarde van de oplossing werd ingesteld op 8 met behulp van een 1 M NaOH-oplossing. Vervolgens werd de temperatuur van de oplossing verhoogd tot 80 °C. Een volume van 25 ml van een 0,2 M-oplossing van NaBH4 werd druppelsgewijs aan de oplossing toegevoegd en nog een uur geroerd. Het mengsel werd afgekoeld, gefiltreerd en herhaaldelijk gewassen met DI-water. Het elektrokatalysatorpoeder werd 3 uur bij 120 °C onder vacuüm gedroogd en met een stamper en vijzel fijngemaakt om een fijn poeder te verkrijgen.
Karakterisatie van de elektrokatalysator
Het röntgendiffractiepatroon (XRD) en de kristalstructuur van alle elektrokatalysatoren werden onderzocht met een röntgendiffractometer (D8 Advance/Bruker AXS Duitsland) met behulp van poedervormige monsters en bedreven bij 40 kV en 20 mA. De analyse van het oppervlak en de poriegrootte met behulp van BET werd uitgevoerd door Micromeritics ASAP 2020 in de stikstofadsorptie/desorptie-isotherm bij 77 K. Een onderzoek naar de oppervlaktemorfologie voor de door elektrokatalysatoren ondersteunde nanovezels en de voorbereide elektrokatalysator werd uitgevoerd met behulp van veldemissie scanning-elektronen microscopie (FESEM (SUPRA 55 VP)). Er werd een kaartanalyse uitgevoerd om de verdeling van de elementen op een geselecteerd gebied in een samengestelde elektrokatalysator te observeren. De gedetailleerde structuur van de drager en de samengestelde elektrokatalysator werd geanalyseerd met beelden met hoge resolutie verkregen via transmissie-elektronenmicroscopie (TEM (Tecnai G2 F20 X-Twin)).
Evaluatie van de elektrochemische meting
Elektrochemische metingen werden geëvalueerd door het elektrochemische werkstation van Autolab. De activiteit van de methanoloxidatiereactie (MOR) voor de elektrokatalysator werd gemeten met behulp van de cyclische voltammetrie (CV) van een celsysteem met drie elektroden. Dit systeem gebruikte een glasachtige koolstofelektrode (GCE, 3 mm diameter) als de werkelektrode en Pt en zilver/zilverchloride (Ag/AgCl) elektroden als respectievelijk de tegen- en referentie-elektroden, die bij kamertemperatuur werden gebruikt. De werkelektrode moet voor gebruik worden gereinigd met polijstpapier en aluminiumoxide. De voorbereiding van de elektrokatalysatorinkt voor de werkelektrode werd gedurende 30 minuten ultrasoon gedispergeerd met 15 mg van de elektrokatalysator in een mengsel van 400 L DI-water, 400 μL IPA en 125 μL Nafion-oplossing (5 gew.%). Een micropipet werd gebruikt om 2,5 μL elektrokatalysator-inkt op een GCE over te brengen. De werkelektrode werd gedurende 1 uur bij kamertemperatuur aan de lucht gedroogd en vervolgens gedurende 30 minuten in een oven op 80 ° C verwarmd. De werkelektrode was toen klaar voor CV-meting. Een oplossing van 0,5 M H2 SO4 in 2 M methanol werd bereid als een elektrolyt. Deze elektrolytoplossing werd doorborreld met stikstofgas (N2 ) gedurende 20 min om het zuurstofvrije gehalte te bereiken. De CV-meting is uitgevoerd met een scansnelheid van 20 mV s −1 , en het bereik van potentialen was van 0 tot 1,1 V versus Ag/AgCl. De langetermijnprestaties van alle elektrokatalysatoren werden beoordeeld met behulp van chronoamperometrie (CA) in de elektrolytoplossing bij een potentiaal van 0,5 V gedurende 3600 s.
MEA-fabricage
Membraanelektrode-assemblage (MEA) bestaat uit drie hoofdonderdelen:membraan, anode en kathode. Nafion 117 wordt geselecteerd als membraan en het membraan wordt behandeld om de onzuiverheden te verwijderen met waterstofperoxide (H2 O2 ) en DI-water zoals toegepast in de studie van Hasran et al. [17]. Het behandelde membraan wordt bewaard in de beker gevuld met gedeïoniseerd water totdat het klaar is voor gebruik. Koolstofdoek wordt gebruikt als anode- en kathode-onderlaag. Dit koolstofdoek is behandeld met 5 gew.% polytetrafluorethyleen (PTFE) om het waterdicht te maken. Het koolstofdoek wordt ondergedompeld in de PTFE-oplossing en gedurende 30 minuten bij 380 °C in de oven gedroogd. De ruglaag is gecoat met een gasdiffusielaag van koolstof, waarbij de belasting 2 mg cm −2 is . De koolstof wordt gemengd met de IPA en Nafion-dispersie D520 (Dupont). De koolstofsuspensie wordt op het koolstofdoek gegoten en 1 uur in de oven bij 100 ° C gedroogd. Vervolgens is de elektrokatalysatorlaag klaar om te worden gecoat en gesynthetiseerd door PtRu/TiO2 -CNF en commerciële elektrokatalysator PtRu/C, gebruikt voor het anodedeel, en Pt/C voor het kathodedeel. 2 mg cm −2 belading van elektrokatalysator wordt toegevoegd met IPA (1100 L), DI-water (300 L) en Nafion-dispersie (24 mg). De oplossing wordt gedurende 1 minuut in de homogenisator gedispergeerd en op het koolstofdoek gegoten. De anode en kathode worden 1 uur bij 100 °C in de oven gedroogd. De anode en kathode worden samengeklemd met membraan in het midden met behulp van hete pers bij een toestand van 135 ° C en 50 kPa gedurende 3 minuten. De MEA is klaar om te worden gebruikt in prestatietests met één cel.
