3D-filamentwikkeling maakt zitconcept in het voertuig mogelijk
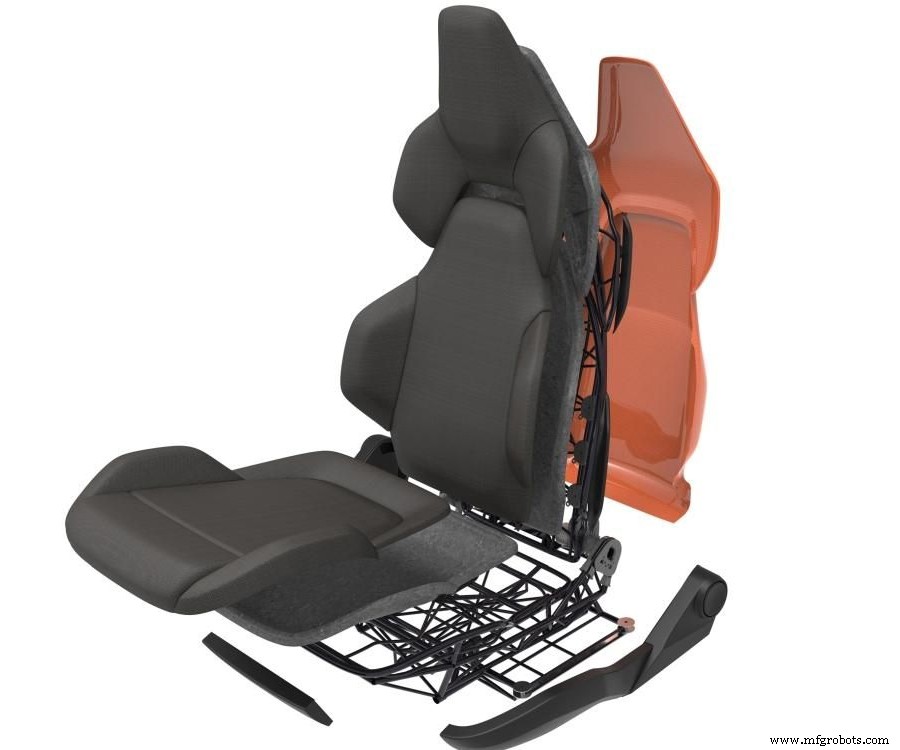
Duurzaamheid en verantwoordelijkheid voor het milieu worden steeds vaker de drijvende kracht achter technologische trends in de auto-industrie. Energiezuinige en emissiearme voertuigen zijn een prioriteit geworden voor de internationale automobielsector, en trends in de richting van alternatieve vervoerstechnologieën zoals elektromobiliteit en stedelijke luchtmobiliteit (UAM) winnen aan kracht. OEM's zijn op zoek naar nieuwe materialen en processen om deze toekomstige vormen van reizen mogelijk te maken, maar de veranderingen in de automobielsector gaan vaak traag. Om nieuwe materialen en processen volledig te kunnen toepassen, moeten ze niet alleen gekwalificeerd zijn, ze moeten ook kosteneffectief zijn en ze moeten productie in grote hoeveelheden mogelijk maken.
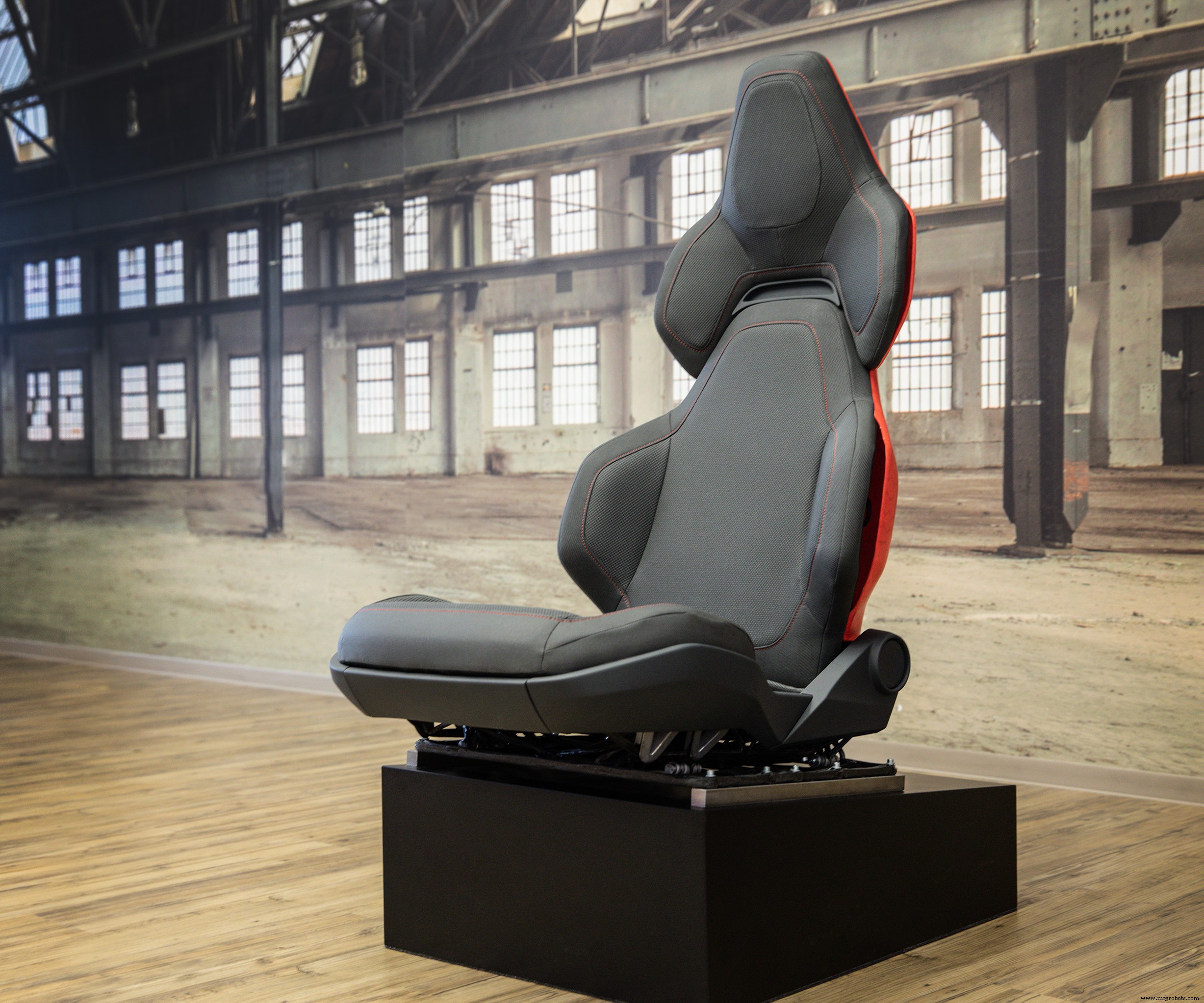
Ultra lichtgewicht zadel. Het Ultra Leichtbausitz (ULBS) zitconcept is ontwikkeld door een samenwerking tussen meerdere bedrijven met behulp van een combinatie van technologieën. Bron | csi entwicklungstechnik
Onlangs heeft een innovatief project met potentieel voor de automobielsector - evenals voor opkomende markten zoals hypercars en luchttaxi's - aangetoond hoe nieuwe materialen, processen en technologieën, en nauwe samenwerking tussen bedrijven, vervoerswijzen van de volgende generatie mogelijk kunnen maken. Het doel van het project was om een autostoeltje volledig te heroverwegen met behulp van geavanceerde generatieve technologieën, en om dit te doen met slechts zoveel van het juiste materiaal als nodig is op de juiste plaats — en om snel resultaat te boeken. Het resulterende ultralichte, metaal-composiet hybride voertuigstoelprototype werd in slechts zeven maanden van ontwerp tot fabricage ontwikkeld via een simulatiegestuurde ontwerpaanpak, flexibele projectbeheermethoden en nauwe samenwerking en systeemintegratie tussen de betrokken bedrijven.