Eencellige prestatietests
Prestatietests van DMFC-enkele cellen werden uitgevoerd in passieve toestand en op kamertemperatuur. De MEA met een 2 . van 4 cm actieve gebied wordt vermeld op de enkele cel, waar het anodedeel is bevestigd aan de methanoltank. Tien milliliter 3 M methanol wordt in de tank getankt en getest met potentiostaat/galvanostaat (WonATech, Korea). De celpolarisatiecurve wordt verkregen voor verschillende elektrokatalysatoren.
Resultaten en discussie
Structurele karakterisering
Het patroon en de kristalstructuur van gefabriceerde katalysatordrager, TiO2 -CNF, gesynthetiseerde elektrokatalysator, PtRu/TiO2 -CNF en andere elektrokatalysatoren (PtRu/C, PtRu/CNF en PtRu/TiO2 ) werden onderzocht met XRD-analyse. Deze analyse werd voltooid met behulp van een röntgendiffractometer in het bereik van 5°–90° met 2θ , zoals weergegeven in Fig. 1. Het resultaat voor gesynthetiseerde TiO2 -CNF toont het bestaan van alle materialen, TiO2 , en C. De diffractiepiek van 25° (1 0 1) vertegenwoordigt de TiO2 anataasstructuur, terwijl de piek bij 27° (1 1 0) de TiO2 . is rutiel structuur. Deze bestaande structuren vormen een tetragonale structuur (kristallografische structuur voor anataas en rutiel) [18]. Dit monster had echter de anatasestructuur omdat de TiO2 structuur veranderde van anatase in rutiel terwijl het monster werd blootgesteld aan temperaturen hoger dan 700 ° C [19], terwijl de temperatuur die in dit onderzoek werd gebruikt slechts 600 ° C was.
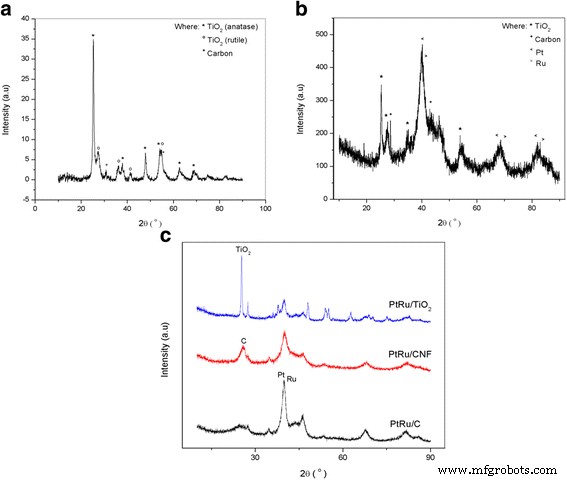
Röntgendiffractiepatronen. een TiO2 -CNF, b PtRu/TiO2 -CNF, en c vergeleken elektrokatalysatoren
De TiO2 -CNF toont meer diffractiepieken voor TiO2 anatase bij 38° (1 1 2), 48° (2 0 0), 55° (2 1 1), 63° (2 0 4), 69° (1 1 6) en 75° (2 1 5) , terwijl die van TiO2 rutiel zijn 36° (1 0 1), 41° (1 1 1) en 54° (2 1 1). De koolstof vertoont bij de diffractiepieken van 31° (1 1 0) en 55° (2 1 1) in kubische structuur. Het XRD-patroon voor PtRu/TiO2 -CNF elektrokatalysator toont de diffractiepiek voor alle betrokken elektrokatalysatoren, Pt, Ru, TiO2 , en C. De piek voor TiO2 en C is bijna hetzelfde met de TiO2 -CNF-monster, en de Pt en Ru vallen op met nog eens vier pieken voor elk materiaal, namelijk Pt op 39,7° (1 1 1), 46,2° (2 0 0), 67,5° (2 2 0) en 81,3° (3 1 1). De diffractiepieken voor Ru zijn 40,7° (1 1 1), 47° (2 0 0), 69° (2 2 0) en 83,7° (3 1 1). Beide metalen komen in de kubische structuur. De gesynthetiseerde elektrokatalysator wordt vergeleken met enkele elektrokatalysatoren ondersteund met verschillende katalysatordragers, namelijk roet (PtRu/C), koolstof nanovezel (PtRu/CNF) en titaniumdioxide nanodeeltjes (PtRu/TiO2 ), en het diffractiepatroon wordt berekend in Fig. 1c.
Hoge Bragg-hoeken waren duidelijk zichtbaar, vooral in het bereik van 25 ° -60 ° voor het gehele elektrokatalysatormonster. Hieruit bleek dat er een bimetaal- of legeringsinteractie optrad in de katalysator [20]. Een zwakke en brede intensiteit werd waargenomen voor alle elektrokatalysatormonsters, wat hoge dispersies in het voorbereide monster illustreert. De kristallietgrootte werd gemeten met behulp van de Debye-Scherrer-vergelijking [8]; kristalliet grootte = 0.98α /β cosθ . Waar α is de golflengte van de röntgenstraal, θ is de hoek bij de piek, en β is de breedte van de piek op halve hoogte. De waarde van de kristallietgrootte was beschikbaar via Eva-software voor het analyseren van de XRD-resultaten en werd berekend met behulp van de Debye-Scherrer-vergelijking. De kristallietgrootte voor alle monsters is in tabel 2 weergegeven. De kristallietgrootte voor PtRu werd berekend als 4,64 tot 9,84 nm, TiO2 varieerde van 19 tot 38,4 nm en C was tussen 10,7 en 19,2 nm.
Oppervlakte- en porositeitsanalyse van alle elektrokatalysatormonsters werden geanalyseerd met behulp van BET-analyse. De stikstofabsorptie/desorptie-isotherm wordt uitgevoerd bij 77 K. Het oppervlak, het totale porievolume en de gemiddelde poriediameter van PtRu/TiO2 -CNF, PtRu/C, PtRu/CNF en PtRu/TiO2 elektrokatalysatoren staan vermeld in tabel 3. Het BET-oppervlak voor de nanovezelstructuur van metaaloxidecomposiet, PtRu/TiO2 -CNF elektrokatalysator, toont de laagste waarde met 50,59 m 2 /g, gevolgd door PtRu/CNF, PtRu/TiO2 , en PtRu/C-elektrokatalysatoren in oplopende volgorde. De resultaten die in deze studie zijn verkregen, liggen dicht bij de resultaten van het BET-oppervlak dat is uitgevoerd door een ander onderzoek [6], waarbij de PtRu/C-elektrokatalysator een veel groter oppervlak vertoont in vergelijking met de elektrokatalysator van metaaloxidecomposiet.
Het totale porievolume, V Totale porie , toont resultaten in oplopende volgorde geïnitieerd door PtRu/TiO2 -CNF < PtRu/CNF < PtRu/TiO2 < PtRu/C (0,227 < 0,370 < 0,529 < 0,734). Het resultaatpatroon van het totale porievolume en het BET-oppervlak is hetzelfde, wat aangeeft dat een toename van het volume van het porievolume het totale oppervlak van de elektrokatalysator kan vergroten. Vermindering van oppervlakte en porievolume van PtRu/TiO2 -CNF-elektrokatalysator is te wijten aan blootstelling en gebruik van carbonisatietemperaturen tot 600 ° C; ondertussen ondergaan andere elektrokatalysatoren geen carbonisatie en blootstelling aan hoge temperaturen. Dit komt door het sintereffect, wat vervolgens leidt tot de groei van deeltjes en kristallisatie [21].
De stikstofadsorptie/desorptie-isothermgrafieken bij 77 K voor alle elektrokatalysatoren zijn samengevat in Fig. 2. De resultaten laten zien dat de poriën voor alle elektrokatalysatormonsters mesoporeuze eigenschappen benadrukken, die een gemiddelde diameter hebben binnen het bereik van 2-50 nm, wat kan grotendeels worden toegeschreven aan de grote opening in het elektrokatalysatorrooster. Dit type elektrokatalysator heeft het vermogen om het distributieniveau en de homogeniteit van de geïmmobiliseerde katalysator te verhogen, wat resulteert in een betere stabiliteit en katalytische activiteit [22].
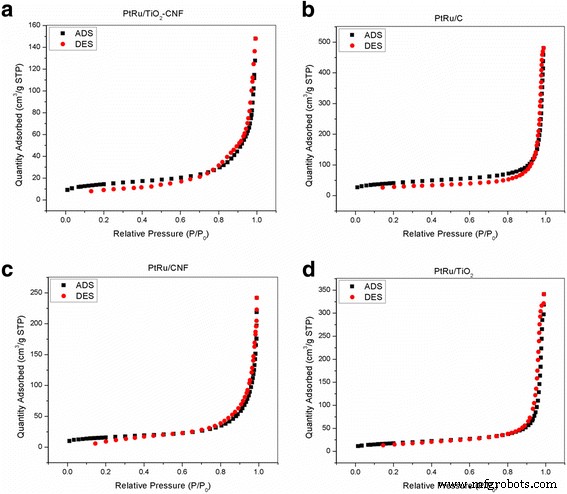
Stikstofadsorptie (ADS) en desorptie (DES) isotherm bij 77 K. a PtRu/TiO2 -CNF, b PtRu/C, c PtRu/CNF, en d PtRu/TiO2
De gemiddelde poriediameter van de vier geteste elektrokatalysatormonsters lag tussen 22 en 33 nm, en de poriediameter van de PtRu/TiO2 -CNF vertoonde de laagste diameter in vergelijking met andere elektrokatalysatoren. De grootte van de kleine diameter illustreert de grootte van het deeltje als geheel. De kleine deeltjesgrootte heeft een hoge oppervlakte-tot-volumeverhouding en resulteert mogelijk in een verhoogde oppervlaktereactiviteit en oplosbaarheid en kan het toxiciteitsprofiel van de stof veranderen. Bovendien lijkt de waarneming van de stikstofadsorptie/desorptie-isothermgrafiek vlak bij relatief lage druk (P /P o ≤ 0.6), wat te wijten kan zijn aan de absorptie van microporiën in het monster. In een relatief hogedrukgebied (0.6 < P /P o < 1.0), is er een toename in het adsorptievermogen van het monster vanwege de adsorptie van monolaag- en/of meerlaagse stikstofmoleculen in de mesostructuur.