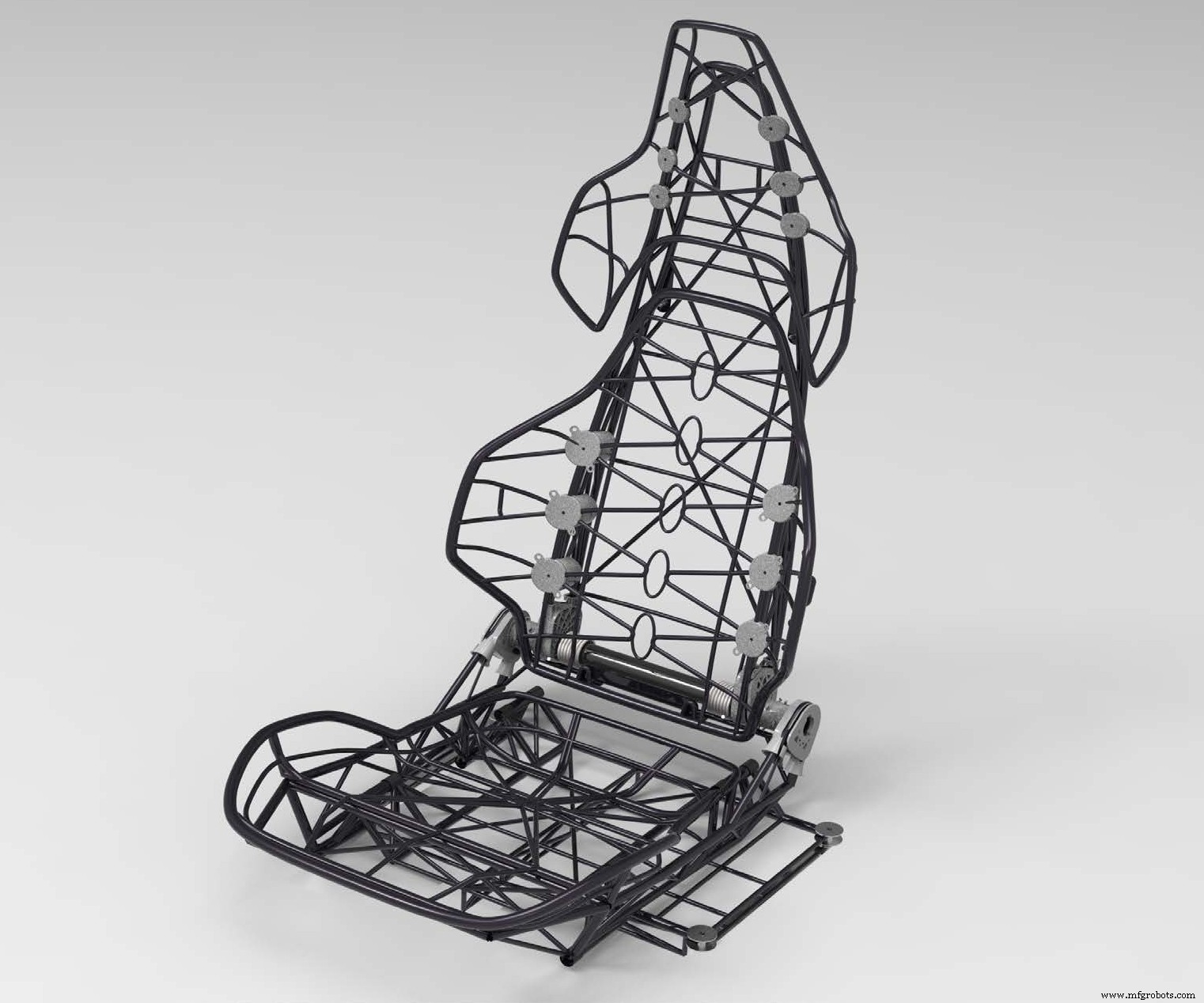
Een betere stoel bouwen
De Ultraleichtbausitz (ULBS) ultralichte stoel haalbaarheidsstudie is ontwikkeld door een samenwerking tussen meerdere bedrijven met behulp van een combinatie van technologieën. De visie van het project was, in de woorden van de groep, "het creëren van een ultralichtgewicht zitconcept dat uitblinkt in de markt in termen van gewichtsoptimalisatie." Initiërende bedrijven csi entwicklungstechnik GmbH (csi, Neckarsulm, Duitsland), Alba Tooling &Engineering (Forstau, Oostenrijk) en Automotive Management Consulting (AMC, Penzberg, Duitsland) ontwikkelden het prototype zitconcept in samenwerking met Covestro (Leverkusen, Duitsland), LBK Fertigung (Friedberg, Duitsland), Robert Hofmann (Lichtenfels, Duitsland) en 3D|CORE (Herford, Duitsland).
Het samenwerkingsproject resulteerde in een stoelprototype met een gewicht van iets meer dan 10 kilogram, inclusief het kussen, het structurele frame, functionele inzetstukken en de zitconsole waarmee het op een voertuig kan worden gemonteerd. De stoel is 20% lichter dan vergelijkbare lichtgewicht stoelen op de markt, waarvan veel aftermarket-stoelen. Volgens ULBS-projectleider Stefan Herrmann, verantwoordelijk voor lichtgewicht design bij CSI, zijn er momenteel geen concurrerende stoelen op de markt die minder dan 12 kilogram wegen.