Afbeelding 9 toont de SEM-afbeeldingen voor de nanovezelondersteuning, TiO2 -CNF. De afbeelding illustreert dat de nanovezel soepel wordt geproduceerd zonder agglomeraten, kralen of verbonden nanovezels, wat gebeurt vanwege equivalente elektrospinparameters [23]. De verdeling voor de diameter van TiO2 -CNF wordt onderzocht door 100 diametermetingen voor deze katalysatordrager te verzamelen en geanalyseerd door de "Origin Software", en de grootte van de distributiediameter is 136,73 ± 39,56 nm in het bereik van 90-170 nm.
De voorbereide elektrokatalysator, PtRu/TiO2 -CNF, onderging ook SEM-analyse, en het beeld wordt getoond in Fig. 10. Figuur 10a is de katalysator die is afgezet op de drager, PtRu/TiO2 -CNF, na het maalproces. Het SEM-beeld zag dat de lange vezel bedekt is met Pt- en Ru-nanodeeltjes. De afbeelding toont echter enige agglomeratie van Pt- en Ru-nanodeeltjes. Om de verdeling van Pt en Ru te zien, wordt de afbeelding getoond in Fig. 10b voor Pt en Fig. 10c voor Ru. De resultaten van de mapping illustreerden dat beide metalen uniform op de nanovezel waren gedispergeerd; er trad echter enige agglomeratie op voor Pt als gevolg van een fout tijdens het depositieproces. De agglomeratie van nanodeeltjes was een reactieresultaat vanwege overmatig gebruik van de NaOH-oplossing tijdens de pH-aanpassing voor het depositieproces [24].
De TEM-beelden voor de voorbereide katalysatordrager, TiO2 -CNF, en elektrokatalysator, PtRu/TiO2 -CNF, worden getoond in Fig. 11. De TEM-afbeeldingen van katalysatordrager Fig. 11a laten zien dat de TiO2 werd homogeen gedispergeerd in een koolstofnanovezel met een diameter van 136 nm, vanwege de homogene dispersie van polymeeroplossing en TiO2 voorloper tijdens sol-gel methode. Afbeelding 11b toont het beeld van katalysator afgezet op TiO2 -CNF, waarbij PtRu-deeltjes met een diameter van ongeveer 7 nm werden afgezet op de TiO2 -CNF en blootgesteld aan de TiO2 oppervlakte. Deze verbinding en de blootstelling aan TiO2 kan een actievere reactieplek opleveren tijdens de voorstelling. De PtRu-deeltjes klonterden echter samen en waren niet homogeen verdeeld over het oppervlak van de nanovezel.
Elektrochemische karakterisering
De elektrochemische karakterisering wordt toegepast op alle katalysatoren om hun potentieel en prestaties als anodische katalysator in DMFC te zien. Er zijn twee hoofdmetingen in deze sectie, namelijk cyclische voltammetrie (CV), om de elektrokatalytische prestaties te meten, en chronoamperometrie (CA), om de stabiliteit en duurzaamheid van de monsters op lange termijn te testen. Afbeelding 3 toont de CV-profielen van alle katalysatoren in 0,5 M H2 SO4 oplossing in het potentiaalbereik tussen -0,2 en 1,2 V. Het waterstofadsorptie-/desorptiegebied, in het bereik van -0,2 tot 0,1 V, wordt ook aangegeven als het elektrochemisch actieve oppervlak (ECSA) dat wordt berekend. De ECSA is de schatting van het oppervlak van PtRu-nanodeeltjes in de elektrokatalysator [25]. De procedure omvatte een cyclus van elektrodestroom in het spanningsbereik, waarbij de ladingsoverdrachtsreacties adsorptiebeperkt zijn op de activeringsplaatsen. De totale lading die nodig is voor monolaag adsorptie/desorptie wordt gebruikt als reactieve oppervlakteplaatsen voor ECSA [26]. Het geëvalueerde ECSA-resultaat wordt weergegeven in tabel 4. ECSA voor de CV-meting werd bepaald met behulp van de onderstaande vergelijking:
$$ \mathrm{ECSA}\ \left({\mathrm{m}}^2{\mathrm{g}}_{\mathrm{Pt}}^{-1}\right)=\frac{Q}{ \varGamma .{W}_{Pt}} $$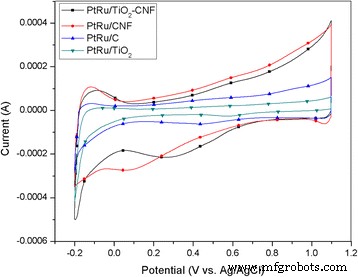
Cyclische voltammetrieprofielen van de verschillende katalysatordragers, PtRu/TiO2 -CNF, PtRu/CNF, PtRu/C en PtRu/TiO2 in 0,5 M H2 SO4 oplossing met een scansnelheid van 20 mV s −1
waar Q is de ladingsdichtheid of het gebied onder de grafiek ((C) van het CV-experiment), Γ (2,1 CmPt −2 ) is de constante voor de lading die nodig is om de protonmonolaag op de Pt te verminderen, en W Pt is de Pt die wordt geladen (gPt ) op de elektrode. De ECSA-berekeningsresultaten laten zien dat de gesynthetiseerde elektrokatalysator, PtRu/TiO2 -CNF, heeft de hoogste waarde van 10,4 m 2 gPtRu −1 , gevolgd door PtRu/CNF (8,4 m 2 /gPtRu ), PtRu/C (0,94 m 2 gPtRu −1 ), en PtRu/TiO2 (0,76 m 2 gPtRu −1 ). Dit gebeurde vanwege verschillende sleutelfactoren. Een daarvan is de kristallietgrootte van PtRu, zoals vermeld in tabel 2 van XRD-analyse; de PtRu-kristallietgrootte voor PtRu/TiO2 -CNF is de kleinste en vertoont een hoge ECSA-waarde. De kleinste kristallietgrootte kan een toename van het katalysator- en reactieoppervlak veroorzaken. De trend van de kristallietgrootte wordt gevolgd met de trend van de ECSA-waarde voor PtRu/CNF en PtRu/C. Echter, PtRu/TiO2 monster kan vermoedelijk een hogere ECSA-waarde produceren dan PtRu/C, aangezien de kristallietgrootte kleiner is, maar de verkregen ECSA is lager. Dit kan gebeuren door de agglomeratie van het PtRu-deeltje in het monster. Deze agglomeratie kan het potentiële oppervlak om te reageren verkleinen en de ECSA verminderen.
De elektrokatalytische prestaties van gesynthetiseerde elektrokatalysatoren en andere elektrokatalysatoren werden geanalyseerd met CV zoals geïllustreerd in Fig. 4. De CV-curve voor de elektrokatalysatoren, inclusief PtRu/TiO2 -CNF, PtRu/C, PtRu/CNF en PtRu/TiO2 , wordt gemeten in 2 M methanol met 0,5 M H2 SO4 met verzadigde N2 gassen bij kamertemperatuur. De meerdere curven worden gemeten binnen het potentiaalbereik van -0,1 tot 1,1 V vs. Ag/AgCl. Afbeelding 4 laat zien dat de piekstroomdichtheid in afnemende volgorde PtRu/TiO2 was -CNF > PtRu/CNF > PtRu/C > PtRu/TiO2 . De piekstroomdichtheid van PtRu/TiO2 -CNF voor de MOR bleek ongeveer 0,639 V vs. Ag/AgCl te zijn. De piekstroomdichtheid en andere CV-waarden voor alle monsters worden vermeld in Tabel 4. De stroomdichtheidswaarde voor de PtRu/TiO2 -CNF-katalysator is 345,64 mA(mgPtRu ) −1 , die 1,85 en 5,54 keer hoger zijn dan PtRu/CNF en commerciële elektrokatalysator, PtRu/C. Dit toont aan dat de TiO2 -CNF-katalysatordrager was een betere vervanging voor de roetkatalysatordrager. Dit komt omdat het nanovezelmengsel, door het carbonisatieproces, de elektro- en thermische geleidbaarheid van de katalysator kan verhogen [27].
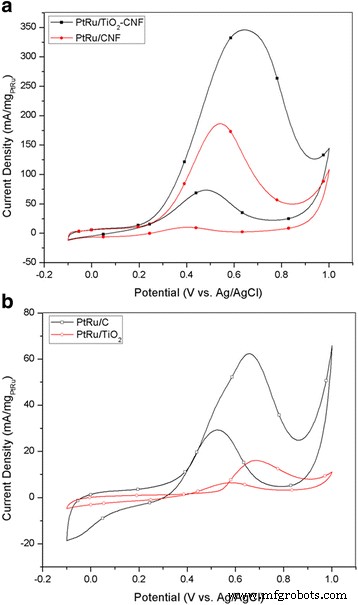
CV in 2 M methanol en 0,5 M H2 SO4 met een scansnelheid van 20 mV s −1 . een PtRu/TiO2 -CNF en PtRu/CNF. b PtRu/C en PtRu/TiO2
Nanovezelstructuur in de samengestelde elektrokatalysator kan het totale oppervlak en de actieve reactieplaats op het oppervlak van de elektrokatalysator vergroten. Een ander voordeel was de aanwezigheid van hoge anataas TiO2 samenstelling zoals resulteerde in XRD-analyse. Hogere elektrokatalytische activiteit wordt verkregen door anatase dan rutiel TiO2 . De interactie tussen metaal en drager vertoont ook een positief effect met een hogere piekstroomdichtheid, waarbij de materiaalcombinatie tussen PtRu en TiO2 -CNF vertoont een succesvolle combinatie voor elektrokatalysator in DMFC. De op één na hoogste piekstroomdichtheid met de waarde van 186,29 mA/mgPtRu behoort tot PtRu/CNF dat 2,99 keer hoger is dan de commerciële elektrokatalysator, PtRu/C. Dit resultaat komt overeen met de studie van Zainoodin et al. [28] en Ito et al. [29]. De gelijkenis van PtRu/TiO2 -CNF en PtRu/CNF is de ondersteunende structuur van de nanovezelkatalysator. De hoge piekstroomdichtheid voor beide monsters toont aan dat de nanovezel een uitstekende prestatie van methanoloxidatie kan geven vanwege het vermogen van nanovezel om het oppervlak van de elektrokatalysator te vergroten en de katalytische activiteit te verbeteren. De prestatie voor PtRu/C is veel lager dan die welke het gevolg was van de agglomeratie van PtRu, waar de ECSA-waarde en kristallietgrootte van XRD worden weergegeven. Deze situatie vermindert het potentieel van het oppervlak van de elektrokatalysator om een actieve plaats te zijn en verlaagt de prestatie van de elektrokatalysator. De zeer lage activiteit van PtRu/TiO2 was te wijten aan de aard van de TiO2 katalysatordrager met lage elektrische geleidbaarheid [4]. Deze resultaten laten duidelijk zien dat het elektrisch geleidende medium essentieel was voor de katalysatorsystemen voor een elektrochemische reactie [30].