"Een directe vergelijking is echter vaak geen appels met appels, omdat aftermarket-stoelen vaak de zitconsole niet in de gewichtsdefinitie opnemen", zegt Herrmann, "Ook het zitcomfort van de ULBS is een stuk hoger in vergelijking met stoelen met vergelijkbaar gewicht. Bestaande stoelen zijn vaak kuipstoelen, die een nog lager gewicht hebben maar niet zo comfortabel, of traditionele supersportstoelen, die een veel hoger gewicht hebben.”
De ULBS beschikt over verschillende innovatieve technologieën, waarvan de fiber roving skeletstructuur op basis van procestechnologie xFK in 3D de meest prominente rol speelt. (Zie "Filamentwikkeling, opnieuw uitgevonden" voor meer informatie over xFK in 3D en andere filamentwikkeltechnologieën.) Het fundamentele belang van de bekroonde technologie voor eindeloze depositie van vezelroving ligt in de vrijheid van ontwerp, in de simulatiegestuurde en materiaal- geoptimaliseerde vezelplaatsing zowel precies in de belastingsrichting als bij het eenvoudig, kostenefficiënt en afvalvrij aanbrengen van vezelmateriaal. Voor de lastoverdracht in deze raamwerkstructuur is gebruik gemaakt van 3D-geprinte onderdelen. In gebieden met de hoogste belasting, zoals de rugleuningen, maakt de stoel gebruik van 3D-geprinte structuren gemaakt van roestvrij staal met een hoge sterkte en hoge modulus. In minder belaste gebieden wordt aluminium 3D-printen gebruikt.
csi entwicklungstechnik, een engineeringbedrijf dat gespecialiseerd is in carrosserie-in-witte (BIW)-constructies, evenals auto-interieurs en exterieurs met zakelijke gebieden zoals koolstofvezelversterkte polymeren (CFRP) en additieve fabricage, hield toezicht op en coördineerde het project op basis van de idee van het AMC. csi verzorgde de styling, verharding, concept, simulatie, design engineering en projectmanagement voor het project.