De meerdere CV-curven in Fig. 4a, b tonen de omgekeerde scan en de kleine oxidatiepiek verschijnt tussen 0,4 en 0,57 V versus Ag/AgCl. De vorming van onvolledige geoxideerde koolstofhoudende soorten tijdens de eerste oxidatiepiek resulteerde in de kleine oxidatie op reversed scan, ook bekend als reversed oxidatiepiek [31]. This oxidation peak shows the tolerance of electrocatalyst towards the carbonaceous species by calculating the ratio of forward (I f ) and reversed (I b ) oxidation peak. The oxidation peak ratio called as CO tolerance is tabulated in Table 4. The result shows that both samples using nanofiber support, PtRu/TiO2 -CNF, and PtRu/CNF have the highest electrocatalyst tolerance against carbonaceous species, which means these can lower the catalyst poisoning potential, with the ratio exceeding 4.7 respectively. This result shows that nanofiber structure and the combination of metal oxide in electrocatalyst can reduce the main problem faced by DMFC technology and have high potential to replace the commercial support used in this technology.
The synthesis electrocatalyst, PtRu/TiO2 -CNF, is compared with other PtRu-based electrocatalyst, nanostructured catalyst support, and combination of metal oxide in electrocatalyst for DMFC technology and shown in Table 5. The result shows that the peak current density for PtRu/TiO2 -CNF is the highest among other electrocatalysts. However, the high value of current density is obtained by using the nanostructure catalyst support and TiO2 as one of the side material in the composite electrocatalyst. Even though there are several different types of metal oxide used in the other study, the performance shows a gap with the TiO2 -utilized electrocatalyst.
Other than CV, linear sweep voltammetry (LSV) is one of the important electrochemical studies of electroactive substance. LSV is quite similar to CV, which measures the current response as a voltage function. Figure 5 shows the LSV plot for all the electrocatalysts that were measured in 2 M methanol and 0.5 M H2 SO4 at the scan rate of 20 mVs −1 in the N2 gas environment. The result shows that the synthesized electrocatalyst, PtRu/TiO2 -CNF, shows the highest current density that was calculated over the electrode surface area. The trend of the current density for LSV and CV is equalized. The LSV point shows the rising region between 0.5 and 0.7 V vs Ag/AgCl, and this region is known as a Tafel region that appeared when the electron transfer kinetics occur in the electrocatalyst surface [32]. The LSV data is extracted to present Tafel plot, where it relates the electrochemical reaction rate to the overpotential.
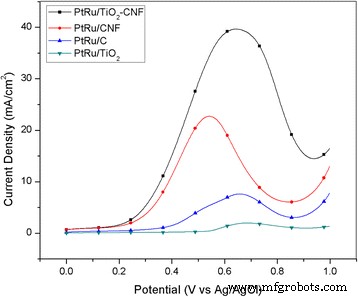
LSV in 2 M methanol and 0.5 M H2 SO4 at the scan rate of 20 mV s −1 for all samples
The Tafel plot of overpotential, E , against log I is presented in Fig. 6, and data extraction of the plot is tabulated in Table 6. This plot can provide and calculate the slope of anodic Tafel plot (b een ) and ionic exchanging current density (j ) from the slope and interception of the Tafel plot. Anodic Tafel slope, b een , for all the electrocatalyst has not much difference in value, while the ionic exchange current density gives a big gap between each electrocatalyst. The ionic exchange current density is also known as a catalytic activity explainer [33]. The j for all electrocatalysts shows the difference, where the highest value belongs to PtRu/TiO2 -CNF with the value of 0.5012 mA cm −2 . This result demonstrates that the synthesized electrocatalyst can produce the highest catalytic activity of bimetallic PtRu compared with other electrocatalyst. Even though the bimetallic composition for all the electrocatalysts is same, the synthesized electrocatalyst gets a greater help from the metal oxide in producing the highest active area for catalytic activity. PtRu/CNF and PtRu/C electrocatalysts have the same value, while PtRu/TiO2 has the lowest of ionic exchange current density with 0.112 and 0.046 mA cm −2 , respectievelijk.