Herrmann legt uit:"csi was verantwoordelijk voor de werkpakketten op het gebied van de digitale procesketen - styling, engineeringontwerp, oppervlakteontwerp, CAE-simulatie, topologiesimulatie, validatiesimulatie en virtuele bevestiging van het project."
Hij benadrukt dat wat het ULBS-project opmerkelijk maakt, niet alleen het gebruik van innovatieve materialen en productiemethoden is, maar ook de ontwikkeling van een complex onderdeel dat nieuwe componentontwerpen omvat binnen een kort tijdsbestek van zeven maanden door nauwe samenwerking tussen partners.
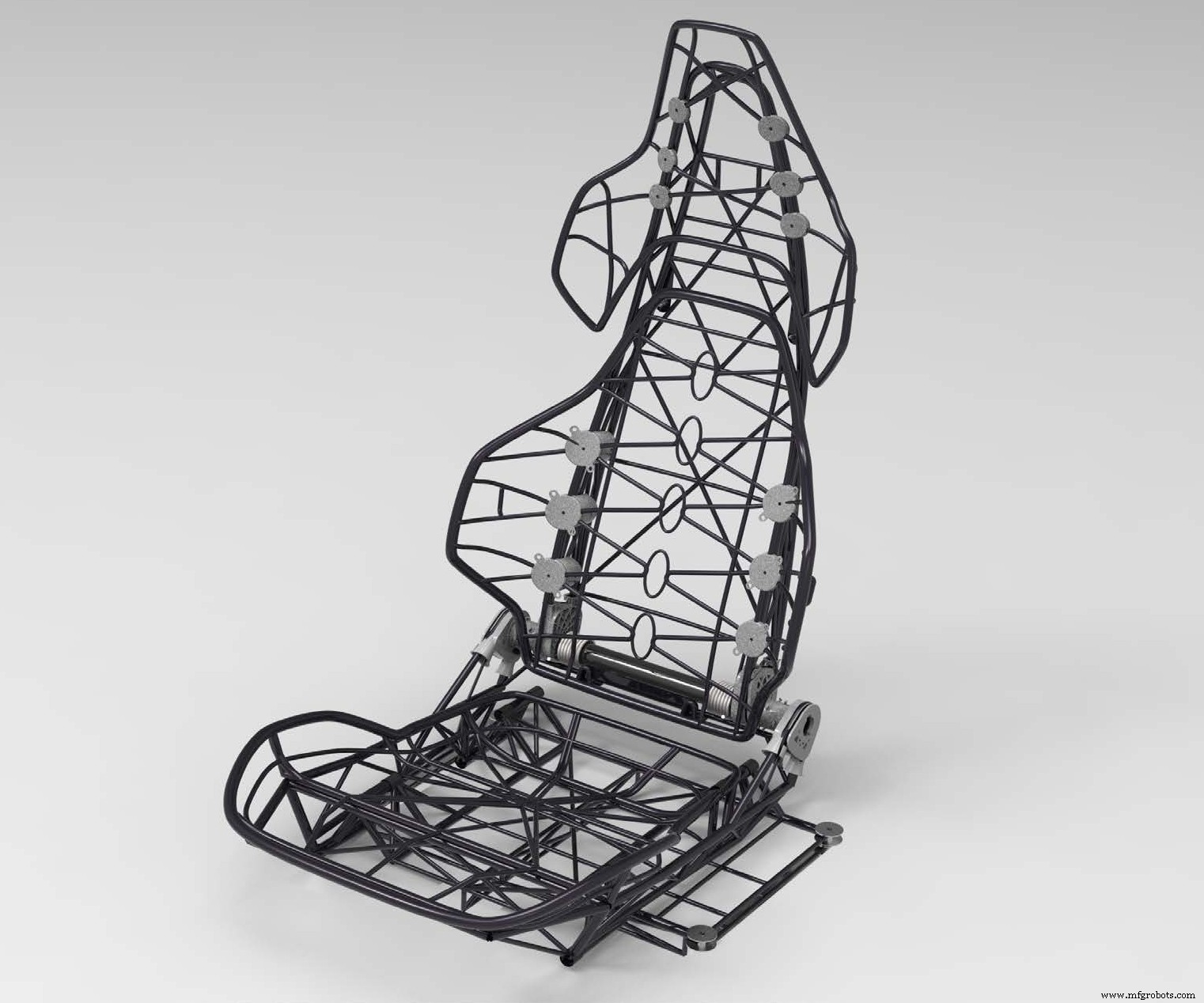
Filamentgewonden stoelframe. Een groot deel van de gewichtsvermindering in het ULBS-project is het resultaat van AMC's vezelwikkelprocestechnologie xFK in 3D. Bron | csi entwicklungstechnik
Een frame opwinden
Een groot deel van de gewichtsvermindering in het ULBS-project is het resultaat van AMC's xFK in 3D, een zeer flexibele, configureerbare, kosteneffectieve en duurzame vezelcomposiettechnologie voor het opwinden van componenten.
xFK in 3D is al gebruikt voor een verscheidenheid aan producten en toepassingen voor verschillende industrieën en marktsegmenten. SGL Group Wiesbaden, Duitsland) toonde verschillende auto- en fietsonderdelen vervaardigd met deze technologie op de internationale composietenbeurs JEC World 2018. Een van de getoonde onderdelen, een koolstofvezel kettingblad ontwikkeld door AMC, zou het gewicht tot 70% verminderen vergeleken met een aluminium versie.
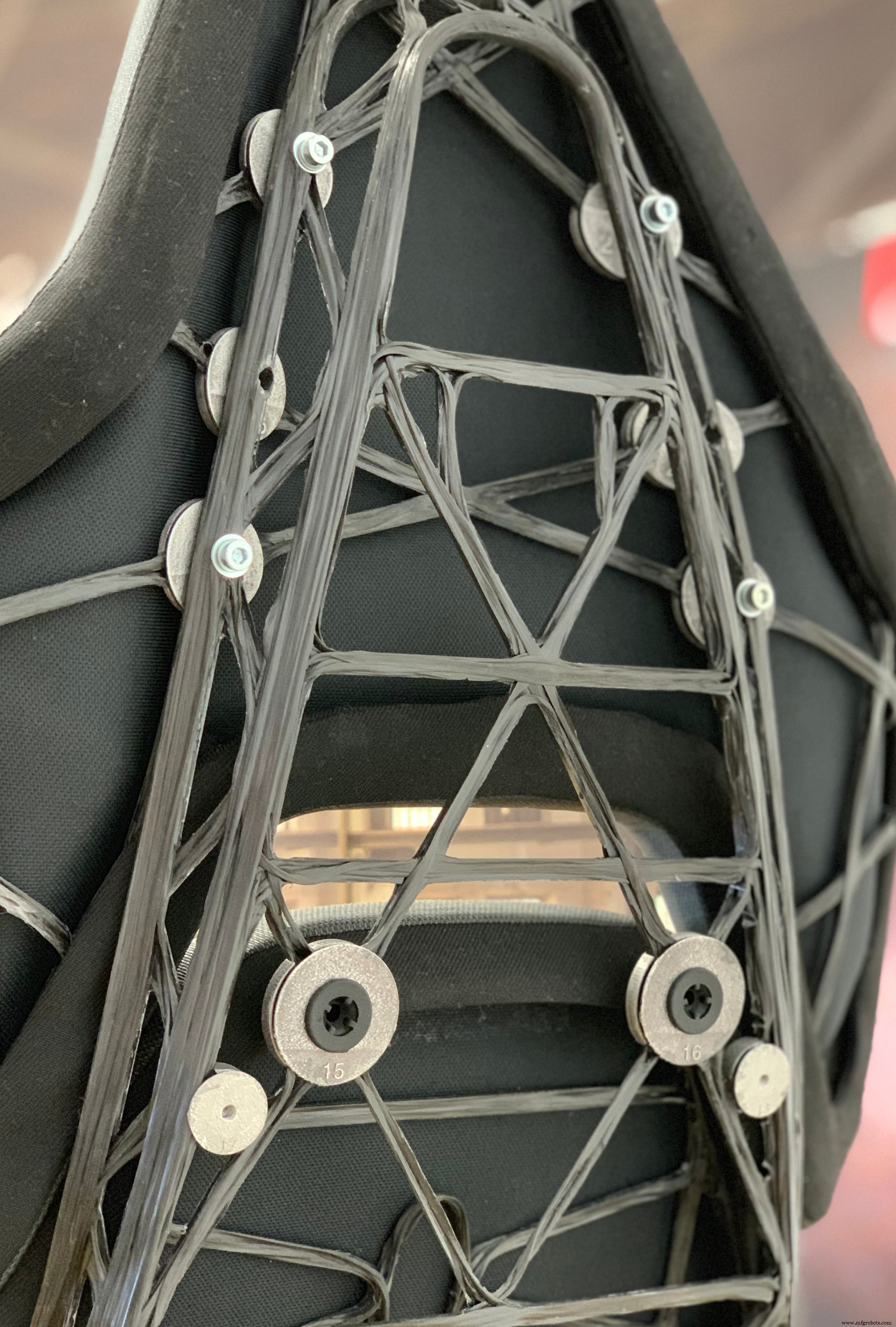
Wikkelbussen. Een met thermohardende hars geïmpregneerde vezelroving wordt rond een positioneringsinrichting gewikkeld, waardoor vezels kunnen worden gerangschikt om te passen bij de belastingen van elk onderdeel en de gewenste functies. Bron | csi entwicklungstechnik