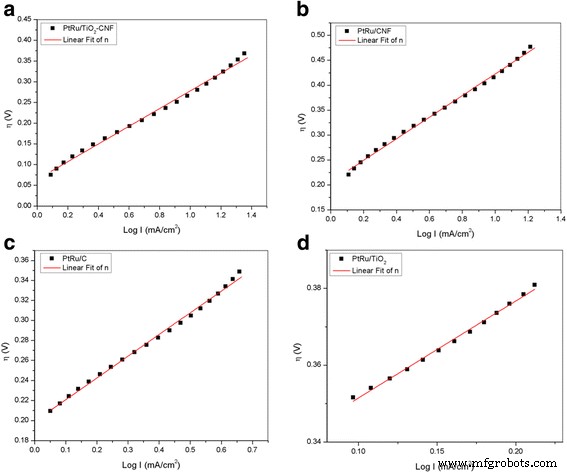
Tafel plot of the electrocatalyst a PtRu/TiO2 -CNF, b PtRu/CNF, c PtRu/C, and d PtRu/TiO2
The CA experiments were conducted to determine the stability and durability of the electrocatalyst for the long-term performance of MOR in a 2-M solution of methanol containing 0.5 M H2 SO4 for 3600 s. Figure 7 shows the CA curve for the PtRu/TiO2 -CNF, PtRu/C, PtRu/CNF, and PtRu/TiO2 electrocatalysts at a constant potential, 0.5 V. The current density of PtRu/TiO2 electrocatalysts shows the effect of a sharp drop at the start of the experiment, possibly due to the effect of poisoning by methanol oxidation mediation. The PtRu/TiO2 -CNF, PtRu/CNF, and PtRu/C electrocatalysts showed a slight decline of approximately 5 and 3% in current density, respectively. After 3600 s, all of the electrocatalysts were stable, and the reducing current density ratios in increasing order are as follows:PtRu/CNF (6.16) < PtRu/TiO2 -CNF (6.54) < PtRu/C (11.66) < PtRu/TiO2 (14.82). The PtRu/TiO2 -CNF electrocatalyst showed the reducing current density ratio is slightly higher than PtRu/CNF, but this electrocatalyst reached the highest current density of all the electrocatalysts. This was due to good dispersion of the catalyst support and also to increased use of catalysis [6].
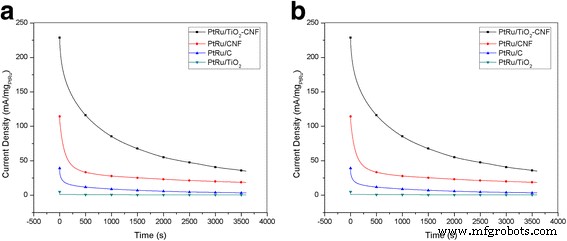
CA curve at potential of 0.5 V vs Ag/AgCl for PtRu/TiO2 -CNF, PtRu/C, PtRu/CNF, and PtRu/TiO2 katalysatoren
DMFC Single-Cell Performance
The synthesized electrocatalyst, PtRu/TiO2 -CNF, with the highest electrochemical/half-cell performance was tested with single-cell performance. The performance is compared with commercial electrocatalyst, PtRu/C, using same composition, 20 wt% of PtRu. The 4-cm 2 anode electrocatalyst layer clamped with cathode and membrane to be MEA, ready for single-cell performance using 3 M methanol of passive system. Figure 8 shows the current–voltage curve for PtRu/TiO2 -CNF and PtRu/C. The PtRu/TiO2 -CNF showed the highest performance compared to the commercial electrocatalyst, which is 1.66 times higher. The maximum power density for synthesized electrocatalyst was 3.8 mW cm −2 , while PtRu/C was 2.2 mW cm −2 .
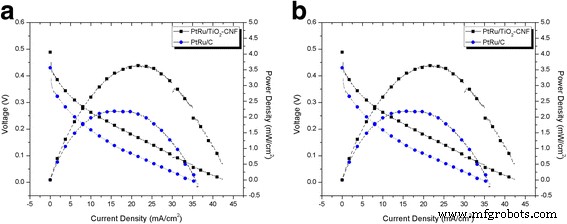
Current–voltage curve for PtRu/TiO2 -CNF and PtRu/C in 3 M methanol with 2 mg cm −2 catalyst loading at room temperature
The best PtRu/TiO2 -CNF performance is confirmed by comparing this result with the previous study of commercial PtRu/C electrocatalyst, using the same catalyst loading in passive mode system that is tabulated in Table 7. The overall electrochemical and single-cell performance conclude that the combination of bimetallic catalyst, PtRu, and introduction of metal oxide nanofiber with carbon nanofiber have high potential to be replaced with PtRu/C in DMFC technology (Figs. 9, 10, and 11). By using the low composition of bimetallic catalyst and electrocatalyst loading, the synthesized electrocatalyst reveals the superior DMFC performance.