Het xFK in 3D-proces windt dragende constructies afvalvrij op met behulp van met thermohardende hars geïmpregneerde continue vezels. Een met epoxyhars verzadigde vezelroving wordt rond een positioneringsinrichting of wikkelbussen gewikkeld, waardoor vezels specifiek kunnen worden gerangschikt om te passen bij de belastingen van elk onderdeel en de gewenste functies.
"Een groot voordeel van xFK in 3D is de eliminatie van zwakke punten met betrekking tot belastingoverdracht en belastingintroductie in constructies", zegt Herrmann. Hij legt uit dat zwakke punten zich vaak niet in het continuüm van de constructie bevinden, maar in de gebieden waar belastingen in de constructie worden geïntroduceerd, vooral waar aangrenzende componenten zijn verbonden met de constructie. De xFK in 3D-technologie maakt belastingoverdracht over verbindingen mogelijk en maakt het mogelijk vezels uit te lijnen volgens de gewenste componentfuncties en belastinggevallen, en in drie dimensies te vervaardigen.
Het filamentwikkelproces levert ook extra voordelen op. Het proces helpt materiaalverspilling tot een minimum te beperken — minder dan 1% van de vezelroving wordt verspild.
csi herkende xFK in de sterke punten van 3D en ontwierp het ULBS-stoelframe dat zou worden gebouwd onder advies van Dr. Clause Georg Bayreuther, hoofd technologie van AMC.
"In samenwerking met csi-ingenieurs, AMC-consultants en Alba's gereedschapsexperts hebben we dit concept en de structuur ontwikkeld voor het stoelframe dat moet worden vervaardigd met behulp van het xFK in 3D-proces", zegt Peter Fassbaender, technologieconsultant en initiatiefnemer van xFK in 3D-technologie.
Alba vervaardigde het gereedschap voor het CFRP-stoelframe en leverde technische ondersteuning. Ook, hoewel het stoelframe is gewikkeld uit koolstofvezel, zijn natuurlijke vezels of basaltvezels ook goede kandidaten.
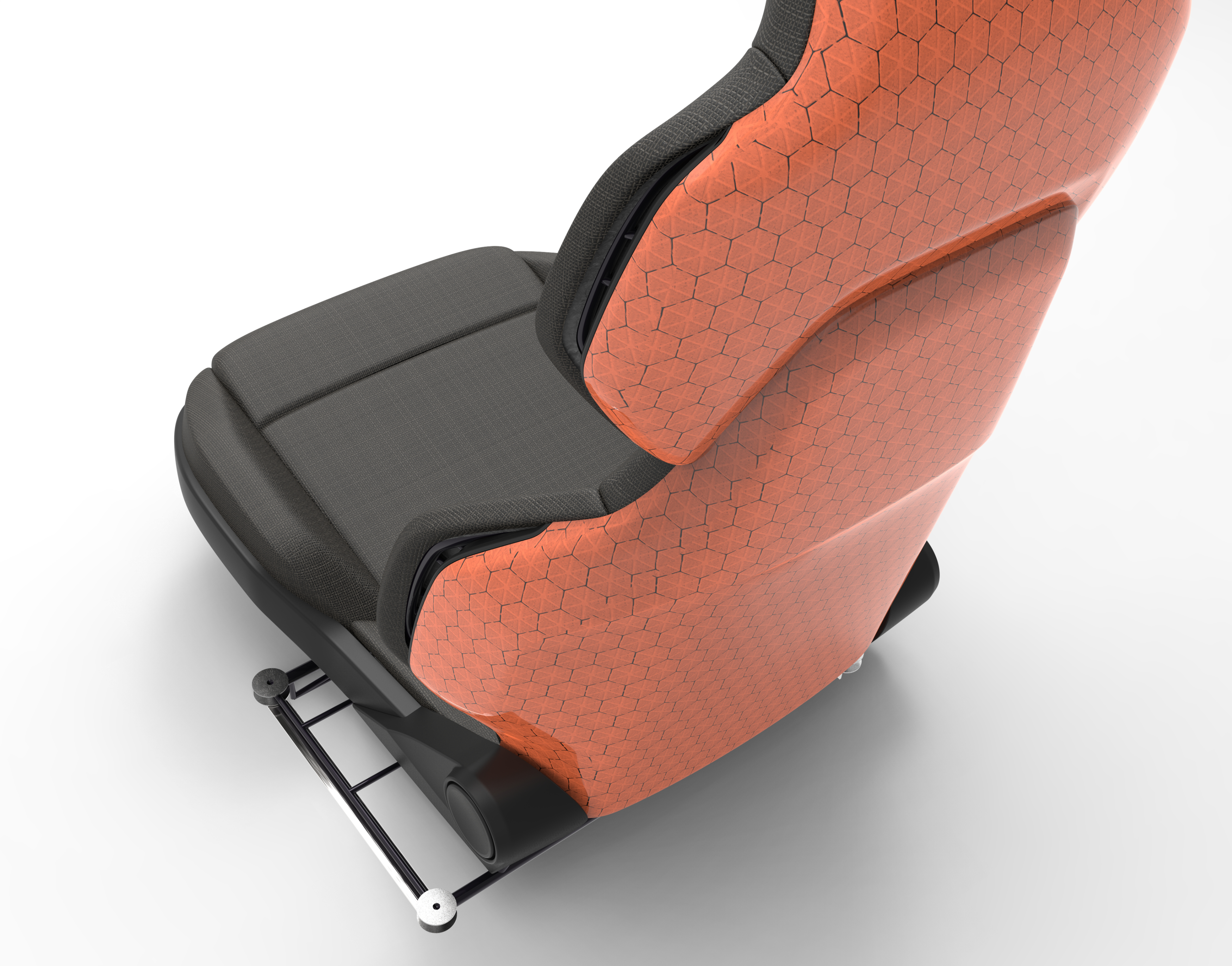
Nieuwe technologieën. Het ULBS-prototype maakt gebruik van een combinatie van nieuwe technologieën, waaronder een achterpaneelschaal gemaakt van intralaminair versterkend kernmateriaal (IRC) en 3D-geprinte rugleuningkussens gemaakt van thermoplastisch polyurethaan (TPU). Bron | csi entwicklungstechnik
Een hybride materiaalstructuur
Naast het frame bevat het ULBS-prototype verschillende andere nieuwe innovaties. Alba, die het gereedschap leverde, leverde ook het gereedschap, de engineering en de fabricage voor het schuimlichaam van de stoel en voerde de montage van de stoel uit. Een vezelvliesmat bedekt het CFRP-frame van de stoel, dat vervolgens wordt bedekt door een 3D-geprinte PUR-schuimhoes. Het zitkussengedeelte is gemaakt van traditioneel schuim.