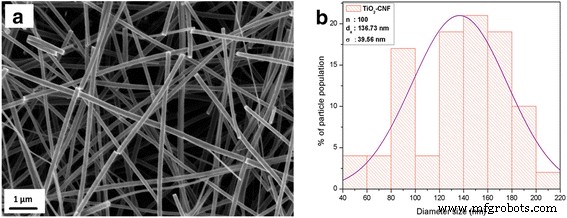
SEM images. een TiO2 -CNF image (magnification × 10,000). b Distribution of diameter size for TiO2 -CNF
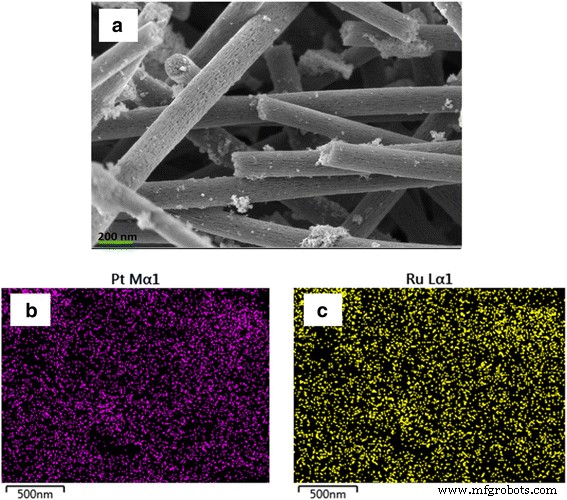
PtRu/TiO2 -CNF catalyst after deposition and milling. een SEM images (magnification × 30,000), b mapping of Pt nanoparticles, and c mapping of Ru nanoparticles
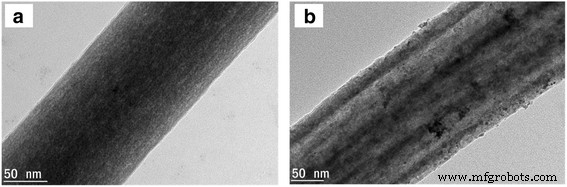
TEM images for prepared a TiO2 -CNF catalyst support and b PtRu/TiO2 -CNF electrocatalyst
Conclusies
De TiO2 -CNF was synthesized using an electrospinning method and applied in the DMFC as a catalyst support for an anodic catalyst. The catalytic activity for the electrocatalyst was prepared for different catalyst supports including PtRu/TiO2 -CNF, PtRu/C, PtRu/CNF, and PtRu/TiO2 , which were compared with one another. The results showed that the prepared electrocatalyst, PtRu/TiO2 -CNF, had the highest current density, which was 5.54 times higher than that of the commercial electrocatalyst, PtRu/C. The DMFC single-cell performance of PtRu/TiO2 -CNF reveals the superior performance almost twice higher than that of PtRu/C. The highest catalytic activity was due to the nanofiber catalyst structure and the introduction of TiO2 as the catalyst support. The reaction with the metal support interface between the PtRu and TiO2 -CNF catalysts helped to improve the properties of the catalyst layer. PtRu/TiO2 -CNF is a promising candidate for support of the anode catalyst in DMFCs.
Afkortingen
- BET:
-
Brunauer-Emmett-Teller
- CA:
-
Chronoamperometry
- CNF:
-
Carbon nanofiber
- CNT:
-
Carbon nanotube
- CNW:
-
Carbon nanowire
- CV:
-
Cyclische voltammetrie
- DI:
-
Deionized
- DMF:
-
Dimethylformamide
- DMFC:
-
Direct methanol fuel cell
- ECSA:
-
Electrochemical surface area
- GCE:
-
Glazige koolstofelektrode
- GHS:
-
Globally Harmonized System
- HOR:
-
Hydrogen oxidation reaction
- IPA:
-
Isopropyl alcohol
- LSV:
-
Linear sweep voltammetry
- MEA:
-
Membrane electrode assembly
- MOR:
-
Methanol oxidation reaction
- ORR:
-
Oxygen reduction reaction
- PTFE:
-
Polytetrafluoroethylene
- SEM:
-
Scanning elektronenmicroscoop
- TEM:
-
Transmissie elektronenmicroscoop
- UN:
-
United Nations
- XRD:
-
Röntgendiffractie
Nanomaterialen
- 3D-printen van aangepaste brandstofinjectorgrijpers voor een pick-and-place-robot
- Nanovezels en filamenten voor verbeterde medicijnafgifte
- Technieken voor additieve productie en prototypering
- Nieuw, hittegestabiliseerd nylon 6 voor hybride en elektrische aandrijflijnen
- One-Pot Green-synthese van met Ag versierde SnO2-microsfeer:een efficiënte en herbruikbare katalysator voor reductie van 4-nitrofenol
- Nieuwe biocompatibele Au Nanostars@PEG-nanodeeltjes voor in vivo CT-beeldvorming en eigenschappen voor nierklaring
- Vervaardiging en karakterisering van nieuwe composiet Tio2 koolstof nanovezel anodische katalysatorondersteuning voor directe methanolbrandstofcel via elektrospinmethode
- Verbeterde prestaties van een nieuwe anodische PdAu/VGCNF-katalysator voor elektro-oxidatie in een glycerolbrandstofcel
- Vergelijking tussen foliumzuur en op gH625 peptide gebaseerde functionalisering van Fe3O4 magnetische nanodeeltjes voor verbeterde celinternalisatie
- Hoe u het brandstofverbruik voor zware constructie- en landbouwmachines kunt maximaliseren?
- De fabricage en bewerking van metalen onderdelen voor brandstofinjectiesystemen