Verdere gewichtsvermindering werd bereikt door het gebruik van 3D|CORE, een materiaal met een intralaminaire versterkende kern (IRC), in de structuur van het achterpaneel van de rugleuning. Het materiaal is een intralaminair versterkend kernmateriaal (IRC) - een structurele sandwichkern die bestaat uit kernlichamen van geëxtrudeerd polystyreen (XPS) en polyethyleentereftalaat (PET) in een geïntegreerd honingraatpatroon. Tijdens de productie van composietonderdelen wordt de honingraatstructuur gevuld met hars, wat resulteert in een hoge intralaminaire sterkte. De 3D|Core is geassembleerd tussen twee lagen glasvezel om een voorvorm te creëren, die is doordrenkt met thermoplastische epoxyhars met behulp van vacuüm-ondersteunde harsoverdracht (VA-RTM).
Covestro leverde zijn Dispercoll-lijm als bindmiddel voor de vezelvliesmatten, evenals het 3D-geprinte rugleuningkussen. Volgens Herrmann zorgen de mechanische eigenschappen van Dispercoll voor een goede slijtvastheid, wat belangrijk is omdat oppervlaktecontact tussen het kussen en het frame het vlies na verloop van tijd aan slijtage kan onderwerpen.
“Als je een enkele vezel hebt, als je dat in een textiel stopt, krijg je microbewegingen tussen de harde CFRP-delen en de fleecematten. De onderdelen van het zitframe kunnen tegen het textiel wrijven en het vernietigen”, legt Herrmann uit.
Traditionele stoelen hebben doorgaans een groter oppervlak dat de demping ondersteunt en hebben dit probleem niet. Bij xFK in 3D is er echter een kleiner contactoppervlak vanwege de framestructuur.
“Als xFK in 3D-structuren tegen de fleecestof drukt, moet je een specifiek en duurzaam bindmiddel hebben; dit is wat Dispercoll in deze context biedt”, voegt Herrmann toe.
Covestro leverde ook wat naar verluidt 's werelds eerste 3D-geprinte kussen is. Terwijl conventioneel en gereedschapsintensief schuim typisch wordt gebruikt in rugleuningen, verhoogt het gebruik van de 3D-geprinte rugleuningkussens, die zijn gemaakt van TPU (thermoplastisch polyurethaan), de flexibiliteit en aanpasbaarheid van de ULBS-stoel verder met betrekking tot zijn esthetiek, functionele integratiemogelijkheden en comfort.
Een stoel voor de toekomst
Het ULBS-project realiseert verschillende doelen. Het resulterende concept, hoewel nog niet op de markt, heeft het potentieel om tal van nichemarkten te bedienen, zoals hypercars, luchttaxi's, ultralichtgewicht voertuigen, micromobiliteit, helikopters, multicopters en luchtvaart. Hoewel weliswaar duurder dan productieautostoelen, demonstreert de ULBS verschillende technologieën die afval minimaliseren en zo de materiaalkosten verlagen. In vergelijking met andere koolstofvezeltechnologieën levert xFK in 3D een zeer lage hoeveelheid afval op. In feite is het hele project gericht op het gebruik van minimale middelen en slechts het noodzakelijke minimum van het materiaal. De ULBS biedt ook de mogelijkheid om hernieuwbare en duurzame bronnen zoals natuurlijke vezels in de framestructuur, kussens en textiel te gebruiken.
Maar wat nog belangrijker is, het project laat zien hoe bedrijven de time-to-market kunnen minimaliseren door samen te werken via korte en flexibele coördinatieprocedures. Het is ook een goed voorbeeld van het gebruik van design thinking om een product met succes van idee naar hardware-prototype te brengen door te focussen op de functionele vereisten en vooruit te kijken naar toekomstige toepassingen en duurzaamheidsdoelen.
vezel
- Kronkelende configuraties
- Fietszitje
- Eenwieler
- Kinderzitje
- Ultra-wide band-chip maakt smartphone-gebaseerde voertuigtoegang mogelijk
- Edge computing-platform maakt diepgaande toegang tot autogegevens mogelijk
- Prestatiekenmerken van glasvezelgaren
- Koolstofvezel toiletbrilhoes
- Liftgate-ontwerp stelt aangepaste filamentwikkeling op de proef
- Nieuwe technologieën en markten op World of Filament Winding-evenement
- Roth filamentwinder om grote Ariane 6 gewichts-/kostenbesparingen te vergemakkelijken